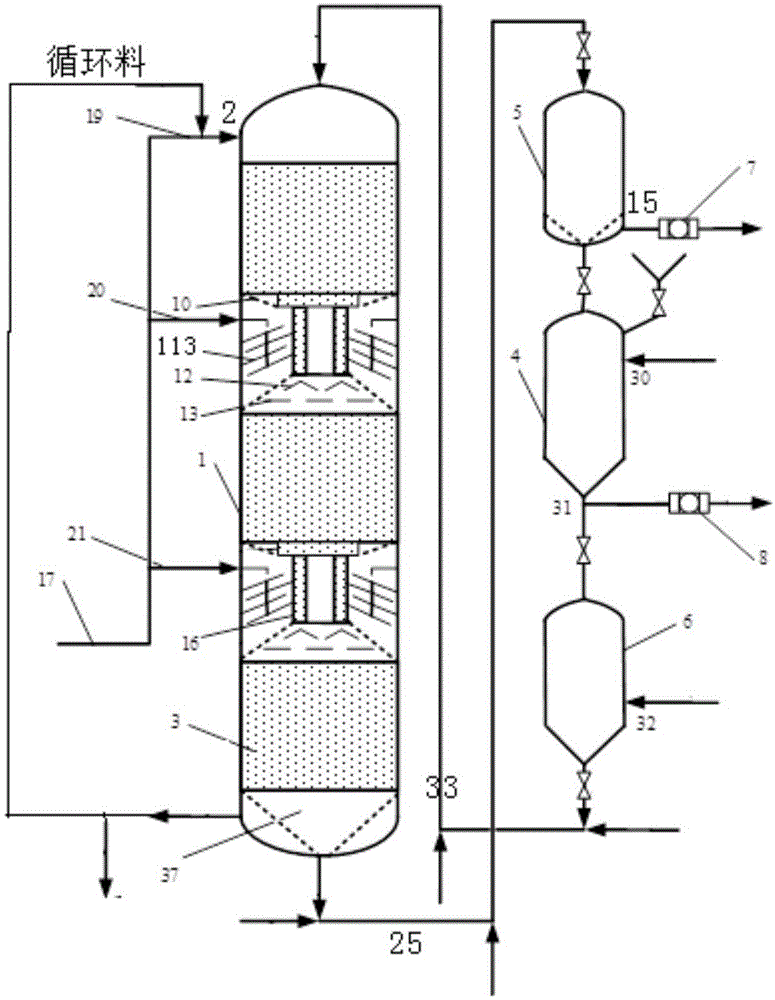
本发明涉及固体酸烷基化领域,具体涉及一种固体酸烷基化方法。
背景技术:
:目前,炼油工业的最主要任务之一是提供运输燃料,汽油作为一种重要的运输燃料,被广泛的应用于交通运输等行业中。随着汽油消耗量的增加和环保标准的日益严格,围绕着如何解决汽油清洁化生产的问题成为研究和讨论的热点。在强酸的作用下,以异构烷烃(主要是异丁烷)和烯烃(c3~c5烯烃)为原料生成烷基化油的技术为汽油的清洁化生产提供了可能。烷基化油具有较高的辛烷值和较低的蒸汽压,主要由饱和烃组成,且不含硫、氮、烯烃和芳烃等物质,因而被称为清洁化汽油,是航空汽油和车用汽油理想的调和组分。烷基化技术按催化剂形式可以分为液体酸烷基化和固体酸烷基化。目前,世界范围内约90%的烷基化产能是由液体酸烷基化技术(硫酸法和氢氟酸法)提供的,虽然液体酸烷基化技术比较成熟,且具有较好的反应选择性,但是也存在很多问题,比如液体酸烷基化过程都存在设备腐蚀严重的问题。除此之外,对于硫酸法而言,其过程耗酸量巨大,大量的废酸在运输和处理上都存在一定的安全隐患,对于氢氟酸法而言,由于氢氟酸具有较强的腐蚀性和毒性,而且容易挥发,会对人体造成很大的伤害。因此,与之对比,采用固体酸作为催化剂,不仅不会对环境造成污染,而且不存在设备腐蚀的问题,可以视为一种绿色的烷基化工艺技术,具有很好的发展前景。但是在固体酸烷基化过程中,由于固体酸催化剂容易失活,为了保持一定的反应活性,需要进行频繁的再生操作,因此,开发一种能够实现反应和再生过程连续化的反应器技术,对推动固体酸烷基化技术发展来说是十分重要的。us8373014公开了一种采用重叠式放置的径向移动床作为反应器的固体酸烷基化反应方法。该方法中,采用了类似催化重整重叠式径向移动床的结构,单段反应器中设有外围起反应物料分布作用的环形桶和起物料收集作用的中心管以及夹在二者之间的反应床层区;两段反应器之间采用催化剂物料输送管将上段催化剂床层中的催化剂输送到下段反应器的反应床层区。处于中间反应器的流出物料被分为两部分,一部分泵回上游反应器与新鲜原料经混合器混合后作为上游反应器的进料,此部分可称为循环用料;另一部分引入下游反应器的进料混合器前与新鲜原料混合后作为下游反应器的进料,此部分未经泵增压直接使用。此外,循环料部分还需要经过一换热器以引出反应热。cn1879956a公开了一种流化床固体酸烷基化技术,该工艺技术主要包括提升管反应器、流化床反应器、环流再生器和移动床再生器。其中提升管反应器中液速范围在0.1~3m/s,流化床反应器中液速范围在0.26~7.68cm/s。再生过程可根据再生时间来确定再生反应器的形式,如果再生的时间为几秒到几十秒,可单独采用环流再生器。如果再生时间为几十秒到几十分钟,可单独采用移动床再生器,并且再生液的液速为0.2~3cm/s。cn1113906a公开了一种流化床固体酸芳烃烷基化工艺技术,该工艺过程主要包括液固上行反应器、待生催化剂沉降返洗塔、液固并流向上再生器、再生后催化剂沉降返洗塔。其中要求所用的催化剂粒径在0.05~0.8mm,反应器和再生器中能够携带催化剂向上流动的液体液速是颗粒终端沉降速度的1~15倍,在沉降返洗塔内,采用自下向上流动的洗涤液对催化剂进行洗涤再生,洗涤液的流速为颗粒终端沉降速度的0.5~5倍。现有技术公开的固定床烷基化技术和流动床烷基化技术为了实现反应装置的连续稳定进行,至少需要两台以上的反应器切换操作,每隔一段时间对床层内的催化剂进行高温再生,深度再生后还要对高温床层进行降温操作,由于装置频繁的在反应与再生温度之间进行切换,使得其在工业应用中连续稳定运行时带来了很多问题。另外,现有技术中,固体酸烷基化反应装置内的催化剂很难维持稳定的较高的目标产物选择性。技术实现要素:本发明为了克服现有技术固体酸烷基化反应无法连续稳定运行,且目标产物选择性有待进一步提高的问题,提供一种固体酸烷基化方法。采用本发明提供的方法不但能够实现固体酸烷基化反应的连续稳定运行,而且能够提高目标产物选择性。