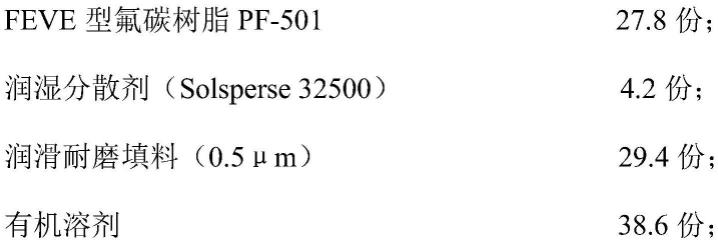
1.本发明属于防腐涂料技术领域,具体涉及一种减摩耐磨防腐涂料及其制备方法。
背景技术:2.防腐涂料在机械、石油化工、建筑、海洋工程等钢结构上得到广泛应用。目前针对设备的装配结合面及相对运动面,包括铰接转动轴配合面和吊耳滑行面以及承载关节轴承、齿轮、衬套等部件,通常为加工成型且有一定精度的非涂层防护表面,采用润滑油脂进行保护,但维修时需反复拆装,结合面部位易受摩擦和挤压。另在风沙较为严重的荒漠地带,即使对装配结合面及相对运动面定期添加润滑油脂维护,因油脂对沙尘的吸附,在低频往复摩擦过程中产生的磨削可使运动滞涩,磨痕破坏处金属部件的腐蚀速度加快。区别于通常的机械设备,军用设备在实际使用中可能会在各种地理环境大范围的转移,用于部件防护的减摩防腐涂层除了需要耐受一般环境条件的腐蚀及低频往复摩擦磨损外,还可能需要耐受高盐雾、高湿热、强太阳辐射、冷热交变、风沙刮擦等环境条件。此外,该类结构部件通常有一定的精度要求;在这种情况下,虽然弹性体类、粉末类涂层防护有效,但因该类涂层干膜较厚(通常200μm以上),并不适宜这类部件的防护。
3.公开号为cn107603358a,名称为一种复合石墨烯的氟碳防腐涂料的制备方法的专利,公开了采用液相转移超声法制备溶剂型石墨烯分散液,并与三氟乙烯聚合物和四氟乙烯聚合物混合搅拌,再加入固化剂、重防腐添加剂、成膜助剂,分散剂、防沉剂等搅拌混合均匀后,调节粘度,制得复合石墨烯的氟碳防腐涂料,该方案利用石墨烯复合材料制具有消弱紫外光辐射特性,通过将紫外光波转换成热或二次辐射能量,延长阻止涂层高分子链的断裂,提升重防腐能力,使得涂料具有很强的防腐性能,但该材料的耐磨、耐候性能未知。
4.公开号为cn104804571a,名称为具有有机氟碳涂层的油管及有机氟碳涂料的专利,公开了由重量百分比为50.0%~70.0%氟碳树脂、0.5%~2.0%分散剂、0.5%~1.5%流平剂、0.2%~1.0%防沉剂、1.0%~3.0%消泡剂、5.0%~10.0%增塑剂、10.0%~20.0%石墨、0.5%~1.0%炭黑、0.2%~0.5%有机钛螯合物、5.0%~10.0%混合溶剂和1.0%~2.0%固化剂的组分制成的涂料,该涂料具有抗氧化、耐磨、防腐蚀等优势,但其主要使用在油田的空气驱油管和石油输送管道,而是否能够适用于经常拆卸组装的设备尚未可知。
5.因此,研究一种能够解决设备易摩擦磨损部件在高盐雾、高湿热、强太阳辐射及盐碱、酸雨、冷热交替等环境的腐蚀防护问题,最大程度地确保设备的环境适应性的涂料具有重要意义。
技术实现要素:6.本发明针对现有技术的不足,旨在解决设备易摩擦磨损部件在高盐雾、高湿热、强太阳辐射及盐碱、酸雨、冷热交替等环境的腐蚀防护问题,最大程度地确保设备的环境适应性,提出了一种减摩耐磨防腐涂料及其制备方法。
7.具体是通过以下技术方案来实现的:
8.一种减摩耐磨防腐涂料由a、b组分按质量比为4~10:1混合而成,所述a组分按质量份计包括以下成分:氟碳树脂20~35份,润滑耐磨填料25~35份,润湿分散剂0.5~5.0份,有机溶剂35~50份;所述b组分按质量份计包括以下成分:固化剂20~100份,稀释剂0~80份且不取零;所述的氟碳树脂为feve型氟碳树脂;所述的润滑耐磨填料为石墨、聚四氟乙烯、碳化硅、二硫化钼中的一种或几种。
