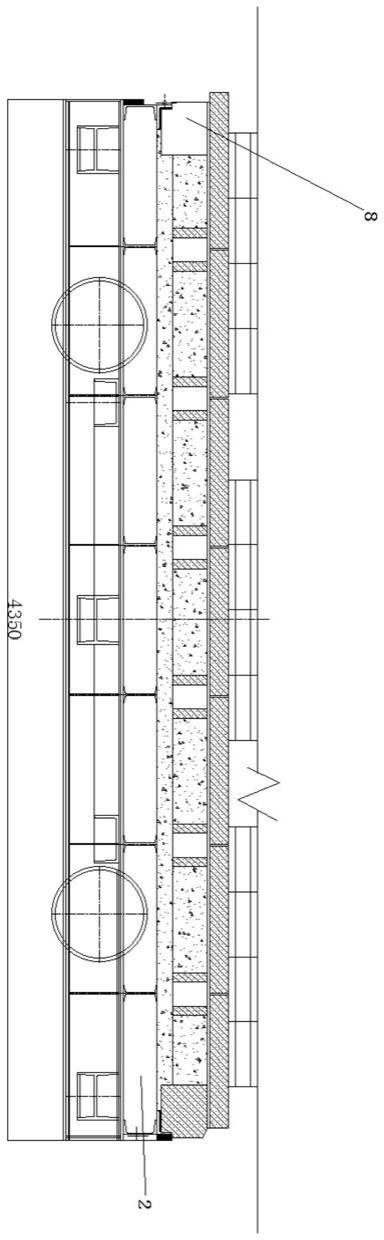
[0001]
本发明属于机电设备技术领域,尤其涉及一种烧结砖厂烧结工序自动控制装置及方法。
背景技术:[0002]
目前,根据国家绿色建筑的定义,以保障建筑物安全和品质为行业发展基本宗旨,最大限度地节约资源,积极拓展各种工业尾矿、煤矸石、粉煤灰、页岩、建筑基坑土、建筑渣土、江河湖(渠)海淤泥、污泥等资源的有效再生运用,是确保烧结墙体材料行业可持续发展的主要路径。同时,需要面对粘土、页岩、煤矸石、粉煤灰等不同成分组成的原料,真空挤砖机前端生产工艺对物料处理方式、配水情况不同致使物料成分均化、含水量等情况不同,同时根据市场等情况挤出半成品有实心砖、空心砖和尺寸差异要求。随着我国经济快速发展,砖瓦工业也步入发展快车道,传统在运行过程中,通过岗位工人工观察进行人工经验调节,缺乏精准预防手段,影响产品质量。
[0003]
结合国家当前供给侧改革和目前新技术发展趋势,有必要开发一种通过计算机软件自动控制、实现质量可追溯调节的系统方案,达到提高设备运转率、降低消耗、产量及质量得到提高的目的。该方案既能在新建生产线中使用,又能在老设备上改造使用。
技术实现要素:[0004]
为解决上述技术问题,本发明提供了一种隧道窑及码坯窑车焙烧状态和焙烧氛围控制、可追溯方法,可以解决现有技术中存在的问题,提高设备运转率、降低消耗,提高产量,保证质量的可追溯性。
[0005]
本发明通过以下技术方案得以实现。
[0006]
一种烧结砖厂隧道窑,包括烧结隧道窑、码坯窑车、隧道窑排烟风机、隧道窑冷却风机、隧道窑平压风机、煤粉喷射装置、喷刻数码标签标牌、测温一次元件、测压一次元件、数码标签识别装置和计算机控制单元;
[0007]
所述烧结隧道窑包括从烧结隧道窑进车端指向出车端方向依次分布的预热带、焙烧带和冷却带;
[0008]
所述码坯窑车上安装有喷刻数码标签标牌,多台码坯窑车沿着烧结隧道窑长度方向依次排列并顺序进、出烧结隧道窑;
[0009]
所述隧道窑排烟风机设置在烧结隧道窑上方;
[0010]
所述隧道窑冷却风机设置在烧结隧道窑上方且靠近烧结隧道窑窑尾冷却带;
[0011]
所述隧道窑平压风机设置在烧结隧道窑下方;
[0012]
所述煤粉喷射装置设置在烧结隧道窑上方且通过喷煤孔向烧结隧道窑内喷射煤粉;
[0013]
多个所述测温一次元件设置在烧结隧道窑窑顶位置,且设置区域覆盖预热带、焙烧带和冷却带;
[0014]
所述测压一次元件包括位于烧结隧道窑窑顶的第一压力检测元件、位于烧结隧道窑窑底的第二压力检测元件以及位于排烟管内的第三压力检测元件;
[0015]
所述数码标签识别装置位于烧结隧道窑进车端;
[0016]
所述计算机控制单元与码坯窑车、隧道窑排烟风机、隧道窑冷却风机、隧道窑平压风机、煤粉喷射装置、测温一次元件、测压一次元件和数码标签识别装置电连接。
[0017]
优选的,所述喷刻数码标签标牌上包含有二维码,以二维码形式读取码坯窑车的相关信息,包括编号信息、物料信息等。
[0018]
优选的,所述隧道窑排烟风机、隧道窑冷却风机和隧道窑平压风机分别与变频器电连接。
[0019]
优选的,所述第一压力检测元件和第二压力检测元件位于烧结隧道窑内焙烧带。
[0020]
优选的,所述数码标签识别装置有两个,两个数码标签识别装置分别位于码坯窑车移动路径的左、右两侧。
[0021]
