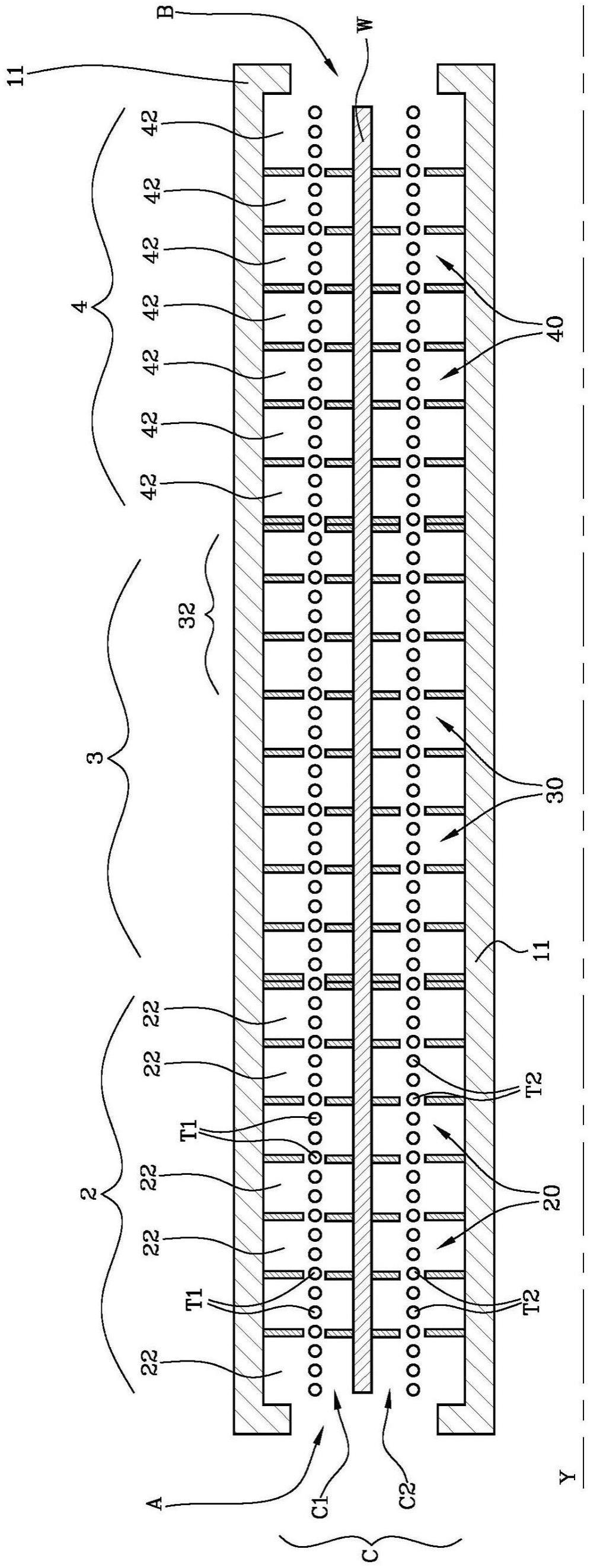
用于烧制陶瓷板的窑
1.本发明涉及一种用于烧制陶瓷板的窑
。
2.在陶瓷砖或陶瓷板的生产过程中,每个生产线都配置为一次仅能够生产一种产品
。
在实践中,每种产品都具有其自身的特性,尤其是在为了获得最终产品所必需的热处理方面
。
根据不同的特征
(
诸如所使用的混合物
、
规格
、
上釉类型和最终装饰
)
,每种类型的产品通常都需要不同的干燥时间和烧制时间
。
3.陶瓷产品生产线上的一些机器
(
例如数码打印机
)
可以快速地改变其配置
。
而另一方面,执行生产过程的最长阶段且在结构上最重要的机器
(
即,窑
)
具有相当大的配置刚性,其需要相对较长的调节时间和设置时间
。
4.通常,用于陶瓷板的窑包括以下四个区域
。
5.第一区域,也称为“预窑”,材料在该第一区域中被加热到约
250℃
至约
300℃
之间的温度
。
在该第一区域中,引入材料并通过逐步加热来制备,使得材料完全干燥,以消除来自前面步骤
(
诸如上釉和
/
或储存
)
的残余湿气
。
这是为了避免在烧制期间材料破裂和爆裂,这是因为在第一区域的初始区域中已经出现的高温会使得水急剧蒸发
。
尽管预窑是与窑分离的功能单元,但是预窑与窑的共同之处是都具有辊平面,该辊平面将材料从预窑区域连续地输送到实际窑
。
6.第二区域,也称为“预热”区域,材料在该第二区域中从约
300℃
被加热到约
500℃。
在该区域中,材料内部发生一些重要变化过程,诸如水
(
吸湿性和沸石性
)
完全消除
、
部分所施加的挥发性有机物质蒸发和
/
或分解以及包含在混合物中的有机物质燃烧
。
该区域对于引入窑中的工件的完整性是特别重要的,因为如果这些工件没有被适当干燥,则可能会导致蒸发过快,从而导致工件本身“爆裂”。
待加工的工件厚度越大,这种现象就越严重
。
7.在该区域中,温度相对较低并且该温度是从随后的加热区域
