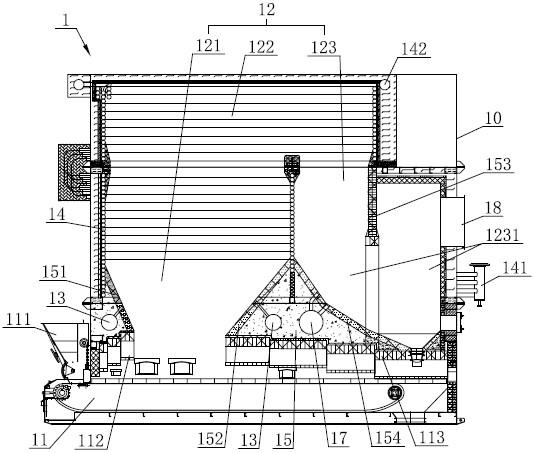
1.本实用新型涉及为石膏粉生产线供热的锅炉设备技术领域,尤其是一种导热油和烟气组合供热的炉排锅炉。
背景技术:2.石膏粉生产线的原料为磷石膏,生产线用热和热回收主要有三大区域,分别是磷石膏的粉碎和烘干、磷石膏粉低温炒制和石膏熟粉冷却,为石膏粉生产线供热的锅炉利用高温烟气烘干磷石膏、利用高温导热油低温炒粉。
3.如图1所示为现有石膏粉生产线供热用的锅炉,其仅采用一台导热油锅炉同时输出高温导热油和高温烟气为生产线供热,导热油锅炉具有辐射受热段122和对流受热段124,对流受热段124通过可上下提升的闸板16分隔成u型通道,出烟口18设置在通道尾端。导热油锅炉底部的链条排炉11烧煤产生的烟气先经过辐射受热段122并与盘管14内的导热油换热,根据烟气经过辐射受热段122尾端时烟气温度是否满足生产线干燥用热需求来控制闸板16的升降,若温度过高,则放下闸板16,全部烟气进入对流受热段124的蛇形管片降温后再从出烟口排出,若温度基本满足需求,则提升闸板16,将部分烟气短路、直接通向出烟口18,部分烟气通过对流换热段125,两者在出烟口汇合排出。但该种锅炉存在以下缺点:(1)导热油供热量和烟气供热量的比例比较难调节,烟气温度不易控制;(2)燃煤产生的烟气易在对流受热段124的蛇形管片上积灰,影响使用;(3)导热油炉通入温度较低环境风至链条排炉11助燃,升温慢、耗煤量高;(4)导热油炉输至生产线中经干燥风净化后的烟气直接通过烟囱排放,没有循环利用烟气及余热,换热效率低,一次性投入人力成本、电耗等运行成本高,经济性差,浪费资源。
技术实现要素:4.本技术人针对上述现有锅炉存在导热油炉不回收利用生产线干燥风净化后的烟气进行调温而是直接排放、能耗高、换热效率低,以及导热油供热量和烟气供热量不易调节、烟气温度不易控制、烟气颗粒易在对流受热段的蛇形管片上积灰、影响使用等缺点,提供一种结构合理的导热油和烟气组合供热的炉排锅炉,不易积灰、导热油供热量和烟气供热量的比例可控,使用上述炉排锅炉的热能中心充分循环使用生产线的烟气、导热油和余温,节约资源和成本的同时提高供热效率。
5.本实用新型所采用的技术方案如下:
6.一种导热油和烟气组合供热的炉排锅炉,其壳体内包括位于底部的炉排和上方的炉膛,炉膛内部沿高温烟气的流向上依次为第一混烟段和辐射受热段,辐射受热段内设置盘管,辐射受热段尾端连接第二混烟段,第二混烟段尾端连接出烟口,至少一根第一进烟管与第一混烟段连接,至少一根第二进烟管与第二混烟段连接。
7.通过在炉排与辐射受热段之间加入第一混烟段,可利用输入低温的烟气与炉排燃煤产生的高温烟气混合降温,减少辐射换热量,避免温度高于换热需求的烟气上升至辐射
受热段内造成热能浪费,且可以延长炉膛内各部件的使用寿命,同时也可作为第二混烟段内烟气调温的前端补充调温,降低能耗,从而较为精准地调节导热油供热量和烟气供热量的比例,以及精准地将烟气温度控制在生产线需要的范围内。
8.作为上述技术方案的进一步改进:
9.第二混烟段为设置在壳体内部的空腔段,第一混烟段和空腔段之间通过挡墙分隔。取消现有技术中的对流受热段而设置空腔段,烟气在空腔段不容易积灰,不会影响换热效率,且烟气颗粒直接输入至生产线中不会影响石膏粉质量。
10.空腔段利用竖直设置的第三挡墙隔成u型通道,空腔段底部为具有折墙段的第四挡墙。
