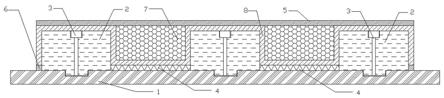
1.本发明涉及夹层结构复合材料技术领域,具体的说是格栅增强泡沫夹芯复合材料成型用预成型体及其成型方法。
背景技术:2.传统泡沫夹芯复合材料由强度、模量较大的上下复合材料面板和介于上下面板之间的低密度泡沫夹芯材料复合而成,具有较高的比强度、比刚度;同时,低密度泡沫夹芯材料具有防火、隔热、隔声、吸能等功能。因此,传统泡沫夹芯复合材料成为一种典型结构功能一体化材料,已广泛应用于轨道交通、高速列车、航空航天、船舶与海洋工程等领域。但是,随着工程应用对结构性能要求不断提高,传统泡沫夹芯复合材料已经无法满足需求。因此,现有技术中已经尝试将复合材料格栅结构引入到传统泡沫夹芯复合材料的泡沫夹芯材料中,以构建一种新型夹层结构复合材料——格栅增强泡沫夹芯复合材料。这种材料的主体部分为传统泡沫夹芯复合材料,增强部分为复合材料格栅结构。格栅增强泡沫夹芯复合材料集成了传统泡沫夹芯复合材料和复合材料格栅结构的各自优势,既保留了传统泡沫夹芯复合材料较低密度、较高强度、较高模量等优点,又发挥了复合材料格栅结构出色的力学性能。即:在整体密度略微增加的前提下,格栅增强泡沫夹芯复合材料的平压、侧压、弯曲、剪切等力学性能显著提升,尤其是侧压性能,成倍数级增加。
3.在这种格栅增强泡沫夹芯复合材料中,由于格栅结构的引入,原本作为一个整体的泡沫芯材板被分割成了一个个离散的泡沫芯材条。在制备夹层预成型体时,干态纤维织物(经树脂浸润成型后即为复合材料格栅结构)与泡沫芯材条交替铺放,干态纤维织物呈波浪形穿插于离散的泡沫芯材条之间,泡沫芯材条被干态纤维织物“半包覆”。为了尽可能提高相邻泡沫芯材条之间以及泡沫芯材条与干态纤维织物之间贴合度,并尽可能减少干态纤维织物的局部皱褶,需要对干态纤维织物施加一定张力。但由于泡沫芯材密度较低(≤400kg/m3),带有一定张力的波浪形干态纤维织物会使紧贴于其上的泡沫芯材条崩出。此外,即使按照上述操作交替铺放泡沫芯材条和干态纤维织物,松开干态纤维织物上施加的张力后,原本贴合较好的预成型体也会再次发生“松弛”,导致制备的夹层预成型体排列不整齐、整体厚度不均匀、格栅结构厚度不均一等情况,进而影响格栅增强泡沫夹芯复合材料外观尺寸及质量一致性。
4.格栅增强泡沫夹芯复合材料是一种新型复合材料夹层结构,目前尚无公开的、完备的制备模具和成型工艺解决方案。从公开报道看,国外的英国金斯顿大学(kingston university)、伊朗塔比阿特莫达勒斯大学(tarbiat modares university)等采用vartm(vacuum assisted resin transfer molding,真空辅助树脂传递模塑)成型工艺成功制备出不同形状格栅结构增强的泡沫夹芯复合材料,但其公开报道中有关成型过程阐述极其简单,模具设计、工艺方案等技术细节尚未披露;此外,基于vartm成型工艺的复合材料,尤其是大尺寸复合材料结构的制造成本相对较高,并不适宜于工业应用。
5.格栅增强泡沫夹芯复合材料的结构特点——泡沫芯材完全离散且干态纤维织物
反对称穿插于其中,导致成型过程中最大难点是夹层预成型体尺寸精确和整体稳定性控制以及夹层预成型体整体制备,解决上述难点的关键在于泡沫芯材位置、格栅结构厚度和形状精确控制。