/
烧制区域的烟气中获得的,热交换主要通过烟气与材料本身之间的对流进行
。
烟气的速度越快,这种热交换就越有效
。
另一方面,随着烟气的速度增加,在烟囱的出口处出现高温烟气,从而降低了窑的热效率
。
8.第三区域,也称为加热区域,材料在该第三区域中从约
500℃
被进一步加热到约
1000℃。
9.在该温度范围内会发生几种现象,诸如有机物质燃烧
、
石英转变
、
成分水释放
、
碳酸盐分解以及硫化铁
(
如果混合物中存在的话
)
转变
。
应当注意的是,正是在这个温度区域中才有可能产生所谓的“黑心”。
10.对流特点在这一步骤中也起到重要的作用,尤其是在加热的初始阶段,因为对流特点有利于上面描述的化学现象
/
物理现象
。
具体地,对流型的热交换促使材料整个厚度内的温度均匀性更好,即减小了在材料的厚度方向上的热梯度
。
11.第四区域是温度超过
1000℃
的实际烧制步骤
。
在该区域中,材料被烧结,从而使尺寸发生变化
。
该区域需要最大的灵活性以避免平整度缺陷
、
校准缺陷和色调缺陷或者至少使平整度缺陷
、
校准缺陷和色调缺陷最小化
。
根据所使用的混合物的特征玻璃化曲线,在窑的该区段中发生的化学转变
/
物理转变的总体效果是收缩,即体积减小
。
烧制的尾部由存在
的隔板来限定,该隔板将烧制区域的最后模块与第一快速冷却模块隔开
。
该隔板的存在旨在防止热气体通过冷却区域,反之亦然,即防止冷气体通过烧制区域
。
在烧制步骤的下游设置有第五区域,也称为冷却区域,在该第五区域内,材料的温度以受控的方式逐渐降低
。
12.冷却区域被依次划分成以下区域:
13.a.
快速冷却区域,材料在该快速冷却区域中相对快速地冷却到约
650℃
;
14.b.
间接冷却区域,材料在该间接冷却区域中从约
650℃
冷却到约
300℃
;在该区域中,冷却必须足够平缓,使得石英转变过程不会引起材料破裂;
15.c.
