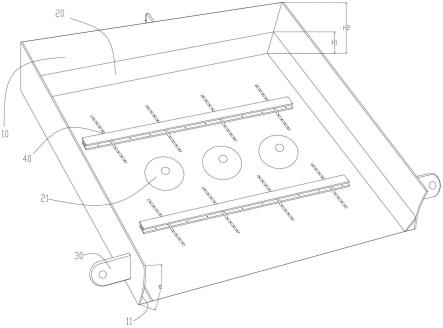
1.本实用新型涉及铁合金铁水浇铸技术领域,尤其涉及一种长寿命硅锰合金浇铸块料转运装置。
背景技术:2.浇注成型冷却后形成的硅锰合金坯料,质量重,温度较高,边缘处存在尖锐或弧状凸起,通过转运盘在吊运过程中,易对转运盘底面造成冲击,而转运盘底面缺少刚性支撑,常引起转运盘底面中间位置出现大面积变形,使用时间较长后,还有出现破损、穿孔等状况,大幅降低转运盘使用寿命。
技术实现要素:3.有鉴于此,针对上述不足,有必要提出一种长寿命硅锰合金浇铸块料转运装置。
4.一种长寿命硅锰合金浇铸块料转运装置,包括簸箕状外壳体、簸箕状内壳体、吊耳、防滑机构,所述簸箕状内壳体固定设置于簸箕状外壳体内壁上,所述吊耳设置有三组,分别设置于簸箕状外壳体三侧外壁上,所述防滑机构在簸箕状内壳体上表面设置有若干组,所述防滑机构包括工字钢、固定杆、第一螺栓螺母组件,所述工字钢设置于簸箕状内壳体上表面,所述固定杆一端设置于工字钢一侧,所述固定杆另一端穿过工字钢预设通孔并延伸至工字钢另一侧,所述第一螺栓螺母组件一端设置于固定杆上表面,所述第一螺栓螺母组件另一端穿过固定杆预设通孔、簸箕状内壳体预设通孔、簸箕状外壳体预设通孔并延伸至簸箕状外壳体下表面。
5.优选的,所述簸箕状内壳体高度为簸箕状外壳体高度的1/5~4/5。
6.优选的,所述簸箕状外壳体靠近敞口的端部两侧还分别设置有弧面,所述弧面角度为15~45
°
。
7.优选的,所述固定杆设置数量为所述工字钢设置数量的2倍以上,所述第一螺栓螺母组件设置数量为所述固定杆设置数量的4倍以上。
8.优选的,所述工字钢两侧凹槽上表面还设置有若干组第二螺栓螺母组件,所述第二螺栓螺母组件一端设置于工字钢凹槽上表面,所述第二螺栓螺母组件另一端穿过工字钢预设通孔、簸箕状内壳体预设通孔、簸箕状外壳体预设通孔并延伸至簸箕状外壳体下表面。
9.优选的,所述簸箕状内壳体上表面还设置有若干组加强凸台,所述加强凸台位于相邻防滑机构两侧的4个固定杆之间,所述加强凸台上窄下宽,横截面呈圆形。
10.由上述技术方案可知,本实用新型提供了一种长寿命硅锰合金浇铸块料转运装置,其有益效果是:采用簸箕状外壳体、簸箕状内壳体双层壳体,提升转运装置整体的结构强度,在簸箕状内壳体上表面设置若干组防滑机构,通过横向设置的工字钢、纵向设置的固定杆,以将硅锰合金重力及冲击外力均匀分散到簸箕状内壳体上表面各处,有效防止簸箕状内壳体上表面出现局部受力过大情况发生,显著提升其使用寿命,同时还在簸箕状内壳体上表面设置若干组加强凸台,大幅减少簸箕状内壳体上表面局部区域出现变形、破碎情
况,并防止硅锰合金坯料在簸箕状内壳体上表面出现滑动。本装置通用性强,上料、吊运、下料方便可靠,转运效率高,使用寿命大幅提升。
附图说明
11.图1为长寿命硅锰合金浇铸块料转运装置的结构示意图。
12.图2为图1中簸箕状内壳体、簸箕状外壳体的局部放大示意图。
13.图3为图1中弧面的局部放大示意图。
14.图4为图1中防滑机构的局部放大示意图。
15.图中:簸箕状外壳体10、弧面11、簸箕状内壳体20、加强凸台21、吊耳30、防滑机构40、工字钢41、第二螺栓螺母组件411、固定杆42、第一螺栓螺母组件43。
具体实施方式
16.为了更清楚地说明本实用新型实施例的技术方案,下面将对实施例中所需要使用的附图作简单的介绍,显而易见地,下面描述中的附图是本实用新型的一些实施例,对于本领域普通技术人员来讲,在不付出创造性劳动的前提下,还可以根据这些附图获得其它的附图。
17.参见图1至图4,本实用新型提供了一种长寿命硅锰合金浇铸块料转运装置,包括簸箕状外壳体10、簸箕状内壳体20、吊耳30、防滑机构40,所述簸箕状内壳体20固定设置于簸箕状外壳体10内壁上,所述固定方式为焊接,所述吊耳30设置有三组,分别设置于簸箕状外壳体10三侧外壁上,所述防滑机构40在簸箕状内壳体20上表面设置有若干组,所述防滑机构40包括工字钢41、固定杆42、第一螺栓螺母组件43,所述工字钢41设置于簸箕状内壳体20上表面,所述固定杆42一端设置于工字钢41一侧,所述固定杆42中间位置呈“几”字型,以便于从工字钢41预设通孔中穿过,所述固定杆42另一端穿过工字钢41预设通孔并延伸至工字钢41另一侧,所述第一螺栓螺母组件43一端设置于固定杆42上表面,所述第一螺栓螺母组件43另一端穿过固定杆42预设通孔、簸箕状内壳体20预设通孔、簸箕状外壳体10预设通孔并延伸至簸箕状外壳体10下表面,以将固定杆42固定于工字钢41及簸箕状内壳体20上表面。