为了实现上述目的,本发明第一方面提供一种固体酸烷基化方法,包括:该方法在液固轴向移动床反应与再生装置中进行,液固轴向移动床反应与再生装置包括依次连接的轴向移动床反应器、待生剂接收器、催化剂再生器和再生剂接收器,其中,再生剂接收器的催化剂出口与轴向移动床反应器的催化剂入口连通;轴向移动床反应器设置有至少两个上下放置的催化剂床层,轴向移动床反应器在每个催化剂床层的上方设置有进料口;相邻两个催化剂床层之间设置有催化剂输送管使得催化剂能够在轴向移动床反应器中自上而下移动;液相原料从每个催化剂床层上方设置的进料口送入轴向移动床反应器中与催化剂接触反应。优选地,相邻两个催化剂床层之间设置有反应物料折流件,所述反应物料折流件用于强化反应后物料和进料口送入的液态新鲜原料的混合。优选地,相邻两个催化剂床层之间设置有催化剂分布件,所述催化剂分布件用于分散催化剂输送管出口的催化剂。本发明提供的固体酸烷基化方法具有如下优势:1)与固定床烷基化技术相比,仅需要使用一台反应器即可实现反应装置的连续稳定运行;2)与流动床烷基化技术相比,本发明提供的方法能够实现催化剂的寿命分布,可以将失活的部分催化剂移出系统,然后补入新鲜的催化剂;而流动床反应器无法实现催化剂的寿命分布;3)本发明提供的方法使用轴向移动床反应器,单台(套)设备即可满足要求,减少了装置的投资成本,另外通过将失活的催化剂颗粒引出反应器外进行深度再生,在不影响反应装置稳定运行的前提下,实现了催化剂反应和再生的连续化操作,维持了装置内的催化剂具有较为稳定的平衡活性,提高了烷基化油中目标产物的选择性。附图说明图1是本发明提供的一种具体实施方式的液固轴向移动床反应与再生装置;图2是本发明提供的一种折流件的示意图;图3是本发明提供的一种具体实施方式的液固轴向移动床反应与再生装置。附图标记说明1-轴向移动床反应器2-进料口3-催化剂床层4-催化剂再生器5-待生剂接收器6-再生剂接收器7-脱液过滤器8-再生后介质过滤器10-分离件11-反应物料折流件111-主轴112-输送部件113-折流板12-锥型分布挡板13-水平分布挡板15-退液相料出口16-催化剂输送管17-管线19-第一分支管线20-第二分支管线21-第三分支管线25-第一颗粒流量调节器30-再生介质进料口31-再生后介质出料口32-液相料补充入口33-第二颗粒流量调节器37-底部催化剂收集区38-催化剂缓冲罐具体实施方式在本文中所披露的范围的端点和任何值都不限于该精确的范围或值,这些范围或值应当理解为包含接近这些范围或值的值。对于数值范围来说,各个范围的端点值之间、各个范围的端点值和单独的点值之间,以及单独的点值之间可以彼此组合而得到一个或多个新的数值范围,这些数值范围应被视为在本文中具体公开。本发明中,在未作相反说明的情况下,使用的方位词如“上、下”通常是指通常是指参考附图所示的上和下。使用的方位词如“内、外”是指相对于各部件本身的轮廓的内、外。本发明第一方面提供一种固体酸烷基化方法,包括:该方法在液固轴向移动床反应与再生装置中进行,液固轴向移动床反应与再生装置包括依次连接的轴向移动床反应器1、待生剂接收器5、催化剂再生器4和再生剂接收器6,其中,再生剂接收器6的催化剂出口与轴向移动床反应器1的催化剂入口连通;轴向移动床反应器1设置有至少两个上下放置的催化剂床层3,轴向移动床反应器1在每个催化剂床层3的上方设置有进料口2;相邻两个催化剂床层3之间设置有催化剂输送管16使得催化剂能够在轴向移动床反应器1中自上而下移动;液相原料从每个催化剂床层3上方设置的进料口送入轴向移动床反应器1中与催化剂接触反应。在本发明中,所述的依次连接是指,轴向移动床反应器1的催化剂出口与待生剂接收器5的催化剂入口连接,待生剂接收器5的催化剂出口与催化剂再生器4的催化剂入口连接,催化剂再生器4的催化剂出口与再生剂接收器6的催化剂入口连接。再生剂接收器6的催化剂出口与轴向移动床反应器1的催化剂入口连通,以将再生催化剂送入轴向移动床反应器1中。本发明所述轴向移动床反应器是指催化剂的移动方向为轴向的移动床反应器。