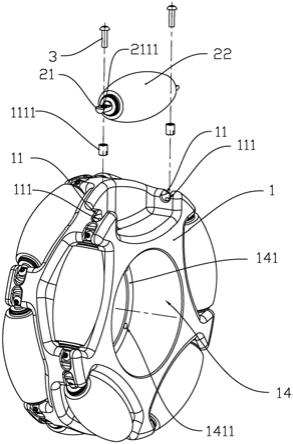
1.本实用新型涉及全向轮技术领域,特别是一种具有一体式轮毂的全向轮。
背景技术:2.全向轮是一种可以用于搭建全方位移动平台的轮子。全向轮的特点是在一个大的轮毂的圆周上,均匀排布若干与大轮毂轴线成一定角度的小辊子。通常每个全向轮带一个电机作为动力,而轮毂上均布的那些小辊子则不带动力,并可绕辊子自身轴线自由旋转。这种特殊的结构,使得每个全向轮同时具有如下3个自由度,即:绕大轮毂轴线的转动,绕辊子与地面接触点的转动,以及沿辊子轴线垂线方向的平移。
3.目前市场上的全向轮,其轮毂与辊子的角度通常分为90
°
和45
°
两种。当三个及三个以上的90
°
的全向轮,或四个及四个以上的45
°
的全向轮,按照一定规则排布,组成一个全向移动平台时,通过控制各全向轮各自的转速和转向的不同排列组合,即可实现设备在不转自身方向的情况下直接向任意方向的运动。相比用普通轮系构建的平台,全向移动平台具有更高的运动灵活性,能适应在更狭小的空间中运动。
4.而现有的90
°
全向轮和45
°
全向轮的轮毂,其绝大多数为分体式构造,90
°
全向轮通常分为左中右3段,左右两个法兰通过中间轮毂套连接;而45
°
全向轮通常分为左右2片,左右2片再通过螺钉连接成型。这样组合出来的全向轮,其材料利用率低,轮毂整体强度低,重量大,加工量大,组合后存在装配误差,导致全向轮的整体精度不高,安装拆卸的维护成本高,不利于工业化大批量生产。
5.为了解决上述技术问题,申请号为cn201420248828.4,名称为一种两侧轮毂一体成型的45
°
全向轮和申请号为cn201220566389.2,名称为一种90
°
全向轮的中国专利,分别公开了一种一体式轮毂的全向轮,上述两个技术方案虽然部分解决了分体式轮毂引起的缺陷,但是其辊子与轮毂的连接依然比较复杂,不仅安装和拆卸辊子时,需从轮毂凸缘两侧分别拆散辊子各部,而不能将辊子组件单独成套拆卸,给拆装和维修带来了极大的不便和困难,而且,其轮毂两侧作为辊子支撑的凸台相互孤立突出,削弱了轮毂的整体强度和刚性,并妨害全向轮承载能力的进一步提高。
技术实现要素:6.为了克服现有技术的不足,本实用新型提供了一种轮毂为一体成型结构,减少部件,减少安装步骤,方便辊子安装和拆卸,并提高轮毂的整体强度和刚性,消除组合误差,提高整体精度的全向轮。
7.为了实现上述目的,本实用新型采用的技术方案是:一种具有一体式轮毂的全向轮,包括一体式的轮毂以及分布在轮毂周侧的若干辊子,所述辊子包括辊子轴以及套设在辊子轴上的滚轮,所述辊子轴两端的轴伸裸露在外,所述轮毂上设置有供辊子轴的轴伸嵌入的具有敞开口的u形安装槽,所述辊子轴的轴伸嵌入u形安装槽后通过连接件固定在u形安装槽内。
8.上述技术方案中,u形安装槽为沿轮毂上辊子安装轴线开设的敞开口的u形凹腔,辊子轴的两端轴伸可直接嵌入u形安装槽,然后通过连接件固定在轮毂上,这样辊子可独立安装和拆卸,方便维修和更换。因为辊子承载工作负荷时,其所承受的径向力指向辊子轴伸底下的u形槽底,因此这样在轮毂两侧开设u形安装槽,其实并不影响辊子承载工作负荷时的受力和定位。而且由于轮毂是整体成型,零部件少,特别是当其采用铸造成型时,其切削加工量可降到最低。另外,轮毂两侧作为支撑辊子的凸缘不再孤立单薄地凸出,因而辊子支撑部位的结构强度和刚性得到加强,辊子轴线的位置精度和轮毂的承载能力得到进一步提高,使轮毂便于制造和装配,便于工业化批量生产,大大提高了轮毂的整体强度和刚性,也由于轮毂为单一零件,不存在组合误差,容易实现更高的整体精度,提高全向轮的品质。
