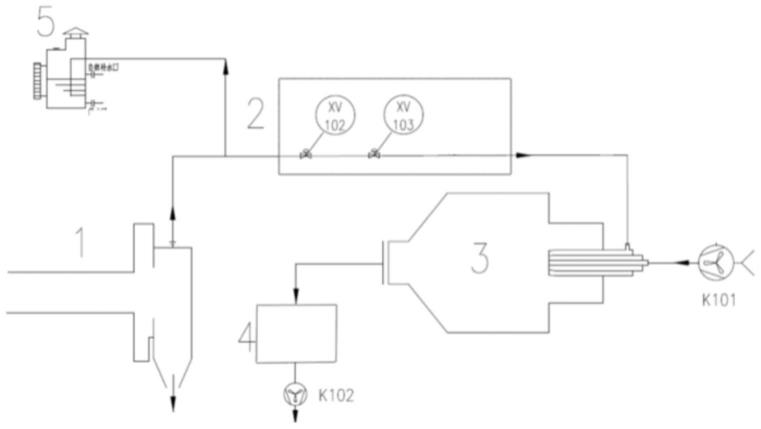
1.本发明涉及一种生物质热解稳压系统及其方法。
背景技术:2.有机固体废弃物,主要包括农林生物质、生活垃圾及其衍生物、含油污泥、水处理污泥等。有机固废主要处置方案有:焚烧、填埋、热解气化等。填埋方案成本高,且无法从根本上实现有机固废的无害化和资源化,在更多情况下是作为对无法暂时处置的固废和危废的暂存方案。当前焚烧技术在中小规模下存下以下瓶颈:(1)烟气量大,小规模下烟气处理成本尤其高;(2)难以做到固废的资源化,焚烧产生的烟气热能属于低品位能量,参数不高,难以做高值化利用;(3)焚烧必须具备规模效应,而当前大量固废,尤其单体大宗危废无法实现集中式大规模处理。
3.热解技术是指在无氧条件下利用温度加热有机固废,使有机固废中有机质组分发生热裂解反应转化为热解气和固体残渣,进而将固体残渣有机杂质含量降低至规范要求以下,该方法是目前油泥、干垃圾、工业废盐等有机固废无害化/资源化利用的方式。热解气主要成分为氢气、一氧化碳、二氧化碳、水蒸气以及气态烃等物质,也会含有少量焦油和粉尘。焦油和粉尘的存在使得热解气冷凝以后再利用的方案易出现管道堵塞等问题。此外,热解气未经冷凝直接气化或焚烧的工艺方案也具有热效率更高的优点,正越来越多应用于有机固废资源化利用领域。
4.由于有机固废常采用柱塞泵进料,柱塞泵进料有脉冲进料的特征。有机固废热解常采用回转式反应器或螺旋式反应器,物料在内部存在周期性的翻滚搅动,从而导致热解设备产生的热解气存在一定的波动性。为保证物料在反应器内翻滚从而实现彻底脱除有机物,这些反应器常存在较大的转动部件,而反应器的固相进料出料部件处于相对静止,静止部件和转动部件存在较大的动密封连接位置,易发生气体泄漏,若采用微负压操作,现场操作人员不易发现这些泄漏,因此在实际生产过程中,为保证系统和人员的安全,热解反应器常采用+20~+500pa范围内的微正压操作。而有基本机固废柱塞泵进料脉冲进料的特征,进一步导致热解设备产生的热解气存在一定的波动性;当热解气量低时,热解反应器操作压力由微正压变成负压,极易使下游设备的高温空气或周围环境的空气吸入热解反应器发生爆燃。
5.为稳定有机固废热解反应器内的操作压力,增加有机固废热解系统对热解气量波动的耐受能力,在有机固废热解系统中,需要配置相应的稳压子系统,以保证热解反应器运行工况的稳定性。而热解气冷却易出现焦油冷凝结焦的特征,对稳压方案提出了较高的要求。
6.现有技术中,有机固废或者生物质热解气化系统由于产生的燃气流量存在系统波动,为保证向后续利用系统稳定供气,常采用缓冲罐作为稳压方案。如cn 102559289 a(生物质合成气冷却、洗涤工艺及系统)中,针对1000℃以上的高温含尘含焦油生物质合成气,在经过一系列激冷、余热利用、除尘、电捕焦等净化处理后,设置一个稳压罐作为稳压方案;
再如cn 108728143 a(生物质非原位催化热解液化系统)中,生物质经过气化液化过程中,为保证燃气流量稳定,也采用稳压罐作为系统稳压方案。以缓冲罐作为稳压方案的优点是方案成熟,比较适用于燃气经过净化后再进行利用的相关工艺;对于未净化的高温含尘含焦油燃气,采用该方案容易出现焦油结焦析出。
7.另一种较为常见的稳压方案时应用于上下游存在一定压差情形的燃气稳压阀,相应的案例可参见cn 204420240 u和cn 206637072 u。这类燃气稳压阀均涉及较为复杂的结构,导致此类方案仅适用于较为洁净的燃气,同时此类阀门压降较大,适用于上下游存在一定压差的场景,对常采用微正压操作的且热解气洁净度相对较差的有机固废热解装置的适用性也比较差。
技术实现要素:8.本发明针对有机固废热解利用系统对热解气压力稳定有较高要求,而热解反应器微正压的操作压力,热解气高含尘、冷却易出现焦油冷凝结焦等特征导致现有的稳压罐、稳压阀等方案无法有效解决有机固废热解气直接利用的场景需求的缺陷,提供了一种生物质热解稳压系统及其方法,具有设备成本低,操作简单,不易结焦,成本低等特点。
