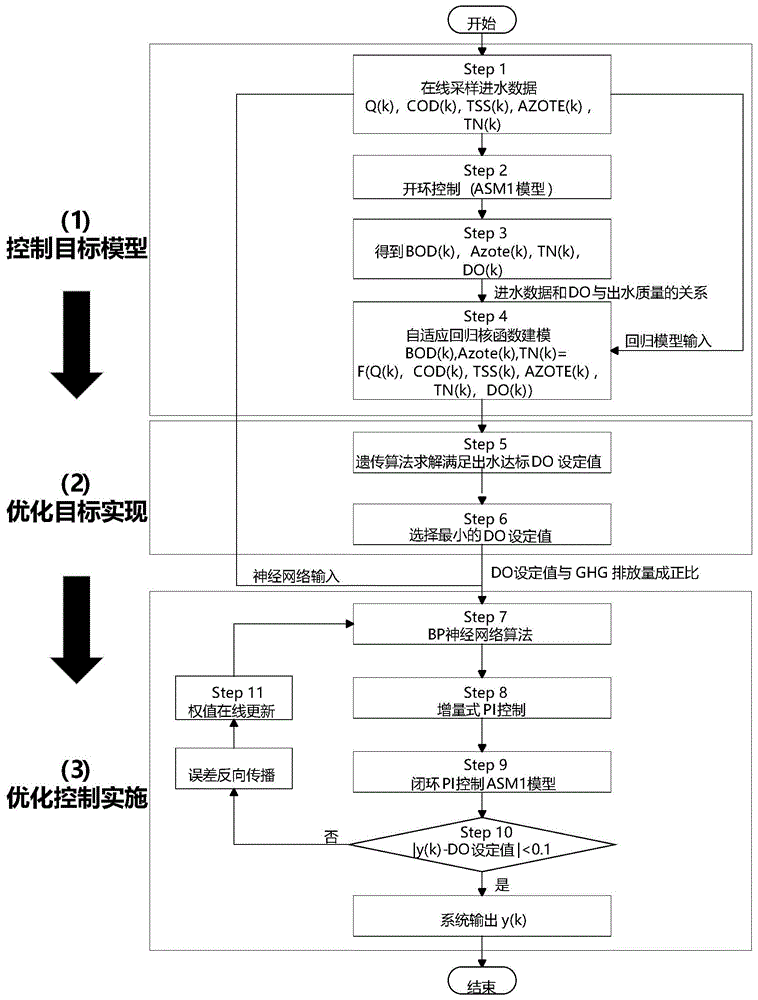
本发明涉及造纸污水生化处理过程溶解氧浓度控制及ghg(greenhousegas,温室气体)排放的
技术领域:
,具体涉及一种用于造纸污水处理ghg减排的溶解氧分层优化控制方法。
背景技术:
:造纸工业是重要的水资源消耗型行业,同时产生大量的工业污水。对造纸污水进行活性污泥法处理过程中,会产生大量的ghg,包括co2、ch4和n2o。ghg排放至大气,形成造纸工业“隐形”的二次污染。造纸工业正在面临巨大的ghg减排压力,对ghg的排放控制需求十分迫切。在污水处理过程实现ghg减排的研究中,常采用新的污水处理工艺代替活性污泥法处理工艺,但是这些新工艺具有处理成本较高和化学品残留的缺点,无法替代活性污泥法的大规模应用。利用自动控制系统实现ghg减排是可行的途径,但是由于缺乏ghg在线监测设备和对ghg排放机理的研究,目前污水处理过程的自动控制系统都没有包含对ghg排放的控制。溶解氧浓度是污水活性污泥法处理过程中的主要工艺参数,对出水水质、运行成本和ghg排放都有较大的影响,是影响ghg排放的重要因素。过高的溶解氧浓度使得曝气机耗电产生的ghg增加,过低的溶解氧浓度又会引起反硝化过程大量产生n2o。目前,溶解氧控制手段已经普遍应用于污水处理过程,其控制目标主要集中在降低运行成本和提高出水质量,将ghg排放量纳入控制系统作为控制目标,可以实现对ghg减排的优化控制。因此,基于ghg排放量的在线监测模型,针对ghg排放量随着曝气量线性增加的特点,采用分层优化控制的思想,提出了一种基于溶解氧浓度的动态优化控制策略,以减少ghg的排放。通过建立回归核函数模型来描述出水质量与进水特征和溶解氧浓度之间的关系,为优化控制系统提供控制目标模型;采用遗传算法寻找溶解氧浓度的优化设定值;采用bp-pi(backpropagationneuralnetwork-proportional-integralcontrol,反向传播神经网络比例积分控制)控制方案对优化设定值进行跟踪控制,以实现在出水质量达标的同时有效减少ghg的排放量。技术实现要素:本发明的目的是为了解决现有技术中的上述缺陷,提供一种用于造纸污水处理ghg减排的溶解氧分层优化控制方法,目的在于将ghg减排纳入控制系统的优化目标,采用分层优化控制,通过调节造纸污水a/o(anoxic/oxic,厌氧/好氧)处理工艺过程的溶解氧浓度,在出水水质达标的基础上,实现ghg的减排。本发明的目的可以通过采取如下技术方案达到:一种用于造纸污水处理ghg减排的溶解氧分层优化控制方法,所述的方法包括以下步骤:s1、在线采集进水数据,开环输入asm1(activatedsludgemodelno.1,活性污泥1号模型)仿真模型,得到出水bod、氨氮、总氮浓度和曝气过程溶解氧浓度;s2、根据采集的进水数据和溶解氧浓度,采用自适应回归核函数,建立出水bod(biochemicaloxygendemand,生化需氧量)、氨氮和总氮浓度的预测模型,作为出水约束层;s3、采用遗传算法,求解在满足出水指标的前提下实现ghg减排的溶解氧浓度优化设定值,建立优化设定层;s4、根据优化的溶解氧浓度设定值,采用bp神经网络优化pi控制器参数,对溶解氧浓度进行跟踪控制,并分析溶解氧浓度分层优化控制下的ghg减排效果。进一步地,所述的步骤s1中,所采集的进水数据来自在线造纸污水a/o处理工艺自动监控系统,分别为:进水流量、cod(chemicaloxygendemand,化学需氧量)、tss(totalsuspendedsolids,总悬浮固体)、氨氮和总氮;为了符合asm1仿真模型的变量设定,将进水数据中的cod、总氮组分分别划分为7个变量:快速可生物降解基质ss、溶解性不可降解有机物si、慢速可生物降解基质xs、颗粒性不可生物降解有机物xi、硝态氮或亚硝态氮sno、颗粒性可生物降解有机氮xnd和溶解性可生物降解有机氮snd;asm1仿真模型的输入变量为