最终冷却区域,材料在该最终冷却区域中相对快速地冷却到足够低以使其可操纵的温度
。
16.上面描述的所有步骤都是材料在单个输送平面上通过时进行的,如上面所提及的,该单个输送平面由电动辊限定
。
应当注意的是,窑可以包括一个或最多两个独立的通道,每个通道都具有其自己的辊输送平面
。
17.窑内所产生的所有热能主要通过燃烧器来获得,燃烧器布置在辊平面上方和
/
或下方并且沿着窑适当地分布
。
18.根据所需的生产力和待烧制的板的规格,需要正确地确定窑的尺寸,以确保烧制和冷却的均匀性
。
由于所生产的板的尺寸和厚度增加,烧制时间增加,因此所使用的窑的长度增加
。
一般而言,当前窑的长度不小于
150m
,通常在
180m
至
200m
之间或更大
。
因此,窑是具有相当大尺寸的结构,其需要非常庞大的整体布局和同样大的建筑物
。
19.当前窑的特征使得无法有效地管理生产变化,特别是无法以具有成本效益的方式管理不同产品的同时生产
。
换句话说,到目前为止,生产的变化需要设定新的烧制参数并且重新启动窑,以用于适应的过渡期
。
因此,在开始新生产之前需要相当长的时间,这大大降低了生产工厂的利润率
。
20.本发明的目的是提供一种能够提高生产循环灵活性的窑
。
21.根据本发明的窑的一个优点是可以有效地且经济地管理具有不同规格和特征的板的生产
。
22.根据本发明的窑的另一优点是可以提高当前生产线的生产力
。
23.通过在附图中以非限制性实例的方式示出的本发明的实施方式的以下详细描述,本发明的其他特征和优点将变得更加显而易见,在附图中:
[0024]-图1示出了根据本发明的窑在平行于纵向前进方向
(y)
的竖直平面上的示意性截面图;
[0025]-图2示出了根据本发明的窑的第二实施方式的示意图,该图在平行于纵向前进方向
(y)
的竖直平面上截取
。
[0026]
根据本发明的用于烧制陶瓷板
(l)
的窑包括加热模块
(2)、
烧制模块
(3)、
冷却模块
(4)
,这三个模块沿着板
(l)
的前进方向
(y)
彼此相继地连接
。
[0027]
这三个模块
(2
,3,
4)
一起限定设置有入口开口
(a)
和出口开口
(b)
的加工室
(c)。
加工室
(c)
整体上由壳体
(11)
界定
。
所述壳体
(11)
包含隔热材料
。
入口开口
(a)
和出口开口
(b)
位于壳体
(11)
上
。
[0028]
输送系统
(t1
,
t2)
沿着加工室
(c)
从入口开口布置到出口开口
。
输送系统
(t1
,
t2)
构造成沿着前进方向
(y)
输送板
(l)。
实质上,借助于输送系统
(t1
,
t2)
,板
(l)
旨在沿着加工
室
(c)
被运送穿过每个模块
(2
,3,
4)
,首先是加热模块
(2)、
然后是烧制模块
(3)、
最后是冷却模块
(4)。
[0029]
加热模块
(2)
设置成将板
(l)
从环境温度,或者在板
(l)
经受初始加热或干燥的情况下
(
在任何情况下都不是必需的
)
,从高于环境温度的温度
(
在约
100℃
至
250℃
之间
)
开始加热到约
700℃
的温度
。
在实践中,加热模块
(2)
可以执行板
(l)
的干燥步骤,在这种情况下,板
(l)
从环境温度开始进入加热模块
(2)。
在干燥步骤由加热模块
(2)
外的外部执行的情况下,板
(l)
将在约
100℃
至
250℃
之间的温度下进入加热模块
(2)。
加热模块
(2)
基本上包括由支撑框架支撑的容纳壳体,该容纳壳体在内部包围与外部环境隔离的加热室
(20)。
加热模块包括:至少一个入口开口,板
(l)
可以穿过该至少一个入口开口被引入到加热室
(20)
中;以及至少一个出口开口,板
