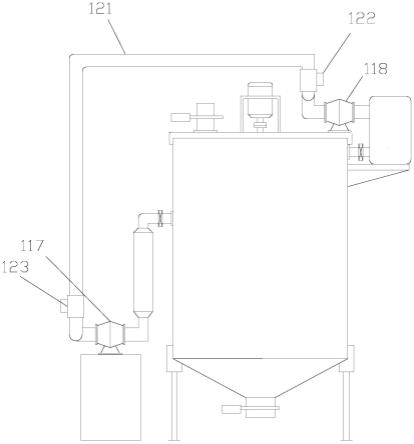
锦纶纤维、抗菌锦纶纤维及阻燃锦纶纤维的生产方法
1.本专利申请是(申请号为202110323033x、名称为“一种锦纶纤维的生产方法”、申请日为2021-3-26)的发明专利申请的分案申请。
技术领域
2.本发明涉及一种化纤的生产方法,具体地说是一种锦纶纤维的生产方法。
背景技术:3.锦纶是生活中常用的化学纤维,其原料通常为切片,经熔融挤压等工序后形成锦纶纤维。为了使锦纶具有特定的功能或特定的颜色,在纺丝生产中会添加母粒,如各种功能性的母粒类似抗菌母粒或者各种色母粒,其生产工序是在螺杆挤出机熔融挤压之前与切片形成混合,然后和切片一起熔融挤压。新购得的母粒含水量较高,加之存放原因更甚,母粒含水量影响后序可纺性,因此在生产时与干切片的混合前需要对母粒进行干燥。现有的干燥过程一般借助母粒干燥机,诸如:2012200857463色母粒干燥装置,该装置采用热风干燥,而在干燥时,依靠搅拌桨对母粒进行搅动,以提高干燥的效率,这种方式存在技术问题诸多,如单纯采用风干方式耗时长,干燥效率低,同时,在搅拌桨对母粒的搅拌过程中,母粒与过滤网、与搅拌桨的摩擦容易产生粉尘,本领域技术人员熟知,切片在脉冲式输送时,首先要尽量减少切片与输送管壁的摩擦,用意就是要减少切片中的粉末量,以确保后序的纺丝性能,母粒也是如此,在母粒干燥装置中产生较多粉尘并不可取。而如采用专利2014203269890的色母粒干燥器,仅依靠下落与热风接触,干燥效率明显较低,难以满足工艺需求,这对企业来讲是不利的。另外一端,干燥后的母粒若暂存于温度较低的容器中,存在容易反潮的技术问题,基于这些技术问题,由此产生本专利的改进措施。
技术实现要素:4.本发明的目的是:提供一种锦纶纤维的生产方法,采用这种方法可以确保母粒的干燥效果,可防止母粒反潮,可减少粉尘,从而实现母粒更好地添加,确保工艺需求。
5.本发明设计一种锦纶纤维的生产方法,包括如下步骤:s1混料:将干燥后的切片与经母粒干燥器干燥后的母粒一起添加至混料装置中混合;s2熔融:经混料装置混合后的切片与母粒一起进入螺杆挤出机内进行熔融挤出,得到纺丝熔体;s3动态混合:所述纺丝熔体从螺杆挤出机流出后进入动态混合装置进行动态混合;s4纺丝:将动态混合后的纺丝熔体输送至纺丝箱体,经计量泵输送至各个纺丝组件中进行纺丝生成纤维;s5吹风冷却:采用侧吹风装置对纤维进行吹风冷却:s6集束上油:对纤维进行集束上油;
s7卷绕成型:将上油后的丝束进行拉伸和预网络,最后由卷绕机卷绕成型,其特征在于:所述母粒干燥器对母粒干燥时包括三个步骤,第一步先在风干斗中进行搅拌风干,同时对母粒干燥器进行抽气除尘,利用空气过滤器除去搅拌时产生的母粒粉尘,第二步经搅拌风干后的母粒落入加热斗中进行加热干燥,第三步将加热干燥后的母粒落于存料腔内进行保温存放,并随时用于输出与切片的混合。
6.本发明进一步的方案如下:s2熔融步骤中螺杆挤出机加热区共有5个,一区温度245-250℃,二区温度250-260℃,三区温度260-268℃,四区温度260-268℃,五区温度260-265℃。
7.s4纺丝步骤中纺丝箱体温度263-268℃。
8.s5吹风冷却步骤中侧吹风温度18-20℃,湿度65%-68%。
9.s6集束上油步骤中:上油量为1.0-1.2%;s7卷绕成型步骤中:卷绕速度4200-4500m/min。