9.进一步优选,所述的氟碳树脂为pf-501、zx-1003、jf-2x、jf-3x中的一种。
10.所述的润滑耐磨填料的粉末粒径为0.5~5μm。
11.所述的润滑耐磨填料按质量份计由如下组合方式中的任意一种:1)石墨0.1~15份,碳化硅0.1~20份,聚四氟乙烯0.1~15份,二硫化钼0.1~10份;2)石墨0.1~15份,碳化硅0.1~20份,聚四氟乙烯0.1~15份;3)石墨0.1~15份,碳化硅0.1~20份,二硫化钼0.1~10份;4)石墨0.1~15份,聚四氟乙烯0.1~15份,二硫化钼0.1~10份;5)碳化硅0.1~20份,聚四氟乙烯0.1~15份,二硫化钼0.1~10份。
12.所述的润湿分散剂为高分子超分散剂;优选solsperse 32500、akn-2350、ld-1132中的一种。
13.所述的有机溶剂为乙酸丁酯、环己酮、二甲苯中的一种或几种;
14.所述的固化剂为hdi固化剂,所述的hdi固化剂为六亚甲基二异氰酸酯缩二脲(简称hdi缩二脲)、六亚甲基二异氰酸酯三聚体(简称hdi三聚体)中的一种;优选desmodurn75、desmodurn3390;
15.所述的稀释剂为乙酸丁酯、环己酮、二甲苯中的一种或几种。
16.本发明提供了前述减摩耐磨防腐涂料的制备方法,具体包括以下步骤:
17.1)将a组分配方中的部分有机溶剂加入氟碳树脂中,在200-550rpm速率下搅拌10-20分钟,得到均匀且质量分数为50%的透明溶液;
18.2)在步骤1)得到的透明溶液中加入润湿分散剂,在200-550rpm速率下搅拌5-10分钟,得到混合溶液;
19.3)在步骤2)得到的混合溶液中加入润滑耐磨填料和a组分配方中剩余有机溶剂,在200-550rpm速率下搅拌5-10分钟,之后球磨分散2~6h,得到浆料;
20.4)将步骤3)得到的浆料用100目~400目筛网过滤,得到a组分;
21.5)按b组分配方量取固化剂和稀释剂,并将两者混合,在200-550rpm速率下搅拌10-20分钟,得到b组分;
22.6)将a、b组分按质量比为4~10:1混合,在200-550rpm速率下搅拌10-20分钟,之后用100目~400目筛网过滤,即制得减摩耐磨防腐涂料。
23.本发明还提供了所述减摩耐磨防腐涂料的涂层制备方法,具体包括以下步骤:
24.1)底材表面处理:底材表面无可溶性盐、油脂、锈蚀、污物、旧涂层等杂质,表面清洁度经喷射清理至少达到gb/t 8923规定的sa2.5,或经手工、动力工具清理达到gb/t 8923规定的st3,底材表面残存灰尘数量和大小不得超过gb/t 18570.3规定的等级2,底材的表面粗糙度与gb/t 13288.1中规定的中(g)或细(g)一致;
25.2)涂料混配:减摩耐磨防腐涂料现配现用,4~6h内涂装有效;
26.3)涂料喷涂:常温空气喷涂制备涂层,采用与试样平行、垂直交替的方式喷涂,喷
