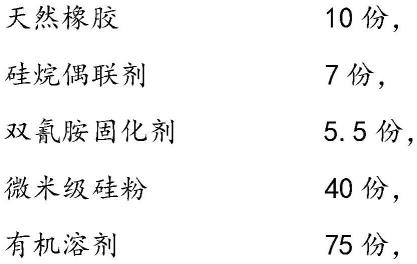
1.本发明属于铝基板技术领域,具体涉及一种用于高耐压铝基板的胶粘剂组合物及其制备方法。
背景技术:2.铝基板是一种具有良好散热功能的金属基覆铜板,一般单面板由三层结构所组成,分别是电路层(铜箔)、绝缘层和金属基层(铝板)。用于高端使用的也有设计为双面板,结构为电路层、绝缘层、铝基、绝缘层、电路层。极少数应用为多层板,可以由普通的多层板与绝缘层、铝基贴合而成。
3.铝基板与电路层之间必须要有一层导热绝缘层,来实现金属基板与电路层之间的绝缘和粘合。例如专利申请文件cn 111040701 a公开了一种耐高温、高韧性环氧树脂胶黏剂,由组分a和组分b制得,其中,组分a由双酚a型环氧树脂、增韧剂超支化聚酯化合物、活性稀释剂、硅烷偶联剂、耐热填料微米级氧化铝粉、触变剂、消泡剂制得,组分b由聚酰胺固化剂、脂环胺固化剂、硅烷偶联剂、耐热填料微米级氧化铝粉,触变剂和消泡剂制得;本发明还公开了一种耐高温、高韧性环氧树脂胶黏剂的制备方法,采用加热搅拌分别制备组分a和组分b再混合。
4.以上现有技术中的导热绝缘层主要是由有机树脂材料填充单一的氧化铝导热粒子制备而成,使得铝基板整体的耐压性能较低。因此,还需要对现有技术中的铝基板进一步改进,在保持良好热传导性的基础上提高其耐压性能。
技术实现要素:5.针对现有技术中存在的技术问题,本发明提供了一种用于高耐压铝基板的胶粘剂组合物及其制备方法。
6.本发明采用的技术方案如下:
7.一种用于高耐压铝基板的胶粘剂组合物。所述铝基板包括金属基层、导热绝缘层和电路层,所述导热绝缘层由胶粘剂干燥后获得,其中,所述胶粘剂组合物由以下重量份数组分组成:
[0008][0009]
所述胶粘剂组合物的粘度为涂4#杯1-8min。
[0010]
采用以上技术方案,采用双酚a型环氧树脂和酚醛树脂复配作为有机树脂基体,与单一的双酚a型环氧树脂相比,得到的所述胶粘剂组合物有利于提高所述铝基板的耐压性;此外,通过将天然橡胶与有机树脂材料复配,得到的所述胶粘剂组合物有利于提高铝基板的耐压性。所述胶粘剂组合物通过在有机树脂基体中添加微米级硅粉作为导热填料粒子,从而能够改善整个体系的导热性能。本发明增加了有机溶剂的用量,适当减小了所述胶粘剂组合物的粘度,使得单层胶粘剂层的厚度控制在90-110μm范围内,双层胶粘剂层叠加在一起经热压合工序后形成所述导热绝缘层,使得所述导热绝缘层更均匀,保证所述铝基板的耐压性。
[0011]
双酚a型环氧树脂为常见的胶粘剂有机树脂材料,但本发明减少了其用量,只采用30-50份,便于添加合适含量的酚醛树脂与之复配。但双酚a型环氧树脂的添加量不能低于30份,否则影响所述胶粘剂的粘结性。进一步,双酚a型环氧树脂的添加量优选为35-45份,更优选为40份。
[0012]
酚醛树脂,是一种合成塑料,无色或黄褐色透明固体,因电气设备使用较多,也俗称电木,热传导性、耐燃性、耐水性和绝缘性优良,耐酸性较好,耐碱性差,机械和电气性能良好。本发明发现在双酚a型环氧树脂中复配酚醛树脂作为有机树脂基体,能增强所述铝基板的耐压性。如果酚醛树脂的含量低于10份,则所述铝基板的耐压性提高的不明显;如果酚醛树脂的含量高于30份,则双酚a型环氧树脂的含量降低,则会影响所述胶粘剂的粘结性。因此,考虑到所述铝基板的综合性能,本发明中选择采用10-30份的酚醛树脂。进一步,酚醛树脂的添加量优选为15-25份,更优选为20份。
