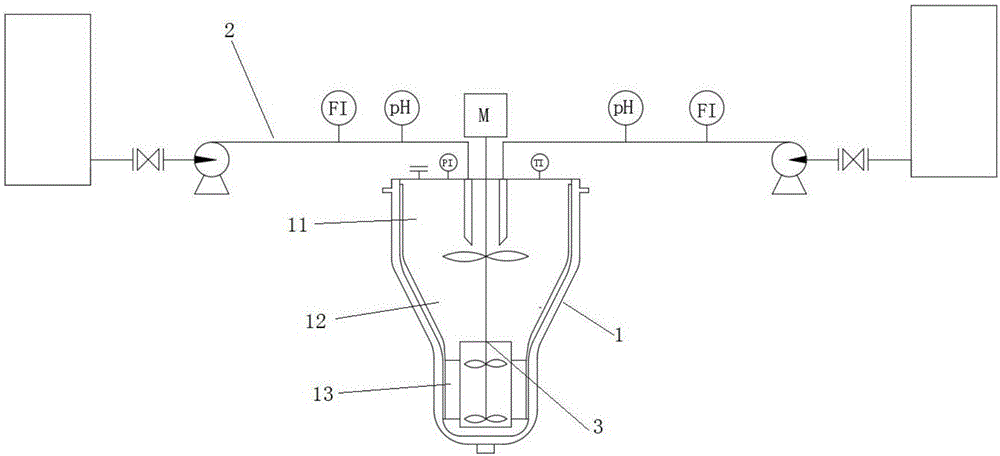
本发明属于反应釜
技术领域:
,具体涉及一种用于制备大比重和大颗粒晶体的反应装置。
背景技术:
:反应器是化工、冶金常用设备,按结构大致可分为管式、釜式、塔式、固定床和流化床等类型。现有的技术投入成本低,操作简单,在传统搅拌浸渍罐的原型基础上,仅通过调整反应釜高度与反应釜直径之比,以达到稳定或改变搅拌状态的目的,其获得的晶体颗粒较均匀,但是不能获得大颗粒大比重的晶体颗粒。技术实现要素:为了克服现有技术的不足,本发明的目的旨在提供一种用于制备大比重和大颗粒晶体的反应装置。本发明的技术方案是这样实现的:本发明实施例提供一种用于制备大比重和大颗粒晶体的反应装置,其包括反应罐、进料机构和搅拌机构,所述反应罐的顶部设置至少一个进料机构,所述搅拌机构设置在反应罐内;所述反应罐的腔体由上至下分为第一区域、第二区域和第三区域,所述第三区域的直径小于第一区域的直径用于加快晶体颗粒的富集。优选地,所述第一区域与第三区域的直径比为1:1~5:1,所述第一区域的高度与第二区域和第三区域的高度和的比值为1:1~5:1。优选地,所述搅拌机构包括搅拌电机、搅拌轴、搅拌桨组件、导流筒和挡板,所述搅拌电机设置在反应罐的顶部,所述搅拌桨组件设置在反应罐内并且通过搅拌轴与搅拌电机连接,所述导流筒设置在反应罐内并且位于第三区域,所述挡板沿反应罐内壁的轴向设置,所述挡板的一端固定于反应罐的内壁,另一端向水平方向弯折并且用于连接所述导流筒。优选地,所述搅拌桨组件包括由上至下依次设置的第一搅拌桨、第二搅拌桨和第三搅拌桨,所述第二搅拌桨和第三搅拌桨均位于导流筒内。优选地,所述第一搅拌桨、第二搅拌桨和第三搅拌桨的直径均为反应罐底部直径的30~70%,所述第一搅拌桨、第二搅拌桨和第三搅拌桨均为45°倾斜度的四叶搅拌桨,所述第三搅拌桨与反应罐底壁的距离大于第三搅拌桨的直径的0.5倍。优选地,所述导流筒的直径为反应罐底部直径的40~80%,导流筒的高度为底部第三搅拌桨333的直径的1~6倍。优选地,所述挡板的数量为1~6个,所述挡板的宽度与反应罐的直径的比值为1:10~1:50。优选地,所述反应罐的顶部开设有至少一个与进料机构配合的进料管口、温度计放置口、压力表放置口和人孔,所述反应罐的底部开设有出料口,所述反应罐的外层设置有循环介质夹层,所述循环介质夹层设置有循环介质进口和循环介质出口。优选地,所述进料机构包括储料槽和进料管,所述进料管用于连接储料槽和进料管口,所述进料管上设置有阀门、泵、流量计和ph计。优选地,还包括温控单元,所述温控单元包括水浴循环单元、蒸汽加热单元和温度计,所述水浴循环单元和蒸汽加热单元均通过管路与循环介质夹层连通,所述管路设置有阀门;所述温度计设置于温度计放置口内并且与水浴循环单元和蒸汽加热单元联动。与现有技术相比,本发明实施例提供一种用于制备大比重和大颗粒晶体的反应装置,其包括反应罐、进料机构和搅拌机构,所述反应罐的顶部设置至少一个进料机构,所述搅拌机构设置在反应罐内;所述反应罐的腔体由上至下分为第一区域、第二区域和第三区域,所述第三区域的直径小于第一区域的直径用于加快晶体颗粒的富集,这样,本发明通过对反应罐特殊几何空间、进料机构和搅拌机构的综合设计,使晶体在第一区域成核,成核后进入第二区域,待生长到一定程度后,固体颗粒沉降至第三区域的底部,由于第三区域的直径小于第一区域,有助于加快固体颗粒的富集,随着底部固体颗粒的富集,物质浓度增大,使其过饱和区域与饱和溶解度曲线之间的亚稳区的区间会变大,有利于颗粒的生长,从而得到大比重、大颗粒晶体。