:进水流量、tss、快速可生物降解基质ss、溶解性不可降解有机物si、慢速可生物降解基质xs、颗粒性不可生物降解有机物xi、活性异养微生物xbh、活性自养微生物xba、颗粒性可生物降解有机氮xnd、微生物衰减产生的惰性颗粒物质xp、和nh3的总和snh、溶解氧so、硝态氮或亚硝态氮sno、溶解性可生物降解有机氮snd和碱度salk,输出变量为:cod、bod、氨氮、总氮和tss;出水bod、氨氮和总氮浓度的计算方法如下:bod5=0.75·(xs,e+xi,e+xbh,e+xba,e+xp,e)(1)azote=snh,e+snd,e+xnd,e+ixb·(xbh,e+xba,e)+ixp·(xi,e+xp,e)(2)tn=sno,e+azote(3)其中,xs,e代表出水的慢速可生物降解基质(g/m3),xi,e代表出水的颗粒性不可生物降解有机物(g/m3),xbh,e代表出水的活性异养微生物(g/m3),xba,e代表出水的活性自养微生物(g/m3),xp,e代表出水的微生物衰减产生的惰性颗粒物质(g/m3),xnd,e代表出水的颗粒性可生物降解有机氮(g/m3),snh,e代表出水的nh4+和nh3(g/m3),snd,e代表出水的溶解性可生物降解有机氮(g/m3),sno,e代表出水的硝态氮或亚硝态氮(g/m3),ixb代表n在生物量cod中的比例(gn/g生物量cod),ixp代表n在颗粒物质cod中的比例(gn/颗粒物质cod);出水bod、氨氮、总氮浓度和曝气过程溶解氧浓度是基于asm1仿真模型在开环控制曝气量恒定,即氧传递系数kla=10h-1的情况下计算得到的。进一步地,所述的步骤s2中,自适应回归核函数模型的核函数形式为高斯核函数,模型输入变量为:进水流量、cod、tss、氨氮、总氮浓度和曝气过程溶解氧浓度,输出变量为:出水bod、氨氮和总氮浓度;在回归过程中,设置误差为0.001-0.0005,经过迭代,分别得到出水bod值、氨氮和总氮浓度的回归预测模型;出水bod、氨氮和总氮浓度预测模型的输入与输出之间的关系如下:bod5=f1(qin,codin,tssin,azotein,tnin,do)(4)azote=f2(qin,codin,tssin,azotein,tnin,do)(5)tn=f3(qin,codin,tssin,azotein,tnin,do)(6)其中,qin为进水流量(m3/h),codin为进水化学需氧量浓度(g/m3),tssin为进水总悬浮固体浓度(g/m3),azotein为进水氨氮浓度(g/m3),tnin为进水总氮浓度(g/m3),do为溶解氧浓度(g/m3)。进一步地,所述的步骤s3中,遗传算法的初始种群规模为50-100,最大进化代数为1000-5000,个体基因数为5,变异率为0.1-0.7,交叉率为0.3-0.9;所述的优化设定层,是指利用遗传算法分别对步骤s2中出水bod、氨氮和总氮浓度的预测模型进行求解,获得分别满足出水bod、氨氮和总氮限值的最低溶解氧浓度设定值,然后选择其中的最大值作为溶解氧浓度优化设定值,这个设定值同时满足三个出水排放指标(出水bod、氨氮和总氮浓度);构建优化设定层的原因从两方面阐述,一方面,同一工况下,即开环控制时曝气量恒定为10h-1时,闭环控制中的溶解氧浓度设定值与出水质量呈正相关;另一方面,溶解氧浓度越高,ghg排放总量越大;因此步骤s2所构建的优化设定层可以在满足出水限值的同时,达到ghg减排的效果。进一步地,所述的步骤s4中,bp神经网络的层数为3,输入层神经元个数为7,隐含层神经元个数为18,输出层神经元个数为2,输入层变量为:溶解氧浓度优化设定值、当前溶解氧浓度、进水流量、cod、tss、氨氮和总氮,输出层变量为:pi控制器参数kp和ki;所述的溶解氧浓度跟踪控制,首先构建以溶解氧浓度优化设定值为控制目标的bp神经网络,将从之前步骤中获得的进水数据、溶解氧浓度优化设定值和当前溶解氧浓度作为bp神经网络的7个输入,得到优化的pi控制器参数,然后应用增量式pi控制,对溶解氧浓度进行控制,得到控制器的输出,即曝气量kla值,通过曝气机对造纸污水a/o处理工艺过程进行闭环控制,将溶解氧浓度控制在优化的设定值上,从而实现溶解氧浓度的优化跟踪控制。