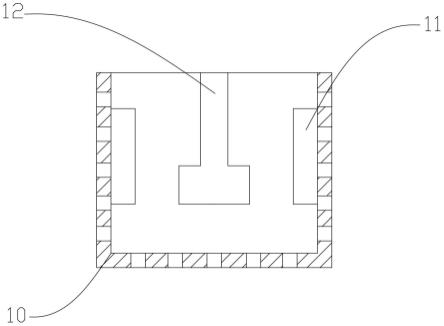
1.本发明涉及窑炉技术领域,具体为窑热循环节能系统。
背景技术:2.随着人类进入了工业社会,窑炉得到了飞速地发展。它也在各个行业中扮演着越来越重要的角色。为了使窑炉烧制出令人满意的产品,需要对其烧制过程进行控制,而现有的隧道窑在对内部进行加热时,无法对利用过的热气进行循环使用,使热气保温性能较差,加热后热量很容易散失,造成人们在对其加热时浪费能源,不利于节省成本,也不符合环保理念。
3.陶瓷企业的窑炉所产生的烟气带走的热量是巨大的,占窑炉总热量的25%~35%,若将这部分余热利用起来,其经济效益相当可观。可是在实际运用中,由于人们的节能观念不足以及技术水平的落后,致使我国陶瓷窑炉烟气余热的利用率非常低,一般只有2%~3%。
4.如中国专利公开号为cn208832976u的实用新型文献中,一种热循环隧道窑,包括隧道窑本体,隧道窑本体由外墙和内保温砖墙构成,隧道窑本体分成预热带、烧成段和冷却带,外墙的两侧内壁设置有内保温砖墙,隧道窑本体的顶部设置有加热总管路,冷却带的一端贯通内保温砖墙和外墙设置有第一下循环管路,第一下循环管路的另一端固定安装有第一抽风机,第一抽风机的顶部固定连接有第一上循环管路,第一上循环管路的另一端与加热总管路相连通。
5.窑车载着陶罐从入口往出口前进,依次经过预热带、烧成带和冷却带。通常,由预热带向烧成带的转换温度为800~850℃,此后窑内的传热方式既有热对流又有热辐射,在烧成带窑内温差超过15℃时就有可能导致产品出现桔釉、针孔、釉泡及至变形等欠烧或过烧缺陷,为了减少烧成带的温差,使来自窑墙和窑顶火焰的热辐射作用得到相互补充。在实际的窑炉设计中应在窑顶与被烧制品的上边缘之间选择上部火焰喷嘴的最佳位置,改进火焰喷嘴口附近的环境,避免窑内局部温度过高。
6.上述技术通过增设抽风机和循环管路,将冷却喷水时产生的余热和加热烘烤时散发的余热进行回收循环再利用,加热腔内的热量通过内墙的间隙进入到隧道窑的通道内,外墙采用封闭式结构,减少热量浪费。但是该专利仅对冷却喷水时产生的余热和加热烘烤时散发的余热进行了循环应用,而未对助燃气体进入窑炉内所产生的射流进行改进。
7.通常助燃气体为外界的空气,空气在进入到进气通道后,通过风机施加动力,甚至在其他方案中,还会利用(废气)余热与进入的空气进行热交换,以提升进入的空气的温度,避免进入的空气影响窑炉内部的温度。但是在实际使用时,进入的空气依然与窑炉内部存在较大的温差,在进入时这部分空气在风机的作用下,通常以射流的形式进入到窑炉内部,然后与提供燃料的喷嘴喷射的燃料(多为天然气、煤气)接触并进行助燃。外界空气直入窑体内部,导致射流对窑炉内的局部区域持续进行热交换,在窑体内部造成部分低温区域,如果这部分低温区域与烧制的产品接触,严重时会造成产品受热不均,影响产品成型质量(甚至影响产品烧制成功率),因此需要一种能够改善窑炉内气体射流,避免射流持续影响窑炉
局部温度的窑热循环节能系统。
技术实现要素:8.本发明提供了窑热循环节能系统,目的为改善窑炉内气体射流,避免射流持续影响窑炉局部温度。
9.为了达到上述目的,本方案提供如下技术方案:窑热循环节能系统,包括预热带、烧成带和冷却带,预热带的侧壁设有第一开口,烧成带的侧壁设有第二开口,冷却带的侧壁设有第三开口,预热带、烧成带和冷却带都开有若干与已经安装好的火焰喷嘴配套的助燃通孔;还包括:热风管、助燃管、风机、改向管和旋转桶,热风管将第三开口和第二开口分别与第一开口连通,第一开口与第二开口之间的热风管形成预热通道,第三开口与第二开口之间的热风管形成保温通道,风机固定于保温通道内和预热通道内,用于将烧成带内的高温烟气抽进热风管内;助燃管与热风管紧密贴合固定,助燃管的一端连通助燃通孔,助燃管的另一端与大气连通;改向管的基端固定在窑体内壁的助燃通孔处并与助燃通孔连通,旋转桶外罩于改向管的自由端并与改向管转动连接,旋转桶内侧面倾斜固定有在受到改向管内气流作用下驱使旋转桶转动的受风板,旋转桶的侧面开有多个出口,所述出口中存在正对火焰喷嘴的出口。