6.因此,设计并制造一种操作方便、成型难度较低的平板型辅助模具,并设计一种成本相对较低的成型工艺,来进行大尺寸格栅增强泡沫夹芯复合材料的制备对实际生产来说实为必要。
技术实现要素:7.为了解决上述技术问题,本发明提供了一种格栅增强泡沫夹芯复合材料成型用预成型体及其成型方法。该预成型体能够方便、快速的完成离散型泡沫芯材与干态纤维织物的交错式穿插复合,并能保证成品复合材料的尺寸精确性、整体稳定性和质量一致性。成型工艺本身方法简单,操作方便,且成本较低,尤其适合进行大尺寸格栅增强泡沫夹芯复合材料的制备。
8.本发明为解决上述技术问题所采用的技术方案为:格栅增强泡沫夹芯复合材料成型用预成型体,包括一块水平设置的矩形平板状金属底板,在矩形平板状金属底板的上表面上,沿其长度方向,左右间隔、且平行设置有多个限位组,每个限位组均由沿矩形平板状金属底板的宽度方向左右对称设置的两个定位块构成,所述的定位块为竖直设置的平板状结构,在每个定位块的底部均向下延伸设置有一个卡座,该卡座能够与金属底板上预设的卡槽相配合,在每个定位块的顶部中心处还开设有一个竖直通孔,该竖直通孔内穿设有一个锁紧螺栓,所述的锁紧螺栓为沉头螺栓,且锁紧螺栓依次穿过定位块和卡座后拧紧在金属底板的卡槽内,实现定位块在金属底板上表面的装卡锁紧固定;在沿矩形平板状金属底板的长度方向上,每相邻两个定位块之间的间隙中均铺设有一个硅胶垫片,该硅胶垫片和定位块的宽度一致,使金属底板的上表面在沿其长度方向的左右两侧,分别组构成有一个由定位块和硅胶垫片间隔分布,且具有固定宽度的栅栏状结构,在金属底板上位于两个栅栏状结构之间的位置铺设有一层厚度与硅胶垫片一致的下面板,该下面板的上方设置有交错排布的泡沫夹芯结构和格栅结构;所述的泡沫夹芯结构包括间隔穿插设置的泡沫芯材组ⅰ和泡沫芯材组ⅱ,该泡沫芯材组ⅰ和泡沫芯材组ⅱ由左右平行设置的多个泡沫芯材条组成,且多个泡沫芯材条具有相同高度,所述的泡沫芯材组ⅰ中泡沫芯材条的个数与限位组的个数一致,泡沫芯材组ⅰ中的多个泡沫芯材条分别卡设在每个限位组中的两个定位块之间,且泡沫芯材组ⅰ中泡沫芯材条的上表面与定位块的上表面处于同一水平面,所述的泡沫芯材组ⅱ中泡沫芯材条的个数为硅胶垫片个数的一半,泡沫芯材组ⅱ中的多个泡沫芯材条分别设置在每相邻两个限位组之间,且泡沫芯材组ⅱ中泡沫芯材条的两端分别延伸覆盖至其所对应的硅胶垫片的上方,所述的格栅结构为待成型的干态纤维织物,该干态纤维织物呈凹凸起伏状反对称结构,且其紧贴泡沫芯材组ⅰ的顶部、泡沫芯材组ⅱ的底部以及两者中每相邻两个泡沫芯材条之间的间隙进行铺敷,所述交错排布的泡沫夹芯结构和格栅结构共同组构成了一个上表面水平的平台状结构,该平台状结构的上部还铺敷有上面板。
9.进一步的,所述的卡槽和卡座均为长方体形结构。
10.进一步的,所述的卡座与其相对应的定位块为一体结构。
11.进一步的,所述的定位块为金属材质。
12.进一步的,所述定位块的纵切面为矩形、三角形或等腰梯形中的任意一种。
13.进一步的,所述上面板与下面板的厚度、材质均一致。
14.进一步的,所述上面板和下面板为玻璃纤维、碳纤维、碳/玻混杂纤维、石英纤维、kevler纤维、超高分子量聚乙烯纤维和pb0纤维中至少一种的混编织物,且该混编织物的面密度≥100g/m2。
15.进一步的,所述的干态纤维织物为玻璃纤维、碳纤维、碳/玻混杂纤维、石英纤维、kevler纤维、超高分子量聚乙烯纤维和pb0纤维中至少一种的混编织物,且该混编织物的面密度≥100g/m2。
