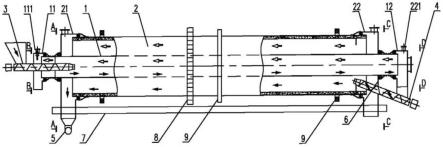
1.本实用新型属于污泥处理技术领域,特别涉及一种含油污泥热解与焚烧集成化的高效处理装置,可应用于含油污泥类危险废弃物减量化、无害化和资源化处置过程。
背景技术:2.含油污泥指石油钻采过程中产生的钻井废弃油基岩屑和落地油泥。钻井废弃油基岩屑是钻井中排放的含油泥浆和岩屑等形成的复杂多相体系,其浸出液有较高毒性。落地油泥是在石油钻井和井喷过程中,原油溢出、洒落或泄漏,渗入地面与土壤、砂石、水等形成的混合物。落地油泥含水率低,油泥中原油、泥砂含量比例变化大,且含有大颗粒砂石及杂物,密度大、粘度大、流动性差。含油污泥如果不及时处理会对周边土壤和地下水造成严重污染。因此,含油污泥的减量化、无害化和资源化处理是十分必要和迫切的。
3.目前,工程化应用的含油污泥处理技术包括热水化学清洗、调质-机械分离-筛分、离心等)、溶剂萃取、热解、焚烧等技术。同时,按照国家有关文件规定,含油率大于5%以上的应先回收原油。通常而言,热水化学清洗、调质-机械分离、溶剂萃取可将含油率降低至2%左右,热解和焚烧技术可以将含油率降低至0.3%以下。国内对含油污泥处理的标准提升为石油烃含量低于0.3%,热水化学清洗、调质-机械分离、溶剂萃取对含油污泥处置已经很难达到处理要求,尤其是,溶剂萃取生产成本较高,综合利用工艺技术复杂,热处理技术在其技术优势下成为最优选择。
4.然而,含油污泥经单独热解处理时,虽然能够回收含油污泥中的部分石油烃,但是总体综合能耗很高;含油污泥经单独焚烧时,虽然能够稳定达到处理指标,但是无法回收含油污泥中的石油烃,造成资源浪费,且存在二次污染风险。造成热解过程能耗大幅增加的主要原因是,由于含油污泥中的重质石油烃组分很难发生分解,要想达到总石油烃处理标准低于0.3%的标准,则必须大幅提高热解温度。对于轻质石油烃和水分而言,在较低热解温度下即可完成挥发脱除过程。除此之外,现有间接加热式热解回转窑长时间处于高温环境下,由于自身结构与材料强度限制,筒体经常出现“扭曲和弯折”问题,常规解决方法是采用耐高温不锈钢和提高筒体壁厚;增加了筒体传热热阻,降低了传热效率,增加运行成本。另外,对于单独采用含油污泥焚烧技术而言,当初始物料中有机组分过高,与明火接触时存在爆炸风险,过高的温度下也极易在筒壁上产生“结焦”现象。
5.热解与焚烧耦合联用技术可以克服现有含油污泥单独采用热解技术能耗过高,以及单独采用焚烧技术无法进行资源回收的“弊病”,但若只是把热解和焚烧简单串联在一起,虽然也能实现含油污泥中回收油品资源、尾渣无害化,但是热解和焚烧是两套独立设备,焚烧无法直接向热解提供热量,因此造成两套设备均能耗高,而且两套独立设备部件多运行维护量大。
技术实现要素:6.本实用新型的目的在于克服上述现有技术的不足,提供一种含油污泥热解与焚烧
集成化的高效处理装置,将热解和焚烧耦合进一套集成化设备中,含油污泥中易于热解脱附的石油烃类在内筒中发生热解脱附过程,其中难于热解的石油烃类在外筒内焚烧处置。本装置既能实现从含油污泥中回收油品资源和尾渣无害化,同时具有实现高效利用尾渣和废气余热高效利用的优点。
7.一种含油污泥热解与焚烧集成化的高效处理装置,包括:内筒、外筒、内筒窑头罩、内筒窑尾罩、外筒窑头罩、外筒窑尾罩、进料螺旋输送机、中转螺旋输送机、出渣螺旋输送机、燃烧器、撬装支架、链轮传动装置和支撑托轮,其中:
8.所述内筒通过多个滑动限位构件支撑固定于外筒内,工作时内筒随外筒在链轮传动装置的带动下一起转动,内筒内壁设有多根链条防结焦器;内筒窑头罩和内筒窑尾罩分别与内筒外壁间采用鱼鳞片面密封和弹簧压紧密封且不随内筒转动,内筒窑头罩设置有进料螺旋输送机接口、油气排放接口、温度和压力检测接口;内筒窑尾罩设置有中转螺旋输送机接口、内筒窑尾检修孔、温度和压力检测接口;进料螺旋输送机用螺栓固定于内筒窑头罩上,进料螺旋输送机出料口设置有收口锁气结构,用于防止进料时空气进入内筒并且确保内筒处于绝氧环境;
