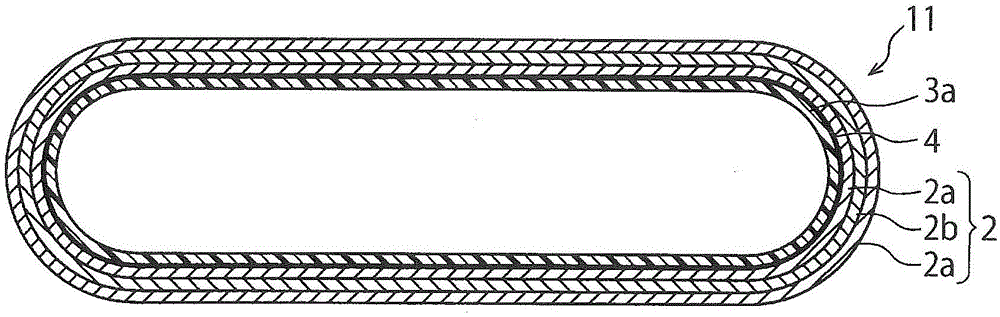
本发明涉及多层无缝带及其制造方法。更详细而言,本发明涉及例如可用于产业相关领域的、没有接合部、在作为传送及加热处理带时条件变动少、能减小厚度、并且强度耐久性、耐热性、非粘合性及耐磨耗性、防滑性(gripproperty)优异的多层无缝带及其制造方法。
背景技术:
:以往,在耐热性及拉伸强度等优异的耐热性纤维织物上复合耐热性、非粘合性优异的耐热性树脂而成的耐热性复合片材是已知的,这些耐热性复合片材已作为产业相关领域的耐热非粘合性片材、耐热非粘合性传送带等使用。作为上述耐热性复合片材中使用的耐热性纤维织物,例如,使用了将玻璃纤维、芳族聚酰胺纤维等以平纹组织、网状组织、斜纹组织、缎纹组织等形式织造而成的织物。另外,作为前述耐热性复合片材中使用的耐热性树脂,例如,使用了聚四氟乙烯树脂(ptfe)等氟树脂。然而,通常,对于氟树脂而言,虽然耐热性、耐寒性、非粘合性、耐药品性、耐燃烧性、耐气候性、电绝缘性、低摩擦性等优异,但由于缺乏耐磨耗性并且低摩擦性优异,因而存在容易打滑这样的问题。作为与氟树脂相比耐磨耗性优异的耐热性树脂,可举出聚酰亚胺系树脂等。另外,作为与氟树脂相比低摩擦性差、防滑性优异、不易打滑的耐热性材料,可举出聚酰亚胺系树脂、硅橡胶、氟橡胶等。需要说明的是,硅橡胶、氟橡胶具有缓冲性,也可作为缓冲材料利用,作为它们各自的特征,通常,硅橡胶在表面具有粘合性,其粘合性过度时,有时密合于对象物,异物容易附着并且不易除去,而且根据用途,有时聚硅氧烷成分的迁移被视为问题。关于该点,对于氟橡胶而言,虽然不存在聚硅氧烷成分,粘合性也小,但硬度硬,在价格上有不利方面,有长处也有短处。作为提高了耐磨耗性及防滑性的非粘合性复合片材以及传送带的制造方法,例如,提出了具有由氟树脂和耐热性纤维织物形成的复合材料层、和由聚酰亚胺系树脂或硅橡胶形成的表面层的多层片材;和将该多层片材裁成带状、将该多层片材的带状物的相对的两个端部接合而得到环状体从而形成的环形带的制造方法(日本特开2011-31572号公报(专利文献1))。通过前述的专利文献1中记载的片材以及环形带,有效地使用了提高了耐磨耗性及防滑性的非粘合性多层片材以及传送带,但是,因接合部的高低差而导致的条件变动以及因强度差而导致的耐久强度性成为需要改善之处。现有技术文献专利文献专利文献1:日本特开2011-31572号公报技术实现要素:发明所要解决的课题本发明是考虑上述情况并进行研究而得到的,目的在于提供没有接合部的、与所期望的用途、要求性能等相适应的条件变动少、能减小厚度、并且具有强度耐久性、优异的耐热性、非粘合性和必要的耐磨耗性、防滑性的多层无缝带及其制造方法。用于解决课题的手段本发明的多层无缝带的特征在于,具有:包含耐热性纤维的无缝带基材;和包含氟树脂、聚酰亚胺系树脂、硅橡胶或氟橡胶的表面层。对于这样的本发明的多层无缝带而言,作为优选的方式,包含下述的方案,其具有:含有包含耐热性纤维的无缝带基材和氟树脂的至少1层复合材料层;和包含聚酰亚胺系树脂、硅橡胶或氟橡胶的表面层。对于这样的本发明的多层无缝带而言,作为优选的方式,包含下述的方案,其中,在前述的复合材料层与前述的表面层之间存在有表面活化处理面。对于这样的本发明的多层无缝带而言,作为优选的方式,包含下述的方案,其中,前述的表面活化处理面是通过对前述的复合材料层实施的二氧化硅粒子附着烧成处理、金属钠蚀刻处理、等离子体放电处理或电晕放电处理而形成的。对于这样的本发明的多层无缝带而言,作为优选的方式,包含下述的方案,其周长为30~5000mm,特别优选周长为200~3600mm。对于这样的本发明的多层无缝带而言,作为优选的方式,包含下述的方案,其宽度为4~1500mm,特别优选其宽度为4~1000mm。对于这样的本发明的多层无缝带而言,作为优选的方式,包含下述的方案,包含耐热性纤维的无缝带基材的厚度为30~1000μm,特别优选为30~700μm,对于表面层的厚度而言,在氟树脂的情况下为1~300μm,特别优选为5~200μm,在聚酰亚胺系树脂的情况下为1~300μm,特别优选为5~200μm,在硅橡胶的情况下为1~700μm,特别优选为10~500μm,在氟橡胶的情况下为1~700μm,特别优选为10~500μm。此处,在多层无缝带的一侧的表面(即,多层无缝带的内侧面或外侧面中的一方的表面)上形成了由单一材料形成的前述表面层的情况下,该表面层的厚度成为前述范围内,在多层无缝带的两侧的表面(即,多层无缝带的内侧面及外侧面这两方的表面)上形成了由单一材料形成的前述的表面层的情况下,分别的一侧的表面层的厚度成为前述范围内。在多层无缝带的一侧或两侧的表面上形成了层叠多层不同的材料层而成的表面层的情况下,各材料层每1层的厚度成为前述范围内。而且,本发明的多层无缝带的制造方法的特征在于,在包含耐热性纤维的无缝带基材上形成包含氟树脂、聚酰亚胺系树脂、硅橡胶或氟橡胶的表面层。另外,本发明的多层无缝带的制造方法的特征在于,在包含耐热性纤维的无缝带基材中含浸氟树脂的粒子的水性悬浮液,进行干燥,然后进行烧成,由此形成复合材料层,然后,在该复合材料层上涂布聚酰亚胺系树脂、硅橡胶或氟橡胶,形成表面层。对于这样的本发明的多层无缝带的制造方法而言,作为优选的方式,包含下述的方案:在形成前述的复合材料层之后,对该复合材料层进行二氧化硅粒子附着烧成处理、金属钠蚀刻处理、等离子体放电处理或电晕放电处理,形成表面活化处理面,然后,涂布前述的聚酰亚胺系树脂、硅橡胶或氟橡胶,形成表面层。发明的效果通过本发明,能得到没有接合部的、与所期望的用途、要求性能等相适应的条件变动少、能减小厚度、并且具有强度耐久性、优异的耐热性、非粘合性及耐磨耗性、防滑性的多层无缝带。而且,通过本发明,能以能形成所期望的宽度的多层无缝带的方式进行切割。另外,根据情况,通过先形成宽度宽的多层无缝带,然后,将该宽度宽的多层无缝带切割成所期望的宽度,从而能同时制造多条长度相同的多层无缝带。另外,通过调节切割时的宽度,从而也容易分别制作宽度不同的多层无缝带。