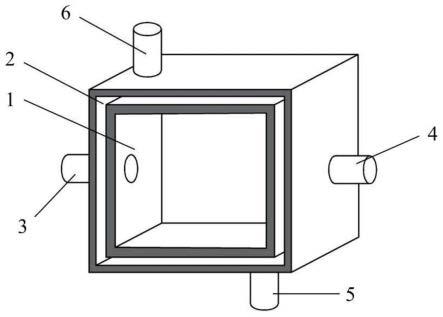
1.本发明涉及资源回收技术领域,尤其是涉及一种退役风机叶片热解回收玻璃纤维的方法及其得到的再生玻璃纤维。
背景技术:2.随着风力发电行业的迅速发展,风电年新增装机量大幅攀升。风机叶片是风电机组的重要组成部分,激增的风电装机容量必将催生大量退役叶片。当前,风机叶片的设计寿命通常为20年,市场上早期运行叶片已超过15年,因此,部分老旧风电场投运的叶片已陆续开始退役。未来,退役叶片总量更将迅猛增长。
3.玻璃纤维复合材料因其价格便宜,综合性能优异,是目前风机叶片中用量最大、使用面最广的高性能复合材料。风机叶片中纤维和树脂占比为叶片总质量90%以上。传统的填埋处理占用大量土地,很可能污染土壤和地下水,更难以实现高价值纤维的资源化回收。直接焚烧退役风机叶片也会产生二噁英等有毒物质,严重污染环境,危害人体健康。
4.热解技术具有减量化明显、无害化彻底、资源化程度高等优势,是一类重要的复合材料再循环回收技术。中国专利cn113046107a公开了一种热解回收系统,结合热解反应器和循环流化床锅炉对退役风机叶片进行回收处置;中国专利cn114656985a公开了将退役风机叶片在高温氮气中进行高温热解,再经风力分选分离得到纤维材料;中国专利cn112024583a公开了将退役风机叶片在固定床气化炉中进行热裂解,进而从产生的灰渣中回收玻璃纤维;中国专利cn113278438a公开了借助燃煤电厂低品位的蒸汽作为反应过程中的隔离保护气,并利用微波热解从退役的风机叶片中回收纤维。然而,退役风机叶片中的聚合物树脂热分解会产生热解炭并残留于这些固体产物中,因此,上述热解得到的固体产物并非是干净清洁的再生玻璃纤维,而含炭的再生纤维通常无法与树脂进行有效粘结,难以二次利用。为了去除这些残炭,上述技术方案中均需增加机械分离或氧化等后处理工艺,导致回收工艺更加复杂,增加了系统的能耗,同时也会对再生纤维的性能产生不利影响。目前尚未有成熟有效的技术可以解决这些问题。
5.有鉴于此,特提出本发明。
技术实现要素:6.本发明的目的之一在于提供一种退役风机叶片热解回收玻璃纤维的方法,该方法能够直接得到表面干净清洁且力学性能良好的玻璃纤维,无需进行进一步机械分离或氧化等后处理工艺来去除热解炭。
7.本发明的目的之二在于提供一种上述方法得到的再生玻璃纤维。
8.为了实现本发明的上述目的,特采用以下技术方案:
9.第一方面,本发明提供了一种退役风机叶片热解回收玻璃纤维的方法,包括以下步骤:
10.(1)将退役风机叶片拆除金属构件后,切割成叶片块材;
11.(2)将步骤(1)得到的叶片块材和促热解剂置于热解反应器中,在惰性气氛下进行热解反应;其中,所述促热解剂选自为乙酸、过氧化氢、有机醇(脂肪族一元或二元醇)、过硫酸盐中的一种配制而成的水溶液;
12.(3)反应后,将固体产物从热解反应器中取出,冷却,得到再生玻璃纤维;所述再生玻璃纤维的含炭量<1%,再生玻璃纤维拉伸强度保留率在97%以上。
13.下面对各步骤进行详细说明。
14.步骤(1)
15.首先将退役风机叶片拆除金属构件后,机械切割成合适尺寸的叶片块材。
16.优选地,叶片块材的尺寸为30~100cm
×
20~50cm
×
10~20cm。
17.步骤(2)
18.然后,将叶片块材置于热解反应器中,在惰性气氛和一定温度下进行热解反应;热解的同时向反应器中通入一定量的乙酸、过氧化氢、有机醇(例如异丙醇、正丁醇、乙二醇等脂肪族一元或二元醇中的一种)、过硫酸盐(例如过硫酸钠、过硫酸钾、过硫酸氢钾中的一种)等配制成的水溶液作为促热解剂。
