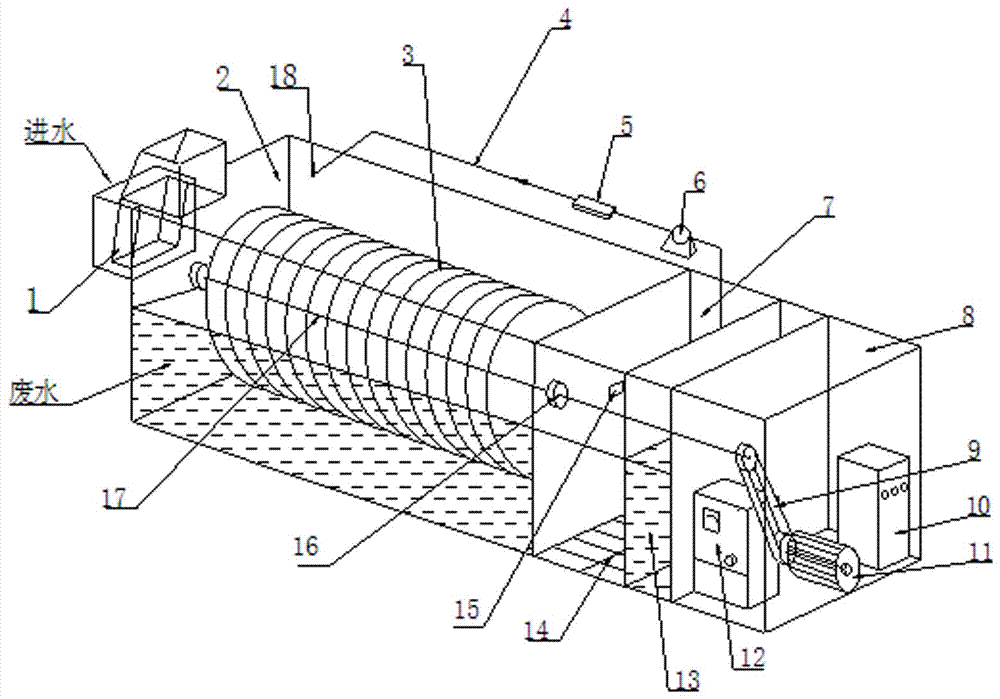
本发明属于水处理
技术领域:
,特别涉及一种畜禽养殖废水前处理全好氧脱氮工艺及一体化设备。
背景技术:
:当前,废水污染尤其是畜禽养殖废水污染,已经成为农业面源污染的主要来源。其中,畜禽养殖废水属于悬浮物、有机污染物和氨氮“三高”的有机废水,由于对其处理成本高,处理难度大,大量未经处理的养殖废水常常直接排放,对农村生态和环境造成严重破坏。如何高效处理这类废水,已成为制约畜禽规模化养殖业的发展瓶颈。对于规模化养殖场废水,目前国内外采用的成熟处理工艺主要是厌氧-好氧联合或厌氧-自然处理联合工艺,养殖废水经过厌氧发酵处理后,虽然大部分cod(有机物)被去除,但氨氮只是形态发生变化,浓度仍然很高,造成了低碳高氨氮沼液的产生,导致c/n比严重失调,脱氮效果差。生物膜好氧工艺发展已经成熟,但传统生物膜工艺的挂膜时间需要20-25天,其在处理沼液时由于微生物耐高氨氮性能差、碳源不足而导致后续工艺流程复杂、处理成本高和脱氮效果差等实际问题。为了优化沼液的c/n比,目前采用的方法主要有:利用氨吹脱法、磷酸铵镁结晶法等物化方法大幅度降低沼液中氨氮;或者用添加原水或补加碳源调整碳氮比;或者用臭氧氧化和微电解等方法提高沼液中有机物可生化性等。这些方法一定程度提高了沼液的可生化性和脱氮效果,但是往往以提高单位废水处理能耗和成本为代价,对于日均产废水几百吨的规模化养殖场来说,运行成本太高,无力承担,致使目前畜禽养殖场废水处理长期存在难以有效解决的问题。技术实现要素:本发明的目的之一是提供一种畜禽养殖废水前处理全好氧脱氮工艺,采用本发明所述工艺,通过全好氧脱氮的方式,采用耐高cod,耐高氨氮,耐低温、高脱氮效率的异养硝化-好氧反硝化功能菌进行菌液挂膜,完成一体化设备的启动,缩短设备启动周期,为功能菌的富集创造条件。本发明所述方法,从养殖废水的源头对废水原水中的主要污染物进行前处理,经处理后的畜禽养殖废水,其水质可以满足后续常规水处理工艺的进水水质要求(cod<2000mg/l,nh4+-n<200mg/l)。本发明的技术方案是:畜禽养殖废水前处理全好氧脱氮工艺,该工艺步骤如下:1)菌剂接种生长-吸附挂膜将废水原水经固液分离除去悬浮物后注入全好氧反应区中,通过控制进水的流量,使好氧反应区的水力停留时间控制在12~24h的范围,在全好氧反应区的废水原水中加入全好氧脱氮菌剂和液态富集培养基形成混合液,全好氧脱氮菌剂和液态富集培养基的加入总量为水的4~10%重量百分比,其中,全好氧脱氮菌剂体积:液态培养基质体积为3~8:100,使全好氧反应区的溶解氧浓度保持在0.5~1.5mg/l,每24小时测一次混合液的od值,当od值达到1.05~1.22并开始下降时,则全好氧脱氮菌剂在全好氧反应区设置的用于固定全好氧脱氮菌的载体吸附挂膜接种完成;所述全好氧脱氮菌剂为苍白杆菌或可低温去除高氨氮的异养硝化-好氧反硝化复合菌剂;2)挂膜成熟当测得混合溶液的od值为0.20~0.25,用于固定全好氧脱氮菌的载体上的生物膜变厚,颜色加深,则全好氧脱氮菌在用于固定全好氧脱氮菌的载体上挂膜成熟;将步骤1)所述混合液排出;3)稳定运行阶段向全好氧反应区中连续注入新的经固液分离除去悬浮物后的废水原水,通过控制进水的流量,使好氧反应区的水力停留时间控制在12~24h的范围,同时维持溶解氧浓度在1.5~3mg/l,每24h测一次出