附图说明[图1]为表示本发明的多层无缝带的结构的截面图[图2]为表示本发明的多层无缝带的结构的截面图[图3]为表示本发明的多层无缝带的结构的截面图[图4]为表示本发明的多层无缝带的结构的截面图[图5]为表示本发明的多层无缝带的结构的截面图[图6]为表示本发明的多层无缝带的结构的截面图[图7]为表示本发明的多层无缝带的结构的截面图[图8]为表示本发明的多层无缝带的结构的截面图[图9]为表示本发明的多层无缝带的结构的截面图[图10]为表示本发明的多层无缝带的结构的截面图[图11]为表示本发明的多层无缝带的结构的截面图[图12]为表示本发明的多层无缝带的结构的截面图[图13]为表示本发明的多层无缝带的结构的截面图[图14]为表示本发明的多层无缝带的结构的截面图[图15]为表示本发明的多层无缝带的结构的截面图[图16]为表示本发明的多层无缝带的结构的截面图[图17]为表示本发明的多层无缝带的结构的截面图[图18]为表示本发明的多层无缝带的结构的截面图[图19]为表示本发明的多层无缝带的结构的截面图[图20]为表示本发明的多层无缝带的结构的截面图[图21]为表示本发明的多层无缝带的结构的截面图[图22]为表示本发明的多层无缝带的结构的截面图[图23]为表示本发明的多层无缝带的结构的截面图[图24]为表示本发明的多层无缝带的结构的截面图[图25]为表示本发明的多层无缝带的结构的截面图[图26]为表示本发明的多层无缝带的结构的截面图[图27]为表示本发明的多层无缝带的结构的截面图具体实施方式本发明的多层无缝带的特征在于,具有:包含耐热性纤维的无缝带基材;和包含氟树脂、聚酰亚胺系树脂、硅橡胶或氟橡胶的表面层。对于这样的本发明的多层无缝带而言,作为优选的方式,包含下述的方案,其具有:含有包含耐热性纤维的无缝带基材和氟树脂的至少1层复合材料层;和包含聚酰亚胺系树脂、硅橡胶或氟橡胶的表面层。此处,本说明书中所谓的无缝带,具体是指无缝(即,无接缝)环形带。对于这样的本发明的多层无缝带而言,作为优选的方式,包含下述的方案,其中,在前述的复合材料层与前述的表面层之间存在有表面活化处理面。对于这样的本发明的多层无缝带而言,作为优选的方式,包含下述的方案,其中,前述的表面活化处理面是通过对前述的复合材料层实施的二氧化硅粒子附着烧成处理、金属钠蚀刻处理、等离子体放电处理或电晕放电处理而形成的。作为这样的本发明的多层无缝带的优选的具体例,可举出例如图1~图27中记载的例子。图1所示的本发明的多层无缝带11是具有由氟树脂2a和包含耐热性纤维的无缝带基材2b形成的1层复合材料层2和由聚酰亚胺系树脂形成的表面层3a的多层无缝带,前述表面层3a是隔着通过对前述复合材料层2的内面进行的表面活化处理而形成的处理面4而形成的。图2所示的本发明的多层无缝带12是具有由氟树脂2a和包含耐热性纤维的无缝带基材2b形成的1层复合材料层2和由硅橡胶形成的表面层3b的多层无缝带,前述表面层3b是隔着通过对前述复合材料层2的内面进行的表面活化处理而形成的处理面4而形成的。图3所示的本发明的多层无缝带13是具有由氟树脂2a和包含耐热性纤维的无缝带基材2b形成的1层复合材料层2和由氟橡胶形成的表面层3c的多层无缝带,前述表面层3c是隔着通过对前述复合材料层2的内面进行的表面活化处理而形成的处理面4而形成的。图4所示的本发明的多层无缝带14是具有由氟树脂2a和包含耐热性纤维的无缝带基材2b形成的1层复合材料层2和由聚酰亚胺系树脂形成的表面层3a的多层无缝带,前述表面层3a是隔着通过对前述复合材料层2的外面进行的表面活化处理而形成的处理面4而形成的。图5所示的本发明的多层无缝带15是具有由氟树脂2a和包含耐热性纤维的无缝带基材2b形成的1层复合材料层2和由硅橡胶形成的表面层3b的多层无缝带,前述表面层3b是隔着通过对前述复合材料层2的外面进行的表面活化处理而形成的处理面4而形成的。图6所示的本发明的多层无缝带16是具有由氟树脂2a和包含耐热性纤维的无缝带基材2b形成的1层复合材料层2和由氟橡胶形成的表面层3c的多层无缝带,前述表面层3c是隔着通过对前述复合材料层2的外面进行的表面活化处理而形成的处理面4而形成的。图7所示的本发明的多层无缝带17是具有由氟树脂2a和包含耐热性纤维的无缝带基材2b形成的1层复合材料层2和由聚酰亚胺系树脂形成的表面层3a的多层无缝带,前述表面层3a是隔着通过对前述复合材料层2的两面进行的表面活化处理而形成的处理面4而形成的。图8所示的本发明的多层无缝带18是具有由氟树脂2a和包含耐热性纤维的无缝带基材2b形成的1层复合材料层2和由硅橡胶形成的表面层3b的多层无缝带,前述表面层3b是隔着通过对前述复合材料层2的两面进行的表面活化处理而形成的处理面4而形成的。图9所示的本发明的多层无缝带19是具有由氟树脂2a和包含耐热性纤维的无缝带基材2b形成的1层复合材料层2和由氟橡胶形成的表面层3c的多层无缝带,前述表面层3c是隔着通过对前述复合材料层2的两面进行的表面活化处理而形成的处理面4而形成的。图10所示的本发明的多层无缝带20是具有由氟树脂2a和包含耐热性纤维的无缝带基材2b形成的1层复合材料层2、位于内面的由聚酰亚胺系树脂形成的表面层3a和位于外面的由硅橡胶形成的表面层3b的多层无缝带,前述表面层3a和3b是隔着通过对前述复合材料层2的两面进行的表面活化处理而形成的处理面4而形成的。图11所示的本发明的多层无缝带21是具有由氟树脂2a和包含耐热性纤维的无缝带基材2b形成的1层复合材料层2、位于内面的由硅橡胶形成的表面层3b和位于外面的由聚酰亚胺系树脂形成的表面层3a的多层无缝带,前述表面层3b和3a是隔着通过对前述复合材料层2的两面进行的表面活化处理而形成的处理面4而形成的。图12所示的本发明的多层无缝带22是具有由氟树脂2a和包含耐热性纤维的无缝带基材2b形成的1层复合材料层2、位于内面的由聚酰亚胺系树脂形成的表面层3a和位于外面的由氟橡胶形成的表面层3c的多层无缝带,前述表面层3a和3c是隔着通过对前述复合材料层2的两面进行的表面活化处理而形成的处理面4而形成的。图13所示的本发明的多层无缝带23是具有由氟树脂2a和包含耐热性纤维的无缝带基材2b形成的1层复合材料层2、位于内面的由氟橡胶形成的表面层3c和位于外面的由聚酰亚胺系树脂形成的表面层3a的多层无缝带,前述表面层3c和3a是隔着通过对前述复合材料层2的两面进行的表面活化处理而形成的处理面4而形成的。图14所示的本发明的多层无缝带24是具有由氟树脂2a和包含耐热性纤维的无缝带基材2b形成的1层复合材料层2、位于内面的由聚酰亚胺系树脂形成的表面层3a和位于外面的由硅橡胶形成的表面层3b和由氟橡胶形成的表面层3c的多层无缝带,前述表面层3a和3b是隔着通过对前述复合材料层2的两面进行的表面活化处理而形成的处理面4而形成的。图15所示的本发明的多层无缝带25是具有由氟树脂2a和包含耐热性纤维的无缝带基材2b形成的1层复合材料层2、位于内面的由硅橡胶形成的表面层3b和由氟橡胶形成的表面层3c和位于外面的由聚酰亚胺系树脂形成的表面层3a的多层无缝带,前述表面层3b和3a是隔着通过对前述复合材料层2的两面进行的表面活化处理而形成的处理面4而形成的。图16所示的本发明的多层无缝带26是具有由氟树脂2a和包含耐热性纤维的无缝带基材2b形成的1层复合材料层2、和位于内面的由硅橡胶形成的表面层3b和由氟橡胶形成的表面层3c的多层无缝带,前述表面层3b是隔着通过对前述复合材料层2的一面进行的表面活化处理而形成的处理面4而形成的。