本发明相对于现有技术具有如下的优点及效果:1、针对造纸污水a/o处理工艺过程中溶解氧对ghg排放的显著影响作用,将溶解氧的优化控制思想应用到ghg减排中,建立了一种用于造纸污水生化处理中ghg减排的溶解氧分层优化控制方法。2、提供了一种基于动态溶解氧浓度设定值的优化控制方案,整个优化控制分为出水约束层、优化设定层和跟踪控制层三个模块,通过控制溶解氧浓度,在出水水质达标的基础上,实现ghg的减排。3、通过基于动态溶解氧浓度设定值的分层优化控制,可以为造纸污水生化处理过程中ghg排放量的减少提供技术支持和方法指导。附图说明图1是造纸污水a/o处理工艺过程akrbp-pi优化控制流程图;图2是造纸污水a/o处理工艺过程140个批次进水数据;图3是造纸污水a/o处理工艺过程开环仿真实验测量的溶解氧浓度(曝气量恒定为10h-1);图4(a)是140个批次的出水bod浓度的回归预测结果;图4(b)是140个批次的出水氨氮浓度的回归预测结果;图4(c)是140个批次的出水总氮浓度的回归预测结果;图5(a)是采用遗传算法求解akr-bod模型所得的溶解氧浓度优化设定值;图5(b)是采用遗传算法求解akr-氨氮模型所得的溶解氧浓度优化设定值;图5(c)是采用遗传算法求解akr-总氮模型所得的溶解氧浓度优化设定值;图5(d)是采用遗传算法求解akr模型所得的溶解氧浓度优化设定值;图6是用于造纸污水a/o处理工艺过程中ghg减排的溶解氧分层优化控制方案;图7是造纸污水a/o处理工艺过程实施akrbp-pi分层优化控制的溶解氧浓度设定值与测量值;图8是造纸污水a/o处理工艺过程采用不同控制方案的kla变化;图9(a)是造纸污水a/o处理工艺过程采用不同控制方案的出水cod变化;图9(b)是造纸污水a/o处理工艺过程采用不同控制方案的出水bod变化;图9(c)是造纸污水a/o处理工艺过程采用不同控制方案的出水氨氮变化;图9(d)是造纸污水a/o处理工艺过程采用不同控制方案的出水总氮变化;图9(e)是造纸污水a/o处理工艺过程采用不同控制方案的出水tss变化;图10(a)是造纸污水a/o处理工艺过程采用不同控制方案的ghg直接排放量;图10(b)是造纸污水a/o处理工艺过程采用不同控制方案的ghg间接排放量;图10(c)是造纸污水a/o处理工艺过程采用不同控制方案的ghg总排放量;图11(a)是造纸污水a/o处理工艺过程采用不同控制方案的各ghg直接排放源(内源性衰变)的排放量;图11(b)是造纸污水a/o处理工艺过程采用不同控制方案的各ghg直接排放源(bod去除)的排放量;图11(c)是造纸污水a/o处理工艺过程采用不同控制方案的各ghg直接排放源(硝化过程)的排放量;图11(d)是造纸污水a/o处理工艺过程采用不同控制方案的各ghg直接排放源(反硝化过程)的排放量;图12(a)是造纸污水a/o处理工艺过程采用不同控制方案的各ghg间接排放源(曝气机耗电)的排放量;图12(b)是造纸污水a/o处理工艺过程采用不同控制方案的各ghg间接排放源(水泵耗电)的排放量;图12(c)是造纸污水a/o处理工艺过程采用不同控制方案的各ghg间接排放源(化学品添加)的排放量;图12(d)是造纸污水a/o处理工艺过程采用不同控制方案的各ghg间接排放源(污泥处理)的排放量;图13是造纸污水a/o处理工艺过程采用不同控制方案的各ghg排放源的减排量。具体实施方式为使本发明实施例的目的、技术方案和优点更加清楚,下面将结合本发明实施例中的附图,对本发明实施例中的技术方案进行清楚、完整地描述,显然,所描述的实施例是本发明一部分实施例,而不是全部的实施例。基于本发明中的实施例,本领域普通技术人员在没有做出创造性劳动前提下所获得的所有其他实施例,都属于本发明保护的范围。