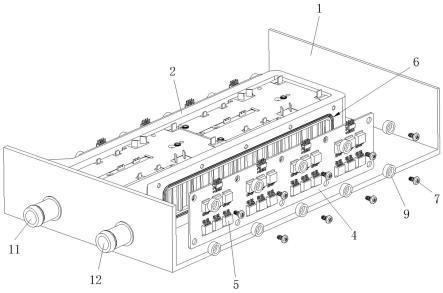
1.本实用新型涉及电力电子技术领域,具体涉及一种复用金属基电路板的冷却流道结构及车载充电机。
背景技术:2.随着电子技术的发展,电子设备得到了日益广泛的应用,同时电子设备的功率密度持续提升,发热功率也随之增大。因此,散热问题已经成为制约电子技术进一步发展的主要瓶颈。大量实践表明:温度是造成电子设备失效的主因之一,并且随着温度的增加,器件失效的概率呈指数增长。电子设备需要长时间在接近满负荷的情况下工作,在有限的条件下,解决这类电子设备的散热问题面临着极大的挑战。在诸如电动汽车等应用领域,比如电机控制器、车载充电机、充电模块的环境温度很高,由于这些零部件中内部包括了igbt、mos管、电容等功能元件,对温度非常敏感,尤其在高温环境下,轻则会影响零部件的性能发挥,重则将产生爆炸等事故。
3.目前,车载充电机功率传输系统中用到的大功率转换器件大部分为插件类型,功率器件直接贴合在金属基电路板(铝基板或者铜基板)上,然后金属基电路板固定在平面(与水平面平行)冷却流道上。采用传统平面化冷却流道对功率器件进行散热,金属基电路板、冷却流道、冷却流道盖板均与水平面平行设置,导致冷却流道散热结构的平面及空间利用率低,同时传统的金属基电路板上众多的功率转接接口占据金属基电路板上大量的面积,金属基电路板用于散热的有效面积及利用率低。
4.图1示出了现有金属基电路板与冷却流道贴合的示意图,其组合体包括依次叠置的电子元件5、铜箔层4a、绝缘层4b、金属基板4c、导热硅脂层4d、流道本体2侧壁、冷却流道3。因此,传统的平面化冷却流道的功率器件的散热结构及车载充电机,其结构整体的空间利用率低,不利于功率密度的提高及产品集成小型化的要求。
5.因此,如何设计一种小型化、高密度的散热冷却流道是业界亟待解决的技术问题。
技术实现要素:6.为了解决现有技术中存在的上述缺陷,本实用新型提出一种复用金属基电路板的冷却流道结构及车载充电机。
7.本实用新型采用的技术方案是设计一种复用金属基电路板的冷却流道结构,包括:机壳、设于机壳上的流道本体、设于流道本体内部的冷却流道,所述流道本体的侧壁至少有一面设有镂空窗口,用金属基电路板的散热面封堵镂空窗口,金属基电路板带电子元件的一面背离镂空窗口,金属基电路板的散热面与镂空窗口的边沿之间设有密封装置。
8.所述金属基电路板包括依次叠置的电子元件、铜箔层、绝缘层、金属基板,金属基板的外侧面为所述散热面。
9.所述金属基电路板的散热面上设有多条波纹凹槽,波纹凹槽的方向与冷却流道中水流的方向垂直。
10.所述金属基电路板的边沿上设有通孔,所述镂空窗口的边沿设有螺丝孔,螺钉穿过通孔与螺丝孔螺接,从而将金属基电路板封堵住镂空窗口。
11.所述螺钉穿过绝缘套后在插入通孔,螺钉的螺帽沉入绝缘套凹槽中。
12.所述所述冷却流道的内侧壁上设有湍流发生器。
13.所述冷却流道呈条带状,弯曲成u字形布置,其两端分别设有进水口和出水口,冷却流道的纵截面呈开口的深槽状,冷却流道开口处设有冷却流道盖板。
14.所述金属基电路板设置在u字形冷却流道的外向侧壁上,u字形冷却流道的弯内中部可设置发热元件。
15.所述金属基电路板与镂空窗口之间设有一个绝缘框,所述绝缘框采用窗框结构,其横截面为“l”字形;金属基电路板放置于绝缘框内,金属基电路板的周边为绝缘框侧壁,金属基电路板与镂空窗口之间为绝缘框底壁。
16.所述金属基电路板带电子元件的一面灌注一层灌封胶,灌封胶外表面覆盖一层绝缘板。
17.所述密封装置采用密封胶圈,所述金属基电路板采用铝基电路板。
18.本实用新型还设计了一种车载充电机,包括充电电路和冷却系统,所述冷却系统采用上述的复用金属基电路板的冷却流道结构。
19.本实用新型提供的技术方案的有益效果是:
20.本实用新型复用金属基电路板作为冷却流道的一部分,基板的散热面直接与冷却流道内的冷却液接触进行热传递,有效提升了冷却流道的空间利用率,结合金属基电路板较强的导热性能及紧凑的板面体积,保证了信号传输、整体功率密度的同时提高了对功率器件的散热效率及整体空间利用率,有利于车载充电机和超充液冷模块的整体集成化、小型化和轻量化;功率器件以贴片化取代插件,使得功率器件的一致性更好;通过金属基电路板的顶端面直接设置引脚以实现功率的传输,节省了金属基电路板工作面的面积,做到最大化的利用金属基电路板的有效散热面积。
