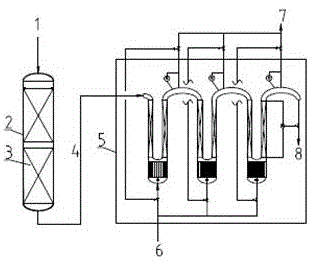
本发明属于石油化工领域,具体为一种一种柴油超深度脱硫装置及柴油加氢反应系统。
背景技术:
:随着人们环保意识的提高以及环保法规的日益严格,对柴油中硫含量的要求越来越严格。目前较为先进的柴油加氢脱硫技术采用液相加氢的方法,理论基础的核心是氢气在液体中的溶解度,高温高压是氢气溶解度及溶解速率的直接推动力,温度/压力越高,则氢气的溶解度和溶解速率越大,越有利于加氢反应的进行及催化剂的长周期运转。相比于传统的固定床气/液/固三相加氢工艺而言,液相加氢具有加氢反应速率快、反应效率高、能耗低、投资少等诸多优势。柴油液相加氢反应工艺一般是以反应生成油作为循环油,在反应器高压分离器采出后经循环泵返回反应器入口,与新鲜原料油混合后进入反应器,其中循环油是必不可少的,一方面由于反应器内没有循环氢,所有需要利用循环油带走反应热,减少催化剂表面的高温积碳、结焦等现象,另一方面由于柴油加氢过程的氢耗量大,通过循环油来溶解氢气,满足反应过程中所需的氢耗。这种柴油液相加氢脱硫方法一般情况下通常只能生产硫含量不大于350ppm,较好的是生产不大于200ppm的柴油,原因是这种方法对于柴油组分中含有的硫如苯并噻酚、二苯并噻酚(特别是4-甲基二苯并噻酚、4,6二甲基二苯并噻酚)等复杂分子中含有的硫难以脱除,采用较为苛刻的条件进行深度则会造成大量的芳烃损失,也是不可取的;另一方面,柴油液相加氢中的循环油含有一定量的硫化氢,h2s分压能够影响加氢脱硫反应的活化能,降低加氢脱硫反应速率,且h2s在催化剂表面为单层吸附,一旦吸附中心被h2s占据,少量h2s存在就会大大降低加氢脱硫速率,因此常规的柴油液相加氢工艺难以实现深度脱硫或超深度脱硫,采用有效的手段消除h2s的影响是解决深度脱硫的关键问题,为此,柴油需要开发新的反应方法或反应器形式,来实现深度脱硫或超深度脱硫。cn03133543.8提出了一种柴油深度脱硫、脱芳烃工艺,是将常规并流加氢精制反应器与深度加氢脱硫和脱芳烃反应器结合起来,原料油首先通过常规加氢精制反应器,反应后的液相物料和新氢混合从深度加氢脱硫、脱芳烃反应器顶部进入反应器,进行气液并流加氢反应,反应后物料在气液分离区内分离,气相排出并进入常规加氢精制反应器,液相向下流动与从反应器底部引入的新氢逆流接触,精制产物最终从反应器底部排出。该发明是在常规加氢反应器内采用逆流加氢过程,目的是反应过程中排出一定量的硫化氢气体,但是由于反应过程氢气与原料油为气液逆流接触,液体物料由于重力作用在下流过程中会将气体物料携带下来,而难以实现排出硫化氢气提的目的。cn201210422814.5提出一种fcc柴油深度脱硫的方法,该方法包括以下步骤:将fcc柴油边搅拌边升温;混合过氧化氢和甲酸;将过氧化氢和甲酸的混合物加入到升温后的fcc柴油中,再加入亚铁离子后控制温度并高速搅拌一段时间;降温到25℃,油水分离;25℃下用二甲基甲酰胺萃取油。该方法为了实现深度脱硫,采用氧化脱硫的方法。该方法由于反应过程中引入氧化剂过氧化氢和甲酸,一方面过氧化氢容易分解,使用过程中较为危险,另一方面氧化剂的用量控制比较困难,带入成品油系统会带来安全隐患,因此该方法难以工业实施。cn201410511740.1提出了一种用于精制柴油深度脱硫的脱硫吸附剂及其制备方法,是将稻壳洗净烘干,粉碎后在马弗炉中炭化,得到稻壳灰,将稻壳灰加入无机碱的水溶液中,在100℃以下放置12~36h,然后置于马弗炉中焙烧活化,待冷却后用去离子水洗至中性,100~130℃温度下干燥,研磨,得到未改性的脱硫吸附剂。本发明还公开了该脱硫吸附剂的制备方法。