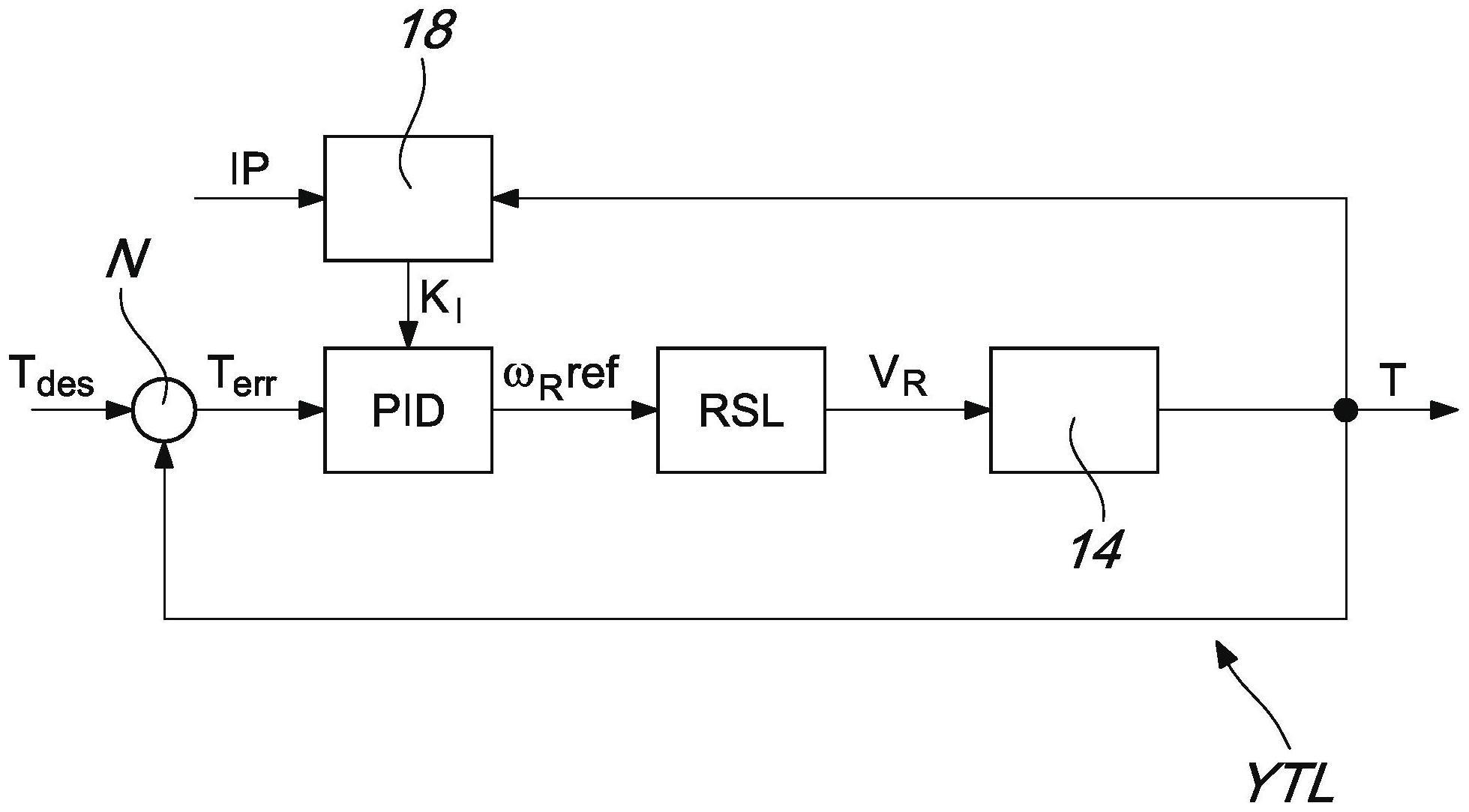
用于控制机动化积极式纱线供给器的纱线张力的方法
1.本发明涉及用于控制机动化积极式纱线供给器(motorized positive yarn feeder)的纱线张力的方法。
2.众所周知,在一般的织造工艺中,纱线可以通过称为“积极”型的机动化纱线供给器被供给向下游的纺织机,例如特别是针织机。
3.这种类型的供给器设置有机动化卷轴(reel),纱线被反复缠绕在该卷轴上(例如,3圈或4圈),使得纱线通过摩擦附着到卷轴上。通过转动卷轴,纱线从上游的线轴展开,并被供给到下游的针织机。
4.在工作期间,控制单元基于从张力传感器接收的信号通过闭环调制卷轴的旋转速率,以便将供给到针织机的纱线的张力稳定在由用户设定的曲线(profile)或固定值。
5.影响纱线张力最大的因素之一是纱线从供给器离开的速度与被针织机抽拉的速度之间的差。
6.因此,为了提高控制回路的性能,对于某些应用,已知在工作期间将针织机的速度信息传输到供给器。
7.影响纱线张力的其他因素还有纱线的刚度以及供给器与针织机之间的距离。
8.因此,再次为了提高控制回路的性能,在一些情况下,控制单元使得可以根据纱线的类型并间接地根据供给器和针织机之间的距离手动选择一些调节参数。
9.用于优化控制回路性能的上述解决方案使线路设置相当复杂,因为它们需要手动输入关于所有供给器的操作参数和/或以电子方式将针织机连接到供给器以便传输速度信息。此外,这最后一种解决方案并不总是可行的,因为许多针织机,特别是那些仍在广泛使用的较新的针织机,没有配备在外部传输速度信号的设备。
10.因此,本发明的目的在于提供以下方法,该方法使得可以以比已知解决方案更精确且更可靠的方式控制纱线的张力,在工作期间自动优化与所涉及的各种因素(特别是纱线的类型、针织机的速度变化以及供给器与针织机之间的距离)有关的性能。
11.通过继续描述将变得更加明显的该目的以及这些和其它目标通过具有权利要求1中所描述特征的调整纱线张力的方法来实现,而从属权利要求限定本发明的其他有利的、尽管是次要的特征。
附图说明
12.现在将参考本发明的优选但非排他的实施例更详细地描述本发明,这些实施例在附图中通过非限制性示例示出,其中:
13.图1是将纱线供给到针织机的机动化积极式纱线供给器的示意图;
14.图2是根据本发明的方法的框图视图;
15.图3是描绘了根据本发明的方法中一些过程参数变化的影响的组合图;
16.图4是普通针织机的纱线抽拉速度分布曲线的示例图表。
17.图1是将纱线y供给到纺织机,特别是针织机km的机动化积极式纱线供给器10的示意图。
18.供给器10包括机动化卷轴12,纱线y被反复缠绕在该卷轴上(例如,3圈或4圈),使得纱线通过摩擦附着到卷轴上。通过转动卷轴12,纱线y从上游的线轴s上展开,并被供给到下游的针织机km。
19.可以集成到供给器10中的控制单元cu被连接以基于从张力传感器14(也可选地集成在供给器10中)接收到的信号通过闭环调节卷轴12的旋转速度,以便将供给到机器的纱线的张力稳定在固定值或由用户设置的曲线上。
20.供给器10还设置有用于测量卷轴12的角速度ωr的装置(未示出),该装置通常可以包括编码器、一系列霍尔传感器或其他类似的已知设备。
21.如本领域技术人员将容易理解的,纱线y的释放速度vr可以假定为等于卷轴12的角速度ωr与卷轴12的半径的乘积。
22.供给器10被布置在距针织机km的距离l处,针织机km以抽拉速度v
km
抽拉纱线。关于本发明,距离l和抽拉速度v