根据本发明提供的方法,轴向移动床反应器1设置有至少两个上下放置的催化剂床层,优选设置3-8个上下放置的催化剂床层3。本发明对催化剂床层3的厚度没有特别的限定,优选地,各个催化剂床层3的厚度各自独立地为轴向移动床反应器1高度的10-30%。本发明实施例中以轴向移动床反应器1的高度为15m,内径为600mm为例进行示例性说明,但本发明并不限于此。本领域技术人员可以根据实际情况进行适当调整。本发明所述的液相原料可以为本领域常规使用的各种能够进行固体酸烷基化反应的原料。例如,所述液相原料含有异构烷烃和烯烃。所述异构烷烃可以为烷基化反应中常用的异构烷烃,优选为c4-c6的异构烷烃,更优选为异丁烷。所述烯烃优选为单烯烃,更优选为c3-c6的单烯烃,进一步优选为c4单烯烃。根据本发明的固体酸烷基化方法,进入各催化剂床层的物料的异构烷烃和烯烃可以为常规选择。优选地,进入各催化剂床层的物料的异构烷烃和烯烃的摩尔比(即,烷烯比)为200-1000:1。这样不仅能使烯烃完全或基本完全转化,而且能获得更高的产物选择性,同时还能使烷基化催化剂具有更高的活性稳定性。优选地,进入各催化剂床层的物料的异构烷烃和烯烃的摩尔比为400-750。根据本发明,轴向移动床反应器中的反应温度优选为低于异构烷烃的临界温度,更优选为不高于120℃(如30-120℃),进一步优选为不高于100℃,更进一步优选为30-100℃,如60-80℃的温度下进行。烷基化反应条件中,压力一般可以为1-3.4mpa,优选为1.2-3.2mpa,如1.5-3.0mpa。所述压力为表压。根据本发明,以烯烃计的进入各催化剂床层的物料的质量空速可以为0.05-1h-1,优选为0.07-0.5h-1,例如为0.08-0.25h-1。根据本发明的一种优选实施方式,催化剂在轴向移动床反应器中的停留时间为6-72h,优选为12-72h。根据本发明提供的方法,对所述催化剂没有特别的限定,可以为本领域常规使用的各种催化剂,例如可以为固体酸催化剂。优选地,所述固体酸催化剂含有分子筛和耐热无机氧化物,以所述固体酸催化剂的总量为基准,分子筛的含量为65-95重量%,进一步优选为65-90重量%,耐热无机氧化物的含量为5-35重量%,进一步优选为10-35重量%。进一步优选地,所述分子筛选自fau结构沸石、beta结构沸石和mfi结构沸石中至少一种。本发明中,所述耐热无机氧化物是指最高使用温度不低于600℃的无机氧化物。所述耐热无机氧化物可以为氧化铝和/或氧化硅。在本发明的一种更为优选的实施方式中,所述固体酸催化剂还含有金属活性组分,所述金属活性组分选自fe、co、ni、pd和pt中至少一种,以所述固体酸催化剂的总量为基准,金属活性组分的含量为0.15-2重量%。采用根据该优选实施方式的催化剂,在其余条件相同的情况下,能获得更长的周期寿命和使用寿命,同时还能获得更高的产物选择性。根据本发明,所述催化剂的平均粒径可以为0.3-3mm。根据本发明的一种优选实施方式,相邻两个催化剂床层3之间设置有分离件10,所述分离件10与催化剂输送管16连通,所述分离件10用于上游催化剂床层反应后物料和催化剂的分离,分离件10分离得到的催化剂通过催化剂输送管16向下移动。上游催化剂床层反应后物料和催化剂经过分离件10进行分离,得到反应后物料和催化剂,催化剂通过催化剂输送管16向下移动,而反应后物料在相邻两个催化剂床层之间的空间(本发明中称其为反应床层前的床层空间)与催化剂床层3的上方的进料口送入的液态新鲜原料混合,然后流入下游催化剂床层。根据本发明的一种具体实施方式,所述分离件10可以是具有孔的筛网(孔径可以根据催化剂颗粒大小决定),其允许反应后物料通过,以实现反应后物料和催化剂的分离。为了使得流入下游催化剂床层的反应后物料和液态新鲜原料混合更加均匀,优选地,相邻两个催化剂床层3之间设置有反应物料折流件11,所述反应物料折流件11用于强化反应后物料和进料口2送入的液态新鲜原料的混合。本发明对所述反应物料折流件11的具体结构没有特别的限定,只要能够起到强化强化反应后物料和液态新鲜原料的混合即可。