图17所示的本发明的多层无缝带27是具有由氟树脂2a和包含耐热性纤维的无缝带基材2b形成的1层复合材料层2、和位于外面的由硅橡胶形成的表面层3b和由氟橡胶形成的表面层3c的多层无缝带,前述表面层3b是隔着通过对前述复合材料层2的一面进行的表面活化处理而形成的处理面4而形成的。图18所示的本发明的多层无缝带28是具有由氟树脂2a和包含耐热性纤维的无缝带基材2b形成的1层复合材料层2、位于两面的由硅橡胶形成的表面层3b和位于内面的由氟橡胶形成的表面层3c的多层无缝带,前述表面层3b是隔着通过对前述复合材料层2的两面进行的表面活化处理而形成的处理面4而形成的。图19所示的本发明的多层无缝带29是具有由氟树脂2a和包含耐热性纤维的无缝带基材2b形成的1层复合材料层2、位于两面的由硅橡胶形成的表面层3b和位于外面的由氟橡胶形成的表面层3c的多层无缝带,前述表面层3b是隔着通过对前述复合材料层2的两面进行的表面活化处理而形成的处理面4而形成的。图20所示的本发明的多层无缝带30是具有由氟树脂2a和包含耐热性纤维的无缝带基材2b形成的1层复合材料层2、位于两面的由硅橡胶形成的表面层3b、和位于两面的由氟橡胶形成的表面层3c的多层无缝带,前述表面层3b是隔着通过对前述复合材料层2的两面进行的表面活化处理而形成的处理面4而形成的。图21所示的本发明的多层无缝带31是具有包含耐热性纤维的无缝带基材2b、和位于两面的由聚酰亚胺系树脂形成的表面层3a的多层无缝带。图22所示的本发明的多层无缝带32是具有包含耐热性纤维的无缝带基材2b、和位于两面的由硅橡胶形成的表面层3b的多层无缝带。图23所示的本发明的多层无缝带33是具有包含耐热性纤维的无缝带基材2b、和位于两面的由氟橡胶形成的表面层3c的多层无缝带。图24所示的本发明的多层无缝带34是具有包含耐热性纤维的无缝带基材2b、位于两面的由硅橡胶形成的表面层3b和位于内面的由氟橡胶形成的表面层3c的多层无缝带。图25所示的本发明的多层无缝带35是具有包含耐热性纤维的无缝带基材2b、位于两面的由硅橡胶形成的表面层3b和位于外面的由氟橡胶形成的表面层3c的多层无缝带。图26所示的本发明的多层无缝带36是具有包含耐热性纤维的无缝带基材2b、位于两面的由硅橡胶形成的表面层3b和位于两面的由氟橡胶形成的表面层3c的多层无缝带。图27所示的本发明的多层无缝带37是具有包含耐热性纤维的无缝带基材2b、位于两面的由氟树脂形成的表面层2a的多层无缝带。本发明的多层无缝带的周长可根据具体的用途、目的等适当变更。优选为30~5000mm,特别优选为200~3600mm。多层无缝带的周长在前述范围内时,优选作为产业相关领域中使用的耐热非粘合性传送及加热处理带。例如,特别优选用于热封机(例如,包装用膜等的热熔接机等)、衬布粘接机(例如,制作被用于衬衫等的衣领、袖等变硬的部分的衬布时的将带有糊的外层材料与芯加热粘接的机械等)的用途。此外,可通过利用前述装置进行制造时的使用条件(例如,产品尺寸、熔接尺寸、制造速度、处理温度等)进行设计以成为最合适的周长。周长小于30mm时及大于5000mm时,存在制作变难的倾向。此处所谓的周长,是指不对无缝带施加张力的条件下的无缝带的内周面的长度。以往,周长的多层带是用接合带实现的,但通过本发明,变得能用多层无缝带来实现,能提供无接合部、条件变动少、能减小厚度、并且强度耐久性、耐热性、非粘合性、耐磨耗性、防滑性优异的环形带。<复合材料层>本发明的多层无缝带中的复合材料层含有:包含耐热性纤维的无缝带基材和氟树脂。作为本发明中的氟树脂,没有特别限制,可举出选自由聚四氟乙烯(ptfe)、四氟乙烯-全氟烷基乙烯基醚共聚物(pfa)、四氟乙烯-六氟丙烯共聚物(fep)组成的组中的耐热性树脂。其中,特别优选聚四氟乙烯。根据需要,可在前述氟树脂中配合导电性粉。由此,能实现导电性以及防静电性、导热性的赋予或提高以及耐磨耗性的提高等。作为导电性粉的优选的具体例,可举出炭黑及导电性氧化钛。相对于氟树脂而言,其配合量优选为1~40质量份。本发明中,作为包含耐热性纤维的无缝带基材,没有特别限制,可举出由玻璃纤维、芳族聚酰胺纤维形成的织物。无缝带基材的厚度通常为30~1000μm,特别优选为30~700μm。无缝带基材的厚度为上述范围内时,优选作为产业相关领域的耐热非粘合性传送及加热处理带。表面层的厚度小于30μm时,难以织造,而且强度变弱,另一方面,超过1000μm时,存在变得性能过剩(日文:オーバースペック)的倾向。以往,对于前述厚度的耐热性纤维而言,通过以片状层叠多层而形成片材、将所得片材接合而形成带的方式来实现,但通过本发明,变得能以无缝带状形成为多层,能提供无接合部、条件变动少、能减小厚度、并且强度耐久性、耐热性、非粘合性、耐磨耗性、防滑性优异的环形带。关于织构,可举出选自由平纹组织、网状组织、斜纹组织、缎纹组织组成的组中的耐热性纤维。其中,特别优选为平纹组织。这样的复合材料层例如可优选通过以下方式形成:将前述的氟树脂的粒子的水性悬浮液含浸在前述的耐热性纤维无缝织物中,进行干燥,然后进行烧成。作为制备水性悬浮液时的溶剂,例如为水,特别优选为纯水。相对于溶剂100质量份而言,水性悬浮液中的氟树脂的粒子的量优选为20~60质量份,特别优选为30~60质量份。对于本发明中的复合材料层而言,优选的是,氟树脂充分渗透至无缝带基材的内部,并且无缝带基材的表面被氟树脂被覆。因此,将无缝带基材的织物与氟树脂的总量作为100质量份,氟树脂的施用量为10~80质量份,特别优选为40~70质量份。<表面层>本发明的多层无缝带具有由氟树脂、聚酰亚胺系树脂或硅橡胶或氟橡胶形成的表面层。本发明中,聚酰亚胺系树脂没有特别限制,例如优选为聚酰亚胺及聚酰胺酰亚胺,特别优选为聚酰亚胺。本发明中,通过涂布而形成表面层时,为了使该涂布容易进行,可使用液状的聚酰亚胺清漆,根据需要,可配合溶剂。由此,能减小粘度,实现涂布性的提高。液状聚酰亚胺清漆的粘度优选为1~8000cp,特别优选为10~1000cp。另外,根据需要,可在聚酰亚胺中配合导电性粉。由此,例如能实现导电性以及防静电性、导热性的赋予或提高以及耐磨耗性的提高等。本发明中,硅橡胶没有特别限制,特别优选为液状硅橡胶。本发明中,通过涂布而形成表面层时,为了使该涂布容易进行,根据需要,可在硅橡胶中配合溶剂。由此,能减小粘度,实现涂布性的提高。液状硅橡胶的粘度优选为1~100000cp,特别优选为10~50000cp。另外,根据需要,可在硅橡胶中配合导电性粉。由此,例如能实现导电性以及防静电性、导热性的赋予或提高以及耐磨耗性的提高等。