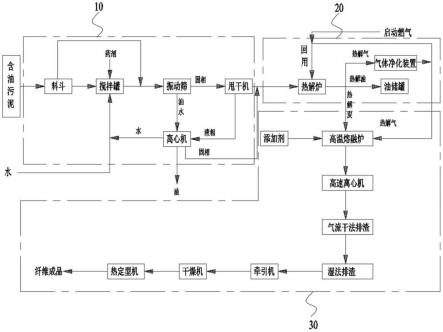
1.本实用新型涉及固废、环保领域,特别是涉及一种含油污泥高值化利用系统。
背景技术:2.油田在开发生产过程中,不可避免的产生大量含油污泥。经初步调查,我国每年含油污泥新增产量达100万吨左右,由于油泥中含有水、泥沙、硫化物、苯系物、酚类、烃类等,不仅占用土地和空间,而且严重的污染空气、土壤和地下水,在一定程度上制约了国内油田生产的发展。含油污泥已经被国家列为危险固体废弃物,因此开发一种既能消除含油污泥对环境的危害又可回收资源的处理技术对油田的可持续发展具有重要的实际意义。
3.含油污泥种类繁多、性质复杂,相应的处理技术也呈现多元化趋势,目前含油污泥处理技术有筛选流化~调质~离心技术、焚烧、化学热洗、热解析、地耕法、堆肥法、生物反应、溶剂萃取技术等,国内油田多采用填埋、浓缩脱水、固化处理、催化裂解等,其共同的缺点是未能回收利用具有较高经济价值的原油,高温热解析处理是日前国外广泛用于含油污泥处理技术,可实现含油污泥的无害化、减量化、资源化处理。含油污泥来源不同,含油率不同,低则5%以下,高则达到50%以上,若按平均值20%计,热解析资源化技术年可回收利用近20万吨原油,具有十分可观的经济价值。
4.高温热解气化是将含油污泥通过热化学转化(如碳化、热解、气化)可产生固态、液态和气态产物,这些产物按需求制成可回收、易利用、易运输及易储存的能源形态,可供热发电或用作化工及其它产业的原料。根据原料不同和热处理目的的差异,可采用碳化、气化、热解、液化或者其他相关的热化学反应和工艺。热解气化采用的反应器形式很多,如移动床、固定床、流化床、烧蚀床、悬浮炉和回转窑等,其中工业生产以移动床、固定床、回转窑和流化床为主。例如,公开号为:cn208087547u的专利文献公开了一种外热式回转窑危废碳化装备,所述回转窑装置包括有外热式回转窑和二次燃烧室,所述热解气化装置包括热解炉和用于储存可燃烟气的储存室。以固废回转窑为基础,降低一次能源的补给量,各系统均能完全燃烧,尾气处理通过分子裂解装置,去除包括二噁英在内的有害物质,达到更高的排放标准。公开号为:cn110375310a的专利文献公开了一种加压流化床含油污泥焚烧系统及其焚烧处理方法,所述流化床焚烧炉加入含油污泥在流化状态下加压燃烧,分离出的飞灰用于制砖;产生的烟气通过余热回收系统将其显热回收利用。
5.但是,上述技术存在以下缺点:一旦多膛炉产生的残渣无法满足相关的排放标准,依然是危险废物时,还需对冷却后残渣进一步处置,满足相关的标准要求。流化床焚烧消耗能源高,无法回收含油污泥中油品资源化产品,同时分离出的飞灰用于制砖,产品砖是否适用相应的产品标准会使产品砖应用场景受到限制,产品砖附加价值低难以满足远距离运输使用。另外因大多油泥均因其粘度大,含油含水较高,采用流化床焚烧法处理,流化效果差,同时焚烧易产生二噁英类剧毒气体,增加尾气净化投资成本。
6.由于现有技术的上述种种缺点,提供一种连续、高效、产品附加价值高的热解和获得高附件价值产品系统是十分必要的。
技术实现要素:7.本实用新型的目的是针对现有技术存在的问题,提出一种含油污泥高值化利用系统,将含油污泥实现减量化、无害化和资源化利用以及节能减排。
8.为实现上述目的,本实用新型提供了一种含油污泥高值化利用系统,包括依次相连的预处理单元、有机物绝氧热解单元、高温熔融提纤单元;
9.所述预处理单元包括依次相连的料斗、搅拌罐、振动筛、甩干机和离心分离机,所述离心分离机用于分离振动筛与甩干机脱出的固液相;
10.所述有机物绝氧热解单元包括与所述甩干机依次相连的热解炉、油气冷却净化系统、热解气循环回用系统,所述油气冷却净化系统包括冷凝塔、存储冷凝得到的液态混合物的油贮罐以及对冷凝处理后的不凝气进行脱硫的气体净化装置;
11.所述高温熔融提纤单元包括与所述热解炉依次相连的高温熔融炉、高速离心机、干排渣装置、湿排渣装置、牵引机、干燥机、热定型机,所述牵引机与所述干排渣装置、湿排渣装置的纤维出料端连接将除渣后的纤维送入干燥机;