具体的,反应物料折流件11放置于反应床层前的床层空间内,其数量可以为1个或者两个以上,优选为1-6个。根据本发明的第一种优选实施方式,如图2所示,所述反应物料折流件11包括主轴111和沿主轴轴向螺旋延伸的输送部件112。具体地,输送部件112形成的螺旋延伸的流道的入口根据进料口2的位置进行设定使得反应后物料和液态新鲜原料从输送部件112形成的螺旋延伸的流道流动,进而实现混合。根据本发明的第二种优选实施方式,如图1所示,所述反应物料折流件11包括多个折流板113,多个折流板113沿轴向移动床反应器1的轴向倾斜设置,且多个折流板113相互之间交错设置以形成能够供反应物料通过的流道。所述多个折流板113沿轴向移动床反应器1的轴向可以是倾斜向下设置,也可以是倾斜向上设置(如图1所示)。优选地,折流板113的延伸方向与水平面的夹角在5-60°,进一步优选为10-40°。本发明中所述的折流板113相互之间交错设置是指折流板113相互之间不形成封闭区域,使得反应物料能够顺利的向下流动。根据本发明的一种具体实施方式,如图1所示,部分折流板113固定连接于轴向移动床反应器1的器壁,部分折流板113固定连接于催化剂输送管16的管壁,且折流板113相互之间平行设置。优选地,相邻折流板113之间的距离为15-60mm。根据本发明的一种优选实施方式,相邻两个催化剂床层3之间设置有催化剂分布件,所述催化剂分布件用于分散催化剂输送管16出口的催化剂。如果不设置催化剂分布件,催化剂输送管16出口的催化剂容易在下游催化剂床层形成锥状堆积。优选所述催化剂分布件包括锥型分布挡板12,所述锥型分布挡板12与催化剂输送管16同轴设置。催化剂输送管16出口的催化剂依靠重力作用,落于锥型分布挡板12的尖端,通过锥型分布挡板12的分散作用,向催化剂输送管16的水平两侧分散。进一步优选地,锥型分布挡板12与催化剂输送管16的数量相同。根据本发明的一种优选实施方式,所述催化剂分布件还包括设置在所述锥型分布挡板12下方的水平分布挡板13,所述水平分布挡板13上设置有供催化剂通过的孔。本发明对所述水平分布挡板13的数量没有特别的限定,可以为1个,也可以为两个以上,优选分别设置在相邻两个锥型分布挡板12的径向中间位置(且轴向下方位置)。所述径向和轴向指的是轴向移动床反应器1的径向和轴向。进一步优选地,沿轴向移动床反应器1的中心水平向外方向上,所述水平分布挡板13上的孔逐步变大。采用该种优选实施方式,靠近轴向移动床反应器1的中心位置通过锥型分布挡板12的分散的催化剂部分从所述水平分布挡板13孔通过,部分不能够通过的催化剂被分散至轴向移动床反应器1的边缘位置,更有利于保证催化剂的均匀分散。进一步优选地,所述水平分布挡板13可为中间区域开孔率低、边壁处开孔率高的圆形分布板。处于轴向移动床反应器1各催化剂床层中的催化剂随着反应的进行会逐渐失活的同时也会逐渐下落至更下游的催化剂床层最终到达轴向移动床反应器1底部,随后通过催化剂输送管线输送至待生剂接收器5。根据本发明的一种优选实施方式,轴向移动床反应器1下部设置有底部催化剂收集区37。通过最下游催化剂床层的催化剂送入底部催化剂收集区37,收集一定量后送至待生剂接收器5。根据本发明的一种具体实施方式,如图1所示,轴向移动床反应器1与待生剂接收器5、待生剂接收器5与催化剂再生器4、催化剂再生器4与再生剂接收器6、再生剂接收器6与轴向移动床反应器1的连通管线上分别设置有容器间的物料管线阀。根据本发明的一种优选实施方式,待生剂接收器5(优选底部)设置退液相料出口15。本发明可以在待生剂接收器5中通过直接减压或引入高压氢气、氮气等充压的方式脱除催化剂中携带的液相物料,液相物料可以通过退液相料出口15外输。优选地,从所述退液相料出口15送出的退液相料输送管线上设置有脱液过滤器7。所述脱液过滤器7用于阻隔催化剂细粉或细小颗粒。待生剂接收器5中脱液后的催化剂送入催化剂再生器4中进行再生。所述催化剂再生器4设置有再生介质进料口30和再生后介质出料口31。