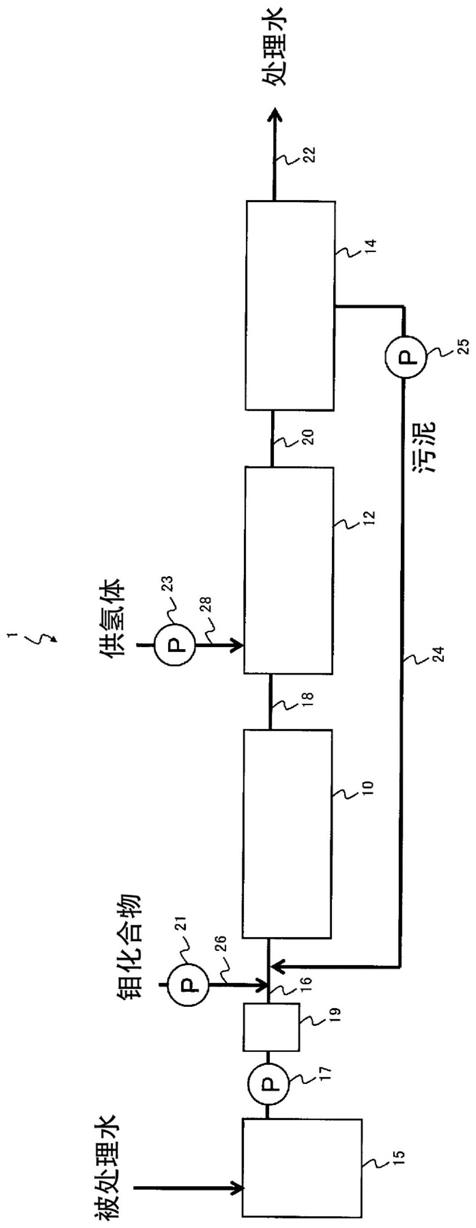
environmental distribution,journal of biotechnology,155(2011),pp.104-117非专利文献3:molybdenum as a micronutrient for nitrobacter,journal of bacteriology,89(1965),pp.123-128非专利文献4:molecular analysis of ammonia oxidation anddenitrification in natural environments,fems microbiology reviews,24(2000),pp.673-690
技术实现要素:发明要解决的课题
[0007]
本发明的目的在于提供水处理方法和水处理装置,其中,在含有氨态氮的被处理水的生物学处理中,即使被处理水中的氮浓度为高浓度也能够以高处理速度稳定处理。用于解决课题的技术方案
[0008]
本发明是一种水处理方法,其中,对含有氨态氮的被处理水进行生物学处理,上述水处理方法包括:硝化工序,其中,通过微生物活性污泥中所包含的硝化菌将上述氨态氮氧化为亚硝酸或硝酸态氮,其中,上述硝化菌包含自养型氨氧化菌和亚硝酸氧化菌;上述硝化工序中存在钼化合物,使钼浓度相对于上述被处理水成为0.025mgmo/gn以上,每单位污泥的硝化速度为0.11[kgn/(kgvss
·
天)]以上。
[0009]
在上述水处理方法中,上述硝化工序中的钼浓度相对于上述被处理水优选为2mgmo/l以下。
[0010]
在上述水处理方法中,上述被处理水中的氮浓度优选为100mgn/l以上。
[0011]
在上述水处理方法中,优选还包括脱氮工序,其中,通过上述微生物活性污泥中所包含的脱氮菌,将上述硝化工序中生成的亚硝酸或硝酸态氮还原为氮气。
[0012]
上述水处理方法中的上述脱氮工序中,优选对上述供氢体的添加量赋予时间变动,以使在处理水的水力停留时间内的供氢体的最大浓度与最小浓度之差成为50mgtoc/l以上,由此使包含上述硝化菌和脱氮菌的微生物活性污泥颗粒化。
[0013]
在上述水处理方法中,优选上述脱氮工序至少包括第一脱氮工序和第二脱氮工序,在上述脱氮工序中,至少在上述第一脱氮工序中供给供氢体,使在上述第二脱氮工序中的处理水的水力停留时间内的上述第一脱氮工序中的供氢体的最大浓度与上述第二脱氮工序中的供氢体的最小浓度之差成为50mgtoc/l以上。
[0014]
本发明是一种水处理装置,其对含有氨态氮的被处理水进行生物学处理,上述水处理装置具备:硝化单元,其中,通过微生物活性污泥中所包含的硝化菌将上述氨态氮氧化为亚硝酸或硝酸态氮,其中,上述硝化菌包含自养型氨氧化菌和亚硝酸氧化菌;以及硝化速度控制单元,其中,按照以下方式进行控制:在上述硝化单元中存在钼化合物,使钼浓度相对于上述被处理水成为0.025mgmo/gn以上,并且使每单位污泥的硝化速度成为0.11[kgn/(kgvss
·
天)]以上。
[0015]
在上述水处理装置中,优选上述硝化速度控制单元按照以下方式进行控制:使上述硝化单元中的钼浓度在上述被处理水中成为2mgmo/l以下。
[0016]
在上述水处理装置中,上述被处理水中的钼浓度优选为0.0001mgmo/l以下。
[0017]
在上述水处理装置中,上述被处理水中的氮浓度优选为100mgn/l以上。
[0018]
在上述水处理装置中,优选还具备:脱氮单元,其中,上述通过上述微生物活性污
泥中所包含的脱氮菌,将在上述硝化单元中生成的亚硝酸或硝酸态氮还原为氮气。
[0019]
在上述水处理装置中,优选还具备:供氢体浓度控制单元,其中,按照以下方式进行控制:在上述脱氮单元中,对上述供氢体的添加量赋予时间变动,以使在处理水的水力停留时间内的供氢体的最大浓度与最小浓度之差成为50mgtoc/l以上,由此使包含上述硝化菌和脱氮菌的微生物活性污泥颗粒化。
[0020]
在上述水处理装置中,优选上述脱氮单元至少具备第一脱氮单元和第二脱氮单元,上述供氢体浓度控制单元,按照以下方式进行控制:在上述脱氮单元中,至少在上述第一脱氮单元中供给供氢体,其中,使在上述第二脱氮单元中的处理水的水力停留时间内的上述第一脱氮单元中的供氢体的最大浓度与上述第二脱氮单元中的供氢体的最小浓度之差成为50mgtoc/l以上。发明效果
[0021]
根据本发明,在含有氨态氮的被处理水的生物学处理中,即使被处理水中的氮浓度为高浓度,也能够以高处理速度稳定地进行处理。
附图说明
[0022]
图1是表示本发明的实施方式涉及的水处理装置的示例的概略结构图。图2是表示本发明的实施方式涉及的水处理装置的其它示例的概略结构图。图3是表示本发明的实施方式涉及的水处理装置的其它示例的概略结构图。图4是表示本发明的实施方式涉及的水处理装置的其它示例的概略结构图。图5是表示本发明的实施方式涉及的水处理装置的其它示例的概略结构图。图6是表示本发明的实施方式涉及的水处理装置的其它示例的概略结构图。图7是表示本发明的实施方式涉及的水处理装置的其它示例的概略结构图。图8是表示本发明的实施方式涉及的水处理装置的其它示例的概略结构图。图9是表示实施例1和比较例1中,硝化槽容积负荷[kgn/(m3·
d)]、硝化槽的氨态氮浓度[mgn/l]相对于经过天数[天]的图表。图10是表示实施例1和比较例1中,脱氮槽容积负荷[kgn/(m3·