12.所述热解气循环回用系统将气体净化装置的不凝气返回至热解炉与高温熔融炉。
13.优选地,所述振动筛包括一级筛分和二级筛分,所述一级筛分的筛孔为10~20mm方形筛孔,所述二级筛分的筛孔为1~10mm方形筛孔。
14.优选地,所述高温熔融炉接收由热解炉热解得到的固体物料与甩干机甩干后得到的部分固体物料,在燃气和富氧的作用下进行高温熔融加热,所述固体物料加热温度为1500~2200℃。
15.优选地,所述高速离心机通过上下交错布置的四级高速旋转圆盘高速旋转快速成纤,其中,自上而下设置直径为150~200mm且转速为3800~4200r/min的第一辊、直径为220~300mm且转速为5000~5500r/min的第二辊、直径为350~400mm且转速为5500~6000r/min的第三辊、直径为350~400mm且转速为6000~7000r/min的第四辊。
16.基于上述技术方案,本实用新型的优点是:
17.本实用新型采用绝氧热解装置对含油污泥进行绝氧热解,可获得油品能源,同时可避免含油污泥直接焚烧产生大量二噁英,另外获得的热解气属于清洁能源,直接燃烧的废气达锅炉排放标准。
18.高温熔融炉只对部分含有少量难分离有机物的无机物进行进一步燃烧,大大减少因直接焚烧原生含油污泥产生大量废气问题,同时高温熔融炉内不含或是只有极少量的有机物,可有效抑制二噁英的产生,另外杜绝了属于危废飞灰的产生,降低了高温熔融过程中的进料量,大大减少了整个高温熔融系统的能耗问题。通过高温熔融提纤系统可实现热解产生的固体物高温熔融,获得无毒性、高附加值的纤维产品,可用于建材、工业耐高温高强度要求产品中,另外获得可用于清洁燃烧的燃料气。送入高温熔融炉的热解气属于清洁燃气,燃烧产生废气能达到锅炉废气排放标准,从而显著降低了高温熔融炉废气处理成本。
19.本实用新型的整个工艺有机结合到一起,一方面通过分级处理工艺可有效避免因直接焚烧含油污泥导致无机物和水带走大量热,导致整个系统能源利用率低;另一方面既解决含油污泥因直接焚烧的污染问题,同时获得附加价值高的燃料油和纤维等能源产品,彻底实现了油泥危险废弃物完全资源化回收利用。
附图说明
20.此处所说明的附图用来提供对本实用新型的进一步理解,构成本技术的一部分,本实用新型的示意性实施例及其说明用于解释本实用新型,并不构成对本实用新型的不当限定。在附图中:
21.图1为含油污泥高值化利用系统示意图;
22.图2为含油污泥高值化利用方法步骤图。
具体实施方式
23.下面通过附图和实施例,对本实用新型的技术方案做进一步的详细描述。
24.本实用新型提供了一种含油污泥高值化利用系统,如图1、图2所示,其中示出了本实用新型的一种优选实施方式。本实用新型解决现有处理工艺中所存在的环保问题,无法与现有国家推行的危险废弃物资源化利用相一致,从而提供一种可以利用含油污泥中可回收资源,显著降低废气排放量和废气中二噁英问题,同时将因热解产生的固渣资源化回收利用制成高附件价值产品,同时降低因焚烧产生的大量的co2温室气体。
25.如图1所示,所述含油污泥高值化利用系统包括依次相连的预处理单元10、有机物绝氧热解单元20、高温熔融提纤单元30。
26.所述预处理单元10包括依次相连的料斗、搅拌罐、振动筛、甩干机和离心分离机,所述离心分离机用于分离振动筛与甩干机脱出的固液相。所述料斗用于暂存含油污泥,为后续预处理系统供应连续的物料。所述搅拌罐与所述料斗装置相连,用于对含油污泥加药搅拌处理,向含油污泥中通入1-3倍体积温度60~80℃的温水,同时加入总质量1-8%的硅酸钠药剂,在搅拌罐中进行充分的搅拌混合。