此外,根据需要,可在硅橡胶中添加固化促进剂、固化延迟剂。本发明中,氟橡胶没有特别限制,特别优选为液状氟橡胶。本发明中,通过涂布而形成表面层时,为了使该涂布容易进行,根据需要,可在氟橡胶中配合溶剂。由此,能减小粘度,实现涂布性的提高。氟橡胶的粘度优选为1~300000cp,特别优选为10~1000cp。另外,根据需要,可在氟橡胶中配合导电性粉。由此,例如能实现导电性以及防静电性、导热性的赋予或提高以及耐磨耗性的提高等。此外,根据需要,可在氟橡胶中添加固化促进剂、固化延迟剂。前述的表面层的形成可通过以下方式进行:在复合材料层的表面活化处理面上涂布前述的聚酰亚胺系树脂或硅橡胶或氟橡胶,进行干燥,然后进行烧成。聚酰亚胺系树脂的烧成温度优选为300~400℃,特别优选为330~370℃。硅橡胶的烧成温度优选为50~200℃,特别优选为50~150℃。氟橡胶的烧成温度优选为20~200℃,特别优选为20~150℃。烧成时间可根据烧成温度等适当确定。表面层的厚度可根据本发明的多层无缝带的具体的用途、目的等适当确定。氟树脂表面层的厚度优选为1~300μm,特别优选为5~200μm,聚酰亚胺树脂表面层的厚度优选为1~300μm,特别优选为5~200μm,硅橡胶表面层的厚度优选为1~700μm,特别优选为10~500μm,氟橡胶表面层的厚度优选为1~700μm,特别优选为10~500μm。如上文所述,此处,在多层无缝带的一侧的表面(即,多层无缝带的内侧面或外侧面中的一方的表面)上形成了由单一材料形成的前述表面层的情况下,该表面层的厚度成为前述范围内,在多层无缝带的两侧的表面(即,多层无缝带的内侧面及外侧面这两方的表面)上形成了由单一材料形成的前述的表面层的情况下,分别的一侧的表面层的厚度成为前述范围内。在多层无缝带的一侧或两侧的表面上形成了层叠多层材料层而成的表面层的情况下,各材料层每1层的厚度成为前述范围内。多层无缝带的表面层的厚度在前述范围内时,作为产业相关领域的耐热非粘合性传送及加热处理带,能长期良好地维持耐久性、耐热性、非粘合性、耐磨耗性及防滑性等各种特性。表面层的厚度小于前述范围的情况下,不能满足前述性能,另一方面,高于前述范围时,存在变得性能过剩的倾向。以往,前述厚度的多层带是用接合带实现的,但通过本发明,变得能用多层无缝带来实现,能提供无接合部、条件变动少、能减小厚度、并且强度耐久性、耐热性、非粘合性、耐磨耗性、防滑性优异的环形带。<表面活化处理>本发明的多层无缝带中,优选的是,前述表面层可以是隔着通过对前述复合材料层实施的表面活化处理而形成的处理面而形成的。此处所谓的表面活化处理,是指下述处理:通过对前述的本发明的复合材料层的表面的氟树脂进行处理,使其表面张力下降,使复合材料层的氟树脂与作为多层无缝带的表面层而形成的聚酰亚胺系树脂或硅橡胶或氟橡胶的接合成为可能,并且,呈现充分的接合强度。未进行该表面活化处理的情况下,不能在前述的复合材料上形成由聚酰亚胺系树脂或硅橡胶或氟橡胶形成的表面层,不能达成本发明的目的。作为本发明中的优选的表面活化处理,可举出例如二氧化硅粒子附着烧成处理、金属钠蚀刻表面处理、等离子体放电处理、电晕放电处理。其中,特别优选二氧化硅粒子附着烧成处理。此处,本发明中的表面活化处理的详细情况如下文所示。二氧化硅粒子附着烧成处理:在由氟树脂和耐热性纤维无缝织物形成的复合材料层的表面上,涂布二氧化硅粒子与氟树脂粒子的混合水性悬浮液,然后进行烧成处理,由此,提高复合材料层表面的亲水性。金属钠蚀刻表面处理:在由氟树脂和耐热性纤维无缝织物形成的复合材料层的表面上,涂布金属钠溶液,由此,提高复合材料层表面的亲水性。等离子体放电处理:在由氟树脂和耐热性纤维无缝织物形成的复合材料层的表面上,实施辉光放电处理,提高复合材料层表面的亲水性。电晕放电处理:在由氟树脂和耐热性纤维无缝织物形成的前述的复合材料层的表面上,实施电晕放电处理,提高复合材料层表面的亲水性。关于表面活化处理,优选对前述复合材料层的形成前述的表面层的部位的整面进行,但也可对前述复合材料层的形成表面层的部位的一部分进行。通过实施这样的表面活化处理,能显著降低在复合材料层表面的氟树脂面上滴加纯水时的接触角(jisk6768)。对于在表面活化处理前为106°左右的接触角而言,通过二氧化硅粒子附着烧成处理,降低至80~90°,通过金属钠蚀刻表面处理,降低至50~60°,通过等离子体放电处理,降低至50~60°。另外,根据需要,可进行底涂处理。由此,例如能实现接合强度的提高等。<宽度调节>这样的本发明中,通过先形成宽度宽的多层无缝带,然后,将该宽度宽的无缝带切割成所期望的宽度,从而能同时制造多条长度相同的多层无缝带。另外,通过调节切割前述的宽度宽的多层无缝带时的宽度,从而也容易分别制作宽度不同的多层无缝带。本发明的多层无缝带的宽度可根据具体的用途、目的等适当变更。优选为4~1500mm,特别优选为4~1000mm。多层无缝带的宽度为上述范围内时,优选作为产业相关领域中使用的耐热非粘合性传送及加热处理带。例如,特别优选用于热封机(例如,包装用膜等的热熔接机等)、衬布粘接机(例如,制作被用于衬衫等的衣领、袖等变硬的部分的衬布时的将带有糊的外层材料与芯加热粘接的机械等)的用途。此外,可通过利用前述装置进行制造时的使用条件(例如,产品尺寸、熔接尺寸、制造速度、处理温度等)进行设计以成为最合适的宽度。宽度小于4mm时及大于1500mm时,存在制作变难的倾向。以往,前述宽度的多层带是用接合带实现的,但通过本发明,变得能用多层无缝带来实现,能提供无接合部、条件变动少、能减小厚度、并且强度耐久性、耐热性、非粘合性、耐磨耗性、防滑性优异的环形带。<多层无缝带的制造方法>本发明的多层无缝带的制造方法的特征在于,在包含耐热性纤维的无缝带基材2b中含浸氟树脂的粒子的水性悬浮液,进行干燥,然后进行烧成,由此形成复合材料层2,然后,在该复合材料层2上涂布聚酰亚胺系树脂、硅橡胶或氟橡胶,形成表面层3a、3b、3c。尤其是,例如图1~图3所示那样的优选在复合材料层2与表面层3a、3b、3c之间存在有表面活化处理面4的多层无缝带可通过以下方式制造:在包含耐热性纤维的无缝带基材2b中含浸氟树脂的粒子的水性悬浮液,进行干燥,然后进行烧成,由此形成复合材料层2,对该复合材料层2进行二氧化硅粒子附着烧成处理、金属钠蚀刻处理、等离子体放电处理或电晕放电处理,形成活化处理面4,然后,涂布聚酰亚胺系树脂、硅橡胶或氟橡胶,形成表面层3a、3b、3c。实施例以下,示出本发明中被认为优选的实施例与以往方法等的比较研究结果。<实施例a1>(1)在氟树脂与玻璃纤维无缝织物的复合材料的一面上形成了聚酰亚胺树脂表面层的多层无缝带首先,为了得到氟树脂与玻璃纤维无缝织物的复合材料,将氟树脂(ptfe)的水性悬浮液含浸并附着于玻璃纤维无缝织物(厚度95μm),于80℃进行干燥,然后于380℃的温度进行烧成,得到氟树脂与玻璃纤维无缝织物的复合材料(厚度130μm)。