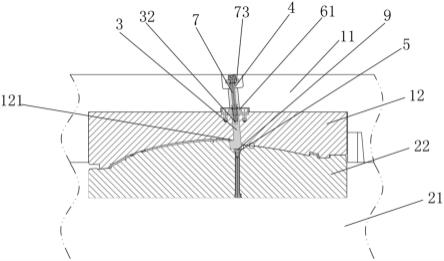
1.本实用新型涉及成型模具,特别涉及一种注塑成型模具。
背景技术:2.imd(in-mold decoration)模内注塑表面装饰技术的英文缩写, 是一种用于大规模制造的塑料件表面装饰的加工技术;其工艺过程总体上是将已印刷好图案的膜片热压成型并切好外形后放入注塑模具内,将成形用的树脂注入注塑模具内,使树脂与膜片接合,使印刷有图案的膜片与树脂形成一体后固化成产品;因此imd产品的表面是一层硬化的透明薄膜,中间是印刷图案层,背面是塑胶层;其优点是生产出来的塑料件外观漂亮,可以有多种颜色,多种花纹,较喷涂工艺的外壳耐磨,亮度高,立体感强,并可长期保持颜色的鲜明不易褪色;防尘,防潮性好。imd是目前国际风行的表面装饰技术,此种加工技术已广泛应用到电子、电器外壳的生产领域中,主要应用于家电产品的表面装饰及功能性面板,常用在手机视窗镜片及外壳、洗衣机控制面板、冰箱控制面板、空调控制面板、汽车仪表盘、电饭煲控制面板多种领域的面板、标志等外观件上。
3.此种装饰面板在加工时,膜片热压成型,形成具有面板和处于面板外侧的闭环形侧围,此膜片成型后并切好放放注塑模具内,因加工的误差膜片在成型后很难与注塑模具完全吻合,膜片放入模具型腔中后容易出现膜片位于型腔侧部位处出现弹翘起来的情况,合模时会压坏膜片导致产品不良,因此imd工艺比较关键的问题是将热压成型并切好外形膜片放入注塑模具型腔时如何进行定位,传统的膜片定位一直是模具设计过程中的一大难题,在模具设计时需要在注塑模具内设计定位机构,以固定膜片在注塑模具型腔中位置。目前常规是采用在型腔侧设置横向平移的滑块组件进行定位膜片,即滑块滑到膜片位于型腔侧的侧围处并与膜片侧围的底面相贴配合,对膜片进行定位,且滑块组件采用油缸或弹簧进行驱动;合模前,滑块组件先复位,放置膜片时起卡住固定膜片的作用;但是当型腔位置非常窄小时,滑块组件会没有空间布置,因此在局部狭小空间的成型模具中对薄膜在模具中定位没有更加合理的定位措施,导致生产良率低。
4.有鉴于此,本发明人对上述问题进行深入研究,遂由本案产生。
技术实现要素:5.本实用新型的目的在于提供一种方便膜片定位,且定位机构不受模具空间位置限制,生产良率高的易于膜片定位的模内注塑成型模具。
6.为了达成上述目的,本实用新型的解决方案是这样的:
7.一种易于膜片定位的模内注塑成型模具,包括母模具和处于母模具下方的公模具,母模具具有母模板和处于母模板内的母模仁,公模具具有公模板和处于公模板内的公模仁,母模仁的底面凹设有上成型模腔,公模具的顶面凸伸入上成型模腔内的模芯结构,母模具位于上成型模腔的型腔侧安装有用于膜片定位的定位机构;上述定位机构包括定位斜销、复位弹簧和强力磁铁,上述定位斜销呈向上成型模腔的方向倾斜设置,且定位斜销以能
上下平移的方式紧配合安装于母模仁内,上述母模仁的顶面设有限制定位斜销向上脱出母模仁外的上限位结构,上述定位斜销下端端部凸设有伸入上成型腔室型腔侧内并能顶紧在上成型模腔内膜片侧围底面上的顶紧头,上述顶紧头朝向上成型模腔的一侧面呈由内至外向下倾斜的倾斜面,上述母模板内设有能上下平移并穿过上限位结构至定位斜销处推动定位斜销向下移动的推动杆,上述复位弹簧套装于推动杆外,并张紧于推动杆的上端部与上限位结构之间,且上述推动杆的上端与母模板上设有限制推动杆下移行程的下限位结构,上述推动杆与定位斜销的上端部推动配合,上述公模仁的顶面对应于顶紧头处下凹有与顶紧头相匹配的容置凹槽,上述强力磁铁固定在上述容置凹槽的槽底上,且上述强力磁铁与顶紧头相磁吸配合。