一种烧结砖厂码坯窑车焙烧状态和焙烧氛围控制方法,采用前述的烧结砖厂隧道窑,且包括以下步骤:
[0022]
s1、在计算机控制单元中以组态软件制成隧道窑理想烧成曲线,该理想烧成曲线不是固定不变的,而是根据实际烧成曲线以及砖坯原料特性进行调整;
[0023]
s2、码坯窑车码满砖坯后连续进入烧结隧道窑,计算机控制单元通过安装在码坯窑车侧面的喷刻数码标签标牌以及烧结隧道窑进车端设置的数码标签识别装置,并根据烧结隧道窑长度和码坯窑车长度,识别每台码坯窑车在烧结隧道窑内实时位置;
[0024]
s3、计算机控制单元通过烧结隧道窑上多个测温一次元件检测的实际温度参数,对应码坯窑车位置组成实际生产过程中形成的实际烧成曲线,以实际烧成曲线与理想烧成曲线进行比值跟踪,当实际烧成曲线偏离理想烧成曲线时,计算机控制单元发出信号控制隧道窑排烟风机调整烧成温度,或驱动煤粉喷射装置投入煤粉,需要注意的是,这里的比值跟踪是指将测量温度值与理想温度值进行比较和跟踪;
[0025]
s4、计算机控制单元通过测压一次元件检测窑内压力,通过隧道窑排烟风机、隧道窑冷却风机和隧道窑平压风机以控制燃烧气氛,使窑内焙烧带中部及其两端的窑空间压力稳定在“0压”点左右的位置。需要说明的是,这里的“0压”点是指烧结隧道窑内焙烧带相对稳定,送风和抽风压力为“0”的情况,“左右”是指大约等于的意思。隧道窑排烟风机负压抽风,隧道窑冷却风机正压送风,隧道窑平压风机主要用于大跨度隧道窑窑底压力均衡。
[0026]
优选的,所述s1中制成理想烧成曲线时,根据计算机控制单元实时呈现的每台码坯窑车的焙烧温度、压力参数曲线,针对不同砖坯原料特性,基于码坯窑车上砖坯烧成质量判断,修改隧道窑理想烧成曲线。即计算机控制单元(可实时呈现每台码坯窑车的焙烧温度、压力参数曲线,针对不同砖坯原料理化特性、含水量、砖坯体量尺寸等情况,基于码坯窑车上砖坯烧成质量判断,修改隧道窑理想烧成曲线。
[0027]
进一步,所述砖坯原料特性包括砖坯原料理化特性、含水量和砖坯体量尺寸。
[0028]
一种烧结砖厂码坯窑车焙烧状态和焙烧氛围可追溯方法,采用前述的烧结砖厂隧道窑,实时采集烧结隧道窑内的温度和压力参数,对应每台码坯窑车生成实际烧成曲线,并将实际烧成曲线与理想烧成曲线进行比值跟踪,实现每台码坯窑车上砖坯烧成质量的可追溯性,即通过前述s3、s4中检测的参数生成的实际烧成曲线与理想烧成曲线比值跟踪,实现
每台码坯窑车上砖坯烧成质量的可追溯性。
[0029]
计算机控制单元通过组态软件制成理想烧成曲线时,通过砖坯质量的精准追溯做出调节,适用于不同物料成分、水分及空心砌块、大尺寸装备式墙体材料等条件和工艺要求情况。
[0030]
本发明公开了一种隧道窑及码坯窑车焙烧状态和焙烧氛围控制、可追溯方法,涉及到烧结隧道窑、码坯窑车、风机、变频器、喷刻数码标签标牌、测温和测压一次元件、煤粉喷射装置和计算机控制单元等。
[0031]
砖厂烧结隧道窑分预热带、焙烧带、冷却带,隧道窑烧结热工制度包括温度制度、压力制度等。
[0032]
在窑车侧面安装喷刻码标签标牌的标牌,隧道窑外进车端设置码标签标牌识别装置,窑车由顶车机连续送入隧道窑,根据隧道窑和窑车长度,计算机控制单元识别每台窑车窑内实时位置,自动生成每台窑车烧成状态曲线,根据出窑砖坯质量实现每台窑车上砖坯烧成氛围的可追溯性,实时调节不同原料、水分、砖坯尺寸的理想烧成曲线,采用下述温度、压力控制方式自动比值跟踪调节窑内烧成氛围。