10.所述的母粒干燥器包括筒体,筒体顶部设有进料管、底部设有出料管,所述筒体内设有所述的风干斗和加热斗,风干斗通体设有风孔,在风干斗内设有搅抖桨,搅抖桨的驱动轴与位于筒体顶上的电机传动连接,风干斗外侧设有风罩,风罩的内表面是与风干斗形状相配合的斜面,在斜面上布满出风槽;所述加热斗位于风干斗下方,加热斗的上端面通过杆体设置有锥形导向器,加热斗的下端面设置有加热元件;加热斗与筒体底部之间的区域为所述的存料腔;该母粒干燥器还包括进风管和出风管,进风管一端连接进风机、另一端连接风罩,在进风管上设有加热夹套;所述风干斗上方设有集尘罩,所述出风管与集尘罩相连接,在出风管上设有空气过滤器和抽风机;所述进料管、出料管、进风管、出风管以及风干斗和加热斗的出口管上都设有阀门。
11.将进料管置于筒体顶部偏心位置,在筒体内设置导向器将从进料管落下的母粒导向风干斗内。
12.在母粒干燥器对母粒干燥的第一步中具有对风干斗进行称重的步骤。
13.所述筒体内设有环状座,环状座上端面设有多根导杆,所述风干斗穿设在环状座内,风干斗的外翻的口沿供所述导杆穿过,在风干斗的口沿与环状座之间设有称重传感器。
14.本发明所设计的锦纶纤维的生产方法,采用在切片中添加母粒的方式来生产,可以使锦纶成品具有特定的功能或者颜色,更有利于企业品种的丰富性。而采用特有母粒干燥方法,可以确保母粒满足干燥工艺需求,同时可除去因搅拌磨擦产生的粉尘,确保后道纺丝性能,同时干燥后的母粒存于有保温作用的存料腔内,可以有效防止返潮,采用本方法可以有效确保锦纶的产品质量。
附图说明
15.附图用来提供对本发明的进一步理解,在附图中:图1是实施例1所描述的锦纶纤维的生产方法所采用的设备流程图;图2是实施例1所描述的母粒干燥器的外观示意图;图3是实施例1所描述的母粒干燥器的结构示意图;图4是图3中a处的放大图;图5是实施例5所描述的母粒干燥器的外观示意图;
图6是实施例6所描述的母粒干燥器的结构示意图;图7是图6中空气过滤器的放大图;图8是封底板的俯视图;图9是翻板呈水平状时封底板边缘的剖视图;图10是翻板呈耷拉状时封底板边缘的剖视图;标号:母粒干燥器1、混料装置2、螺杆挤出机3、动态混合装置4、纺丝箱体5、侧吹风装置6、卷绕机7、干切片料仓81、母粒料仓82、计量螺杆9;筒体101、进料管102、出料管103、风干斗104、加热斗105、搅抖桨106、电机107、风罩108、斜面109、出风槽110、杆体111、锥形导向器112、加热元件113、存料腔114、进风管115、出风管116、进风机117、抽风机118、加热夹套119、空气过滤器120、循环风管121、三通阀一122、三通阀二123、环状座124、导杆125、称重传感器126、集尘罩127、导向器128、阀门129、机壳130、伸缩罩131、集尘斗132、集尘罐133、升降器134、顶板135、外壁136、内壁137、内翻边138、过滤网139、抽气腔140、封底板141、凹槽142、转轴143、翻板144、清洁毛刷145、l形片146、凸筋147、抱箍148、横向部149、安装架150、导向杆151、支杆152、进口管道153、出口管道154、仓门155。
具体实施方式
16.下面通过实施例结合附图对本发明作进一步的描述。
17.实施例1:如图1所示,本实施例所描述的锦纶纤维的生产方法,包括如下步骤:s1混料:将干燥后的切片与经母粒干燥器1干燥后的母粒一起添加至混料装置2中混合;所述母粒采用色母粒;s2熔融:经混料装置2混合后的切片与母粒一起进入螺杆挤出机3内进行熔融挤出,得到纺丝熔体;螺杆挤出机加热区共有5个,一区温度245℃,二区温度250℃,三区温度260℃,四区温度265℃,五区温度 260℃;s3动态混合:所述纺丝熔体从螺杆挤出机3流出后进入动态混合装置4进行动态混合;s4纺丝:将动态混合后的纺丝熔体输送至纺丝箱体5,经计量泵输送至各个纺丝组件中进行纺丝生成纤维;纺丝箱体5温度263℃s5吹风冷却:采用侧吹风装置6对纤维进行吹风冷却:侧吹风温度18℃,湿度65%;s6集束上油:对纤维进行集束上油;上油量为1.0%;s7卷绕成型:将上油后的丝束进行拉伸和预网络,最后由卷绕机7卷绕成型,卷绕速度4200m/min;所述母粒干燥器1对母粒干燥时包括三个步骤,第一步先在风干斗104中进行搅拌风干,同时对母粒干燥器1进行抽气除尘,利用空气过滤器120除去搅拌时产生的母粒粉尘,第二步经搅拌风干后的母粒落入加热斗105中进行加热干燥,第三步将加热干燥后的母粒落于存料腔114内进行保温存放,并随时用于输出与切片的混合;其中母粒干燥器1的结构如下:如图2所示,所述的母粒干燥器1包括筒体101,筒体101顶部设有进料管102、底部