(l)
可以穿过该至少一个出口开口从加热室
(20)
中取出
。
本领域中已知的加热装置设置成将热量引入到加热室
(20)
中,以便根据预定的时间趋势使板
(l)
逐渐加热
。
这种加热装置还可以包括热回收回路,该热回收回路配置为将从板
(l)
转移到冷却模块
(4)
中的至少一部分热量和
/
或由烧制模块
(3)
散发的至少一部分热量传送到加热模块
(2)。
[0030]
与传统烧制窑的预窑区域和预热区域中相同的步骤
(
包括传统窑的加热步骤的第一次转变
)
也在加热模块
(2)
内发生
。
[0031]
例如,在加热模块
(2)
内,形成板
(l)
的材料会发生一些重要转变,其中包括成分水消除
(500℃
至
600℃)、
石英从
α
转变到
β
同时体积增加
(573℃)、
有机物质燃烧
(350℃
至
650℃)。
有机物质燃烧是非常重要的,并且必须使其可以完全完成,从而为有机物质燃烧所产生的气体从板
(l)
逸出留出必要的时间
。
[0032]
板
(l)
的加热过程必须以受控的方式
(
即温度随预定的时间趋势而升高
)
进行
。
在材料质量相同的情况下,该时间趋势基本上由加热模块
(2)
内的温度以及板
(l)
穿过加热模块
(2)
的速度来限定
。
优选地,加热模块
(2)
内的温度是不均匀的,而是温度从入口到出口逐渐升高
。
加热模块
(2)
内的温度
(
尽管是分布式的
)
与板
(l)
的前进速度之间的组合基本上限定了板
(l)
的温度随时间的升高,包括板本身的厚度内的温度梯度
。
该趋势在下文中将称为加热曲线
。
[0033]
在优选的实施方式中,加热模块
(2)
包括沿着板
(l)
的前进方向位于彼此侧面的多个子模块
(22)。
具体地,每个子模块
(22)
在内部界定加热室
(20)
的一部分
。
[0034]
每个子模块
(22)
都可以通过隔热板与相邻的子模块隔开,隔热板设置有多个开口,这些开口沿着前进方向彼此对准,以允许运送板
(l)。
换句话说,除了运送板
(l)
所穿过的开口之外,这些子模块
(22)
可以彼此隔开
。
每个子模块
(22)
包括其自己的加热装置,这些加热装置可以独立于其他子模块
(22)
的加热装置进行控制,以允许调节每个子模块
(22)
的温度
。
在该实施方式中,通过调节每个子模块
(22)
内的温度,可以准确地控制板
(l)
沿着前进方向的加热曲线
。
实质上,在每个子模块
(22)
内都实现了一定的温度升高
。
总体上,子模块
(22)
的顺序限定了板
(l)
的从在加热模块
(2)
的入口处时的温度到在出口处时的温度的加热时间曲线,该加热时间曲线也与前进速度有关
。
[0035]
在实践中,为了获得给定的板
(l)
的加热曲线,可以限定子模块
(22)
的最少数量,作为从加热模块
(2)
的入口到出口的整体加热的一部分,每个子模块都负责实现一定的温度跃升
。
[0036]
加热模块
(2)
包括一定数量的子模块
(22)
的优点是能够为每个子模块
(22)
配备其自己的独立于其他子模块
(22)
的空气再循环系统
。
这种空气再循环
(
在传统窑中是不可能的
)
使得可以产生最佳的空气流,以用于通过从来自烧制模块
(3)
和
/
或来自冷却模块
(4)
的热烟气到板
(l)
的对流来进行热传递
。
空气体积在子模块
(22)
内的再循环通过本领域中已知的装置
(
例如风扇
)
来进行
。
[0037]
烧制模块
(3)
设置成将板
(l)
从在加热模块
(2)
的出口处时的温度加热到约
1230℃
的温度
。
[0038]
在烧制模块
(3)
中,完成了在烧制模块
(3)
之前就在加热模块