9.作为本实用新型的进一步设置,所述u形安装槽的槽底设置有连接孔,所述辊子轴的轴伸上设置有供连接件穿过的径向孔,所述连接件穿过轴伸的径向孔后与连接孔连接实现将辊子固定在轮毂上。
10.上述技术方案中,连接孔可以是螺纹孔也可以是内壁光滑的孔,当内壁是光滑的孔时,可在内壁上设置l形卡槽,也可以内嵌自攻螺套,只需实现可拆卸连接即可,不做限制。
11.作为本实用新型的进一步设置,所述连接件为螺钉,所述连接孔内嵌套有自攻螺套,所述螺钉穿过辊子轴的轴伸后与自攻螺套螺纹连接。
12.上述技术方案中,轮毂采用高强度铝合金低压铸造成型,自攻螺套为不锈钢材料制成,若连接孔内壁直接设置螺纹,拆装次数多了以后,螺钉与连接孔的螺纹连接容易滑丝或损坏,尤其是对铝制的轮毂,一旦出现某一个螺纹连接失效或损坏,就会导致整个轮毂都需要更换,使轮毂工作寿命缩短,使用成本变高。设置了自攻螺套后,自攻螺套内壁上的螺纹如果滑丝或损坏,只需简单更换自攻螺套即可,而不至于因为一个或几个螺孔的滑丝导致整个轮毂失效而失去使用价值,于是就节约了成本,并可延长轮毂的使用寿命,减少废弃物的产生。
13.作为本实用新型的进一步设置,所述辊子的轴线与轮毂的轴线成90
°
夹角,所述辊子沿轮毂的周向间隔分布围成一圈后分别位于轮毂的两侧,所述轮毂单侧的辊子数量大于或等于3个,轮毂两侧的辊子数量相同且交错分布。
14.上述技术方案中,最关键之处,在于从轮毂轴向看起来,两侧辊子母线的包络面为圆柱面,所以该全向轮能够连续地向前滚动。
15.作为本实用新型的进一步设置,所述轮毂圆周的左右两侧分别设置有沿其周向间隔分布的腰鼓形凹腔,左右两侧的腰鼓形凹腔交错分布,所述u形安装槽位于腰鼓形凹腔的对应两端,任意一个腰鼓形凹腔对应安装一个辊子。
16.上述技术方案中,大大提高了全向轮的整体强度,加工量小,材料利用率高,便于工业化批量生产,结构简单,整体精度容易控制,能够实现全向轮长期稳定运行。
17.作为本实用新型的进一步设置,所述辊子的轴线与轮毂的轴线成45
°
夹角,所述轮毂上的辊子数量大于或等于8个。
18.上述技术方案中,辊子的母线很特殊,使得从轮毂轴向看起来,所有辊子母线的包络面为圆柱面,所以该全向轮能够连续地向前滚动。
19.作为本实用新型的进一步设置,所述轮毂的左右两侧轮缘上设置有支撑环,两所
述支撑环相对设置,两所述支撑环与轮毂为一体成型结构,所述u形安装槽间隔分布在支撑环上,两侧相对的两个u形安装槽为一组,每组u形安装槽的轴线与轮毂轴线成45度左旋或右旋夹角,所述辊子位于每组的两个u形安装槽之间。
20.上述技术方案中,两支撑环间隔设置,二者之间的空隙可容置若干辊子,两支撑环与轮毂为一体成型结构,大大提高了轮毂的整体强度和刚性,由于轮毂为单一零件,不存在组合误差,容易实现更高的整体精度,提高全向轮品质,零部件少,便于制造和装配,便于工业化批量生产。