d)]、处理水的总氮浓度[mgn/l]相对于经过天数[天]的图表。图11是表示比较例2中,硝化槽容积负荷[kgn/(m3·
d)]、硝化槽的氨态氮浓度[mgn/l]相对于经过天数[天]的图表。图12是表示比较例2中,脱氮槽容积负荷[kgn/(m3·
d)]、处理水的总氮浓度[mgn/l]相对于经过天数[天]的图表。图13是表示实施例2中,硝化槽容积负荷[kgn/(m3·
d)]、硝化槽的氨态氮浓度[mgn/l]相对于经过天数[天]的图表。图14是表示实施例2中,脱氮槽容积负荷[kgn/(m3·
d)]、处理水的总氮浓度[mgn/l]相对于经过天数[天]的图表。图15是表示实施例3中,硝化槽容积负荷[kgn/(m3·
d)]、硝化槽的氨态氮浓度[mgn/l]相对于经过天数[天]的图表。图16是表示实施例3中,脱氮槽容积负荷[kgn/(m3·
d)]、处理水的总氮浓度[mgn/l]相对于经过天数[天]的图表。
图17是表示实施例中,硝化速度[kgn/(kgvss
·
d)]相对于钼浓度(mo/n[mg/g])的图表。
具体实施方式
用于实施发明的方式
[0023]
以下,对本发明的实施方式进行说明。该实施方式是实施本发明的示例,本发明并不限定于该实施方式。
[0024]
将本发明的实施方式涉及的水处理装置的示例的概略示出图1,对其结构进行说明。
[0025]
水处理装置1是对含有氨态氮的被处理水进行生物学处理的水处理装置,其具备硝化装置10作为硝化单元,其中,通过微生物活性污泥中所包含的硝化菌,将氨态氮氧化为亚硝酸或硝酸态氮,上述硝化菌包含自养型氨氧化菌和亚硝酸氧化菌;以及硝化速度控制单元,其中,按照以下方式进行控制:在硝化装置10中存在钼化合物,使钼浓度相对于被处理水成为0.025mgmo/gn以上,并且使每单位污泥的硝化速度成为0.11[kgn/(kgvss
·
天)]以上。水处理装置1可以还具备脱氮装置12作为脱氮单元,其中,通过微生物活性污泥中所包含的脱氮菌,将在硝化装置10中生成的亚硝酸或硝酸态氮还原为氮气。
[0026]
水处理装置1还可以具备固液分离装置14作为固液分离单元,其中,从微生物活性污泥分离处理水而得到处理水;具备污泥送回配管24作为送回单元,其中,将固液分离装置14中分离的污泥送回至固液分离装置14的前段。另外,水处理装置1也可以具备被处理水调整槽15,其中,贮存被处理水。
[0027]
图1的水处理装置1中,被处理水调整槽15的出口与硝化装置10的入口,介由作为被处理水供给量调整单元的被处理水供给泵17,通过配管16连接,硝化装置10的出口与脱氮装置12的入口通过配管18连接,脱氮装置12的出口与固液分离装置14的入口通过配管20连接,在固液分离装置14的处理水出口连接有配管22,固液分离装置14的污泥出口与配管16介由污泥送回泵25通过污泥送回配管24连接。在配管16上,在被处理水供给泵17的下游侧设置有流量测定装置19作为用于测定被处理水的流量的被处理水流量测定单元,在流量测定装置19的下游侧且污泥送回配管24的连接点的上游侧,介由作为钼化合物供给量调整单元的钼化合物供给泵21,连接有钼化合物供给配管26,在脱氮装置12中,介由作为供氢体供给量调整单元的供氢体供给泵23连接有供氢体供给配管28。
[0028]
对本实施方式涉及的水处理方法和水处理装置1的动作进行说明。
[0029]
包含氨态氮的被处理水,介由被处理水供给泵17从被处理水调整槽15通过配管16,向硝化装置10送液。硝化装置10中,通过微生物活性污泥中所包含的硝化菌,上述硝化菌包含自养型氨氧化菌和亚硝酸氧化菌,将被处理水所包含的氨态氮氧化为亚硝酸或硝酸态氮(硝化工序)。在此,在配管16中存在钼化合物,其中,介由钼化合物供给泵21通过钼化合物供给配管26供给钼化合物,使钼浓度相对于被处理水成为0.025mgmo/gn以上(钼化合物供给工序)。硝化液通过配管18向脱氮装置12送液。
[0030]
脱氮装置12中,介由供氢体供给泵23通过供氢体供给配管28供给供氢体,通过微生物活性污泥中所包含的异养型脱氮菌,将硝化装置10(硝化工序)中生成的亚硝酸或硝酸态氮还原为氮气(脱氮工序)。脱氮液通过配管20向固液分离装置14送液。
[0031]
固液分离装置14中,从脱氮液的微生物活性污泥分离处理水而得到处理水(固液分离工序)。通过固液分离而得到的处理水通过配管22而排出。另一方面,通过固液分离而得到的污泥的至少一部分,介由污泥送回泵25通过污泥送回配管24而送回至配管16,与被处理水混合。污泥只要送回至固液分离装置14(固液分离工序)的前段即可,例如,可以送回至硝化装置10、脱氮装置12,也可以送回至配管18、20。通过固液分离而得到的污泥的至少一部分,可以从固液分离装置14排出到体系外部。
[0032]
本发明人等发现,在使用包含硝化菌的微生物活性污泥,上述硝化菌包含自养型氨氧化菌和亚硝酸氧化菌,处理包含氨态氮的含氮被处理水,特别是被处理水中的氮浓度例如为100mgn/l以上的高浓度的含氮被处理水的方法中,在微生物的代谢活性降低,处理速度降低的情况下,通过按照以下方式进行控制,从而使硝化菌的代谢活性大幅恢复,进而提高,能够稳定得到高处理速度,即,存在钼化合物,使钼浓度相对于被处理水成为0.025mgmo/gn以上,并且使每单位污泥的硝化速度成为0.11[kgn/(kgvss
·
