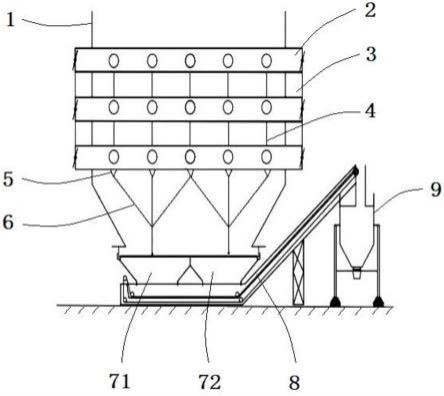
1.本实用新型涉及一种前后墙对冲燃烧的煤粉锅炉,尤其是一种前后墙对冲燃烧锅炉二次风道自吸式输灰系统。
背景技术:2.公知的,前后墙对冲燃烧的煤粉锅炉(简称前后墙对冲燃烧锅炉)是将一定数量的旋流式燃烧器布置在两面相对的炉墙上,形成对冲火焰的燃烧方式的燃烧没备。其主要优点是上部炉膛宽度方向上的烟气温度和速度比较均匀,使过热蒸汽温度偏差较小,并可降低整个过热器和再热器的金属最高温度点。
3.目前,前后墙对冲燃烧锅炉的二次风道矩形横列安装。二次风由尾部空预器出口引出,母箱90
°
平均分支给各层燃烧器使用,二次风压头低,流量大,流体经过转弯烟道时阻力增大,产生压降,热风通过空预器时携带部分飞灰撞击风门、风道壁、导流板、燃烧器均减速沉降堆积,随着机组参与深度调峰,启停频繁,空预器堵塞后热二次风携带灰量增大。热空气携带飞灰在经过燃烧器及二次风挡板门等送往炉膛燃烧器,这些设备部位处时阻力较大,飞灰碰撞沉降严重,处理这些部位的积灰,需投入大量的人力、物力和财力,耗费工时较长,安全管控风险大,环境污染严重,且风道积灰造成风道截面变小,影响锅炉调峰稳燃所需要的氧量,增大送风机的出力,造成厂用电量增加。
技术实现要素:4.为了克服现有技术的上述不足,本实用新型提供一种前后墙对冲燃烧锅炉二次风道自吸式输灰系统,该输灰系统能够有效避免二次风道积灰的产生,且无需增加外部气力输送装置,也无需停机,低成本、安全、高效。
5.本实用新型解决其技术问题采用的技术方案是:包括:二次风道,所述二次风道分成两组,分别布置在两面相对的炉墙上,每组二次风道均由上下交替分布的风道层和风道间隔层组成,每个风道层上对应安装一层燃烧器,每个燃烧器下方的二次风道上均设有排灰口,垂直方向上的排灰口通过排灰管道连通,位于最下面的排灰口下方设有集灰斗,多个集灰斗通过输灰管道串联至锅炉渣井的水封挡板处,通过锅炉负压抽吸飞灰。
6.相比现有技术,本实用新型的一种前后墙对冲燃烧锅炉二次风道自吸式输灰系统,首先针对对冲燃烧锅炉二次风道积灰,利用排灰口、排灰管道、集灰斗、输灰管道组成的输灰系统,可以从根本上解决目前积灰对锅炉燃烧影响及停机清灰等弊端,降低了公司人力、物力、财力的投资,保证了机组运行的可靠和经济性。其次,本实用新型主要利用锅炉负压运行,灰靠自重流动和炉底风压抽吸的作用进行循环输送,减少了增加外部气力输送装置,减少了系统的复杂性和新增设备的投用成本。
附图说明
7.下面结合附图和实施例对本实用新型进一步说明。
8.图1是本实用新型一个实施例的主视图。
9.图2是本实用新型一个实施例的侧视图。
10.图中,1、锅炉,11、前炉墙,12、后炉墙,2、风道层,3、风道间隔层,4、排灰管道,5、集灰斗,6、输灰管道,7、锅炉渣井,71、左侧锅炉渣井,72、右侧锅炉渣井,8、刮板捞渣机,9、渣仓,10、燃烧器。
具体实施方式
11.为使本实用新型实施例的目的、技术方案和优点更加清楚,下面将结合本实用新型实施例中的附图,对本实用新型实施例中的技术方案进行清楚、完整地描述,显然,所描述的实施例是本实用新型的一部分实施例,而不是全部的实施例。基于本实用新型中的实施例,本领域普通技术人员在没有做出创造性劳动前提下所获得的所有其他实施例,都属于本实用新型的保护范围。
12.图1和图2示出了本实用新型一个较佳的实施例的结构示意图,图2中的一种前后墙对冲燃烧锅炉二次风道自吸式输灰系统,包括:二次风道,所述二次风道分成两组,分别布置在两面相对的炉墙上,这里的两面相对的炉墙通常是指锅炉1的前炉墙11和后炉墙12,燃烧器10通过二次风道送入空气作为二次风,在图示结构中,位于前炉墙11和后炉墙12上的燃烧器10以正对对冲方式布置,作为其他变形方案,也可以按照预设的规律交错布置。
