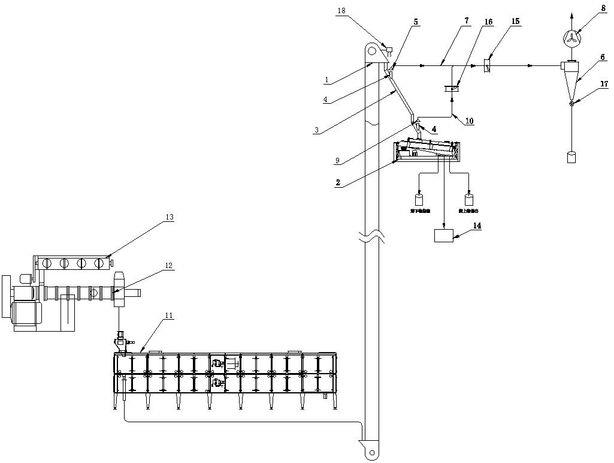
1.本实用新型涉及一种基于负压吸风的热料除湿系统,尤其涉及一种基于负压吸风、适用于膨化饲料成品提升中的热料除湿系统,属于饲料生产设备技术领域。
背景技术:2.在膨化饲料生产过程中,粉状混合原料经调质器进行高温高湿处理后,通过膨化机被制成颗粒状饲料成品,由于刚出膨化机的颗粒状饲料的温度和湿度均较高,则需要对该物料进行烘干。而自烘干机排出的物料温度为45-65℃、水分9-12% ,故需进一步的冷却(如:冷却至较室温高3-5℃的温度),再做后续处理,直至进入成品仓,其中,涉及的工艺流程为:调质
→
膨化
→
烘干
→
冷却
→
提升
→
筛分
→
喷涂
→
进入成品仓。目前,该流程中的调质器、膨化机、烘干机和冷却器一般为从高楼层至低楼层依次布置,烘干后的热料直接进入到冷却器中进行冷却,在提升经冷却器冷却后的物料时,提升机内一般不会产生冷凝水。
3.但为了使车间布局更加紧凑,有时会将冷却器安置在高处(如:楼上),此时,涉及的工艺流程为:调质
→
膨化
→
烘干
→
提升
→
筛分
→
冷却
→
喷涂
→
进入成品仓,该流程中调质器、膨化机和烘干机一般为从高楼层至低楼层依次布置,烘干出来的热料经提升、筛分后,再进入到冷却器中。在此过程中,提升机所提物料为具有一定温度和湿度的物料,特别是在天气较冷时,经常会在提升机的出料口处看到有水蒸气冒出,同时,在提升过程中物料遇冷(提升机筒壁)后会产生冷凝水,冷凝水聚集在筒壁上,当集聚到一定程度后,会倒流至提升机机座处。
4.而目前,烘干机出口处的物料在进入提升机时,为了减少畚斗对颗粒状饲料成品的挤压损伤,一般采用逆向进料,这就存在物料易落到提升机机座里的现象,致使掉落在机座里的物料与机座处的冷凝水混合,如果清理不及时,往往会造成霉变,这就存在霉变颗粒状饲料混入至合格饲料中的风险,严重造成产品质量问题。
5.此外,提升机皮带轮上沾有冷凝水后,会造成打滑,严重影响提升机的正常运行。
6.现有技术cn202354341u中目的是提供一种结构简单、有效抽出饲料排出膨化机而没有烘干之前的蒸汽,不会出现霉化现象,而且膨化机周围温度,改善操作人员的工作环境的膨化饲料抽蒸汽系统。
技术实现要素:7.本实用新型旨在克服现有技术的不足,提出了一种基于负压吸风的热料除湿系统。在本技术方案中,通过在提升机出料口与分级筛进料口设置本热料除湿系统,能够有效的对热料在提升过程中释放出的湿热风进行收集和处理,从而避免由于冷凝水而引起物料霉变,以及提升机皮带轮打滑失效等问题。
8.为了实现上述技术目的,提出如下的技术方案:
9.一种基于负压吸风的热料除湿系统,设置在提升机与分级筛之间,提升机出料口与分级筛进料口之间通过溜管连接,溜管上设有用于排出湿热风的外溢管,外溢管呈竖直
方向设置,且外溢管设在靠近提升机出料口处和分级筛进料口处,对于提升机出料口与外溢管之间的具体距离,可根据实际需求要求设定;
10.所述热料除湿系统包括设在外溢管管口处的蒸汽收集斗ⅰ和除尘器,蒸汽收集斗ⅰ与除尘器之间通过排湿风网连接,排湿风网上设有风机,风机设在除尘器的工序后侧,蒸汽收集斗ⅰ、排湿风网、除尘器及风机之间形成提升机出料口处湿热风沉降再排出的连续通路;
