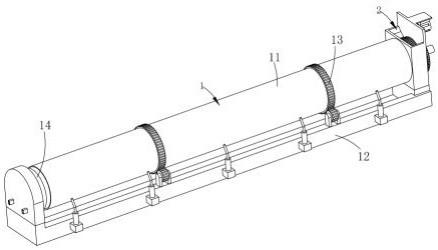
1.本发明涉及二氧化钛制备技术领域,尤其涉及一种高纯二氧化钛生产设备及其工艺。
背景技术:2.硫酸法制备二氧化钛时,用硫酸酸解含钛矿物,得到硫酸氧钛溶液,经纯化和水解得到偏钛酸沉淀,再进入转窑焙烧产出二氧化钛颜料产品,是非连续生产工艺,工艺流程复杂,需要20道左右的步骤,排放废弃物较多,晶型转变需更多操作步骤,采用的焚烧工艺需要消耗大量能源,硫酸法工艺主要包括以下几个步骤:1)除杂:fq6+3h2sch=fe2( so4)3+3h2o,tio2+2h2so4=ti ( so4)2+2hzo;2)然后:fe+f& (so4) 3=3fe2so4;3)调ph至5-6,使 ti ( so4)2水解:ti (so4)2+3h2o=h2tio3j +2h2so4;4)过滤沉淀加热得到tio2: h2tio3= tq2+h2ot。
3.而一般水合二氧化钛(偏钛酸)在150~300℃之间是脱去游离水和结晶水的过程,650℃左右为脱硫过程,700~950℃期间开始锐钛型向金红石型转化,在碱金属催化剂(盐处理剂)的存在下,转化温度可降低,转化速率可加快;在煅烧过程中二氧化钛的相对密度,随着品型结构的改变而变化,从600℃的3.92(锐钛型)到1000~1200℃金红石型的4.25,加入促进剂后金红石型的转化温度可降低至850~900℃。
4.中国专利cn109850941b公开了一种工业硫酸钛液水解制备高纯二氧化钛的方法,属于化工技术领域。工业硫酸钛液水解制备高纯二氧化钛的方法包括:将硫酸钛液冷冻析出硫酸亚铁结晶、过滤,得滤液a;取1体积滤液a和0.20~1.00体积水分别预热至90~98℃;再在搅拌条件下将滤液a加到水中,再加热维持微沸状态20~40min,停止加热和搅拌熟化20~40min;再加热保持微沸状态120~240min,冷却至60~70℃,趁热过滤,将过滤得到的固体洗涤干净,得纯化的偏钛酸;将纯化的偏钛酸以10~15℃/min的升温速率升至750~850℃,并保温100~150min,冷却得高纯二氧化钛。
5.但是该技术方案,虽然可以实现利用硫酸法来获取到二氧化钛,但是在得到的偏钛酸(水合二氧化钛)采用回转窑进行煅烧时,由于煅烧脱水、脱硫气体直接对输入窑内的水合二氧化钛进行预热处理,使得接触预热气体的水合二氧化钛加剧污染,从而降低了脱水、脱硫效率,并且在高温煅烧时,形成的烧结颗粒不仅不便于在窑内与二氧化钛粉末的分离,而且存在于二氧化钛粉末内时,还容易因颗粒大小的不均匀化而影响二氧化钛的煅烧均匀性。
技术实现要素:6.本发明的目的是针对现有技术的不足之处,提供一种高纯二氧化钛生产设备,通过抽气组件沿气流上升方向往复动作抽取回转窑组件内进行脱水、脱硫的气体,隔离导送至正在输料的给料组件,沿内、外螺旋通道均匀导热至输送的二氧化钛进行隔离预热,清理
组件对脱水、脱硫后的持续高温煅烧二氧化钛进行烧结颗粒的辊压后初步过滤,并经旋涡状的过滤件拾取烧结料旋转离心,直至烧结料旋转至旋涡状中心被吹送至排气通道送出,以实现对水合二氧化钛对窑内的输入料隔离预热以及对煅烧过程中烧结料从窑内与二氧化钛粉末的连续分离、排放处理。