水的有机物和氨氮浓度,待全好氧反应区的连续出水中有机物和氨氮浓度出现明显降低,连续三天测得出水中的氨氮浓度误差在5%以内,则脱氮处理稳定运行;4)臭氧反应处理当测得全好氧反应区的废水出水中有机氮含量>100mg/l时,启动臭氧发生器,让进入臭氧反应区的废水进行氧化处理,臭氧按2~8mg/l投入臭氧反应区,臭氧与废水的反应时间为20~60min,并使氧化处理后的废水部分回流到全好氧反应区加入全好氧反应区的废水中,再次按照步骤3)所述方法进行脱氮处理,氧化处理后的废水回流全好氧反应区的回流比为50%~200%;当测得全好氧反应区的废水出水中有机氮含量<100mg/l时,则不启动臭氧发生器,让废水出水直接进入储存区;5)前处理结束测得储存区中废水出水中有机物浓度为300~1500mg/l,氨氮浓度为130~200mg/l,其中cod的削减率为60~70%,氨氮的削减率为70~80%,有机氮的削减率为70~75%,总氮的削减率为80~90%,经前处理的废水从储存区流出进行后序处理。步骤1)所述富集培养基的组分为:硫酸铵2.67g~4.44g/l(氨氮600~1000mg/l),碳源3.55~11.8g/l(cod3000~10000mg/l),维氏盐溶液30~60ml/l,调节ph值至7.0~7.5,100~121℃高压蒸汽灭菌10~30min。所述维氏盐溶液g/l的组分为:k2hpo43.0~6.0,mgso47h2o1~3,nacl2~4,feso47h2o0.01~0.09,mnso44h2o0.01~0.09。步骤1)所述富集培养基的碳氮比为5-25。步骤1)所述富集培养基的碳源为琥珀酸钠、柠檬酸钠、乙酸钠、葡萄糖、蔗糖、淀粉、聚己内酯、聚丁二酸丁二醇酯等碳源中的一种或几种的组合。当采用乙酸钠和柠檬酸钠的组合作为碳源,则乙酸钠:柠檬酸钠的重量比为1~2:4~5;当采用葡萄糖和淀粉的组合作为碳源,则葡萄糖:淀粉的重量比为1~2:6~8;当采用淀粉和柠檬酸钠的组合作为碳源,则淀粉:柠檬酸钠的重量比为2~3:4~5;当采用琥珀酸钠和柠檬酸钠的组合作为碳源,则琥珀酸钠:柠檬酸钠的重量比为1~3:1;当采用淀粉和聚己内酯的组合作为碳源,则淀粉:聚己内酯的重量比为3~4:6~7。步骤3)所述连续出水中有机物和氨氮浓度出现明显降低是cod<350mg/l,nh4+-n<150mg/l。畜禽养殖废水前处理全好氧脱氮一体化设备,废水前处理全好氧脱氮设备包括全好氧反应区、臭氧反应区、储存区和设备控制区;所述全好氧反应区的进水端设有机械格栅,全好氧反应区设有排水阀和在出水端设有溢流口与臭氧反应区连通,所述全好氧反应区中设有用于固定全好氧脱氮菌的载体,所述臭氧反应区的出水端设有溢流口与储存区连通,所述臭氧反应区与全好氧反应区还通过设有回流泵和流量计的回流管道相连,所述储存区设有溢流口与后序处理装置相连;所述设备区内设有电器控制柜、臭氧发生器,所述臭氧发生器与臭氧反应区内设置的臭氧矩阵通过输送管连接,所述臭氧发生器、回流泵、机械格栅的工作由电器控制柜控制。所述全好氧反应区为生物反应池,生物反应池中设置的用于固定全好氧脱氮菌的载体为生物转盘或生物转笼,所述生物转盘或生物转笼转速由设备区中电器控制柜控制的电动机驱动;所述生物转盘或生物转笼圆周边缘的线速度控制在1~3m/min,或者7.5~15m/min。