[0013]
天然橡胶,是指从巴西橡胶树上采集的天然胶乳,经过凝固、干燥等加工工序而制成的弹性固状物。天然橡胶是一种以聚异戊二烯为主要成分的天然高分子化合物,天然橡胶其橡胶烃(聚异戊二烯)含量在90%以上,还含有少量的蛋白质、脂肪酸、糖分及灰分等。天然橡胶是非极性橡胶,所以电绝缘性能良好。将天然橡胶添加到本发明的胶粘剂中,有助于增加所述铝基板的耐热性,因此,本发明中天然橡胶的添加量为5-15份,进一步,天然橡胶的添加量优选为8-12份,更优选为10份。
[0014]
本发明中对有机溶剂的种类不作特殊限定,只要能形成均匀的胶粘剂浆料即可,例如可以采用dmf、乙酸乙酯、丙酮等。但有机溶剂的添加量对本发明至关重要,因为这关系到胶粘剂的粘度和最后形成的导热绝缘层的厚度问题。如果有机溶剂添加量低于70份,则
胶粘剂粘度高于涂4#杯8min,涂膜厚度可能不均匀且光洁度较差;如果有机溶剂添加量高于80份,则胶粘剂粘度低于涂4#杯1min,不能在电路层上形成100μm左右厚度的胶粘剂层,耐压性大大降低。因此,本发明中有机溶剂的添加量为70-80份。进一步,有机溶剂的添加量为73-77份,更进一步,有机溶剂的添加量为75份。
[0015]
由于铝基板与电路层之间必须要有一层导热绝缘层,来实现金属基板与电路层之间的绝缘和粘合。而目前的导热绝缘层主要是由有机树脂材料填充导热粒子制备而成的。但目前,导热粒子填料一般采用单一的氧化铝,但氧化铝热传递性能有限。本发明通过以微米级硅粉代替氧化铝,大大提高了铝基板的导热性能。进一步,纳米级硅粉的粒径优选为3-7μm,更优选为5μm。
[0016]
另外,本发明还提供了一种用于高耐压铝基板的胶粘剂组合物的制备方法。所述制备方法包括以下步骤:将所述胶粘剂组合物各组分按照比例称量、混合均匀,得到所述胶粘剂组合物。
[0017]
此外,本发明还提供了一种高耐压铝基板,包括金属基层、导热绝缘层和电路层,其中,所述导热绝缘层由以上任一项所述的胶粘剂组合物干燥后获得。
[0018]
此外,本发明还提供了一种耐高压铝基板的制备方法。所述制备方法包括以下步骤:
[0019]
(1)将所述胶粘剂组合物辊涂在所述电路层表面形成胶粘剂层一,以及将所述胶粘剂组合物辊涂在离型膜表面形成胶粘剂层二;
[0020]
(2)将所述胶粘剂层二覆盖在所述胶粘剂层一表面,去处离型膜,并将所述金属基层覆盖在所述胶粘剂层二表面,形成铝基板半成品;
[0021]
(3)将所述铝基板半成品热压合,形成所述铝基板。
[0022]
在以上技术方案中,通过双层100μm左右的胶粘剂层压合成一层200μm左右的导热绝缘层,得到的导热绝缘层更均匀,质量更好。如果增大所述胶粘剂组合物的粘度,然后直接由一层200μm左右的胶粘剂层压合形成一层200μm左右的导热绝缘层,理论上是可以的,但实际生产中技术并不成熟,得到的导热绝缘层质量不达标,厚度过大容易导致耐冲剪性变差,会有分层和爆边的情况。
[0023]
进一步,本发明对耐压性要求较高,因此,所述导热绝缘层的厚度为180-220μm,更优选为200μm,可以使得本发明获得的所述铝基板耐热性达到9-11.5kv的优异程度。