16.进一步的,所述泡沫芯材条的材质为聚氯乙烯、聚甲基丙烯酰亚胺、聚对苯二甲酸乙二醇酯和聚氨酯中的任意一种,且泡沫芯材条的密度≤400kg/m3。
17.一种格栅增强泡沫夹芯复合材料的成型方法,包括以下步骤:(1)金属底板的准备将金属底板平放于水平操作台上,之后,采用酒精或丙酮对金属底板的上表面和卡槽进行清洗,清洗干净并晾干后,对金属底板的上表面和卡槽进行脱模蜡均匀涂抹3次,且每次间隔10
‑
20min;(2)定位块的清洗及安装采用酒精或丙酮对定位块及其卡座的外表面进行清洗,清洗干净并晾干后,对定位块及其卡座的外表面进行脱模蜡均匀涂抹3次,且每次间隔10
‑
20min,之后,将定位块的卡座插入步骤(1)中金属底板上的卡槽内,然后,采用锁紧螺栓经由定位块上预设的竖直通孔,将定位块锁紧固定在金属底板的卡槽内,并保证定位块不能晃动;(3)硅胶垫片的放置采用硅胶垫片将限位组之间每相邻两个定位块之间的间隙铺满;(4)下面板的铺敷在金属底板的上表面上由定位块和硅胶垫片围成的区域内铺敷与步骤(3)所选硅胶垫片厚度一致的下面板;(5)泡沫芯材组ⅰ中泡沫芯材条的铺放取多个泡沫芯材条左右依次铺放在每个限位组中的两个定位块之间,使这些泡沫芯材条组构成泡沫芯材组ⅰ,且泡沫芯材组ⅰ中各个泡沫芯材条的纵切面与定位块的纵切面一致;(6)干态纤维织物的铺敷取干态纤维织物铺敷于泡沫芯材组ⅰ的上表面;(7)泡沫芯材组ⅱ中泡沫芯材条的铺放取多个泡沫芯材条左右间隔铺放在干态纤维织物的上表面,使这些泡沫芯材条组构成泡沫芯材组ⅱ,之后,将泡沫芯材组ⅱ中的各个泡沫芯材条分别向下预压,使之挤入每相邻两个限位组之间的间隙中,然后,在干态纤维织物和泡沫芯材组ⅱ共同组构成的平台状结构上表面放置用于进行压紧和固定的条形重物;(8)上面板的铺敷撤去步骤(7)中的条形重物,并在平台状结构的上表面铺敷上面板,构成预成型
体;(9)预成型体的封装按照vari成型工艺在步骤(8)制备的预成型体上进行脱模布、导流网的铺放以及注胶管路的设置,然后,用真空袋膜整体封装预成型体;(10)注胶和脱模按照vari成型工艺对步骤(9)封装好的预成型体进行注胶,待树脂完全固化后,拆卸预成型体中的定位块,脱模后,即制得成品格栅增强泡沫夹芯复合材料。
18.有益效果:1、本发明的格栅增强泡沫夹芯复合材料成型用预成型体通过装置中限位组的设置,可精确控制泡沫芯材的位置以及格栅结构的厚度,有效实现格栅增强泡沫夹芯复合材料成型过程中预成型体的尺寸精确控制、整体厚度控制、整体稳定性和成型产品的质量一致性。同时,以复合材料的上下面板厚度为基准,通过定位块底部卡座以及金属底板上卡槽的配合设置,既提升了整个预成型体的装卸便捷性,又能够较好地控制下面板与上面板厚度的一致性,实用效果较好。
19.2、本发明的预成型体在完成复合材料的制备之后,其中涉及到的模具单元(包括金属底板、定位块等)可在拆卸、脱模后进行反复多次使用。且模具单元整体制造成本较低,易脱模,易拆卸、易装配,利用率高,并易于保养维护,实用效果好。
20.3、本发明的预成型体通过定位块形状和相邻定位块间距的设计,可对格栅结构的形状进行准确调控,并完成格栅结构厚度的精确控制,以实现不同类型格栅增强泡沫夹芯复合材料的制备。