所述全好氧生物反应区为接触氧化池,或者生物流化床,或者生物滴滤塔,或者曝气生物滤池;接触氧化池或生物流化床或生物滴滤塔或曝气生物滤池中均设有用于固定全好氧脱氮菌的载体,优选地,所述用于固定全好氧脱氮菌的载体为悬挂式填料,或者悬浮填料,或者填充填料。富集培养基的最适碳氮比范围为5-25。本发明所述菌剂为苍白杆菌,参见专利申请号为201810209286.2权利要求1和说明书第0010段;可低温去除高氨氮的异养硝化-好氧反硝化复合菌剂(下称复合菌剂)参见201810209983.8权利要求1-4和说明书第0007-0010段。苍白杆菌和复合菌剂均耐高氨氮(nh4+-n>800mg/l)、耐低温(<5℃)并且脱氮效率高(nh4+-n>90%,tn>90%),采用苍白杆菌或复合菌剂接种挂膜,一方面可将挂膜启动的时间缩短到12-18天,另一方面可快速适应养殖废水中高浓度环境,有利于功能菌的繁殖和富集。本发明的另一目的是提供一种畜禽养殖废水前处理全好氧脱氮一体化设备。通过一体化设备的结构及运行条件优化,实现接种功能菌的优势化构建,充分发挥功能菌所具有的各种优良性能。本发明的目的是这样实现的:一种畜禽养殖废水前处理全好氧脱氮一体化设备,废水前处理全好氧脱氮设备包括全好氧反应区、臭氧反应区、储存区和设备控制区;所述全好氧反应区的进水端设有机械格栅,全好氧反应区设有排水阀和在出水端设有溢流口与臭氧反应区连通,所述全好氧反应区中设有用于固定全好氧脱氮菌的载体,所述臭氧反应区的出水端设有溢流口与储存区连通,所述臭氧反应区与全好氧反应区还通过设有回流泵和流量计的回流管道相连,所述储存区设有溢流口与后序处理装置相连;所述设备区内设有电器控制柜、臭氧发生器,所述臭氧发生器与臭氧反应区内设置的臭氧矩阵通过输送管连接,所述臭氧发生器、回流泵、机械格栅的工作由电器控制柜控制。所述全好氧反应区为生物反应池,生物反应池中设置的用于固定全好氧脱氮菌的载体为生物转盘或生物转笼,所述生物转盘或生物转笼转速由设备区中电器控制柜控制的电动机驱动;所述生物转盘或生物转笼圆周边缘的线速度控制在1~3m/min,或者7.5~15m/min。所述全好氧生物反应区为接触氧化池,或者生物流化床,或者生物滴滤塔,或者曝气生物滤池;接触氧化池或生物流化床或生物滴滤塔或曝气生物滤池中均设有用于固定全好氧脱氮菌的载体。所述用于固定全好氧脱氮菌的载体为悬挂式填料,或者悬浮填料,或者填充填料。与现有技术相比,本发明具有如下显著优点:(1)本发明由于采用菌剂挂膜的方式进行一体化设备的启动,并且所采用的全好氧脱氮菌为异养菌,生长速率快,因此,其设备的启动时间为12~15天,明显少于活性污泥挂膜的传统生物膜工艺设备启动的时间20~25天,有启动时间短的优点。(2)本发明采用适用范围广、耐受性能强的全好氧脱氮菌作为接种菌剂,接种菌剂中的杂菌较传统生物膜采用活性污泥挂膜的工艺大大减少,对基质和溶氧的竞争较弱,并且全好氧菌剂对高氨氮和高有机物的耐受性能强,有利于功能菌的富集和优势化构建。该一体化设备的在高氨氮、低温等不利条件下的脱氮效果要远高于传统生物膜脱氮工艺,优势更明显。(3)本发明采用全好氧脱氮技术,在一个构筑物中,一种运行条件下就可以实现“氨氮、亚硝态氮和硝态氮”的去除,和传统脱氮工艺相比,该一体化处理设备的工艺流程更简洁,建设运行成本和运维管理难度更低。(4)本发明通过“以废治废”的方式,利用原水中的高浓度的有机物去除原水中的高浓度氨氮,从源头实现有机物和氨氮含量的大幅削减,这是其他传统处理工艺无法实现的。