10.本技术方案原理及有益的技术效果:因为包括窑体和热风管,预热带开有预热通道,窑体烧成带开有保温通道,风机固定于保温通道内和预热通道内,所以当窑炉运行过程中,烧成带和冷却带的高温烟气中会从保温通道和冷却通道口处被风机抽取进热风管内,被抽取的高温烟气中的余热与预热带中冷空气和助燃管内的助燃空气(因为助燃管与热风管紧密贴合固定)进行热交换,实现对预热带产品的预热效果和对助燃气体的加热效果,节省能源消耗。本方案中,助燃气体包括从预热带以常规方式进入的助燃气体和从助燃管以精确助燃方式进入的助燃气体。上述余热利用过程,主要是针对从助燃管内进入的助燃气体。
11.但是如果助燃管内进入的助燃气体不加以约束,其形成的是气体淹没射流。即气体自孔口、管嘴或条缝向外喷射所形成的流动,称为气体淹没射流,简称气体射流,射流按一定的扩散角向前做扩散运动,在射流的形成过程中,会产生横向动量交换,旋涡的出现使之进行热量交换。换句话来说,由于这部分助燃气体的温度与烧成带或者说火焰喷嘴的温度存在较大的温差,在出口断面和轴心上均存在温差,尤其是轴心部分,在其射程内如果与产品稳定接触,极易导致产品受热不均,影响产品的烧制质量。
12.在本方案中旋转桶转动连接在改向管上,旋转桶内侧面倾斜固定的受风板,旋转桶上开有多个出口,改向管入口固定在窑体上的助燃通道处,所以当助燃通道内的风进入改向管中,从改向管的出口处出来时,会冲击旋转桶内侧上固定的受风板,带动旋转桶进行旋转,使得预热通道内的风会从旋转桶中的多个出口处喷射出去,使得原始状态下的射流不会一直射向一个区域,从而避免需要加工的产品的局部受热不均而产生质量问题。
13.窑炉内的传热方式便既有对流传热又有辐射传热,在烧成带窑内温差超过15℃时就有可能导致桔釉、针孔、釉泡及至变形等欠烧或过烧缺陷,预热带向烧成带转换的区域为
了避免窑内温差大影响产品质量,故该段固设有多于其他区域的火焰喷嘴,局部区域存在着温度过高的风险。因为旋转桶上开有多个出口,其中有正对烧成带火焰喷嘴周围的出口,所以助燃通道中出去的助燃风从正对烧成带火焰喷嘴周围的出口出去的助燃风会冲击火焰喷嘴周围。既能够将火焰喷嘴附近的高温空气与气体射流的低温空气充分混合,又能够将气体射流的低温空气的射程变短,减少低温区域的影响范围。满足了对窑炉内火焰燃烧环境对于氧气的需要的同时又避免了窑体内局部温差过大的情况。
14.本方案实现了改善窑炉内气体射流的需求,将助燃通道内的助燃风的进入方式进行改变,使得原本的有限空间射流不再持续射向窑炉内的固定方向,避免进行过度的局部热交换,减少了桔釉、针孔、釉泡及至变形、欠烧或过烧缺陷等问题的出现,提升了产品的成型质量,对窑炉的余热进行了充分的利用,节省了能源损耗;助燃风冲击火焰喷嘴周围,解决了预热带向烧成带转换的区域火焰喷嘴设置过多导致窑炉内局部温度过高的问题,同时又满足了对窑炉内火焰燃烧环境对于氧气的需要。
15.进一步,所述旋转桶上正对烧成带火焰喷嘴的出口设置为旋转一整周,二分之一至三分之二的时间内,出口为正对烧成带火焰喷嘴。
16.有益效果:既照顾了对于预热带向烧成带转换的区域过多火焰喷嘴带来的局部温度过高的降温需求,又避免了固定出口持续直吹火焰喷嘴的所导致的温度过度降低。
17.进一步,还包括温度传感器、控制器和气阀,所述气阀固定在热风管管口处,所述温度传感器固定在窑体内的保温通道口旁,用于检测窑体烧成带的温度;所述控制器用于接受温度传感器的信号,并判断温度大小是否符合阈值,若温度大小处于阈值范围内,则打开气阀,若温度大小低于阈值大小,则关闭气阀。
18.有益效果:最大程度地利用烧成带的余热,避免了抽取过多烟气对于烧成带温度产生不利的影响,实现智能化的气阀调节。