9.所述外筒设置有多个支撑托轮和一个链轮传动装置,倾斜一定角度置于撬装支架上,外筒内壁通过浇筑方式设置有耐火浇注料隔热保温层,耐火浇注料隔热保温层内表面设置有导向板;外筒窑头罩和外筒窑尾罩固定于撬装支架上,与外筒外壁间采用鱼鳞片面密封和弹簧压紧密封且不随内筒转动;外筒窑头罩设置有出渣螺旋输送机接口、检修孔、废气排放接口、温度和压力检测接口和内筒安装接口;外筒窑尾罩设置有中转螺旋输送机接口、燃烧器接口、助燃风接口、温度和压力检测接口和内筒安装接口;中转输送螺旋机用螺栓固定于内筒窑尾罩和外筒窑尾罩上并且将内筒的热解残渣输送至外筒焚烧;中转输送螺旋机出料口设置有收口锁气结构以防止内外筒气体互窜;燃烧器设置于内筒窑尾和外筒窑尾之间,驱动电机和减速机通过链轮传动装置为双套筒回转窑提供动力。
10.进一步的,所述进料螺旋输送机的一端固定螺旋,螺旋轴的长度小于螺旋外套筒长度,外筒设置有收口锁气结构以确保内筒处于绝氧环境。
11.含油污泥在内外筒发生不同反应,在内筒无氧环境下发生热解反应,在外筒富氧环境下热解残渣充分焚烧。油田产生的含油污泥通过进料螺旋输送机3送入内筒1,在内筒1绝氧环境下首先被间接加热发生热解反应,生成油气和热解残渣,油气从内筒窑头排出,并在冷凝器内冷却,可凝部分冷凝回收,不凝气部分返回燃烧器在外筒2内随天然气一起燃烧,热解残渣从内筒窑尾排出进入中转输送螺旋机4,通过中转螺旋输送机4送入外筒,热解残渣中的碳和未分解的重质石油烃在外筒内充分焚烧,焚烧后剩余尾渣从外筒窑头排出进入出渣输送螺旋机5冷却排放。燃烧器6安装于内外筒之间,燃烧器采用长焰和短焰两种,从窑头罩和窑尾罩喷入内筒与外筒之间的夹层内,既加热内筒,又促使热解残渣中的炭充分燃烧。
12.上述含油污泥热解与焚烧集成化的高效处理装置的工作过程如下:
13.步骤一:依次开启回转窑驱动装置、引风机、助燃风机,燃烧器点火,预热回转窑内外筒,采用阶梯升温,升温速率保持50℃/h,阶梯升温至600℃;
14.步骤二:开启制氮机向内筒通入氮气置换空气,氮气置换运行时间30min;
15.步骤三:开启进料螺旋输送机将含油污泥送入内筒内,同时开启抽气风机,维持内
筒负压在-150~-50pa之间;抽气风机抽出的油气经冷凝器冷却,可凝部分冷凝回收,不可凝部分返回外筒焚烧;焚烧废气经过烟气净化装置进一步处理后达标排放;
16.步骤四:开启中转螺旋输送机和出渣螺旋输送机,内筒热解残渣经过中间螺旋输送机送入外筒焚烧;焚烧后的尾渣通过出渣螺旋输送机冷却排出;出渣送至尾渣暂存间,进行检测验收;
17.步骤五:含油污泥在内筒无氧环境下依次进行干燥、汽化脱附、裂解气化、碳化;在外筒富氧环境下依次进行焚烧、降温、尾渣排出。
18.本实用新型提供的设备采用的内外套筒结构设计,将无氧热解和有氧焚烧相耦合,经集成化设备处理后的物料能够稳定达标(石油烃含量低于0.3%),且单套设备产能大幅提升(处理量达到10~15t/h),有效减少了二次污染和能源浪费问题。同时,整套设备采用模块化和撬装化设计,驱动装置少,结构紧凑,易于模块化布置,尺寸适中,占地面积小,便于整体运输与安装。本实用新型提供的设备采用外筒多点支撑内筒的结构,使得可采用薄壁普通不锈钢筒替代厚壁耐高温不锈钢筒,降低制造和运行成本的同时还解决了在高温环境下常规筒体发生“扭曲和弯折”的问题;且其传热性能大大提高,物料受热均匀出料一致性好,设备体积更紧凑,设备制造成本有效降低,能耗低,生产效率高,运行安全可靠,工艺调节操作灵活可靠。