(5)本发明由于可采用空气自然接触的复氧方式来维持一体化设备全好氧反应区的好氧环境,用于固定全好氧脱氮菌的载体采用生物转盘或生物转笼,通过驱动生物转盘或生物转笼进行空气自然接触复氧,由于驱动生物转盘或生物转笼的低速电动机的功率远低于采用人工曝气的曝气机的功率,因此和传统脱氮工艺相比,它的能耗和运行成本更低。(6)本发明当养殖废水中有机氮含量>100mg/l时,可通过臭氧反应区功能对好氧反应区的出水进行氧化处理,臭氧处理可将好氧反应区出水中残留的有机氮转化为氨氮,再回流到好氧反应区进一步处理,可实现70-80%的有机氮去除。(7)本发明中一体化设备的全好氧反应区可采用的工艺形式多样,可根据处理废水的不同类型选择与之匹配的填料和处理工艺,和单一的传统生物膜脱氮工艺相比,应用更加灵活多变,适用范围也更广。经固液分离后的畜禽养殖废水采用本发明所述工艺及一体化设备进行前处理,原水的水质组成为:cod浓度为7000~10000mg/l,氨氮浓度为500~1000mg/l,有机氮20~250mg/l,硝酸盐氮30~160mg/l,总磷10~18mg/l,ph值为7.1~7.5。经本发明所述工艺和一体化设备进行前处理后的得到的水,其原水中cod(2000-10000mg/l)、氨氮(500-1000mg/l)、有机氮(100-300mg/l)和总氮(600-1400mg/l)的削减率可分别达到60~70%,70~80%,70~75%,80~90%,出水水质完全满足后续处理的进水要求。本发明所述的有机物是指化学需氧量(cod)。本发明所述工艺和设备,充分利用原水中高浓度的有机物将原水中的高浓度氨氮去除,在不改变原水可生化性和c/n比的同时大幅削减原水中有机物、氨氮和总氮的含量,保证后续水处理工艺的稳定正常运行。既可用于特定的畜禽养殖废水处理领域,也可以用于城镇污水厂提标改造深度、黑臭水体治理、水产循环养殖废水处理、地下水硝酸盐污染治理和农村分散污水处理等领域废水脱氮处理。附图说明图1为一体化设备的一种实施例示意图。具体实施方式参见图1,一种畜禽养殖废水前处理全好氧脱氮一体化设备的实施例。废水前处理全好氧脱氮设备包括全好氧反应区2、臭氧反应区7、储存区13和设备控制区8。本实施例的所述全好氧反应区2为生物反应池,臭氧反应区7为臭氧反应池,储存区13为出水储存池,设备控制区8为安装电器控制柜10、臭氧发生器12、电动机11的设备间,各区之间通过隔墙分隔形成依次相连的一体化设备。所述全好氧反应区2中设有用于固定全好氧脱氮菌的载体,所述用于固定全好氧脱氮菌的载体为生物转盘3或生物转笼,所述生物转盘3或生物转笼转速由设备区8中电器控制柜10控制的电动机11驱动。所述生物转盘3或生物转笼圆周边缘的线速度控制在1~3m/min,或者7.5~15m/min;当用于菌剂接种生长-吸附挂膜阶段时,将生物转盘3或生物转笼的线速度控制在1~3m/min范围,让好氧反应区的溶解氧浓度保持在0.5~1.5mg/l的范围,保证菌剂接种生长-吸附挂膜;当挂膜成熟采取连续注进养殖废水原水模式运行时,则将生物转盘3或生物转笼的线速度提高到7.5~15m/min,能够使全好氧反应区的废水原水中有机物和氨氮浓度出现明显削减,其中cod的削减率可达60~70%,氨氮的削减率可达70~80%,有机氮的削减率可达70~75%,总氮的削减率可达80~90%。