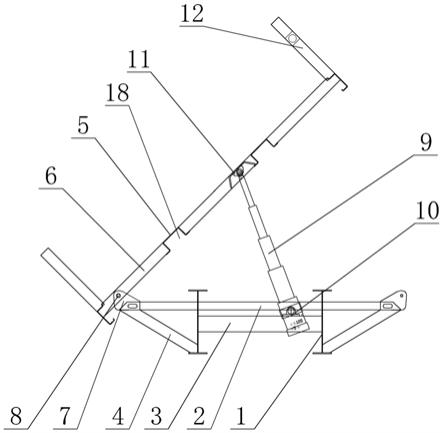
1.本实用新型涉及一种车架及侧翻自卸车,更具体的说,尤其涉及一种的副架下沉式车架及其构成的侧翻自卸车。
背景技术:2.侧翻式自卸是常见的自卸车类型之一,其具有结构相对简洁、使用方便的优点,由于侧翻式自卸在货物自动卸载时,需要利用油缸将车辆副架顶起,使副架连同车厢向一侧翻转,依靠货物的滑落实现货物的自动卸载。
3.现有侧翻式自卸车的副架均是平方在主架工字钢上,这就使得副架的高度相对较高,高度较高的副架在翻转卸货的过程中,容易导致整个车架的重心升高,如果此时车辆处于相对不平整的地面上,容易出现卸货过程中出现翻车,不仅影响使用人员的人身安全,而且也会导致车辆受损。因此,如果能对现有侧翻式车架加以改进,将副架的高度降低,有利于保证卸货过程中的安全性。
技术实现要素:4.本实用新型为了克服上述技术问题的缺点,提供了一种副架下沉式车架及其构成的侧翻自卸车。
5.本实用新型的副架下沉式车架,包括主车架、副车架和驱使副车架翻转的油缸,主车架由两平行设置的主架大梁构成,两主架大梁之间经大梁横称相连接,副车架由两平行设置的副架纵梁组成,两副架纵梁经间隔分布的副架横称相连接;主车架一侧的上端间隔固定有多个翻转连接板,副车架经翻转销铰接于翻转连接板上;其特征在于:所述两副架纵梁上均设置有开口朝下的纵梁凹槽,两主架大梁的上端突出于大梁横称,当副车架落在主车架上时:两主架大梁的上端卡入两纵梁凹槽中。
6.本实用新型的副架下沉式车架,所述两主架大梁经多个间隔分布的顶称相连接,顶称上固定有下顶座,顶称上方的副架横称上固定有上顶座,所述油缸的缸体铰接于下顶座上,油缸的活塞杆铰接于上顶座上。
7.本实用新型的副架下沉式车架,所述副车架的两侧设置有副架边梁,副架边梁经副架横称与副架纵梁相连接。
8.本实用新型的副架下沉式车架,所述主架大梁为工字钢,所述副架纵梁为“几字形”折弯件,当副车架落在主车架上时:“几字形”折弯件的凹槽与副架纵梁的上端相配合。
9.本实用新型的副架下沉式车架构成的侧翻自卸车,所述副车架的两侧间隔设置有立柱和侧门,副架的后端设置有后门板、前端设置有前挡板,所述主车架的下方设置有悬架,悬架上设置有车轮。
10.本实用新型的有益效果是:本实用新型的副架下沉式车架及其构成的侧翻自卸车,通过将主车架上的两主架大梁设置为顶端突出于大梁横称的形式,并在副车架的两副架纵梁上设置朝下的两纵梁凹槽,这样,当副车架落到主车架上时,两主架大梁的上端卡入
两纵梁凹槽中,与现有侧翻自卸车架相比,降低了副车架的高度;当油缸驱使副车架翻转进行卸货的过程中,由于副车架的重心降低,有效避免了由于副车架重心过高所导致的翻车事故的发生,同时,由于副车架的重心降低,也增加了货物运输过程中车辆的稳定性。
附图说明
11.图1为本实用新型的副架下沉式车架的结构示意图;
12.图2为本实用新型的副架下沉式车架的翻转示意图;
13.图3为本实用新型中副车架的结构示意图;
14.图4为本实用新型中副架纵梁的横截面示意图;
15.图5为本实用新型的副架下沉式车架构成的侧翻自卸车的主视图;
16.图6为本实用新型中侧翻自卸车的左视图;
17.图7为本实用新型中侧翻自卸车的后视图。
18.图中:1主架大梁,2大梁横称,3顶称,4斜撑,5副架纵梁,6副架横称,7翻转连接板,8翻转销,9油缸,10下顶座,11上顶座,12侧门板,13立柱,14后门板,15前挡板,16悬架,17车轮,18纵梁凹槽,19副架边梁。
具体实施方式
19.下面结合附图与实施例对本实用新型作进一步说明。
20.如图1和图2所示,分别给出了本实用新型的副架下沉式车架的结构示意图和翻转示意图,图3给出了本实用新型中副车架的结构示意图,所示的副架下沉式车架由主车架、副车架和油缸9组成,主车架由两主架大梁1以及若干大梁横称2组成,两主架大梁1平行设置,两主架大梁1经间隔分布的大梁横称2固定连接,两主架大梁1之间还经多根间隔设置的顶称3相连接,顶称3还用于实现对油缸9的支撑。
21.所示的副车架由两副架纵梁5、两副架边梁9和若干副架横称6组成,两副架纵梁5平行设置,两副架纵梁5之间的距离与两主架大梁1之间的距离相等。两副架纵梁5之间经间隔分布的副架横称6相连接,两副架边梁9位于两副架纵梁5的两侧,相邻的副架边梁9与副架纵梁5之间也经间隔分布的副架横称6固定连接。