再生介质通过再生介质进料口30送入催化剂再生器4中与催化剂接触对催化剂进行再生(优选完全再生),再生后介质通过再生后介质出料口31外排。优选地,从所述再生后介质出料口31送出的再生后介质输送管线上设置有再生后介质过滤器8。该过滤器用于阻隔再生器的催化剂流入下游的气体循环增压设备以及收集再生过程因摩擦或吹扫产生的细粉或细小颗粒。根据本发明的方法,对于再生的方式没有特别限定,可以在常规的再生条件下进行。所述再生介质可以为含氧气氛或含氢气氛。具体地,所述再生可以在含氢气氛中进行,也可以在含氧气氛中进行。所述含氧气氛含有氧气以及可选的载气,所述载气可以选自非活性气体,其具体实例可以包括但不限于氮气和零族元素气体(如氩气)。所述含氧气氛中,氧气的含量可以为0.5-20体积%。另外,还可以根据再生的进程对氧气的含量进行调整。所述含氢气氛中可以含有氢气和c4液化气,氢气的含量为70-99体积%。作为再生的一个实例,所述再生在氢气气氛中进行,可以在100-400℃、优选180-280℃的温度下进行再生;再生时,反应器内的压力可以为0.1-5mpa,优选为0.5-3.5mpa,所述压力为表压。作为再生的另一个实例,所述再生在含氧气氛中进行,可以在180-500℃的温度下进行再生;再生时,反应器内的压力可以为0.01-0.5mpa,所述压力为表压。根据本发明,优选地,所述再生介质在催化剂再生器4中的表观流速为0.003-0.8m/s,进一步优选为0.02-0.5m/s。根据本发明的一种优选实施方式,该方法还包括:向催化剂再生器4中引入新鲜催化剂。具体地,催化剂再生器4可以设置有新鲜催化剂进料口供新鲜催化剂进入催化剂再生器4中。通过在催化剂再生器4上设置新鲜催化剂进料口,可将部分失去活性的催化剂或难以恢复初始活性的催化剂置换为新鲜催化剂,保证装置的处理能力。具体地,与新鲜催化剂进料口连通的新鲜催化剂输送管线上设置有泵。再生后的催化剂会通过催化剂再生器4底部的催化剂输送管线流入再生剂接收器6中。根据本发明的一种优选实施方式,该方法还包括采用液相料置换再生剂接收器6中催化剂间隙的气体。具体地,再生剂接收器6设置有液相料补充入口32。通过液相料补充入口32向再生剂接收器6中引入液相料置换催化剂间隙的气体。本发明对所述液相料没有特别的限定,例如可以为烷烃或轴向移动床反应器1底部得到的反应产物。再生后的催化剂会通过再生剂接收器6与轴向移动床反应器1间的催化剂输送管道返回轴向移动床反应器1,继续参与反应,直至失活后被输送至待生剂接收器5,催化剂按照上述流程循环。根据本发明的一种优选实施方式,待生剂接收器5、催化剂再生器4和再生剂接收器6依次自上而下设置,待生剂接收器5、催化剂再生器4和再生剂接收器6之间的催化剂流通管线为垂直设置或与水平面间的夹角不小于40度倾斜设置。采用该种优选实施方式更便于催化剂颗粒料从上而下的顺畅流通,防止物料堆积或残存在管线中,影响阀门密封性或催化剂再生的效果。根据本发明的一种优选实施方式,轴向移动床反应器1的催化剂出口与待生剂接收器5的催化剂入口的连通管线上设置有第一颗粒流量调节器25;再生剂接收器6的催化剂出口与轴向移动床反应器1的催化剂入口的连通管线上设置有第二颗粒流量调节器33。本发明对所述第一颗粒流量调节器25和第二颗粒流量调节器33没有特别的限定,只要能够调节催化剂颗粒的流量即可。进一步优选地,所述第一颗粒流量调节器25和第二颗粒流量调节器33各自独立地为l型或近似l型的物料输送阀组。具体地,所述l型或近似l型的物料输送阀组上还连通至少一路液相物料进料管线。设置颗粒流量调节器可以增加颗粒物料的流通阻力,同时,在该调节器上连通至少一路的液相物料进料管线,用以增加颗粒物料的流动推动力并降低颗粒物料的流动阻力。通过设置l型或近似l型的物料输送阀组,通过改变进入阀组的液相物料流量可调节催化剂的排出速率,从而达到控制和调节处于反应器中的催化剂在各反应床层的下落速率和停留时间。根据本发明的一种优选实施方式,该装置还包括催化剂缓冲罐38,所述催化剂缓冲罐38设置在轴向移动床反应器1、待生剂接收器5之间,催化剂缓冲罐38的催化剂入口与轴向移动床反应器1的催化剂出口连通,催化剂缓冲罐38的催化剂出口与待生剂接收器5的催化剂入口连通。