19.进一步,还包括隔热砖和隔热板,在窑车表面放置有隔热砖,隔热板放置在隔热砖上。
20.有益效果:实现对于窑车表面的隔热保温,避免窑炉内的高温直接传导到窑车上,对窑车结构造成不可复原的损伤。
21.进一步,所述隔热砖间留有0.1cm至0.3cm的空隙。
22.有益效果:隔热砖间留下的空隙,可以避免高温环境下的隔热砖受热膨胀导致砖体破裂,适当距离的空隙使得隔热砖的隔热效果不会过度降低,节省能源。
23.进一步,所述窑车的车轮采用zg340-640材质。
24.有益效果:车轮强度不足,表面硬度较浅或根本就没有淬火时,车轮磨损较快会影响窑车的正常运行和产品运送,采用zg340-640材质的车轮可以提升车轮强度,保证窑车的正常运行和产品运送。
25.进一步,还包括砂封板、支撑架和砂封槽,所述砂封槽底面固定在支撑架上表面,砂封板固定在窑车侧面,砂封槽内装有在窑车行驶时仍能没过砂封板底端的砂粒。
26.有益效果:保证了窑车行进过程中的密封效果,隔热效果好,大幅减小了窑车上下表面的热交换,保护了窑车下表面部分免受高温带来的损伤。
附图说明
27.图1为本发明旋转桶处的局部剖视图;图2为本发明旋转桶处的三维视图;图3为本发明窑车口的主视图。
具体实施方式
28.下面通过具体实施方式进一步详细的说明:说明书附图中的附图标记包括:1、窑体;2、轨道;3、砂封槽;4、支撑架;5、窑车;6、隔热砖;7、隔热板;8、叠砖;9、砂封板;10、旋转桶;11、受风板;12、改向管。
29.实施例如图1-3所示:窑热循环节能系统,包括窑体1,窑体1包括预热带、烧成带和冷却带,预热带的侧壁设有第一开口,烧成带的侧壁设有第二开口,冷却带的侧壁设有第三开口,预热带、烧成带和冷却带都开有若干与已经安装好的火焰喷嘴配套的助燃通孔;还包括:热风管、助燃管、风机、改向管12和旋转桶10,热风管将第三开口和第二开口分别与第一开口连通,第一开口与第二开口之间的热风管形成预热通道,第三开口与第二开口之间的热风管形成保温通道,风机固定于保温通道内和预热通道内,用于将烧成带内的高温烟气抽进热风管内;助燃管与热风管紧密贴合固定,助燃管的一端连通助燃通孔,助燃管的另一端与大气连通。
30.感应单元,感应单元包括温度传感器、控制器和气阀,气阀焊接在热风管管口处,温度传感器采用1105bk型温度传感器,该温度传感器为带陶瓷保护管的热电偶组件,适用于燃烧过程和热气体环境内的温度测量,最高工作温度为1500℃,能够充分适用窑炉内的高温环境。温度传感器螺栓连接在窑体1内的保温通道口旁,用于检测窑体1烧成带的温度;控制器采用采用stm32f103zet6单片机,放置在窑炉外,避免窑炉内的高温环境带来的影响,同时该单片机价格低廉,可靠性高且低噪音,控制器用于接受温度传感器的信号,并判断温度大小是否符合阈值,温度大小的阈值区域选取1110℃-1150℃,若温度大小处于阈值范围内,则打开气阀,若温度大小低于阈值大小,则关闭气阀,从而最大程度地利用烧成带的余热,避免了抽取过多高温烟气对于烧成带温度产生不利的影响,实现智能化的气阀调节。
31.窑炉运行过程中,烧成带和冷却带的高温烟气中的余热会从保温通道和冷却通道口处被风机抽取进热风管内,再进入预热通道,利用炉内余热进行热循环,实现对预热带产品的预热效果和对助燃气体的加热效果,节省能源消耗。
32.旋转桶10通过桶边缘焊接的滑轮和改向管开有的滑槽转动连接在烧成带助燃口旁的改向管上,受风板11倾斜地焊接在旋转桶10内侧面,旋转桶10上开有多个出口,其中有正对烧成带火焰喷嘴周围的出口,旋转桶10上正对烧成带火焰喷嘴的出口设置为180度至240度的圆弧形通孔,出口为正对烧成带火焰喷嘴,改向管12入口焊接在窑体1内壁的助燃通道处。改向管的基端固定在窑体内壁的助燃通孔处并与助燃通孔连通。
