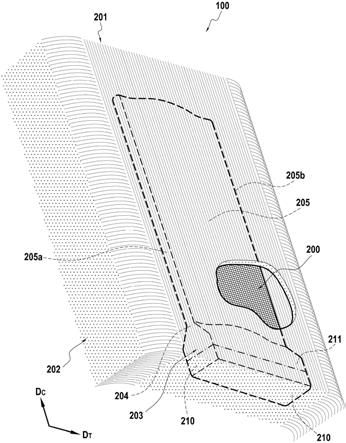
1.本发明涉及复合材料部件的制造,更具体地说,涉及通过三维(3d)或多层编织制造用于该部件的增强纤维织构。
背景技术:2.本发明的一个应用领域是结构复合材料部件(即,具有由基质致密化的纤维增强物的结构部件)的制造。复合材料可以制造总质量低于由金属制成的相同部件的部件。
3.更具体地说,本发明涉及具有一个或多个超厚部分的复合材料部件,例如航空发动机叶片的根部,所述超厚部分对应于复合材料部件的厚度显著变化的区域。在厚度变化的复合材料的情况下,厚度的变化控制在意图形成部件增强物的纤维织构水平下。
4.已经提出生产用于涡轮机的复合材料叶片。我们特别参考文件us7101154和us 2011/0311368,其中描述了由如下组成的解决方案:使超厚部件中的线支数增加(因此使横截面增加),从而降低了用压缩使得3d纤维织构成型时减少厚度的能力。然而,使用高支数的线使得预制件中的纤维量局部增加。如果纤维量过大,那么制造的孔隙网络可能不足以允许基质成分良好地进入预制件的芯部,因此不足以获得具有良好机械性能的均质复合材料。
技术实现要素:5.因此,理想的是能够提供具有超厚部件的3d或多层纤维预制件,其没有上述缺点。
6.为此目的,根据本发明,提出了用于复合材料部件的纤维预制件的制造方法,所述方法包括以下步骤:
[0007]-通过在多个纬层和经层之间进行三维或多层编织(weave)来制造纤维织构,该纤维织构包括超厚部分,所述超厚部分具有牺牲部分和在经向方向上与所述牺牲部分相邻的可用部分,牺牲部分,
[0008]-将纤维织构置于成型工具组中,
[0009]-使纤维织构成型,以获得具有牺牲部分和相邻可用部分的纤维预制件,
[0010]-去除纤维预制件的牺牲部分,
[0011]
在该方法中,当编织纤维坯料时,将一个或多个膨胀元件插入位于纤维织构的牺牲部分的芯部处的纬层中,各膨胀元件的横截面大于存在于可用部分中的纬线或股线的横截面或支数(count)。
[0012]
将膨胀元件插入纤维织构芯部处纬层中的牺牲部分中使得牺牲部分和可用部分中纤维织构基本都可膨胀或胀大。因此,可以获得更显著膨胀或鼓起的可用部分。在牺牲部分并未包括横截面大于存在于可用部分中的纬线或股线的横截面或支数的膨胀元件,需要在可用部分中插入大量大横截面的线或股线,以达到现有技术解决方案所需的厚度。然而,在该情况下,超厚部分中的纤维量变得过多,并且与致密化和最佳机械特性的相容性较差。
事实上,如果纤维量过多,则更难将基质前体引入纤维增强物的全部孔隙中。此外,如果纤维量过多,则所沉积的基质量将较低,可能会使所获得的复合材料的机械特性降低。
[0013]
膨胀元件局限于牺牲部分,使得可以在可用部分中使用与目标纤维量兼容的线或股线。换言之,本发明可以通过使用位于牺牲部分中的膨胀元件,在可用部分中获得显著膨胀,所述牺牲部分稍后将从最终预制件中消除。因此,膨胀元件的横截面尺寸和量可以仅根据可用部分的厚度需求来限定,存在于可用部分中的线或股线的尺寸能够仅限定为达到所需纤维量。因此,可以获得可用部分,所述可用部分既通过具有所需厚度满足尺寸要求,又通过具有与致密化工艺兼容的受控纤维量和最终复合材料的良好机械性能满足制造要求。
[0014]
在一个实施方式中,将编织物插入位于纤维织构的牺牲部分的芯部处的纬层中,各编织物的横截面大于存在于可用部分中的纬线或股线的横截面或支数(count)。
[0015]
根据一个特定特征,位于包括编织物的纬层附近的纬层包含线或股线,所述线或股线的支数大于位于牺牲部分表层中的纬层的线或股线的支数。
[0016]
根据另一个特定特征,编织物的横截面对应于5k(5000根纤丝)的支数,位于包含编织物的纬层附近的纬层的线或股线包括支数为1k(1000根纤丝)至4k(4000根纤丝)的线或股线,位于牺牲部分表层中的纬层的线或股线的支数为0.5k(500根纤丝)。
[0017]