附图说明
21.下面结合实施例和附图对本实用新型进行详细说明,其中:
22.图1是现有金属基电路板与冷却流道贴合的示意图;
23.图2是本实用新型金属基电路板与冷却流道结合原理示意图;
24.图3是流道本体与金属基电路板分离示意图;
25.图4是流道本体的镂空窗口示意图;
26.图5是金属基电路板正面(带电子元件面)视图;
27.图6是金属基电路板背面(散热面)视图;
28.图7是较佳实施例爆炸分解视图;
29.图8是较佳实施例俯视图;
30.图9是较佳实施例底面视图;
31.图10是使用现有冷却流道结构功率器件内部晶元热仿真数据图;
32.图11是使用现有冷却流道结构功率器件外表热仿真数据图;
33.图12是使用本实用新型冷却流道结构功率器件内部晶元热仿真数据图;
34.图13是使用本实用新型冷却流道结构电机功率器件外表热仿真数据图;
35.图14是金属基电路板与镂空窗口之间设置绝缘框的立体示意图;
36.图15是金属基电路板、灌封胶、绝缘板分解的立体示意图。
具体实施方式
37.为了使本实用新型的目的、技术方案及优点更加清楚明白,以下结合附图及实施例,对本实用新型作进一步详细说明。应当理解,此处所描述的具体实施例仅仅用于解释本实用新型,并不用于限定本实用新型。
38.本实用新型公开了一种复用金属基电路板的冷却流道结构,其包括:机壳1、设于机壳上的流道本体2、设于流道本体内部的冷却流道3,所述流道本体的侧壁至少有一面设有镂空窗口(参看图4示出的流道本体的镂空窗口示意图),用金属基电路板4的散热面封堵镂空窗口(参看图3示出的流道本体与金属基电路板分离示意图),金属基电路板带电子元件5的一面背离镂空窗口,金属基电路板的散热面与镂空窗口的边沿之间设有密封装置。
39.参看图2示出的金属基电路板与冷却流道结合原理示意图,本实用新型中的所述金属基电路板包括依次叠置的电子元件5、铜箔层4a、绝缘层4b、金属基板4c,金属基板4c的外侧面为所述散热面。
40.本实用新型中,金属基板的散热面之间作为冷却流道3的侧壁与冷却液直接接触进行散热。散热效果得到极大提高。
41.现有散热结构和本实用新型散热结构的热阻计算数据和散热的仿真数据对比如下:
42.铜导热系数:
43.焊锡导热系数:
44.铝基板铝基导热系数:
45.机壳导热系数:
46.铝基板绝缘层热阻:
47.散热硅脂热阻:
[0048][0049]
to263铜基散热面积:s
device
:=7.74mm
·
8.59mm=66.487mm2[0050]
焊锡厚度:th
solder
:=0.1mm
[0051]
铝基板铜箔厚度:th
copper
:=0.105mm
[0052]
铝基板厚度:th
al
:=2mm
[0053]
导热硅脂厚度:th
si
:=0.1mm
[0054]
水道壁厚度:th
alsi12fe
:=2mm
[0055]
器件热阻:
[0056]
焊接面热阻:
[0057]
铜箔热阻:
[0058]
铝基板绝缘层热阻:
[0059]
铝基板铝基热阻:
[0060]
导热硅脂热阻:
[0061]
水道壁热阻:
[0062]
总热阻:
[0063]
参看图10示出的使用现有冷却流道结构功率器件内部晶元热仿真数据图,图11示出的使用现有冷却流道结构功率器件外表热仿真数据图,图12示出的使用本实用新型冷却流道结构功率器件内部晶元热仿真数据图,图13示出的使用本实用新型冷却流道结构电机功率器件外表热仿真数据图。从四张图中对比可知,使用本实用新型后,功率器件内部晶元内部的温度下降46度左右,功率器件外表的温度下降26度左右,降温效果良好。
[0064]
参看图5示出的金属基电路板正面(带电子元件面)视图,所述金属基电路板包含金属基板、电子元件5(主要是指功率器件mos管)、功率信号连接端子15,功率器件贴片回流焊焊接在金属基板上,功率器件以贴片化取代插件,使得功率器件的一致性更好,通过功率信号端子与主pcb板组件16进行功率信号传输。进一步地,金属基板的顶端设有与功率器件电连接的至少一个插接端口,pcb板设有允许插接端口插入的槽孔,槽孔中布置有用于与插接端口电连接的导体。
[0065]
