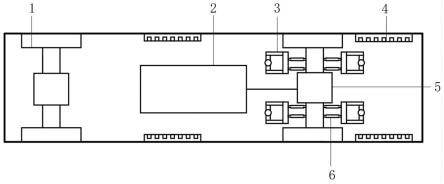
1.本发明涉及轨道列车技术领域,具体涉及一种高速列车轨道缺陷检测系统及检测方法。
背景技术:2.随着经济社会的高速发展,轨道运输速度不断提升。与传统的货运客运列车相比,高速列车(速度≥200km/h)在轨道运输中所占的比例越来越大,进而推动了高速轨道列车的制动系统的升级。传统的货运客运列车所采用的摩擦制动方式是一种典型的接触式制动方式,具有易热失效、制动时易产生抖动、制动声音大等缺点,适用于速度较低、载重较小的普通列车制动,而不再满足高速列车制动的安全要求。现代高速列车常采用的制动方式为涡流制动与摩擦制动相结合的制动方式。将高速列车制动分为缓速和止动两个阶段,在高速列车处于高速运动阶段采用涡流制动方式进行缓速,在速度降低到一定程度后再采用传统的摩擦制动方式进行止动,这样不仅可以增加摩擦制动的寿命,也可以保证高速列车运行时的平稳性。
3.涡流制动方式的原理是当高速列车需要减速运行时,运用涡流效应来消耗动能从而达到降速的目的。从能量角度来看,涡流缓速过程实际上就是把高速列车动能转化为轨道中的涡流热能。根据涡流缓速过程的基本原理可知,高速列车速度快、载重大的特点使得高速轨道中产生的涡流热能更大、温升更大。与普通轨道相比,高速轨道长时间处于高温环境中,更易出现轨道内部损伤、轨道表面与亚表面疲劳裂纹等缺陷,因此,有必要对因涡流制动可能产生的轨道缺陷进行检测。
4.目前常用于轨道缺陷检测的无损检测技术有以下几种:电涡流检测、超声波检测、磁粉检测、射线检测、渗透检测、红外热成像无损检测技术等。
5.电涡流检测通过在轨道中产生旋涡状的感应交变电流,使用探测传感器获得轨道的缺陷特征。电涡流检测具有非接触测量、测量效果好等优点,缺点是只能够检测到钢轨表面和近表面结构状态,对于轨道内部的核伤与裂纹则难以进行检验,以及需要额外配备电涡流产生装置,检测频率较低。
6.超声波检测技术主要采用轮式探头发出超声波对钢轨内部产生的疲劳裂纹进行检测,具有设备价格低廉等优点,但是超声波检测技术为接触式测量,并且对于表面和近表面的疲劳裂纹,如轨头龟裂和压溃等缺陷很难或根本无法检测出来,检测效果较差。
7.磁粉检测技术是利用铁磁性材料或工件磁化后在不连续处漏磁场与磁粉相互作用,从而形成在合适光照下目视可见的磁痕,以此来显示出缺陷位置、形状和大小的检测方法。具有很高的检测准确度、灵敏度和可靠性,但是检测范围小、检测速度慢,对检测人员的技术和经验要求高,无法做到高频率的检测。
8.射线检测技术是通过辐射照射到物体上,入射的光子将会与组成轨道的原子发生相互作用,从而使得轨道内部的疲劳裂纹与相邻区域产生透过射线强度的差异的检测方法。具有检测结果准确等优点,但是不能发现与射线方向垂直的微小线性缺陷,并且对环境
有辐射污染,对操作人员要求高。
9.渗透检测技术是在一定灯光条件下,缺陷处的渗透液痕迹会发出荧光或显色,通过观察荧光处或带颜色区域的分布情况来检测裂纹的形貌。渗透检测技术的检测速度相对较慢,而且在检测过程中需要用到显像剂和渗透液,污染性会较高。
10.红外热成像无损检测技术,一般是以红外辐射原理为基础,通过红外辐射测量分析的方法和技术对试件、材料及其他被测对象进行测量和检验。红外无损检测技术正是通过测出物体表面的温度分布,进而对轨道内部是否存在疲劳裂纹做出判断。红外热成像无损检测技术具有无接触、可大面积检测、结果直观、可同时实现表面及内部检测等优点。但是需要配备额外发热源对轨道表面进行高温加热,使得轨道表面温度进一步升高。
