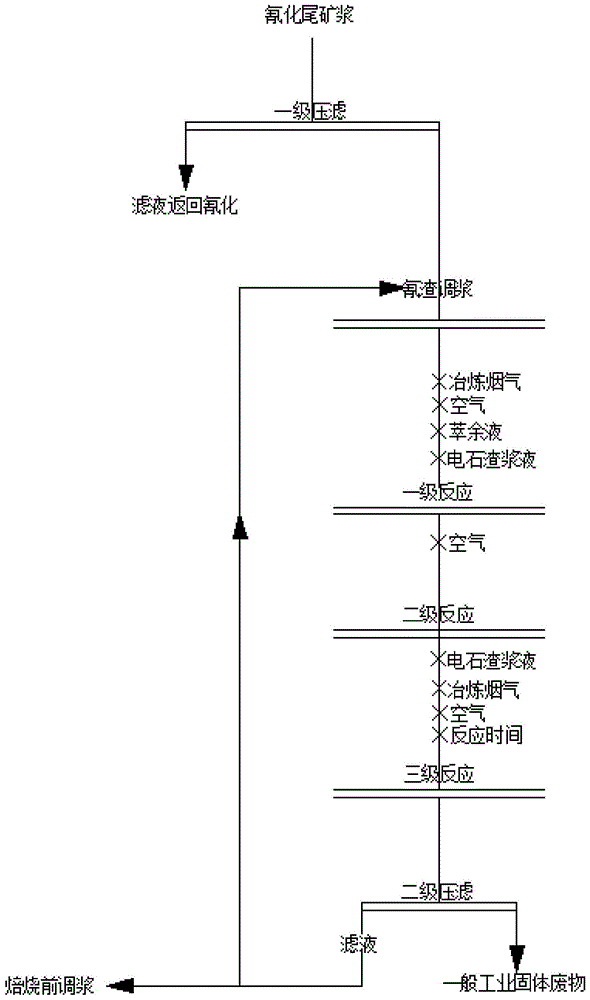
本发明涉及环保领域中固体废物的综合治理,特别涉及一种采用萃余液与冶炼烟气协同综合治理氰化尾渣的方法。
背景技术:
:在黄金行业,由于氰化提金工艺具有工艺简单、金回收率高等特点一直被列为首选工艺。然而由于在浸出过程中投加大量的氰化钠,金被浸出的同时,其余重金属也被浸出,导致氰化尾渣中氰化物和重金属含量超标,尤其是采用金精矿提金的工艺产生的氰化尾渣毒性更高,鉴别为危险废物。含硫较高的金精矿中一般铁和二氧化硅含量高,此种氰化尾渣非常适合作为水泥骨料进行综合利用,但是由于其性质为危险废物,水泥生产企业需具有危险废物处理资质,但是具有资质的水泥生产企业较少,所有目前很多企业仅少量的氰化尾渣得以综合利用,大部分氰化尾渣只能在厂区贮存或者在尾矿库填埋,不仅浪费了资源,而且环境风险较大,不仅给企业管理上增加了负担,同时企业也面临由于环保不合格随时被关停的风险。而且2018年环保税的实施,企业将面临高额的环保税和危险废物处置费用。针对于氰化尾渣,最好的出路就是首先满足环保要求,再实现全资源化利用。目前,氰化尾渣的综合治理技术并不多,主要有双氧水氧化法、次氯酸钠氧化法、因科法、铁盐降氰法等。上述方法均需采购药剂投加到氰化尾渣综合治理系统中,药剂投加量大,运行成本高,且每种处理方法均有其局限性,针对于难处理的氰化尾渣,需投加比理论药剂量更多的药剂,而且还无法稳定达标。如何保障系统安全稳定运行和降低投资及运行成本成为氰化尾渣综合治理亟需解决的问题,也是本发明要解决的实际问题。技术实现要素:本发明提供一种萃余液与冶炼烟气协同综合治理氰化尾渣的方法,以解决目前存在的药剂投加量大,运行成本高,无法稳定达标的问题。本发明采取的技术方案是:包括下列步骤:(1)对氰化尾矿浆进行固液分离,滤液返回氰化系统,滤渣落入调浆槽;(2)采用循环水作为浸提剂对氰化尾渣中污染物进行解吸,将氰化尾渣调成一定矿浆浓度;(3)将调好的矿浆泵入或溢流到矿浆缓冲槽,起到缓冲、均化、调节作用,减小进浆指标和流量波动对系统的冲击;(4)将缓冲槽内矿浆泵入或溢流到第一级反应器内,投加萃余液、通入冶炼烟气和空气,同时投加ph调整剂调节矿浆中ph,确保反应高效;(5)矿浆通过第一级反应后溢流到第二级反应器,通入空气,继续反应;(6)矿浆通过第二级反应后溢流到第三级反应器,再次通入冶炼烟气和空气,投加ph调整剂调节矿浆中ph;(7)矿浆经第三级反应器反应后溢流到压滤进浆缓冲槽,利用渣浆泵将矿浆泵入压滤机进行固液分离,液体返回步骤(2)循环利用;(8)各级反应器采用密闭处理,采用离心风机将各级反应器尾气引入吸收塔,采用碱液循环喷淋方式对尾气进行吸收,保证尾气达标排放。本发明所述步骤(2)中,矿浆浓度为30%-50%,过低将增加动力消耗和设备投资,过高矿浆将变得粘稠,不利于处理。本发明所述步骤(4)中,萃余液量按照与矿浆量体积比0.01:1-0.1:1投加,冶炼烟气量按照与矿浆量体积比5:1-10:1投加,空气量按照与冶炼烟气量1:1-2:1投加,采用旋流曝气装置投加,保证足够溶解氧,维持ph值为8-10;本发明所述步骤(4)中,ph调整剂为10%电石渣浆液;本发明所述步骤(5)中,空气量按照与矿浆量体积比1:1-5:1投加;本发明所述步骤(6)中,冶炼烟气量按照与矿浆量体积比1:1-5:1投加,空气量按照与冶炼烟气量1:1-2:1投加,通过ph调整剂调节矿浆中ph值为7-7.5;本发明所述步骤(6)中,ph调整剂为10%电石渣浆液。