7.为实现上述目的,本发明提供如下技术方案:一种高纯二氧化钛生产设备,包括回转窑组件,所述回转窑组件包括脱水煅烧区域、脱硫煅烧区域以及转型煅烧区域;其特征在于,还包括:给料组件,用于将水合二氧化钛送入至所述回转窑组件的所述给料组件布置在所述回转窑组件的窑尾一端;抽气组件,用于抽取脱水、脱硫气体对所述给料组件输送的水合二氧化钛进行隔离供热的所述抽气组件设于所述回转窑组件;以及清理组件,沿所述回转窑组件回转输送方向对二氧化钛进行碾压、对烧结料进行旋转分离的所述清理组件布置在所述回转窑组件内;所述抽气组件设于所述回转窑组件内的脱水脱煅烧区域、脱硫煅烧区域上方;所述清理组件设于所述回转窑组件的脱硫煅烧区域末端至转型煅烧区域。
8.进一步的,所述给料组件包括:壳体,所述壳体顶部开设有进料口;输料转体,将脱水、脱硫气体热量封闭传导至进料口输入的水合二氧化钛的所述输料转体插设在所述壳体上且顶部与所述进料口相对应;以及传动组件,用于驱动所述输料转体旋转输料的所述传动组件安装在所述壳体上。
9.进一步的,所述输料转体包括:输料杆件,所述输料杆件的外壁开设有外螺旋通道;隔气通道,所述隔气通道沿所述输料杆件周向方向呈环形开设于所述输料杆件的一侧;以及排气口,开设于所述输料杆件上且布置在所述隔气通道相对立一侧的所述排气口与所述隔气通道相连通;所述隔气通道的内壁开设有与所述外螺旋通道相对应的内螺旋通道。
10.进一步的,所述抽气组件包括:抽气管道,端部链接在所述壳体上的所述抽气管道与所述隔气通道相对应连通,所述抽气管道的底部均匀设有进气道;抽取部,用于往复调整所述进气道通气量进行抽气动作的所述抽取部滑动设于所述抽气管道内;以及将所述抽取部与所述传动组件传动连接的动力组件。
11.进一步的,所述抽气管道包括:横向布置的收集管道;将所述收集管道连通引导至所述回转窑组件旋转中心的中间管道;以及锥形状布置、将所述中间管道内气体引导至所述隔气通道的引导管道。
12.进一步的,所述抽取部包括:与动力组件相连接的驱动轴;安装在所述驱动轴上的吸气组件;以及安装于所述吸气组件底部且与所述进气道一侧滑动连接的下挡板;动力组件使驱动轴带动吸气组件对应于进气道进行抽气,动力组件使驱动轴沿抽气管道轴向方向来回移动,使移动的下挡板改变进气道通气量。
13.进一步的,所述清理组件包括:沿所述回转窑组件轴向方向布置的机架,所述机架的两侧分别开设有输气通道、排气通道;过滤组件,铲起辊碾煅烧过程中的二氧化钛、旋转滤出烧结颗粒的所述过滤组件安装在所述输气通道、排气通道之间。
14.进一步的,所述过滤组件包括:铲压组件,铲起、辊碾二氧化钛后进行过滤排放的所述铲压组件呈j形状布置;旋转过滤组件,旋转拾取所述铲压组件上未滤出物料进行旋转筛滤分离出烧结颗粒的所述旋转过滤组件设于所述铲压组件的上方;以及挡件,用于遮挡扬起物料的所述挡件设于所述旋转过滤组件的顶部一侧;铲压组件铲起并辊碾二氧化钛的
同时,对旋转移动的二氧化钛中烧结颗粒进行初步过滤,旋转过滤组件拾取烧结旋转分离,使分离的二氧化钛落至铲压组件、烧结颗粒经输气通道的输气动力吹入排气通道。
15.进一步的,所述旋转过滤组件包括:旋涡状布置的过滤件;安装于所述过滤件两侧且分别于所述输气通道、排气通道相连通的旋转座;以及驱动所述旋转座、过滤件旋转动作的联动组件;所述联动组件通过动力组件传动。