11.空腔段内置在锅炉壳体内并通过第三挡墙分隔,可在充分利用炉膛内部空间的同时延长烟气的流动距离,更好地调节烟气的温度,第四挡墙设置成折墙段,烟气流出辐射受热段后向下流动,并在撞击第四挡墙的折墙段后向上流动,保证烟气能顺利流向出烟口。
12.第一混烟段两侧为具有倾斜面的第一挡墙和第二挡墙,第一挡墙和第二挡墙内分别设有第一进烟管,第一进烟管一端的倾斜管与第一混烟段连通,另一端与壳体对应开设的进烟口连接,从而在壳体与第一混烟段之间形成进烟通道。
13.在第一混烟段设置上宽下窄的导流通道,可以使炉排产生的烟气上升后迅速充斥整个第一混烟段,第一进烟管输入调温烟气并与炉排燃煤产生的烟气混合后进行调温。
14.第四挡墙中设置第二进烟管,其一端通过倾斜管与空腔段连通,另一端与壳体对应开设的进烟口连接,从而在壳体与空腔段之间形成进烟通道。辐射受热段流入烟气在空腔段弯折流动的过程中可以更好地与第二进烟管输入的烟气混合,更好地调节烟气温度。
15.盘管为整体形状与辐射受热段膛体形状相匹配的上宽下窄的框型管。盘管内输入导热油,高温烟气在盘管与壳体围合形成的通道内流动并与导热油进行换热,可增大换热面积,提高换热效率。
16.出烟口开设在空腔段尾端的壳体中央,且位于第二进烟管斜上方。出烟口设置在壳体的中央,保证调温效率的同时可节约壳体的耐高温材料的用量,节约成本,出烟口位于第二进烟管上方,避免第二进烟管和出烟口开设冲突,从而导致第二进烟管输出的烟气直接从出烟口排出,影响控制调温。
17.第二混烟段为设置与壳体连通的混烟管,辐射受热段尾端与混烟管连接,混烟管尾部为出烟口,混烟管与至少一根第二进烟管连接。第二混烟段为外置的混烟管,可在保证混烟长度的同时减少炉排锅炉的体积,灵活适应不同的生产线场地条件,且不容易积灰。
18.盘管为上窄下宽的框型管。盘管在出烟口处留有一段出烟空间,便于烟气从盘管与壳体围合形成的通道流向出烟口。
19.所述第一进烟管与第二进烟管均设置有调节阀。通过温度传感器测得第一混烟段和第二混烟段的温度以便于控制调节回烟量,导热油供热量和烟气供热量的比例可控,烟气温度和导热油温度可控。
附图说明
20.图1为现有锅炉的剖视图;
21.图2为实施例一的炉排锅炉剖视图;
22.图3为实施例一中热能中心系统的pid图;
23.图4为实施例二中热能中心系统的pid图。
24.图中:1、炉排锅炉;10、壳体;11、炉排;111、料斗;112、前拱;113、后拱;12、炉膛;121、第一混烟段;122、辐射受热段;123、第二混烟段;1231、空腔段;1232、混烟管;124、对流受热段;13、第一进烟管;14、盘管;141、导热油入口;142、导热油出口;15、挡墙;151、第一挡墙;152、第二挡墙;153、第三挡墙;154、第四挡墙;16、闸板;17、第二进烟管;18、出烟口;
25.2、生产线设备;21、粉碎烘干设备;22、低温炒粉设备;23、冷却熟粉设备;
26.3、主引风机;4、回流风机;5、一次风机;6、脱硫塔;7、烟囱;8、调节阀。
具体实施方式
27.下面结合附图,说明本实用新型的具体实施方式。
28.实施例一
29.如图2所示,本发明提供一种导热油和烟气组合供热的热能中心的炉排锅炉1,其方形壳体10内包括位于底部的炉排11和设置在炉排11上方的炉膛12,炉膛12内沿高温烟气的流向上依次为第一混烟段121、辐射受热段122和第二混烟段123,第一混烟段121与第二混烟段123之间通过挡墙15分隔。