枪压力0.2~0.4mpa,枪嘴与工件之间垂直距离10~25cm;涂层厚度由喷涂次数控制,每次喷涂厚度为10~20μm,重复喷涂2~5次,涂层总厚度为20~100μm;
27.4)涂层固化:保持环境清洁无尘;涂层固化在大气中进行,涂层表干时间1h以内,实干时间24h,完全固化3~5天。
28.有益效果:
29.本发明的涂料是一种常温固化型涂料,制作、施工和维护方法简便,制成的涂层与钢、铝、铜等基材有良好的附着力,涂层的柔韧性、耐冲击性、硬度、耐磨性等机械性能良好,涂层的耐酸碱、耐湿热、耐盐雾、耐温度冲击及抗紫外老化等防腐性能优异,涂层的摩擦系数低,在液压油、润滑脂、汽油等介质中适应性良好,可用于铰接转动轴配合面、吊耳滑行面以及承载关节轴承、齿轮、衬套等装配部件的结合面和运动摩擦面在湿热、盐雾、强太阳辐射及盐碱、酸雨、冷热交替等严苛工况下的腐蚀防护。
30.1)本发明的涂料以feve型氟碳树脂为基体树脂,确保了涂层优异的耐候性、耐腐蚀性、高柔韧性及其与不同金属底材(如q345a钢、40cr钢、5a06铝、06cr18ni11ti、铸铝104、铸钢zg270-500、h65铜、t2铜、2a12铝、2014铝等)良好的附着力,耐酸碱及耐溶剂性优良,适于重防腐蚀涂装;
31.2)本发明的涂料通过微米级填料的协同作用调节涂层的耐磨、自润滑以及力学性能,其中石墨微粉、聚四氟乙烯微粉、二硫化钼微粉提高涂层的自润滑性能,碳化硅微粉提高涂层的耐磨性,结合高分子分散剂对几种微米级填料的均匀稳定分散,提高涂层致密性、柔韧性以及疏水性能,从而保证持久、优异的防腐、减摩效果;
32.3)本发明的涂料以feve型氟碳树脂配合hdi缩二脲或hdi三聚体固化,因此涂膜常温即可固化,涂装工艺简单,对结构部件无尺寸限制,特别适用于对精度要求的结构部件及不能提供高温环境固化的设备的涂装维护。
具体实施方式
33.下面对本发明的具体实施方式作进一步详细的说明,但本发明并不局限于这些实施方式,任何在本实施例基本精神上的改进或代替,仍属于本发明权利要求所要求保护的范围。
34.实施例1
35.一种减摩耐磨防腐涂料由a组合和b组分按如下配方制成:
36.a组分按质量份计配方为:
[0037][0038]
b组分按质量份计配方为:
[0039]
固化剂(desmodurn3390)
ꢀꢀꢀꢀꢀꢀꢀꢀꢀꢀꢀꢀꢀꢀꢀꢀꢀꢀ
20.0份;
[0040]
稀释剂
ꢀꢀꢀꢀꢀꢀꢀꢀꢀꢀꢀꢀꢀꢀꢀꢀꢀꢀꢀꢀꢀꢀꢀꢀꢀꢀꢀꢀꢀꢀꢀꢀꢀ
80.0份;
[0041]
所述润滑耐磨填料由石墨8.3质量份、聚四氟乙烯13.3质量份、碳化硅7.8质量份组成;所述有机溶剂和稀释剂均由乙酸丁酯、二甲苯、环己酮按7:2:1的质量比组成;
[0042]
所述减摩耐磨防腐涂料的制备方法,包括如下步骤:
[0043]
1)将a组分配方中的部分有机溶剂加入feve型氟碳树脂中,在450rpm速率下搅拌10分钟,得到均匀、质量分数为50%的透明溶液,
[0044]
2)在步骤1)得到的透明溶液中加入润湿分散剂,在450rpm速率下搅拌10分钟,得到混合溶液;
[0045]
3)在步骤2)得到的混合溶液中加入润滑耐磨填料和a组分配方中的余量有机溶剂,在500rpm速率下搅拌5分钟,之后球磨分散4h,得到浆料;