参看图6示出的金属基电路板背面(散热面)视图所述金属基电路板4的散热面上设有多条波纹凹槽4e,波纹凹槽的方向与冷却流道3中水流的方向垂直。波纹凹槽最大限度的增加散热面积,波纹凹槽上形成的筋位也能进一步增加金属基板整个面的强度。
[0066]
参看图3示出的流道本体与金属基电路板分离示意图和7示出的较佳实施例爆炸分解视图,所述金属基电路板4的边沿上设有通孔4f,所述镂空窗口的边沿设有螺丝孔8,螺钉7穿过通孔与螺丝孔螺接,从而将金属基电路板4封堵住镂空窗口。在图4示出的一个实施例中,为方便设置螺丝孔8,避免螺丝孔8成为通孔,在有螺丝孔8的位置的流道本体2背离镂
空窗口的一面设置了加强筋2a以增加此处的厚度。
[0067]
参看图3图7示出的较佳实施例,所述螺钉7穿过绝缘套9后在插入通孔4f,螺钉7的螺帽沉入绝缘套9凹槽中。绝缘套9的立体结构如图3。螺钉与金属基板之间通过一个绝缘套隔开,这样有效的增加金属基板的利用率,因为功率器件贴在金属基板上,螺钉是与流道本体2接触的,功率器件与螺钉之间需要保证一定的安规距离,绝缘套可以减少这个安规距离,增加金属基板的有效利用率。进一步地,螺钉帽与绝缘套的内凹槽接触,绝缘套的外平面与金属基板功能面(焊接电子元件的一面)接触,这样保证螺钉与金属基板的功能面绝缘。进一步地,螺钉7的螺帽沉入绝缘套9凹槽中,这样增加了螺钉到金属基板功能面的爬电距离。
[0068]
参看图4图7示出的较佳实施例,所述所述冷却流道3的内侧壁上设有湍流发生器10。所述湍流发生器10为波浪形的沟槽,冷却液在水道流动时,会有部分流体流入沟槽,沟槽可以形成很多小条的散热流道,带走原器件的热量。进一步的,沟槽形成了多条小的散热流道,沟槽与沟槽之间的形成的筋位又能增加整个外壳立体水道底部的强度。
[0069]
参看图8示出的较佳实施例俯视图,所述冷却流道3呈条带状,弯曲成u字形布置,其两端分别设有进水口11和出水口12。参看图9示出的较佳实施例底面视图,冷却流道3的纵截面呈开口的深槽状,冷却流道3开口处设有冷却流道盖板13。所述冷却流道盖板13通过搅拌摩擦焊与流道本体2进行密封和固定。进一步地,流道本体2做一个沉下去的仿形(仿照冷却流道盖板13的外形)的凹槽来对冷却流道盖板13做一个定位和限位的功能,让冷却流道盖板13放在凹槽中,就可以满足冷却流道盖板13的限位和定位。固定密封方式不局限于用搅拌摩擦焊,也可以采用密封硅橡胶和螺钉固定密封。
[0070]
参看图7示出的较佳实施例爆炸分解视图;所述金属基电路板4设置在u字形冷却流道3的外向侧壁上,u字形冷却流道3的弯内中部可设置发热元件。当本实用新型应用到车载充电机中时,所述发热元件为磁性元件,磁性元件放置在u字型内,磁性元件左右两侧均与流道本体2接触,磁性元件与流道本体2的间隙采用导热灌胶胶填充,这样的布置最大程度提升磁性元件散热效果,提高了磁芯元件的使用功率,并减小电源模块的整体体积及提升电源模块的整体功率密度。
[0071]
参看图14示出的较佳实施例,所述金属基电路板4与镂空窗口之间设有一个绝缘框20,所述绝缘框采用窗框结构,其横截面为“l”字形;金属基电路板4放置于绝缘框内,金属基电路板的周边为绝缘框侧壁,金属基电路板与镂空窗口之间为绝缘框底壁。增加绝缘框20,一方面可以增加金属基电路板与镂空窗口之间的绝缘,另一方面可增加金属基电路板上表面的电路与机壳之间的爬电距离和电气间隙。
[0072]
参看图15示出的较佳实施例,所述金属基电路板4带电子元件5的一面灌注一层灌封胶21。灌注灌封胶可以强化电子器件的整体性,提高对外来冲击、震动的抵抗力;提高内部元件、线路间绝缘,有利于器件小型化、轻量化;避免元件、线路直接暴露,改善器件的防水、防潮性能。
[0073]
参看图15示出的较佳实施例,灌封胶外表面覆盖一层绝缘板22。这样可以进一步提升金属基电路板4的绝缘性能。
[0074]
参看图7示出的较佳实施例,所述密封装置采用密封胶圈6。在镂空窗口的边沿设有容纳密封胶圈的密封胶圈卡槽14。
[0075]
在较佳实施例中,所述金属基电路板4采用铝基电路板。
[0076]
本实用新型还设计了一种车载充电机,包括充电电路和冷却系统,所述冷却系统采用上述的复用金属基电路板的冷却流道结构。
[0077]
以上实施例仅为举例说明,非起限制作用。任何未脱离本技术精神与范畴,而对其进行的等效修改或变更,均应包含于本技术的权利要求范围之中。