27.所述搅拌罐与振动筛相连,所述的振动筛用于对充分搅拌后的混合液进行振动分离。a)所述筛分装置首选多级倾斜平板式筛网,根据含油污泥具体情况可分为一级筛分和二级筛分,或是多级筛分;b)所述振动筛包括一级筛分和二级筛分,所述一级筛分的筛孔为10~20mm方形筛孔,主要用于筛除含油污泥中的细渣土;所述二级筛分的筛孔为1~10mm方形筛孔,主要用于筛除含油污泥中的固体物;c)通过筛分得到的固体物直接送至甩干机;d)通过筛分后的筛下混合液通过管道直径送入甩干机、离心机。
28.进一步,所述离心机用于对筛分后的混合液进一步离心分选,获得水、油和以无机物为主固体组分;所述甩干机与振动筛相连,通过甩干机对振动筛送来的固体进行固液分离,分离后的液体送入所述的离心机;分离后的固体送入后续单元。
29.如图1所示,所述有机物绝氧热解单元20包括与所述甩干机依次相连的热解炉、油气冷却净化系统、热解气循环回用系统,所述油气冷却净化系统包括冷凝塔、存储冷凝得到的液态混合物的油贮罐以及对冷凝处理后的不凝气进行脱硫的气体净化装置。所述热解气循环回用系统将气体净化装置的不凝气返回至热解炉与高温熔融炉。
30.所述甩干机分离得到的无机物为主的固体物送入所述的绝氧热解系统,固体物中的有机物在300~700℃温度下进行热分解,产生油气混合物通过引风机送入油气冷却净化系统,冷凝得到的液态混合物以混合燃料油为主,送入油贮罐贮存外售;通过冷凝后的不凝气通过气体净化装置进行脱硫后返回至热解炉作为燃料供热解用;
31.进一步,所述热解炉启炉所需燃气由外供燃气提供,一旦热解炉产生热解气后,所
述热解炉所需燃气由外供燃气切换至自产燃气系统;所述热解炉产生的热解固体产物送入高温熔融提纤单元,所述热解炉产生的部分热解气送入高温熔融炉。
32.如图1所示,所述高温熔融提纤单元30包括与所述热解炉依次相连的高温熔融炉、高速离心机、干排渣装置、湿排渣装置、牵引机、干燥机、热定型机,所述牵引机与所述干排渣装置、湿排渣装置的纤维出料端连接将除渣后的纤维送入干燥机。
33.所述高温熔融炉主要接收由热解炉热解得到的固体,也可接甩干后得到的部分固相组分,在燃气和富氧的作用下进行高温熔融加热,固体物料加热温度1500-2200℃,物料中有机物完全分解和燃烧,高温区的温度可以达到1800-2000℃;
34.进一步,所述高温熔融炉所需的纯氧来源于空分系统,产生的烟气先经过脱硝装置进行脱硝处理,脱硝后的高温烟气通过余热锅炉进行余热回收利用,再通过除尘系统收集烟气中的飞灰,然后对除尘后的烟气进行活性炭吸附以及脱硫处理,烟气达标后排放。
35.所述高速离心机用于接收所述高温熔融炉熔融液,通过上下交错布置的四级高速旋转圆盘高速旋转,实现熔融液快速成纤。自上而下第一辊直径150-200mm且转速为3800-4200r/min、第二辊直径220-300mm且转速为5000-5500r/min、第三辊直径350-400mm且转速为5500-6000r/min、第四辊直径350-400mm且转速为6000-7000r/min;
36.更进一步,所述干排渣装置、湿排渣装置用于接收所述高速离心机高速甩丝获得的纤维,通过气流干法排渣装置可将纤维中较大颗粒杂质分离,分离后的纤维在湿法排渣装置中进一步处理,可进一步将纤维中残留的细小颗粒进行分离,获得纤维品质达到98%以上的优质纤维;所述的牵引机与所述干湿排渣装置纤维出料端连接,通过将除渣后的纤维送入干燥机;所述干燥机与所述牵引机相连,干燥机设置温度为80-150℃,纤维经过干燥机后被加热干燥;所述热定型机用于接收被干燥后的纤维,实现纤维的热定型,获得可满足后段打包的定型纤维产品。
37.本实用新型采用绝氧热解装置对含油污泥进行绝氧热解,可获得油品能源,同时可避免含油污泥直接焚烧产生大量二噁英,另外获得的热解气属于清洁能源,直接燃烧的废气达锅炉排放标准。
38.高温熔融炉只对部分含有少量难分离有机物的无机物进行进一步燃烧,大大减少因直接焚烧原生含油污泥产生大量废气问题,同时高温熔融炉内不含或是只有极少量的有机物,可有效抑制二噁英的产生,另外可杜绝了属于危废飞灰的产生,降低了高温熔融过程中无机物的进料量,大大减少了整个高温熔融系统的能耗问题。通过高温熔融提纤系统可实现热解产生的固体物高温熔融,无机物转化为无毒性、高附加值的纤维产品,可用于建材、工业耐高温高强度要求产品中,另外获得可用于清洁燃烧的燃料气。送入高温熔融炉的热解气属于清洁燃气,燃烧产生废气能达到锅炉废气排放标准,从而显著降低了高温熔融炉废气处理成本。