天)]以上。此外,本发明人等发现,在使用包含硝化菌和异养型脱氮菌的微生物活性污泥,上述硝化菌包含自养型氨氧化菌和亚硝酸氧化菌,处理包含氨态氮的含氮被处理水,特别是被处理水中的氮浓度例如为100mgn/l以上的高浓度的含氮被处理水的方法中,在微生物的代谢活性降低,处理速度降低的情况下,通过按照以下方式进行控制,从而使硝化菌和脱氮菌的代谢活性大幅恢复,进而提高,能够稳定得到高处理速度,即,存在钼化合物,使钼浓度相对于被处理水成为0.025mgmo/gn以上,并且使每单位污泥的硝化速度成为0.11[kgn/(kgvss
·
天)]以上。
[0033]
在含氮被处理水,特别是高浓度的含氮被处理水的生物学处理中,通过钼化合物,使微生物活性污泥中的包含氨氧化菌和亚硝酸氧化菌的硝化菌的活性提高,从而即使被处理水中的氮浓度为高浓度也能够以高处理速度稳定处理。此外,在含氮被处理水,特别是高浓度的含氮被处理水的生物学处理中,通过钼化合物,不仅提高微生物活性污泥中的脱氮菌的活性,而且还提高包含氨氧化菌和亚硝酸氧化菌的硝化菌的活性,从而即使被处理水中的氮浓度为高浓度也能够以高处理速度稳定处理。
[0034]
每单位污泥的硝化速度,只要控制为0.11[kgn/(kgvss
·
天)]以上即可,优选控制为0.24[kgn/(kgvss
·
天)]以下。如果每单位污泥的硝化速度小于0.11[kgn/(kgvss
·
天)],则钼的添加效果不显著。此外,如果每单位污泥的硝化速度超过0.24[kgn/(kgvss
·
天)],则存在以下情形,硝化槽内残留氨态氮,根据槽内ph而使游离的氨浓度上升,由此导致氨氧化细菌或亚硝酸氧化细菌的活性降低,处理性能恶化。
[0035]
每单位污泥的硝化速度由处理量((被处理水氨态氮浓度-处理水氨态氮浓度[mg/l])
×
流量[m3/天])和槽内污泥量(mlss[mg/l]
×
水槽容积[m3])决定。测定被处理水氨态氮浓度和处理水氨态氮浓度、硝化装置10内的污泥浓度,调整被处理水供给泵17的流量使其成为特定的每单位污泥的处理速度即可。此外,通过钼化合物供给泵21进行相对于流入氨态氮量的钼添加量的控制即可。此时,被处理水供给泵17、流量测定装置19、钼化合物供给泵21,在硝化装置10中,作为硝化速度控制单元发挥功能,其中,按照以下方式进行控制:存在钼化合物,使钼浓度相对于被处理水成为0.025mgmo/gn以上,并且使每单位污泥的硝化速度成为0.11[kgn/(kgvss
·
天)]以上。也可以通过电连接等将被处理水供给泵17、流量测定装置19、钼化合物供给泵21与控制装置连接,进行自动控制。
[0036]
通常,在进行排水的生物学处理时,为了维持微生物的增殖和代谢反应,需要保持被处理水中的营养素平衡。作为细胞的构成成分的营养素,被称为“亲生物元素”的碳(c)、氧(o)、氮(n)、氢(h)、磷(p)成为必须成分。另外,虽然需求量比亲生物元素少,但硫(s)、钾(k)、钠(na)、钙(ca)、镁(mg)、氯(cl)、铁(fe)也是作为细胞构成要素所必需的成分,因此在被处理水中的各种元素的含量少的情况下,优选添加补给上述元素。另一方面,虽然需求量少,但也可存在参与微生物的酶代谢的微量元素,例如可举出氟(f)、硅(si)、钒(v)、铬(cr)、锰(mn)、钴(co)、镍(ni)、铜(cu)、锌(zn)、砷(as)、硒(se)、钼(mo)、碘(i)等。但是,包含这些重金属类的微量元素类的需求量非常微量,设想在被处理水中存在必要充分的量,因此通常不会从外部添加到被处理水、处理体系内。另一方面,在对从半导体产业等使用超纯水的工厂排出的排水进行生物学处理时,在设想为上述微量元素类不足的情况下,有时通过在被处理水中混合自来水、工业用水、井水等来补给。但是,在被处理水中的氮浓度比较高(例如100mgn/l以上)的情况下,有时硝化速度降低。即使在这样的状态下,在本实施方式涉及的水处理方法和水处理装置中,通过向处理体系内供给特定量的钼化合物,也能够实现处理的稳定化、高速处理。
[0037]
与被处理水中的氮成分的处理相关的反应主要分为以下。1.nh
4+
→
no
2-
(氨氧化菌)2.no
2-
→
no
3-
(亚硝酸氧化菌)3.no
3-
→
n2(脱氮菌)
[0038]
关于脱氮菌在无氧条件下的硝酸的异化还原反应(硝酸呼吸),进行生物化学研究。例如,根据非专利文献2可知,从硝酸到氮气的反应被细分为[no
3-
→
no
2-
→
no
→
n2o
→
n2],催化[no
3-
→
no
2-
]的还原反应的酶明显与钼元素相关。即,关于排水处理体系中的脱氮反应,所需量的程度不明确,但设想通过添加钼化合物,其活性提高。
[0039]
另外,通过研究阐明亚硝酸氧化菌在氧化亚硝酸时需要钼。例如,在非专利文献3中,研究了亚硝酸氧化菌即硝化杆菌(nitrobacter)的培养条件,通过添加至少10-9
m的钼,显示硝化杆菌的亚硝酸的利用以及细胞增殖上升11倍。即,关于排水处理体系中的亚硝酸氧化反应,设想通过添加钼化合物而其活性提高。
[0040]
另一方面,作为与氨氧化菌的氨氧化代谢相关的酶,已知将氨氧化而生成羟胺的氨单加氧酶(ammonium monooxygenase,amo)以及从生成的羟胺进一步生成亚硝酸的羟胺氧化还原酶(hydroxylamine oxidoreductase,hao)这2种酶有参与,但它们并不是钼参与的酶反应的报告(参照非专利文献4)。