本发明的脱硫剂比表面积大,孔容和孔径分布理想,强酸性基团含量高,对dbt硫有效吸附容量在25.48~38.62mgs/g之间,脱硫活性、尤其是对于二苯并噻吩类有机硫化物的脱硫活性高,满足生产低硫或超低硫柴油需要。该方法采用的是吸附脱硫的方法实现深度脱硫,但是吸附脱硫存在吸附剂硫容低、容易穿透、频繁再生、再生系统复杂、再生能耗高等诸多问题。综上所述,采用现有液相加氢工艺难以实现柴油深度脱硫或超深度脱硫,而采用非加氢脱硫的方法中,如氧化脱硫方法存在氧化剂残留在油品中影响脱硫油的氧化安定性的问题;萃取脱硫方法存在体系中引入了新的溶剂、氧化脱硫油回收率低等问题;吸附脱硫存在吸附硫容低、吸附剂使用周期短等问题,使这些非加氢深度脱硫方法在实际应用过程中存在较多的问题,难以实现工业化。技术实现要素:针对现有技术的不足,本发明提供一种柴油超深度脱硫装置及柴油加氢反应系统。本发明通过多个串联的“u形”管式加氢反应器,能够将反应过程中h2s、nh3等气体及时移出反应体系,实现深度加氢脱硫及超深度脱硫。本发明的柴油超深度脱硫装置包含至少三个串联的管式反应器,相邻的管式反应器通过弧形管连通;所述的管式反应器,外形为“u形”,包括两侧的直管段、底部连通两侧直管段的水平段,两侧的直管段分别为加氢反应段和气提段,水平段为纳/微米氢注入段;加氢反应段顶部设置液相加氢原料入口,加氢反应段内装填加氢催化剂,纳/微米氢注入段填装若干组陶瓷膜管束,陶瓷膜管束连通外部氢气,气提段内装填加氢催化剂;上一个反应器的气提段顶部末端通过弧形管与下一个反应器的加氢反应段进料口连通,最后一个反应器气提段顶部末端连通弧形管,弧形管末端连接反应产物出口;所述弧形管的水平切线高于气提段顶部,弧形管最高点处设置气体出口。本发明装置中,优选设置4~8个串联的管式反应器。本发明装置中,所述的加氢反应段的高径比为1:1~30:1,优选5:1~15:1。本发明装置中,所述的加氢催化剂可以根据加氢过程的实际需要确定装填的加氢催化剂。如加氢脱硫催化剂、加氢脱氮催化剂、加氢脱金属催化剂等等。本发明装置中,所述的陶瓷膜管束为管壳式结构,管壳内可以包含一根或多根膜管,管内通入氢气,在压差推动下氢气通过管壁上的纳/微米孔道进行渗透扩散,形成纳/微米气泡进入管外的壳体空间,并分散至壳体空间的液相中,形成一种携带了纳/微米气泡氢的液相原料。所述的纳/微米气泡氢的尺寸一般为10~1000nm,优选为50~500nm。本发明装置中,所述的水平段的长径比15:1~1:15,优选2:1~1:2。本发明装置中,所述的加氢反应段的直径与水平段的直径比1:50~1:1,优选1:10~1:1。本发明装置中,所述的气提段的顶部与加氢反应段的顶部位于同一高度,气提段的管径小于或等于加氢反应段的管径,高径比为1:1~50:1,优选10:1~30:1。本发明装置中,所述的弧形管顶部有气体空间,弧形管最高点处设置气体出口,用于连续或间断排放反应过程中生成的h2s、nh3等反应气体。弧形的圆心角为0°~360°,优选180°~270°。气提段末端位置处设置有出料液位控制,保证加氢反应段和气提段发生反应时为全液相加氢。本发明的柴油超深度脱硫装置主要用于柴油原料(硫含量一般为0.2wt%~2wt%)经固定床加氢后的进一步深度脱硫或超深度脱硫,一般脱除二苯并噻吩、烷基苯并噻吩、烷基二苯并噻吩等较难脱除的噻吩类化合物。一般经固定床加氢后的油品中硫含量为50μg/g~1000μg/g,优选200μg/g~600μg/g。本发明同时提供一种柴油加氢反应系统,包括加氢反应器和上述的柴油超深度脱硫装置;所述的加氢反应器用于原料油的加氢改质,使油品中大部分发生硫/氮/氧/金属等的加氢转化、烯烃及二烯烃加氢饱和、芳烃部分加氢饱和等反应,以改善油品的质量;所述的柴油超深度脱硫装置用于加氢反应器的流出物的深度加氢脱硫。