(2)
中开始的石英的转变过程和有机物质的燃烧过程
。
随后,在烧制模块
(3)
中,实际烧制步骤在超过
1000℃
的温度下进行
。
在该区域中,根据所使用的混合物的特征玻璃化曲线,发生材料的烧结,即发生其整体效果是收缩
(
即体积减小
)
的化学转变
/
物理转变
。
[0039]
烧制模块
(3)
还设置成执行板
(l)
的快速冷却,从板
(l)
所达到的约
1230℃
的最高温度到约
700℃。
在实践中,考虑到板
(l)
的前进方向,在烧制模块
(3)
内,从在加热模块
(2)
的出口处时的温度加热到约
1230℃
,并且在将温度保持在
1230℃
一段必要的时间后,相对快速地冷却到约
700℃。
[0040]
烧制模块
(3)
基本上包括由支撑框架支撑的容纳壳体,该容纳壳体在内部包围与外部环境隔离的烧制室
(30)。
烧制模块
(3)
包括:至少一个入口开口,板
(l)
可以穿过该至少一个入口开口被引入到烧制室中;以及至少一个出口开口,板
(l)
可以穿过该至少一个出口开口从烧制室中取出
。
本领域中已知的加热装置设置成将热量引入到烧制室
(30)
中,以便根据预定的时间趋势使板
(l)
逐渐加热
。
这种加热装置包括本领域中已知的多个气体燃烧器,这些气体燃烧器相对于烧制室以预定的方式分布
。
对每千克板
(l)
的材料来说,被引入到烧制室中的热量是相当大的,约为
450kcal/kg。
因此,烧制室的容纳壳体通过本领域中已知的解决方案与外部环境良好地隔热
。
[0041]
烧制模块
(3)
的实现板
(l)
的快速冷却的区域位于出口侧,并且包括烧制模块
(3)
的出口本身
。
在可能的实施方式中,快速冷却区域
(32)
基本上没有加热装置
。
在快速冷却区域
(32)
内,存在本领域中已知的适于将相对较冷的空气传送到待冷却的板上的装置
。
优选地,快速冷却区域
(32)
通过一个或多个隔热板与烧制模块
(3)
的其余部分隔开,隔热板设置有多个开口,以允许运送板
(l)。
这些开口沿着板
(l)
的前进方向彼此对准
。
有利地,从板
(l)
转移到快速冷却区域
(32)
内的一部分热量被传送到加热模块
(2)
内
。
[0042]
冷却模块
(4)
设置成将板
(l)
从在烧制模块
(3)
的出口处时的温度冷却到环境温度,或者冷却到低于
150℃
或
100℃
的温度
。
[0043]
冷却模块
(4)
基本上包括由支撑框架支撑的容纳壳体,该容纳壳体在内部包围与外部环境隔离的冷却室
(40)。
冷却模块
(4)
包括:至少一个入口开口,板
(l)
可以穿过该至少一个入口开口被引入到冷却室
(40)
中;以及至少一个出口开口,板
(l)
可以穿过该至少一个出口开口从冷却室
(40)
中取出
。
[0044]
本领域中已知的冷却装置设置成从冷却室
(40)
中吸取热量,以便根据预定的时间趋势使板
(l)
逐渐且受控地冷却
。
这种冷却装置可以包括上面已经提及的热回收回路,该热回收回路配置为将从板
(l)
转移到冷却模块
(4)
中的至少一部分热量和
/
或由烧制模块
(3)
散发的至少一部分热量传送到加热模块
(2)。
[0045]
在该冷却模块内,在形成板
(l)
的材料中发生一些重要转变,其中包括在约
650℃
至约
300℃
之间的冷却中发生的石英的转变
。
这种冷却必须足够平缓,使得石英转变过程不会像传统窑中的冷却模块那样使得材料破裂
。
[0046]
板
(l)
的冷却过程还必须以受控的方式
(
即温度随预定的时间趋势而降低
)
进行
。
在材料质量相同的情况下,该时间趋势基本上由冷却模块
(4)
内的温度以及板
(l)
穿过冷却模块
(4)