19.优选地,热解反应的惰性气氛为氮气或氩气气氛。
20.优选地,热解反应的温度为400~600℃;热解反应的时间为30~60min。
21.优选地,促热解剂的浓度为5~10mol/l,其用量与叶片块材的质量之比为1~1.5l/kg。
22.本发明采用特殊的一类促热解剂,其共同特点是能够在高温下产生具有较强氧化能力的活性自由基,如h
·
自由基、oh
·
自由基、so
4-·
自由基等。这部分活性自由基与聚合物大分子链进行有效碰撞,使树脂基体裂解过程中能够充分与自由基结合形成短链小分子产物,抑制聚合物裂解产物的二次聚合及热解炭的生成,促使退役风机叶片中的树脂基体(环氧树脂)完全裂解,进而实现还原气氛下有机树脂裂解残余在纤维表面的有机热解炭的原位脱除,避免了燃烧、机械分离等后处理除炭工艺对再生玻璃纤维性能造成损伤。
23.步骤(3)
24.将反应后的固体产物从热解反应器中取出,冷却后即可得到表面干净清洁且力学性能良好的再生玻璃纤维。
25.再生玻璃纤维的含炭量<1%,再生玻璃纤维拉伸强度保留率可以达到97%以上。
26.第二方面,本发明提供了一种上述方法得到的再生玻璃纤维;
27.所述再生玻璃纤维的含炭量<1%,再生玻璃纤维拉伸强度保留率可以达到97%以上。
28.与已有技术相比,本发明的有益效果为:
29.1、本发明通过快速热解技术处理退役风机叶片,避免了填埋处理对资源的浪费及直接焚烧产生的二噁英等有毒有害气体;同时,对热解反应进行优化改进,避免树脂热解后热解炭氧化对玻璃纤维品质造成影响,在热解过程中向反应器内加入促热解剂,在高温下释放h
·
、oh
·
、so
4-·
等具有较强氧化能力的活性自由基,与聚合物大分子链进行有效碰撞,使树脂基体裂解过程中能够充分与自由基结合形成短链小分子产物,抑制聚合物裂解产物的二次聚合及热解炭的生成,促使退役风机叶片中的树脂基体(环氧树脂)完全裂解,
进而实现还原气氛下有机树脂裂解残余在纤维表面的有机热解炭的原位脱除。能够在不增加任何后处理工艺的情况下,成功回收表面干净清洁、性能良好的玻璃纤维,避免了燃烧、机械分离等后处理工艺对纤维性能的损伤以及系统能耗的增加。再生玻璃纤维能与其他聚合物树脂间产生较好的界面粘结性,进而生产制造新的复合材料。
30.2、本发明提出的方法可以有效实现退役风机叶片的减量化、无害化、资源化处理,同时可回收干净清洁、再利用价值高的再生玻璃纤维,工艺简单、节能环保。
附图说明
31.图1为本发明一种实施方式的热解反应器的结构示意图;
32.图2为本发明一种实施方式的热解反应器的剖面图。
33.图标:1-热解反应器内腔室;2-热解反应器外腔室;3-惰性气体及促热解剂进口通道;4-热解产气出口通道;5-高温烟气进口通道;6-低温烟气出口通道。
具体实施方式
34.下面将结合实施例对本发明的技术方案进行清楚、完整地描述,显然,所描述的实施例是本发明一部分实施例,而不是全部的实施例。基于本发明中的实施例,本领域普通技术人员在没有做出创造性劳动前提下所获得的所有其他实施例,都属于本发明保护的范围。
35.下面通过实施例对本发明作进一步说明。如无特别说明,实施例中的材料为根据现有方法制备而得,或直接从市场上购得。
36.以再生玻璃纤维的含炭量及拉伸强度保留率作为回收效果评价指标,计算公式为:
[0037][0038][0039]