本实施例采用生物转盘3,所述生物转盘3主体结构的总长度为3~6米,总高度为1.3~2.6米,总容量为1.6~10m3。生物转盘3的盘片为圆形结构,反应区内的盘片数量为20~40个,这些盘片依次排列固定在一中心转轴17上,生物转盘3的盘片材料为聚丙烯和聚乙烯中的一种,盘片的直径为1~2米,中心转轴17通过轴承16支承在隔墙上,中心转轴17的一端延伸到设备控制区8中,通过带传动机构9与电动机12连接,由电动机12驱动生物转盘3转动,电动机12的功率为1.0~2.0kw。所述中心转轴17的位置高于全好氧反应区2的水位上限10cm左右,使生物转盘3的面积至少有一半能够与空气接触。所述全好氧反应区2的进水端设有机械格栅1,机械格栅1用于连续自动拦截并清除畜禽养殖废水中的各种固体杂物及悬浮物。全好氧反应区2的出水端与臭氧反应区7进水端连通,在全好氧反应区2与臭氧反应区7之间的隔墙上设有溢流孔15,该溢流孔15位于全好氧反应区2的水位上限处,使设备连续工作时全好氧反应区2经生物反应后的废水能够从溢流孔15溢流到臭氧反应区7。所述臭氧反应区7与全好氧反应区2还通过设有回流泵6和流量计5的回流管道4相连,所述回流管道4的上游进口位于臭氧反应区7的池底,回流管道4的下游出口18位于生物转盘2前端的全好氧反应区2池侧壁,该下游出水口18可高于全好氧反应区2的水位上限,通过回流管道4能够将臭氧反应区7中经臭氧氧化的废水循化回流到全好氧反应区2中。所述臭氧反应区7的出水端与储存区13进水端连通,在臭氧反应区7与储存区13之间的隔墙上同样设有溢流孔,使经过臭氧反应区7而不需臭氧氧化的废水能够直接溢流到储存区13内,经观察测得储存区废水中有机物和氨氮浓度达标后,然后从储存区13出水口(未示出)排出,进入后序的处理。所述储存区13的出水口位于储存区13低位,且设有阀门(未示出)。所述设备区8内设有电器控制柜10、臭氧发生器12,所述臭氧发生器12与臭氧反应区7内设置的臭氧矩阵14通过输送管连接,所述臭氧发生器12、回流泵6、机械格栅1、电动机11的工作由电器控制柜10控制。本畜禽养殖废水前处理全好氧脱氮一体化设备不仅仅局限于上述实施例,其中所述全好氧生物反应区为接触氧化池,或者生物流化床,或者生物滴滤塔,或者曝气生物滤池;接触氧化池或生物流化床或生物滴滤塔或曝气生物滤池中均设有用于固定全好氧脱氮菌的载体,所述用于固定全好氧脱氮菌的载体为悬挂式填料,或者悬浮填料,或者填充填料,同样可以实现畜禽养殖废水前处理全好氧脱氮。一种畜禽养殖废水前处理全好氧脱氮工艺,其特征在于该工艺步骤如下:1)菌剂接种生长-吸附挂膜将畜禽养殖废水原水经机械格栅固液分离除去残留悬浮物后注入全好氧反应区中,通过蠕动泵控制进水的流量,使好氧反应区的水力停留时间控制在12~24h的范围。在全好氧反应区的废水原水中加入全好氧脱氮菌剂和液态富集培养基形成混合液,以具有高效异养硝化-好氧反硝化性能的全好氧脱氮菌为接种菌剂,全好氧脱氮菌剂和液态富集培养基的加入总量为水的4~10%重量百分比,其中,全好氧脱氮菌剂体积:液态培养基质体积为3~8:100,使全好氧反应区的溶解氧浓度保持在0.5~1.5mg/l。采用紫外分光光度计监测接种过程中菌剂/培养基的混合液中光密度(od)值和氨氮浓度的变化,每24小时测一次混合液的od值,当od值达到1.05~1.22并开始下降时,菌剂接种生长阶段结束;随着混合液od值快速下降,氨氮的去除速率逐渐上升,表明菌剂开始吸附在盘片上进行挂膜,直至全好氧脱氮菌剂在全好氧反应区设置的用于固定全好氧脱氮菌的载体吸附挂膜接种完成。