的速度来限定
。
优选地,冷却模块
(4)
内的温度是不均匀的,而是从入口到出口逐渐降低
。
冷却模块
(4)
内的温度
(
尽管是分布式的
)
与板
(l)
的前进速度之间的组合基本上限定了板
(l)
的温度随时间的降低
。
该趋势在下文中将称为冷却曲线
。
[0047]
在优选的实施方式中,冷却模块
(4)
包括沿着板
(l)
的前进方向位于彼此侧面的多个子模块
(42)。
具体地,每个子模块
(42)
在内部界定冷却室
(40)
的一部分
。
[0048]
在优选配置中,每个子模块
(42)
都可以通过隔热板与相邻的子模块隔开,隔热板设置有多个开口,这些开口沿着前进方向彼此对准,以允许运送板
(l)。
换句话说,除了运送板
(l)
所穿过的开口之外,这些子模块
(42)
彼此隔开
。
每个子模块
(42)
包括其自己的冷却装置,这些冷却装置可以独立于其他子模块
(42)
的冷却装置进行控制,以允许调节每个子模块
(42)
的温度
。
在该实施方式中,通过调节每个子模块
(42)
内的温度,可以准确地控制板
(l)
沿着前进方向的冷却曲线
。
实质上,在每个子模块
(42)
内都实现了一定的温度降低
。
总体上,子模块
(42)
的顺序限定了板
(l)
的从冷却模块
(4)
的入口处的温度到出口处的温度的冷却时间曲线,该冷却时间曲线也与前进速度有关
。
[0049]
在实践中,为了获得给定的板
(l)
的冷却曲线,可以限定子模块
(42)
的最少数量,作为从冷却模块
(4)
的入口到出口的整体冷却的一部分,每个子模块
(42)
都负责实现一定的温度降低
。
[0050]
有利地,加工室
(c)
包括彼此热隔离的至少一个第一通道
(c1)
和至少一个第二通道
(c2)。
这两个通道
(c1
,
c2)
中的每个通道都沿着前进方向
(y)
从入口开口
(a)
延伸到出口开口
(b)。
[0051]
换句话说,加工室
(c)
被分隔成彼此热隔离的至少两个部分,这两个部分由第一通道
(c1)
和第二通道
(c2)
限定
。
然后,每个通道
(c1
,
c2)
都布置成穿过加热模块
、
烧制模块和冷却模块
(2
,3,
4)
这三个模块,即这三个模块
(2
,3,
4)
中的每个模块进而被分隔成由第一通道
(c1)
限定的第一部分和由第二通道
(c2)
限定的第二部分
。
[0052]
输送系统
(t1
,
t2)
包括至少一个第一线
(t1)
和至少一个第二线
(t2)
,它们分别沿着第一通道
(c1)
和第二通道
(c2)
从入口开口
(a)
布置到出口开口
(b)。
[0053]
第一通道
(c1)
和第二通道
(c2)
包括可以彼此独立地激活和调节的各自的温度调节器
。
实质上,第一通道
(c1)
的温度调节器设置成调节第一通道
(c1)
内的温度
。
类似地,第二通道
(c2)
的温度调节器设置成调节第二通道
(c2)
内的温度
。
[0054]
在实践中,每个通道
(c1
,
c2)
的温度调节器都能够针对加热模块
(2)、
烧制模块
(3)
和冷却模块
(4)
的每个部分独立地控制和调节每个部分的温度
。
[0055]
与现有技术相比,设置至少包括第一通道
(c1)
和第二通道
(c2)
的加工室
(c)
提供了非常显著的优点
。
[0056]
每个通道
(c1
,
c2)
由于其与其他通道热隔离并且可以独立于其他通道进行温度控制而能够相对于其他通道加工具有不同特征的板
(l)。
具体地,每个通道
(c1
,
c2)
都可以执
行其自己的与由其他通道执行的烧制循环不同的烧制循环
。
因此,该窑能够同时加工至少两种类型的板
(l)
,每种类型的板都具有其自身的烧制循环