[0041]
专利文献1中记载了以下方法:为了有效率进行硝化反应,使钴与被处理水共存,并且进一步共存钼、钙、镁成分。在专利文献1的实施例中,在钼浓度为1mgmo/l共存下(14.3mgmo/gn)验证氮浓度为70mgn/l的比较低浓度的被处理水的硝化脱氮处理试验,在硝化的污泥负荷为2.5gn/(kgmlss
·
小时)[=0.06kgn/(kgmlss
·
天)]的条件下,得到氮的除去率为90%的结果,但难以认为其得到显著的效果。
[0042]
本发明人等发现,在使用氨氧化菌和亚硝酸氧化菌共存的微生物活性污泥,处理含有特别高浓度的氮的被处理水的方法中,通过供给特定量的钼,不仅提高亚硝酸氧化反应,还能够大幅提高氨氧化菌的活性。另外,本发明人等发现,在使用含有氨氧化菌和亚硝酸氧化菌、脱氮菌的各种细菌类共存的微生物活性污泥,处理特别是含有高浓度的氮的被
处理水的方法中,通过供给特定量的钼,不仅能够提高亚硝酸氧化、脱氮(硝酸还原)反应,还能够大幅提高氨氧化菌的活性。在氨氧化菌和亚硝酸氧化菌这样的自养型细菌和能够同化有机物的脱氮菌这样的异养型细菌共存的微生物活性污泥中,包含增殖速度大于硝化菌的脱氮菌的异养型细菌在污泥中占优势。通常,设想各细菌的代谢反应独立,但在存在多个功能微生物的微生物活性污泥中,各细菌存在共存关系。虽然添加钼化合物使氨氧化活性提高的机理尚不明确,但推测可通过钼的供给使脱氮菌这类异养型细菌的代谢活性增加,因此相对导致氨氧化的活性的提高。
[0043]
在本实施方式中,作为处理对象的被处理水是包含氨态氮的含氮水,特别是含有高浓度的氨态氮的含氮水,还可以包含有机态氮。作为被处理水,例如可举出电子产业排水、金属精炼工厂排水、发电站排水等产业排水,包含在污泥处理过程中排出的消化脱离水的排水等。在此,电子产业排水包含各种化学药品,另外,虽然根据制造的产品,排水中的成分也远远不同,但作为含氮水,例如可举出晶片清洗排水等。在该排水中,除氨以外,大多包含四甲基氢氧化铵(tmah)、过氧化氢、氟离子、异丙醇(ipa)等。
[0044]
被处理水中的钼浓度,例如为0.0001mgmo/l以下。另外,在被处理水中的氮浓度优选为100mgn/l以上的情况下,更优选为400mgn/l以上的情况下,优选应用本实施方式涉及的水处理方法和水处理装置。
[0045]
在对上述含氮水进行生物学处理时,过氧化氢、氟离子等阻碍性物质对生物具有阻碍性,因此优选预先除去。作为这些阻碍性物质的处理方法,可使用现有技术,例如,在过氧化氢的处理中,可举出添加酶的方法、注入还原剂的方法、与活性炭接触的方法等。另外,在氟离子的处理中,可举出添加钙以氟化钙的形式而除去的方法、利用离子交换树脂进行处理的方法等。
[0046]
除去过氧化氢、氟离子等阻碍性物质的含氮水,优选在进行生物学处理工序的处理之前,暂时贮存在水槽中,使生物学处理工序涉及的流量、水质稳定化,并且通过碱或酸等ph调节剂调节为合适的ph(例如,ph6.5~8.0)。然后,将调整流量、水质、ph等的含氮水(被处理水)输送至生物学处理工序。
[0047]
硝化装置10中的硝化工序是向硝化部(例如硝化槽)供给被处理水,将被处理水中的铵离子等氨态氮在需氧(例如氧的存在下)的条件下氧化为亚硝酸或硝酸态氮的工序。硝化部例如连接有空气导入管,成为看向硝化部内的被处理水供给空气等含氧气体的结构。然后,在硝化部内,通过硝化菌的作用,将被处理水中的铵离子等氨态氮硝化为亚硝酸或硝酸态氮。在此,所谓硝化菌是指,将铵离子等氨态氮氧化为亚硝酸根离子的自养型氨氧化菌以及将亚硝酸根离子氧化为硝酸根离子的自养型亚硝酸氧化菌的总称。
[0048]
在被处理水中所包含的钼不足的情况下,只要从外部添加钼化合物即可。钼化合物,例如以钼化合物溶液的形式,通过钼化合物供给配管26向被处理水供给,通过将钼化合物与被处理水混合而供给到体系内。钼化合物,例如与处理的氮量呈比例地供给即可。通过以特定量供给钼化合物,能够维持高的硝化菌(氨氧化菌和亚硝酸氧化菌)和脱氮菌的活性,且进行稳定运输或者高速处理。
[0049]
作为钼化合物,例如可举出钼酸钠、钼酸钾、钼酸铵等钼酸化合物等。作为钼化合物的形态,没有特别限定,例如如果是溶液的状态,则微生物活性污泥中的细菌容易利用,例如优选预先制备并添加钼酸钠、钼酸钾等的水溶液。
[0050]
关于钼化合物的添加场所,可以向进行硝化处理前的配管16供给,也可以向混合有被处理水和微生物活性污泥的硝化装置10供给。另外,如果考虑添加的钼化合物作为送回污泥送回至比固液分离工序更靠近前段,并在体系内循环,则也可以将钼化合物供给配管与配管18、脱氮装置12连接而供给。
[0051]
在硝化装置10(硝化工序)中存在钼化合物,使钼浓度相对于被处理水成为0.025mgmo/gn以上的方式,优选使钼浓度成为0.1mgmo/gn以上的方式。作为钼浓度的上限,没有特别限制,例如为0.25mgmo/gn以下。在硝化装置10(硝化工序)中,如果钼浓度相对于被处理水小于0.025mgmo/gn,则有时不会显现硝化菌(氨氧化菌和亚硝酸氧化菌)和脱氮菌的活性维持效果。
[0052]
在硝化装置10(硝化工序)中,钼浓度相对于被处理水优选为2mgmo/l以下。如果钼浓度相对于被处理水超过2mgmo/l,则有时硝化反应受到阻碍。
[0053]
在硝化部内可以设置担载微生物的载体。作为担载微生物的载体,没有特别限定,例如优选利用塑料、聚氨酯等树脂制等载体。