21.4、本发明的成型工艺在完成整个预成型体的制备以后,可按照vari成型工艺常规步骤进行脱模布、导流网、注胶口、出胶口、注胶管路等的敷设,然后即可整体封装,不仅实现了上、下面板与泡沫夹芯结构和格栅结构的一体化整体成型,使工艺整体可在一次成型操作中完成整个复合产品的制备,制备效率较高,制备成本低,还能够很好的保证成品的外观一致性和质量稳定性。成型工艺本身技术稳定,流程简单,操作方便,便于实施。
附图说明
22.图1为本发明中预成型体的纵向剖开结构示意图(包含定位块);图2为本发明中预成型体的纵向剖开结构示意图(不包含定位块);图3为本发明中预成型体的横向剖开结构示意图;图4为本发明中定位块和卡座的主视图;图5为图4的俯视图;图6为图4的仰视图;图7为实施例1中所采用平板型辅助模具的结构示意图;图8为图7的俯视图;图9为实施例2中所采用平板型辅助模具的结构示意图;图10为图9的俯视图;附图标记:1、金属底板,2、定位块,201、竖直通孔,202、卡座,3、锁紧螺栓,4、硅胶垫片,5、上面板,6、下面板,7、泡沫芯材条,8、干态纤维织物。
具体实施方式
23.下面结合附图和具体实施例对本发明的技术方案做进一步详细的阐述和说明。
24.如图所示,一种基于vari成型工艺和平板型模具的格栅增强泡沫夹芯复合材料的成型方法,包括平板型辅助模具的设计、预成型体的制备以及基于vari成型工艺的格栅增强泡沫夹芯复合材料一体化整体成型方法。
25.平板型辅助模具主要组成部分包括金属底板1、定位块2、锁紧螺栓3、硅胶垫片4,金属底板1呈矩形平板状,且水平设置,矩形平板状金属底板1的上表面上,沿其长度方向,左右间隔、且平行设置有多个限位组,每个限位组均由沿矩形平板状金属底板1的宽度方向左右对称设置的两个定位块2构成,金属底板1的上表面加工有多个矩形盲孔状卡槽,所述的定位块2为竖直设置的平板状结构,定位块2在其高度方向上加工有圆形的竖直通孔201,该竖直通孔201内用于穿设锁紧螺栓3,所述的锁紧螺栓3为沉头螺栓,定位块2底面加工有与金属底板1上表面卡槽尺寸相匹配的矩形卡座202,定位块2集定位、限位功能于一体。所述锁紧螺栓3依次穿过定位块2和卡座202后拧紧在金属底板1的卡槽内,实现定位块2在金属底板3上表面的装卡锁紧固定;硅胶垫片4铺设在每相邻两个定位块2之间的间隙中,所述硅胶垫片4和定位块2的宽度一致,使金属底板1的上表面在沿其长度方向的左右两侧,分别组构成有一个由定位块2和硅胶垫片4间隔分布,且具有固定宽度的栅栏状结构。
26.预成型体的制备依托于平板型辅助模具,包括上面板5和下面板6的铺敷、泡沫芯材条7的铺放、干态纤维织物8(经树脂浸润成型后即为复合材料格栅结构)的铺敷等。其中,下面板6的厚度与硅胶垫片4一致,铺敷在金属底板1上位于两个栅栏状结构之间的位置,在下面板6的上方设置有交错排布的泡沫芯材条7和干态纤维织物8。
27.格栅增强泡沫夹芯复合材料的成型方法,包括以下步骤:(1)金属底板1准备金属底板1平放于水平操作台,之后,采用酒精或丙酮对金属底板1的上表面和卡槽进行清洗,清洗干净并晾干后,对金属底板1的上表面和卡槽进行脱模蜡均匀涂抹3次,且每次间隔10
‑
20min;(2)定位块2的清洗及安装采用酒精或丙酮对定位块2及其卡座202的外表面进行清洗,清洗干净并晾干后,对定位块2及其卡座202的外表面进行脱模蜡均匀涂抹3次,且每次间隔10
‑