接下来,为了对氟树脂与玻璃纤维无缝织物的复合材料进行表面活化处理,在二氧化硅的水性悬浮液100质量份中混合ptfe树脂的水性悬浮液100质量份,得到表面活化处理液。接下来,将表面活化处理液涂布并附着于氟树脂与玻璃纤维无缝织物的复合材料的一面,于80℃进行干燥,然后于380℃的温度进行烧成,使二氧化硅附着烧成,得到表面活化处理面。接下来,为了得到液状聚酰亚胺清漆,在液状聚酰亚胺清漆100质量份中混合溶剂(二甲基乙酰胺(dmac))100质量份,得到粘度为50cp的液状聚酰亚胺清漆。接下来,将前述的液状聚酰亚胺清漆涂布并附着于前述的氟树脂与玻璃纤维无缝织物的复合材料(厚度130μm)的表面活化处理面,于80℃进行干燥,然后于350℃的温度进行烧成,得到在氟树脂与玻璃纤维无缝织物的复合材料的一面上形成了聚酰亚胺树脂表面层的多层无缝带(厚度135μm)(图1、图4)。利用后述的评价方法对按照上述方式得到的复合材料的氟树脂层面与多层无缝带的聚酰亚胺树脂层面进行比较。将评价结果示于表1。1)磨耗试验:按照jish8682-1来实施。(使用suga磨耗试验机,在速度为40次、负荷为0.8kg、试验次数为300次、将磨耗轮(直径为50mm、宽度12mm)作为相对材料、耐水膜为#4000的条件下进行测定。)2)摩擦系数:按照jisk7125来实施。(使用岛津制作所公司制摩擦系数试验机,在滑动速度为100mm/min、负荷为200g的条件下、使用sus304作为相对材料进行测定。)3)接触角:按照jisk6768来实施。(使用协和界面化学公司制的接触角计ca-d型,使用蒸馏水作为试验液来进行测定。)[表1]表1试验项目氟树脂层面(ptfe)聚酰亚胺树脂层面磨耗量(mg)0.500.13动摩擦系数0.090.28接触角(°)10695根据前述的评价结果,聚酰亚胺树脂与氟树脂相比,耐磨耗性优异,非粘合性、低摩擦性差。由该结果可知,聚酰亚胺树脂与氟树脂相比,不易磨耗、打滑。对于实施例a1的结构而言,优选的是,将氟树脂面应用于要求非粘合性、低摩擦性的工件侧,将聚酰亚胺树脂面应用于要求耐磨耗性、防滑性的工件非接触侧,但不限于此。<实施例b1>(2)在氟树脂与玻璃纤维无缝织物的复合材料的一面上形成了硅橡胶表面层的多层无缝带与实施例a1同样地操作,得到氟树脂与玻璃纤维无缝织物的复合材料(厚度130μm)。在该复合材料的一面上,与实施例a1同样地操作,得到表面活化处理面。接下来,为了得到液状硅橡胶,在液状硅橡胶100质量份中混合有机溶剂(甲苯)10质量份,混合固化剂10质量份,得到粘度为50000cp的液状硅橡胶。接下来,将前述的液状硅橡胶涂布并附着于复合材料的表面活化处理面,于90℃的温度使其固化,进行硅橡胶表面层的形成,得到在复合材料的一面上形成了硅橡胶表面层的多层无缝带(厚度195μm)(图2、图5)。对按照上述方式得到的实施例b1的氟树脂层面与硅橡胶层面进行比较。将评价结果示于表2。[表2]表2试验项目氟树脂层面(ptfe)硅橡胶层面磨耗量(mg)0.500.37动摩擦系数0.091.22接触角(°)106104根据前述的评价结果,硅橡胶与氟树脂相比,非粘合性、低摩擦性差。由该结果可知,硅橡胶与氟树脂相比,不易打滑。对于该实施例b1的环形带的结构而言,优选的是,将氟树脂面应用于要求非粘合性、低摩擦性的工件侧,将硅橡胶面应用于要求防滑性的工件非接触侧,但不限于此。<实施例c1>(3)在氟树脂与玻璃纤维无缝织物的复合材料的一面上形成了氟橡胶表面层的多层无缝带与实施例a1同样地操作,得到氟树脂与玻璃纤维无缝织物的复合材料(厚度130μm)。在该复合材料的一面上,与实施例a1同样地操作,得到表面活化处理面。接下来,为了得到液状氟橡胶,在液状氟橡胶100质量份中混合有机溶剂(mek)10质量份,混合固化剂10质量份,得到粘度为1000cp的液状氟橡胶。接下来,将前述的液状氟橡胶涂布并附着于复合材料的表面活化处理面,于60℃的温度使其固化,进行氟橡胶表面层的形成,得到在复合材料的一面上形成了氟橡胶表面层的多层无缝带(厚度150μm)(图3、图6)。对按照上述方式得到的实施例c1的氟树脂层面与氟橡胶层面进行比较。将评价结果示于表3。[表3]表3试验项目氟树脂层面(ptfe)氟橡胶层面磨耗量(mg)0.500.23动摩擦系数0.091.10接触角(°)10691根据前述的评价结果,氟橡胶与氟树脂相比,非粘合性、低摩擦性差。由该结果可知,氟橡胶与氟树脂相比,不易打滑。对于该实施例c1的环形带的结构而言,优选的是,将氟树脂面应用于要求非粘合性、低摩擦性的工件侧,将氟橡胶面应用于要求防滑性的工件非接触侧,但不限于此。<实施例a2>(4)在氟树脂与玻璃纤维无缝织物的复合材料的两面上形成了聚酰亚胺树脂表面层的多层无缝带与实施例a1同样地操作,得到氟树脂与玻璃纤维无缝织物的复合材料(厚度130μm)。在该复合材料的两面上,与实施例a1同样地操作,进行表面活化处理面及聚酰亚胺树脂表面层的形成,得到在复合材料的两面上形成了聚酰亚胺树脂表面层的多层无缝带(厚度140μm)(图7)。对于实施例a2的结构而言,优选的是,应用于要求耐磨耗性、防滑性的用途,但不限于此。<实施例b2>(5)在氟树脂与玻璃纤维无缝织物的复合材料的两面上形成了硅橡胶表面层的多层无缝带与实施例a1同样地操作,得到氟树脂与玻璃纤维无缝织物的复合材料(厚度130μm)。在该复合材料的两面上,与实施例b1同样地操作,进行表面活化处理面及硅橡胶表面层的形成,得到在复合材料的两面上形成了硅橡胶表面层的多层无缝带(厚度260μm)(图8)。对于实施例b2的结构而言,优选的是,应用于要求防滑性的用途,但不限于此。<实施例c2>(6)在氟树脂与玻璃纤维无缝织物的复合材料的两面上形成了氟橡胶表面层的多层无缝带与实施例a1同样地操作,得到氟树脂与玻璃纤维无缝织物的复合材料(厚度130μm)。在该复合材料的两面上,与实施例c1同样地操作,进行表面活化处理面及氟橡胶表面层的形成,得到在复合材料的两面上形成了氟橡胶表面层的多层无缝带(厚度170μm)(图9)。对于实施例c2的结构而言,优选的是,应用于要求防滑性的用途,但不限于此。<实施例a3>(7)在氟树脂与玻璃纤维无缝织物的复合材料的一面上形成了聚酰亚胺树脂表面层、在另一面上形成了硅橡胶表面层的多层无缝带与实施例a1同样地操作,得到氟树脂与玻璃纤维无缝织物的复合材料(厚度130μm)。在该复合材料的两面上,与实施例a1同样地操作,得到表面活化处理面。