本实施例的用于固定全好氧脱氮菌的载体采用生物转盘,也可以采用生物转笼。通过电动机将生物转盘的线速度控制在1~3m/min范围,有利于接种菌剂吸附固定在生物转盘上,借助生物转盘的转动,采用自然接触复氧的方式获得全好氧环境,让好氧反应区的溶解氧浓度保持在0.5~1.5mg/l的范围,保证菌剂接种生长-吸附挂膜,可以将启动挂膜的时间缩短到12~18天,提高挂膜效率。所述的全好氧脱氮菌剂为苍白杆菌或复合菌剂。所述富集培养基的组分为:硫酸铵2.67g~4.44g/l(氨氮600~1000mg/l),碳源3.55~11.8g/l(cod3000~10000mg/l),维氏盐溶液30~60ml/l,调节ph值至7.0~7.5,100~121℃高压蒸汽灭菌10~30min。其中,所述维氏盐溶液g/l的组分为:k2hpo43.0~6.0,mgso47h2o1~3,nacl2~4,feso47h2o0.01~0.09,mnso44h2o0.01~0.09。富集培养基中的碳源可能为琥珀酸钠、柠檬酸钠、乙酸钠、葡萄糖、蔗糖、淀粉、聚己内酯、聚丁二酸丁二醇酯等碳源中的一种或几种的组合的重量比,具体见下表:碳源类型淀粉乙酸钠柠檬酸钠琥珀酸钠葡萄糖葡萄糖+淀粉乙酸钠:柠檬酸钠琥珀酸钠+柠檬酸钠淀粉+聚己内酯重量配比-----1-2:6-81-2:4-51-3:13-4:6-7富集培养基的最适碳氮比(重量比)范围在5-25之间。通过上述方式实现全好氧功能菌的优势化构建。2)挂膜成熟当采用紫外分光光度计测得混合溶液的od值降到最低为0.20~0.25,同时通过分光光度法测得氨氮浓度绘制氨氮浓度随时间的变化曲线上,氨氮的去除速率出现明显向下的拐点,且生物转盘上的生物膜变厚,颜色加深,则表明全好氧脱氮菌挂膜成熟;然后将步骤1)所述混合液从全好氧反应区排出。3)稳定运行阶段向全好氧反应区中连续注入新的经固液分离除去悬浮物后的畜禽养殖废水原水,这种养殖废水的组分为:cod浓度为6000~9080mg/l,氨氮浓度为600~800mg/l,有机氮30~200mg/l,硝酸盐氮50~150mg/l,总磷12~18mg/l,ph值为7.02~7.42。采取连续注入养殖废水的模式进行废水处理运行,通过进水蠕动泵控制进水流量,使好氧反应区的水力停留时间控制在12~24h的范围,将生物转盘的边缘线速度提高到7.5~15m/min,以有效抑制丝状菌生长,同时维持溶解氧浓度在1.5~3mg/l,每24h采用紫外分光光度计测一次出水的有机物和氨氮浓度,待全好氧反应区的连续出水中有机物和氨氮浓度出现明显降低(cod<350mg/l,nh4+-n<150mg/l),并且连续三天测得出水的氨氮浓度误差在5%以内,则表明脱氮处理稳定运行。4)臭氧反应处理当测得全好氧反应区的废水出水中有机氮含量>100mg/l时,启动臭氧发生器,让进入臭氧反应区的废水进行氧化处理,臭氧按2~8mg/l投入臭氧反应区,臭氧与废水的反应时间为20~60min,并使氧化处理后的废水部分回流到全好氧反应区加入全好氧反应区的废水中,再次按照步骤3)所述方法进行脱氮处理。氧化处理后的废水回流全好氧反应区的回流比为50%~200%。当测得全好氧反应区的废水出水中有机氮含量<100mg/l时,则不启动臭氧发生器,让废水出水直接进入储存区。