设有出料管103,所述筒体101内设有所述的风干斗104和加热斗105,风干斗104通体设有风孔,在风干斗104内设有搅抖桨106,搅抖桨106的驱动轴与位于筒体101顶上的电机107传动连接,电机107转动后可以带动搅抖桨106转动,从而实现对风干斗104内母粒的搅拌;如图3和4所示,风干斗104外侧设有风罩108,风罩108的内表面是与风干斗104形状相配合的斜面109,在斜面109上布满出风槽110,这样使得从风罩108吹出的热风更好地吹向风干斗104,风干斗104通体设有风孔,热风穿过风孔可以对内部正处于搅拌状态的母粒进行热风风干,降低其含水率;所述加热斗105位于风干斗104下方,加热斗105的上端面通过杆体111设置有锥形导向器112,加热斗105的下端面设置有加热元件113,使得加热斗105具有加热功能,锥形导向器112可以将从风干斗落下的母粒更好地向周围分配,使母粒在加热斗105中更均匀地加热;加热斗105与筒体101底部之间的区域为所述的存料腔114,经加热斗105后的母粒可以存放于该存料腔114中,随时用于向下输出与干切片的混合。该母粒干燥器1还包括进风管115和出风管116,进风管115一端连接进风机117、另一端连接风罩108,在进风管115上设有加热夹套119;所述风干斗104上方设有集尘罩127,所述出风管116与集尘罩127相连接,在出风管116上设有空气过滤器120和抽风机118;所述进料管102、出料管103、进风管115、出风管116以及风干斗104和加热斗105的出口管上都设有阀门;将进料管102置于筒体101顶部偏心位置,这样电机107可以位于顶部正中位置便于搅拌,在筒体101内设置导向器128将从进料管102落下的母粒导向风干斗104内。
18.本实施例中在母粒干燥器对母粒干燥的第一步中具有对风干斗进行称重的步骤。所述筒体101内设有环状座124,环状座124上端面设有多根导杆125,所述风干斗104穿设在环状座124内,风干斗104的外翻的口沿供所述导杆125穿过,在风干斗104的口沿与环状座124之间设有称重传感器126,这个设计是用于对风干斗104达到预设重量时停止进料的控制,需要说明的是:如果风干斗104不具有称重功能,那么可以依靠控制进料时间来控制进料的量。
19.在生产时,上方母粒仓82内的母粒经进料管102进入母粒干燥器1并落入风干斗104内,电机107工作带动搅抖桨106转动,进风机117和加热夹套119工作形成向内吹的热风,热风通过风罩108内表面上的出风槽110向上吹,对风干斗104内的搅拌着的母粒进行风干,带走大部分母粒中水份,抽风机118工作,通过集尘罩127向外抽筒体101内顶部的空气,空气中因搅拌产生的母粒粉尘被滤除在空气过滤器120中,干净空气向外排放;当称重传感器126称得风干斗104达到预设重量时停止进料,进行风干一段时间(时间本领域技术人员可以根据实际情况选择,如5分钟)后热风停止,风干斗104出口管上的阀门打开将风干斗104中的母粒向下排放,在锥形导向器112的分配作用下进入加热斗105内并在加热斗中加热,在加热斗中加热干燥一段时间(时间本领域技术人员可以根据实际情况选择,如4分钟)后,加热斗105出口管上的阀门打开,将加热斗105内的母粒存放于存料腔114中,并随时准备向下输出,干燥后的切片和母粒在各自计量螺杆9的作用下按比例进入混料装置2中混合。