[0054]
脱氮装置12中的脱氮工序,例如是向完全混合型的脱氮部(例如脱氮槽)供给供氢体,在无氧条件下将由硝化部生成的亚硝酸或硝酸态氮还原为氮气的工序。在脱氮部(例如脱氮槽)内,通过异养型细菌即脱氮菌的作用,亚硝酸或硝酸态氮被还原为氮气。在脱氮部中,为了有效率进行处理,优选设置用于在无氧条件下混合硝化液和微生物活性污泥的搅拌装置。
[0055]
脱氮部内可以设置担载微生物的载体。作为担载微生物的载体,没有特别限定,优选利用塑料、聚氨酯等树脂制等载体。
[0056]
本实施方式中使用的用于脱氮的供氢体,例如可举出甲醇、乙醇、异丙醇等醇类,乙酸等有机酸类,氢气、丙酮、葡萄糖、甲乙酮、四甲基氢氧化铵(tmah)等中的1种或多种,但并不限定于此,作为供氢体,可使用以往公知的供氢体。作为供氢体,也可以利用被处理水中所包含的有机物等。
[0057]
固液分离装置14中的固液分离工序是,将通过微生物活性污泥内的硝化菌和脱氮菌,对氮成分进行硝化和脱氮处理后得到的脱氮液分离为处理水和微生物活性污泥,得到处理水的工序。
[0058]
作为固液分离装置14,没有特别限定,例如可举出沉淀分离、加压浮上、过滤、膜分离等分离装置。在固液分离工序中,可得到处理水,并且也可得到分离后的微生物活性污泥,将微生物活性污泥的一部分作为剩余污泥抽出至体系外部,一部分例如送回至硝化装置10(硝化工序),由此可维持体系内的微生物活性污泥量。
[0059]
在脱氮装置12中添加供氢体,但是在担忧脱氮处理后残留供氢体,处理水质恶化的的情况下,可以在脱氮装置12(脱氮工序)与固液分离装置14(固液分离工序)之间设置氧化装置作为用于对供氢体进行需氧处理的氧化单元。
[0060]
图2表示上述方式的水处理装置的示例。在图2的水处理装置3中,在脱氮装置12(脱氮工序)与固液分离装置14(固液分离工序)之间具备氧化装置30。脱氮装置12的出口与氧化装置30的入口通过配管32连接,氧化装置30的出口与固液分离装置14的入口通过配管34连接。
[0061]
在脱氮装置12(脱氮工序)中得到的脱氮液通过配管32向氧化装置30送液。氧化装
置30中的氧化工序,在氧化部(例如氧化槽)对供氢体进行需氧处理。在氧化部(例如氧化槽)中,例如与硝化部相同连接有空气导入管,成为可向氧化部内的被处理水供给空气等含氧气体的结构。
[0062]
在氧化装置30中氧化处理的氧化处理液通过配管34向固液分离装置14送液,然后,与图1的水处理装置1同样进行处理。
[0063]
在被处理水中包含有机物和氮的情况下,也可以不从外部添加用于脱氮反应的供氢体,而将被处理水中的有机物作为供氢体而进行脱氮反应。
[0064]
将上述方式的水处理装置的示例示于图3。在图3的水处理装置5中,被处理水调整槽15的出口与脱氮装置12的入口介由被处理水供给泵17通过配管36连接,脱氮装置12的出口与硝化装置10的入口通过配管38连接,硝化装置10的出口与固液分离装置14的入口通过配管40连接,在固液分离装置14的处理水出口连接有配管42,固液分离装置14的污泥出口与配管36介由污泥送回泵25通过污泥送回配管44连接。在配管36上,在被处理水供给泵17的下游侧设置有用于测定被处理水的流量的流量测定装置19,在流量测定装置19的下游侧且污泥送回配管44的连接点的上游侧介由钼化合物供给泵21连接有钼化合物供给配管26。配管40和脱氮装置12通过硝化液送回配管46连接。
[0065]
在水处理装置5中,包含氨态氮的被处理水,介由被处理水供给泵17从被处理水调整槽15通过配管36向脱氮装置12送液。另一方面,从后段的硝化装置10使硝化液的至少一部分通过硝化液送回配管46向脱氮装置12送液。在此,在配管36中存在钼化合物,其中,介由钼化合物供给泵21通过钼化合物供给配管26供给钼化合物,使钼浓度相对于被处理水成为0.025mgmo/gn以上(钼化合物供给工序)。
[0066]
在硝化装置10中,通过微生物活性污泥中所包含的硝化菌,上述硝化菌包含自养型氨氧化菌和亚硝酸氧化菌,将被处理水所包含的氨态氮氧化为亚硝酸或硝酸态氮(硝化工序)。在脱氮装置12中,通过微生物活性污泥中所包含的异养型脱氮菌,将硝化装置10(硝化工序)中生成的亚硝酸或硝酸态氮还原为氮气(脱氮工序)。脱氮液通过配管38向硝化装置10送液,硝化液的至少一部分通过配管40向固液分离装置14送液。然后,与图1的水处理装置1同样进行处理。
[0067]
在进一步降低处理水的氮浓度的情况下,在图3的水处理装置5中的硝化装置10与固液分离装置14之间,还可以具备后脱氮装置作为后脱氮单元,具备氧化装置作为氧化单元。
[0068]
将上述方式的水处理装置的示例示于图4。图4的水处理装置7还具备后脱氮装置48作为后脱氮单元以及具备氧化装置30作为氧化单元。硝化装置10的出口与后脱氮装置48的入口通过配管50连接,后脱氮装置48的出口与氧化装置30的入口通过配管52连接,氧化装置30的出口与固液分离装置14的入口通过配管54连接。在后脱氮装置48中,介由供氢体供给泵23连接有供氢体供给配管28。配管50与脱氮装置12通过硝化液送回配管46连接。
[0069]