39.本实用新型的还提供一种含油污泥高值化利用方法,如图2所示,所述含油污泥高值化利用方法包括如下步骤:
40.步骤a,对含油污泥进行热水洗搅拌,再通过振动筛分和甩干、离心分离,获得油、水和固三相组分;步骤b,经预处理后得到的固体产物送入热解炉当中进行绝氧热解,热解的固体残渣送入高温熔融炉中熔炼,获得的热解气为热解炉和高温熔融炉提供能量;步骤c,经高温熔融炉熔炼的液体通过高速离心机甩丝,获得纤维;步骤d,纤维依次经过排渣、牵
引、干燥和定型后获得纤维成品。
41.具体地,步骤a中在对含油污泥进行热水洗搅拌时,将含油污泥送入料斗装置进行暂存,向搅拌罐加入总体积三分之二的热水,并开启搅拌罐,向搅拌罐中加入暂存的含油污泥,在搅拌过程中加入总质量3~5%的硅酸钠药剂,且对搅拌罐进行恒温加热,确保稳定控制在65
±
5℃。
42.将含油污泥混合液在搅拌罐中搅拌20-30min后,送入振动筛中,开启振动筛,对含油污泥混合液进行筛分。振动筛设置上下两层,上层一级筛孔采用筛孔为20mm方形筛孔;下层二级筛孔采用筛孔为5mm方形筛孔。通过振动筛的振动作用,实现了固液分离,固体从筛网出料端筛出,筛分后的液体进入振动装置下部。
43.将二级振动筛分得到的固相送入甩干装置中进一步甩干处理,甩干装置分离的液相和振动分离后得到的液相均送入离心机当中,混合液在转速为4500rpm转速下离心分离,获得油、水和固三相。
44.将离心得到含有油分的固体组分,以及甩干后得到的固体送入热解炉,物料在热解炉的加热下,固体物中的有机物在500~650℃温度下进行干燥和热分解,产生油气混合物通过引风机送入油气冷却系统,冷凝得到的液态混合物以混合燃料油为主,送入油贮罐贮存外售;通过冷凝后的不凝气通过气体净化装置进行脱硫后返回至热解炉作为燃料供热解用。
45.热解产生的固体残渣直接送入高温熔融炉中,在燃气和富氧的作用下进行充分燃烧,熔融炉温度控制在1800℃~1900℃。产生的高温烟气先经过脱硝装置进行脱硝处理,然后通过除尘系统收集烟气中的粉尘,最后对除尘后的烟气进行活性炭吸附以及脱硫处理。
46.将熔融液垂直流入高速离心装置中,依次通过第一、二、三和四辊轮,四辊轮自上而下第一辊直径180mm且转速为3930r/min、第二辊直径250mm且转速为5120r/min、第三辊直径370mm且转速为5760r/min、第四辊直径370mm且转速为6400r/min;通过上下交错布置不同直径和转速的四级高速旋转圆盘高速旋转,实现熔融液快速成纤。
47.甩丝获得的纤维通过气流干法排渣装置分离纤维中较大颗粒杂质,分离后的纤维在湿法排渣装置中进一步处理,可进一步将纤维中残留的细小颗粒进行分离,获得纤维品质达到99%以上的优质纤维;干法排渣分离后的纤维在牵引装置作用下进入干燥进中,纤维在100~120℃的干燥机中进行干燥,脱除水分后送入热定型装置中进行热定型,获得的最终纤维产品打包存放。
48.本实用新型的整个工艺有机结合到一起,一方面通过分级处理工艺可有效避免因直接焚烧含油污泥导致无机物和水带走大量热,导致整个系统能源利用率低;另一方面既解决含油污泥因直接焚烧的污染问题,同时获得附加价值高的燃料油和纤维等能源产品,彻底实现了油泥危险废弃物完全资源化回收利用。
49.最后应当说明的是:以上实施例仅用以说明本实用新型的技术方案而非对其限制;尽管参照较佳实施例对本实用新型进行了详细的说明,所属领域的普通技术人员应当理解:依然可以对本实用新型的具体实施方式进行修改或者对部分技术特征进行等同替换;而不脱离本实用新型技术方案的精神,其均应涵盖在本实用新型请求保护的技术方案范围当中。