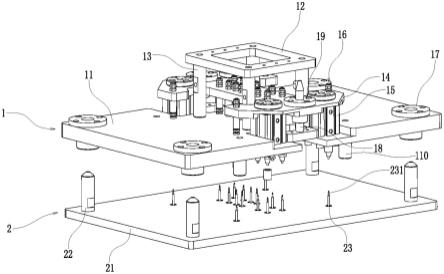
1.本实用新型涉及一种自动埋钉机构。
背景技术:2.为了方便产品的装配,通常会将螺母或螺钉预先压入到产品的配件中使之成为一体,这种方法就成为埋钉;随着加工技术的不断发展,目前的埋钉大都借助埋钉设备来自动完成,但是现有的埋钉设备定位精度较低,一旦螺母或螺钉的数量较多时,就会导致螺母或螺钉的埋入位置发生了偏差,致使产品因无法装配而造成报废,加工不良率较高,只能通过减少单次同时埋入螺母或螺钉的数量来解决,但却导致加工效率较低,有待于进一步改进。
技术实现要素:3.针对上述现有技术的现状,本实用新型所要解决的技术问题在于提供一种大幅度的提高了定位精度,进而显著提高加工效率并显著降低了加工不良率的自动埋钉机构。
4.本实用新型解决上述技术问题所采用的技术方案为:一种自动埋钉机构,包括上模以及设于上模下方并与上模相互配合的下模,其特征在于,所述上模包括横向设置的压板、横向设于压板上方的顶板、多个竖直固定在压板与顶板之间的连接柱、横向设于压板与顶板之间的牵引板、多个固定在压板顶部的牵引气缸、以及多个竖直设于牵引板与压板之间的压入组件;每个所述牵引气缸的伸缩端均竖直向上设置并均固定在牵引板上;所述下模包括横向设于压板下方的底板以及多个竖直嵌设在底板中的顶杆,所述顶杆的数量和位置均与压入组件的数量和位置相互配合;所述压入组件包括竖直嵌设在压板中的导向套、竖直穿插设置在牵引板中的压杆、两个套设螺接在压杆上端并上下叠置的螺母、以及套设在压杆上的弹簧,所述压杆的下端向外形成有第一台阶圈,所述弹簧的上下两端分别顶紧在牵引板的底部和第一台阶圈的顶部以使下方的一个螺母压紧在牵引板的顶部,所述第一台阶圈的端部中心向下形成有压针,所述压针的端部向下活动穿插设置在导向套中;所述压针的端部中心开设有压孔,对应地,所述顶杆的端部中心向上形成有顶针,每个顶杆上的所述顶针均与对应的一个压入组件中的压杆上的压孔相互配合。
5.优选地,所述导向套的外壁上至少开设有两个沿圆周方向等角度均匀分布的沉孔,每个所述沉孔中还均嵌入有一个钢珠,每个所述沉孔的底面上均开设有一个通孔;每个所述钢珠的内侧均穿过对应的一个通孔并均伸入到导向套的内部且滚动贴合在压针的外壁上。
6.优选地,所述导向套上还套设固定有压套,所述压套设于每个沉孔的外围,每个所述钢珠的外侧均滚动贴合在压套的内壁上。
7.优选地,所述第一台阶圈的顶部还向外形成有第二台阶圈,所述弹簧的下端套设在第二台阶圈外。
8.优选地,所述压板的顶部还固定有若干个第一定位柱,对应地,所述牵引板中还嵌设有相同数量的第一定位套,每个所述第一定位柱均活动插入在对应的一个第一定位套
中。
9.优选地,所述底板的顶部还固定有若干个第二定位柱,对应地,所述压板中还嵌设有相同数量的第二定位套,每个所述第二定位柱均活动插入在对应的一个第二定位套中。
10.优选地,所述压板的底部还固定有若干个限位柱。
11.优选地,所述导向套的外周面还向外形成有限位圈,所述限位圈的上端贴合在压板的底部。
12.与现有技术相比,本实用新型的优点在于:本实用新型大幅度的提高了定位精度,即使螺母或螺钉的数量较多也能一次性的同时埋入以显著提高加工效率,并有效避免埋入位置发生偏差以保证产品能顺利装配,进而彻底避免报废的发生以显著降低了加工不良率。
附图说明
13.图1为本实用新型的左前侧结构图;
14.图2为本实用新型的压入组件的分解结构图。
具体实施方式
15.除非另外定义,本实用新型使用的技术术语或者科学术语应当为本实用新型所属领域内具有一般技能的人士所理解的通常意义。本实用新型中使用的“第一”、“第二”以及类似的词语并不表示任何顺序、数量或者重要性,而只是用来区分不同的组成部分。“包括”或者“包含”等类似的词语意指出现该词前面的元件或者物件涵盖出现在该词后面列举的元件或者物件及其等同,而不排除其他元件或者物件。“连接”或者“相连”等类似的词语并非限定于物理的或者机械的连接,而是可以包括电性的连接,不管是直接的还是间接的。“上”、“下”、“左”、“右”等仅用于表示相对位置关系,当被描述对象的绝对位置改变后,则该相对位置关系也可能相应地改变。
16.为了保持本实用新型实施例的以下说明清楚且简明,本实用新型省略了已知功能和已知部件的详细说明。
