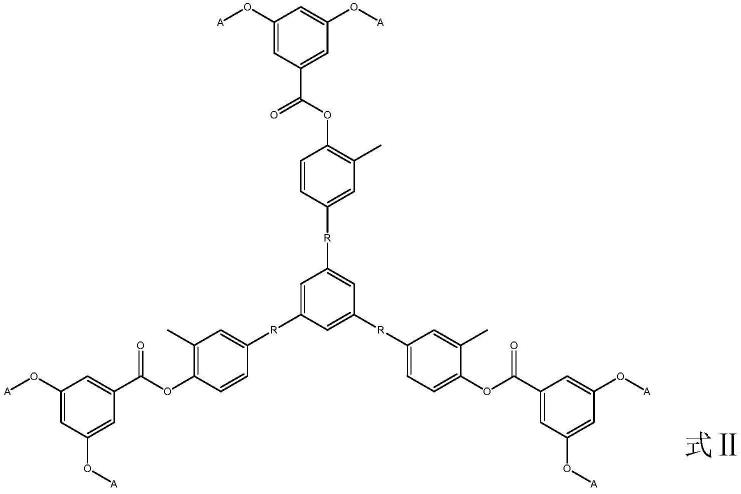
1.本发明属于液晶涂料技术领域,涉及一种高附着力液晶组合物及使用方法和应用。
背景技术:2.胆甾相液晶具有周期性螺旋结构。不同螺距长度可选择性反射对应波长的光,从而可应用于防蓝光、防紫外线、隔热等领域。一般通过向列相液晶与手性剂复配来制备胆甾相液晶。含有丙烯酸酯官能团的向列相液晶单体可经紫外光照射固化成膜,因此可制成uv固化液晶涂层液,涂布在各种基材上,从而制成防蓝光膜、防紫外线膜、隔热膜等。紫外光固化涂料具有固化速度快,生产效率高的特点。但其固化收缩率高以及快速固化产生的内应力致使固化后的涂层与基材附着力较差,易与基材剥离。目前关于改善液晶涂料附着力的文献资料较少。大多针对基材改性和基材表面处理,例如塑料薄膜表面电晕处理。专利201480049768.6(申请号)采用了一种附着力促进剂,该附着力促进剂为侧链包含一个或多个伯氨基的(甲基)丙烯酸类侧链聚合物。但该促进剂添加量少,对固化收缩率降低有限,因此对基材的附着力提升有限。不能满足高附着力应用场景。
3.同时常用的丙烯酸酯类可聚合液晶在室温下粘度高,需要大量有机溶剂溶解稀释才能应用涂布。对环境造成了严重的污染。
技术实现要素:4.针对上述液晶涂料存在的问题,本发明解决了现有可聚合液晶涂料在各种塑料薄膜表面的附着力差的问题。同时本发明组合物在涂布时可少使用甚至不使用有机溶剂,减少了环境污染。
5.本发明的技术方案如下:
6.一种液晶组合物,以重量份计,所述液晶组合物包含50-90%的棒状可聚合液晶单体、10-30%的星型可聚合液晶单体、0-10%的手性剂和0-10%的光引发剂。
7.优选地,以重量份计,所述液晶组合物包含50-90%的棒状可聚合液晶单体、10-30%的星型可聚合液晶单体、1-10%的手性剂和1-10%的光引发剂。
8.优选地,所述棒状可聚合液晶单体选自如下结构:
[0009][0010]
其中,m1、m2、m3、m4各自独立地选自酯基、偶氮基或席夫碱基,n1、n2为1~10的整数。
[0011]
优选地,m1、m2、m3、m4各自独立地选自如下结构的一种:
[0012][0013]
优选地,所述星型可聚合液晶单体选自如下结构:
[0014][0015]
r为n3为1~10中的任意整数;
[0016]
a为h和/或脂肪族丙烯酸酯基,其中式ⅱ中每个苯氧基所连的两个a中,至少有一个为脂肪族丙烯酸酯基。
[0017]
优选地,所述脂肪族丙烯酸酯基为
[0018][0019]
其中,n4为1~10中的任意整数。
[0020]
优选地,所述手性剂为右旋手性剂r811,r5011,r1011,r6n或左旋手性剂s811,s5011,s1011,s6n其中的一种或几种复配使用,其中,左旋手性剂与右旋手性剂不能复配使用。
[0021]
优选地,所述光引发剂为光引发剂184,光引发剂tpo,光引发剂1173,光引发剂651中的一种或两种以上复配使用。
[0022]
所述的液晶组合物的应用,包括如下步骤:
[0023]
(1)将液晶组合物熔融充分混合后冷却,添加0~50%质量分数的有机溶剂制成液晶涂料;
[0024]
(2)将其涂布在塑料薄膜基材表面后经过紫外光照射即可固化成膜。
[0025]
优选地,可根据目标涂层厚度及施工所需体系粘度添加一定量的甲苯、二甲苯、乙
酸乙酯、乙酸丁酯、环己酮等有机溶剂。所述塑料薄膜基材为pet,pc,pa,pp中的一种或两种以上。
[0026]
本发明采用星型可聚合液晶单体,降低涂层固化后的收缩率,从而提高涂层的附着力。无需添加任何促进剂。星型可聚合液晶单体的加入降低固化收缩率的同时不会降低交联密度,从而不会降低涂层表面硬度和抗划伤性。同时制备的液晶涂层透明度高。星型液晶单体的加入可降低混晶的粘度。将本发明的液晶组合物加热熔融,搅拌充分混合均匀后降温即得液晶涂料,可视情况加入少量有机溶剂甚至不加有机溶剂。减少了有机溶剂的使用,更加环保。可应用于防蓝光、防紫外线、隔热等领域。