8.上述容置凹槽的槽底下凹有强力磁铁相匹配的安装凹陷,上述公模仁内开设有其上端与安装凹陷相通、下端通过公模仁底面的连通孔,该连通孔内安装有固定针,上述强力磁铁通过固定螺丝与固定针锁固在一起,且上述固定螺丝的头部下沉于强力磁铁内。
9.上述母模仁内位于上成型模腔的型腔侧外设有沿上下方向延伸并贯穿母模仁上下两端的斜销孔,上述定位斜销为一方形杆体,上述定位斜销朝向上成型模腔的一面和背向上成型模腔的一面均为向上成型模腔倾斜的斜面,上述定位斜销的下端部向下延伸有伸出斜销孔外的延伸部,上述延伸部朝向上成型模腔的一面凸设有方形块体,此方形块体朝向上成型模腔的一面为斜面,此方形块体为所述的顶紧头,三斜面的倾角相同。
10.上述母模仁的顶面下凹有扩径凹陷,上述斜销孔处于扩径凹陷内,上述上限位结构包括限位块和安装螺母,上述限位块为条形方块,上述条形方块嵌装于扩径凹陷内,并通过安装螺母锁固在母模仁上,上述定位斜销的底面与限位块的底面相贴配合,上述限位块上开设有上下贯穿的穿过孔,上述推动杆的下端部穿过上述穿过孔与定位斜销的上部相配合连接。
11.上述定位斜销的顶面下凹有安装凹陷,上述推动杆的下端部向下延伸有嵌紧于安装凹陷内的嵌紧缩径杆。
12.上述母模板内开设有上下贯穿母模板上下两侧的通道,上述通道具有上扩径段、缩径段和下扩径段,上述复位弹簧的上部处于上扩径段内,复位弹簧的下部处于缩径段内,上述限位块的下部处于扩径凹陷内,限位块的上部处于下扩径段内,上述下限位结构安装于上扩径段内。
13.上述推动杆的上端端部具有头部,推动杆的上端外套紧有与头部上下相叠配合的限位头,上述复位弹簧张紧于限位头与限位块之间,限位头的外径大于缩径段的内径,上扩径段与缩径段形成有一台阶,此限位头与台阶构成所述的下限位结构。
14.采用上述技术方案后,本实用新型的一种易于膜片定位的模内注塑成型模具,安装膜片时,先推动推动杆向下平移,此时推动杆的下移推动定位斜销向下移动,复位弹簧被压缩,顶紧头与上成型模腔的腔底形成有让位空间,使膜片放置时不受顶紧头的限制,放置后,释放推动杆,复位弹簧复位,定位斜销复位,使顶紧头上移与上成型模腔内的膜片位于型腔侧的侧围上下相贴紧,上成型模腔型腔侧的倒扣嵌入膜片侧围与定位斜销之间,从而扣住膜片,避免膜片位于型腔室出现弹翘起来的情况,膜片安装后,母模仁与公模仁合模,顶紧头伸入容置凹槽内并与模芯结构外侧密贴插穿封胶,得以注塑,且顶紧头被强力磁铁吸住;注塑完成后,母模仁上移脱模,当开膜到2mm时受强力磁铁的磁力大于复位弹簧的弹
力使定位斜销受强力磁铁的下拉力而与产品一同停留在公模具上,复位弹簧被压缩;当母模具上移动到5mm时母模具上的倒扣与产品完全分离,当母模具上移动到8mm时受下限位结构的影响限制,母模具无法相对于推动杆继续上移,而母模具的上拉力远大于强力磁铁的吸力,此时母模具与推动杆一同上移,当母模具继续上移至9mm时定位斜销与强力磁铁完全分离,顶紧头脱离出容置凹槽外与公模仁分离,定位斜销从公模仁中脱离出来,复位弹簧的回复力推到推动杆下移复位,定位斜销相应复位回初始位置即可进行下一循环周期的操作。与现有技术相比,本新型的模内注塑成型模具,利用定位机构的顶紧头可对注塑成型模具内的膜片位于型腔侧的边沿起到定位作用,不会使膜片出现弹翘的现象,且定位机构一部分设置在母模具内、另一部分设置在公模具内,无需占用模具的型腔面外表部位,能适用于不同尺寸的注塑模具,不受注塑模具型腔面的尺寸影响,安装适用性强,特别适用于型腔面为狭小空间的注塑成型模具,大大提高了此种尺寸的注塑成型模具的生产良率。
附图说明
15.图1为本实用新型的合模结构示意图;