在实施方式的另一示例中,牺牲部分和可用部分包含在所述部件之间连续编织的相同数量的纬线。本发明的纤维织构完全是纺织品(即,没有添加任何插入件),并且其线通过3d或多层编织连接,允许该结构抗分层。
[0018]
本发明还涉及一种用于复合材料部件的制造方法,所述方法包括以下步骤:
[0019]-按照本发明所述的纤维预制件制造方法来制造纤维预制件,
[0020]-将包含至少一种基质材料前体的液体组合物注射到纤维预制件中,
[0021]-使所述液体组合物转化为基质,以获得复合材料部件,所述复合材料部件包含通过基质致密化的纤维增强物。
[0022]
该方法尤其可用于制造复合材料的涡轮机叶片,例如,涡轮叶片,尤其是用于航空发动机的燃气涡轮叶片。
附图说明
[0023]
[图1]图1非常示意性地显示了根据本发明实施方式,意图生产纤维织构的三维编织纤维坯料,
[0024]
[图2]图2是尺寸放大的经向横截面图,其部分显示了图1的纤维织构超厚部分的编织图案的平面图,
[0025]
[图3]图3是由图1的纤维坯料获得的纤维织构的示意图,
[0026]
[图4]图4是分解透视示意图,显示了根据本发明一个实施方式的成型工具组以及图3的纤维织构在其内的放置,
[0027]
[图5]图5是安装后图4的工具组的透视示意图,
[0028]
[图6]图6是透视示意图,其显示了图5中成型工具组在压机中的放置以及通过压制进行的成形操作,
[0029]
[图7]图7显示了在图6的成形操作后去除所获得的纤维预制件的牺牲部分,
[0030]
[图8]图8显示了在去除牺牲部分后图7的纤维预制件,
[0031]
[图9]图9显示了将基质前体液体组合物注入图8的纤维预制件的操作,
[0032]
[图10]图10是根据本发明制造方法所获得的复合材料叶片的透视示意图。
具体实施方式
[0033]
本发明通常应用于制造纤维预制件,该纤维预制件能够构成用于制造复合材料部件(尤其是航空发动机叶片)的纤维增强物,所述部件通过用基质使纤维织构致密化而获得。在相对较低温度(通常最高为300℃)下使用复合材料的情况下,基质一般为树脂,或者在热结构复合材料的情况下,基质是耐火材料,例如碳或陶瓷。
[0034]
本发明的纤维预制件由通过三维编织或多层编织制造的纤维织构获得。
[0035]
术语“三维编织”或“3d编织”是指至少一些经线将多个纬层上的纬线连接在一起的编织方法。
[0036]
本文的“多层编织”是指使用多层纬线的3d编织,各层的基本图案等同于常规2d图案(例如,平纹型图案、缎纹型图案、或斜纹型图案),但是图案的某些点将纬层结合在一起。
[0037]
通过3d或多层编织制造纤维织构可以在单个纺织操作中获得层之间的连接,并由此所获得的纤维织构和复合材料部件具有良好机械强度。
[0038]
有利的是在致密化后便于获得没有显著不规则性的表面状态,即良好的完成状态(finish condition),以避免或限制机械加工的精加工操作(finishing operation),或避免在树脂基质复合材料的情况中形成树脂丛块(clump)。为此,在具有内部部分或芯部、以及外部部分或表层(其与纤维织构外表面相邻)的纤维织构的情况中,优选通过用平纹型图案、缎纹型图案、或斜纹型图案编织来制造表层,以限制表面不规则性,并且缎纹型图案还提供了光滑的表面外观。可在纤维织构的外表面产生表层编织图案的变化,以赋予特定的所需性能,例如,由有利于紧密连接的平纹图案切换成有利于光滑表面状况的缎纹图案。
[0039]
而且有利的是,在复合材料部件内获得尽可能均匀的机械性能,以促进增强纤维织构的致密化,并且纤维织构的芯部及其表层之间的致密化梯度尽可能低,在cvi致密化的情况下尤为如此。为此,为了便于接近预制件的芯部,可以通过互锁编织在芯部处进行编织,这在多层薄织物之间提供了简单连通。
[0040]
本文的“互锁编织”是指3d编织图案,其中各经层与多个纬层连接,并且相同经列中的所有线在图案平面中具有相同移动。
[0041]