在水处理装置7中,包含氨态氮的被处理水介由被处理水供给泵17从被处理水调整槽15通过配管36向脱氮装置12送液。另一方面,从后段的硝化装置10,硝化液的至少一部分通过硝化液送回配管46向脱氮装置12送液。在此,在配管36中存在钼化合物,介由钼化合物供给泵21通过钼化合物供给配管26供给钼化合物,使钼浓度相对于被处理水成为0.025mgmo/gn以上(钼化合物供给工序)。
[0070]
在硝化装置10中,通过微生物活性污泥中所包含的硝化菌,上述硝化菌包含自养型氨氧化菌和亚硝酸氧化菌,将被处理水所包含的氨态氮氧化为亚硝酸或硝酸态氮(硝化工序)。在脱氮装置12中,通过微生物活性污泥中所包含的异养型脱氮菌,将硝化装置10(硝化工序)中生成的亚硝酸或硝酸态氮还原为氮气(脱氮工序)。脱氮液通过配管38向硝化装置10送液,硝化液的至少一部分通过配管50向后脱氮装置48送液,在后脱氮装置48中,通过脱氮菌,将硝化装置10(硝化工序)中生成的亚硝酸或硝酸态氮还原为氮气(脱氮工序)。脱氮液通过配管52向氧化装置30送液。然后,与图2的水处理装置3同样进行处理。硝化液的至少一部分通过硝化液送回配管46向脱氮装置12送液。
[0071]
在脱氮工序中,优选对供氢体的添加量赋予时间变动,以使在处理水的水力停留时间内的供氢体的最大浓度与最小浓度之差为50mgtoc/l以上,由此使包含硝化菌和脱氮菌的微生物活性污泥颗粒化。通过对在脱氮反应中进行添加的供氢体的浓度赋予变动,能够容易形成脱氮菌自造粒而成的颗粒。
[0072]
此外,通过使该颗粒在进行硝化、脱氮的含氮水的处理系统内循环,从而能够将硝化菌等全部的菌群颗粒化,以实质上相同的颗粒处理含氮被处理水的处理装置整体。
[0073]
此外,在增大脱氮工序中的供氢体的最大浓度与最小浓度之差,且高效进行微生物活性污泥的颗粒化的情况下,脱氮工序可以是至少包含第一脱氮工序和第二脱氮工序的2个以上的工序。脱氮工序至少包含第一脱氮工序和第二脱氮工序,在脱氮工序中,可以至少在第一脱氮工序中供给供氢体,使在第二脱氮工序中的处理水的水力停留时间内的第一脱氮工序中的供氢体的最大浓度与第二脱氮工序中的供氢体的最小浓度之差为50mgtoc/l以上。
[0074]
将上述方式的水处理装置的示例示于图5。图5的水处理装置9具备第一脱氮装置58和第二脱氮装置60作为脱氮单元。硝化装置10的出口与第一脱氮装置58的入口通过配管62连接,第一脱氮装置58的出口与第二脱氮装置60的入口通过配管64连接,第二脱氮装置60的出口与氧化装置30的入口通过配管66连接。
[0075]
硝化装置10中得到的硝化液,通过配管62向第一脱氮装置58送液。在第一脱氮装置58中,介由供氢体供给泵23通过供氢体供给配管28供给供氢体,与微生物活性污泥中所包含的异养型脱氮菌接触后,混合液通过配管64向第二脱氮装置60送液,在第二脱氮装置60中,通过脱氮菌,将硝化装置10(硝化工序)中生成的亚硝酸或硝酸态氮还原为氮气(脱氮工序)。脱氮液通过配管66向氧化装置30送液。然后,与图2的水处理装置3同样进行处理。
[0076]
在图1的水处理装置1中,可以在被处理水调整槽和处理水槽中设置测定氨态氮的浓度的氨态氮浓度测定装置,测定被处理水和处理水的氨态氮的浓度。
[0077]
将上述方式的水处理装置的示例示于图6。图6的水处理装置2可以具备贮存处理水的处理水槽67,配管22与处理水槽67的入口连接。在被处理水调整槽15和处理水槽67中,分别设置氨态氮浓度测定装置63、65作为氨态氮浓度测定单元。氨态氮浓度测定装置65可以不设置在处理水槽67中,而设置在硝化装置10中。由此,可掌握硝化装置10中的处理量。
[0078]
通过氨态氮浓度测定装置63测定被处理水的氨态氮浓度,通过氨态氮浓度测定装置65测定处理水的氨态氮浓度,测定硝化装置10内的污泥浓度,调整被处理水供给泵17的流量使其成为特定的每单位污泥的处理速度即可。此外,通过钼化合物供给泵21进行钼添加量相对于流入氮量的控制即可。此时,被处理水供给泵17、流量测定装置19、钼化合物供
给泵21、氨态氮浓度测定装置63、65作为硝化速度控制单元发挥功能,其中,按照以下方式进行控制:在硝化装置10中存在钼化合物,使钼浓度相对于被处理水成为0.025mgmo/gn以上,并且使每单位污泥的硝化速度成为0.11[kgn/(kgvss
·
天)]以上。通过该结构,能够追随被处理水的浓度变动。也可以通过电连接等将被处理水供给泵17、流量测定装置19、钼化合物供给泵21、氨态氮浓度测定装置63、65与控制装置连接,进行自动控制。
[0079]
在图1的水处理装置1中,可以在硝化装置和脱氮装置中使用载体。
[0080]
将上述方式的水处理装置的示例示于图7。在图7的水处理装置4中,在硝化装置10中,载体68保持在水槽内,在脱氮装置12中,载体70保持在水槽内,在各水槽的流出口设置有抑制载体68、70流出的丝网72、74。
[0081]
硝化装置10内的污泥量的测定,根据浮游中的污泥量的测定和载体的填充量来计算。由于附着于每单位载体的污泥量大致恒定,因此通过预先测定每单位载体的污泥附着量,能够进行测定。
[0082]
在图7的水处理装置4中,也可以不设置固液分离装置,而制成不进行污泥送回的结构。
[0083]
将上述方式的水处理装置的示例示于图8。图8的水处理装置6在脱氮装置12的后段具备氧化装置30。在氧化装置30中,载体76保持在水槽内,在水槽的流出口设置有抑制载体76流出的丝网78。
[0084]
在图8的水处理装置6中,脱氮装置12的出口与氧化装置30的入口通过配管80连接,在氧化装置30的处理水出口连接有配管82。