加氢反应器以及柴油超深度脱硫装置的个数可以根据实际需要设置。其中所述的加氢反应器可以为本领域熟知的固定床加氢反应器或其他类型的加氢反应器,可以为上流式或下流式,可以为适用于气/液/固三相加氢工艺的固定床加氢反应器,或固定床液相加氢反应器;如采用固定床液相加氢反应器时,所述加氢反应条件为:反应温度280℃~400℃,优选300℃~360℃;反应压力3.0mpa~10.0mpa,优选4.0mpa~6.0mpa;新鲜进料液时体积空速0.5h-1~8.0h-1,优选2.0h-1~6.0h-1;循环比为0.5~5,优选1.0~2.5。本发明的柴油超深度加氢脱硫方法,包括如下内容:初步加氢脱硫后的原料油进入柴油超深度脱硫装置,依次流经至少3个串联的管式反应器,反应产物由最后一个管式反应器末端流出;其中液相物料在串联的管式反应器内进行如下反应过程:液相物料在加氢反应段与加氢催化剂接触发生加氢反应,得到的反应产物进入纳/微米氢气注入段,与经陶瓷膜管分散的纳/微米氢气混合,混合物流进入气提段与加氢催化剂接触进行加氢反应,同时氢气将物流中的h2s、nh3等反应气体气提出来,经弧形管顶部的气体出口排出。本发明方法中,所述的初步加氢脱硫后的原料油的硫含量降低至50μg/g~1000μg/g,优选200μg/g~600μg/g;初步加氢过程优选采用常规固定床液相加氢反应工艺及液相加氢反应器,可以是上流式或下流式。本发明方法中,优选采用4~8个串联的管式反应器。本发明方法中,所述的管式加氢反应器,加氢反应段的加氢反应条件为:280~420℃,优选320~380℃,反应压力3.0~10.0mpa,优选4.0~6.0mpa,液时体积空速1.0~20h-1,优选5.0h~15.0h-1。本发明方法中,所述的管式加氢反应器,进入纳/微米氢注入段的液相物料的停留时间为0.1~5分钟,优选0.5~2.0分钟,过短的停留时间达不到均匀分散氢气的效果,过长的停留时间会使纳/微米氢气气泡聚并长大为大气泡。纳/微米氢注入段中纳/微米氢的给量与原料油的质量比一般为0.01%~0.5%,优选0.05%~0.2%。本发明方法中,气提段的加氢反应条件为:反应温度为280~420℃,优选320~380℃,反应压力3.0~10.0mpa,优选4.0~6.0mpa,液时体积空速50.0~500h-1,优选150~350h-1。本发明方法中,所述的原料油不仅仅限于柴油馏分,原则上为可以能够进行液相加氢的各种油品,一般为馏程在130~550℃范围内任意馏分的烃类原料,可以选自但不限于石脑油、重整生成油、航煤、柴油、蜡油、润滑油、常压渣油、脱沥青油、生物柴油、动物油或植物油等中的一种或多种,优选直馏柴油、催化柴油或及焦化柴油。所述固定床反应进料中,原料油及循环油与氢气的混合一般采用本领域熟知溶氢方式得到,如通过静态混合器将氢气溶解在油品中,氢气与原料油(新鲜原料油与循环原料油的质量之和)质量比一般为0.1%~1.5%,优选0.4%~0.8%。本发明方法中,所述的加氢反应器采用的催化剂可以根据反应的需要使用适宜的加氢催化剂,实现不同的加氢目的,如加氢精制催化剂、预加氢精制催化剂、加氢改质催化剂、选择性加氢催化剂、加氢处理催化剂、加氢裂化催化剂、补充加氢催化剂等,各种催化剂可以选择商品催化剂,也可以根据现有技术制备。催化反应可以脱除部分或全部烃类原料中的硫、氮、氧、砷、金属、残碳等杂质,或饱和/部分饱和烯烃、芳烃、二烯烃,或发生烃类分子异构化、烷基化、环化、芳构化、裂化、裂解等反应;催化剂活性组分包括但不局限于贵金属、co、mo、ni、w、mg、zn、稀土元素等一种或多种组合。