附图说明图1为本发明实施例用于制备大比重和大颗粒晶体的反应装置的结构示意图简图;图2为本发明实施例用于制备大比重和大颗粒晶体的反应装置的结构示意图;图3为本发明实施例用于制备大比重和大颗粒晶体的反应装置的反应罐的结构示意图;图4为本发明实施例用于制备大比重和大颗粒晶体的反应装置的进料机构的结构示意图;图5为本发明实施例用于制备大比重和大颗粒晶体的反应装置的搅拌机构的结构示意图;图6为本发明实施例用于制备大比重和大颗粒晶体的反应装置的温控单元的结构示意图。附图标记如下:1——反应罐、11——第一区域、12——第二区域、13——第三区域、14——进料管口、15——温度计放置口、16——压力表放置口、17——人孔、18——出料口、19——循环介质夹层、191——循环介质进口、192——循环介质出口、2——进料机构、21——储料槽、22——进料管、23——阀门、24——泵、25——流量计、26——ph计、3——搅拌机构、31——搅拌电机、32——搅拌轴、33——搅拌桨组件、331——第一搅拌桨、332——第二搅拌桨、333——第三搅拌桨、34——导流筒、35——挡板、4——温控单元、41——水浴循环单元、42——蒸汽加热单元、43——温度计。具体实施方式为了使本发明的目的、技术方案及优点更加清楚明白,以下结合附图及实施例,对本发明进行进一步详细说明。应当理解,此处所描述的具体实施例仅仅用以解释本发明,并不用于限定本发明。本发明实施例提供一种用于制备大比重和大颗粒晶体的反应装置,如图1和2所示,其包括反应罐1、进料机构2和搅拌机构3,所述反应罐1的顶部设置至少一个进料机构2,所述搅拌机构3设置在反应罐1内;所述反应罐1的腔体由上至下分为第一区域11、第二区域12和第三区域13,所述第三区域13的直径小于第一区域11的直径用于加快晶体颗粒的富集。本发明通过对反应罐特殊几何空间、进料机构和搅拌机构的综合设计,使晶体在第一区域成核,成核后进入第二区域,待生长到一定程度后,固体颗粒沉降至第三区域的底部,由于第三区域的直径小于第一区域,有助于加快固体颗粒的富集,随着底部固体颗粒的富集,物质浓度增大,使其过饱和区域与饱和溶解度曲线之间的亚稳区的区间会变大,有利于颗粒的生长,从而得到大比重、大颗粒晶体。反应罐1的材质可根据反应体系的不同进行选择,常用的反应罐的材质有:硼硅玻璃、不锈钢、石英、合金等。所述第一区域11与第三区域13的直径比为1:1~5:1,所述第一区域11的高度与第二区域12和第三区域13的高度和的比值为1:1~5:1。所述反应罐1的顶部开设有至少一个与进料机构2配合的进料管口14、温度计放置口15、压力表放置口16和人孔17,所述反应罐1的底部开设有出料口18,所述反应罐1的外层设置有循环介质夹层19,所述循环介质夹层19设置有循环介质进口191和循环介质出口192。