33.既照顾了对于预段向烧成带转换的区域过多火焰喷嘴带来的局部温度过高的降温需求,又避免了固定出口持续直吹火焰喷嘴的所导致的温度过度降低。
34.气体自孔口、管嘴或条缝向外喷射所形成的流动,称为气体淹没射流,简称气体射
流,射流按一定的扩散角向前做扩散运动,在射流的形成过程中,会产生横向动量交换,旋涡的出现使之进行热量交换。当助燃通道内的风进入改向管12中,从改向管12的出口处出来时,会冲击旋转桶10内侧上焊接的受风板11,带动旋转桶10进行旋转,使得预热通道内的风会从旋转桶10中的多个出口处喷射出去,使得原始状态下的射流不会一直射向一个区域,从而避免需要加工的产品的局部温差过大而产生质量问题。
35.顶车机进程将窑车5推动,窑车5通过在轨道2上的滚动进入窑炉内后,顶车机返程退出窑炉,窑炉门关闭。窑车5在窑炉内依次通过预热带、烧成带和冷却带,直至最后出炉成型预热带向烧成带转换的区域后窑内的传热方式便既有对流传热又有辐射传热,在烧成带窑内温差超过15℃时就有可能导致桔釉、针孔、釉泡及至变形等欠烧或过烧缺陷,预热带向烧成带转换的区域为了避免窑内温差大影响产品质量,故该段固设有多于其他区域的火焰喷嘴,局部区域存在着温度过高的风险。助燃通道中出去的助燃风从正对烧成带火焰喷嘴周围的出口出去的助燃风会冲击火焰喷嘴周围,满足了对窑炉内火焰燃烧环境对于氧气的需要的同时又避免了窑体1内局部温度过高。
36.隔热单元,隔热单元包括隔热砖6、砂封板9和砂封槽3,砂封槽3螺栓连接在窑体1侧壁下端,用于支撑砂封槽3的支撑架4螺栓连接在窑体1侧壁上,螺栓连接在砂封槽3下端,为砂封槽3提供良好支撑,砂封槽3内装有砂粒,砂封板9侧面螺栓连接在窑车5侧面,砂封板9插入砂封槽3的砂粒中,砂粒能够通过0.2*0.2cm的滤网,砂封槽3内使用的砂粒不能过大,当砂粒过大的话,被经过的窑车5砂封板9犁起,此时砂粒之间是有缝隙的,有缝隙就无法起到密闭作用,就无法阻止车底冷空气进入窑膛或者窑膛高温气体挤进车底。当窑车5运行时,砂封板9在砂封槽3内移动,和砂粒间形成良好的隔热层,保证窑车5上下表面的密封效果,隔热效果一流,减小了窑车5上表面的热空气和窑车5下表面空气的热交换,有效地保护了窑车5下表面部分免受高温带来的损伤。
37.窑车5上放置有隔热砖6,隧道窑的两侧、窑顶和窑车5面形成窑的四个受热面除了窑车5面外其余三个面在窑炉烧成过程中温度保持恒定不变它们的热消耗仅限于向外传导的热损失,而窑车5是在室温下推入隧道窑中,当窑车5在窑炉内前进的过程中除了向下传导的热量外还吸收并贮存热量使其车面及窑道内的温度一致,窑车5上的陶罐依次经过窑炉中的预热带、烧成带、冷却带,最后成型出炉,而当窑车5从隧道窑出来后,窑车5温度又会降至室温,所以采用隔热砖6可以减少窑车5的蓄热量和热损失。
38.隔热砖6上放置有固定板,固定板的设置便于放置陶罐,提升陶罐在窑车5行进过程中的稳定性。隔热砖6间留有0.1cm至0.3cm的空隙,避免高温环境下的隔热砖6受热膨胀导致砖体破裂,适当距离的空隙使得隔热砖6的隔热效果不会过度降低,节省能源。
39.叠砖8叠放在隔热板7上,再将陶罐放置于叠砖8上,这使得使得陶罐底部也能接受到窑炉内高温的炙烤成型,受热更均匀。
40.与传统方案相比,本方案实现了改善窑炉内气体射流的需求,将助燃通道内的助燃风的进入方式进行改变,使得原本的有限空间射流不再持续射向窑炉内的固定方向,避免进行过度的热交换,影响产品的成型质量,对窑炉的余热进行了充分的利用,节省了能源损耗。
41.以上所述的仅是本发明的实施例,方案中公知的具体结构及特性等常识在此未作
过多描述。应当指出,对于本领域的技术人员来说,在不脱离本发明结构的前提下,还可以作出若干变形和改进,这些也应该视为本发明的保护范围,这些都不会影响本发明实施的效果和专利的实用性。本技术要求的保护范围应当以其权利要求的内容为准,说明书中的具体实施方式等记载可以用于解释权利要求的内容。