本发明方法中,所述的管式反应器内的加氢反应段及气提段可以填装与固定床反应器相同或不同的加氢催化剂,优选采用加氢脱硫活性较高的加氢催化剂,可以使用市售产品,也可以根据本领域常规知识制备;加氢脱硫活性高的催化剂可以使用一般以氧化铝或含硅氧化铝为载体,mo、co为加氢活性组分。以催化剂的重量为基准,金属mo含量以氧化物计为6wt%~20wt%,金属co含量以氧化物计为1wt%~12wt%。现有的柴油加氢反应过程中,副产物h2s对加氢脱硫反应、加氢脱氮和加氢脱芳反应也有明显的抑制作用,这些副产物无法被及时移出体系,不利于深度加氢;现有技术的原位气提均是采用反应过程排气的方式进行,不但造成氢气资源的浪费,而且基于操作压力高、物料的流动方式等原因的影响导致气提效果均不理想。同时在柴油深度脱硫及超深度脱硫过程中,硫含量越低,其脱硫速率越低,脱硫越困难,就需要更加苛刻的条件,如反应温度、压力需要更高、空速需要更低,这就造成装置能耗高、柴油收率低等问题,而采用传统固定床加氢方式在缓和的条件下对于实现部分脱硫如达到硫含量≤350μg/g是较为容易的,再进一步实现深度脱硫及超深度脱硫,即将硫含量降低至≤50μg/g,甚至≤10μg/g较为困难,是影响脱硫率的关键所在。现有技术的柴油液相加氢工艺采用普通的氢油混合过程及混合器结构,原料油能够溶解分散的氢气量较少,大幅度降低了反应速率和反应效率,导致深度脱硫及超深度脱硫时的反应速率极低,同时氢气不足,容易出现高温结焦。本发明通过常规固定床加氢反应器在缓和条件下发生加氢反应,将硫含量降低至≤350μg/g,然后将加氢反应产物引入柴油超深度脱硫装置,实现深度脱硫甚至超深度脱硫。柴油超深度脱硫装置包含至少3个串联的“u形”管式反应器,每个“u形”管式反应器均经过加氢反应段的液相加氢反应、水平段内纳/微米氢注入、气提段的反应产物气提和气提气排放四个过程。首先通过加氢反应段与纳/微米氢注入段的连通,一方面纳/微米氢注入段可以为加氢反应段逆流的原位补氢,保证了充足的氢气量,避免加氢反应过程中的氢气不足,出现高温结焦,加快加氢反应速率和反应效率;另一方面通过加氢反应段与纳/微米氢注入段连接位置的导流结构,使来自加氢反应段的物流在水平方向上与纳/微米氢错流接触,增加气液的传质推动力,强化纳/微米氢的溶解分散;在纳/微米氢注入段中,将膜管分散器设置为管壳式结构,壳体式的物料有一定的停留时间,目的是将纳/微米氢分散溶解在原料油的过程中,通过一定的时间的物料停留和返混,促使h2s、nh3等反应气体组分的向液相表面扩散与迁移,为后续的气提段的气提提供必要的物理条件;纳/微米氢注入段与气提段的连通,通过水平段与气提段之间的导流变径结构,一方面可以将纳/微米氢注入段的物料快速引入气提段,另一方面可以使反应物料的动能增加,增加h2s、nh3等反应气体扩散时所需的动能,实现强化气提,能够将h2s、nh3等反应气体在反应过程中持续的气提出来,提高加氢脱硫反应速率和反应深度。附图说明图1是本发明的柴油加氢反应系统及深度加氢脱硫方法的示意图。图2是本发明的柴油超深度脱硫装置中管式反应器的示意图。1为含氢原料油(新鲜原料油与循环油之和),2为加氢反应器,3为催化剂床层,4为加氢反应器出料,5为柴油深度加氢脱硫装置,6为柴油深度加氢脱硫装置注入氢气,7为反应器顶部排放气,8为深度加氢反应产物。9为“u形”的管式反应器,10为加氢反应段,11为纳/微米氢注入段,12为陶瓷膜管分散器,13为气提段,14为弧形管。具体实施方式下面结合附图说明和实施例对本发明进行详细说明,但不因此限制本发明。