具有特殊的几何空间的反应罐1为该反应装置的主体设备,从外形上看,上宽下窄,第一区域11直径较大,有助于反应初期晶体的成核,第三区域13的直径明显小于第一区域11,第二区域12为尺寸过渡区,这样,经过第二区域12悬浮区的充分搅拌,使成核的晶粒沉降至第三区域13,由于第三区域13的直径的急剧减小,加快了成核的晶粒的富集,随着底部固体颗粒的富集,物质浓度增大,使其过饱和区域与饱和溶解度曲线之间的亚稳区的区间会变大,有利于成核的晶粒继续生长,从而获得大比重、大颗粒晶体;反应罐1顶部上设计有多个进料管口14,温度计放置口15、压力表放置口16以及人孔17,便于监测反应罐1内反应体系的状态,进料管口14采用0~85°斜角的背向进料方式,使带反应的料液处于搅拌中心,有助于料液的混合及反应;底部设置出料口18,出料口18可以根据需求与压滤机或浓密器等设备连通;反应罐1的外层设置有循环介质夹层19,用于与温控单元4相连接,能够通过温控单元4对反应罐1进行蒸汽加热、水浴加热或水浴冷却。所述进料机构2包括储料槽21和进料管22,所述进料管22用于连接储料槽21和进料管口14,所述进料管22上设置有阀门23、泵24、流量计25和ph计26。阀门23和泵24的设置用于控制进料机构2的开启和闭合,进料管22上流量计25和ph计26的设置,用于监控料液的流量及流速;储料槽21材质选择原则是不对原料造成污染且价格优廉,一般根据料液的性质来决定,常用的储槽材质有pp、玻璃钢、不锈钢等;阀门23的类型可选择为截止阀、球阀、蝶阀等;阀门23端部可采用螺纹连接、法兰连接和焊接端部连接;阀门23主要零部件材质的选择需考虑工作介质的温度、压力等物理性能和腐蚀性等化学性能,同时还应考虑介质中是否含有固体颗粒等综合因素;泵24为进料泵,进料泵的型式和性能需符合反应装置的流量、扬程、压力、温度、汽蚀流量、吸程等工艺参数的要求,一般选用离心泵,扬程很高时,可考虑容积式泵或高速泵;流量计25可选用转子流量计、旋涡流量计、超声波流量计等;ph计26为在线ph计,需综合考虑被测介质的物理和化学性质,电极安装方式、电极信号线长度等,常用的品牌有梅特勒-托利多、雷磁、上海三信、横河等。进料机构2中的泵24、流量计25、ph计26等设备的联动,可有效的精确的控制进料流量;进料管安装位置和进料管管口的特殊设计,可有效控制反应器中反应物的浓度;所述搅拌机构3包括搅拌电机31、搅拌轴32、搅拌桨组件33、导流筒34和挡板35,所述搅拌电机31设置在反应罐1的顶部,所述搅拌桨组件33设置在反应罐1内并且通过搅拌轴32与搅拌电机31连接,所述导流筒34设置在反应罐1内并且位于第三区域13,所述挡板35沿反应罐1内壁的轴向设置,所述挡板35的一端固定于反应罐1的内壁,另一端向水平方向弯折并且用于连接所述导流筒34。搅拌机构3通过搅拌电机31的频率来实现控制搅拌轴32和搅拌桨组件33的转数,使反应体系完全混合。所述搅拌桨组件33包括由上至下依次设置的第一搅拌桨331、第二搅拌桨332和第三搅拌桨333,所述第二搅拌桨332和第三搅拌桨333均位于导流筒34内。所述第一搅拌桨331、第二搅拌桨332和第三搅拌桨333的直径均为反应罐1底部直径的30~70%,所述第一搅拌桨331、第二搅拌桨332和第三搅拌桨333均为45°倾斜度的四叶搅拌桨,所述第三搅拌桨333与反应罐1底壁的距离大于第三搅拌桨333的直径的0.5倍。搅拌桨组件33的搅拌桨的数量可以根据反应罐1内料液的体积进行增减,当反应罐1所盛液体的高度大于第三搅拌桨333直径的3倍时,需要增加第二搅拌桨332,当反应罐1所盛液体的高度为第三搅拌桨333的直径的6倍以上(包括6倍)需要增加第一搅拌桨331,位于上层的搅拌桨距离液面的高度不得低于搅拌桨直径的0.5倍;若采用三个搅拌桨时,所述第一搅拌桨331与进料管口14的距离大于5mm。