实施例本实施例公开了一种用于造纸污水处理ghg减排的溶解氧分层优化控制方法,控制流程如图1所示,该方法具体包括以下步骤:步骤s1、在线采集进水数据,开环输入asm1仿真模型,得到出水bod、氨氮、总氮浓度和曝气过程溶解氧浓度;该步骤具体如下:所采集的进水数据来源于在线造纸污水a/o处理工艺自动监控系统,共有140个批次,包括:进水流量、cod、tss、氨氮和总氮;进水数据的变化曲线图如图2所示;为了符合asm1模型的变量设定,对进水数据中cod和总氮组分进行划分处理,划分方法如下:将cod划分为快速可生物降解基质ss、溶解性不可降解有机物si、慢速可生物降解基质xs和颗粒性不可生物降解有机物xi四种成分,分别占cod组分的18.11%、4.11%、19.97%和57.81%;将总氮划分为硝态氮或亚硝态氮sno、颗粒性可生物降解有机氮xnd和溶解性可生物降解有机氮snd三种成分,分别占总氮组分的2.23%、91.63%和6.14%;asm1仿真模型的输入变量为:进水流量、tss、快速可生物降解基质ss、溶解性不可降解有机物si、慢速可生物降解基质xs、颗粒性不可生物降解有机物xi、活性异养微生物xbh、活性自养微生物xba、颗粒性可生物降解有机氮xnd、微生物衰减产生的惰性颗粒物质xp、nh4+和nh3的总和snh、溶解氧so、硝态氮或亚硝态氮sno、溶解性可生物降解有机氮snd和碱度salk,输出变量为:cod、bod、氨氮、总氮和tss;出水bod、氨氮和总氮浓度的计算方法如下:bod5=0.75·(xs,e+xi,e+xbh,e+xba,e+xp,e)(7)azote=snh,e+snd,e+xnd,e+ixb·(xbh,e+xba,e)+ixp·(xi,e+xp,e)(8)tn=sno,e+azote(9)其中,xs,e代表出水的慢速可生物降解基质(g/m3),xi,e代表出水的颗粒性不可生物降解有机物(g/m3),xbh,e代表出水的活性异养微生物(g/m3),xba,e代表出水的活性自养微生物(g/m3),xp,e代表出水的微生物衰减产生的惰性颗粒物质(g/m3),xnd,e代表出水的颗粒性可生物降解有机氮(g/m3),snh,e代表出水的和nh3(g/m3),snd,e代表出水的溶解性可生物降解有机氮(g/m3),sno,e代表出水的硝态氮或亚硝态氮(g/m3),ixb代表n在生物量cod中的比例(gn/g生物量cod),ixp代表n在颗粒物质cod中的比例(gn/颗粒物质cod);将上述经过处理的进水数据输入曝气量恒定(kla=10h-1)的开环asm1仿真模型,模拟造纸污水a/o处理工艺过程,得到出水bod、氨氮、总氮浓度和曝气过程溶解氧浓度;溶解氧浓度的变化曲线(曝气量恒定为10h-1)如图3所示,结合图2的进水特征曲线可以看出,曝气过程溶解氧浓度受进水变量的影响,在曝气量恒定的情况下,进水流量和污染物浓度降低,相应的溶解氧浓度会升高,如第120批次。步骤s2、根据采集的进水数据和溶解氧浓度,采用自适应回归核函数,建立出水bod、氨氮和总氮浓度的预测模型,作为出水约束层;该步骤具体如下:从步骤s1可以看出,出水的bod、氨氮和总氮浓度与xs、xi、xp、xbh、xba、snh、snd和sno变量相关,在实际污水处理过程中,这些变量是不可测的;一方面,出水水质强烈依赖于进水特征以及曝气过程溶解氧浓度,受进水变量和曝气量的影响而变化;另一方面,xs、xi、xp、xbh、xba是tss和cod的成分,snh、snd和sno是氨氮和总氮的主要组成部分;因此,根据步骤s1的开环仿真结果,将进水流量、cod、tss、氨氮、总氮浓度和曝气过程溶解氧浓度作为输入变量,建立出水bod、氨氮和总氮浓度回归预测模型;回归预测模型的建立方法及预测结果如下:自适应回归核函数建模:自适应回归核函数模型的核函数形式为高斯核函数,模型输入变量为:进水流量、cod、tss、氨氮、总氮浓度和曝气过程溶解氧浓度,输出变量为:出水bod、氨氮