11.目前,国际与国内较为普遍采用的轨道缺陷检测方法是将上述无损检测装备安装到单独的检测车上,通过人工驾驶检测车对轨道进行定期巡检,并对损伤轨道进行定期维护。该方法是人工驾驶检测车进行定期检测,但是该种方法检测效率低,检测频率低,这导致了无法及时发现轨道缺陷,并且该种方法人力成本高、设备成本高,限制了该种方法的应用范围。
12.目前红外热成像缺陷检测技术与涡流缓速技术均为单独使用,市场上还没有出现将红外热成像检测方法与涡流缓速方法相结合并应用于高速轨道探伤的方法及装置。
技术实现要素:13.本发明的目的在于提供一种高速列车轨道缺陷检测系统及检测方法,通过热成像技术与涡流制动技术相结合,可以实时检测轨道的缺陷,及时对轨道进行维护。
14.为实现上述目的,本发明一方面公开了一种高速列车轨道缺陷检测系统,包括轨道缺陷检测装置和电磁涡流制动装置,所述电磁涡流制动装置安装于列车底部、轨道的正上方,所述轨道缺陷检测装置安装于转向架两侧,所述轨道缺陷检测装置、所述电磁涡流制动装置均通过数据线与工控机连接;在至少三个安装有电磁涡流制动装置的列车车厢底部安装所述轨道缺陷检测装置;所述轨道缺陷检测装置包括热成像仪和热成像检测单元,所述热成像仪包括热像仪机芯、热成像镜头设备和热成像报警设备;所述热成像检测单元包括电源、检测与控制模块、镜头驱动器、外部通讯接口和输入通讯接口,所述外部通讯接口与外部输入设备、所述检测与控制模块相连,外部输入设备通过外部通讯接口将控制信号传输至检测与控制模块;所述检测与控制模块与热成像报警设备与所述镜头驱动器、所述输入通讯接口相连接,在接收到控制热成像镜头设备的控制信号时,当输出信号达到预设值时,将信号传送至所述镜头驱动器,进而驱动热成像镜头设备;所述输入通讯接口与热成像仪机芯相连接;所述镜头驱动器与热成像镜头设备相连接,以控制镜头转动;所述电源分别与输入通讯接口、外部通讯接口、镜头驱动器、检测与控制模块相连接;所述检测与控制模块将数据传送至输入通讯接口,然后通过输入通讯接口将控制数据发送给热成像仪机芯,以此来控制热成像仪机芯。在工作过程中热成像仪机芯给输入通讯接口传送温度数据,输入通讯接口将数据传送至检测与控制模块,以控制热成像报警设备;
15.所述电磁涡流制动装置包括电动推杆、升降台、串联磁路混合励磁直线涡流制动装置,所述电动推杆上部通过螺栓与所述转向架相连,所述电动推杆的下方通过螺栓与升降台连接,所述升降台的下方通过螺栓与串联磁路混合励磁直线涡流制动装置相连。
16.进一步地,所述轨道缺陷检测装置通过减震器与所述转向架连接。
17.进一步地,列车车厢底部设置四只电磁涡流制动装置和四只轨道缺陷检测装置,其中两只电磁涡流制动装置和两只轨道缺陷检测装置用于列车行进的一个方向上的制动与检测,其余用于列车行进的相反方向上的制动与检测。
18.进一步地,同车厢上不同方向上的电磁涡流制动装置与轨道缺陷检测装置互为备用。
19.进一步地,所述轨道缺陷检测装置还包括承载单元,所述承载单元用于承载所述热成像仪并控制热成像仪动作,所述承载单元包括上承载结构,所述上承载结构包括左下支撑柱、左上支撑柱、俯仰电机、深沟球轴承、右上支撑柱、右下支撑柱、电池;所述左下支撑柱通过防松螺钉与所述左上支撑柱相连,所述右下支撑柱与所述右上支撑柱通过防松螺钉相连;所述俯仰电机安装在所述左上支撑柱上,所述电池安装在所述左下支撑柱上,所述深沟球轴承安装在所述右上支撑柱上,所述俯仰电机输出轴与热成像仪左侧相连,所述热成像仪右侧与所述深沟球轴承轴联。