16.为实现上述目的,本发明还提供了一种高纯二氧化钛生产设备用于煅烧水合二氧化钛的工艺,其特征在于,包括以下步骤:步骤一、隔离抽气,给料组件在对回转窑组件窑尾给料时,传动驱动轴转动的同时,沿回转窑组件轴向方向来回移动,使布置在脱水脱煅烧区域、脱硫煅烧区域上方的吸气组件旋转抽气的同时,调整进气道通气量,对从进气道至二氧化钛之间进行抽气强度的往复调整;步骤二、隔离供热送料,抽取气体经抽气管道进入隔气通道中,水合二氧化钛原料经外螺旋通道朝向回转窑组件窑尾给料,同时抽出气体经内螺旋通道均匀隔离导热至另一侧正在输出的水合二氧化钛原料;步骤三、烧结过滤,经回转窑组件脱水、脱硫后的二氧化钛到达清理组件,铲压组件沿回转窑组件旋转内壁铲起二氧化钛并辊碾处理,二氧化钛细粉穿过铲压组件排出,留在铲压组件内的烧结颗粒及少量二氧化钛细粉被旋转过滤组件旋转拾取,并沿旋涡状轨道不断旋转分离,直至烧结颗粒旋转至过滤件中心,被输气通道气力作用吹出至排气通道排出。
17.本发明的有益效果在于:(1)本发明通过给料组件和抽气组件之间的相互配合,可以实现将经窑头提供的煅烧热量抽取作用于正在给料的给料组件的同时,还能够实现气流的隔离导热,从而保证了对输送至窑尾的水合二氧化钛预热的同时,还解决了因气流携带蒸发水、硫,直接接触水合二氧化钛而形成污染;(2)本发明通过输料杆件外侧、隔气通道内侧的双螺旋通道结构设计,可以保证在输送水合二氧化钛的过程中,使热量沿隔气通道内侧均匀的送至输料杆件外壁,从而保证了水合二氧化钛的受热均匀性;(3)本发明通过抽气管道和抽取部之间的配合设计,可以通过往复改变进气道通量的方式,以实现沿气流上升高度方向快速抽取蒸发气;(4)本发明通过抽气组件和清理组件之间的相互配合,可以实现对抽气脱水、脱硫后的二氧化钛在进行持续的转型成金红石型时,对烧结的颗粒进行旋转过滤并清除出去,从而解决了二氧化钛煅烧时清理烧结颗粒的同时,还解决了因烧结颗粒存在于二氧化钛粉末中而影响二氧化钛粉末的受热均匀性的技术问题;(5)本发明通过铲压组件和旋转过滤组件之间的相互配合以及旋转过滤组件旋涡状的过滤设计,可以实现将烧结颗粒初步铲出过滤的同时,还能够实现拾取初步过滤的烧结料经旋转过滤的方式,快速清除烧结颗粒表面吸附的二氧化钛,并同步完成对清理完成的烧结颗粒连续性排出;综上所述,本发明具有水合二氧化钛煅烧时隔离预热输入物料、快速清除烧结颗粒等优点。
附图说明
18.图1为本发明整体结构示意图;图2为本发明图1的剖视图;图3为本发明回转窑组件的内部结构示意图;图4为本发明清理组件的结构示意图;图5为本发明图4的剖视图;图6为本发明过滤组件的剖视图;图7为本发明联动组件的局部结构示意图;图8为本发明抽气组件的结构示意图;图9为本发明图8中a处放大图;图10为本发明抽气管道的底部一侧结构示意图;图11为本发明抽气管道端截面的结构示意图;图12为本发明送料组件的结构示意图;图13为本发明图12的剖视图;图14为本发明图13中b处放大图;图15为本发明生产工艺流程图。
19.具体实施方式
20.下面将结合本发明实施例中的附图,对本发明实施例中的技术方案进行清楚、完整地描述,显然,所描述的实施例仅是本发明一部分实施例,而不是全部的实施例。基于本发明中的实施例,本领域普通技术人员在没有做出创造性劳动前提下所获得的所有其他实施例,都属于本发明保护的范围。
21.在本发明的描述中,需要理解的是,术语“中心”、“纵向”、“横向”、“长度”、“宽度”、“厚度”、“上”、“下”、“前”、“后”、“左”、
ꢀ“
右”、“竖直”、“水平”、“顶”、“底”、“内”、“外”、
“ꢀ