和总氮浓度;在回归过程中,设置误差为0.001-0.0005,经过迭代,分别得到出水bod值、氨氮和总氮浓度的回归预测模型;出水bod、氨氮和总氮浓度预测模型的输入和输出之间的关系为:bod5=f1(qin,codin,tssin,azotein,tnin,do)(10)azote=f2(qin,codin,tssin,azotein,tnin,do)(11)tn=f3(qin,codin,tssin,azotein,tnin,do)(12)其中,qin为进水流量(m3/h),codin为进水化学需氧量浓度(g/m3),tssin为进水总悬浮固体浓度(g/m3),azotein为进水氨氮浓度(g/m3),tnin为进水总氮浓度(g/m3),do为溶解氧浓度(g/m3);回归预测结果:图4(a)-图4(c)是出水bod、氨氮和总氮浓度的回归预测结果,从图中可以看出,这3个出水排放指标的预测值与asm1计算值的拟合程度很好;采用均方误差(mean-squareerror,mse)评价预测模型的精度,mse越小,模型预测精度越高;bod预测模型的mse值为5.36×10-4,氨氮预测模型的mse值为5.65×10-4,总氮预测模型的mse值为4.90×10-4,3个预测模型的精度都较高;从图4(a)-图4(c)的出水水质曲线图以及图2的进水特征曲线图可以看出,在开环控制中其他操作工况不变的条件下,出水bod、氨氮和总氮浓度的变化主要是由进水特征的变化决定的;进水流量和进水bod值的变化表现比较接近,与出水bod值的波动变化近似,出现了五个峰值,这说明出水bod值主要是受到了进水流量和进水bod值变化的影响;出水氨氮和总氮的模型也出现了相同的情形,出水氨氮和总氮的变化在40-140批次中达到了三个近似的峰值,与进水流量和总氮的变化呈现相似的趋势,都在相同的时间点出现峰值,而进水氨氮并未出现相似变化,呈无规律强烈变化;对比图4(a)-图4(c)的出水水质曲线图和图3的溶解氧浓度曲线图,进一步探究曝气过程溶解氧浓度与出水水质的关系;可以看出,溶解氧浓度与出水水质具有一定的相关性;溶解氧浓度变化出现了5个峰值,与出水水质变化出现的谷值几乎重合;另一方面,如图2和3所示,在1-20批次的进水过程中,进水流量普遍低于平均值7883.5m3/h,溶解氧浓度保持在一个较低的水平,而进水氨氮和总氮的变化均超过了平均值(分别为17.1g/m3和48.5g/m3),说明该阶段进水中,含氮污染物的负荷较高,开环控制时提供恒定的曝气量(kla=10h-1)无法去除较高负荷的含氮污染物,导致出水氨氮和总氮浓度过高,不能满足出水水质的排放标准;综上所述,在开环模拟中,其他工况不发生变化的情况下,进水特征和溶解氧浓度决定着出水质量;因此,以进水数据和溶解氧浓度为回归模型的输入,可以很好地预测出水质量,利用自适应回归核函数模型,构建进水数据和溶解氧浓度与出水质量之间的关系数学模型。步骤s3、采用遗传算法,求解在满足出水指标的前提下实现ghg减排的溶解氧浓度优化设定值,建立优化设定层;该步骤具体如下:由于溶解氧浓度越高,ghg排放总量就越大,采用遗传算法(遗传算法的初始种群规模为50-100,最大进化代数为1000-5000,个体基因数为5,变异率为0.1-0.7,交叉率为0.3-0.9)分别对步骤s2中出水bod、氨氮和总氮浓度的预测模型进行求解,获得分别满足出水bod、氨氮和总氮限值的最低溶解氧浓度设定值,以减少ghg排放,求解结果分别如图5(a)、图5(b)、图5(c)所示,分别满足出水bod、氨氮和总氮限值的最低溶解氧浓度设定值的平均值分别为0.851g/m3,0.915g/m3,0.856g/m3;基于图5(a)、图5(b)、图5(c),需要进一步对溶解氧浓度设定值进行优化,以同时满足三个出水排放指标(出水bod、氨氮和总氮浓度);由于在同一工况下(即开环控制时曝气量恒定为10h-1),闭环控制中的溶解氧浓度设定值与出水质量呈正相关,分别求解出水bod、氨氮和总氮浓度预测模型所得的三个设定值中,最高的设定值可以同时满足三个出水排放指标,选择三个设定值中的最大值,则可以同时使出水bod、氨氮和总氮不超过限值,并且达到ghg减排的效果;同时满足三个出水排放指标的溶解氧浓度优化设定值如图5(d)所示,其平均值为0.882g/m3;利用溶解氧浓度设定值优化的方法,可以有效地将出水排放指标控制在限值以下,同时减少不必要的高曝气操作,以期达到减少ghg排放的目的。