20.进一步地,所述承载单元还包括下承载结构,所述下承载结构包括转台、摆动电机、底座、小齿轮、底板、保护罩、大齿轮、中心转轴、中心轴套、衬套;所述衬套与转台用螺钉相连,实现热成像仪在以中心转轴轴线为中心左右转动,转台上方与左支撑柱下、右支撑柱下用螺钉相连,中心轴套穿过中心转轴,并与中心转轴间隙配合,以此来起到定位中心转轴的作用,摆动电机与底座上表面通过螺栓相连,摆动电机的输出轴的外部与小齿轮通过键联接,进而带动小齿轮转动,小齿轮与大齿轮相互啮合,大齿轮与中心转轴通过紧定螺钉相连,中心转轴与转台相连接,衬套与中心转轴通过过盈配合相连,与转台下部通过螺钉相连;保护罩与底板上部相连,大齿轮和小齿轮位于保护罩内部。
21.另一方面,本发明还公开了一种高速列车轨道缺陷检测方法,包括
22.在至少三节列车车厢底部布置电磁涡流制动装置和轨道缺陷检测装置;
23.在高速情况下,电磁涡流制动装置启动,对列车实施降速制动,轨道吸收电涡流制动产生的热量;
24.轨道缺陷检测装置对吸收热量后的轨道进行热成像识别,并将数据传送到工控机中生成轨道缺陷值;
25.工控机对各轨道缺陷检测装置的轨道缺陷值进行实时监测,当至少三节车厢的轨道缺陷检测装置的缺陷值大于预设的缺陷阈值后,工控机控制所述轨道缺陷检测装置报警并标记轨道段所在位置。
26.进一步地,轨道缺陷检测装置出现故障后,由工控机进行装置切换,将同车厢用于相反方向运行检测的轨道缺陷检测装置切换过来,加入实时检测。
27.进一步地,电磁涡流制动装置出现故障后,由工控机进行装置切换,将同车厢用于相反方向运行检测的电磁涡流制动装置切换过来,以保证列车运行安全。
28.本发明的有益效果是:基于热成像仪及热成像检测单元的高速轨道缺陷检测系统与电涡流制动技术相结合,在高速列车的电磁涡流制动装置在制动过程中产生的大量热量被轨道吸收后产生温度变化,通过热成像仪及其检测单元对其进行相应的识别与判断,当三个及以上轨道缺陷检测装置中的热成像检测单元同时检测到轨道缺陷数量超过阈值时,热成像检测单元的检测与控制模块,会控制热成像报警设备自动报警,并自动记录轨道缺
陷发生时高速列车的实时位置与实时运行速度。与现有的各种高速轨道缺陷检测装置相比,本发明具有可实时检测高速轨道缺陷、提升高速轨道缺陷检测准确性、提升高速轨道缺陷检测频率、实现自动检测、简化设备、降低人力及设备成本等优点,对现代高速列车行驶安全系数的提高具有重大意义。
附图说明
29.图1为本发明轨道缺陷检测系统应用于高铁列车的装配位置示意图;
30.图2为轨道缺陷检测装置的上承载结构示意图;
31.图3为轨道检测装置的下承载结构示意图;
32.图4为电磁涡流制动装置结构示意图;
33.图5为热成像检测单元控制原理图;
34.图6为本发明轨道缺陷检测系统的工作流程图;
35.图7是电磁涡流制动装置冗余切换流程图;
36.图中,1-车轮,2-工控机,3-轨道缺陷检测装置,4-电磁涡流制动装置,4-1-电动推杆,4-2-升降台,4-3-串联磁路混合励磁直线涡流制动装置,5-转向架,6-减震器,7-左下支撑柱,8-左上支撑柱,9-俯仰电机,10-热成像仪,11-深沟球轴承,12-右上支撑柱,13-右下支撑柱,14-电池,15-转台,16-摆动电机,17-底座,18-小齿轮,19-底板,20-保护罩,21-大齿轮,22-中心转轴,23-中心轴套,24-衬套。
具体实施方式
37.下面结合附图及具体实施例对本发明作进一步详细说明。