[0046]
4)将步骤3)得到的浆料用400目筛网过滤,得到a组分;
[0047]
5)按b组分配方量取固化剂与稀释剂,并将两者混合后,在400rpm速率下搅拌10分钟,得到b组分;
[0048]
6)将a、b组分按质量比为4:1混合,在300rpm速率下搅拌10分钟,之后用400目筛网过滤即可使用。
[0049]
实施例2
[0050]
一种减摩耐磨防腐涂料由a组合和b组分按如下配方制成:
[0051]
a组分按质量份计配方为:
[0052][0053]
b组分按质量份计配方为:
[0054]
固化剂(desmodurn75)
ꢀꢀꢀꢀꢀꢀꢀꢀꢀꢀꢀꢀꢀꢀꢀꢀꢀꢀ
28.7份;
[0055]
稀释剂
ꢀꢀꢀꢀꢀꢀꢀꢀꢀꢀꢀꢀꢀꢀꢀꢀꢀꢀꢀꢀꢀꢀꢀꢀꢀꢀꢀꢀꢀꢀꢀ
71.3份;
[0056]
所述润滑耐磨填料由石墨8.6质量份、聚四氟乙烯8.1质量份、二硫化钼13.8质量份组成;所述有机溶剂由乙酸丁酯、二甲苯、环己酮按7:2:1的质量比组成;所述稀释剂由乙酸丁酯、二甲苯按7:3的质量比组成;
[0057]
所述减摩耐磨防腐涂料的制备方法,包括如下步骤:
[0058]
1)将部分有机溶剂加入feve型氟碳树脂中,在400rpm速率下搅拌15分钟,得到均匀、质量分数为50%的透明溶液,
[0059]
2)在步骤1)得到的透明溶液中加入润湿分散剂,在400rpm速率下搅拌5分钟,得到混合溶液;
[0060]
3)在步骤2)得到的混合溶液中加入润滑耐磨填料并补足有机溶剂,在450rpm速率下搅拌5分钟,之后球磨分散4h,得到浆料;
[0061]
4)将步骤3)得到的浆料用240目筛网过滤,得到a组分;
[0062]
5)按b组分配方量取固化剂与稀释剂,并将两者混合后,在400rpm速率下搅拌10分钟,得到b组分;
[0063]
6)将a、b组分按质量比为5:1混合,在350rpm速率下搅拌10分钟,之后用240目筛网过滤即可使用。
[0064]
实施例3
[0065]
一种减摩耐磨防腐涂料由a组合和b组分按如下配方制成:
[0066]
a组分按质量份计配方为:
[0067][0068]
b组分按质量份计配方为:
[0069]
固化剂(desmodurn75)
ꢀꢀꢀꢀꢀꢀꢀꢀꢀꢀꢀꢀꢀꢀꢀꢀꢀꢀꢀꢀ
42.1份;
[0070]
稀释剂
ꢀꢀꢀꢀꢀꢀꢀꢀꢀꢀꢀꢀꢀꢀꢀꢀꢀꢀꢀꢀꢀꢀꢀꢀꢀꢀꢀꢀꢀꢀꢀꢀꢀ
57.9份;
[0071]
所述润滑耐磨填料由聚四氟乙烯9.3质量份、碳化硅14.8质量份、二硫化钼8.6份组成;所述有机溶剂为乙酸丁酯;所述稀释剂由乙酸丁酯、二甲苯、环己酮按3:1:1的质量比组成;
[0072]
所述减摩耐磨防腐涂料的制备方法,包括如下步骤:
[0073]
1)将部分有机溶剂加入feve型氟碳树脂中,在400rpm速率下搅拌10分钟,得到均匀、质量分数为50%的透明溶液,
[0074]
2)在步骤1)得到的透明溶液中加入润湿分散剂,在400rpm速率下搅拌5分钟,得到混合溶液;
[0075]
3)在步骤2)得到的混合溶液中加入润滑耐磨填料并补足有机溶剂,在470rpm速率下搅拌5分钟,之后球磨分散3h,得到浆料;
[0076]