9.一种生物质热解稳压系统,其包括热解反应装置、水封罐、阀门组和热解气利用装置;所述热解反应装置的热解气出口和所述热解气利用装置的进料口通过第一管道连接,所述第一管道上设有所述阀门组;所述热解反应装置的热解气出口还设有第二管道,所述第二管道和所述水封罐连接,用于实现水封稳压;其中,所述阀门组包括若干串联的流量调节阀。
10.较佳地,所述流量调节阀的个数为2~4个。
11.较佳地,所述流量调节阀为蝶阀、球阀或套筒调节阀,更佳地为蝶阀。
12.较佳地,所述热解反应装置为回转式反应器或螺旋式反应器。
13.较佳地,所述热解气利用装置为气化炉或热风炉。
14.较佳地,所述生物质热解稳压系统,还包括鼓风机,所述热解气利用装置的进风口通过管道和所述鼓风机连通。
15.较佳地,所述生物质热解稳压系统,还包括热量利用单元,所述热量利用单元的进料口和所述热解气利用装置的出料口连接,所述热量利用单元用于将所述热解气利用装置中的产物燃烧向外界提供能量;所述热量利用单元较佳地为焚烧炉或锅炉;
16.其中,所述生物质热解稳压系统还包括引风机,所述热量利用单元的出料口和所述引风机连通。
17.一种生物质热解稳压方法,其采用如上述所述的生物质热解稳压系统进行,按下述条件进行:
18.生物质热解的起炉阶段:建立所述水封罐的水封水位,所述热解反应装置和所述水封罐处于连通并运行工况状态;开启所述阀门组的所述流量调节阀并设置阀门开度;将所述热解反应装置和所述热解气利用装置加热;
19.生物质热解的增大负荷阶段:维持所述热解反应装置和所述热解气利用装置微负压运行;以启动负荷开启所述热解反应装置的进料装置,再增大所述进料装置的进料负荷,配合调整所述流量调节阀的阀门开度,所述热解反应装置运行为正压力运行;所述热解气
利用装置运行为负压力运行;
20.生物质热解的运行阶段:待所述进料装置的进料负荷处于标准进料负荷时,配合调整所述流量调节阀的阀门开度,所述热解反应装置运行的压力为正压力运行;所述热解气利用装置运行的压力为负压力运行;
21.生物质热解的停炉阶段:停止所述热解反应装置的进料,待所述热解反应装置内的原料彻底排空后,降低所述热解反应装置及所述热解气利用装置的运行温度至停炉温度以下,关闭所述热解反应装置及所述热解气利用装置。
22.本发明中,所述起炉阶段中,所述水封水位可根据所述热解反应装置的压力要求建立,所述水封水位为水封管至水面的距离,较佳地,所述水封水位为20mm~200mm,例如40mm。
23.较佳地,所述起炉阶段中,所述热解反应装置加热至450~650℃,例如500℃。
24.较佳地,所述起炉阶段中,所述热解气利用装置加热至650~1050℃,例如750℃。
25.较佳地,所述运行阶段中,所述热解反应装置的运行压力为20~400pa。
26.较佳地,所述运行阶段中,所述热解气利用装置的运行压力为-50~-550pa。
27.本发明中,所述增大负荷阶段中,在所述启动负荷开启前,所述维持所述热解反应装置和所述热解气利用装置微负压运行的方式,可为通过启动引风机进行维持。
28.在本发明某一优选实施方案中,所述的生物质热解稳压方法,可按下述条件进行:
29.所述起炉阶段:所述生物质热解稳压系统的所述流量调节阀为蝶阀,将两个所述蝶阀的阀门开度设置位于40
°
~60
°
之间;所述生物质热解稳压系统还包括引风机,启动所述引风机,所述引风机的运行频率为8~12hz;
30.所述增大负荷阶段:维持所述热解反应装置和所述热解气利用装置微负压运行;以30%~70%负荷开启所述热解反应装置的进料装置;
31.再增大所述进料装置的进料负荷,所述热解反应装置运行的压力为100~200pa;所述热解气利用装置运行的压力为-250~-500pa;配合两个所述蝶阀的阀门开度为50
°
~60
°
之间;并依据上述压力调整所述引风机的频率为12~20hz;
32.所述运行阶段:待所述进料装置的进料负荷处于标准进料负荷时,所述热解反应装置运行的压力为150~250pa;所述热解气利用装置运行的压力为-550~-300pa,配合两个所述蝶阀的阀门开度位于55~70
°
之间,并依据上述压力调整所述引风机的频率为20~35hz;