5)前处理结束测得储存区中废水出水中有机物和氨氮浓度分别为300-1500mg/l,130-200mg/l,其中cod的削减率为60~70%,氨氮的削减率为70~80%,有机氮的削减率为70~75%,总氮的削减率为80~90%,经前处理的废水从储存区流出进行后序处理。以下是采用本发明所述方法进行畜禽养殖废水前处理的实施例:实施例1重庆綦江某猪场养殖废水为原废水,其水质参数为:cod浓度为2680mg/l,氨氮浓度为534.7mg/l,总氮浓度为704.1mg/l,硝态氮浓度为149.5mg/l,磷酸盐浓度为15.5mg/l,ph:7.2,原水do:2.8mg/l。室温25-28℃,水力停留时间(hrt)设置为24h,生物转盘转速34rpm/min,对应盘片线速度为15m/min,溶解氧浓度为2-3mg/l。由于该养殖废水中有机氮含量低,所以无需通过臭氧反应区,也无需回流。该高氨养殖废水,采用上述方法进行前处理后,氨氮、有机物和总氮的有效削减。处理前后水质情况如下表1所示。表1重庆綦江某猪场养殖废水经一体化设备处理前后水质变化情况实施例2重庆巴南某奶牛场养殖废水为原水,其水质参数为:cod浓度为9028.7mg/l,氨氮浓度为760.4mg/l,总氮浓度为1140.6mg/l,硝态氮浓度为155.1mg/l,磷酸盐浓度为18.3mg/l,ph:7.4,原水do:2.1mg/l。由于奶牛场废水中有机氮含量较大,好氧反应区的出水随后进入臭氧反应区。室温25-28℃,水力停留时间(hrt)设置为24h,生物转盘转速为34rpm/min,对应盘片线速度为15m/min,溶解氧浓度为2-3mg/l。臭氧的投加浓度为6mg/l,反应时间45min,氧化后出水回流到生物转盘前段的回流比为150%。上述高氨氮奶牛场养殖废水,采用上述方法进行前处理后,其有机物、氨氮和总氮的有效去除。处理前后水质情况如下表2所示。表2重庆巴南某奶牛场废水经一体化设备处理前后水质变化情况本发明通过畜禽养殖废水前处理全好氧脱氮工艺及一体化设备进行畜禽养殖废水前处理,将固液分离后的养殖废水原水经过机械格栅后,残留悬浮物被进一步去除;在全好氧反应区内,以具有高效异养硝化-好氧反硝化性能的全好氧脱氮菌为接种菌剂,借助生物膜反应器内生物转盘的吸附实现菌剂的固定,借助生物转盘的转动,采用自然接触复氧的方式获得全好氧环境,通过反应器结构和运行条件优化,最终以转盘盘片上生物膜的形式实现全好氧脱氮菌剂的富集和优势化构建,形成全好氧脱氮技术。生物转盘上的全好氧脱氮菌利用原水中的高浓度cod和氨氮作为碳源和氮素,利用自然接触复氧获得的溶解氧,通过异养硝化-好氧反硝化的脱氮形式,实现原水中cod、氨氮和tn浓度的大幅消减;对于有机氮含量较高的养殖废水,全好氧反应区的出水通过臭氧反应区的氧化,有机氮被转换成氨氮,随后回流到生物转盘的进水端,获得氨氮和有机物浓度的进一步削减。全好氧反应区或臭氧反应区的出水进入储水池,随后进入后续的水处理单元。本发明能够缩短设备启动周期,同时也为功能菌的富集创造条件。通过一体化设备的结构及运行条件优化,实现接种功能菌的优势化构建,充分发挥功能菌所具有的各种优良性能。本发明的应用范围不局限于某一特定废水处理领域,如畜禽养殖废水,也可广泛应用于城镇污水厂提标改造深度、黑臭水体治理、水产循环养殖废水处理、地下水硝酸盐污染治理和农村分散污水处理等领域废水脱氮处理。当前第1页12