[0033]
温度控制:预热带预热升温,开始车位温度不超过100~105℃,低于600℃属于预热带;焙烧带包括焙烧、保温两个环节,焙烧温度一般定为1050℃左右,保温4~8小时;温度低于800℃一般属于冷却带。在隧道窑顶部设置多只热电偶,检测烧成温度,自动跟踪理想烧成曲线,通过窑头排烟风机、窑尾冷却风机的变频器调节电机转速、焙烧带顶部煤粉喷射装置少量添加煤粉等措施做调整。
[0034]
压力控制:窑内压力决定着窑内气体流动的运动状态,从而影响着热量的交换,各个不同燃烧阶段,窑内压力也不相同,因为预热带和焙烧带前端的低温和中温阶段采用负压抽力,窑内的负压就相对较大;进入焙烧带后,高温阶段抽力较小,因而形成微负压或微正压状态,原则上使窑内焙烧带中部及其两端压力稳定在“0压”点左右的位置;冷却阶段因有窑尾鼓风而形成正压状态。隧道窑底平行均匀布置2~5台平压风机主要用于大跨度隧道窑窑底压力均衡。这是采用计算机控制单元通过压力变送器检测、控制窑上风机运行状态以平衡压力参数的过程。
[0035]
与现有技术相比,本发明利用烧成隧道窑内的检测元件生成了两条实际烧成曲线,一条用于控制烧成隧道窑内的烧成氛围,一条用于记录码坯窑车的烧成过程。本发明的优势在于:精准跟踪每台码坯窑车焙烧状态,通过计算机软件自动控制控制,对砖坯烧成条件和工艺要求有一定的适应性。整个隧道窑烧成系统作为一个系统来优化自动调节,达到提高设备运转率、降低消耗、产量及质量得到提高的目的,增加企业的经济效益。
附图说明
[0036]
图1是码坯窑车安装喷刻数码标签的标牌的大样图;
[0037]
图2是隧道窑温度烧成曲线示意图;
[0038]
图3是隧道窑实时可追溯热工系统控制装置结构示意图;
[0039]
图4是图3中b-b剖面示意图;
[0040]
图4-1是图4中a区域的放大示意图;
[0041]
图4-2是图4中b区域的放大示意图;
[0042]
图4-3是图4中c区域的放大示意图;
[0043]
图4-4是图4中d区域的放大示意图;
[0044]
图中:烧结隧道窑-1、码坯窑车-2、隧道窑排烟风机-3、隧道窑冷却风机-4、隧道窑平压风机-5、变频器-6、煤粉喷射装置-7、喷刻数码标签标牌-8、测温一次元件-9、测压一次元件-10、数码标签识别探头-11、计算机控制单元-12。
具体实施方式
[0045]
下面结合附图和具体实施例对本发明作进一步的说明,但不应就此理解为本发明所述主题的范围仅限于以下的实施例,在不脱离本发明上述技术思想情况下,凡根据本领域普通技术知识和惯用手段做出的各种修改、替换和变更,均包括在本发明的范围内。
[0046]
下面进一步描述本发明的技术方案,这里具体按6.9米截面跨度的烧结隧道窑1描述,码坯窑车2共有70台,单台码坯窑车2长4.35米,70台码坯窑车2连续进入烧结隧道窑1,烧结隧道窑1长度对应33台码坯窑车2的车位长度(即按窑车车位划分为33个车位区域),图4-1~图4-4中码坯窑车2侧面的数字序号以及码坯窑车2上方方框内的数字序号代表1~33号车位,即烧结隧道窑1中只能同时容纳33台码坯窑车2,剩余的码坯窑车2在烧结隧道窑1外等候循环进入。需要注意的是,本发明保护的范围并不局限于该尺寸和数量。
[0047]
如图1所示,为码坯窑车2侧面大样图,在码坯窑车2车头侧面安装带有二维码的喷刻数码标签标牌8,喷刻数码标签标牌8上有包含该码坯窑车2所有生产信息的二维码。