[0024]
相较于现有技术,本发明的有益效果是:
[0025]
(1)所述胶粘剂组合物采用双酚a型环氧树脂和酚醛树脂复配作为有机树脂基体,与单一的双酚a型环氧树脂相比,有利于提高所述铝基板的耐压性;
[0026]
(2)所述胶粘剂组合物通过在有机树脂基体中添加纳米级硅粉作为导热填料粒子,从而能够改善整个体系的导热性能;
[0027]
(3)所述胶粘剂组合物合理调配了有机溶剂的用量,适当减小了所述胶粘剂组合物的粘度,使得单层胶粘剂层的厚度控制在100μm范围内,然后双层胶粘剂层压合得到的导热绝缘层综合质量高,大大提高了所述铝基板的耐压性。
具体实施方式
[0028]
以下示出实施例更详细地说明本发明。本发明不限于以下的实施例。
[0029]
实施例1
[0030]
一种用于高耐压铝基板的胶粘剂组合物。所述胶粘剂组合物由以下重量份数组分组成:
[0031][0032]
所述胶粘剂组合物的粘度为涂4#杯5min;
[0033]
双酚a型环氧树脂采用低分子固态双酚a型环氧树脂,微米级硅粉的粒径为5μm。
[0034]
一种高耐压铝基板,包括金属基层、导热绝缘层和电路层,其中,所述导热绝缘层由以上所述的胶粘剂组合物干燥后获得。具体制备方法包括以下步骤:
[0035]
(1)将所述胶粘剂组合物辊涂在所述电路层表面形成100μm厚度的胶粘剂层一,以及将所述胶粘剂组合物辊涂在离型膜表面形成100μm厚度的胶粘剂层二;
[0036]
(2)将胶粘剂层二覆盖在所述胶粘剂层一表面,去除离型膜,并将所述金属基层覆盖在所述胶粘剂层二表面,形成铝基板半成品;
[0037]
(3)将所述铝基板半成品热压合,形成所述铝基板;其中,所述导热绝缘层的厚度为200μm。
[0038]
实施例2
[0039]
一种用于高耐压铝基板的胶粘剂组合物。所述胶粘剂组合物由以下重量份数组分组成:
[0040][0041]
所述胶粘剂组合物的粘度为涂4#杯5min;
[0042]
双酚a型环氧树脂采用低分子固态双酚a型环氧树脂,微米级硅粉的粒径为5μm。
[0043]
一种高耐压铝基板,包括金属基层、导热绝缘层和电路层,其中,所述导热绝缘层由以上所述的胶粘剂组合物干燥后获得。具体制备方法包括以下步骤:
[0044]
(1)将所述胶粘剂组合物辊涂在所述电路层表面形成100μm厚度的胶粘剂层一,以及将所述胶粘剂组合物辊涂在离型膜表面形成100μm厚度的胶粘剂层二;
[0045]
(2)将胶粘剂层二覆盖在所述胶粘剂层一表面,去除离型膜,并将所述金属基层覆盖在所述胶粘剂层二表面,形成铝基板半成品;
[0046]
(3)将所述铝基板半成品热压合,形成所述铝基板;其中,所述导热绝缘层的厚度为200μm。
[0047]
实施例3
[0048]
一种用于高耐压铝基板的胶粘剂组合物。所述胶粘剂组合物由以下重量份数组分组成:
[0049][0050]
所述胶粘剂组合物的粘度为涂4#杯5min;
[0051]
双酚a型环氧树脂采用低分子固态双酚a型环氧树脂,微米级硅粉的粒径为5μm。
[0052]
一种高耐压铝基板,包括金属基层、导热绝缘层和电路层,其中,所述导热绝缘层由以上所述的胶粘剂组合物干燥后获得。具体制备方法包括以下步骤:
[0053]