[0027]
与现有技术相比,本发明具有如下有益效果:
[0028]
(1)本发明的液晶组合物无需添加任何促进剂就能获得高附着力。且制备的涂层透明度高。
[0029]
(2)同时由于星型液晶单体的加入使组合物熔融混合后形成的混晶粘度更低,因此可少使用甚至不使用有机溶剂便可应用涂布。
具体实施方式
[0030]
下面结合具体实施例对本发明作进一步具体详细描述,但本发明的实施方式不限于此,对于未特别注明的工艺参数,可参照常规技术进行。
[0031]
将本发明的液晶组合物加热熔融,搅拌充分混合均匀后降温,视情况加入一定量的有机溶剂或不加入有机溶剂,将此液晶涂料涂布在pet,pc,pa等薄膜上,经高压汞灯或者uvled灯固化成膜。
[0032]
实施例1
[0033]
一种液晶组合物,配方详见表1。
[0034]
表1
[0035][0036]
将表1中的组合物加热到150℃,充分搅拌混合均匀后降温,即得液晶涂料。
[0037]
实施例2
[0038]
一种液晶组合物,配方详见表2。
[0039]
表2
[0040][0041][0042]
将表2中的组合物加热到150℃,充分搅拌混合均匀后降温即得液晶涂料。
[0043]
实施例3
[0044]
一种液晶组合物,配方详见表3。
[0045]
表3
[0046]
[0047]
将表3中的组合物加热到150℃,充分搅拌混合均匀后降温,即得液晶涂料。
[0048]
实施例4
[0049]
表4
[0050][0051][0052]
将表4中的组合物加热到150℃,充分搅拌混合均匀后降温,即得液晶涂料。
[0053]
实施例5
[0054]
表5
[0055][0056]
将表5中的组合物加热到150℃,充分搅拌混合均匀后降温,即得液晶涂料。
[0057]
实施例6
[0058]
表6
[0059][0060]
将表6中的组合物加热到150℃,充分搅拌混合均匀后降温即得液晶涂料。
[0061]
实施例7
[0062]
表7
[0063][0064]
将表7中的组合物加热到150℃,充分搅拌混合均匀后降温,即得液晶涂料。
[0065]
实施例8
[0066]
表8
[0067][0068]
将表8中的组合物加热到150℃,充分搅拌混合均匀后降温即得液晶涂料。
[0069]
实施例9
[0070]
表9
[0071][0072][0073]
将表9中的组合物加热到150℃,充分搅拌混合均匀后降温,即得液晶涂料。
[0074]
实施例10
[0075]
表10
[0076][0077]
将表10中的组合物加热到150℃,充分搅拌混合均匀后降温,即得液晶涂料。
[0078]
对比例1
[0079]
表11
[0080][0081]
将表11中的组合物加热到150℃,充分搅拌混合均匀后降温,即得液晶涂料。
[0082]
对比例2
[0083]
表12
[0084][0085]
将表12中的组合物加热到150℃,充分搅拌混合均匀后降温,即得液晶涂料。
[0086]
对比例3
[0087]
表13
[0088][0089]
将表13中的组合物加热到150℃,充分搅拌混合均匀后降温,即得液晶涂料。
[0090]
实验效果
[0091]
表14
[0092][0093][0094]
附着力测试方法:gb/t9286-2021。
[0095]
粘度的测试方法:gb/t2794-2013。
[0096]
涂层透光率的测试方法:透光率雾度仪sgw-810,可见光波段。
[0097]
涂层表面铅笔硬度测试方法:gb/t6739-2006。
[0098]
上述实施例为本发明较佳的实施方式,但本发明的实施方式并不受上述实施例的限制,其他的任何未背离本发明的精神实质与原理下所作的改变、修饰、替代、组合、简化,均应为等效的置换方式,都包含在本发明的保护范围之内。