在该复合材料的一面上,与实施例a1同样地操作,形成聚酰亚胺树脂表面层,在另一面上,与实施例b1同样地操作,进行硅橡胶表面层的形成,得到在氟树脂与玻璃纤维无缝织物的复合材料的一面上形成了聚酰亚胺树脂表面层、在另一面上形成了硅橡胶表面层的多层无缝带(厚度200μm)(图10、图11)。对按照上述方式得到的实施例a3的多层片材的聚酰亚胺树脂面与硅橡胶层面进行比较。将评价结果示于表4。[表4]表4试验项目聚酰亚胺树脂层面硅橡胶层面磨耗量(mg)0.130.37动摩擦系数0.281.22接触角(°)95104根据前述的评价结果,硅橡胶与聚酰亚胺树脂相比,非粘合性优异,耐磨耗性、低摩擦性差。由该结果可知,硅橡胶与聚酰亚胺树脂相比,不易打滑。对于实施例a3的结构而言,优选的是,将硅橡胶面应用于要求非粘合性、防滑性的工件侧,将聚酰亚胺树脂面应用于要求耐磨耗性的工件非接触侧,但不限于此。<实施例a4>(8)在氟树脂与玻璃纤维无缝织物的复合材料的一面上形成了聚酰亚胺树脂表面层、在另一面上形成了氟橡胶表面层的多层无缝带与实施例a1同样地操作,得到氟树脂与玻璃纤维无缝织物的复合材料(厚度130μm)。在该复合材料的两面上,与实施例a1同样地操作,得到表面活化处理面。在该复合材料的一面上,与实施例a1同样地操作,形成聚酰亚胺树脂表面层,在另一面上,与实施例c1同样地操作,进行氟橡胶表面层的形成,得到在氟树脂与玻璃纤维无缝织物的复合材料的一面上形成了聚酰亚胺树脂表面层、在另一面上形成了氟橡胶表面层的多层无缝带(厚度155μm)(图12、图13)。对按照上述方式得到的实施例a4的多层片材的聚酰亚胺树脂面与氟橡胶层面进行比较。将评价结果示于表5。[表5]表5试验项目聚酰亚胺树脂层面氟橡胶层面磨耗量(mg)0.130.23动摩擦系数0.281.10接触角(°)9591根据前述的评价结果,氟橡胶与聚酰亚胺树脂相比,耐磨耗性、低摩擦性差。由该结果可知,氟橡胶与聚酰亚胺树脂相比,不易打滑。对于实施例a4的结构而言,优选的是,将氟橡胶面应用于要求防滑性的工件侧,将聚酰亚胺树脂面应用于要求耐磨耗性的工件非接触侧,但不限于此。<实施例a5>(8)在氟树脂与玻璃纤维无缝织物的复合材料的一面上形成了聚酰亚胺树脂表面层、在另一面上形成了硅橡胶和氟橡胶表面层的多层无缝带与实施例a1同样地操作,得到氟树脂与玻璃纤维无缝织物的复合材料(厚度130μm)。在该复合材料的两面上,与实施例a1同样地操作,得到表面活化处理面。在该复合材料的一面上,与实施例a1同样地操作,形成聚酰亚胺树脂表面层,在另一面上,与实施例b1同样地操作,进行硅橡胶表面层的形成,在该硅橡胶表面层上,与实施例c1同样地操作,进行氟橡胶表面层的形成,得到在氟树脂与玻璃纤维无缝织物的复合材料的一面上形成了聚酰亚胺树脂表面层、在另一面上形成了硅橡胶和氟橡胶表面层的多层无缝带(厚度220μm)(图14、图15)。对于实施例a5的结构而言,优选的是,将氟橡胶面应用于要求防滑性、不存在聚硅氧烷成分的迁移的工件侧、将聚酰亚胺树脂面应用于要求耐磨耗性的工件非接触侧,但不限于此。<实施例b4>(9)在氟树脂与玻璃纤维无缝织物的复合材料的一面上形成了硅橡胶和氟橡胶表面层的多层无缝带与实施例a1同样地操作,得到氟树脂与玻璃纤维无缝织物的复合材料(厚度130μm)。在该复合材料的一面上,与实施例a1同样地操作,得到表面活化处理面。在该复合材料的一面上,与实施例b1同样地操作,进行硅橡胶表面层的形成,在该硅橡胶表面层上,与实施例c1同样地操作,进行氟橡胶表面层的形成,得到在氟树脂与玻璃纤维无缝织物的复合材料的一面上形成了硅橡胶和氟橡胶表面层的多层无缝带(厚度215μm)(图16、图17)。对于实施例b4的结构而言,优选的是,将氟树脂面应用于要求非粘合性、低摩擦性的工件侧,将氟橡胶面应用于要求防滑性、不存在聚硅氧烷成分的迁移的工件非接触侧,但不限于此。<实施例b5>(10)在氟树脂与玻璃纤维无缝织物的复合材料的两面上形成了硅橡胶、且在一面上形成了氟橡胶表面层的多层无缝带与实施例a1同样地操作,得到氟树脂与玻璃纤维无缝织物的复合材料(厚度130μm)。在该复合材料的两面上,与实施例a1同样地操作,得到表面活化处理面。在该复合材料的两面上,与实施例b1同样地操作,进行硅橡胶表面层的形成,在该硅橡胶表面层的一面上,与实施例c1同样地操作,进行氟橡胶表面层的形成,得到在氟树脂与玻璃纤维无缝织物的复合材料的两面上形成了硅橡胶、且在一面上形成了氟橡胶表面层的多层无缝带(厚度280μm)(图18、图19)。对于实施例b5的结构而言,优选的是,将氟橡胶面应用于要求防滑性、不存在聚硅氧烷成分的迁移的工件接触侧、将硅橡胶面应用于更要求防滑性的工件非接触侧,但不限于此。<实施例b6>(11)在氟树脂与玻璃纤维无缝织物的复合材料的两面上形成了硅橡胶和氟橡胶表面层的多层无缝带与实施例a1同样地操作,得到氟树脂与玻璃纤维无缝织物的复合材料(厚度130μm)。在该复合材料的两面上,与实施例a1同样地操作,得到表面活化处理面。在该复合材料的两面上,与实施例b1同样地操作,进行硅橡胶层的形成,在该硅橡胶层表面的两面上,与实施例c1同样地操作,进行氟橡胶的形成,得到在氟树脂与玻璃纤维无缝织物的复合材料的两面上形成了硅橡胶和氟橡胶表面层的多层无缝带(厚度300μm)(图20)。对于实施例b6的结构而言,优选的是,应用于要求防滑性、不存在聚硅氧烷成分的迁移的用途,但不限于此。<实施例a6>(12)在玻璃纤维无缝织物的两面上形成了聚酰亚胺系树脂表面层的多层无缝带在玻璃纤维无缝织物的两面上,与实施例a1同样地操作,进行聚酰亚胺系树脂表面层的形成,得到在玻璃纤维无缝织物的两面上形成了聚酰亚胺系树脂表面层的多层无缝带(厚度130μm)(图21)。对于实施例a6的结构而言,优选的是,应用于要求耐磨耗性、防滑性的用途,但不限于此。<实施例b7>(13)在玻璃纤维无缝织物的两面上形成了硅橡胶层的多层无缝带在玻璃纤维无缝织物的两面上,与实施例b1同样地操作,进行硅橡胶表面层的形成,得到在玻璃纤维无缝织物的两面上形成了硅橡胶表面层的多层无缝带(厚度130μm)(图22)。对于实施例b7的结构而言,优选的是,应用于要求防滑性的用途,但不限于此。<实施例c4>(14)在玻璃纤维无缝织物的两面上形成了氟橡胶层的多层无缝带在玻璃纤维无缝织物的两面上,与实施例c1同样地操作,进行氟橡胶表面层的形成,得到在玻璃纤维无缝织物的两面上形成了氟橡胶表面层的多层无缝带(厚度130μm)(图23)。对于实施例c4的结构而言,优选的是,应用于要求防滑性的用途,但不限于此。