本发明是利用黄金行业焙烧企业生产过程中产生的含有高浓度二氧化硫的冶炼烟气和萃取提铜工艺中萃余液对氰化工艺产生的氰化尾渣进行综合治理,将其达到一般工业固体废物要求。本发明针对氰化尾渣特性以及生产企业已有条件,有针对性地提供一种工艺流程简单、处理效率高的“以废治废、因地制宜”的处理方法,可降低运行成本、提高系统稳定性,对于难处理氰化尾渣可保证指标达标率100%。本发明的有益效果:本发明充分考虑了企业废水、废气和废渣情况,以氰化尾渣达标治理为主要目标,实现了三废综合治理,具有处理效果好、处理效率高、系统运行稳定、运行成本低、工艺流程简单、便于实现工业应用、通用性强等优点,系统工艺水循环调浆利用,废水“零排放”,符合清洁生产要求。附图说明图1是本发明的流程图。具体实施方式实施例1包括下列步骤:(1)对氰化尾矿浆进行固液分离,滤液返回氰化系统,滤渣落入调浆槽;(2)采用循环水作为浸提剂对氰化尾渣中污染物进行解吸,将氰化尾渣调成30%矿浆浓度;(3)将调好的矿浆泵入或溢流到矿浆缓冲槽,起到缓冲、均化、调节作用,减小进浆指标和流量波动对系统的冲击;(4)将缓冲槽内矿浆泵入或溢流到第一级反应器内,投加萃余液、通入冶炼烟气和空气,其中萃余液量按照与矿浆量体积比0.01:1投加,冶炼烟气量按照与矿浆量体积比5:1投加,空气量按照与冶炼烟气量1:1投加,采用旋流曝气装置投加,保证足够溶解氧,同时投加10%电石渣浆液调节矿浆中ph值为8,确保反应高效;(5)矿浆通过第一级反应后溢流到第二级反应器,通入空气,空气量按照与矿浆量体积比1:1投加,继续反应;(6)矿浆通过第二级反应后溢流到第三级反应器,再次通入冶炼烟气和空气,其中冶炼烟气量按照与矿浆量体积比1:1投加,空气量按照与冶炼烟气量1:1投加,投加10%电石渣浆液调节矿浆中ph值为7;(7)矿浆经第三级反应器反应后溢流到压滤进浆缓冲槽,利用渣浆泵将矿浆泵入压滤机进行固液分离,液体返回步骤(2)循环利用;(8)各级反应器采用密闭处理,采用离心风机将各级反应器尾气引入吸收塔,采用碱液循环喷淋方式对尾气进行吸收,保证尾气达标排放。实施例2包括下列步骤:(1)对氰化尾矿浆进行固液分离,滤液返回氰化系统,滤渣落入调浆槽;(2)采用循环水作为浸提剂对氰化尾渣中污染物进行解吸,将氰化尾渣调成40%矿浆浓度;(3)将调好的矿浆泵入或溢流到矿浆缓冲槽,起到缓冲、均化、调节作用,减小进浆指标和流量波动对系统的冲击;(4)将缓冲槽内矿浆泵入或溢流到第一级反应器内,投加萃余液、通入冶炼烟气和空气,其中萃余液量按照与矿浆量体积比0.05:1投加,冶炼烟气量按照与矿浆量体积比8:1投加,空气量按照与冶炼烟气量1:1.5投加,采用旋流曝气装置投加,保证足够溶解氧,同时投加10%电石渣浆液调节矿浆中ph值为9,确保反应高效;(5)矿浆通过第一级反应后溢流到第二级反应器,通入空气,空气量按照与矿浆量体积比3:1投加,继续反应;(6)矿浆通过第二级反应后溢流到第三级反应器,再次通入冶炼烟气和空气,其中冶炼烟气量按照与矿浆量体积比3:1投加,空气量按照与冶炼烟气量1:1.5投加,投加10%电石渣浆液调节矿浆中ph值为7.3;(7)矿浆经第三级反应器反应后溢流到压滤进浆缓冲槽,利用渣浆泵将矿浆泵入压滤机进行固液分离,液体返回步骤(2)循环利用;(8)各级反应器采用密闭处理,采用离心风机将各级反应器尾气引入吸收塔,采用碱液循环喷淋方式对尾气进行吸收,保证尾气达标排放。