式(1)中:r为再生玻璃纤维的含炭量,%;mc为再生玻璃纤维表面残留热解炭的质量,kg;m为再生玻璃纤维的质量,kg。
[0040]
式(2)中:x为再生玻璃纤维拉伸强度保留率,%;σ为再生玻璃纤维的拉伸强度,mpa;σ0为原始玻璃纤维的拉伸强度,mpa。
[0041]
实施例的热解反应可以在热解反应器中进行,热解反应器的结构如图1、图2所示,但不限于此;具体过程为:将叶片块材置于热解反应器内腔室1中,在高温下进行热解反应;在热解过程中,通过惰性气体及促热解剂进口通道3,向热解反应器内腔室1中持续地通入惰性气体及一定量的促热解剂;热解产生的高热值可燃气通过热解产气出口通道4排出并燃烧,燃烧产生的高温烟气通过高温烟气进口通道5通入热解反应器外腔室2进行换热,为热解过程提供能量,换热后烟气通过低温烟气出口通道6排出;到达反应时间后,将反应产生的固体产物从热解反应器内腔室1中取出并冷却。
[0042]
实施例1
[0043]
首先将退役风机叶片机械切割成30cm
×
30cm
×
10cm的叶片块材;将热解反应器升
温到550℃,并用氮气吹扫;然后将切割后的叶片块材迅速置于高温热解反应器中进行热解反应;在热解过程中持续通入氮气,同时向反应器内通入6mol/l的乙酸水溶液,其用量与叶片块材的质量比为1.5l/kg;反应60min后,将反应产生的固体产物从反应器中取出,冷却后即可得到表面干净清洁的玻璃纤维,含炭量为0.9%。通过纤维拉伸测试,本实施例中所得再生玻璃纤维的拉伸强度为原始纤维的97.6%。
[0044]
实施例2
[0045]
首先将退役风机叶片机械切割成50cm
×
20cm
×
10cm的叶片块材;将热解反应器升温到600℃,并用氩气吹扫;然后将切割后的叶片块材迅速置于高温热解反应器中进行热解反应;在热解过程中持续通入氩气,同时向反应器内通入10mol/l的乙酸水溶液,其用量与叶片块材的质量比为1l/kg;反应40min后,将反应产生的固体产物从反应器中取出,冷却后即可得到表面干净清洁的玻璃纤维,含炭量为0.8%。通过纤维拉伸测试,本实施例中所得再生玻璃纤维的拉伸强度为原始纤维的98.5%。
[0046]
实施例3
[0047]
首先将退役风机叶片机械切割成50cm
×
40cm
×
10cm的叶片块材;将热解反应器升温到400℃,并用氮气吹扫;然后将切割后的叶片块材迅速置于高温热解反应器中进行热解反应;在热解过程中持续通入氮气,同时向反应器内通入5mol/l的过氧化氢水溶液,其用量与叶片块材的质量比为1.5l/kg;反应50min后,将反应产生的固体产物从反应器中取出,冷却后即可得到表面干净清洁的玻璃纤维,含炭量为0.8%。通过纤维拉伸测试,本实施例中所得再生玻璃纤维的拉伸强度为原始纤维的98.2%。
[0048]
实施例4
[0049]
首先将退役风机叶片机械切割成70cm
×
30cm
×
10cm的叶片块材;将热解反应器升温到450℃,并用氩气吹扫;然后将切割后的叶片块材迅速置于高温热解反应器中进行热解反应;在热解过程中持续通入氩气,同时向反应器内通入8mol/l的过氧化氢水溶液,其用量与叶片块材的质量比为1l/kg;反应50min后,将反应产生的固体产物从反应器中取出,冷却后即可得到表面干净清洁的玻璃纤维,含炭量为0.6%。通过纤维拉伸测试,本实施例中所得再生玻璃纤维的拉伸强度为原始纤维的97.1%。
[0050]
实施例5
[0051]
首先将退役风机叶片机械切割成30cm
×
20cm
×