km
假定为未知的,纱线y的机械特性(特别是刚度)也是未知的。
23.众所周知,抽拉速度v
km
例如在提供设计期间可以在很大范围内变化。闭环控制系统的目的在于限制由于针织机的抽拉速度v
km
的所述变化而引起的纱线y的张力变化。
24.图2示出了闭环控制系统的架构。
25.以本身已知的方式,控制系统通常包括纱线张力控制回路ytl、卷轴速度控制回路rsl和穿过电动机(未示出)的电流的控制回路,该电流的控制回路被包含在速度控制回路rsl内。
26.优选地,速度控制回路rsl和电流控制回路借助于恒定参数线性调节器以常规方式进行控制,以便在输入端接收参考角速度ωrref并在输出端返回释放速度vr。如前所述,释放速度vr和抽拉速度v
km
之间的差生成纱线y上的张力t。张力t由张力传感器14测量,并与张力控制回路ytl的减法器节点n中的期望张力tdes进行比较,从而生成张力误差terr。期望张力tdes可以具有恒定值或可随时间变化的曲线。
27.根据本发明,参考角速度ωrref由比例-积分-微分调节器pid生成,该pid在输入端接收张力误差terr,并具有积分常数ki,该积分常数ki不是常数而是通过自校准程序18迭代地更新,该自校准程序18适于最小化由张力传感器14生成的信号的性能指数(或成本函数)。
28.在下面描述的优选实施例中,张力信号的方差用作性能指数。
29.优选地,自校准程序包括以下步骤:
[0030]-通过应用当前的积分常数ki对张力信号t的预设数量n的样本计算方差v(ki),
[0031]-借助于黑盒优化算法选择新的积分常数ki',
[0032]-如果新的积分常数ki'落在预定的最小保护值k
imin
和最大保护值k
imax
之间所包含的间隔内,则使用新的积分常数ki'重复该程序,否则使用当前的积分常数ki重复该程序。
[0033]
根据本发明的目的和目标,在实践中还发现,具有以上述方式迭代更新的积分常数的比例-积分-微分调节器pid具有以下效果:使由针织机的速度变化引起的张力峰值的幅度最小化,同时避免张力信号的过多振荡(excessive oscillations)。
[0034]
如本领域技术人员容易理解的,这两个目的通常是冲突的,因为“积极的”或“快速的”调整需要张力峰值的快速减小,但由于张力测量噪声而可能导致稳态振荡。反之亦然,“稳健的”或“缓慢的”调整会产生更规则的张力信号走向,但峰值幅度高。
[0035]
实验还发现,在上述自校准程序中,张力信号的样本方差是与上述目的有关的系统性能的可靠指标。
[0036]
由于方差是在预定的时间间隔内计算的,因此所述的自校准程序在这里描述的系统中特别有效,因为众所周知,针织机通常具有周期性的速度曲线,因此使得用不同的连续积分常数获得的方差之间的比较具有重要意义。
[0037]
与此相关,在具有比针织机的周期更长持续时间的时间间隔内计算方差是合适的。
[0038]
为了补偿不正确间隔的使用并考虑电压信号的噪声,在结构性变化中,可以考虑张力信号在预设数量的连续间隔m上的平均方差e[var(ki)]作为性能指数,而不是方差的点值var(ki)。
[0039]
图3示出了针对某一工作点的中间纱线、平均方差e[var(ki)]随着积分常数ki变化的走向的示例,以及张力t的和释放速度vr在所考虑的域部分内的积分常数的最小值k
imin
和最大值k
imax
处的走向,以及使平均方差e[var(ki)]最小化的值。
[0040]
图4中示出了生成图3的图的针织机km的抽拉速度v
km
的走向。
[0041]