实施例3包括下列步骤:(1)对氰化尾矿浆进行固液分离,滤液返回氰化系统,滤渣落入调浆槽;(2)采用循环水作为浸提剂对氰化尾渣中污染物进行解吸,将氰化尾渣调成50%矿浆浓度;(3)将调好的矿浆泵入或溢流到矿浆缓冲槽,起到缓冲、均化、调节作用,减小进浆指标和流量波动对系统的冲击;(4)将缓冲槽内矿浆泵入或溢流到第一级反应器内,投加萃余液、通入冶炼烟气和空气,其中萃余液量按照与矿浆量体积比0.1:1投加,冶炼烟气量按照与矿浆量体积比10:1投加,空气量按照与冶炼烟气量2:1投加,采用旋流曝气装置投加,保证足够溶解氧,同时投加10%电石渣浆液调节矿浆中ph值为10,确保反应高效;(5)矿浆通过第一级反应后溢流到第二级反应器,通入空气,空气量按照与矿浆量体积比5:1投加,继续反应;(6)矿浆通过第二级反应后溢流到第三级反应器,再次通入冶炼烟气和空气,其中冶炼烟气量按照与矿浆量体积比5:1投加,空气量按照与冶炼烟气量2:1投加,投加10%电石渣浆液调节矿浆中ph值为7.5;(7)矿浆经第三级反应器反应后溢流到压滤进浆缓冲槽,利用渣浆泵将矿浆泵入压滤机进行固液分离,液体返回步骤(2)循环利用;(8)各级反应器采用密闭处理,采用离心风机将各级反应器尾气引入吸收塔,采用碱液循环喷淋方式对尾气进行吸收,保证尾气达标排放。下边通过具体实例对本发明做进一步说明。某黄金冶炼企业含氰尾矿浆,采用下述方法对其进行处理,(1)对氰化尾矿浆进行固液分离,滤液返回氰化系统,滤渣落入调浆槽;(2)采用循环水作为浸提剂对氰化尾渣中污染物进行解吸,将氰化尾渣调成40%矿浆浓度,矿浆量为10m3/h;(3)将调好的矿浆泵入或溢流到矿浆缓冲槽,起到缓冲、均化、调节作用,减小进浆指标和流量波动对系统的冲击;(4)将缓冲槽内矿浆泵入或溢流到第一级反应器内,投加萃余液0.5m3/h、通入冶炼烟气50m3/h和空气100m3/h,采用旋流曝气装置投加,保证足够溶解氧,同时投加10%电石渣浆液调节矿浆中ph值为9,确保反应高效;(5)矿浆通过第一级反应后溢流到第二级反应器,通入空气50m3/h,继续反应;(6)矿浆通过第二级反应后溢流到第三级反应器,再次通入冶炼烟气和空气,再次通入冶炼烟气30m3/h和空气45m3/h,投加10%电石渣浆液调节矿浆中ph值为7.3;(7)矿浆经第三级反应器反应后溢流到压滤进浆缓冲槽,利用渣浆泵将矿浆泵入压滤机进行固液分离,液体返回步骤(2)循环利用;(8)各级反应器采用密闭处理,采用离心风机将各级反应器尾气引入吸收塔,采用碱液循环喷淋方式对尾气进行吸收,保证尾气达标排放。通过采用上述方法对其进行处理,调浆后液相污染物组成见表1,投加萃余液和冶炼烟气对调浆后矿浆进行处理,萃余液污染物组成见表2,冶炼烟气中二氧化硫平均体积分数为5.5%,处理后矿浆中液相污染物组成见表3,毒性浸出结果见表4,浸出毒性达到一般工业固体废物要求。表1调浆后液相污染物组成项目cntcnfscncodcl-so42-mgfe指标273.56237.28167.58698105784110.937.68项目hgasznpbcuagniau指标0.04350.06384.40.3992.520.130.240.025注:单位为mg/l。表2萃余液污染物组成表3处理后矿浆液相污染物组成表4处理后氰化尾渣毒性浸出结果项目cntcuzncdcrhgbeag指标0.191<0.040<0.040<0.040<0.080<0.00008<0.040<0.040项目asnisecr6+pbbaf指标<0.810<0.080<0.450<0.004<0.120<0.240<0.014注:单位为mg/l。以上所述仅为本发明的实施例,并非因此限制本发明的专利范围,凡是利用本发明说明书及附图内容所作的等效结构或等效流程变换,或直接或间接运用在其他相关的
技术领域:
,均同理包括在本发明的专利保护范围内。当前第1页12