33.所述停炉阶段:停止所述热解反应装置的进料,待所述热解反应装置内的原料彻底排空后,降低所述热解反应装置及所述热解气利用装置的运行温度至停炉温度以下,关闭所述热解反应装置及所述热解气利用装置,关闭所述引风机。
34.本发明中,为实现稳定操作压力以及防下游气体返混,本发明的系统配置了所述阀门组。当热解气通过一定阀门开度的所述流量调节阀时,就会形成局部压阻,进而对热解气流动形成一定阻力,使所述热解反应装置和所述热解气利用装置操作压力差大于一定数值,通过压差从而实现两者之间的防返混。由于所述流量调节阀的阀门开度对局部助力系数较为敏感,且所述流量调节阀的阀门开度与气流局部阻力系数的关系已经被明确,在气流密度、粘度等常规物性已知的情况下,可以通过阀门开度以及下游风机的调节,实现对所述热解反应装置以及所述热解气利用装置操作压力的准确控制。
35.本发明中,当所述阀门组的管线仅配置一个所述流量调节阀时,所述流量调节阀常需要保持一个较低的开度才能实现上下游的压差分配,此时阀门开度与管道局部阻力非常敏感,较容易出现难以将阀门开度调整至需要的压阻,且当系统热解气量波动时,压差变化较大,易导致系统操作压力波动。通过串联配置多个所述流量调节阀,可以实现阀门维持在较高的开度,此时,系统热解气量波动对压差的影响也会维持在较低的水平,实现维持所述热解反应器微正压操作压力的目标,此外,阀门开度较高可以避免粉尘在这些位置沉降聚集导致的堵塞,当然过多的所述流量调节阀的数量也会导致系统成本和运行控制复杂度的上升。
36.本发明中,当出现热解气量波动过大时,系统压力变化可能会超出所述阀门组的调节范围,为解决该问题,本发明的系统配置了所述水封罐,在系统正常运行时,所述水封罐配置一定的水封液位高度(水封高度形成的静液柱压与所述热解反应装置的最高操作压力一致),若所述热解反应装置的操作压力高于设定的最高操作压力时,热解气会自动鼓泡排出降低所述热解反应装置操作压力。
37.本发明中,热解气中易含有较多焦油,在热解气管道前流过时可能会出现焦油冷凝析出。可通过在热解气管线上配置密实保温层实现管线保温目标,保证热解气在管线上不发生明显降温,从而有效防止焦油析出。
38.本发明中,通常所述热解反应装置的静止部件和转动部件存在较大的动密封连接位置,气密性较差。为保证所述热解反应装置运行过程的安全性,所述热解反应装置常采用+20~+400pa左右的微正压操作,热解气生成量波动易导致所述热解反应装置操作压力变化过大,进而导致所述热解反应装置的操作压力超过动密封装置设计值或者下游的所述热解气利用装置的烟气/气化气返混进入所述热解反应装置。
39.在符合本领域常识的基础上,上述各优选条件,可任意组合,即得本发明各较佳实例。
40.本发明所用试剂和原料均市售可得。
41.本发明的积极进步效果在于:
42.(1)本发明的生物质热解稳压系统,依靠阀门组、水封水罐等设备,可以满足有机固废微正压热解系统的含尘含焦油热解气的稳压需求;在实现稳压的情况下,通过多个阀门的压力分配,有效实现上下游的压差分布,从而实现热解气的防返混功能;系统实现设备成本低,操作简单;
43.(2)本发明的生物质热解稳压系统方法,能稳定操作压力、防返混、防焦油冷凝析出,兼顾系统紧急排放。
附图说明
44.图1为本发明实施例1的生物质热解稳压系统示意图。
45.附图标记说明:
46.回转式反应器 1
47.阀门组 2
48.热风炉 3
49.热量利用单元 4
50.水封罐 5
51.鼓风机 k101
52.引风机 k102
具体实施方式
53.下面通过实施例的方式进一步说明本发明,但并不因此将本发明限制在的实施例范围之中。下列实施例中未注明具体条件的实验方法,按照常规方法和条件,或按照商品说明书选择。
54.实施例1
55.一种生物质热解稳压系统,如图1所示。其包括回转式反应器1、水封罐5、阀门组2、热风炉3、热量利用单元4、鼓风机k101和引风机k102;回转式反应器1的热解气出口和热风炉3的进料口通过第一管道连接,第一管道上设有阀门组2;回转式反应器1的热解气出口还设有第二管道,第二管道和水封罐5连接,用于实现水封稳压;其中,阀门组2包括2个串联的蝶阀。