21.作为本实用新型的进一步设置,所述轮毂上连接有轮毂减速器,所述轮毂上设置有与轮毂减速器的外圆配合面连接的安装孔、安装端面和螺孔。
22.上述技术方案中,由于轮毂为单一零件,不存在组合误差,容易实现更高的整体精度和更高的承载能力,提高全向轮品质,零部件少,便于制造和装配,便于工业化批量生产。
23.下面结合附图对本实用新型作进一步描述。
附图说明
24.附图1为本实用新型具体实施例1的结构立体图;
25.附图2为本实用新型具体实施例1的结构爆炸图;
26.附图3为本实用新型具体实施例1的辊子结构爆炸剖视图;
27.附图4为本实用新型具体实施例1的轮毂结构立体图;
28.附图5为本实用新型具体实施例2的结构立体图;
29.附图6为本实用新型具体实施例2的轮毂结构立体图;
30.附图7为本实用新型具体实施例2的结构爆炸图。
31.附图8为本实用新型具体实施例2的辊子结构爆炸剖视图。
具体实施方式
32.本实用新型的具体实施例如图1
‑
8所示,一种具有一体式轮毂的全向轮,包括一体式的轮毂1以及分布在轮毂1周侧的若干辊子2,所述辊子2包括辊子轴21以及套设在辊子轴21上的滚轮22,所述辊子轴21两端的轴伸211裸露在外,所述轮毂1上设置有供辊子轴21的轴伸211嵌入的具有敞开口的u形安装槽11,所述辊子轴21的轴伸211嵌入u形安装槽11后通过连接件3固定在u形安装槽11内。u形安装槽11为沿轮毂1上辊子2安装轴线开设的敞开口的u形凹腔,辊子轴21的两端轴伸211可直接嵌入u形安装槽11,然后通过连接件3固定在轮毂1上,这样辊子2可独立安装和拆卸,方便维修和更换,由于轮毂1是整体成型,零部件少,而且作为支撑辊子2的凸缘不再孤立单薄地凸出,因而辊子2支撑部位的结构强度和刚性得到加强,辊子轴21线的位置精度和轮毂1的承载能力得到进一步提高,使轮毂1便于制造和装配,便于工业化批量生产,大大提高了轮毂1的整体强度和刚性,也由于轮毂1为单一零件,不存在组合误差,容易实现更高的整体精度,提高全向轮的品质。轮毂通常为低压铸造结构。但必要时如打样或极小批量试制时也可用整块材料整体加工出来。
33.上述u形安装槽11的槽底设置有连接孔111,所述辊子轴21的轴伸211上设置有供连接件3穿过的径向孔2111,所述连接件3穿过轴伸211的径向孔2111后与连接孔111连接实现将辊子2固定在轮毂1上。连接孔111可以是螺纹孔也可以是内壁光滑的孔,当是内壁光滑
的孔时,可在内壁上设置l形卡槽,也可以内嵌自攻螺套,只需实现可拆卸连接即可,不做限制。
34.上述连接件3为螺钉3,所述连接孔111内嵌套有自攻螺套1111,所述螺钉3穿过辊子轴21的轴伸211后与自攻螺套1111螺纹连接。
35.若连接孔111内壁直接设置螺纹,拆装次数多了以后,螺钉3与连接孔111的螺纹连接容易滑丝或损坏,尤其是对铝制的轮毂1,一旦出现某一个螺纹连接失效或损坏,就会导致整个轮毂1都需要更换,使轮毂1工作寿命缩短,使用成本变高。设置了自攻螺套1111后,自攻螺套1111内壁上的螺纹如果滑丝或损坏,只需更换自攻螺套1111即可,而不至于因为一个或几个螺孔的滑丝导致整个轮毂1失去使用价值,于是就节约了成本,并可延长轮毂1的使用寿命,减少废弃物的产生。