。
通过增加通道的数量,显然也增加了可以同时加工的板
(l)
的类型的数量
。
[0057]
此外,多个通道
(c1
,
c2)
中的至少一个通道可以执行连续且较长的烧制循环,例如用于烧制包括大量板
(l)
的批次
。
另一个通道可以用于生产包括较少数量板
(l)
的较小批次,并且经受更频繁的重新配置
。
[0058]
加工室
(c)
至少包括彼此隔离的第一通道
(c1)
和第二通道
(c2)
的另一个优点是除了能够控制温度之外,还能够控制每个通道内产生的压力,从而能够调整待烧制的板
(l)
的类型
。
[0059]
优选地,多个通道
(c1
,
c2)
在竖直方向上彼此叠置
。
这允许在高度上占据空间,即以一种更实用的方式在生产工厂内占据空间
。
[0060]
多个通道
(c1
,
c2)
之间的热隔离可以通过介于多个通道
(c1
,
c2)
之间的隔热分离壁
(w)
来实现
。
隔热壁
(w)
基本上水平地且平行于输送方向
(y)
布置
。
对于隔热壁
(w)
的配置而言,本领域技术人员可以获得多种材料和多种结构
。
[0061]
如已经指出的,输送系统
(t1
,
t2)
包括至少一个第一线
(t1)
和至少一个第二线
(t2)
,它们分别沿着第一通道
(c1)
和第二通道
(c2)
从入口开口
(a)
布置到出口开口
(b)。
有利地,第一线和第二线
(t1
,
t2)
可以彼此独立地操作,以允许板
(l)
沿着第一通道
(c1)
和第二通道
(c2)
以不同的速度输送
。
这是特别重要的,因为这允许根据所需的烧制循环来调节每个通道
(c1
,
c2)
内的速度
。
[0062]
每个线
(t1
,
t2)
都包括基本上水平布置的至少一个可移动平面
。
每个线
(t1
,
t2)
都设置有本领域中已知的马达装置,该马达装置设置成使板
(l)
沿着前进方向
(y)
从相应通道
(c1
,
c2)
的入口朝向出口移动
。
[0063]
在优选的实施方式中,本领域中已知的板
(l)
的可移动支撑平面各自包括彼此共面的多个辊,这些辊的旋转轴线布置成位于水平平面上
。
每个线
(t1
,
t2)
的马达装置都设置成使形成相应的可移动平面的至少一部分辊或全部辊旋转
。
这些辊优选地由耐火材料制成,或者在任何情况下都能耐受烧制模块
(3)
中的高温
。
[0064]
在图1中示出的实施方式中,每个线
(t1
,
t2)
都包括单个的可移动平面
。
在可能的实施方式
(
未示出
)
中,每个线
(t1
,
t2)
都包括彼此叠置的且基本上水平的两个或更多个可移动平面
。
每个可移动平面都可以设置有可以独立于其他可移动平面操作的马达装置
。
[0065]
在图2中示出的实施方式中,加工室
(c)
包括五个通道
(c1
,
c2
,
c3
,
c4
,
c5)
,它们通过多个隔热壁
(w)
彼此热隔离
。
具体地,这些隔热壁
(w)
中的一个隔热壁介于两个相邻的通道之间
。
每个通道
(c1
,
c2
,
c3
,
c4
,
c5)
都设置有相应的线
(t1
,
t2
,
t3
,
t4
,
t5)
,这些线都设置有可以独立于其他线操作的马达装置
。
同样在图2的实施方式中,通道
(c1
,
c2)
优选地在竖直方向上彼此叠置
。
这允许在高度上占据空间,即以一种更实用的方式在生产工厂内占据空间
。
设置五个通道
(c1
,
c2
,
c3
,
c4
,
c5)
允许窑的生产力相应地倍增
。
每个通道可以专用于加工与其他通道不同的产品,从而实现与其他通道不同的烧制循环
。
显然,根据具体的生产需求,两个或更多个通道可以专用于相同产品并实现相同的烧制循环
。