<实施例b8>(15)在玻璃纤维无缝织物的复合材料的两面上形成了硅橡胶层、并且在一面上形成了氟橡胶层的多层无缝带在玻璃纤维无缝织物的两面上,与实施例b1同样地操作,进行硅橡胶表面层的形成,在该硅橡胶层的一面上,与实施例c1同样地操作,进行氟橡胶表面层的形成,得到在玻璃纤维无缝织物的两面上形成了硅橡胶层、并且在一面上形成了氟橡胶层的多层无缝带(厚度150μm)(图24、图25)。对于实施例b8的结构而言,优选的是,将氟橡胶面应用于要求防滑性、不存在聚硅氧烷成分的迁移的工件接触侧,将硅橡胶面应用于更重视防滑性的工件非接触侧,但不限于此。<实施例j1>(1)在玻璃纤维无缝织物的两面上形成了氟树脂表面层的多层无缝带在玻璃纤维无缝织物的两面上,与实施例a1同样地操作,进行氟树脂表面层的形成,得到在玻璃纤维无缝织物的两面上形成了氟树脂表面层的多层无缝带(厚度130μm)(图27)。对于实施例j1的结构而言,优选的是,应用于要求非粘合性、低摩擦性、不要求防滑性的用途,但不限于此。<实施例b9>(16)在玻璃纤维无缝织物的复合材料的两面上形成了硅橡胶层和氟橡胶层的多层无缝带在玻璃纤维无缝织物的两面上,与实施例b1同样地操作,进行硅橡胶表面层的形成,在该硅橡胶层的两面上,与实施例c1同样地操作,进行氟橡胶表面层的形成,得到在玻璃纤维无缝织物的两面上形成了硅橡胶层和氟橡胶层的多层无缝带(厚度170μm)(图26)。对于实施例b9的结构而言,优选的是,应用于要求防滑性、不存在聚硅氧烷成分的迁移的用途,但不限于此。<比较例a1>在实施例a1的复合材料上,不进行表面活化处理,涂布液状聚酰亚胺清漆,但未能接合,未能得到具有能进行使用的充分的接合强度的多层无缝带。<比较例b1>在实施例a1的复合材料上,不进行表面活化处理,涂布液状硅橡胶,但未能接合,未能得到具有能进行使用的充分的接合强度的多层无缝带。<比较例c1>在实施例a1的复合材料上,不进行表面活化处理,涂布液状氟橡胶,但未能接合,未能得到具有能进行使用的充分的接合强度的多层无缝带。<比较例a2>将在氟树脂与玻璃纤维织物的复合材料的一面上形成了聚酰亚胺树脂表面层的多层片材整面层叠接合而成的环形带首先,为了得到氟树脂与玻璃纤维的复合材料,将氟树脂(ptfe)的水性悬浮液含浸并附着于平纹组织的玻璃纤维布(厚度50μm),于80℃进行干燥,然后于380℃的温度进行烧成,得到氟树脂与玻璃纤维的复合材料(厚度80μm)。此外,为了得到层叠用的氟树脂与玻璃纤维的复合材料,将氟树脂(ptfe)的水性悬浮液含浸并附着于平纹组织的玻璃纤维布厚度(厚度30μm),于80℃进行干燥,然后于380℃的温度进行烧成,得到氟树脂与玻璃纤维的复合材料(厚度50μm)。接下来,为了对氟树脂与玻璃纤维的复合材料(厚度80μm)进行表面活化处理,在二氧化硅的水性悬浮液100质量份中混合ptfe树脂的水性悬浮液100质量份,得到表面活化处理液。接下来,将表面活化处理液涂布并附着于氟树脂与玻璃纤维的复合材料的一面,于80℃进行干燥,然后于380℃的温度进行烧成,使二氧化硅附着烧成,得到表面活化处理层面。接下来,为了得到液状聚酰亚胺清漆,在液状聚酰亚胺清漆100质量份中混合溶剂(二甲基乙酰胺(dmac))100质量份,得到粘度为50cp的液状聚酰亚胺清漆。接下来,将前述的液状聚酰亚胺清漆涂布并附着于前述的氟树脂与玻璃纤维的复合材料(厚度80μm)的表面活化处理面,于80℃进行干燥,然后于350℃的温度进行烧成,得到在氟树脂与玻璃纤维的复合材料的一面上形成了聚酰亚胺树脂表面层的多层片材(厚度85μm)。接下来,针对前述在氟树脂与玻璃纤维的复合材料的一面上形成了聚酰亚胺树脂表面层的多层片材(厚度85μm)和层叠用的氟树脂与玻璃纤维的复合材料(厚度50μm),以成为环形的方式,将氟树脂层面彼此全面层叠而进行重叠,利用加热加压机,于350℃的温度,将它们热熔粘,得到将在氟树脂与玻璃纤维织物的复合材料的一面上形成了聚酰亚胺树脂表面层的多层片材接合而成的环形带(厚度135μm)。<比较例b2>将在氟树脂与玻璃纤维织物的复合材料的一面上形成了硅橡胶表面层的多层片材整面层叠接合而成的环形带与比较例a1同样地操作,得到氟树脂与玻璃纤维的复合材料(厚度80μm)。进而,与比较例a1同样地操作,得到层叠用的氟树脂与玻璃纤维的复合材料(厚度50μm)。在前述复合材料(厚度80μm)的一面上,与比较例a1同样地操作,得到表面活化处理面。接下来,为了得到液状硅橡胶,在液状硅橡胶100质量份中混合有机溶剂(甲苯)10质量份,混合固化剂10质量份,得到粘度为50000cp的液状硅橡胶。接下来,将前述的液状硅橡胶涂布并附着于复合材料的表面活化处理面,于90℃的温度使其固化,进行硅橡胶表面层的形成,得到在复合材料的一面上形成了硅橡胶表面层的多层片材(厚度145μm)。接下来,将前述在氟树脂与玻璃纤维的复合材料的一面上形成了硅橡胶表面层的多层片材(厚度145μm)与层叠用的氟树脂与玻璃纤维的复合材料(厚度50μm)层叠,以成为环形的方式,将氟树脂层面彼此全面层叠而进行重叠,利用加热加压机,于350℃的温度,将它们热熔粘,得到将在氟树脂与玻璃纤维织物的复合材料的一面上形成了硅橡胶表面层的多层片材接合而成的环形带(厚度195μm)。<比较例c2>将在氟树脂与玻璃纤维织物的复合材料的一面上形成了氟橡胶表面层的多层片材全面层叠而成的环形带与比较例a1同样地操作,得到氟树脂与玻璃纤维的复合材料(厚度80μm)。此外,与比较例a1同样地操作,得到层叠用的氟树脂与玻璃纤维的复合材料(厚度50μm)。在前述复合材料(厚度80μm)的一面上,与比较例a1同样地操作,得到表面活化处理面。接下来,为了得到液状氟橡胶,在液状氟橡胶100质量份中混合有机溶剂(mek)10质量份,混合固化剂10质量份,得到粘度为1000cp的液状氟橡胶。接下来,将前述的液状氟橡胶涂布并附着于复合材料的表面活化处理面,于90℃的温度使其固化,进行氟橡胶表面层的形成,得到在复合材料的一面上形成了氟橡胶表面层的多层片材(厚度100μm)。接下来,针对前述在氟树脂与玻璃纤维的复合材料的一面上形成了氟橡胶表面层的多层片材(厚度100μm)和层叠用的氟树脂与玻璃纤维的复合材料(厚度50μm),以成为环形的方式,将氟树脂层面彼此重叠,利用加热加压机,于350℃的温度,将它们热熔粘,得到将在氟树脂与玻璃纤维织物的复合材料的一面上形成了氟橡胶表面层的多层片材接合而成的环形带(厚度150μm)。<比较例a3>将在氟树脂与玻璃纤维织物的复合材料的一面上形成了聚酰亚胺树脂表面层的多层片材整面层叠接合而成的环形带(厚度265μm)与比较例a2同样地操作,得到氟树脂与玻璃纤维的复合材料(厚度130μm)。此外,与比较例a2同样地操作,得到层叠用的氟树脂与玻璃纤维的复合材料(厚度130μm)。