20min,之后,将定位块2的卡座202缓缓插入步骤(1)中金属底板1上的卡槽内,确保卡座202与卡槽咬合较好,然后,采用锁紧螺栓3经由定位块2上预设的竖直通孔201,将定位块2锁紧固定在金属底板1的卡槽内,操作时不宜过拧,以定位块2不晃动为准;(3)硅胶垫片的放置采用硅胶垫片3将限位组之间每相邻两个定位块之间的间隙铺满;硅胶垫片4的长度为左右相邻两个定位块2之间间距,宽度与定位块2宽度相同,硅胶垫片4放置于相邻两个定位块2之间,且所有相邻两个定位块2之间均需要放置硅胶垫片4。
28.(4)下面板的铺敷根据下面板6目标厚度和所选增强纤维织物类型,确定需要铺敷的纤维织物层数、铺设方式等,在金属底板1的上表面上由定位块2和硅胶垫片3围成的区域内铺敷与步骤(3)所选硅胶垫片3厚度一致的下面板6;
(5)泡沫芯材组ⅰ中泡沫芯材条的铺放取多个泡沫芯材条7左右依次铺放在每个限位组中的两个定位块2之间,铺放时自一侧向另一侧间隔铺放,使这些泡沫芯材条7组构成泡沫芯材组ⅰ,且泡沫芯材组ⅰ中各个泡沫芯材条7的纵切面与定位块2的纵切面一致;泡沫芯材条7两端与每个限位组中的一对定位块2对齐,实现泡沫芯材条7在限位组之间的卡设;(6)干态纤维织物的铺敷取干态纤维织物8(经树脂浸润成型后即为复合材料格栅结构)水平铺敷于泡沫芯材组ⅰ的上表面;(7)泡沫芯材组ⅱ中泡沫芯材条的铺放取多个泡沫芯材条7左右间隔铺放在干态纤维织物8的上表面,使这些泡沫芯材条7组构成泡沫芯材组ⅱ,之后,将泡沫芯材组ⅱ中的各个泡沫芯材条7分别向下预压,使之挤入每相邻两个限位组之间的间隙中,然后,及时在干态纤维织物8和泡沫芯材组ⅱ共同组构成的平台状结构上表面放置用于进行压紧和固定的条形重物;(8)上面板的铺敷撤去步骤(7)中的条形重物,并在平台状结构的上表面铺敷上面板5,其铺敷要求与下面板6相同,构成预成型体;(9)预成型体的封装按照vari成型工艺在步骤(8)制备的预成型体上进行脱模布、导流网的铺放以及注胶管路的设置,然后,用真空袋膜整体封装预成型体;(10)注胶和脱模按照vari成型工艺对步骤(9)封装好的预成型体进行注胶,待树脂完全固化后,拆卸预成型体中的定位块2,脱模后,即制得成品格栅增强泡沫夹芯复合材料。
29.上述技术方案中所述的金属底板1材质为45#钢以及更高牌号钢、铝合金、钛合金等金属,上表面平面度≤0.2mm,上表面尺寸比格栅增强泡沫夹芯复合材料目标尺寸至少大100mm,厚度与所选材质模量有关,保证金属底板1面外变形≤5mm,一般不小于15mm。金属底板1与格栅增强泡沫夹芯复合材料目标尺寸相当,其长度≤5m、宽度≤5m。
30.所述定位块2数量必须是2n个(2≤n≤100且n为整数),长度范围为10mm
‑
100mm、宽度范围为8mm
‑
50mm、高度范围为10mm
‑
70mm,相邻定位块2间距为定位块2长度
±
1mm;此外,所有定位块2外观尺寸、材质完全相同,材质为45#钢以及更高牌号钢、铝合金、钛合金等金属,加工公差为
±
0.1mm。定位块2用于锁紧螺栓3贯通的竖直通孔201位置为定位块2高度方向几何中心,竖直通孔201直径为定位块2宽度四分之一至二分之一,加工公差为
±
0.1mm,与金属底板1的卡槽加工公差为
±
0.1mm,且金属底板1卡槽尺寸比定位块2的卡座202大0.1
‑
0.2mm。定位块2纵切面几何形状可根据复合材料结构设计需求确定,可选矩形、梯形、三角形等简单几何形状,也可选其它形状。
31.所述锁紧螺栓3为标准件或非标准件,规格为m6
‑
m12,材质为40#铬钢、42#铬锰钢、12.9级高强度钢、钛合金等高强度金属,也可为45#钢等低强度钢,但需要进行退火处理。