4)将步骤3)得到的浆料用400目筛网过滤,得到a组分;
[0077]
5)按b组分配方量取固化剂与稀释剂,并将两者混合后,在400rpm速率下搅拌10分钟,得到b组分;
[0078]
6)将a、b组分按质量比为7:1混合,在350rpm速率下搅拌10分钟,之后用400目筛网过滤即可使用。
[0079]
实施例4
[0080]
一种减摩耐磨防腐涂料由a组合和b组分按如下配方制成:
[0081]
a组分按质量份计配方为:
[0082][0083][0084]
b组分按质量份计配方为:
[0085]
固化剂(desmodur 3390)
ꢀꢀꢀꢀꢀꢀꢀꢀꢀꢀꢀꢀꢀꢀꢀꢀꢀꢀꢀꢀ
28.9份;
[0086]
稀释剂
ꢀꢀꢀꢀꢀꢀꢀꢀꢀꢀꢀꢀꢀꢀꢀꢀꢀꢀꢀꢀꢀꢀꢀꢀꢀꢀꢀꢀꢀꢀꢀꢀꢀꢀꢀ
71.1份;
[0087]
所述润滑耐磨填料由聚四氟乙烯6.7质量份、碳化硅6.4质量份、二硫化钼4.3份组成;所述有机溶剂为二甲苯;所述稀释剂由乙酸丁酯、二甲苯按6:4的质量比组成;
[0088]
所述减摩耐磨防腐涂料的制备方法,包括如下步骤:
[0089]
1)将部分有机溶剂加入feve型氟碳树脂中,在400rpm速率下搅拌10分钟,得到均匀、质量分数为50%的透明溶液,
[0090]
2)在步骤1)得到的透明溶液中加入润湿分散剂,在400rpm速率下搅拌5分钟,得到混合溶液;
[0091]
3)在步骤2)得到的混合溶液中加入润滑耐磨填料并补足有机溶剂,在470rpm速率下搅拌5分钟,之后球磨分散3h,得到浆料;
[0092]
4)将步骤3)得到的浆料用400目筛网过滤,得到a组分;
[0093]
5)按b组分配方量取固化剂与稀释剂,并将两者混合后,在400rpm速率下搅拌10分钟,得到b组分;
[0094]
6)将a、b组分按质量比为6:1混合,在350rpm速率下搅拌10分钟,之后用325目筛网过滤即可使用。
[0095]
各实施例所得减摩耐磨防腐涂料的测试结果如表1所示;
[0096]
表1
[0097]
[0098][0099]
应用实例
[0100]
将实施例1-4的涂料采用如下方法制成在不同底材上制成涂层,方法具体包括以下步骤:
[0101]
1)底材表面处理:底材表面无可溶性盐、油脂、锈蚀、污物、旧涂层等杂质,表面清洁度经喷射清理至少达到gb/t 8923规定的sa2.5,或经手工、动力工具清理达到gb/t 8923规定的st3,底材表面残存灰尘数量和大小不得超过gb/t 18570.3规定的等级2,底材的表面粗糙度与gb/t 13288.1中规定的中(g)或细(g)一致;
[0102]
2)涂料混配:减摩耐磨防腐涂料现配现用,4h内涂装有效;
[0103]
3)涂料喷涂:常温空气喷涂制备涂层,采用与试样平行、垂直交替的方式喷涂,喷枪压力0.3mpa,枪嘴与工件之间垂直距离20cm;涂层厚度由喷涂次数控制,每次喷涂厚度为10μm,重复喷涂5次,涂层总厚度为50μm;
[0104]
4)涂层固化:保持环境清洁无尘;涂层固化在大气中进行,涂层表干时间1h以内,实干时间24h,完全固化3天;
[0105]
涂料及底材对应表和结果表(每组做六个试样)如下:
[0106]
表2
[0107]