显然,使上述项中的性能最大化的积分常数ki的校准是使张力信号的平均方差e[var(ki)]最小化的校准。
[0042]
最小保护值k
imin
和最大保护值k
imax
基于可以由控制单元cu表示的阈值来定义,还考虑到积分常数ki能够假设只为负值,以防止系统变得不稳定。
[0043]
为了更清楚和简单的阐述,下文将再次参考方差var(ki),而不是平均方差e[var(ki)],尽管如前所述,优选地使用平均方差e[var(ki)],因为它更可靠。
[0044]
如本领域技术人员所熟知的,用于最小化未知的(意味着在这种情况下,积分常数ki的校准和张力信号t的方差var(ki)之间的数学关系是未知的)性能指数(在特定情况下是方差var(ki))的传统黑盒优化算法具有特别是如下的一些缺点:
[0045]-它们计算成本高,因此难以在微控制器上实现;
[0046]-它们通常不会对积分常数ki在一次迭代和下一次迭代之间的变化范围提供保护限制,在工作期间比例积分微分调节器pid的校准有突然变化的风险,这转过来可能产生相当大的瞬变,从而导致纱线断裂;
[0047]-它们被设计成使用比方差var(ki)更复杂的成本函数来解决优化问题,方差var(ki)通常是一个适合采用较简单算法的函数。
[0048]
出于这个原因,优选地,在根据本发明的方法中使用的黑盒优化算法提供:
[0049]-执行第一测试,该第一测试可以被定义为“被动的”,并且其中张力控制回路tl在预定的时间间隔内以固定的当前的积分常数ki工作,然后计算在该时间间隔中张力信号的方差,
[0050]-根据以下公式计算积分常数ki的最小步长δki[0051][0052]
其中,γ
minstep
是通过实验确定的最小步长系数,通常被包括在5到50之间,
[0053]-执行第二被动测试,其中张力控制回路tl在相同时间间隔内以等于ki+δki的增加的积分常数工作,然后对该时间间隔中张力信号t的预设数量n的样本计算方差,
[0054]-执行第三被动测试,其中张力控制回路tl在相同时间间隔内以等于k
i-δki的减小的积分常数工作,然后对该时间间隔中张力信号t的预设数量n的样本计算方差。
[0055]
被动测试由闭环执行,而不会中断张力调整。
[0056]
有利地,在这一点上,可以使用牛顿算法的修改版本,其利用二次模型近似某一点处的成本函数,并选择将该简化模型的一阶导数降为零的点作为下一个待测试点。二阶导数必须为正且不为零,以便具有二次模型的最小值,否则就有必要应用保障措施。特别地,如果二阶导数等于零,就不可能计算下降方向,而如果二阶导数为负,则下降方向将导致局部最大值。
[0057]
更详细地,一阶导数和二阶导数例如可以通过所谓的中心差分公式来计算:
[0058][0059][0060]
基于一阶导数和二阶导数,算法计算移动方向p,检查v(ki+δki)-v(ki)或v(k
i-δki)-v(ki)中的一个是否会返回小于0的结果。在第一种情况下,在图3的图中,该值位于方差的最小值的左边,因此,用足够短的“正”步长就有可能接近最小值;在第二种情况下,该值在方差的最小值的右边,并且用足够短的“负”步长就有可能接近最小值。
[0061]
如果两个差中的一个给出小于0的结果,则应用保护检查,然后选择步长α的长度(extend),以改善方差,并且根据公式ki'=ki+αp将新的积分常数ki'应用于张力控制回路ytl。
[0062]
例如,在二阶导数为正的情况下,移动方向p由一阶导数与二阶导数之间的负比给定(牛顿方向)。
[0063]