芯部和表层也可以通过用不同图案进行多层编织来产生,尤其是在芯部中用缎纹图案,在表层中用平纹或斜纹图案。
[0042]
还可以改变芯部部分中的三维编织的图案,例如通过组合不同的互锁图案、或者组合互锁图案和多层编织图案、或者甚至组合不同的多层编织图案来进行。还可以沿着外表面改变表层中的编织图案。
[0043]
可能期望在纤维织构的不同部分、特别是在芯部和表层中使用不同化学性能的线,从而为所获得的复合材料部件赋予特定性能,特别是在抗氧化性或耐磨损性方面。
[0044]
因此,在具有耐火纤维增强物的热结构复合材料部件的情况下,可以使用在芯部具有碳纤维且在表层具有陶瓷纤维(例如,碳化硅(sic))的预制件,以使表层部分处该复合部件的耐磨损性和抗氧化性增加。
[0045]
现在将对根据本发明的纤维织构的实施方式的示例进行描述。在该示例中,在提
花织机(jacquard type loom)上进行编织。
[0046]
图1非常示意性地显示了纤维坯料100,由此获得意图形成航空发动机叶片纤维增强物的纤维织构200(图2)。
[0047]
纤维织构200的坯料100是以已知方式在提花织机上通过三维编织(或3d编织)、或者通过多层编织获得的,所述提花织机上一束经线或股线201设置在多个层中,所述经线通过同样设置在多个层中的纬层202连接,一些纬层包括编织物(braid),如下文详述。文件us 7101154、us 7241112和wo2010/061140中详细描述了意图形成航空发动机叶片的纤维增强物的纤维预制件的实施方式的详细示例。
[0048]
纤维坯料100以条带形式进行编织,所述条件大致沿与经线201方向对应的方向dc以及沿待制造叶片的纵向方向延伸。在纤维坯料100中,纤维织构在dc方向和与dc方向垂直且与纬线202方向对应的d
t
方向具有可变厚度。厚度变化是根据待制造的叶片(blade)的纵向厚度和叶部(vane)轮廓确定的。在其意图形成根部预制件的部分中,纤维织构200在dc方向上具有根据待制造叶片根部厚度确定的超厚部分203。纤维织构200延伸意图形成叶片支承部的厚度减小部分204和意图形成叶片叶部的部分205。纤维织构200编织成单一件,并且在未编织的线切割后,必须具有叶片的近最终形状和尺寸(“净形状”)。为此,在纤维织构的厚度变化部分中,如厚度减小部分204中,通过在编织期间逐渐去除纬层来实现预制件的厚度减小。
[0049]
根据本发明,纤维织构200在超厚部分203处具有位于织构下端处的牺牲部分210和沿纬向方向dc与牺牲部分210相邻的可用部分211。仍然根据本发明,将一个或多个膨胀元件插入位于纤维织构200的牺牲部分203的芯部处的纬层中,各膨胀元件的横截面大于存在于可用部分211中的纬线或股线的横截面或支数。如下所述,意图去除纤维织构成形后所获得的纤维预制件中的牺牲部分210,以便仅在其中留下意图形成叶片根部的可用部分211。
[0050]
图2是纤维织构200的超厚部分203的编织图案的经向截面平面的局部放大图,该超厚部分203包括通过3d编织获得的牺牲部分210和可用部分211。在该示例中,纤维织构200在其超厚部分203中包括48个纬层或24个半层t1-t48。在位于相反的表层2032和2033之间的芯部2103中,纬层根据互锁型的3d编织通过经线201连接在一起。在表层2032和2033中,经线201和纬线202之间的编织是用不规则缎纹图案的二维编织。缎纹编织仅涉及纬向半层t1和t2以及纬向半层t47和t48。应注意,芯部的互锁3d编织延伸至表层的极端半层t1、t48,以便将这些半层连接至芯部半层。
[0051]