11.所述分级筛进料口处设有蒸汽收集斗ⅱ,蒸汽收集斗ⅱ通过排湿支管与排湿风网连通,蒸汽收集斗ⅱ、排湿支管、排湿风网、除尘器及风机之间形成分级筛进料口处湿热风沉降再排出的连续通路。
12.进一步的,所述提升机工序前侧设有烘干机,烘干机工序前侧设有膨化机,膨化机工序前侧设有调质器,调质器、膨化机、烘干机及提升机之间形成颗粒状饲料成型、烘干及提升的连续通路;提升机设在分级筛的工序前侧,分级筛工序后侧设有冷却器,提升机、分级筛及冷却器之间形成颗粒状饲料提升、筛分及冷却的连续通路。
13.进一步的,所述排湿风网上设有闸门ⅰ,排湿支管上设有闸门ⅱ,闸门ⅰ和闸门ⅱ用于调节和分配提升机及分级筛两个支路的风量,使之在该两设备内形成微负压,保证湿热风的有效收集。
14.进一步的,所述除尘器上设有关风器,除尘器用于对所收集的湿热风进行沉降,可将其中的粉尘和部分冷凝水分离,并通过关风器排出,进而保证排湿风网工作的稳定性和可控性。
15.进一步的,所述风机为变频风机,可通过改变输出频率来改变吸风量;所述提升机上设有用于检测提升机机筒内的温度和湿度的温湿度传感器,并将信号反馈给变频风机,即温湿度传感器与变频风机之间通过电信号联锁。
16.本技术方案中涉及
ꢀ“
之间”、“上”、“竖直方向”、“靠近”、“处”、“工序前侧”、“工序后侧”等位置关系,是根据实际使用状态下的情况而定义的,为本技术领域内的常规用语,也是本领域术人员在实际使用过程中的常规用语。
17.采用本技术方案,带来的有益技术效果为:
18.一、通过在提升机出料口与分级筛进料口设置本热料除湿系统,能够有效的对热料在提升过程中释放出的湿热风进行收集和处理,从而避免由于冷凝水而引起物料霉变,以及提升机皮带轮打滑失效等问题。
19.二、在本实用新型中,热料除湿系统包括设在外溢管管口处的蒸汽收集斗ⅰ和除尘器,蒸汽收集斗ⅰ与除尘器之间通过排湿风网连接,排湿风网上设有风机,风机设在除尘器的工序后侧,蒸汽收集斗ⅰ、排湿风网、除尘器及风机之间形成提升机出料口处湿热风沉降再排出的连续通路;
20.分级筛进料口处设有蒸汽收集斗ⅱ,蒸汽收集斗ⅱ通过排湿支管与排湿风网连通,蒸汽收集斗ⅱ、排湿支管、排湿风网、除尘器及风机之间形成分级筛进料口处湿热风沉降再排出的连续通路;
21.上述设置,在保证物料顺利、稳定的进入每个工序的同时,实现在线除湿,而不影响其正常工序,且对热料在提升过程中释放出的湿热风进行了有效的收集和处理,即提高颗粒状饲料生产过程中的稳定性。
附图说明
22.图1为本实用新型的工作状态示意图;
23.图2为本实用新型中外溢管处湿热风收集示意图;
24.图3为本实用新型中涉及的颗粒饲料生产系统的逻辑连接框图;
25.图中,1、提升机,2、分级筛,3、溜管,4、外溢管,5、蒸汽收集斗ⅰ,6、除尘器,7、排湿风网,8、风机,9、蒸汽收集斗ⅱ,10、排湿支管,11、烘干机,12、膨化机,13、调质器,14、冷却器,15、闸门ⅰ,16、闸门ⅱ,17、关风器,18、温湿度传感器。
具体实施方式