步长α的长度可以通过称为线搜索的程序获得。特别地,如果使用牛顿方向,可以简单地执行所谓的回溯线搜索,其中从α=1开始,并针对ki+p检查方差是否有所改善。如果没有改善,则针对预定数量的步长通过将α减半重复检查,并以此类推。
[0064]
如果两个差均未得出小于0的结果,则使用相同的积分常数ki重复该程序而不执行任何步长。在没有测量噪声的理想条件下,这意味着方差已经非常接近最小值,因此任何方向上的步长都将提供更差的结果。在存在噪声(或由于数值精度问题)的情况下,该程序可能无法导出移动方向。在这种情况下,重复优化步骤,即针对方差的三个测试。
[0065]
有利地,为了避免过度突然的转变,除了已经提到的关于ki值(其必须被包含在最小值k
imin
和最大值k
imax
之间)的保护标准之外,还根据下式应用附加的保护标准:
[0066]
δki≤α|p|≤δki[0067]
其中
[0068][0069]
γ
maxstep
是通过实验确定的最大步长系数,该系统通常可以被包括在1到5之间。
[0070]
如本领域技术人员可以认识到的,算法在工作期间从不中断。一旦达到了保证最小方差的ki校准,则算法围绕它振荡,从而提供真正的自适应控制:如果工作条件发生变化
(纱线的变化、针织机的速度曲线的变化、供给器与针织机之间距离的变化),则程序恢复对最小值的搜索。
[0071]
可以基于实验测试来确定起始积分系数k、在计算方差时要使用的样本数量n(给定采样率,这相当于定义要考虑的时间间隔)、计算平均方差的间隔数量m、以及用于分别计算最小步长γ
minstep
和最大步长γ
maxstep
的系数。
[0072]
作为可替代方案,关于起始积分系数ki,可以在受控条件下(即,使用已知纱线、针织机速度曲线以及供给器与针织机之间的距离)执行根据本发明的程序的预设数量的迭代,以便获得少量纱线类型的初始校准。这些初始校准可以用作工作期间的起始点,以便加快向方差最小值v(ki)的收敛。
[0073]
优选地,可以增量地执行方差计算,以避免对存储数量为n的多个样本的需要,从而限制执行自校准程序所需的存储器容量。
[0074]
优选地,比例-积分-微分调节器的pid的积分部分的时间常数ti和微分部分的时间常数td保持恒定,并从速度控制回路的估计模型开始校准。
[0075]
优选地,卷轴速度控制回路rsl包括用于估计电机的角旋转速率的卡尔曼滤波器,该角旋转速率的估计从角位置的测量开始执行。如前所述,该估计可以有利地由比例积分控制器利用,以便控制卷轴的角速度ωr。
[0076]
在实践中,已经发现卡尔曼滤波器允许改善速度控制回路rsl的性能,并相应地改善整个调节程序的性能,这简化了张力调节回路ytl的实现。
[0077]
虽然已经描述了本发明的一些优选实施例,但是本领域技术人员将能够自然地在权利要求的范围内进行各种修改和变型。
[0078]
特别地,方差(或平均方差)已被用作性能指数。然而,如本领域技术人员将容易理解的,将可以使用从测量值(如在方差的情况下)或从误差(设定点和测量值之间的差)直接计算的其他性能指数。可替代的性能指数的一些示例是均方误差(mse)、均方根误差(rmse)或积分性能指数(如积分平方误差(ise)、积分绝对误差(iae)、时间加权绝对误差的积分(itae)、或甚至时间加权平方误差的积分(itse))。
[0079]
其他可能的性能指数是上述定义的标准化版本或各种组合。每个性能指数基本上定义了峰值抑制和振荡之间的不同权衡,并且必须在一定的测量周期内计算。
[0080]
以上所引用的性能指数均以“零”为理想最小值。