20.这种特有的母粒干燥方法结合了热风风干和加热干燥的优势,干燥初期含水量较高的母粒可通过热风得到有效干燥,并排出湿气;在加热斗105中进行接触性的加热,提高干燥效果,加热斗105热量来自于底面的加热元件113,可以是嵌装在底面上的电加热管或者分布在底面上的电热丝,而由于加热元件113位于存料腔114内顶部,加热元件113同样为
存料腔114提供了热量,加热了内部的空气,这样存料腔114具有了保温作用,可以有效防止干燥后的母粒返潮。称重传感器126可以感知风干斗104内的进粒量,将进入风干斗内的母粒控制在可确保风干效率地数量之内;这样两步合作,风干斗104完成作业后母粒进入加热斗105,此时风干斗104即可进行下一次的风干任务,而加热斗105只需在下一次的风干任务结束之间排空即可,因此可实现有效的连续生产,确保工艺所需的母粒配比量。采用本方法可以有效确保锦纶的产品质量。
21.本实施例所制得锦纶纤维断裂强度4.11cn/dtex,断裂伸长率27.1%,断裂强度变异系数cv%值6.1,断裂伸长变异系数cv%值9.2,条干均匀度cv%值1.18,性能良好。
22.实施例2:本实施例所描述的锦纶纤维的生产方法,与实施例1不同的是:s2熔融步骤中螺杆挤出机加热区一区温度250℃,二区温度260℃,三区温度268℃,四区温度268℃,五区温度265℃。
23.s4纺丝步骤中纺丝箱体5温度268℃。
24.s5吹风冷却步骤中侧吹风温度20℃,湿度68%。
25.s6集束上油步骤中:上油量为1.2%;s7卷绕成型步骤中:卷绕速度4500m/min。
26.本实施例所制得锦纶纤维断裂强度4.12cn/dtex,断裂伸长率27.2%,断裂强度变异系数cv%值6.0,断裂伸长变异系数cv%值9.1,条干均匀度cv%值1.19,性能良好。
27.实施例3:本实施例所描述的锦纶纤维的生产方法,与实施例1不同的是:s2熔融步骤中螺杆挤出机加热区一区温度248℃,二区温度258℃,三区温度265℃,四区温度268℃,五区温度265℃。
28.s4纺丝步骤中纺丝箱体5温度263℃。
29.s5吹风冷却步骤中侧吹风温度19℃,湿度66%。
30.s6集束上油步骤中:上油量为1.1%;s7卷绕成型步骤中:卷绕速度4300m/min。
31.本实施例所制得锦纶纤维断裂强度4.10cn/dtex,断裂伸长率27.3%,断裂强度变异系数cv%值6.0,断裂伸长变异系数cv%值9.0,条干均匀度cv%值1.19,性能良好。
32.实施例4:本实施例所描述的锦纶纤维的生产方法,与实施例1不同的是:s2熔融步骤中螺杆挤出机加热区一区温度250℃,二区温度258℃,三区温度265℃,四区温度268℃,五区温度265℃。
33.s4纺丝步骤中纺丝箱体5温度264℃。
34.s5吹风冷却步骤中侧吹风温度19℃,湿度67%。
35.s6集束上油步骤中:上油量为1.1%;s7卷绕成型步骤中:卷绕速度4400m/min。
36.本实施例所制得锦纶纤维断裂强度4.10cn/dtex,断裂伸长率27.2%,断裂强度变异系数cv%值6.0,断裂伸长变异系数cv%值9.0,条干均匀度cv%值1.20,性能良好。
37.实施例5
上述实施例中,热风直接排放,为了提高循环热风的利用率,所述的母粒干燥器1搅拌风干时阶段性采用循环热风。