30.炉排11为链条炉排,其具有设置在壳体10外的料斗111和进风口(图中未示出),炉排11顶部两侧分别设置前拱112和后拱113,便于将炉排11中燃煤产生的热量及烟气压向炉膛12中。炉膛12底部的第一混烟段121两侧设置具有倾斜面的第一挡墙151和第二挡墙152,从而第一混烟段121形成下窄上宽的漏斗形导流通道,炉排11产生的烟气上升后可迅速充斥整个第一混烟段121。至少一根第一进烟管13与第一混烟段121连接,本实施例中在第一挡墙151和第二挡墙152内分别具有两根第一进烟管13,第一进烟管13一端的倾斜管与第一混烟段121连通,另一端与壳体10对应开设的进烟口(图中未示出)连接,从而在壳体10与第一混烟段121之间形成两条进烟通道,第一进烟管13输入的烟气与炉排11产生的高温烟气混合后一起上升进入辐射受热段122,接触炉顶后向右下方折返向第二混烟段123流动。辐射受热段122内设置有无缝盘管14,盘管14整体形状为与辐射受热段122膛体形状相匹配的上宽下窄的框型管,盘管14两端的导热油入口141和导热油出口142均设置在壳体10上,盘管14内输入导热油,高温烟气在盘管14与壳体10围合形成的通道内流动并与导热油进行换热,具备较大的换热面积,有效提高了换热效率。辐射受热段122尾端连通第二混烟段123,本实施例中第二混烟段123为设置在壳体10内的空腔段1231,因为取消了现有技术中的对流受热段124,故烟气在空腔段1231不会产生积灰,且烟气颗粒直接输入至生产线中亦不会影响石膏粉质量。空腔段1231利用竖直设置的第三挡墙153隔成u型通道,可延长烟气流动距离,空腔段1231底部为具有折墙段的第四挡墙154,烟气流出辐射受热段122后向下流动,并在撞击第四挡墙154的折墙段向右上流动,最后由位于空腔段1231的u型通道尾端的出烟口18排出。至少一根第二进烟管17与空腔段1231连接,本实施例中第四挡墙154中设置一根第二进烟管17,其一端分出两根倾斜管与空腔段1231连通,另一端与壳体10对应开设的进烟口(图中未示出)连接,从而在壳体10与空腔段1231之间形成两条进烟通道,第二进烟管17输出的烟气与在辐射受热段122流入的烟气充分混合并进行调温,最后出烟口18从排出符合生产线温度需求的烟气,本实施例中出烟口18设置在壳体10的中央,保证混烟通道长
度及调温效率的同时可节约壳体10的耐高温材料的用量,节约成本,第二进烟管17位于出烟口18下方,避免第二进烟管17和出烟口18开设冲突,从而第二进烟管17输出的烟气直接从出烟口18排出,影响控制调温。
31.如图3所示,热能中心的炉排锅炉1与石膏粉生产线设备2之间形成导热油、烟气及热能的循环回收利用,以节约资源和成本,保护环境,提高换热效率。生产线设备2具有依次串联的粉碎烘干设备21、低温炒粉设备22和冷却熟粉设备23,炉排锅炉1的出烟口18与粉碎烘干设备21连接,生产线设备2的排气口与主引风机3连接,主引风机3分别连接脱硫塔6和回流风机4,回流风机4与炉排锅炉1的第一进烟管13和第二进烟管17通过管道连接,从而形成高温烟气循环供热系统,管道上均具有调节阀8,可以通过温度传感器测得第一混烟段121和空腔段1231内的温度以便于控制调节回烟量,导热油供热量和烟气供热量的比例可控,烟气温度和导热油温度可控。炉排锅炉1的导热油与生产线设备2的低温炒粉设备22之间通过进油管和回油管连接(图中未示出),从而形成高温导热油循环供热系统。生产线设备2的冷却熟粉设备23通过管道连接至一次风机5,管道上具有调节阀8,可调节一次风机5的进风量,一次风机5与炉排11的进风口之间连接,从而形成熟粉余热回收系统。