20cm的叶片块材;将热解反应器升温到500℃,并用氮气吹扫;然后将切割后的叶片块材迅速置于高温热解反应器中进行热解反应;在热解过程中持续通入氮气,同时向反应器内通入7mol/l的异丙醇水溶液,其用量与叶片块材的质量比为1.5l/kg;反应40min后,将反应产生的固体产物从反应器中取出,冷却后即可得到表面干净清洁的玻璃纤维,含炭量为0.8%。通过纤维拉伸测试,本实施例中所得再生玻璃纤维的拉伸强度为原始纤维的99.4%。
[0052]
实施例6
[0053]
首先将退役风机叶片机械切割成70cm
×
20cm
×
10cm的叶片块材;将热解反应器升温到550℃,并用氩气吹扫;然后将切割后的叶片块材迅速置于高温热解反应器中进行热解反应;在热解过程中持续通入氩气,同时向反应器内通入6mol/l的正丁醇水溶液,其用量与叶片块材的质量比为1.5l/kg;反应30min后,将反应产生的固体产物从反应器中取出,冷却后即可得到表面干净清洁的玻璃纤维,含炭量为0.9%。通过纤维拉伸测试,本实施例中所
得再生玻璃纤维的拉伸强度为原始纤维的98.3%。
[0054]
实施例7
[0055]
首先将退役风机叶片机械切割成50cm
×
30cm
×
10cm的叶片块材;将热解反应器升温到500℃,并用氮气吹扫;然后将切割后的叶片块材迅速置于高温热解反应器中进行热解反应;在热解过程中持续通入氮气,同时向反应器内通入5mol/l的乙二醇水溶液,其用量与叶片块材的质量比为1l/kg;反应50min后,将反应产生的固体产物从反应器中取出,冷却后即可得到表面干净清洁的玻璃纤维,含炭量为0.6%。通过纤维拉伸测试,本实施例中所得再生玻璃纤维的拉伸强度为原始纤维的98.0%。
[0056]
实施例8
[0057]
首先将退役风机叶片机械切割成50cm
×
30cm
×
20cm的叶片块材;将热解反应器升温到550℃,并用氩气吹扫;然后将切割后的叶片块材迅速置于高温热解反应器中进行热解反应;在热解过程中持续通入氩气,同时向反应器内通入9mol/l的过硫酸钠水溶液,其用量与叶片块材的质量比为1.5mol/l;反应40min后,将反应产生的固体产物从反应器中取出,冷却后即可得到表面干净清洁的玻璃纤维,含炭量为0.7%。通过纤维拉伸测试,本实施例中所得再生玻璃纤维的拉伸强度为原始纤维的97.9%。
[0058]
实施例9
[0059]
首先将退役风机叶片机械切割成100cm
×
20cm
×
20cm的叶片块材;将热解反应器升温到450℃,并用氮气吹扫;然后将切割后的叶片块材迅速置于高温热解反应器中进行热解反应;在热解过程中持续通入氮气,同时向反应器内通入6mol/l的过硫酸钾水溶液,其用量与叶片块材的质量比为1.3l/kg;反应60min后,将反应产生的固体产物从反应器中取出,冷却后即可得到表面干净清洁的玻璃纤维,含炭量为0.6%。通过纤维拉伸测试,本实施例中所得再生玻璃纤维的拉伸强度为原始纤维的98.7%。
[0060]
实施例10
[0061]
首先将退役风机叶片机械切割成50cm
×
50cm
×
20cm的叶片块材;将热解反应器升温到500℃,并用氩气吹扫;然后将切割后的叶片块材迅速置于高温热解反应器中进行热解反应;在热解过程中持续通入氩气,同时向反应器内通入8mol/l的过硫酸氢钾水溶液,其用量与叶片块材的质量比为1l/kg;反应50min后,将反应产生的固体产物从反应器中取出,冷却后即可得到表面干净清洁的玻璃纤维,含炭量为0.8%。通过纤维拉伸测试,本实施例中所得再生玻璃纤维的拉伸强度为原始纤维的98.1%。