顺时针”、“逆时针”等指示的方位或位置关系为基于附图所示的方位或位置关系,仅是为了便于描述本发明和简化描述,而不是指示或暗示所指的设备或元件必须具有特定的方位、以特定的方位构造和操作,因此不能理解为对本发明的限制。
22.此外,术语“第一”、
ꢀ“
第二”仅用于描述目的,而不能理解为指示或暗示相对重要性或者隐含指明所指示的技术特征的数量。由此,限定有“第一”、“第二”的特征可以明示或者隐含地包括一个或者更多个该特征。在本发明的描述中,“多个”的含义是两个或两个以上,除非另有明确具体的限定。
23.实施例一如图1所示,一种高纯二氧化钛生产设备,包括回转窑组件1,所述回转窑组件1包括脱水煅烧区域、脱硫煅烧区域以及转型煅烧区域;还包括:给料组件2,用于将水合二氧化钛送入至所述回转窑组件1的所述给料组件2布置在所述回转窑组件1的窑尾一端;抽气组件3,用于抽取脱水、脱硫气体对所述给料组件3输送的水合二氧化钛进行隔离供热的所述抽气组件2设于所述回转窑组件1;以及清理组件4,沿所述回转窑组件1回转输送方向对二氧化钛进行碾压、对烧结料进行旋转分离的所述清理组件4布置在所述回转窑组件1内;所
述抽气组件3设于所述回转窑组件1内的脱水脱煅烧区域、脱硫煅烧区域上方;所述清理组件4设于所述回转窑组件1的脱硫煅烧区域末端至转型煅烧区域。
24.通过上述内容,可以看出,在进行二氧化钛加工生产过程中,在通过硫酸法制得水合二氧化钛后,需要经过煅烧的方式,来完成游离水和结晶水的脱除、脱硫以及将锐钛型对金红石的转化,本发明中的回转窑组件1优选为现有技术中的回转窑,即通过设置从窑尾到窑头的煅烧温度有
①
脱去游离水和结晶水的150-300℃
②
脱硫过程的650℃左右
③
锐钛型向金红石型转化过程的700-950℃;具体在煅烧过程中,通过利用给料组件2不断的输送水合二氧化钛从回转窑组件1的窑尾处加入,并且在加入水合二氧化钛时,为了提高热量利用高效性,通过将经历脱水、脱硫煅烧后的蒸发气体抽出,并以隔离状态送至给料组件2,对正在输入至回转窑1的水合二氧化钛进行隔离预热处理,从而实现将蒸发脱去水、硫排放的同时,还解决了因脱离气流中的水、硫因在未封闭状态下直接对正在输入水合二氧化钛预热而导致的输入二氧化钛的污染;而且在二氧化钛煅烧实现锐钛型对金红石型转化时,由于煅烧温度等因素的影响,容易导致在煅烧时出现烧结现象,而该被烧结颗粒不仅难以直接从回转窑组件1中直接剔除,而且还容易影响周围二氧化钛煅烧时的受热均匀性,因此通过利用清理组件4在进行700-950℃的煅烧处理时,可以通过初步碾压二氧化钛,使得烧结的二氧化钛被碾开,从而释放出其中未被烧结的二氧化钛粉末,并通过旋转过滤分离出经初步碾压的二氧化钛,而过滤后的二氧化钛粉末经过清理组件4向窑头输出。
25.需要补充的是,如图1所示,所述回转窑组件1包括窑头位于低处且窑尾位于高处的窑炉11、设于所述窑炉11下方的窑座12、安装在所述窑座12上且用于驱动所述窑炉11旋转的驱转组件13以及设于所述窑头处的燃烧器14,该驱转组件13、燃烧器14均为回转窑领域中的现有技术,在此不做赘述。
26.如图12所示,所述给料组件2包括:壳体21,所述壳体21顶部开设有进料口211;输料转体22,将脱水、脱硫气体热量封闭传导至进料口211输入的水合二氧化钛的所述输料转体22插设在所述壳体21上且顶部与所述进料口211相对应;以及传动组件23,用于驱动所述输料转体22旋转输料的所述传动组件23安装在所述壳体21上。