所述催化剂缓冲罐38用以保存待生剂接收器在退液相料以及向催化剂再生剂排催化剂期间从轴向移动床反应器1排出的催化剂,保证轴向移动床反应器1内催化剂物料流动的连续性和装置操作的平稳性。本发明提供的方法采用液固轴向移动床反应与再生装置,可以实现固体酸烷基化反应与失活催化剂再生的连续平稳运行,提高了目标产物的选择性和装置操作的弹性,大大降低了催化剂投资成本,提高了装置的经济竞争力。以下说明本发明提供的固体酸烷基化方法的一种具体实施方式。如图1所示,轴向移动床反应器1中设置有三个催化剂床层3,待生剂接收器5、催化剂再生器4和再生剂接收器6依次自上而下设置,且三者之间的催化剂流通管线为垂直设置。含有异丁烷的新鲜烯烃原料自管线17引入,通过第一分支管线19与循环料混合后从进料口2进入轴向移动床反应器1的反应区与第一个催化剂床层3接触反应,通过第二分支管线20和第三分支管线21的新鲜烯烃原料从进料口2送入与上游催化剂床层的反应后料在轴向移动床反应器1的反应床层前的床层空间中进行混合。相邻两个催化剂床层3之间设置有分离件10,反应后料通过分离件10,未通过分离件10的催化剂通过催化剂输送管16向下移动。相邻两个催化剂床层3之间设置反应物料折流件11,通过分离件10的反应后料以及新鲜物流在反应物料折流件11作用下强化混合。相邻两个催化剂床层3之间还设置有催化剂分布件(包括与催化剂输送管16同轴设置的锥型分布挡板12和设置在所述锥型分布挡板12下方的水平分布挡板13),催化剂输送管16出口的催化剂在催化剂分布件作用下分散下落至下游催化剂床层3。轴向移动床反应器1下部设置有底部催化剂收集区37。通过最下游催化剂床层的催化剂送入底部催化剂收集区37,收集一定量后送至待生剂接收器5。轴向移动床反应器1的催化剂出口与待生剂接收器5的催化剂入口的连通管线上设置有第一颗粒流量调节器25,以调节催化剂颗粒流量。待生剂接收器5底部设置退液相料出口15,在待生剂接收器5中脱除催化剂中携带的液相物料,从所述退液相料出口15送出的退液相料输送管线上设置脱液过滤器7以阻隔催化剂细粉或细小颗粒。待生剂接收器5中脱液后的催化剂送入催化剂再生器4中进行再生,所述催化剂再生器4设置有再生介质进料口30和再生后介质出料口31。再生介质通过再生介质进料口30送入催化剂再生器4中与催化剂接触对催化剂进行再生,再生后介质通过再生后介质出料口31外排。从所述再生后介质出料口31送出的再生后介质输送管线上设置再生后介质过滤器8以阻隔细粉或细小颗粒。催化剂再生器4还可以设置有新鲜催化剂进料口供新鲜催化剂进入催化剂再生器4中。通过在催化剂再生器4上设置新鲜催化剂进料口,可将部分失去活性的催化剂或难以恢复初始活性的催化剂置换为新鲜催化剂,保证装置的处理能力。再生后的催化剂通过催化剂再生器4底部的催化剂输送管线流入再生剂接收器6,再生剂接收器6设置有液相料补充入口32。通过液相料补充入口32向再生剂接收器6中引入液相料置换催化剂间隙的气体。再生后的催化剂会通过再生剂接收器6与轴向移动床反应器1间的催化剂输送管道返回轴向移动床反应器1继续参与反应,直至失活后被输送至待生剂接收器5,催化剂按照上述流程循环。再生剂接收器6的催化剂出口与轴向移动床反应器1的催化剂入口的连通管线上设置有第二颗粒流量调节器33,以调节催化剂颗粒流量。以下将通过实施例对本发明进行详细描述。实施例1本实施例在图1所示的液固轴向移动床反应与再生装置上进行。其中,轴向移动床反应器1、待生剂接收器5、催化剂再生器4和再生剂接收器6通过管线依次连接。轴向移动床反应器1的内径为600mm,高为15m,从上至下设置三段催化剂床层3(分别记为第一催化剂床层、第二催化剂床层、第三催化剂床层)每段催化剂床层3的高度为3.5m,相邻催化剂床层3之间的距离为1.2m。第一催化剂床层、第二催化剂床层之间以及第二催化剂床层、第三催化剂床层之间各设置2个圆柱形催化剂输送管16,催化剂输送管16的内径为20mm。