[0085]
脱氮装置12(脱氮工序)中得到的脱氮液通过配管80向氧化装置30送液。氧化装置30中的氧化工序,通过氧化部(例如氧化槽)对供氢体进行需氧处理。在氧化部(例如氧化槽)中,例如与硝化部相同连接有空气导入管,成为能够向氧化部内的被处理水供给空气等含氧气体的结构。
[0086]
虽然担忧在脱氮装置12中添加供氢体,脱氮处理后供氢体残留,处理水质恶化,但是在氧化装置30中,对供氢体进行需氧处理。实施例
[0087]
以下,举出实施例和比较例,更具体说明本发明,但本发明并不限定于以下实施例。
[0088]
以下,示出使用连续通水试验机的实施例和比较例。应予说明,全部在将室温控制在20℃的条件下实施。
[0089]
<实施例1>在实施例1中,使用图5所示的水处理装置9的结构的台式秤试验机。使硝化菌和脱氮菌颗粒化,实施模拟排水的硝化脱氮处理试验。作为模拟排水,使用按照以下方式制备的排水,即,在纯水中溶解氨态氮,使其成为400mgn/l,添加作为其它营养源的磷酸和微量元素药液。本试验中使用的微量元素药液不含钼。用于脱氮的供氢体使用甲醇,将其间歇添加至第一脱氮槽,使第一脱氮槽内的最大甲醇浓度与第二脱氮槽内的最小甲醇浓度之差成为50mgtoc/l以上。在硝化槽、第一脱氮槽、第二脱氮槽中设置ph控制器,使用盐酸或氢氧化钠将槽内ph调整为7~7.5。将从固液分离槽得到的浓缩污泥送回至硝化槽。从第0天至第45天不实施钼添加(比较例1),从第46天起开始添加钼化合物(钼酸钠),使其相对于被处理水为
0.1mgmo/l(实施例1)。钼添加浓度相对于被处理水的氮浓度为0.25mgmo/gn的条件。将结果示于图9、10。图9表示硝化槽容积负荷[kgn/(m3·
d)]、硝化槽的氨态氮浓度[mgn/l]的推移,图10表示脱氮槽容积负荷[kgn/(m3·
d)]、处理水的总氮浓度[mgn/l]相对于经过天数[天]的推移。
[0090]
在初期的比较例1中,以硝化槽中的容积负荷为0.2kgn/(m3·
d)的方式开始通水,硝化槽中氨态氮残留5~60mgn/l,无法使负荷上升,硝化速度停滞在0.15~0.25kgn/(m3·
d)。伴随硝化速度的停滞,脱氮速度也停滞在0.3~0.5kgn/(m3·
d)。在比较例1期间,能够稳定运转的每单位污泥的处理速度在硝化中为0.05kgn/(kgvss
·
d)。
[0091]
接着,开始向被处理水添加钼,然后可确认到处理速度的上升,最大可确认到1.1kgn/(m3·
d)的硝化速度。应予说明,在实施例1期间,硝化槽的氨态氮通常以1mgn/l以下进行推移。伴随硝化速度的上升,也确认到脱氮速度的上升,最大达到2.2kgn/(m3·
d)。在比较例1期间,可确认到表示污泥活性的每单位污泥的处理速度在硝化中以0.24kgn/(kgvss
·
d)稳定运转,在脱氮中以0.54kgn/(kgvss
·
d)稳定运转。
[0092]
<比较例2>在比较例2中,使用图5所示的水处理装置9的结构的台式秤试验机进行连续通水试验。作为模拟排水,使用按照以下方式制备的排水,即,在纯水中调整氨态氮,使其成为800mgn/l,添加其他磷酸和微量元素药液(不含钼)。出于补给微量元素的目的,从第120天至第215天添加不含钼的井水(钼浓度:0.0001mgmo/l以下(检测限以下))进行补给,从第216天至第280天以被处理水的10%流量添加包含钼的工业用水而进行补给。应予说明,工业用水中的钼浓度为0.0006mgmo/l。井水和工业用水中的钼浓度使用icp质谱分析法(icp-ms)来测定。
[0093]
将硝化槽容积负荷[kgn/(m3·
d)]与硝化槽的残留氨态氮浓度[mgn/l]的推移示于图11,将脱氮槽容积负荷[kgn/(m3·
d)]与处理水的总氮浓度[mgn/l]的推移示于图12。由图11可知,虽然使硝化槽容积负荷上升至0.8kgn/(m3·
d),但是在第169天氨态氮浓度残留41mgn/l,在第171天上升至130mgn/l。然后,硝化性能还不稳定,有时在硝化槽内残留10~40mgn/l,无法稳定运转。此外,试验期间中的硝化活性为0.02~0.075kgn/(kgvss
·
d)。伴随硝化的不稳定性,脱氮处理也不稳定,处理水tn最大上升至150mgn/l左右。
[0094]
<实施例2>使用与比较例2相同条件的模拟排水、试验装置,通过连续通水试验验证钼化合物溶液的添加影响。作为钼添加浓度,相对于被处理水的氨态氮浓度800mgn/l,设为0.02mgmo/l,从第175天开始添加。钼添加浓度相对于被处理水的氮浓度为0.025mgmo/gn的条件。
[0095]
将硝化槽容积负荷[kgn/(m3·
d)]和硝化槽的残留氨态氮浓度[mgn/l]的推移示于图13,将脱氮槽容积负荷[kgn/(m3·
d)]和处理水的总氮浓度[mgn/l]的推移示于图14。其结果,不添加钼期间,硝化槽容积负荷没有上升,在第175天55mgn/l的氨态氮残留。从第175天起开始mo化合物的添加,其结果,可确认到氨态氮浓度的降低,即使使容积负荷上升至0.8~0.9kgn/(m3·
d),也能够稳定运转。钼添加前的硝化活性最大为0.05kgn/(kgvss
·
d),钼添加开始后的硝化活性上升至0.11kgn/(kgvss
·
d)。关于脱氮,作为脱氮槽容积负荷,也上升至1.4kgn/(m3·
d)。
[0096]