27.在本实施例中,给料组件2在向回转窑组件1窑尾给料过程中,通过将水合二氧化钛添加至壳体21上方的进料口211中,进而通过传动组件23的驱动带动,从而实现输料转体22的转动,从而实现将水合二氧化钛物料持续的对回转窑组件1的添加,同时,为了实现对水合二氧化钛的预热处理,通过抽气组件3抽取出脱水、脱硫后的热气流进行封闭预热处理,以避免脱出水、硫对输入的水合二氧化钛形成污染。
28.值得注意的是,为了保证水合二氧化钛中脱水气体的充分排出,所述抽气组件3的抽气一端延伸至所述给料组件2的排料位置。
29.如图12和13所示,所述输料转体22包括:输料杆件221,所述输料杆件221的外壁开设有外螺旋通道2211;隔气通道222,所述隔气通道222沿所述输料杆件221周向方向呈环形开设于所述输料杆件221的一侧;以及排气口223,开设于所述输料杆件221上且布置在所述隔气通道222相对立一侧的所述排气口223与所述隔气通道222相连通;所述隔气通道222的内壁开设有与所述外螺旋通道2211相对应的内螺旋通道2221。
30.在本实施例中,输料转体22在对水合二氧化钛进行输料、预热的过程中,通过抽气组件3抽取气体至隔气通道222内,并从排气口223排出回转窑组件1,而在气体经过隔气通
道222时,会经过与输料用的外螺旋通道2211相对应布置的内螺旋通道2221,可以实现热气流对隔气通道222内壁的短暂停留导热的同时,还可以实现隔气通道222内壁与输料杆件221外壁之间距离的均匀性,从而保证了热量传导至输料杆件221外部作用于水合二氧化钛时的均匀性。
31.值得说明的是,如图12和13所示,所述传动组件23包括安装在所述输料杆件221上的第一传动齿轮231、与所述第一传动齿轮231相啮合的第二传动齿轮232以及安装在所述机壳21上且动力端与所述第二传动齿轮232相连接的传动电机233,所述传动电机233优选为伺服电机,所述排气口223穿过所述第一传动齿轮231。
32.如图8和10所示,所述抽气组件3包括:抽气管道31,端部链接在所述壳体21上的所述抽气管道31与所述隔气通道222相对应连通,所述抽气管道31的底部均匀设有进气道311;抽取部32,用于往复调整所述进气道311通气量进行抽气动作的所述抽取部32滑动设于所述抽气管道31内;以及将所述抽取部32与所述传动组件23传动连接的动力组件33。
33.本实施例中,抽气组件3在进行抽气动作时,通过抽取部32不断对各位置处的进气道311下方气体抽取的同时,通过改变进气道311的气通量,在抽取动力不变的条件下,可以实现沿进气道311下方不同高度下的气体抽取动作,而且实现对进气道311下方各高度下的气体高效排出。
34.如图12所示,所述抽气管道31包括:横向布置的收集管道311;将所述收集管道311连通引导至所述回转窑组件1旋转中心的中间管道312;以及锥形状布置、将所述中间管道312内气体引导至所述隔气通道222的引导管道313。
35.在本实施例中,为了保证经抽气管道31抽出气体对隔气通道222的对应、均匀输送,通过利用引导管道313将偏离隔气通道222中心的收集管道311收集气体引入至隔气通道222中心,并均匀的分配至隔离通道222中,从而保证了水合二氧化钛预热时的受热均匀性。