38.如图1所示,一种高速列车轨道缺陷检测系统,包括轨道缺陷检测装置3和电磁涡流制动装置4,电磁涡流制动装置4安装于列车底部、轨道正上方,轨道缺陷检测装置3安装于转向架5两侧,转向架5位于两个车轮1之间。轨道缺陷检测装置3和电磁涡流制动装置4产生的数据均传送到工控机2中,在至少三个安装有电磁涡流制动装置4的列车车厢底部安装轨道缺陷检测装置3。本实施例中,一个列车车厢底部总共安装四个轨道缺陷检测装置3及四个电磁涡流制动装置4,考虑到列车车厢会有双向运行的情况,每一个方向均有两个轨道缺陷检测装置3及两个电磁涡流制动装置4处于工作状态,在同方向上,每个轨道缺陷检测装置3对一根轨道进行检测,两个轨道缺陷检测装置3对两根轨道进行实时检测。在每一个方向上,均是电磁涡流制动装置4位于轨道缺陷检测装置3的前面。
39.同时,在列车单向行驶时,其余两个不工作的电磁涡流制动装置4和轨道缺陷检测装置3作为备用,在工作中的电磁涡流制动装置4或轨道缺陷检测装置3出现问题时,其可以及时投入运行,不会影响整个检测工作。
40.如图5所示,轨道缺陷检测装置3包括热成像仪10和热成像检测单元,所述热成像仪10包括热像仪机芯、热成像镜头设备和热成像报警设备;所述热成像检测单元包括电源、检测与控制模块、镜头驱动器、外部通讯接口和输入通讯接口,外部通讯接口与外部的输入设备相连接,外部通讯接口与检测与控制模块相连,外部输入设备通过外部通讯接口将控制信号传输至检测与控制模块。检测与控制模块与热成像报警设备相互连接。检测与控制模块与镜头驱动器、输入通讯接口相连接,在接收到控制热成像镜头设备的控制信号时,当
输出信号达到预设值时,将信号传送至镜头驱动器,进而驱动热成像镜头设备。输入通讯接口与热成像仪机芯相连接,镜头驱动器与热成像镜头设备相连接,以控制镜头转动。电源分别与输入通讯接口、外部通讯接口、镜头驱动器、检测与控制模块相连接。检测与控制模块将数据传送至输入通讯接口,然后通过输入通讯接口将控制数据发送给热成像仪机芯,以此来控制热成像仪机芯,在工作过程中热成像仪机芯给输入通讯接口传送温度数据,输入通讯接口将数据传送至检测与控制模块,以控制热成像报警设备。通过对热成像检测单元内部模块进行合理布局及连通设计,使其能及时准确地进行信号采集、处理及输出作业。
41.如图4所示,电磁涡流制动装置4包括电动推杆4-1、升降台4-2、串联磁路混合励磁直线涡流制动装置4-3,电动推杆4-1上部通过螺栓与转向架5相连,电动推杆4-1的下方通过螺栓与升降台4-2连接,升降台4-2的下方通过螺栓与串联磁路混合励磁直线涡流制动装置4-3连接。使用串联磁路混合励磁直线涡流制动装置4-3时,电动推杆4-1的实际伸缩长度可以根据实际工况及电控系统参数需要进行确定。
42.轨道缺陷检测装置3通过减震器6与转向架5连接,以减少对轨道缺陷检测装置3的震动。
43.如图2所示,轨道缺陷检测装置3还包括承载单元,承载单元用于承载热成像仪10并控制热成像仪10动作,承载单元包括上承载结构,上承载结构包括左下支撑柱7、左上支撑柱8、俯仰电机9、深沟球轴承11、右上支撑柱12、右下支撑柱13、电池14;左下支撑柱7通过防松螺钉与左上支撑柱8相连,右下支撑柱13与右上支撑柱12通过防松螺钉相连;俯仰电机9安装在左上支撑柱8上,电池14安装在左下支撑柱7上,深沟球轴承11安装在右上支撑柱12上,俯仰电机9输出轴与热成像仪10左侧相连,热成像仪10右侧与深沟球轴承11轴联。
44.如图3所示,承载单元还包括下承载结构,下承载结构包括转台15、摆动电机16、底座17、小齿轮18、底板19、保护罩20、大齿轮21、中心转轴22、中心轴套23、衬套24,其中,衬套24与转台15用螺钉相连,实现热成像仪10在以中心转轴22轴线为中心左右转动,转台15上方与左支撑柱下7、右支撑柱下13用螺钉相连,中心轴套23穿过中心转轴22,并与中心转轴22间隙配合,以此来起到定位中心转轴22的作用,摆动电机16与底座17上表面通过螺栓相连,摆动电机16的输出轴外部与小齿轮18通过键联接,进而带动小齿轮18转动,小齿轮18与大齿轮21相互啮合,大齿轮21与中心转轴22通过紧定螺钉相连,中心转轴22与转台15相连接,衬套24与中心转轴22通过过盈配合相连,与转台15下部通过螺钉相连,保护罩20与底板19上部相连,大小齿轮位于保护罩20内部。