36.上述辊子2的轴线与轮毂1的轴线成90度夹角,所述辊子2沿轮毂1的周向间隔分布围成一圈后分别位于轮毂1的两侧,所述轮毂1单侧的辊子2数量大于或等于3个,轮毂1两侧的辊子2数量相同且交错分布。两侧辊子2母线的包络面为圆柱面,所以该全向轮能够连续地向前滚动。其中螺纹孔常用于钢铁轮毂,而光孔主要用于铝合金等有色金属或工程塑料轮毂。
37.上述轮毂1圆周的左右两侧分别设置有沿其周向间隔分布的腰鼓形凹腔12,左右两侧的腰鼓形凹腔12交错分布,所述u形安装槽11位于腰鼓形凹腔12的对应两端,任意一个腰鼓形凹腔12对应安装一个辊子2。大大提高了全向轮的整体强度,加工量小,材料利用率高,便于工业化批量生产,结构简单,整体精度容易控制,能够实现全向轮长期稳定运行。
38.上述辊子2的轴线与轮毂1的轴线成45度夹角,所述轮毂1上的辊子2数量大于或等于8个。辊子2的母线很特殊,使得从轮毂1轴向看起来,所有辊子2母线的包络面为圆柱面,所以该全向轮能够连续地向前滚动。
39.上述轮毂1的左右两侧轮缘上设置有支撑环13,两所述支撑环13相对设置,两所述支撑环13与轮毂1为一体成型结构,所述u形安装槽11间隔分布在支撑环13上,两侧相对的两个u形安装槽11为一组,每组u形安装槽11的轴线与轮毂1轴线成45度左旋或右旋夹角,所述辊子2位于每组的两个u形安装槽11之间。两支撑环13间隔设置,二者之间的空隙131可容置若干辊子2,两支撑环13与轮毂1为一体成型结构,大大提高了轮毂1的整体强度和刚性,由于轮毂1为单一零件,不存在组合误差,容易实现更高的整体精度,提高全向轮品质,零部件少,便于制造和装配,便于工业化批量生产。
40.上述轮毂1上连接有轮毂减速器,所述轮毂1上设置有与轮毂减速器的外圆配合面连接的安装孔14、安装端面141和螺孔1411。由于轮毂1为单一零件,不存在组合误差,容易实现更高的整体精度和更高的承载能力,提高全向轮品质,零部件少,便于制造和装配,便于工业化批量生产。
41.在本实用新型的描述中,需要说明的是,术语“中心”、“纵向”、“横向”、“上”、“下”、“前”、“后”、“左”、“右”、“竖直”、“水平”、“顶”、“底”“内”、“外”、“顺时针”、“逆时针”等指示的方位或位置关系为基于附图所示的方位或位置关系,仅是为了便于描述本发明和简化描述,而不是指示或暗示所指的装置或元件必须具有特定的方位、以特定的方位构造和操作,因此不能理解为对本发明的限制。此外,术语“第一”、“第二”仅用于描述目的,而不能理解为指示或暗示相对重要性。
42.在本实用新型的描述中,需要说明的是,除非另有明确的规定和限定,术语“安装”、“相连”、“连接”应做广义理解,例如,可以是固定连接,也可以是可拆卸连接,或一体地连接;可以是机械连接,也可以是电连接;可以是直接相连,也可以通过中间媒介间接相连,可以是两个元件内部的连通。对于本领域的普通技术人员而言,可以具体情况理解上述术语在本发明中的具体含义。此外,在本发明的描述中,除非另有说明,“多个”的含义是两个或两个以上。
43.本实用新型不局限于上述具体实施方式,本领域一般技术人员根据本实用新型公开的内容,可以采用其他多种具体实施方式实施本实用新型的,或者凡是采用本实用新型的设计结构和思路,做简单变化或更改的,都落入本实用新型的保护范围。