36.如图10和11所示,所述抽取部32包括:与动力组件33相连接的驱动轴321;安装在所述驱动轴321上的吸气组件322;以及安装于所述吸气组件322底部且与所述进气道311一侧滑动连接的下挡板323;动力组件33使驱动轴321带动吸气组件322对应于进气道311进行抽气,动力组件33使驱动轴321沿抽气管道31轴向方向来回移动,使移动的下挡板323改变进气道311通气量。
37.本实施例中,抽取部32在进行抽取过程中,通过驱动轴321的转动,可以带动吸气组件322工作,从而实现吸气组件322对各进气道311产生吸力,并且通过驱动轴321的移动带动吸气组件322以及下挡板323的移动,从而实现下挡板323对进气道311的遮挡量进行调整,从而调整进气道311的进气通量。
38.如图11所示,所述吸气组件322包括滑动设于所述收集管道311内的滑动座3221、转动安装在所述滑动座3221内且周向安装在所述驱动座321上的叶轮3222。
39.在本实施例中,叶轮3222为提供吸气动力的风机叶轮,在此不做赘述。
40.如图13所示,所述动力组件33包括用于使驱动轴321旋转的第一动力组件331以及用于使驱动轴321沿其轴向方向来回移动的第二动力组件332。
41.如图14所示,所述第一动力组件331包括与所述驱动轴321滑动连接且设于所述中间管道312内的第一带盘3311、将第一带盘3311安装在所述中间管道312内壁上的第一盘座
3312、设于所述第一带盘3311下方且与所述输料杆件321相连接的动力杆3315、安装在所述动力杆3315上的第二带盘3316、将所述第一带盘3311与第二带盘3316传动连接的第一动力皮带3314以及轴向设于所述驱动轴321上且滑动穿过所述第一带盘3311两侧的花键3313。
42.在本实施例中,在输料杆件221转动时带动第二带盘3316旋转,从而通过第一动力皮带3314传动给第一带盘3311,进而带动通过花键3313连接的驱动轴321转动,从而驱动吸气组件322进行吸气动作。
43.如图9和12所示,所述第二动力组件332包括安装于所述驱动轴321端部的导向件3322、开设于所述导向件3322上且呈对称的s形状布置的导向轨道3322以及与所述引导管道313相连接且滑动插设在所述导向轨道3322内的导向件3323。
44.本实施例中,当驱动轴321转动时,会带动导向件3322转动,从而使得导向件3323在导向轨道3322内移动,从而使得导向件3323沿驱动轴321轴向方向来回驱动驱动轴321移动。
45.实施例二如图4所示,其中与实施例一中相同或相应的部件采用与实施例一相应的附图标记,为简便起见,下文仅描述与实施例一的区别点。该实施例二与实施例一的不同之处在于:所述清理组件4包括:沿所述回转窑组件1轴向方向布置的机架41,所述机架41的两侧分别开设有输气通道411、排气通道412;过滤组件42,铲起辊碾煅烧过程中的二氧化钛、旋转滤出烧结颗粒的所述过滤组件42安装在所述输气通道411、排气通道412之间。
46.在本实施例中,清理组件4在对窑内煅烧过程中的烧结颗粒进行处理时,通过输气通道411输入气力(需要注意的是,为了保证炉内气氛,输入的气体为惰性气体),进而在过滤组件42将烧结颗粒过滤出来后,烧结颗粒会移动至过滤组件42的旋转中心,从而输气通道411顺着该旋转中心将烧结颗粒吹出至倾斜布置的排气通道412内,进而顺着该排气通道412滑出位于回转窑组件1窑头排出。