第一催化剂床层下方、第二催化剂床层下方分别设置有分离件10(缝隙宽度为0.2mm的楔形滤网)。第一催化剂床层、第二催化剂床层之间以及第二催化剂床层、第三催化剂床层之间各设置1个如图2所示的反应物料折流件11,所述反应物料折流件11包括主轴111和沿主轴轴向螺旋延伸的输送部件112,输送部件112形成的螺旋延伸的流道的入口位于第二分支管线20和第三分支管线21的新鲜烯烃原料的进料口2的下方。反应物料折流件11设置于催化剂输送管16所在中心区域与反应器壁之间的环隙空间。第一催化剂床层、第二催化剂床层之间以及第二催化剂床层、第三催化剂床层之间各自还设置有3个与催化剂输送管16同轴设置的锥型分布挡板12(高度为0.1m),3个设置在所述锥型分布挡板12下方的水平分布挡板13(圆形分布板),水平分布挡板13上设置有供催化剂通过的孔,沿轴向移动床反应器1的中心水平向外方向上,所述水平分布挡板13上的孔逐步变大,最大的孔孔径设置为25mm,最小的孔孔径设置为5mm。轴向移动床反应器1下部设置有底部催化剂收集区37。待生剂接收器5、催化剂再生器4和再生剂接收器6依次自上而下设置,待生剂接收器5、催化剂再生器4和再生剂接收器6之间的催化剂流通管线为垂直设置。待生剂接收器5、催化剂再生器4和再生剂接收器6的直径均为1200mm,直管段高均为6m。物料循环管线的直径为250mm。反应新鲜原料为异丁烷、正丁烷和丁烯等的混合物从新鲜料进料管线17进料后,分为三路进入各自对应的催化剂床层3,进入各催化剂床层3的混合后物料的烷烯摩尔比为700:1,在反应器内循环物料的流速为1.9m/s,相应的新鲜料总进料量为482kg/h,烯烃的质量空速为0.25h-1。催化剂在轴向移动床反应器1中的停留时间为72h。使用的催化剂为fau结构分子筛球形催化剂,平均粒径为1.8mm。其制备方法为采用中国石化催化剂分公司生产的fau结构的nay型分子筛,通过离子交换等步骤去除分子筛上的钠离子;然后将分子筛与和氧化铝以65:35的重量比例混合均匀,采用油氨柱成型法制成小球,进一步经干燥、焙烧制得所述催化剂。轴向移动床反应器1中的反应温度为70℃,反应压力为2.5mpa。新鲜料和循环料混合从进料口2送入轴向移动床反应器1中与第一催化剂床层装填的催化剂进行接触反应,分离件10分离得到的反应后物料经与来自第一分支管线19的新鲜料经过折流件11的强化混合送入第二催化剂床层进行反应,分离件10分离得到的催化剂通过催化剂输送管16在催化剂分布件作用下分散下落至下游催化剂床层,最后催化剂下落至底部催化剂收集区37。底部催化剂收集区37得到的催化剂通过催化剂出口送至待生剂接收器5。轴向移动床反应器1的催化剂出口与待生剂接收器5的催化剂入口的连通管线上设置有第一颗粒流量调节器25(l型的物料输送阀组),且l型的物料输送阀组上还连通一路液相物料进料管线以控制催化剂的流量(20kg/h)。向待生剂接收器5中通入氮气以脱除催化剂中携带的液相物料,液相物料通过退液相料出口15外输,从所述退液相料出口15送出的退液相料输送管线上设置有脱液过滤器7。待生剂接收器5中脱液后的催化剂送入催化剂再生器4中进行再生,采用氮气和空气的混合气(氧气的体积浓度为1-21体积%从小至大调整,表观气速为0.1m/s)作为催化剂高温深度再生介质,高温(350-480℃从小至大调整)、常压深度再生的周期为24h,所述混合气通过再生介质进料口30送入,再生后介质通过再生后介质出料口31外排,从所述再生后介质出料口31送出的再生后介质输送管线上设置有再生后介质过滤器8。催化剂再生器4还可以设置有新鲜催化剂进料口供新鲜催化剂进入催化剂再生器4中。再生后的催化剂会通过催化剂再生器4底部的催化剂输送管线流入再生剂接收器6中。再生剂接收器6设置有液相料补充入口32,通过液相料补充入口32向再生剂接收器6中引入反应后含油液相物料置换催化剂间隙的气体,得到的催化剂浆料循环至轴向移动床反应器1顶部。