22.所示主架大梁1的外侧面上固定有向外延伸的大梁横称2,向外延伸的大梁横称2上固定有翻转连接板7,副车架经翻转销8与翻转连接板7相铰接,这样就实现了副车架与主车架可绕由翻转连接板7和翻转销8构成的铰接结构进行翻转。所示顶称3上固定有下顶座10,顶称3上方的副架横称6上固定有上顶座11,油缸9底部的缸体铰接于下顶座10上,油缸9的伸缩杆的上端铰接于上底座11上,这样,当油缸9的伸缩杆伸长时,即可驱使副车架绕与主车架的铰接处进行翻转,油缸9伸缩杆回缩时,副车架降落。
23.所示副架纵梁5上设置有开口朝下的纵梁凹槽18,主架大梁1的上端突出于副架横称6,纵梁凹槽18的宽度大于主架大梁1上端的宽度,当副车架落至主车架上时,主车架的主架大梁1上端卡至纵梁凹槽18中,这样,与现有车翻式车架相比,相当于降低了副车架的高度,当油缸9驱使副车架进行翻转时,由于副车架的高度降低,可避免由于副车架重心过高所导致的翻折现象的发生,可见,本实用新型的副架下沉式车架在卸货过程中更加安全。同时,由于副车架的重心降低,也增加了货物运输过程中车辆的稳定性。
24.所示主架大梁1可采用常规通用的工字钢,如图4所示,给出了本实用新型中副架纵梁的横截面示意图,所示的副架纵梁5可采用“几字形”折弯件,当副车架落至主车架上时,工字钢的上端落入“几字形”折弯件的空腔中。
25.如图5、图6和图7所示,分别给出了实用新型的副架下沉式车架构成的侧翻自卸车的主视图、左视图和右视图,所示的车架采用图1中所示的形式,所示副车架的两侧间隔设置有立柱13和侧门12,副架的后端设置有后门板14、前端设置有前挡板15,所述主车架的下方设置有悬架16,悬架上设置有车轮17,所构成的侧翻自卸车可实现货物的装载、运输和自动卸货,使用起来更加安全。
技术特征:1.一种副架下沉式车架,包括主车架、副车架和驱使副车架翻转的油缸(9),主车架由两平行设置的主架大梁(1)构成,两主架大梁之间经大梁横称(2)相连接,副车架由两平行设置的副架纵梁(5)组成,两副架纵梁经间隔分布的副架横称(6)相连接;主车架一侧的上端间隔固定有多个翻转连接板(7),副车架经翻转销(8)铰接于翻转连接板上;其特征在于:所述两副架纵梁(6)上均设置有开口朝下的纵梁凹槽(18),两主架大梁(1)的上端突出于大梁横称(2),当副车架落在主车架上时:两主架大梁的上端卡入两纵梁凹槽(18)中。2.根据权利要求1所述的副架下沉式车架,其特征在于:所述两主架大梁(1)经多个间隔分布的顶称(3)相连接,顶称上固定有下顶座(10),顶称上方的副架横称(6)上固定有上顶座(11),所述油缸(9)的缸体铰接于下顶座上,油缸的活塞杆铰接于上顶座上。3.根据权利要求1或2所述的副架下沉式车架,其特征在于:所述副车架的两侧设置有副架边梁(19),副架边梁经副架横称(6)与副架纵梁(5)相连接。4.根据权利要求1或2所述的副架下沉式车架,其特征在于:所述主架大梁(1)为工字钢,所述副架纵梁(5)为“几字形”折弯件,当副车架落在主车架上时:“几字形”折弯件的凹槽与副架纵梁的上端相配合。5.一种基于权利要求1所述的副架下沉式车架构成的侧翻自卸车,其特征在于:所述副车架的两侧间隔设置有立柱(13)和侧门(12),副架的后端设置有后门板(14)、前端设置有前挡板(15),所述主车架的下方设置有悬架(16),悬架上设置有车轮(17)。
技术总结本实用新型的副架下沉式车架,包括主车架、副车架和驱使副车架翻转的油缸,主车架由两平行设置的主架大梁构成,副车架由两平行设置的副架纵梁组成,主车架一侧的上端间隔固定有多个翻转连接板,副车架经翻转销铰接于翻转连接板上;特征在于:所述两副架纵梁上均设置有开口朝下的纵梁凹槽,两主架大梁的上端突出于大梁横称,当副车架落在主车架上时:两主架大梁的上端卡入两纵梁凹槽中。本实用新型的副架下沉式车架及其构成的侧翻自卸车,当副车架落到主车架上时,两主架大梁的上端卡入两纵梁凹槽中,与现有侧翻自卸车架相比,降低了副车架的高度,有效避免了由于副车架重心过高所导致的翻车事故的发生。致的翻车事故的发生。致的翻车事故的发生。
技术研发人员:李超 李兆波 张保成
受保护的技术使用者:山东畅达专用车有限公司
技术研发日:2021.06.30
技术公布日:2022/1/21