32.在石膏粉生产用热的工艺中,炉排锅炉1同时为粉碎烘干设备21提供高温烟气、为低温炒粉设备22提供高温导热油。在高温烟气循环供热环节中,高温烟气依次经过粉碎烘干设备21、低温炒粉设备22和冷却熟粉设备23,生产线上的出气口排出的小部分多余高温烟气通过主引风机3引向脱硫塔6,最后经过一系列处理后经烟囱7排放,另外大部分约为110℃的高温烟气通过主引风机3引向回流风机4,再由回流风机4分别回流至炉排锅炉1的第一进烟管13和第二进烟管17进行回收利用。炉排11内燃烧煤释放1200-1300℃的高温烟气,同时第一进烟管13输入110℃左右的回流调温烟气与上述高温烟气混合,使上升至辐射受热段122内的烟气降温至1000℃左右,避免温度高于换热需求的过热烟气上升至辐射受热段122内造成热能浪费,且可以延长炉膛12内各部件的使用寿命,同时也可作为空腔段1231内烟气调温的前端补充调温,降低能耗。烟气与导热油换热后进入空腔段1231并与第二进烟管17输入的回流调温烟气混合降温,经第四挡墙154的折墙段撞击后上升,最终从出烟口18排出后进入粉碎烘干设备21。在高温导热油循环供热环节中,高温烟气通过盘管14管壁与管内导热油换热,导热油升温至250℃左右后从导热油出口142输出至低温炒粉设备22内,低温炒制磷石膏粉,生产线最后排出230℃左右的导热油重新从炉排锅炉1的导热油入口141回流至盘管14内进行加热。在熟粉余热回收环节中,冷却熟粉设备23利用前道产出自带余热的熟粉,利用该部分余热与含氧环境风混合形成预热热风,再由一次风机5输入炉排锅炉1的炉排11内助燃。
33.实施例二
34.如图4所示,本实施例提供一种导热油和烟气组合供热的热能中心的炉排锅炉1,与实施例一不同的是第二混烟段123为设置在壳体10外的混烟管1232。炉排锅炉1的方形壳体10内包括位于底部的炉排11和设置在炉排11上方的炉膛12,炉膛12内部沿高温烟气的流向上依次为第一混烟段121和辐射受热段122,辐射受热段122尾端连接混烟管1232,混烟管1232尾端的出烟口18连接至生产线设备2中的粉碎烘干设备21。炉膛12底部的第一混烟段121两侧为具有倾斜面的第一挡墙151和第二挡墙152,至少一根第一进烟管13与第一混烟段121连接,本实施例中设置为一根第一进烟管13,其开设在第一挡墙151处。辐射受热段
122内具有盘管14,混烟管1232与第二进烟管17连接。
35.实际使用时,粉碎烘干设备21输出的高温烟气一次通过主引风机3和回流风机4回流至第一进烟管13和第二进烟管17,炉排11燃煤产生的高温烟气与第一进烟管13输出的烟气在第一混烟段121混合降温,并上升至辐射受热段122与盘管14内的导热油换热,再由辐射受热段122尾端输送至混烟管1232内并与第二进烟管17输出的烟气混合调温,最终输出符合生产线温度需求的高温烟气至粉碎烘干设备21内。
36.以上描述是对本发明的解释,不是对本发明的限定,在不违背本发明精神的情况下,本发明可以作任何形式的修改。例如将热能中心使用于其他的需要热源的生产线设备中。