26.下面通过对本实用新型实施例中的技术方案进行清楚、完整地描述,显然,所描述的实施例仅是本实用新型的一部分实施例,而不是全部的实施例。基于本实用新型中的实施例,本领域普通技术人员在没有做出创造性劳动前提下所获得的所有其它实施例,都属于本实用新型保护的范围。
27.实施例1
28.如图1所示:一种基于负压吸风的热料除湿系统,设置在提升机1与分级筛2之间,提升机1出料口与分级筛2进料口之间通过溜管3连接,溜管3上设有用于排出湿热风的外溢管4(如图2所示),外溢管4呈竖直方向设置,且外溢管4设在靠近提升机1出料口处和分级筛2进料口处,对于提升机1出料口与外溢管4之间的具体距离,可根据实际需求要求设定;
29.所述热料除湿系统包括设在外溢管4管口处的蒸汽收集斗ⅰ5和除尘器6,蒸汽收集斗ⅰ5与除尘器6之间通过排湿风网7连接,排湿风网7上设有风机8,风机8设在除尘器6的工序后侧,蒸汽收集斗ⅰ5、排湿风网7、除尘器6及风机8之间形成提升机1出料口处湿热风沉降再排出的连续通路;
30.所述分级筛2进料口处设有蒸汽收集斗ⅱ9,蒸汽收集斗ⅱ9通过排湿支管10与排湿风网7连通,蒸汽收集斗ⅱ9、排湿支管10、排湿风网7、除尘器6及风机8之间形成分级筛2进料口处湿热风沉降再排出的连续通路。
31.此外,除尘器6上设有关风器17,除尘器6用于对所收集的湿热风进行沉降,可将其中的粉尘和部分冷凝水分离,并通过关风器17排出,进而保证排湿风网7工作的稳定性和可控性。其中,涉及的分级筛2可为回转分级筛2。
32.其中,通过风机8的设置,将提升机1内部及分级筛2内部形成微负压,并对湿热风进行有效的收集,经除尘器6沉降后,再排出。
33.实施例2
34.基于实施例1,本实施例对所涉及的饲料生产系统做进一步限定,以对本技术方案做进一步的说明。
35.如图3所示:在饲料生产系统中:提升机1工序前侧设有烘干机11,烘干机11工序前侧设有膨化机12,膨化机12工序前侧设有调质器13,调质器13、膨化机12、烘干机11及提升机1之间形成颗粒状饲料成型、烘干及提升的连续通路;提升机1设在分级筛2的工序前侧,分级筛2工序后侧设有冷却器14,提升机1、分级筛2及冷却器14之间形成颗粒状饲料提升、筛分及冷却的连续通路。
36.实施例3
37.基于实施例1-2,本实施例对提升机1内的湿热风和将进入分级筛2的湿热风的排出控制做进一步限定,以对本技术方案做进一步的说明。
38.排湿风网7上设有闸门ⅰ15,排湿支管10上设有闸门ⅱ16,闸门ⅰ15和闸门ⅱ16用于调节和分配提升机1及分级筛2两个支路的风量,使之在该两设备内形成微负压,保证湿热风的有效收集。
39.其中,涉及的风机8为变频风机8,可通过改变输出频率来改变吸风量;提升机1上设有用于检测提升机1机筒内的温度和湿度的温湿度传感器18,并将信号反馈给变频风机8,即温湿度传感器18与变频风机8之间通过电信号联锁。
40.涉及的工作过程如下:
41.1、设定温湿度传感器18的温度及湿度参数,并将闸门ⅰ15和闸门ⅱ16均打开;
42.2、当温度和/或湿度超过设定值时,本系统运行,即变频风机8通过改变频率,改变吸风量,并使温度和湿度维持在一定的范围内,实现湿热风的外排,而保证进入分级筛2内物料的干燥,而不产生冷凝水。