在本文所述的示例中,牺牲部分210具有沿经向方向dc与可用部分211相对侧的第一区域2101以及与第一区域2101和可用部分211两者相邻的第二区域2102。在第一区域2101中,在纤维织构200的最中心纬层中使用编织物10。本文所述示例中,编织物10用作半层t21至t28中的膨胀元件。编织物10的横截面或直径为1.55mm。存在于超厚部分203纬层中的所有其他线或股线的支数对应于小于编织物的横截面。本文的超厚部分203包括分别具有2k(2000根纤丝)、1.5k(1500根纤丝)和0.5k(500根纤丝)支数的线或股线20、30和40,分别对应于0.41mm、0.30mm和0.15mm的横截面或直径。
[0052]
将编织物10插入纤维织构芯部处纬层中的牺牲部分210中使得牺牲部分210和可用部分211中纤维织构基本都可膨胀或胀大。实际上,由于编织物的存在,牺牲部分210的膨
胀反映在相邻的可用部分211中,尤其是由于这两个部件相邻并通过用经线连续编织而连接在一起。因此,可以获得更显著膨胀或鼓起的可用部分。在牺牲部分并未包括横截面大于存在于可用部分中的纬线或股线的横截面或支数的膨胀元件的情况下,需要在可用部分中插入大量大横截面的线或股线,以达到现有技术解决方案所需的厚度。然而,在该情况下,超厚部分中的纤维量变得过多,并且与致密化和最佳机械特性的相容性较差。事实上,如果纤维量过多,则更难将基质前体引入纤维增强物的全部孔隙中。此外,如果纤维量过多,则所沉积的基质量将较低,可能会使所获得的复合材料的机械特性降低。
[0053]
编织物局限于牺牲部分,使得可以在可用部分中使用与目标纤维量兼容的线或股线。换言之,本发明可以通过使用位于牺牲部分中的膨胀元件,在可用部分中获得显著膨胀,所述牺牲部分稍后将从最终预制件中消除。因此,膨胀元件的横截面尺寸和量可以仅根据可用部分的厚度需求来限定,存在于可用部分中的线或股线的尺寸能够仅限定为达到所需纤维量。因此,可以获得意图形成本文叶片根部的可用部分,所述可用部分既通过具有所需厚度满足尺寸要求,又通过具有与致密化工艺兼容的受控纤维量(通常小于50%)和最终复合材料的良好机械性能满足制造要求。
[0054]
如图2所示,与包括编织物10的纬层相邻的纬层包括支数为1k至4k的线或股线30,而表层中的纬层包括支数为0.5k的线或股线。因此,厚度逐渐减小,而不会在纤维织构中产生“孔洞”,可以使织物传输更加平滑。
[0055]
在牺牲部分210的第二区域2102中,纬层主要包括支数为2k的线或股线,但存在于表层附近的包含支数至少1.5k的线或股线的纬层除外,同时存在于表层中的纬层包含0.5k的线或股线。线或股线的支数或尺寸的该分布使得可以获得更平滑的织物传输,避免产生孔洞,同时确保目标纤维体积比和厚度。
[0056]
在可用部分211中,位于表层下方的纬层主要包括在与牺牲部分210结合处支数为1.5k的线或股线30,线或股线30逐渐被支数为0.5k的线或股线40(类似于表层中的线或股线)取代。
[0057]
本发明的纤维织构可以进行编织,特别是、但不限于:由碳纤维、陶瓷纤维(例如碳化硅)、或氧化物纤维(例如氧化铝)的线进行编织。
[0058]
一旦纤维织构200编织成坯料100,则对未编织线进行切割以取出纤维织构。因此,获得如图3所示且以单一件编织的纤维织构200。
[0059]
下一步骤由如下构成:通过使纤维织构200压缩以形成易于致密化的纤维预制件来成形。为此,将纤维织构置于成型工具组300中,如图4所示,所述成型工具组包括其中心中具有第一腔室311的第一壳体310,所述第一腔室311部分对应于待制造叶片的形状和尺寸,腔室311由第一接触面312包围。
[0060]
工具组300还包括其中心中具有第二腔室321的第二壳体320,所述第二腔室321部分对应于待制造叶片的形状和尺寸,第二腔室321由第二接触面322包围,所述第二接触面322意图与第一壳体310的第一接触面312合作。
[0061]
首先使纤维织构200位于第一壳体310的腔室311中,然后使第二壳体320位于第一壳体310上,以使成型工具组300闭合。一旦如图5所示,使成型工具组300闭合,第一和第二壳体在所谓的“组装位置”中,即,第一和第二腔室310、320面对彼此放置,而第一和第二接触面312和322面对彼此放置。在该构造中,第一和第二腔室310、320一起限定了具有待制造