19.此外,燃烧器布置于内外筒窑尾之间使得整套装置窑尾温度最高,内外筒内温度均是从窑尾至窑头逐渐降低,含油污泥进入内筒从窑头向窑尾运动过程温度逐渐升高,含油污泥升温过程中依次发生干燥、低温热解、中温热解、高温热解和碳化,有利于含油污泥中不同油品从低温到高温逐渐脱附热解,有效解决了含油污泥中的油品因温度过高裂解气化,导致油品回收率降低的问题。热解残渣从外筒窑尾进入,处于富氧状态下,热解残渣中的可燃物可充分燃烧,既能给内筒热解提供部分热量还能深度处理其中的残碳和剩余总石油烃;外筒内废气和焚烧残渣向窑头流动,与内筒里的低温含油污泥通过间接热交换逐渐降温冷却,最后焚烧残渣和废气从外筒窑头排出。内筒含油污泥与外筒废气和焚烧残渣逆向流动最大限度的利用了焚烧残渣与废气中的余热量,实现热量的充分利用,起到协同降耗的作用。
附图说明
20.图1是含油污泥热解与焚烧集成化的高效处理装置的剖示意图,其中,空心箭头表示油气移动路线,实心箭头表示物料移动路线;
21.图2是图1中a-a截面视角端面示意图;
22.图3是图1中b-b截面视角端面示意图;
23.图4是图1中c-c截面视角端面示意图;
24.图5是图1中d-d截面视角端面示意图;
25.附图标记说明:
26.内筒-1、内筒窑头罩-11、内筒窑尾罩-12、内筒窑头油气排放接口-111、内筒窑头温度和压力检测接口-112、内筒窑尾检修孔-121、内筒窑尾温度和压力检测接口-122、内筒窑尾热解残渣排口-123;
27.外筒-2、外筒窑头罩-21、外筒窑尾罩-22、外筒窑头废气排放口-211、外筒窑头焚
烧残渣排放口-212、外筒窑头温度和压力检测接口-213、外筒窑头检修孔-214、外筒窑尾燃烧器接口-221、外筒窑尾助燃风接口-222、外筒窑尾温度和压力检测接口-223、外筒窑尾检修孔-224、外筒窑尾中转螺旋输送机接口-225;
28.进料螺旋输送机-3、中转螺旋输送机-4、出渣螺旋输送机-5、燃烧器-6、撬装支架-7、链轮传动装置-8、支撑托轮-9。
具体实施方式
29.为使本领域的技术人员更好地理解本实用新型的技术方案,下面结合实施例对本实用新型提供的一种含油污泥热解与焚烧集成化的高效处理装置进行详细描述。以下实施例仅用于说明本实用新型而非用于限制本实用新型的范围。
30.实施例1
31.如图1所示,本实用新型提供含油污泥热解与焚烧集成化的高效处理装置,包括:内筒1、外筒2、内筒窑头罩11、内筒窑尾罩12、外筒窑头罩21、外筒窑尾罩22、进料螺旋输送机3、中转螺旋输送机4、出渣螺旋输送机5、燃烧器6、撬装支架7、链轮传动装置8和支撑托轮9等。
32.内筒1通过多个滑动限位构件支撑固定于外筒2内,工作时内筒1随外筒2在链轮传动装置的带动下一起转动,内筒1内壁设有多根链条防结焦器;内筒窑头罩11和内筒窑尾罩12分别与内筒外壁间采用鱼鳞片面密封和弹簧压紧密封且不随内筒转动。内筒窑头罩11设置有进料螺旋输送机接口、油气排放接口、温度和压力检测接口。内筒窑尾罩设置有中转螺旋输送机接口、内筒窑尾检修孔、温度和压力检测接口。进料螺旋输送机3用螺栓固定于内筒窑头罩11上,进料螺旋输送机3出料口设置有收口锁气结构,用于防止进料时空气进入内筒并且确保内筒处于绝氧环境。
33.外筒2设置有多个支撑托轮和一个链轮传动装置8,倾斜一定角度置于撬装支架7上。外筒2内壁通过浇筑方式设置有耐火浇注料隔热保温层,耐火浇注料隔热保温层内表面设置有导向板。外筒窑头罩21和外筒窑尾罩22固定于撬装支架7上,与外筒2外壁间采用鱼鳞片面密封和弹簧压紧密封且不随内筒转动。外筒窑头罩21设置有出渣螺旋输送机接口、检修孔、废气排放接口、温度和压力检测接口和内筒安装接口。外筒窑尾罩22设置有中转螺旋输送机接口、燃烧器接口、助燃风接口、温度和压力检测接口和内筒安装接口。中转输送螺旋机4用螺栓固定于内筒窑尾罩和外筒窑尾罩上并且将内筒的热解残渣输送至外筒焚烧;中转输送螺旋机4出料口设置有收口锁气结构以防止内外筒气体互窜。燃烧器6设置于内筒窑尾和外筒窑尾之间,驱动电机和减速机通过链轮传动装置为双套筒回转窑提供动力。进料螺旋输送机3的一端固定螺旋,螺旋轴的长度小于螺旋外套筒长度,外筒设置有收口锁气结构以确保内筒处于绝氧环境。