38.母粒干燥器1与实施例1不同之处在于:如图5所示,所述的进风机117的进口与抽风机118的出口之间连接有循环风管121,循环风管121上靠近抽风机118的一端设有三通阀一122、靠近进风机117的一端设有三通阀二123;在对母粒进行风干时包括两步:a1:三通阀一122和三通阀二123工作使循环风管121处于隔断状态,进风机117从外部直接进风、抽风机118向外部直接排风;此时工作方式实质上同实施例1,可以用于排出初始风干时的大部分湿空气;a2:三通阀一122和三通阀二123工作使循环风管121处于连通状态,热风在进风机117、筒体101、抽风机118和循环风管121之间循环;此时在大部分湿空气排出的情况下可以采用循环热风,同时降低或适时关闭加热夹套119,以节省电能。
39.本实施例所采用的循环热风方案同样适合于实施例2-4。
40.实施例6:常规空气过滤器不具有排出母粒粉尘的功能,需要定期拆开维护,不及时维护容易影响空气过滤的效率和能力,使排风不畅,进而会干扰热风干燥的效率,因此本公司将空气过滤器设计成定时可自动清理母粒粉尘,实施例1不同的是空气过滤器的结构如下:如图6和7所示,所述的空气过滤器包括机壳130、伸缩罩131、集尘斗132、集尘罐133和升降器134,机壳130包括顶板135和顶板135下方四面连续的外壁136和内壁137,外壁136底面设有内翻边138与内壁137底部连接,内壁137中间设有过滤网139,外壁136和内壁137之间形成抽气腔140;空气过滤器120的进口管道153设在顶板135上并与内壁137围成的空间连通,出口管道154设在外壁136上并与抽气腔140连通;所述伸缩罩131连接在机壳130和集尘斗132之间;集尘斗132的上端面通过支杆152连接有封底板141,如图8,封底板141的四条边上都设有凹槽142,凹槽142内设有转轴143,转轴143上穿设有翻板144,转轴143在翻板144上的位置是更靠近翻板144的内端,呈偏心状,翻板144外端设有清洁毛刷145,翻板144内端顶部设有l形片146;凹槽142的侧壁上设有防止翻板144内端过度偏转的凸筋147;所述的集尘罐133连接在集尘斗132的下方,所述升降器134驱动集尘斗132升降。升降器134可采用气缸。
41.其中,所述集尘斗132外设有抱箍148,抱箍148具有一个水平延伸的横向部149,所述升降器134的升降杆顶部与该横向部149的底面连接;所述升降器134设在筒体101侧面,所述机壳130也通过安装架150设在筒体101侧面;筒体侧面还设有导向杆151,导向杆151穿过横向部149的端部,升降器134采用气缸,气缸动作可以推动横向部149在导向杆151上平稳地升降,同时带动连成一体式的集尘斗132和集尘罐133升降;明显地,升降器134驱动集尘斗132升降的方式不限于此。
42.本实施例所述的空气过滤器串在出气管116上,抽风机118工作向外抽气,封底板141置于内壁137底部,对内壁137围成的区域底面起主要的封口作用,由于翻板在转轴上偏心的设置方式,翻板呈耷拉状;抽风机118工作后,空气过滤器120的的出口管道、抽气腔140都成了负压,这样筒体101内的空气经集尘罩127后通过空气过滤器120的的进口管道进入内壁137之间,经过滤网139过滤后进入抽气腔140,并通过空气过滤器120的的出口管道及抽风机118向外输送;由于抽气腔140在抽风机118工作时呈负压,所产生的母粒粉尘被附在
了过滤网139上;在热风干燥的间隙,如风干斗104下料时,进风机和送风机停止工作, 此时空气过滤器120内压力平稳,升降器134可以驱动集尘斗132上行,集尘斗132通过支杆152带动封底板141上行,由于封底板141上的翻板144是耷拉状的(如图10),因此清洁毛刷145无法与过滤网相接触 ,伸缩罩131被压缩,封底板141行至最高处,l形片146与顶板135相抵,在顶板135的作用下,l形片146被矫正至水平状态,翻板144由此成为水平(如图9),清洁毛刷145与对应面的过滤网接触,升降器134可以驱动集尘斗132下行,集尘斗132通过支杆152带动封底板141下行,下行过程中,翻板144成了水平状,清洁毛刷145呈涨紧状,随着封底板141的下行,清洁毛刷145将附在过滤网139上的母粒粉尘刷下来,直至落于集尘罐133,由于封底板141下行时清洁毛刷145受到向上的反向作用力,翻板144无法再回到耷拉状,直至封底板141落于内壁137下方,清洁毛刷145受到的反向作用力消失,翻板144再次呈耷拉状,而屡次刷落的母粒粉尘积在经集尘斗导向后落于集尘罐133中,可以定期打开集尘罐133底部的仓门155进行清理,这样的方式,过滤网139上的母粒粉尘可以被及时清落,过滤网139的透风能力和过滤能力都能得到保证。
43.其中:封底板141与内壁137之间有间隙,间隙的要求:在封底板141上行时,耷拉状的翻板使得清洁毛刷145与内壁137不接触,在封底板141下行时,水平状的翻板使得清洁毛刷145与内壁137接触且过滤网139可以提供足够的反向作用力防止水翻板耷拉,间隙可控制在5-10毫米,工作时也使得封底板141在底部尽量起到封口作用,使封底板141下方气压相对稳定。
44.本实施例所采用的特有的空气过滤器的方案同样适合于实施例2-5。
45.实施例7:本实施例描述一种锦纶纤维的生产方法用于生产抗菌锦纶纤维,是一种抗菌锦纶纤维的生产方法,它与实施例1的区别在于:所述母粒是采用锦纶6切片与纳米银磷酸盐共混造粒制得的抗菌母粒,切片与抗菌母粒重量配比100:5(本领域技术人员可以选择其他比例)。
46.所制得的锦纶纤维在保持锦纶原有优良性能同时具有良好的抗菌性能,可以制成各种抗菌面料。
47.本实施例也可采用实施例2-6的母粒干燥器和干燥方法来生产本实施例所述抗菌锦纶纤维。
48.实施例8:本实施例描述一种锦纶纤维的生产方法用于生产阻燃锦纶纤维,是一种阻燃锦纶纤维的生产方法,它与实施例1的区别在于:所述母粒采用阻燃母粒,该阻燃母粒按重量配比组成如下:切片载体︰功能粉体︰分散剂︰偶联剂︰抗氧剂︰热稳定剂=81.5︰17︰0.2︰0.1︰0.2︰0.1,其中:切片载体为锦纶6切片;功能粉体由磷系芳香聚酰有机胺化合物在烘箱内经180℃干燥活化制得;分散剂为高分子蜡;偶联剂为si900 、抗氧剂为b215、热稳定剂为c101;上述材料混合后经挤出机熔融造粒制得阻燃母粒。
49.所制得的锦纶纤维在保持锦纶原有优良性能同时具有良好的阻燃性能,可以制成各种阻燃布。
50.本实施例也可采用实施例2-6的母粒干燥器和干燥方法来生产本实施例所述抗菌
锦纶纤维。
51.实施例9:本实施例所描述的锦纶纤维的生产方法,包括如下步骤:s1混料:将干燥后的切片与经母粒干燥器1干燥后的母粒一起添加至混料装置2中混合;所述母粒采用色母粒;s2熔融:经混料装置2混合后的切片与母粒一起进入螺杆挤出机3内进行熔融挤出,得到纺丝熔体;s3动态混合:所述纺丝熔体从螺杆挤出机3流出后进入动态混合装置4进行动态混合;s4纺丝:将动态混合后的纺丝熔体输送至纺丝箱体5,经计量泵输送至各个纺丝组件中进行纺丝生成纤维; s5吹风冷却:采用侧吹风装置6对纤维进行吹风冷却; s6集束上油:对纤维进行集束上油;s7卷绕成型:将上油后的丝束进行拉伸和预网络,最后由卷绕机7卷绕成型;所述母粒干燥器1对母粒干燥时包括三个步骤,第一步先在风干斗104中进行搅拌风干,同时对母粒干燥器1进行抽气除尘,利用空气过滤器120除去搅拌时产生的母粒粉尘,第二步经搅拌风干后的母粒落入加热斗105中进行加热干燥,第三步将加热干燥后的母粒落于存料腔114内进行保温存放,并随时用于输出与切片的混合,其中,各工艺参数可由本领域技术人员根据常规需求设定。
52.需要说明的是,本专利的保护范围不限于上述的几个实施例,采用本技术特有母粒干燥方法生产功能性锦纶、锦纶色丝等,应当落于本专利保护范围 。