再生剂接收器6的催化剂出口与轴向移动床反应器1的催化剂入口的连通管线上设置有第二颗粒流量调节器33(l型的物料输送阀组),且l型的物料输送阀组上还连通一路液相物料进料管线以控制催化剂浆料的流量(20kg/h)。实施例2在如图3所示的装置上进行固体酸烷基化反应。与实施例1的区别仅在于该装置在轴向移动床反应器1、待生剂接收器5之间还设置有直径为500mm,直管段高为4.2m的催化剂料缓冲罐38。该实施例增加了催化剂料缓冲罐38保证了待生剂接收器在进行脱液操作和向再生器内转移催化剂时,反应器内的催化剂仍旧保持原有的速度向下缓慢移动,待上述操作完成后,逐步将催化剂缓冲罐内积累的催化剂排至待生剂接收器,保证轴向移动床反应器1内催化剂物料流动的连续性和装置操作的平稳性。实施例3在图1所示的装置上进行固体酸烷基化反应。不同的是,将图2所示的反应物料折流件11替换为如图1所述反应物料折流件11,反应物料折流件11包括8个平行且交错设置的折流板113,折流板113的延伸方向与水平面的夹角为25°,折流板113沿轴向移动床反应器1的轴向倾斜向上设置,4个折流板113固定连接于轴向移动床反应器1的器壁,4个折流板113固定连接于催化剂输送管16的管壁,相邻折流板113之间的距离为25mm。对比例1在两台并联的固定床中型试验装置上进行固体酸烷基化反应,具体操作过程为,当第一台反应器处于烷基化反应时,第二台反应器进行高温深度再生操作,两台并联的固定床反应器切换使用,进而使得装置可以连续稳定运行。每个固定床反应器的内径为200mm,高2500mm。反应器内装填的催化剂制备方法与实施例1中相同,区别仅为小球的直径为2.7mm,装填量为28kg,装填高度为1500mm。反应原料为异丁烷和丁烯的混合物,反应器内的烷烯摩尔比为800:1,新鲜混合烯烃的进料量为6.3kg/h,烯烃的质量空速为0.09h-1。每隔24h需要对床层内的催化剂进行一次高温深度再生,采用氮气和空气的混合气(与实施例1相同)在温度从常温升高到480℃,常压下对床层内的催化剂进行高温氧化再生3h,再生后需要对床层进行冷却操作,整个再生周期24h。再生结束后将处于反应状态的反应器内物料退至再生完毕的反应器,继续用再生后催化剂开展烷基化反应实验,而将退完反应物料的反应器切入再生操作,如此反复循环。上述实施例和对比例的装置连续稳定运行1000h后,对所得的烷基化油进行测定,试验结果如表1所示。表1ronmon烯烃c5+收率tmp/dmhc9+产物wt%实施例195.591.51.993.535.12实施例295.892.02.03.625.08实施例395.792.02.03.605.11对比例195.291.31.963.246.76从表1中可以看出,采用本发明提供的固体酸烷基化方法所得的烷基化油的辛烷值略优于固定床技术,烷基化油中的烯烃收率更高,且具有更高的目标产物(三甲基戊烷)选择性,c9+产物的收率也更低。相比于实施例1,带有催化剂缓冲罐的实施例2,具有更优的产品收率和目标产物选择性。从装置运行角度来看,对于固定床烷基化技术,为了实现反应装置的连续稳定运行,至少需要两台以上的反应器切换操作(如对比例1),每隔一定时间对床层内的催化剂进行高温再生,深度再生后还要对高温床层进行降温操作,由于装置频繁的在反应与再生温度之间进行切换,使得其在工业应用中连续稳定运行时带来了很多问题,而本发明提供的方法采用液固轴向移动床反应与再生装置,单台(套)设备即可满足要求,减少了装置的投资成本,另外通过将失活的催化剂颗粒引出液固轴向移动反应器外进行深度再生,在不影响反应装置稳定运行的前提下,实现了催化剂反应和再生的连续化操作,维持了装置内的催化剂具有较为稳定的平衡活性,提高了烷基化油中目标产物的选择性。因此本发明提供的方法具有更好的工业应用前景。以上详细描述了本发明的优选实施方式,但是,本发明并不限于此。在本发明的技术构思范围内,可以对本发明的技术方案进行多种简单变型,包括各个技术特征以任何其它的合适方式进行组合,这些简单变型和组合同样应当视为本发明所公开的内容,均属于本发明的保护范围。当前第1页12