(1)将所述胶粘剂组合物辊涂在所述电路层表面形成100μm厚度的胶粘剂层一,以及将所述胶粘剂组合物辊涂在离型膜表面形成100μm厚度的胶粘剂层二;
[0054]
(2)将胶粘剂层二覆盖在所述胶粘剂层一表面,去除离型膜,并将所述金属基层覆盖在所述胶粘剂层二表面,形成铝基板半成品;
[0055]
(3)将所述铝基板半成品热压合,形成所述铝基板;其中,所述导热绝缘层的厚度为200μm。
[0056]
对比例1
[0057]
一种用于高耐压铝基板的胶粘剂组合物。所述胶粘剂组合物由以下重量份数组分组成:
[0058][0059][0060]
所述胶粘剂组合物的粘度为涂4#杯5min;
[0061]
双酚a型环氧树脂采用低分子固态双酚a型环氧树脂,微米级硅粉的粒径为5μm。
[0062]
一种高耐压铝基板,包括金属基层、导热绝缘层和电路层,其中,所述导热绝缘层由以上所述的胶粘剂组合物干燥后获得。具体制备方法包括以下步骤:
[0063]
(1)将所述胶粘剂组合物辊涂在所述电路层表面形成100μm厚度的胶粘剂层一,以及将所述胶粘剂组合物辊涂在离型膜表面形成100μm厚度的胶粘剂层二;
[0064]
(2)将胶粘剂层二覆盖在所述胶粘剂层一表面,去除离型膜,并将所述金属基层覆盖在所述胶粘剂层二表面,形成铝基板半成品;
[0065]
(3)将所述铝基板半成品热压合,形成所述铝基板;其中,所述导热绝缘层的厚度为200μm。
[0066]
对比例2
[0067]
一种用于高耐压铝基板的胶粘剂组合物。所述胶粘剂组合物由以下重量份数组分组成:
[0068][0069]
所述胶粘剂组合物的粘度为涂4#杯5min;
[0070]
双酚a型环氧树脂采用低分子固态双酚a型环氧树脂,微米级硅粉的粒径为5μm。
[0071]
一种高耐压铝基板,包括金属基层、导热绝缘层和电路层,其中,所述导热绝缘层由以上所述的胶粘剂组合物干燥后获得。具体制备方法包括以下步骤:
[0072]
(1)将所述胶粘剂组合物辊涂在所述电路层表面形成100μm厚度的胶粘剂层一,以及将所述胶粘剂组合物辊涂在离型膜表面形成100μm厚度的胶粘剂层二;
[0073]
(2)将胶粘剂层二覆盖在所述胶粘剂层一表面,去除离型膜,并将所述金属基层覆盖在所述胶粘剂层二表面,形成铝基板半成品;
[0074]
(3)将所述铝基板半成品热压合,形成所述铝基板;其中,所述导热绝缘层的厚度为200μm。
[0075]
以上实施例1-3和对比例1-2的耐压性能测试数据如表1所示。
[0076]
表1.实施例1-3和对比例1-2的耐压性能
[0077] 击穿电压(kv)实施例111.5实施例29实施例310对比例15对比例26
[0078]
从表1可以看出,实施例2-3的耐压性能低于实施例1的。实施例2的胶粘剂组合物中酚醛树脂的含量比实施例1的低,导致实施例2的铝基板击穿电压也降低。而实施例3的胶粘剂组合物的天然橡胶含量比实施例1的低,导致实施例2的铝基板击穿电压也降低。
[0079]
对比例1的胶粘剂组合物全部采用双酚a型环氧树脂、不含酚醛树脂,导致对比例1的铝基板的击穿电压却明显降低,证明双酚a型环氧树脂和酚醛树脂复配能大大提高铝基板的耐压性。
[0080]
对比例2的胶粘剂组合物没有采用天然橡胶,导致对比例1的铝基板的击穿电压却明显降低,证明天然橡胶和有机树脂材料复配能大大提高铝基板的耐压性。