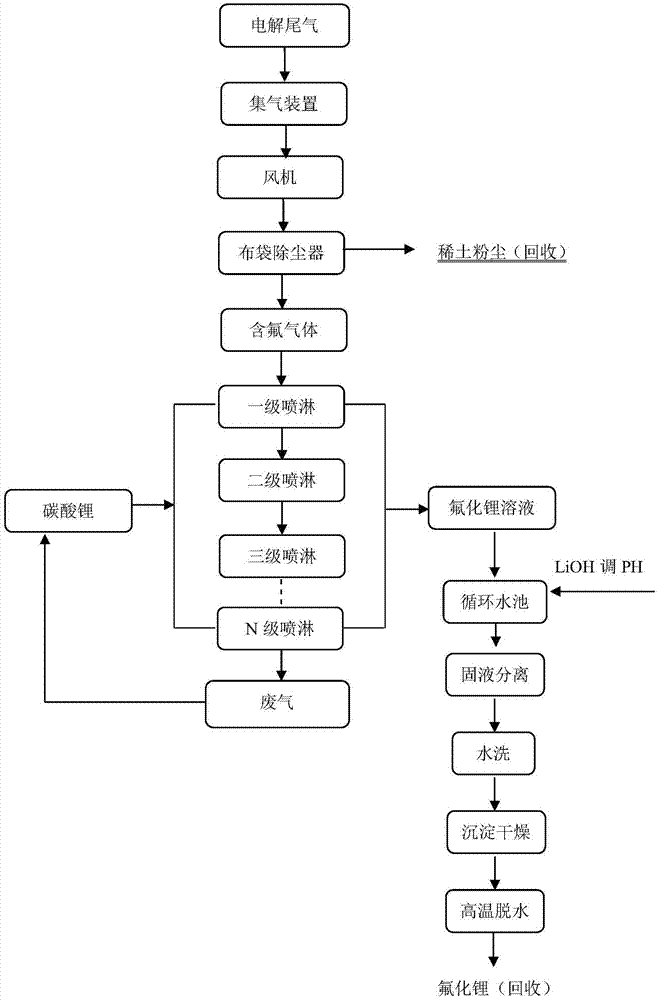
本发明涉及一种氟化物体系电解稀土废气回收利用的方法,属于环境保护及资源回收再利用领域。
背景技术:
:在稀土金属的冶炼过程中,产生的废气主要成分为二氧化碳和少量含氟气体。目前,我国稀土金属冶炼企业处理废气的方法主要有干法和湿法两种工艺。干法处理工艺为:稀土金属冶炼过程中产生的废气先经过捕捉收集,再经过重力沉降、旋风除尘、布袋除尘等去除废气中的稀土粉尘后,使用氧化钙或氢氧化钙与废气中的氟离子反应生产氟化钙,实现除尘、除氟,达到环保排放要求。此工艺能回收大部分的稀土粉尘,处理工艺相对简单,无需二次处理,但会造成氟资源的浪费,如申请号为02114820.1的中国发明专利公开了一种从氟化体系熔盐电解稀土金属废气中除氟除尘的方法,其采用向电解产生的废气中通入氨气,促使氟生产氟化氨细小颗粒后与粉尘一起沉降、过滤处理,废气达标后排放,此种干法处理工艺直接造成了氟资源的浪费。湿法处理工艺为:稀土金属冶炼过程中产生的废气经收集后,直接进入喷淋塔进行除尘、除氟,一级喷淋废气中粉尘及氟离子浓度较高,需经过两级以上喷淋才能达到排放要求,使用6%的氢氧化钠、碳酸钠、碳酸氢钠溶液捕捉负离子,与氟离子反应生成氟化钠。氟化钠容易结晶浓度不宜过高,且属于危险废物,需要用氧化钙或氢氧化钙二次处理,使用氢氧化钙与氟化钠反应生成氟化钙与氢氧化钠,氟化钙沉淀经沉淀、过滤去除,上清液氢氧化钠溶液进入喷淋塔使用。此工艺得到的稀土粉尘中含有一定的氟化钠,不能直接使用,并且该粉尘加工氧化稀土处理工艺复杂,增加了处理废气过程的环保压力;同时由于氟化钠易结晶,容易造成喷淋塔堵塞,设备维护保养难度大,且生成的氟化钠存在二次污染的可能,需要用氧化钙或氢氧化钙二次处理,工艺繁杂,效率低。综上,稀土金属冶炼废气的干法处理工艺和湿法处理工艺都是利用碱性物质脱氟,其最终虽然都可以生成无害物质,然而产出的氟化物利用价值不大,在一定程度上造成了氟资源的浪费。技术实现要素:针对上述现有技术存在的问题,本发明的目的是提供一种处理过程简单安全、可以降低处理成本,且不会对设备造成损害,处理后得到的物质能够被循环利用的氟化物体系电解稀土废气回收利用的方法。为实现上述目的,本发明采用的技术方案是:一种氟化物体系电解稀土废气回收利用的方法,包括如下步骤:步骤一:利用集气装置对于稀土电解过程中产生的尾气进行收集,收集的尾气经由利用风机产生负压的集气管道进入布袋式除尘器或烧结板除尘器中进行稀土粉尘与废气的初步分离,分离出的稀土粉尘用容器进行盛装回收,剩余的含氟气体进入下一步骤;步骤二:将含氟气体通入吸收剂为碳酸氢锂的喷淋吸收塔中进行化学吸收,经化学吸收后,碳酸氢锂与含氟气体中的氟离子发生化学反应,反应按如下的化学式一进行:lihco3+hf→lif+h2o+co2;生成的氟化锂溶液被收集进入循环水池中,在收集过程中测试循环水池的ph值,并向循环水池中加入氢氧化锂溶液调节ph值至3,然后通过循环水池侧壁上设置的水位控制阀缓慢放出上清液,放出上清液后对循环水池中余下的溶液进行多次固液分离和水洗,至水洗液的ph达到6-7时收集沉淀,对沉淀进行初步干燥脱水处理,干燥温度105-110℃,干燥时间3-7小时;然后在420-450℃烘干3-10小时,得到成品氟化锂,其中水洗液导入循环水池中重复利用;步骤三:将经喷淋吸收塔化学吸收后的废气直接导入碳酸锂料液池中,其中废气中和经化学式一反应后得到的二氧化碳与碳酸锂料液池中的碳酸锂反应,使碳酸锂转化成溶解度大的碳酸氢锂,化学反应式如下:li2co3+h2o+co2→2lihco3,将转化得到的碳酸氢锂溶液注入喷淋吸收塔中作为喷淋液循环使用,继续捕获含氟气体中的氟离子。