本发明实施例及对比例中的含氢原料油通过氢油混合设备得到。以附图1说明本发明的柴油深度加氢脱硫方法:含氢原料油1进入加氢反应器2内,在催化剂床层3内填装的加氢催化剂作用下发生加氢改质反应,包含加氢脱硫、加氢脱氮、加氢脱氧、加氢脱金属等、烯烃及二烯烃加氢饱和、芳烃部分加氢饱和等,以改善油品的质量,完成加氢改质反应后得到加氢反应器出料4;加氢反应器出料4进入柴油深度加氢脱硫装置5发生深度加氢脱硫反应,反应后得到深度加氢反应产物8。柴油深度加氢脱硫装置5包含多组串联的“u形”管式反应器9,相邻“u形”管式反应器9通过弧形管14依次串联;“u形”的管式反应器9包含两侧的直管段、底部连通两侧直管段的水平段,两侧的直管段分别为加氢反应段10和气提段13,水平段为纳/微米氢注入段11,纳/微米氢注入段11内设置有陶瓷膜管分散器12,连通外部氢气6,将氢气分散为纳/微米氢气气泡;加氢反应段10以加氢反应器出料为原料,加氢反应段10内装填加氢催化剂,加氢反应原料在加氢反应段10内发生液相加氢反应,随后物料进入纳/微米氢注入段11的壳体,与将陶瓷膜管分散器12形成的纳/微米氢气气泡混合,形成一种携带了纳/微米氢气气泡的加氢反应物料进入气提段13,将物料中的h2s、nh3等反应气体在反应过程中持续气提出来,至弧形管14的最高点设置的气体出口7进行排放,而深度加氢反应产物经过深度加氢反应产物出口8流出。本发明对比例及实施例中采用的原料油为来自某厂的直馏柴油和催化柴油,具体性质见表1。对比例及实施例中,固定床液相加氢反应器及深度加氢系统中采用的催化剂为抚顺石油化工研究院的fhuds-5。表1原料性质对比例1采用常规固定床液相加氢反应器及加氢反应工艺,氢油混合设备采用静态混合器,型号为:sx-2.3-10.0-500;反应器进料中氢气的给量为原料油(新鲜原料油与循环油之和)质量的0.662%。固定床液相加氢反应条件如下:反应温度为352~380℃,反应压力为6.5mpag,液时体积空速为2.5h-1,循环比为2.0。分别以表1中的直馏柴油和催化柴油为原料,经过固定床液相加氢后得到反应产品,反应条件及产品性质见表2和表3。对比例2采用常规固定床液相加氢反应器及加氢反应工艺,氢油混合设备采用膜管微分散器,将氢气分散为500nm的氢气气泡;反应器进料中氢气的给量为原料油(新鲜原料油与循环油之和)质量的0.628%。固定床液相加氢反应条件如下:反应温度为347~372℃,反应压力为6.5mpag,液时体积空速为3.2h-1。以表1中的直馏柴油和催化柴油为原料,经过固定床液相加氢后得到反应产品,反应条件及产品性质见表2和表3。实施例1采用附图1所述的方法,其中加氢反应器中氢气的给量为原料油(新鲜原料油与循环油之和)质量的0.405%,固定床加氢反应器的反应条件如下:反应温度为310~355℃,反应压力为6.0mpag,液时体积空速为4.5h-1。固定床加氢改质后的原料油中的硫含量为576μg/g。固定床加氢改质后的原料油进入深度加氢脱硫装置,该装置包括依次串联三个“u形”管式反应器,其中的膜管微分散器将氢气分散为50nm的氢气气泡,纳/微米注入氢的氢气给量为原料油(“u形”管式反应器进料)质量的0.128%;加氢反应段的反应条件如下:反应温度为310~350℃,反应压力为5.0mpag,液时体积空速为7.5h-1;气提段的反应条件如下:反应温度为310~350℃,反应压力为5.0mpag,液时体积空速为150h-1。深度加氢反应系统中“u形”管式反应器,加氢反应段的直径为高径比为12.2:1;水平段的长径比为1:1;加氢反应段的直径与水平段的直径比1:10;气提段的高径比为38.125:1。