步骤s4、根据优化的溶解氧浓度设定值,采用bp神经网络优化pi控制器参数,对溶解氧浓度进行跟踪控制,并分析溶解氧浓度分层优化控制下的ghg减排效果;该步骤具体如下:在以自适应核函数回归模型预测出水质量(步骤s2)和采用遗传算法求解溶解氧浓度优化设定值(步骤s3)的基础上,建立bp-pi控制模型;图6为用于造纸污水a/o处理工艺过程中ghg减排的溶解氧分层优化控制方案,bp神经网络的结构设置如表1所示;表1.用于造纸污水a/o处理工艺过程中ghg减排的溶解氧浓度跟踪控制的bp神经网络结构设置将进水数据、溶解氧浓度优化设定值和当前溶解氧浓度作为bp神经网络的输入,训练bp神经网络,输出pi控制器参数,然后应用于增量式pi控制,对溶解氧浓度进行控制,得到控制器的输出,即曝气量(kla)值,通过曝气机对造纸污水a/o处理工艺过程进行闭环控制,将溶解氧浓度控制在优化的设定值上,从而实现溶解氧浓度的优化跟踪控制;图7为造纸污水a/o处理工艺过程实施akrbp-pi(adapted-kernel-regressionbackpropagationneuralnetwork-proportional-integralcontrol,自适应回归bp神经网络pi控制)分层优化控制的溶解氧浓度设定值与测量值;从图7可以看出,akrbp-pi控制系统的溶解氧浓度优化设定值是跟随进水特征动态变化的,与溶解氧浓度设定值为固定值的控制系统相比,具有一定的优越性;为了体现akrbp-pi控制的优越性,对造纸污水a/o处理工艺过程分别进行pi控制(控制器参数:kp=0.21391,ti=0.30199;溶解氧浓度设定值:1mg/l;控制输入信号:阶跃变化的曝气量;溶解氧浓度测量滞后时间:30s)和bp-pi控制(神经网络的层数:3;输入层神经元个数:7;隐含层神经元个数:18;输出层神经元个数:2;神经网络输入变量:溶解氧浓度设定值、当前溶解氧浓度、进水量、cod、tss、氨氮和总氮;神经网络输出变量:控制器参数kp和ki;溶解氧浓度设定值:1mg/l),结合步骤s1的开环仿真结果,从控制效果、出水质量和ghg减排效果三个方面来评价上述三种控制方案的优劣;控制效果:在仿真过程中,如图7所示,akrbp-pi控制的动态设定值变化的频率过大,导致在跟踪控制的实施过程中,并不能完全减少溶解氧浓度测量值和优化设定值之间的偏差,控制系统的偏差仍然存在;表2是akrbp-pi控制方案的控制效果与pi和bp-pi控制方案的控制效果对比。其中,性能指标iae(integralabsoluteerror)为绝对误差积分,itae(integraltimeandabsoluteerror)为绝对时间误差积分,ise(integralsquareerror)为平方误差积分;表2的溶解氧浓度控制结果中,bp-pi控制的iae、itae和ise指标都最低,表明其控制稳定性最高;akrbp-pi的控制指标低于bp-pi,但是仍在可接受范围内;表2.