[0048]
如图2所示:为隧道窑温度烧成曲线图,这里是温度理想烧成曲线,横坐标代表码坯窑车2在烧结隧道窑1中的车位位置。
[0049]
如图3、图4、图4-1、图4-2、图4-3和图4-4所示:通过在烧结隧道窑1窑顶预热带安装6支、焙烧带安装3支、冷却带安装7支共16支康铜热电偶作为测温一次元件9,测温一次元件9检测的实际参数输入计算机控制单元12,组成实际生产过程中形成的实际烧成曲线(即烧成隧道窑1内的实际烧成曲线),以此实际烧成曲线与理想烧成曲线比值跟踪,发生异常情况及时发出信号控制烧结隧道窑1中1台额定参数为风量149778m3/h、压力1174pa、电机功率75kw的隧道窑排烟风机3的变频器6,通过控制电机转速调整烧成温度,当温度过低时,辅以烧结隧道窑1焙烧带上的煤粉喷射装置7少量投入煤粉。
[0050]
烧结隧道窑1焙烧带顶部、底侧安装2台微差压变送器作为测压一次元件10检测窑内压力(即烧结隧道窑1窑顶对码坯窑车2车底的压差),通过隧道窑平压风机5变频器6调节风量以控制燃烧气氛,使窑内焙烧带中部及其两端的窑空间压力稳定在“0压”点左右的位置。采用1台额定参数为风量149778m3/h、压力1174pa、电机功率75kw隧道窑排烟风机3负压抽风,采用4台额定参数为风量32389m3/h、压力372pa、电机功率7.5kw隧道窑冷却风机4正压送风,采用3台额定参数为风量46700m3/h、压力262pa、电机功率7.5kw隧道窑平压风机5用于隧道窑窑底压力均衡。
[0051]
隧道窑排烟风机3主风管道上安装1支康铜热电偶,作为测温一次元件9用于风机保护报警;隧道窑排烟风机3主风管道上安装测压一次元件10用于控制排烟风机3对应的变频器6。
[0052]
在70台码坯窑车2侧面安装喷刻数码标签标牌8,烧结隧道窑1外进车端设置两个数码标签识别探头11,码坯窑车2由顶车机连续送入烧结隧道窑1,根据烧结隧道窑1长度和
码坯窑车2长度,计算机控制单元12识别每台码坯窑车2在窑内实时位置,自动生成每台码坯窑车2烧成状态曲线,实现每台码坯窑车2上砖坯烧成质量的可追溯性,具体过程为:当一台码坯窑车2从烧结隧道窑1进车端进入时,位于烧结隧道窑1进车端的数码标签识别探头11读取该台码坯窑车2侧面的喷刻数码标签标牌8上的二维码信息,此时计算机控制单元12开始针对该台码坯窑车2计时,由于码坯窑车2的移动速度已知,长度已知,于是根据操作人员的预设时间间隔可计算出当该台码坯窑车2在某一时刻时在烧成隧道窑1中的位置(即33个车位中的一个),然后读取距离该位置(车位)最近的测温一次元件9的温度值(本实施例中没有按照33个车位配33个测温一次元件9的方式,所以按照最距离最接近原则),最后以这些温度值为纵坐标,车位位置为横坐标,生成类似图2的实际烧成曲线。
[0053]
计算机控制单元12通过人机界面对话设备实现本控系统的技术参数设置和相关参数的显示,自动生成烧结隧道窑1实时(实际)烧成状态曲线和每台码坯窑车2实际烧成曲线,跟踪理想烧成曲线与实际烧成曲线的比较实现自动闭环控制,理想烧成曲线根据烧成砖坯质量追溯每台码坯窑车2烧成过程曲线固化,对砖坯烧成条件和工艺不同要求有一定的适应性。
[0054]
以上对本发明的实施例进行了详细说明,但所述内容仅为本发明的较佳实施例,不能被认为限定本发明的实施范围。凡依本发明范围所作的均等变化与改进等,均应仍归属于本专利涵盖范围之内。