18.具体的,所述簸箕状外壳体10三侧外壁上分别设置有三组吊耳30,其中一组吊耳30设置于簸箕状外壳体10远离敞口一侧的中间位置,剩余两组相对设置于簸箕状外壳体10靠近敞口的两侧侧壁上,三组吊耳30通过外部挂钩相连后,重心位于转运装置的中心位置,以有效减少天车及挂钩在对转运装置吊运过程中的中心偏移现象。
19.具体的,通常采用焊接方式,将工字钢41固定于簸箕状内壳体20上表面,所述工字钢41固定方向与簸箕状内壳体20宽度方向平行,以将受到的硅锰合金重力及冲击外力均匀分散到簸箕状内壳体20宽度方向上表面上,所述工字钢41呈“工”字型结构,可以有效卡住硅锰合金坯料,防止硅锰合金坯料在簸箕状内壳体20上表面移动;所述固定杆42设置于工字钢41两侧,设置方向与工字钢41设置方向垂直,且设置数量较多,以将受到的硅锰合金重力及冲击外力均匀分散到簸箕状内壳体20长度方向上表面上;通过上述方式,将硅锰合金重力及冲击外力均匀分散到簸箕状内壳体20上表面各处,有效防止簸箕状内壳体20上表面出现局部受力过大而引起的变形、破损、穿孔等情况,显著提升其使用寿命。
20.参见图2,进一步,所述簸箕状内壳体20高度h1为簸箕状外壳体10高度h2的1/5~4/5,所述簸箕状内壳体20焊接于簸箕状外壳体10上表面及其三侧内壁上,以提升转运装置整体的结构强度,所述簸箕状内壳体20高度h1较簸箕状外壳体10高度小,一方面确保转运装置侧壁结构强度满足使用要求,另一方面降低其加工成本。
21.参见图3,进一步,所述簸箕状外壳体10靠近敞口的端部两侧还分别设置有弧面11,所述弧面11角度α为15~45
°
,以使簸箕状内壳体20中硅锰合金坯料掉落的渣料、块料优先从弧面11处滑落,同时有利于提升尖锐或弧状凸起硅锰合金坯料的通过性。
22.进一步,所述固定杆42设置数量为所述工字钢41设置数量的2倍以上,所述第一螺栓螺母组件43设置数量为所述固定杆42设置数量的4倍以上,以使簸箕状内壳体20上表面固定设置有足量的工字钢41、固定杆42,确保硅锰合金重力及冲击外力均匀分散到簸箕状内壳体20上表面各处。
23.进一步,所述工字钢41两侧凹槽上表面还设置有若干组第二螺栓螺母组件411,所述第二螺栓螺母组件411一端设置于工字钢41凹槽上表面,所述第二螺栓螺母组件411另一端穿过工字钢41预设通孔、簸箕状内壳体20预设通孔、簸箕状外壳体10预设通孔并延伸至簸箕状外壳体10下表面,以将工字钢41牢固设置于簸箕状内壳体20上表面。
24.具体的,通常工字钢41在簸箕状内壳体20上的固定方式为焊接,由于硅锰合金坯料自身质量大,尖锐及弧状凸起多,易使焊接点破裂,从而造成工字钢41发生移动,甚至掉落等情况发生。优选的,本方案在原工字钢41焊接于簸箕状内壳体20的基础上,在工字钢41两侧凹槽上表面还设置有若干组第二螺栓螺母组件411,显著提升工字钢41固定的牢固性,避免工字钢41与簸箕状内壳体20之间出现相对移动。
25.进一步,所述簸箕状内壳体20上表面还设置有若干组加强凸台21,所述加强凸台21位于相邻防滑机构40两侧的4个固定杆42之间,所述加强凸台21上窄下宽,横截面呈圆形。
26.具体的,相邻防滑机构40两侧的4个固定杆42之间的区域受力大,是最易出现大面积变形甚至破损、穿孔的区域,本方案在上述区域的簸箕状内壳体20上表面设置若干组加强凸台21,该加强凸台21为刚性件,上窄下宽,可减少硅锰合金坯料对该区域的作用力,大幅减少变形、破碎情况发生,同时这些凸台还与其两侧的工字钢41、固定杆42之间形成大量凸凹面,有利于提升硅锰合金坯料在簸箕状内壳体20上表面上堆放的稳定性,防止硅锰合金坯料在簸箕状内壳体20上表面出现滑动。
27.本实用新型实施例装置中的模块或单元可以根据实际需要进行合并、划分和删减。
28.以上所揭露的仅为本实用新型较佳实施例而已,当然不能以此来限定本实用新型之权利范围,本领域普通技术人员可以理解实现上述实施例的全部或部分流程,并依本实用新型权利要求所作的等同变化,仍属于实用新型所涵盖的范围。