以表1中的直馏柴油和催化柴油为原料,经过固定床液相加氢后得到反应产品,反应条件及产品性质见表2和表3。实施例2采用附图1所述的方法,其中加氢反应器中氢气的给量为原料油(新鲜原料油与循环油之和)质量的0.389%,固定床加氢反应器的反应条件如下:反应温度为320~360℃,反应压力为6.0mpag,液时体积空速为5.0h-1。固定床加氢改质后的原料油中的硫含量为355μg/g。固定床加氢改质后的原料油进入深度加氢脱硫装置,该装置包括依次串联5个“u形”管式反应器,其中的膜管微分散器将氢气分散为500nm的氢气气泡,纳/微米注入氢的氢气给量为原料油(“u形”管式反应器进料)质量的0.152%;加氢反应段的反应条件如下:反应温度为320~360℃,反应压力为6.0mpag,液时体积空速为15h-1;气提段的反应条件如下:反应温度为320~360℃,反应压力为6.0mpag,液时体积空速为185h-1。深度加氢反应系统中“u形”管式反应器,加氢反应段的直径为高径比为15:1;水平段的长径比为2:1;加氢反应段的直径与水平段的直径比1:5;气提段的高径比为25:1。以表1中的直馏柴油和催化柴油为原料,经过固定床液相加氢后得到反应产品,反应条件及产品性质见表2和表3。实施例3采用附图1所述的方法,其中加氢反应器中氢气的给量为原料油(新鲜原料油与循环油之和)质量的0.402%,固定床加氢反应器的反应条件如下:反应温度为320~360℃,反应压力为6.0mpag,液时体积空速为5.0h-1。固定床加氢改质后的原料油中的硫含量为47μg/g。固定床加氢改质后的原料油进入深度加氢脱硫装置,该装置包括依次串联7个“u形”管式反应器,其中的膜管微分散器将氢气分散为50nm的氢气气泡,纳/微米注入氢的氢气给量为原料油(“u形”管式反应器进料)质量的0.164%;加氢反应段的反应条件如下:反应温度为320~360℃,反应压力为6.0mpag,液时体积空速为12.5h-1;气提段的反应条件如下:反应温度为320~360℃,反应压力为6.0mpag,液时体积空速为225h-1。深度加氢反应系统中“u形”管式反应器,加氢反应段的直径为高径比为7:1;水平段的长径比为2:1;加氢反应段的直径与水平段的直径比1:25;气提段的高径比为15:1。以表1中的直馏柴油和催化柴油为原料,经过固定床液相加氢后得到反应产品,反应条件及产品性质见表2和表3。表2反应条件及产品性质(直馏柴油原料)名称总硫,μg·g-1氮含量,μg·g-1对比例119656对比例218743实施例14718实施例24515实施例3712表2反应条件及产品性质(催化柴油原料)名称总硫,μg·g-1氮含量,μg·g-1对比例1885177对比例2791145实施例14732实施例24525实施例3916由本实施例及对比例的加氢反应效果可以看出,采用本发明的柴油深度加氢脱硫装置及柴油加氢反应系统能够实现深度脱硫或超深度脱硫,这主要是由于深度加氢脱硫装置中,采用原位补氢的方式补充氢耗,可以避免原料油高温结焦、聚合,而纳/微米氢多点密集补充及与原料油错流接触可以强化氢气的溶解分散程度,使加氢反应达到相同的技术效果时可采用更为缓和的条件,如温度和压力可以更低、空速可以更高、氢气消耗也更低,可以降低操作成本和能耗,提高催化剂使用寿命。以柴油加氢过程为例,通过本发明方法中的纳/微米氢分散时物料在膜管分散器内的停留和返混,实现h2s、nh3等反应气体组分的表面扩散与迁移,为气提段发挥气提功能提供必要的物理条件,这对于后续实现和强化原位气提功能具有重要作用,有利于h2s、nh3等反应气体的气提脱除,从而提高加氢反应深度,实现深度脱硫及超深度脱硫。当前第1页12