叶片形状的内部体积310,并且将纤维织构200置于其中。在本文所述示例中,腔室311意图形成叶片纤维预制件的内弧面侧,而腔室321意图形成叶片预制件的拱背侧。由于存在与可用部分211相邻的牺牲部分210,该部分具有足够的厚度来填充内部体积301的扩大部分3010,以形成叶片的根部。
[0062]
在图6中,将其中具有纤维织构200的成型工具组300置于压缩机400中。压机400包括下部部分410和上部部分420,成型工具组300的第一壳体310位于下部部分410,上部部分420设置在成型工具组300的第二壳体320中。
[0063]
如图6所示,成型工具组300经受压力机400所施加的压实压力pc。施加压力pc导致第一和第二壳体310和320结合在一起直到第一和第二接触面312和322相遇,使得可以根据确定的压缩率对纤维织构200进行压缩,以获得同样确定的纤维量,并根据待制造叶片的轮廓塑造纤维织构。因此,获得了纤维预制件500,所述纤维预制件500具有待制造叶片的形状,并带有对应于纤维织构200的牺牲部分210的牺牲部分510和对应于织构200的可用部分211的相邻可用部分511。
[0064]
然后从工具组300中取出纤维预制件500,以去除牺牲部分510,如图7所示。牺牲部分可以通过常规机械加工来去除,例如,用金刚石工具进行切割。
[0065]
然后,获得了纤维预制件500,其下端仅具有可用部分511作为意图形成叶片根部的超厚部分。可用部分511延伸了与纤维织构200的部分204对应的厚度减小部分504。预制件500还包括与纤维织构200的部分205对应的叶部部分505,该部分沿着分别与纤维织构200的边缘205a和205b对应的前缘部分505a和后缘部分505b之间的d
t
方向延伸。
[0066]
然后,使纤维预制件致密化。使意图形成待制造部件的纤维增强物的纤维预制件致密化包括通过用构成基质的材料填充预制件的空隙的部分或全部体积。根据液态制程(liquid process,lp),该致密化以其自身已知的方式进行。液态制程由用含有基质材料前体的液体组合物浸渍所述预制件构成。所述前体通常以聚合物形式存在,例如在溶剂中任选稀释的高性能环氧树脂。将预制件放置在可以紧密封闭的模具中,并且凹部具有最终模塑叶片形状。随后,使得模具闭合,并将基质前体液体(例如,树脂)注入整个凹部,以浸渍预制件的全部纤维部分。
[0067]
在消除任意溶剂并使聚合物交联之后,通过热处理(通常通过对模具进行加热),将前体转化成基质,即,使其进行聚合,预制件仍保持在形状与待制备部件的形状对应的模具中。
[0068]
当由碳或陶瓷基质形成时,所述热处理由如下构成:使前体热解以根据所用前体和热解条件将基质转变成碳或陶瓷基质。例如,液体陶瓷前体(尤其是sic)可以是聚碳硅烷(pcs)型、或聚钛碳硅烷(ptcs)型、或聚硅氮烷(psz)型的树脂,而液体碳前体可以是具有相对高焦炭含量的树脂,例如酚醛树脂。可以进行从浸渍到热处理的多个连续循环,以实现所需的致密化程度。
[0069]
根据本发明的一个方面,并且特别是当形成有机基质时,纤维预制件可以通过已知的树脂传递模塑(rtm)法来致密化。根据rtm法,将纤维预制件放置在具有待制造部件外部形状的模具中。将热固型树脂注入包括纤维预制件的模具的内部空间中。大体在树脂注入位置和树脂排放孔位置之间的该内部空间中建立压力梯度,以控制并优化用树脂浸渍预制件。
[0070]
将液体基质组合物注入纤维织构以及使转变为基质在注射工具组700中进行,如图9所示。类似于成形工具组300,注射工具700包括:第一壳体710,其中心处包括部分对应于待制造叶片形状和尺寸的第一腔室;以及第二壳体720,其中心处包括部分对应于待制造叶片形状和尺寸的第二腔室。在工具组700如图9所示闭合后,第一和第二腔室(分别地第一壳体和第二壳体710和720)一起限定了具有待制造叶片形状的内部体积701,并且纤维预制件500置于其中。