16.图2为本实用新型中定位机构与成品的组合示意图;
17.图3为本实用新型中母模具的开模结构示意图;
18.图4为本实用新型开模到6mm的状态示意图;
19.图5为本实用新型开模到9mm的状态示意图;
20.图6为本实用新型的开模结构示意图。
具体实施方式
21.为了进一步解释本实用新型的技术方案,下面通过具体实施例来对本实用新型进行详细阐述。
22.本实用新型的一种易于膜片定位的模内注塑成型模具,如图1-6 所示,包括母模具和处于母模具下方的公模具,母模具具有母模板 11和处于母模板内的母模仁12,公模具具有公模板21和处于公模板内的公模仁22,母模仁12的底面凹设有上成型模腔,公模具的顶面凸伸入上成型模腔内的模芯结构,母模具位于上成型模腔的型腔侧安装有用于膜片定位的定位机构。本新型中,母模具与公模具的结构是公知的,在此不再复述。
23.本新型的创新之处在于:所述定位机构包括定位斜销3、复位弹簧4和强力磁铁5,定位斜销3呈向上成型模腔的方向倾斜设置,且定位斜销以能上下平移的方式紧配合安装于母模仁12内,定位斜销 3下端端部凸设有伸入上成型腔室型腔侧内并能顶紧在上成型模腔内膜片100侧围底面上的顶紧头31,顶紧头31朝向上成型模腔的一侧面呈由内至外向下倾斜的倾斜面,优佳的是,母模仁12内位于上成型模腔的型腔侧外设有沿上下方向延伸并贯穿母模仁12上下两端的斜销孔(图中未示出),此定位斜销3为一方形杆体,定位斜销3 朝向上成型模腔的一面(即定位斜销3的左侧面)和背向上成型模腔的一面(即定位斜销3的右侧面)均为向上成型模腔倾斜的斜面,即斜面上部处于斜面下部的左侧,两斜面的倾斜一致,优佳的是,斜面的倾斜度为5度,定位斜销3的下端部向下延伸有伸出斜销孔外的延伸部,延伸部朝向上成型模腔的一面凸设有方形块体,即延伸部相应呈方形杆体,延伸部的左侧面向左凸设有方形块体,此方形块体朝向上成型模腔的一面(即左侧面)为斜面,方形块
体的左侧略伸入上成型模腔内,方形块体伸入上成型模腔内的宽度为 0.3-0.4mm,此方形块体为所述的顶紧头31,此顶紧头的斜面与定位斜销3的斜面倾斜方向及倾斜角度一致。
24.所述母模仁12的顶面设有限制定位斜销3向上脱出母模仁12外的上限位结构,所述母模仁12的顶面下凹有扩径凹陷(图中未示出),斜销孔处于扩径凹陷内,上限位结构包括限位块61和安装螺母62,限位块61为沿左右方向延伸的条形方块,条形方块嵌装于扩径凹陷内,并通过安装螺母62锁固在母模仁12的扩径凹陷内,定位斜销的底面与限位块的底面相贴配合,利用条形方块的尺寸大于定位斜销3的外径使定位斜销3无法向上移动。
25.所述母模板11内设有能上下平移并穿过上限位结构至定位斜销 3处推动定位斜销向下移动的推动杆7,复位弹簧4套装于推动杆7 外,并张紧于推动杆7的上端部与上限位结构之间,且推动杆7的上端与母模板11上设有限制推动杆下移行程的下限位结构,推动杆 7与定位斜销3的上端部推动配合;优佳的是,限位块61上开设有上下贯穿的穿过孔(图中未示出),推动杆7的下端部经穿过孔穿过限位块61与定位斜销3的顶面相贴配合,定位斜销3的顶面下凹有安装凹陷32,此安装凹陷为沿上下方向延伸的条形槽,推动杆7的下端部向下延伸有嵌紧于安装凹陷内的嵌紧缩径杆71,利用嵌紧缩径杆与安装凹陷32套紧配合实现推动杆与定位斜销3的连接。