挡板35是沿反应罐1的内壁轴向安装的窄长形板,挡板35的数量、宽度和安装方位角对搅拌操作会有影响,流体流动时湍流程度越高,所消耗的搅拌功率也越大,而当挡板35的几何尺寸和数量达到一定数值后,再增加挡板35的宽度和数量,搅拌功率也不再增大;挡板的宽度和反应罐的直径的比值与能耗的关系,如下表所示:挡板35的宽度设计取决于介质的粘度,挡板35的宽度和反应罐的直径的比值与介质黏度的关系,如下表所示:一般使用的挡板数量为1~6个。挡板宽度/反应罐直径介质粘度/cp1/12水1/1850001/24100001/4820000所述导流筒34的直径为反应罐1底部直径的40~80%。导流筒34直接焊接在反应罐1的挡板35的端部,导流筒34的高度为底部搅拌桨17的直径的1~6倍,导流筒的直径是反应器底部直径的40~80%。搅拌机构3中的搅拌桨层数根据溶液的高度进行设计、桨板桨叶的直径依据反应罐的直径进行设计、导流筒的高度依据搅拌桨的高度进行设计、导流筒的直径依据反应罐底部直径进行设计,可有效控制反应物的混合程度和混合时间,有利于控制晶体的成核速度和生长环境。还包括温控单元4,所述温控单元4包括水浴循环单元41、蒸汽加热单元42和温度计43,所述水浴循环单元41和蒸汽加热单元42均通过管路与循环介质夹层19连通,所述管路设置有阀门;所述温度计43设置于温度计放置口15内并且与水浴循环单元41和蒸汽加热单元42联动。水浴循环单元41用于对反应罐1内的料液进行加热或冷却。反应罐1外层有循环介质夹层19,可用于蒸汽加热和水浴加热或冷却,温度计43与水浴循环单元41和蒸汽加热单元42联动,可精确控制反应体系的温度,使反应体系温度保持均匀一致,有效解决局部过冷或过热而影响晶体的成核和生长;温度计43同时与冷却单元联动,可设置温度冷却速率,可使降温速度与晶体成核、生长速度相匹配,使晶体生长得均匀。本发明实施例提供一种用于制备大比重和大颗粒晶体的反应装置,其包括反应罐、进料机构和搅拌机构,所述反应罐的顶部设置至少一个进料机构,所述搅拌机构设置在反应罐内;所述反应罐的腔体由上至下分为第一区域、第二区域和第三区域,所述第三区域的直径小于第一区域的直径用于加快晶体颗粒的富集,这样,本发明设置了精确的温控单元、进料机构、搅拌机构等辅助机构,以及特殊几何空间的反应罐主体设备,外形结构紧凑、美观、适用性强;通过对反应罐特殊几何空间、进料机构和搅拌机构的综合设计,使晶体在第一区域成核,成核后进入第二区域,待生长到一定程度后,固体颗粒沉降至第三区域的底部,由于第三区域的直径小于第一区域,有助于加快固体颗粒的富集,随着底部固体颗粒的富集,物质浓度增大,使其过饱和区域与饱和溶解度曲线之间的亚稳区的区间会变大,有利于颗粒的生长,从而得到大比重、大颗粒晶体。本发明具有以下有益效果:1、进料机构的设置,使其具备精确控制进料流量能力,以控制反应体系的浓度;2、温控单元的设置,使其具备精确控制温度的能力,使反应体系的温度要保持均匀一致,以防止局部过冷或过热,影响晶体的成核和生长;并且具备精确的冷却循环机构,使降温速度与晶体成核、生长速度相匹配,使晶体生长得均匀;3、反应罐的特殊结构以及搅拌机构的设置,使其具备控制反应速度的能力,降低结晶速度,以防止自发成核的出现,避免自发成核的晶体生产许多细小的晶核,从而获得大颗粒大比重的晶体。以上所述,仅为本发明的较佳实施例而已,并非用于限定本发明的保护范围。当前第1页12