本发明的喷淋吸收塔在使用时可以直接向其中投入碳酸氢锂作为吸收剂,作为本发明的一个优选的方案,所述步骤二中喷淋吸收塔吸收剂的形成方式是:预先向喷淋吸收塔循环水中加入固态碳酸锂使其溶解,通入含氟气体后,其中的二氧化碳使碳酸锂转化形成碳酸氢锂吸收剂。采用这样的方式可以更加充分地利用含氟气体中的二氧化碳,促进温室气体的减排。优选的,上述方案中所述碳酸锂的投入量占形成的碳酸氢锂吸收剂的质量分数为5-20wt%。更优选的,所述碳酸锂的投入量占形成的碳酸氢锂吸收剂的质量分数为7-15wt%。喷淋吸收塔一般设置为2-5级,为了保证化学反应的充分进行,本发明的喷淋吸收塔设为五级,含氟气体从一级喷淋进入,至最后一级喷淋塔后达标导入碳酸锂料液池。作为本发明的另一个优选的方案,所述步骤二中干燥温度110℃,干燥时间3-7小时;然后在450℃烘干7-10小时。采用上述参数最终氟化锂的综合收率可达98.50%以上。相对于现有技术,本发明具有如下优势:(1)本发明在电解尾气处理过程中,使用布袋除尘或板式除尘分离稀土粉尘与含氟废气,并利用碳酸氢锂作为氟离子的捕捉剂,碳酸氢锂溶解度大,保证了对氟离子具有更好的吸附效果,经检测回收的lif纯度达到了99.0%,得到的氟化锂能够再次被工业电解使用,充分回收利用了氟资源,避免了氟资源的浪费和直接排放对环境的污染破坏;经吸收后废气中和化学反应式一生成的二氧化碳直接作为原料通入碳酸锂料液池中循环制造出碳酸氢锂吸收剂,大大减少了二氧化碳的排放、节省了原料成本,经检测,基本实现了二氧化碳的零排放、对温室效应的控制改善具有重大意义;此外,处理过程中的水洗液导入循环水池中也可以重复利用,节约了水资源;(2)本发明操作过程相对简单、对设备的要求不高,具有较好的经济价值,经30天的化学吸收后,综合收率可以达到84.50%,体系到反应完全平衡后综合收率在96%以上;且处理过程无二次污染、不会产生有害物质,从而不会损坏处理设备,实现了稀土粉尘和工业用氟化锂的回收利用,可为企业环保建设增添动力,同时循环过程中的二氧化碳直接作为反应原料、为二氧化碳的减排作出了较大贡献,应用到工业生产中能够获得经济效益与环保治理的双赢。附图说明图1是本发明的工艺流程图;具体实施方式下面结合附图和实施例对本发明作进一步详细说明。如图1所示,本发明氟化物体系电解稀土废气回收利用的方法,包括如下步骤:步骤一:利用集气装置对于稀土电解过程中产生的尾气进行收集,收集的尾气经由利用风机产生负压的集气管道进入布袋式除尘器或烧结板除尘器中实现稀土粉尘与废气的分离,分离出的稀土粉尘用容器进行盛装回收,剩余的含氟气体进入下一步骤;步骤二:将含氟气体通入吸收剂为碳酸氢锂的喷淋吸收塔中进行化学吸收,经化学吸收后,碳酸氢锂与含氟气体中的氟离子发生化学反应,化学反应式如下:lihco3+hf→lif