17.如图1~2所示,一种自动埋钉机构,包括上模1以及设于上模1下方并与上模1相互配合的下模2;上模1包括横向设置的压板11、横向设于压板11上方的顶板12、多个竖直固定在压板11与顶板12之间的连接柱13、横向设于压板11与顶板12之间的牵引板14、多个固定在压板11顶部的牵引气缸15、以及多个竖直设于牵引板14与压板11之间的压入组件16;每个牵引气缸15的伸缩端均竖直向上设置并均固定在牵引板14上;下模2包括横向设于压板11下方的底板21以及多个竖直嵌设在底板21中的顶杆23,顶杆23的数量和位置均与压入组件16的数量和位置相互配合;压入组件16包括竖直嵌设在压板11中的导向套161、竖直穿插设置在牵引板14中的压杆163、两个套设螺接在压杆163上端并上下叠置的螺母164、以及套设在压杆163上的弹簧162,压杆163的下端向外形成有第一台阶圈1631,弹簧162的上下两端分别顶紧在牵引板14的底部和第一台阶圈1631的顶部以使下方的一个螺母164压紧在牵引板14的顶部,第一台阶圈1631的端部中心向下形成有压针1632,压针1632的端部向下活动穿插设置在导向套161中;压针1632的端部中心开设有压孔1634,对应地,顶杆23的端部中心向上形成有顶针231,每个顶杆23上的顶针231均与对应的一个压入组件16中的压杆
163上的压孔1634相互配合。
18.导向套161的外壁上至少开设有两个沿圆周方向等角度均匀分布的沉孔1611,每个沉孔1611中还均嵌入有一个钢珠166,每个沉孔1611的底面上均开设有一个通孔1612;每个钢珠166的内侧均穿过对应的一个通孔1612并均伸入到导向套161的内部且滚动贴合在压针1632的外壁上。
19.导向套161上还套设固定有压套165,压套165设于每个沉孔1611的外围,每个钢珠166的外侧均滚动贴合在压套165的内壁上。
20.第一台阶圈1631的顶部还向外形成有第二台阶圈1633,弹簧162的下端套设在第二台阶圈1633外。
21.压板11的顶部还固定有若干个第一定位柱18,对应地,牵引板14中还嵌设有相同数量的第一定位套19,每个第一定位柱18均活动插入在对应的一个第一定位套19中。
22.底板21的顶部还固定有若干个第二定位柱22,对应地,压板11中还嵌设有相同数量的第二定位套17,每个第二定位柱22均活动插入在对应的一个第二定位套17中。
23.压板11的底部还固定有若干个限位柱110。
24.导向套161的外周面还向外形成有限位圈1613,限位圈1613的上端贴合在压板11的底部。
25.使用方法:将底板21固定在机台上,然后在顶板12上方设置一个升降气缸并使升降气缸的伸缩端竖直向下并固定在顶板12上,再将工件放置在底板21的顶部并使每个顶杆23上的顶针231均向上伸出到工件中的预留孔上方以完成定位,随后在每个顶针231的端部均放置一个螺母;驱动升降气缸的伸缩端向外伸出以带动顶板12竖直下移,进而借助多个连接柱13带动压板11竖直下移,直到每个限位柱110的端部均压紧在工件的顶部,此时的每个第二定位柱22均插入到对应的一个第二定位套17中以保证压板11与底板21定位精确。
26.接着,驱动每个牵引气缸15的伸缩端均向内收缩以带动牵引板14竖直下移,进而带动每个压入组件16中的压杆163竖直下移以使每个压杆163上的压针1632的端部均伸出到对应的一个导向套161的下端开口处外部,此时的每个第一定位柱18均插入在对应的一个第一定位套19中以保证每个压杆163上的压针1632与对应的一个顶杆23上的顶针231端部定位精确;继续驱动每个压入组件16中的压杆163竖直下移以将每个套设在压针1632上的螺母压入到工件中,此过程中,每个压入组件16中的弹簧162均被压缩。
27.埋钉完成后,驱动每个牵引气缸15的伸缩端均向外伸出以带动牵引板14竖直上移,进而带动每个压针1632的端部均回退到对应的一个导向套161的内部,每个被压缩的弹簧162的反弹力在此时起到了加速复位的作用;再驱动升降气缸的伸缩端向内收缩以带动顶板12竖直上移,进而借助多个连接柱13带动压板11竖直上移,直到每个限位柱110的端部均离开工件的顶部,最后取下埋入有螺母的工件并将另一个工件也按照相同方法放置到底板21上,以此形成一个循环。
28.每个压针1632在上下移动时,每个钢珠166均会沿压针1632的外周面滚动,进而保证了压针1632移动的稳定性和顺畅度。
29.本实用新型大幅度的提高了定位精度,即使螺母或螺钉的数量较多也能一次性的同时埋入以显著提高加工效率,并有效避免埋入位置发生偏差以保证产品能顺利装配,进而彻底避免报废的发生以显著降低了加工不良率。
30.最后应说明的是:以上实施例仅用以说明本实用新型的技术方案,而非对其限制;尽管参照前述实施例对本实用新型进行了详细的说明,本领域的技术人员应当理解,其依然可以对前述各实施例所记载的技术方案进行修改,或者对其中部分技术特征进行同等替换;而这些修改或者替换,并不使相应技术方案的本质脱离本实用新型各实施例技术方案的精神与范围。