[0071]
工具组700还包括可以进行液体基质前体注射和将该前体转化为基质的装置。更准确地说,在本文所述示例中,工具组700的第一壳体710包括意图允许将液体基质前体组合物注射到纤维预制件中的注射口713,而第二壳体包括排放口723,所述排放口723旨在与泵体系配合,以便在注射期间在工具组中产生真空并排出空气。注射工具组700还包括下部部分740和上部部分750,第一和第二壳体710和720位于下部部分740和上部部分750之间,下部部分740和上部部分750装备有加热装置(图9中未显示)。
[0072]
一旦工具组700闭合,通过热固性树脂浸渍预制件500来模塑叶片,所述热固性树脂通过热处理聚合。为此目的,使用已知的树脂传递模塑工艺。根据rtm方法,树脂730(例如热固性树脂)经由第一壳体710的注入口713注入被预制件500占据的内部体积中。第二壳体720的端口723连接至保持压力的排放管(图9中未显示)。该构造可以在树脂注射的预制件500的下部部分和靠近端口723的预制件上部部分之间建立压力梯度。以此方式,基本注射在预制件下部部分处的树脂730将通过在其中循环至排出口723逐渐浸渍整个预制件,剩余部分通过该排出口排出。当然,工具组700的第一和第二壳体710和720可分别包括多个注入口和多个排出口。
[0073]
例如,所使用的树脂可以是温度等级为180℃的环氧树脂(在没有特性损失的情况下所支持的最高温度)。适用于rtm方法的树脂是众所周知的。其优选具有低粘度,以便于注入纤维中。树脂的温度等级和/或化学性质的选择根据部件必须要经受的热机械应力来确定。一旦将树脂注入整个增强体,则其按照rtm方法通过热处理进行聚合。
[0074]
在注入和聚合后,叶片进行脱模。叶片可以任选地经历后固化工艺以改进其热机械特性(提高玻璃化转变温度)。最后,对叶片进行修整以去除多余的树脂,并机械加工倒角。无需机械加工,因为待模塑的部件符合所需尺寸。
[0075]
纤维预制件也可以已知方法通过化学气相渗透(cvi)来进行致密化。将与待制造的叶片纤维增强物对应的纤维预制件放置在容纳反应气体相的烘箱中。不同于针对导致仅在材料表面上沉积的化学气相沉积(cvd)法的特定压力和温度条件,选择烘箱内存在的压力和温度以及气相组成以使气相能在预制件的空隙中进行扩散,从而通过将固体材料沉积在与纤维接触的材料芯部中形成基质,所述固体材料由气体相组成分解或多个成分之间反应得到。
[0076]
sic基质的形成可通过甲基三氯硅烷(mts)分解生成sic,而碳基质可通过碳氢化合物气体(如甲烷和/或丙烷)裂解生成碳。
[0077]
结合液体和气体方法的致密化也可用于促进实施、限制成本和制造周期,同时获得预期用途的满意特性。
[0078]
预制件也可以通过浆料浇铸(例如,含有sic和有机粘合剂的浆料),然后用液态硅进行熔融渗透来致密化。
[0079]
上述致密化方法可以由本发明的纤维预制件开始制造主要具有有机基质(omc)、碳基质(c/c)以及陶瓷基质(cmc)的复合材料部件。
[0080]
如图10所示,然后获得通过基质致密化的纤维增强物形成的叶片100,所述基质的下部部分具有由纤维预制件500的可用部分511形成的根部103,其通过由预制件500的厚度减小部分504形成的载体104和由纤维预制件500的叶部部分505形成的叶部105延伸。叶部105的前缘105a和后缘105b分别对应于纤维预制件500的边缘505a和505b。
[0081]
根据本发明的纤维织构及其制造方法尤其可用于制造具有图10中所示叶片的较复杂几何形状的涡轮机叶片,例如除了图10中所示的那样外还具有一个或多个平台的叶片使其能够执行多个功能(例如叶部密封(vein sealing),防倾斜等)。
[0082]
在该实施方式的另一示例中,可以将一个或多个栓插入纤维织构牺牲部分芯部处的纬层中作为膨胀元件。各栓的横截面大于存在于可用部分中的纬线或股线的横截面或支数。