[0062]
对比例1
[0063]
首先将退役风机叶片机械切割成30cm
×
30cm
×
10cm的叶片块材;将热解反应器升温到550℃,并用氮气吹扫;然后将切割后的叶片块材迅速置于高温热解反应器中进行热解反应;在热解过程中持续通入氮气,不使用任一种促热解剂;反应60min后,将反应产生的固体产物从反应器中取出,冷却后得到表面明显残余有热解炭的玻璃纤维,含炭量为5.7%。通过纤维拉伸测试,本对比例中所得再生玻璃纤维的拉伸强度为原始纤维的59.4%。
[0064]
通过此对比例可知,若不使用促热解剂,则回收得到的再生玻璃纤维表面残留有大量热解炭,且再生玻璃纤维的拉伸强度远不及原始玻璃纤维,难以作为增强材料进行再利用。
[0065]
对比例2
[0066]
首先将退役风机叶片机械切割成30cm
×
30cm
×
10cm的叶片块材;将热解反应器升温到550℃,并用氮气吹扫;然后将切割后的叶片块材迅速置于高温热解反应器中进行热解反应;在热解过程中持续通入氮气,同时向反应器内通入二氧化碳,其用量与叶片块材的质量比为1.5l/kg;反应60min后,将反应产生的固体产物从反应器中取出,冷却后得到表面明显残余有热解炭的玻璃纤维,含炭量为4.1%。通过纤维拉伸测试,本对比例中所得再生玻璃纤维的拉伸强度为原始纤维的55.8%。
[0067]
通过此对比例可知,二氧化碳可与热解炭发生一定程度的反应,但其不能在叶片热解条件下释放h
·
、oh
·
、so
4-·
等具有较强氧化能力的活性自由基,无法发挥本发明中所选用的促热解剂的作用,因此并不能显著减少热解后残留在再生玻璃纤维表面的热解炭含量,且会进一步对再生玻璃纤维的拉伸强度造成不利影响。
[0068]
对比例3
[0069]
首先将退役风机叶片机械切割成50cm
×
30cm
×
20cm的叶片块材;将热解反应器升温到550℃,并用氩气吹扫;然后将切割后的叶片块材迅速置于高温热解反应器中进行热解反应;在热解过程中持续通入氩气,同时向反应器内通入9mol/l的硫酸钠水溶液,其用量与叶片块材的质量比为1.5l/kg;反应40min后,将反应产生的固体产物从反应器中取出,冷却后得到表面明显残余有热解炭的玻璃纤维,含炭量为5.4%。通过纤维拉伸测试,本对比例中所得再生玻璃纤维的拉伸强度为原始纤维的61.2%。
[0070]
通过此对比例可知,在叶片热解条件下,硫酸钠不能生成具有较强氧化能力的so
4-·
自由基,无法促使退役风机叶片中的树脂基体完全裂解,没有发挥出本发明中所选用的促热解剂的作用,因此并不能有效减少热解后残留在再生玻璃纤维表面的热解炭含量,也无法对再生玻璃纤维的拉伸强度起到改善作用。
[0071]
表1列出了各实施例及对比例中的相关工艺参数及再生玻璃纤维的含炭量及拉伸强度保留率。再生玻璃纤维的含炭量均<1%,拉伸强度保留率均在97%以上,证明了本发明提出的退役风机叶片热解回收清洁玻璃纤维方法具有优异的回收效果。
[0072]
表1实施例及对比例中的工艺参数及再生玻璃纤维的含炭量及强度保留率
[0073]
[0074][0075]
最后应说明的是:以上各实施例仅用以说明本发明的技术方案,而非对其限制;尽管参照前述各实施例对本发明进行了详细的说明,本领域的普通技术人员应当理解:其依然可以对前述各实施例所记载的技术方案进行修改,或者对其中部分或者全部技术特征进行等同替换;而这些修改或者替换,并不使相应技术方案的本质脱离本发明各实施例技术方案的范围。