<实施例3>使用与实施例2相同条件的模拟排水、试验装置,通过连续通水试验验证钼化合物的添
加影响。作为添加浓度,相对于被处理水氨态氮浓度800mgn/l,设为0.1mgmo/l,从第343天起开始添加。钼添加浓度相对于被处理水的氮浓度为0.125mgmo/gn的条件。
[0097]
将硝化槽容积负荷[kgn/(m3·
d)]和硝化槽的残留氨态氮浓度[mgn/l]的推移示于图15,将脱氮槽容积负荷[kgn/(m3·
d)]和处理水的总氮浓度[mgn/l]的推移示于图16。其结果,不添加钼期间,在脱氮槽中检测到70~80mg/l左右的硝酸态氮,因此无法提高负荷,硝化槽容积负荷停滞在0.25kgn/(m3·
d)左右。从第343天起开始添加钼溶液,尝试负荷的上升。在第346天在硝化槽检测到氨态氮为37mgn/l,然后观察到氨态氮浓度的降低。虽然使硝化槽容积负荷上升至0.86kgn/(m3·
d),但在硝化槽中没有检测到氨态氮,在脱氮槽中处理水tn也以5mgn/l以下推移。钼添加前的硝化活性停滞在0.05~0.06kgn/(kgvss
·
d),但在钼添加开始后,观察到活性的提高,可确认到上升至0.2kgn/(kgvss
·
d)。
[0098]
将以上的结果汇总示于图17。由图17可知,在硝化工序中存在钼化合物,优选使钼浓度相对于被处理水成为0.025mgmo/gn以上。
[0099]
如此,通过实施例的方法,在包含氨态氮的被处理水的生物学处理中,即使被处理水中的氮浓度为高浓度,也能够以高处理速度稳定进行处理。
[0100]
以下,通过分批试验来评价钼化合物的添加浓度对氨氧化反应和脱氮反应产生的阻碍影响。
[0101]
[脱氮中的钼添加对脱氮的影响试验(分批试验)]使用硝化脱氮污泥,通过使用模拟排水的分批试验验证钼添加对脱氮反应产生的影响。实验方法的具体方法记载如下。
[0102]
1.作为分批试验中使用的模拟排水,使用在井水中添加硝酸态离子和磷酸态磷而得到的排水,使硝酸态离子成为60mgn/l,使磷酸态磷成为1mgp/l。应予说明,模拟排水中的含钼浓度为0.0001mg/l以下。2.利用纯水清洗预先作为供氢体的利用甲醇熟化的污泥,将得到的物质悬浮于模拟排水中,分注至5个烧杯中。3.在污泥与模拟排水的混合液中,将钼酸钠溶液添加至各烧杯中,并进行搅拌,使其成为0mgmo/l、1mgmo/l、5mgmo/l、10mgmo/l、20mgmo/l。4.一边搅拌一边将作为供氢体的甲醇各以相同量添加到各烧杯中,评价硝酸的减少速度。
[0103]
脱氮活性试验的结果,可确认到由硝酸减少速度和烧杯内的污泥量算出的脱氮活性,在未添加mo的系列中为0.43gn/gss/天,在mo浓度为1mgmo/l的系列中为0.46,在5mgmo/l的系列中为0.45gn/gss/天,在10mgmo/l的系列中为0.42gn/gss/天,在20mgmo/l的系列中为0.41gn/gss/天,与未添加mo的系列相比微少,但在mo浓度为1mgmo/l的系列中活性提高8%,在5mgmo/l的系列中活性提高5%。另一方面,在将mo浓度添加为20mgmo/l的高浓度的系列中,与脱氮活性最高的mo浓度1mgmo/l的系列相比,仅确认到约10%的活性降低,未确认到mo对脱氮的显著阻碍。
[0104]
[mo添加对氨氧化的影响试验(分批试验)]使用硝化脱氮污泥,通过使用模拟排水的分批试验验证钼添加对氨氧化反应产生的影响。实验方法的具体方法记载如下。
[0105]
1.作为分批试验中使用的模拟排水,使用在井水中添加氨态离子和磷酸态磷而得
到的排水,使氨态离子为60mgn/l,使磷酸态磷为1mgp/l。应予说明,模拟排水中的含钼浓度为0.0001mg/l以下。2.利用纯水清洗供试污泥,将得到的物质悬浮于模拟排水中,分注至5个烧杯中。3.在污泥和模拟排水的混合液中,将钼酸钠溶液添加到各烧杯中,分别开始曝气,其中,使钼酸钠溶液成为0mgmo/l、0.1mgmo/l、0.5mgmo/l、2mgmo/l、10mgmo/l。4.评价各个氨态氮浓度的减少速度。
[0106]
氨氧化活性试验的结果,由氨减少速度和烧杯内的污泥量算出的氨氧化活性,在未添加mo的系列中为0.18gn/gss/天,在mo浓度为0.1mgmo/l的系列中为0.13gn/gss/天,在0.5mgmo/l的系列中为0.13gn/gss/天,在2mgmo/l的系列中为0.13gn/gss/天,在10mgmo/l的系列中为0.10gn/gss/天,未添加mo的系列的氨氧化活性最高,10mgmo/l的系列的氨氧化活性最低。根据该分批试验结果,认为为了抑制钼浓度对氨氧化反应的阻碍性,优选设为2mgmo/l以下。符号说明
[0107]
1、2、3、4、5、6、7、9:水处理装置、10:硝化装置、12:脱氮装置、14:固液分离装置、15:被处理水调整槽、16、18、20、22、32、34、36、38、40、42、50、52、54、62、64、66、80、82:配管、17:被处理水供给泵、19:流量测定装置、21:钼化合物供给泵、23:供氢体供给泵、24、44:污泥送回配管、25:污泥送回泵、26:钼化合物供给配管、28:供氢体供给配管、30:氧化装置、46:硝化液送回配管、48:后脱氮装置、58:第一脱氮装置、60:第二脱氮装置、63、65:氨态氮浓度测定装置、67:处理水槽、68、70、76:载体、72、74、78:丝网。