接下来,与比较例a2同样地操作,进行表面活化处理面及聚酰亚胺树脂表面层的形成,得到在氟树脂与玻璃纤维的复合材料的一面上形成了聚酰亚胺树脂表面层的多层片材(厚度135μm)。接下来,与比较例a2同样地操作,针对前述在氟树脂与玻璃纤维的复合材料的一面上形成了聚酰亚胺树脂表面层的多层片材(厚度135μm)和层叠用的氟树脂与玻璃纤维的复合材料(厚度130μm),以成为环形的方式,将氟树脂层面彼此全面层叠而进行重叠,进行热熔粘,得到将在氟树脂与玻璃纤维织物的复合材料的一面上形成了聚酰亚胺树脂表面层的多层片材接合而成的环形带(厚度265μm)。<比较例a4>将在氟树脂与玻璃纤维织物的复合材料的一面上形成了聚酰亚胺树脂表面层的多层片材进行端部叠合接合而成的环形带与比较例a2同样地操作,得到氟树脂与玻璃纤维的复合材料(厚度130μm)。接下来,与比较例a2同样地操作,进行表面活化处理面及聚酰亚胺树脂表面层的形成,得到在氟树脂与玻璃纤维的复合材料的一面上形成了聚酰亚胺树脂表面层的多层片材(厚度135μm)。接下来,将前述在氟树脂与玻璃纤维的复合材料的一面上形成了聚酰亚胺树脂表面层的多层片材(厚度135μm)的一个端部的聚酰亚胺树脂表面层和表面活化处理面刮掉,使氟树脂层面露出。针对前述一个端部与另一个端部,以成为环形的方式,将氟树脂层面彼此重叠,进行热熔粘,得到将在氟树脂与玻璃纤维织物的复合材料的一面上形成了聚酰亚胺树脂表面层的多层片材进行端部叠合接合而成的环形带(接合部的厚度为265μm,1片部的厚度为135μm)。<实施例d1~d5>实施例a1~a5中,代替二氧化硅附着烧成处理,进行金属钠蚀刻处理,由此形成表面活化处理面,除此之外,与实施例a1~a5同样地操作,得到本发明的多层无缝带d1~d5。<实施例e1、e2、e4~e6>实施例b1、b2、b4~b6中,代替二氧化硅附着烧成处理,进行金属钠蚀刻处理,由此形成表面活化处理面,除此之外,与实施例b1~b6同样地操作,得到本发明的多层无缝带e1、e2、e4~e6。<实施例f1、f2>实施例c1、c2中,代替二氧化硅附着烧成处理,进行金属钠蚀刻处理,由此形成表面活化处理面,除此之外,与实施例c1~c3同样地操作,得到本发明的多层无缝带f1、f2。<实施例g1~g5>实施例a1~a5中,代替二氧化硅附着烧成处理,进行等离子体处理,由此形成表面活化处理面,除此之外,与实施例a1~a5同样地操作,得到本发明的多层无缝带g1~g5。<实施例h1、h2、h4~h6>实施例b1、b2、b4~b6中,代替二氧化硅附着烧成处理,进行等离子体处理,由此形成表面活化处理面,除此之外,与实施例b1、b2、b4~b6同样地操作,得到本发明的多层无缝带h1、h2、h4~h6。<实施例i1、i2>实施例c1、c2中,代替二氧化硅附着烧成处理,进行等离子体处理,由此形成表面活化处理面,除此之外,与实施例c1、c2同样地操作,得到本发明的多层无缝带i1、i2。后述的表6中,将前述的各实施例及比较例的带的周长、宽度、厚度一并示出。[表6]表6并非是前述实施例中的全部,可在周长为30~5000mm、宽度为4~1500mm的范围内实施。对于各层的厚度而言,可在下述范围内实施:包含耐热性纤维的无缝带基材的厚度为30~1000μm,在表面层为氟树脂层的情况下,其厚度为1~300μm,在表面层为聚酰亚胺系树脂层的情况下,其厚度为1~300μm,在表面层为硅橡胶的情况下,其厚度为1~700μm,在表面层为氟橡胶的情况下,其厚度为1~700μm的范围内。复合强度试验作为实施例的代表例,针对通过前述的实施例a1、b1、c1、d1、e1、f1、g1、h1、i1、比较例a1、b1、c1而得到的各多层无缝带以及多层片材的聚酰亚胺表面层或硅橡胶表面层或氟橡胶层,按照jish5400,实施棋盘格试验(1mm×100升)。将评价结果示于表7。从形成了表面活化处理面的多层无缝带剥离的方格的数目在所有的多层片材中均为0个。另一方面,对于未形成表面活化处理面的比较例a1、b1、c1而言,剥离的方格的数目为100个。[表7]表7剥离的方格的数目实施例a10实施例b10实施例c10比较例a1100比较例b1100比较例c1100实施例d10实施例e10实施例f10实施例g10实施例h10实施例i10拉伸强度试验作为实施例的代表例,针对将通过前述的实施例a1、比较例a2、a3、a4而得到的各多层无缝带以及多层片材接合而成的环形带,按照jisk7137-2,实施拉伸强度试验。将评价结果示于表8。对于比较例a2而言,层叠接合部的复合材料层从1个接缝断裂,总厚度与实施例a1相同,结果强度差。对于比较例a3而言,层叠接合部的复合材料层也从1个接缝断裂,与实施例a1的厚度差接近一倍,结果强度为同等程度。[表8]表8导热性试验作为实施例的代表例,针对将通过前述的实施例a1、比较例a4而得到的各多层无缝带以及多层片材接合而成的环形带,利用后述的评价方法进行比较。将评价结果示于表9。对于厚度厚且为同等程度的比较例a3与比较例a4(接合部)而言,导热性为同等程度,较差,对于厚度薄且为同等程度的实施例a1与比较例a4(未接合部)而言,导热性为同等程度,是优异的。对于比较例a4而言,接合部与未接合部由于厚度差而导致热传导差大。[表9]表9加压10秒后实施例a1147比较例a3129比较例a4(接合部)129比较例a4(未接合部)147导热性试验:将试样设置于上侧加热工具、下侧导热体的加压机的下侧导热体上,在加热工具温度为200℃、压力为1mpa的条件下进行10秒加热及加压,对传递至导热体的温度进行比较。柔软性试验作为实施例的代表例,针对将通过前述的实施例a1、比较例a3而得到的各多层无缝带以及多层片材接合而成的环形带,按照jisr3420,实施挠曲试验。挠曲长度越短,柔软性越优异。将评价结果示于表10。[表10]表10挠曲长度(mm)实施例a120mm比较例a372mm根据以上的评价结果,本发明的多层无缝带与以往的将多层片材接合而成的环形带相比,由于没有接合部,因而不存在从接合部起始的断裂,厚度均匀,而且能使厚度变薄,在同等程度的厚度时,强度强,导热性、柔软性优异,在条件变动、使用温度的降低以及对辊的亲和性方面提高,即使是辊轮直径(pulleydiameter)小的辊也能应对。由此,可提供强度耐久性也优异、而且非粘合性、耐磨耗性、防滑性优异的传送及加热处理带。附图标记说明11、12、13、14、15、16、17、18、19、20、21、22、23、24、25、26、27,28、29、30、31、32、33、34、35、36、37多层片材2复合材料层2a氟树脂2b包含耐热性纤维的无缝带基材3a由聚酰亚胺系树脂形成的表面层3b由硅橡胶形成的表面层3c由氟橡胶形成的表面层4处理面当前第1页12