47.如图4所示,所述过滤组件42包括:铲压组件421,铲起、辊碾二氧化钛后进行过滤排放的所述铲压组件421呈j形状布置;旋转过滤组件422,旋转拾取所述铲压组件421上未滤出物料进行旋转筛滤分离出烧结颗粒的所述旋转过滤组件422设于所述铲压组件421的上方;以及挡件423,用于遮挡扬起物料的所述挡件423设于所述旋转过滤组件422的顶部一侧;铲压组件421铲起并辊碾二氧化钛的同时,对旋转移动的二氧化钛中烧结颗粒进行初步过滤,旋转过滤组件422拾取烧结旋转分离,使分离的二氧化钛落至铲压组件421、烧结颗粒经输气通道411的输气动力吹入排气通道412。
48.本实施例中,过滤组件42在对烧结颗粒进行过滤处理时,通过利用铲压组件421将沿回转窑输送方向移动的二氧化钛粉末进行铲入过滤,并且在过滤时,为了减少烧结颗粒上夹杂有二氧化钛粉末,通过铲压组件421还能够实现对烧结颗粒进行初步碾压处理,再进行过滤,而且在二氧化钛粉末朝向窑头一侧移动时,会逐渐进入至j形状的铲压组件421中,经过过滤留下来的烧结颗粒以及附带的二氧化钛粉末会被旋转过滤组件422拾取到,并不断朝向旋转中心移送的同时进行离心过滤,同时在输气通道411的气力作用下,可以实现对烧结颗粒上附着的二氧化钛粉末的高效去除,同时以便于将分离出来的烧结颗粒快速导出排放;并且为了保证过滤过程中的粉末飞扬,在旋转过滤组件422上方设置的挡件423能够
起到很好的格挡作用。
49.如图5和6所示,所述铲压组件421包括安装在所述机架41上的j形状支架4211、安装在所述j形状支架4211上的j形状过滤网4212、设于所述j形状过滤网4212上方且与所述机架41相连接的压辊4213、设于所述压辊4213一侧的刮刀4216、安装在所述压辊4213上的第五带盘4214、安装在所述旋转过滤组件422上的第六带盘以及将第五带盘4214与第六带盘传动连接的传动带4215;所述j形状支架4211的前段一侧设有倒角状的铲头。
50.本实施例中,在旋转过滤组件422旋转时,会通过第六带盘带动第五带盘4214转动,从而使得压辊4213滚动碾压颗粒较大的烧结颗粒,并通过刮刀4212来实现对转动过程中的压辊4213表面进行清理。
51.值得注意的是,在旋转过滤组件422带动压辊4213转动时,还可以通过调整结构设计使得压辊4213反向转动,从而使得压辊4213转动碾压烧结颗粒的同时,使得烧结颗粒快速通过压辊4213底部的方式也能够实现本发明,具体的,可以通过将旋转过滤组件422的旋转动力传动给一组中间齿轮,再讲中间齿轮与第五带盘4214同轴连接即可,前者正向转动辊压,可以减少未被碾压的烧结颗粒量,后者反向旋转辊压,可以提高烧结颗粒的通过效率,在此不做赘述。
52.如图6所示,所述旋转过滤组件422包括:旋涡状布置的过滤件4221;安装于所述过滤件4221两侧且分别于所述输气通道411、排气通道412相连通的旋转座4222;以及驱动所述旋转座4222、过滤件4221旋转动作的联动组件4223;所述联动组件4223通过动力组件33传动。
53.本实施例中,通过动力组件33将动力经联动组件4223传动给过滤件4221旋转,从而使得过滤件4221沿旋涡状的过滤轨迹不断的过滤出烧结颗粒至旋涡状中心,并通过输气通道411吹出烧结颗粒。
54.值得注意的是,在过滤件4221旋转过滤的过程中,其最大外径在旋转的过程中,会不断的沿j形状过滤网4212的弧形布置面转动,从而当j形状过滤网4212内壁收集到过滤出的烧结颗粒和二氧化钛粉末时,可以实现过滤件4221旋转铲入该烧结颗粒和二氧化钛粉末,进行沿旋涡轨迹旋转过滤的目的。