+h2o+co2;生成的氟化锂溶液被收集进入循环水池中,在收集过程中测试循环水池的ph值,并向循环水池中加入氢氧化锂溶液调节ph值至3,然后通过循环水池侧壁上设置的水位控制阀缓慢放出上清液,放出上清液后对循环水池中余下的溶液进行多次固液分离和水洗,至水洗液的ph达到6-7时收集沉淀,对沉淀进行初步干燥脱水处理,干燥温度105-110℃,干燥时间3-7小时;然后在420-450℃烘干3-10小时,得到成品氟化锂,氟化锂可以继续作稀土电解用,其中水洗液导入循环水池中重复利用;步骤三:将经喷淋吸收塔化学吸收后的废气直接导入碳酸锂料液池中,其中的二氧化碳与碳酸锂料液池中的碳酸锂反应,使碳酸锂转化成溶解度大的碳酸氢锂,化学反应式如下:li2co3+h2o+co2→2lihco3,将转化得到的碳酸氢锂注入喷淋吸收塔中作为喷淋液循环使用,继续捕获含氟气体中的氟离子形成氟化锂,相较于碳酸锂,碳酸氢锂溶解度更大,对氟离子的吸收效果更佳。以下为利用本发明的方法进行电解稀土废气回收利用的一些生产实施例:实施例1从5月8号开始投入1#号循环吸收塔100公斤碳酸锂,5月21号第二次加入50公斤,5月27号收集氟化锂,将氟化锂溶液放入循环水池中,经过氢氧化锂调节ph至3,固液分离、水洗3次后ph至6.5,110℃干燥3小时,在450℃高温脱水3小时后,得到50.36公斤氟化锂,计算的7天综合收率41.67%(只计算单次加入碳酸锂的收率,含氢氧化锂,下同),对得到的氟化锂进行检测,其中的成分如表1所示;表1氟化锂成分分析检验项目检验结果(%)lif99.0na+k0.03fe0.008so42-0.01h2o0.07ca0.050cl-0.01实施例25月27号加入碳酸锂200公斤,6月26号回收氟化锂,经过氢氧化锂调节ph至3,固液分离、水洗4次后ph至7,110℃干燥5小时,在420℃高温脱水9小时后,得到130.28公斤氟化锂,综合收率84.50%;实施例36月26日投入200公斤碳酸锂,7月25日收集氟化锂,经过氢氧化锂调节ph至3,固液分离、水洗3次后ph至6.5,105℃干燥7小时,在430℃高温脱水7小时后,得到147.28公斤氟化锂,综合收率96.04%;实施例47月25日投入200公斤碳酸锂,8月24日收集氟化锂,经过氢氧化锂调节ph至3,固液分离、水洗5次后ph至7,108℃干燥6小时,在440℃高温脱水7小时后,得到151.06公斤氟化锂,综合收率98.50%;实施例58月24日投入200公斤碳酸锂,9月23日收集氟化锂,经过氢氧化锂调节ph至3,固液分离、水洗4次后ph至6.5,110℃干燥7小时,在450℃高温脱水7小时后,得到152.77公斤氟化锂,综合收率99.62%;实施例69月23日投入200公斤碳酸锂,10月22日收集氟化锂,经过氢氧化锂调节ph至3,固液分离、水洗4次后ph至7,110℃干燥5小时,在450℃高温脱水9小时后,得到153.68公斤氟化锂,综合收率100.21%。实施例710月22日投入200公斤碳酸锂,11月21日收集氟化锂,经过氢氧化锂调节ph至3,固液分离、水洗5次后ph至7,110℃干燥3小时,在450℃高温脱水10小时后,得到152.08公斤氟化锂,综合收率99.16%。当前第1页12