56.热风炉3的进风口通过管道和鼓风机k101连通。
57.热量利用单元4的进料口和热风炉3的出料口连接,热量利用单元4用于将热风炉3中的产物燃烧向外界提供能量;
58.其中,生物质热解稳压系统还包括引风机k102,热量利用单元4的出料口和引风机k102连通。
59.生物质热解稳压方法
60.上述的生物质热解稳压系统,该系统处理目标是干垃圾的筛上物,该系统的处理量为200kg/h,下游热解气利用装置为热风炉3,热解气管道内径为100mm,管道长度为3m,满负荷运行时,热解气量为562m3/h,热风炉3烟气经热量利用及喷淋后,体积流量为2200m3/h(经喷淋烟气40℃),气体密度为0.445kg/m3,气体粘度为0.000043pas,引风机k102额定风压3.0kpa,额定流量4000m3/h,回转式反应器1最大在操作压力为400pa。
61.(1)、起炉阶段
62.起炉阶段:建立水封罐5的水封水位至40mm;
63.回转式反应器1和水封罐5处于连通并运行工况状态;回转式反应器1加热至500℃,回转式反应器1加热至750℃;开启两个蝶阀,并将阀门开度分别设置为50
°
和60
°
;启动引风机k102,将运行频率调整至10hz;
64.(2)、增大负荷阶段:
65.回转式反应器1和热风炉3微负压运行;
66.以50%负荷启动回转式反应器1的进料装置,同时启动鼓风机k101,根据热风炉3的热电偶示数增大引风机k102的运行频率,使热风炉3运行温度逐步上升至设计运行温度1100℃;
67.根据回转式反应器1的压力示数变化,逐步增大引风机k102运行频率至15hz,回转式反应器1运行压力约50~150pa微正压,热风炉3处于-50~-150pa微负压运行;
68.待回转式反应器1进出料稳定后,维持回转式反应器1运行稳定,此时,管道及局部阻力为300pa,维持热风炉3操作压力为-150pa,回转式反应器1的操作压力为150pa,当回转
式反应器1内的热解气生成量在85~115%范围内波动时,可维持回转式反应器1的67~247pa的微正压操作压力;
69.将阀门组2的两个蝶阀阀门开度分别设置成55
°
和60
°
,调整引风机k102的运行频率至13hz,将回转式反应器1的运行压力稳定至50~200pa左右的微正压;
70.增大进料系统的进料负荷,根据回转式反应器1的压力示数变化,增大阀门组2的阀门开度,配合两个蝶阀的阀门开度均为60
°
;
71.逐步增大引风机k102运行频率至25hz,保证回转式反应器1处于约100~200pa的微正压操作,使热风炉3运行压力处于约-250~-500pa的微负压;
72.在上述过程中,调整增大鼓风机k101,使热风炉3运行温度处于目标温度以上。
73.(4)运行阶段
74.稳定操作负荷,微调调整引风机k102运行频率,此时,管道及局部阻力为708pa,维持热风炉3操作压力为-550pa,回转式反应器1的操作压力为158pa,配合两个所述蝶阀的阀门开度均为60
°
;
75.当回转式反应器1内的热解气量在90~110%范围内波动时,可维持回转式反应器1的23~306pa的微正压操作压力。
76.(5)停炉阶段
77.停止回转式反应器1进料柱塞泵进料;
78.随着回转式反应器1内物料减少(根据热风炉3热电偶温度变化),逐步关小鼓风机k101运行频率,使热风炉3运行温度处于设计目标温度1100℃以上;
79.根据回转式反应器1和热风炉3的操作压力,逐步关小引风机k102的运行频率,同时关小阀门组2的阀门开度;
80.停止进料2小时后,待确保回转式反应器1内物料彻底清空,开始降温过程;
81.待回转式反应器1和热风炉3运行温度下降至停炉温度,关闭风机鼓风机k101和引风机k102,关闭回转式反应器1的转动电机和热风炉3。
82.本实施例1的生物质热解稳压系统经过系统设计,在生物质热解过程中,在保证生物质充分热解燃烧和利用的同时,实现了对回转式反应器1以及热风炉3的操作压力的准确控制和温度的调节,系统运行中无返混、焦油冷凝析出。