45.当装有轨道缺陷检测装置3的高速列车在轨道上运行时,轨道缺陷检测装置3中的热成像仪及其检测单元不可避免地会产生一定程度的震动,进而导致轨道热成像图像质量产生问题,并进一步影响对轨道缺陷问题的判断,因此通过调整热成像仪10的俯仰与摆动来确保成像效果。具体来讲,俯仰动作靠俯仰电机9执行,其在垂直与轨道横切面的两侧动作,根据轨道因爬坡或下坡产生的角度变化对镜头进行相应微调;摆动动作是通过转台15的转动带动支撑装置转动,从而带动热成像仪10对准轨道的上表面到内侧之间的范围,从而可以检测到尽可能多的轨道图像。
46.另一方面,本发明还公开了一种高速列车轨道缺陷检测方法,包括
47.在至少三节列车车厢底部布置电磁涡流制动装置4和轨道缺陷检测装置3;
48.在高速情况下,电磁涡流制动装置4启动,对列车实施降速制动,轨道吸收电涡流
制动产生的热量;
49.轨道缺陷检测装置3对吸收热量后的轨道进行热成像识别,并将数据传送到工控机2中生成轨道缺陷值;
50.工控机2对各轨道检测装置3的轨道缺陷值进行实时监测,当至少三节车厢的轨道缺陷检测装置3的缺陷值大于预设的缺陷阈值后,工控机2控制所述轨道缺陷检测装置3报警并标记轨道段所在位置。
51.如图6所示,当装有轨道缺陷检测装置3的高速列车在轨道上运行时,电磁涡流制动装置4会由于制动而产生大量的热,轨道吸收热量,导致轨道温度产生变化,热成像检测单元对轨道产生的红外辐射进行测量,并转化为低电平信号,低电平信号再通过放大、限制带宽等处理,从信号中分离出有用的图像信息,再将图像信息发送给工控机2中,工控机2根据热成像图像对该段轨道的缺陷进行自动判断,在同一根轨道上,当至少三个列车车厢上的三个及以上热成像仪10及热成像检测单元同时判断图像信息中轨道表面或内部的疲劳裂纹数量超过阈值时,则判断该段轨道存在安全隐患,工控机2通过输入通讯接口向检测与控制模块发送数据,检测与控制模块控制热成像报警设备报警,检测与控制模块自动记录缺陷数量,并通过位置检测元件、速度检测元件自动记录轨道缺陷的发生位置与轨道缺陷发生时列车的运行速度;当轨道缺陷检测装置在轨道上运行时,已检测轨道无缺陷或轨道表面和内部的疲劳裂纹和核伤数量未超过阈值,所形成的热成像图像在传送给列车内部的计算机设备后被判定为该段轨道无缺陷,热成像报警设备不发生动作。在存在缺陷的轨道段,工控机通过gps等地位系统确定具体位置,并进行信息依规传送。
52.如图6所示还显示了轨道缺陷检测装置3切换冗余的流程图,轨道缺陷检测装置3出现故障后,由工控机2进行装置切换,将同车厢用于相反方向运行检测的轨道缺陷检测装置3切换过来,加入实时检测,并通过轨道缺陷检测装置将相应的故障信息发送到工控机2中。
53.如图7所示,电磁涡流制动装置4出现故障后,由工控机2进行装置切换,将同车厢用于相反方向运行检测的电磁涡流制动装置4切换过来,以保证列车运行安全。
54.通过上述轨道缺陷检测装置3及电磁涡流制动装置4的冗余设置,可以有效保障对轨道的实时缺陷检测与列车的安全运行。
55.上面结合附图对本发明的实施方式作了详细说明,但是本发明并不限于此,在所属技术领域的技术人员所具备的知识范围内,在不脱离本发明宗旨的前提下可以作出的各种变化,都处于本发明权利要求的保护范围之内。