对溶解氧浓度实施三种控制方案的控制效果指标控制方案iaeitaeisepi控制3.28×10-35.78×10-43.23×10-3bp-pi控制1.91×10-42.83×10-61.83×10-6akrbp-pi控制8.92×10-32.56×10-53.17×10-5进一步地,比较三种控制方案的操纵变量kla;图8为造纸污水a/o处理工艺过程采用不同控制方案的kla变化;在图8中,在开环控制下曝气量恒定kla=10h-1;pi控制的pi控制器参数为恒定值,kla从15.5h-1逐步下降至11.2h-1;bp-pi控制的控制器参数跟随进水水质变化,kla在7.8-15.5h-1之间变化;总的来说,在pi和bp-pi控制过程中,溶解氧浓度的设定值恒定为1mg/l,控制过程中的操纵变量kla基本都高于开环控制时的kla,说明要将溶解氧浓度维持到1mg/l的设定值,10h-1的kla并不能达到这个要求;在akrbp-pi控制方案中,溶解氧浓度设定值、pi控制器参数和曝气量都跟随进水水质实现动态变化,操纵变量kla的变化幅度较大,kla在0-14h-1之间变化,且大部分kla都低于10h-1,其平均值为7.90h-1;这说明在不同进水水质特征下,满足出水限值所需要的曝气量是不一样的,因此可以根据进水水质的特征,优化溶解氧浓度设定值,在出水水质达标的情况下,减少ghg的排放;出水质量:图9(a)-图9(e)为造纸污水a/o处理工艺过程采用不同控制方案的出水水质变化;从图中可以看出,虽然akrbp-pi控制下的出水bod(图9(b))、氨氮(图9(c))和总氮(图9(d))相较于pi控制和bp-pi控制,呈现较高的数值,但均未发现超限情况;这可以解释为,在akrbp-pi控制方案中,是以满足出水限值为约束条件的,选取能够同时满足出水bod、氨氮和总氮的最低溶解氧浓度设定值,来实现ghg的减排;一方面,相较于溶解氧浓度设定值恒定为1mg/l的pi和bp-pi控制,在akrbp-pi控制中,部分动态优化的设定值低于1mg/l(图7),在这阶段的出水排放指标虽然高于pi控制和bp-pi控制的情况,但已经可以满足出水排放的标准,改善了开环控制中部分超限情况(图9(a)-图9(e));另一方面,溶解氧浓度设定值恒定为1mg/l的pi和bp-pi控制,其曝气机提供的kla量较高(图8),曝气机多余的耗电,不仅造成了运行成本的增加,也导致了因曝气机耗电间接产生的ghg量增加;对于出水cod(图9(a)),akrbp-pi控制与pi和bp-pi控制效果相差不大,但是都比开环模拟的低;如图9(e)所示,不同的溶解氧浓度控制方法,对出水tss的影响没有差别,这是因为污水处理过程中,tss的组成主要是不参与反应的惰性颗粒物,通过沉淀池的沉降作用进行去除,与溶解氧反应过程关系不大;综上所述,在造纸污水a/o处理工艺过程中采用pi、bp-pi和akrbp-pi控制方案对溶解氧浓度进行动态控制,均可以使出水水质达标,其中,pi和bp-pi控制的溶解氧浓度设定值恒定为1mg/l,而akrbp-pi控制方案的溶解氧浓度设定值是动态优化的;ghg减排效果:图10(a)为造纸污水a/o处理工艺过程采用不同控制方案的ghg直接排放量;在开环、pi、bp-pi和akrbp-pi的控制情况下,ghg直接排放量差别不大,在第1-第8批次的模拟结果中,akrbp-pi控制产生的ghg直接排放量比其他三种情况下的高;如图10(b)所示,ghg间接排放量的变化趋势大致与kla(图8)的变化趋势相近;pi和bp-pi控制方案为了维持恒定的1mg/l溶解氧浓度设定值,产生了大量的ghg,明显高于akrbp-pi控制方案所排放的间接ghg;在akrbp-pi的控制下,动态优化溶解氧浓度的设定值,并普遍低于1mg/l(图8),但是kla变化剧烈,导致曝气机耗电所产生的ghg间接排放量变化较大;综合ghg的直接排放量和间接排放量,如图10(c)所示,从ghg总排放量来看,akrbp-pi控制方案明显减少了ghg的排放;虽然有少量时段的ghg排放量较高,这是因为实施跟踪优化控制时,动态优化设定值的变化幅度过大,控制输出未能实现无偏差的跟踪控制;但是,大部分时段的ghg排放量都低于开环、pi和bp-pi的控制情况;表3是造纸污水a/o处理过程在四种控制方案下的ghg排放量的平均值,括号内为三种控制方案相对于开环情况的减排百分比(其中负号表明排放量增加);可以看出,pi和bp-pi控制对ghg的直接排放有一定减排作用,分别减少了4.99%和4.96%;akrbp-pi控制作用对直接排放量的减少效果较差,仅减少了1.86%;表3.