55.如图5和7所示,所述联动组件4223包括依次安装在所述机架41上的固定座42232、活动穿过所述固定座42232上的旋转轴42231、安装在所述旋转轴42231上且与所述旋转座4222传动连接的第一斜齿轮42233、安装在所述旋转轴42231上的第七齿轮42234、安装在所述机架1上且布置在相邻两组第七齿轮42234之间的传动座42235、活动穿过传动座42235的传动轴杆42236以及安装在所述传动轴杆42236两端且与相邻的两组所述第七齿轮42234传动啮合的第八齿轮42237,所述旋转座4222的一侧布置有与所述第一斜齿轮42233传动啮合的第二斜齿轮。
56.本实施例中,当传动组件33传动给与其对应连接的旋转轴42231转动时,会通过第一斜齿轮42233带动第二斜齿轮转动的同时,使得过滤件4221旋转过滤出烧结颗粒,并且转动的旋转轴42231还会通过第七齿轮42234与第八齿轮42237之间的传动连接,从而依次驱动沿机架41方向布置的各组过滤件4221旋转过滤烧结颗粒,从而实现在煅烧过程中,沿二氧化钛输出方向进行烧结颗粒的过滤。
57.如图9和14所示,所述动力组件33还包括用于驱动联动组件4223的第三动力组件
333,所述第三动力组件333包括安装在穿出至中间管道312外部部分的驱动轴321上的第九传动齿轮3332、安装在所述引导管道313外部的齿轮支架3331、安装在所述齿轮支架3331上且与所述第九传动齿轮3332传动啮合的第十传动齿轮3333、与第十传动齿轮3333同轴安装的第十一带盘3334、设于所述第十一带盘3334下方且安装在所述旋转轴42231上的第十二带盘3335、将所述第十一带盘3334和第十二带盘3335传动连接的动力传动带3336以及安装在所述引导管道313外壁上且与所述旋转轴42231端部活动连接的支架杆3337。
58.本实施例中,当驱动轴321旋转时,会带动第九传动齿轮3332转动,进而传动给第十传动齿轮3333,同时通过带、轮传动,带动旋转轴42231转动,从而驱动过滤件4221进行旋转过滤。
59.实施例三如图15所示,一种高纯二氧化钛生产工艺,包括以下步骤:步骤一、隔离抽气,给料组件2在对回转窑组件1窑尾给料时,传动驱动轴321转动的同时,沿回转窑组件1轴向方向来回移动,使布置在脱水脱煅烧区域、脱硫煅烧区域上方的吸气组件322旋转抽气的同时,调整进气道311通气量,对从进气道311至二氧化钛之间进行抽气强度的往复调整;步骤二、隔离供热送料,抽取气体经抽气管道31进入隔气通道222中,水合二氧化钛原料经外螺旋通道2211朝向回转窑组件1窑尾给料,同时抽出气体经内螺旋通道2221均匀隔离导热至另一侧正在输出的水合二氧化钛原料;步骤三、烧结过滤,经回转窑组件1脱水、脱硫后的二氧化钛到达清理组件4,铲压组件421沿回转窑组件1旋转内壁铲起二氧化钛并辊碾处理,二氧化钛细粉穿过铲压组件421排出,留在铲压组件421内的烧结颗粒及少量二氧化钛细粉被旋转过滤组件422旋转拾取,并沿旋涡状轨道不断旋转分离,直至烧结颗粒旋转至过滤件4221中心,被输气通道411气力作用吹出至排气通道412排出。
60.以上所述仅为本发明的较佳实施例而已,并不用以限制本发明,凡在本发明的精神和原则之内所作的任何修改、等同替换和改进等,均应包含在本发明的保护范围之内。