26.所述公模仁22的顶面对应于顶紧头处下凹有与顶紧头相匹配的容置凹槽221,强力磁铁5固定在容置凹槽221的槽底上,且强力磁铁与顶紧头相磁吸配合;优佳的是,定位斜销与顶紧头均为金属件,能与强力磁铁5相吸配合,容置凹槽221的槽宽大于顶紧头31的最大外径,所述容置凹槽221的槽底下凹有强力磁铁相匹配的安装凹陷(图中未示出),公模仁22内开设有其上端与安装凹陷相通、下端通过公模仁底面的连通孔(图中未示出),该连通孔内安装有固定针8,固定针8的底部具有扩径限位头,公模仁的下底面位于连通孔处向上凹设有限位槽,利用扩径限位头与限位槽的配合使固定针8 无法上移,强力磁铁5通过固定螺丝9与固定针8锁固在一起,且固定螺丝9的头部下沉于强力磁铁内。
27.所述母模板11内开设有上下贯穿母模板上下两侧的通道111,通道111具有上扩径段、缩径段和下扩径段,复位弹簧4的上部处于上扩径段内,上扩径段与缩径段形成有一台阶,复位弹簧3的下部处于缩径段内,限位块61的下部处于扩径凹陷内,限位块61的上部处于下扩径段内,所述推动杆7的上端部设有头部72,推动杆7 的上端外套紧有限位头73,限位头处于上扩径段内,限位头73叠设于头部72下方,限位头73的外径大于缩径段的内径,复位弹簧4 张紧于限位头73与限位块61之间,限位头73与台阶构成所述的下限位结构。
28.本实用新型的一种易于膜片定位的模内注塑成型模具,初始时,复位弹簧4撑开,定位斜销3的顶紧头31的上端面刚好与上模仁12的型腔面相贴配合,顶紧头31的左侧略伸入上成型模腔内,安装膜片100时,先向下推动推动杆7下移,此时推动杆7的下移推动定位斜销3向下移动,复位弹簧4被压缩,顶紧头31的左侧与上成型模腔的腔底形成有让位空间,使膜片100放置时不受顶紧头的限制,放置后,释放推动杆7,复位弹簧4复位,定位斜销3复位,使顶紧头31上移与上成型模腔内的膜片100位于型腔侧的侧围上下相贴紧,上模仁上成型模腔型腔侧的倒扣121嵌入膜片100侧围与定位斜销之间的空间内,并由顶紧头31支撑,从而扣住膜片100,避免膜片位于型腔室出现弹翘起来的情况,膜片安装后,母模仁与公模仁合模,顶紧头31伸入容置凹槽221内并与模芯结构外侧密贴插穿封胶,得以注塑,且顶紧头31被强力磁铁5吸住;注塑完成后,母模仁12上移脱模,当开膜到2mm时受强力磁铁5的磁
力大于复位弹簧 4的弹力使定位斜销3受强力磁铁5的吸住无法随上模仁上移,具有一下拉力而与产品200一同停留在公模仁22上,而上模仁和上模板的上移使复位弹簧4被压缩;当母模具上移动到5mm时母模具上的倒扣121与产品200完全分离,当母模具上移动到8mm时受限位头73 的限制,母模具无法相对于推动杆继续上移,而母模具的上拉力远大于强力磁铁5的吸力,推动杆7只能与母模具一同上移,此时利用顶紧头左侧面的斜面结构使定位斜销在上移时会向右退0.7mm,而顶紧头伸入成品200中的部位为0.3-0.4mm,使定位斜销3随母模具上移时不会撞到成品200的外侧壁;当母模具继续上移至9mm时定位斜销 3与强力磁铁5分离,相应与公模仁22分离,顶紧头脱离出容置凹槽外与公模仁分离,同时复位弹簧4的回复力拉到推动杆7下移复位,顶紧头复位回初始位置,即可进行下一循环周期的操作。与现有技术相比,本新型的模内注塑成型模具,利用定位机构的顶紧头可对注塑成型模具内的膜片位于型腔侧的边沿起到定位作用,不会使膜片出现弹翘的现象,且定位机构一部分设置在母模具内、另一部分设置在公模具内,无需占用模具的型腔面外表部位,能适用于不同尺寸的注塑模具,不受注塑模具型腔面的尺寸影响,安装适用性强,特别适用于型腔面为狭小空间的注塑成型模具,大大提高了此种尺寸的注塑成型模具的生产良率。
29.上述实施例和附图并非限定本实用新型的方法和夹具形状,任何所属技术领域的普通技术人员对其所做的适当变化或修饰,皆应视为不脱离本实用新型的专利范畴。