32.所述硅胶垫片4长度为定位块2长度
±
1mm、宽度为定位块2宽度
±
1mm、厚度为范围为1mm
‑
8mm。
33.所述上面板5和下面板6的材质为玻璃纤维、碳纤维、碳/玻混杂纤维、石英纤维、
kevler纤维、超高分子量聚乙烯纤维、pb0纤维等纤维织物及其混编织物,面密度≥100g/m2。
34.所述格栅用干态纤维织物8为玻璃纤维、碳纤维、碳/玻混杂纤维、石英纤维、kevler纤维、超高分子量聚乙烯纤维、pb0纤维等纤维织物及其混编织物,面密度≥100g/m2。
35.所述格栅用干态纤维织物8(经树脂浸润成型后即为复合材料格栅结构)与上面板5和下面板6用纤维织物可以相同,也可以不同。
36.所述泡沫芯材条7为聚氯乙烯(pvc)、聚甲基丙烯酰亚胺(pmi)、聚对苯二甲酸乙二醇酯(pet)、聚氨酯(pu)等发泡型材料,密度≤400kg/m3,纵切面几何形状与定位块2相同,可根据复合材料结构设计需求确定,可矩形、梯形、三角形等简单几何形状,也可选其它形状。
37.实施例1:结合附图7和8,本实施例的格栅增强泡沫夹芯复合材料中定位块的纵切面形状选用矩形。其中,纵切面为矩形的定位块数量为12对24个,长40mm、宽15mm、高28.5mm,定位块相邻间距为40.8mm,硅胶垫片长40.8mm、宽15mm、厚3.5mm,锁紧螺栓型号为m8,金属底板长1150mm、宽1150mm、厚20mm。
38.上面板和下面板的长929mm、宽920mm、厚3.5mm,格栅结构中干态纤维织物的宽为950mm、厚0.4mm,纵切面为矩形的泡沫芯材条的数量为23个,长950mm(11个)和920mm(12个)两种,宽40mm、高25mm。
39.金属底板、定位块材质均为6061铝合金,锁紧螺栓材质为12.9级高强度钢。
40.上面板和下面板用纤维织物为面密度400g/m2的e玻璃纤维方格布,数量为10层;格栅用干态纤维织物(经树脂浸润成型后即为复合材料格栅结构)为面密度220g/m2的缎纹高强玻璃纤维布,数量为2层。
41.成型工艺与上述步骤相同。
42.实施例2:结合附图9和10,本实施例的格栅增强泡沫夹芯复合材料中定位块的纵切面形状选用等腰梯形。其中,纵切面为等腰梯形的定位块数量为15对30个,上底20mm、下底66.2mm、宽20mm、高42.6mm,定位块相邻间距为20.42,硅胶垫片长20.42mm、宽20mm、厚2.6mm,锁紧螺栓型号为m10,金属底板长1500mm、宽1300mm、厚25mm。
43.上面板的长为1233mm、下面板长1279mm,上面板和下面板宽均为1030mm、厚均为2.6mm,格栅结构宽1070mm、厚0.21mm,纵切面为等腰梯形的泡沫芯材条数量为29个,长1070mm(14个)和1030mm(15个)两种,上底20mm、下底66.2mm、高40mm。
44.金属底板、定位块材质均为45#钢,锁紧螺栓材质为42#铬锰钢。
45.上面板和下面板用纤维织物为面密度350g/m2的双轴向高强玻璃纤维布,数量为8层;格栅用干态纤维织物(经树脂浸润成型后即为复合材料格栅结构)为面密度200g/m2的单向碳纤维布,数量为1层。
46.成型工艺与上述步骤相同。
47.上述所列具体实施方式为非限制性,对于本领域熟练技术人员来说,在不偏离本发明范围内,可进行各种改进和变化。