34.含油污泥在内外筒发生不同反应,在内筒无氧环境下发生热解反应,在外筒富氧环境下热解残渣充分焚烧。油田产生的含油污泥通过进料螺旋输送机3送入内筒1,在内筒1绝氧环境下首先被间接加热发生热解反应,生成油气和热解残渣,油气从内筒窑头排出,并在冷凝器内冷却,可凝部分冷凝回收,不凝气部分返回燃烧器在外筒2内随天然气一起燃烧,热解残渣从内筒窑尾排出进入中转输送螺旋机4,通过中转螺旋输送机4送入外筒,热解残渣中的碳和未分解的重质石油烃在外筒内充分焚烧,焚烧后剩余尾渣从外筒窑头排出进
入出渣输送螺旋机5冷却排放。燃烧器6安装于内外筒之间,燃烧器采用长焰和短焰两种,从窑头罩和窑尾罩喷入内筒与外筒之间的夹层内,既加热内筒,又促使热解残渣中的炭充分燃烧。
35.该套集成化装备正式运行时,依次开启链轮传动装置、引风机、助燃风机,并启动燃烧器点火,开始对回转窑内外筒进行预热,采用阶梯升温,升温速率保持50℃/h,阶梯升温至600℃。随后,开启制氮机向内筒通入氮气置换空气,氮气置换运行时间为30min。
36.针对青海某油田产生的含油污泥,测试初始含油率在20~25%之间,初始含水率在20~30%,将油泥暂存池内的含油污泥取出后送入称量系统,称量系统设有质量传感器和电机转速传感器,在本地控制柜和中控室,均可根据生产需要调整进料量设定值,程序根据设定值自动调整皮带秤转速实现进料量的稳定控制。
37.含油污泥经过上料皮带输送至油泥进料仓,通过进料螺旋输送机向内筒输送。开启进料螺旋输送机将含油污泥送入内筒内,同时开启抽气风机,维持内筒负压在-150~-50pa之间。抽气风机抽出的油气经冷凝器冷却,可凝部分冷凝回收,不可凝部分返回外筒焚烧,焚烧废气经过烟气净化装置进一步处理后达标排放。
38.含油污泥在内筒内进行无氧热解反应,含油污泥在内筒无氧环境下依次发生干燥
→
汽化脱附
→
裂解气化
→
碳化。经过内筒后的物料,总石油烃含量下降至2%左右,此时出料的温度仅为200~250℃,相较于单独使用热解技术达到0.3%的标准时的400~450℃,出料温度大幅下降,有利于降低热解过程的综合能耗。从内筒出来的残渣,再经中转螺旋输送机被转运至外筒内进行焚烧,热解残渣从外筒窑尾进入,处于富氧状态下,热解残渣中的可燃物可充分燃烧,既能给内筒热解提供部分热量还能深度处理其中的残碳和剩余总石油烃;外筒内废气和焚烧残渣向窑头流动,与内筒里的低温含油污泥通过间接热交换逐渐降温冷却,最后焚烧残渣和废气从外筒窑头排出。焚烧后的尾渣通过出渣螺旋输送机冷却排出,出渣送至尾渣暂存间,进行检测验收。设备稳定运行后,检测最终出料中总石油烃含量低于0.3%,且处理量稳定在12t/h左右,设备处理效率和处理能力显著优于现有设备。
39.热解与焚烧耦合联用技术可以克服现有含油污泥单独采用热解技术能耗过高,以及单独采用焚烧技术无法进行资源回收的“弊病”,但若只是把热解和焚烧简单串联在一起,虽然也能实现含油污泥中回收油品资源、尾渣无害化,但是热解和焚烧是两套独立设备,焚烧无法直接向热解提供热量,因此造成两套设备均能耗高,而且两套独立设备部件多运行维护量大。本实用新型将热解和焚烧耦合进一套集成化设备中,在本套设备内,含油污泥中易于热解脱附的石油烃类在内筒中发生热解脱附过程,其中难于热解的石油烃类在外筒内焚烧处置,因此本装置即能实现从含油污泥中回收油品资源和尾渣无害化,同时实现高效利用尾渣和废气余热高效利用的优点。
40.上面结合实施例对本实用新型的实例作了详细说明,但是本实用新型并不限于上述实例,在本领域普通技术人员所具备的知识范围内,还可以在不脱离本实用新型宗旨的前提下作出的各种变化,也应视为本实用新型的保护范围。