造纸污水a/o工艺处理过程在不同控制方案下的ghg排放量平均值akrbp-pi控制对间接排放量的减排效果较明显,减少了10.75%的ghg;相反,pi和bp-pi的控制作用导致ghg间接排放量的增加,分别增加了12.40%和7.12%;从ghg排放总量来看,pi和bp-pi控制都导致了ghg的增加,而akrbp-pi对ghg减排的效果比较明显,实现了ghg排放总量下降8.55%,达到了ghg减排的目的;进一步地分析akrbp-pi控制对各个ghg排放源的影响;图11(a)-图11(d)是造纸污水a/o处理工艺过程采用不同控制方案的各ghg直接排放源的排放量;ghg直接排放源包括内源性衰变、bod去除、硝化过程和反硝化过程;从图11(a)-图11(d)可以看出,实施akrbp-pi控制方案使内源性衰变的ghg排放量增加(图11(a)),硝化过程消耗的co2减少(图11(c)),因此这两个排放源所排放的ghg都增加了;特别是在第1-第8批次期间,硝化过程仅消耗了少量co2,说明该阶段的硝化反应活性较低,含氮污染物的去除效率较低;而bod去除过程的ghg排放量(图11(b))和反硝化过程中n2o的排放量(图11(d)),在第1-第8批次中,akrbp-pi控制下的排放量较低,但总体来说,采用pi、bp-pi和akrbp-pi控制方案的ghg直接排放量相差不大;图12(a)-图12(d)为造纸污水a/o处理工艺过程采用不同控制方案的各ghg间接排放源的排放量;ghg间接排放源包括:曝气机耗电、水泵耗电、化学品添加和污泥处理;akrbp-pi控制的减排作用主要体现在曝气机耗电间接排放的ghg减少(图12(a));相较于开环控制,在第1-第8批次期间,akrbp-pi控制产生的ghg明显较高;这段时间,akrbp-pi控制方案将溶解氧控制在较高的浓度(图7),曝气机输出较多的空气(图8),供系统降解污染物,以满足出水水质的要求;在此之后的仿真时段,akrbp-pi控制将kla控制在较低值(<10h-1),即以较低的kla就可以满足出水限值,并且同时减少ghg的排放;水泵耗电(图12(b))和化学品添加(图12(c))过程因不涉及溶解氧浓度,其间接排放的ghg为恒定值,不受控制方案的影响;图12(d)中污泥处理间接产生的ghg与排出污泥量有关,当排出的污泥量恒定时,便取决于排出污泥的浓度;污泥从沉淀池底部排出,沉淀池中的沉降性能与溶解氧浓度有关;溶解氧浓度越低,污染物颗粒的沉降性能越高,因此排出污泥的污染物浓度越高,造成污泥处理间接产生的ghg量越高;在akrbp-pi控制下,动态优化控制后的溶解氧浓度大多低于1mg/l(图7),因此污泥处理过程所产生的ghg略有增加;为进一步研究akrbp-pi控制方案对ghg减排的作用机制,通过对各排放源ghg减排量的研究可以清晰量化akrbp-pi控制对各个排放源的影响;图13为造纸污水a/o处理工艺过程采用不同控制方案的各ghg排放源的减排量比较(其中负号表明排放量增加);从图13中可以看出,pi和bp-pi控制方案的减排效果主要体现在直接排放源中的硝化过程,但是控制过程中反而极大增加了曝气机耗电所产生的ghg;akrbp-pi控制方案的减排效果主要体现在有效地降低了曝气机耗电所间接产生的ghg,平均减少了35.9kg/h;akrbp-pi控制方案对其它排放源的影响较小,影响范围基本不超过4kg/h,其中对ghg直接排放源的影响普遍较小,内源性衰变过程产生的ghg平均增加了2.03kg/h,bod去除过程产生的ghg减少了2.15kg/h,反硝化过程产生的n2o平均减少了1.62kg/h(co2计)。上述实施例为本发明较佳的实施方式,但本发明的实施方式并不受上述实施例的限制,其他的任何未背离本发明的精神实质与原理下所作的改变、修饰、替代、组合、简化,均应为等效的置换方式,都包含在本发明的保护范围之内。当前第1页12