13.具体实施中,参照图1,每组所述二次风道均由上下交替分布的风道层2和风道间隔层3组成,风道间隔层3的设计是作为中心风的通道,每个风道层2上对应安装一层燃烧器10,具体的,设有a、b、c、d、e、f共3层6组30台燃烧器,其中a、b、c燃烧器布置在前炉墙11的风道内,d、e、f燃烧器布置在后炉墙12的风道内(见图2)。每层2组风道布置10台燃烧器,a、d2组为第一层,b、e2组为第二层,c、f为第三层,共有2个风道间隔层3,分别设置在第一层和第二层之间及第二层和第三层之间。每个燃烧器10下方的二次风道上均设有排灰口,因二次风道立体布置有风道间隔层3,为了防止上层风灰串入风道间隔层3,垂直方向上的排灰口通过排灰管道4连通,所述排灰管道4形成于风道间隔层3,具体的,所述a、b、c,d、e、f燃烧器风道之间分别用厚壁管道联通,共计20根。位于最下面的排灰口下方设有集灰斗5,多个集灰斗5通过输灰管道6串联至锅炉渣井7的水封挡板处,通过锅炉1负压抽吸飞灰。
14.在本实施例中,所述排灰口具体设为φ100的孔,不局限于此,排灰口的形状还可以是矩形、三角形、椭圆形等任意形状,与排灰管道4的截面形状适配,同时参考其他影响因素设定即可,排灰口的大小也综合考量例如管道壁厚、长度、吸尘动力、积尘等确定。
15.考虑磨损余量,延长使用寿命,所述排灰管道4和输灰管道6最好选用厚壁管道,例如厚8mm或10mm的管道。
16.同时还因锅炉1燃烧所需的氧量主要发挥在主燃烧器区域和燃烬风区域,而二次风道积灰需要输送的管道不易管径过大,故根据输灰规范选用φ108的管道方可满足需求。
17.根据排灰口为φ100的孔,所述集灰斗5可以设为1000mm
×
1000mm
×
600mm的60
°
锥形集灰斗,便于沉降堆积的飞灰高效落入。集灰斗5的下部还可以进一步设置隔离插板门或电磁阀门,布置在锅炉1的17米高度平台上,则所述的输灰管道6布置在锅炉1的6米至17米高度区间,既安全,又便于后期维修操作。
18.各管道及连接处必须满焊防止漏风,并在所述输灰管道6与水封挡板的连接处以
及排灰管道4与二次风道的连接处均安装金属膨胀节,包括集灰斗5连接金属膨胀节,以防止冷、热态膨胀拉断管道。
19.参照图1,实施例中,所述锅炉渣井7分成左右侧两个,每组二次风道平分成左右两部分,两部分的集灰斗5分别汇集后连通至左侧锅炉渣井71与右锅炉渣井72。进一步地,所述锅炉渣井7的出口还依次连接有刮板捞渣机8和渣仓9。具体的,前炉墙11最下层的风道设五个集灰斗5,用φ108
×
10mm引出六根,通过三通汇集成两根φ108
×
10mm通往刮板捞渣机8的6米渣井前墙水封挡板处,后炉墙12同前炉墙布置对称,结构相同。通过锅炉1负压抽吸,实现积灰输送流动,落入捞渣机刮往渣仓9。
20.由于所述输灰管道6是安装在锅炉1,锅炉1冷热态膨胀过程必须防止管道挤压下部炉底水封槽外沿,所以输灰管道6的选用也要考虑水封冷热态位移量。
21.本实用新型各实施例一方面主要利用锅炉1负压运行,灰靠自重流动和炉底风压抽吸的作用进行循环输送,减少了增加外部气力输送装置,减少了系统的复杂性和新增设备的投用成本。另一方面,在运行中高效集尘、输尘,大幅减少了燃烧器10及二次风挡板门处的积灰,使二次风的供应充足,促进了充分稳定的燃烧,保证了机组运行的可靠性和经济性。
22.以上所述,仅是本实用新型的较佳实施例,并非对本实用新型做任何形式上的限制,凡是依据本实用新型的技术实质,对以上实施例所做出任何简单修改和同等变化,均落入本实用新型的保护范围之内。