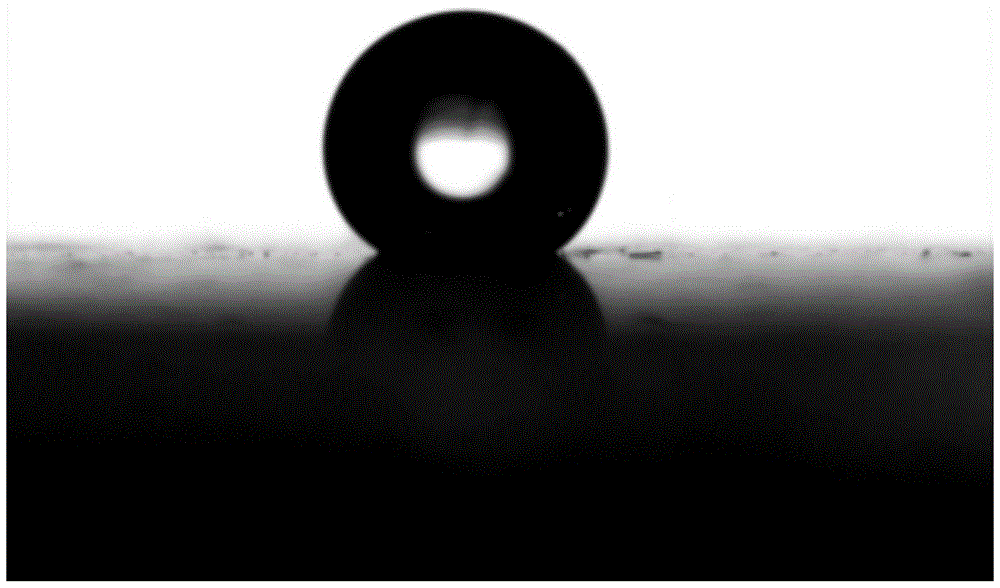
本发明属于无机非金属材料
技术领域:
,尤其涉及一种油水分离膜及其制备方法。
背景技术:
:近年来,随着我国对环境保护的重视和美好家园的向往,人们的环保意识普遍提高,相应环保行业政策相继出台。其中,油水分离的应用需求显得尤为紧迫,诸如海洋远轮的石油泄漏事故所产生的油水分离难题,有机化学实验室的油性/水性两相混合物的分离,以及餐厨行业的地沟油回收处理等。一般来说,目前的分离方法主要包括物理法、生物法、化学法和电化学法等,其中物理法分离又包括重力法分离、离心法分离、过滤法分离等。这些传统的油水分离技术一般具有设备简单、单次处理成本低,操作方法简单等优势,但另一方面,这些方法普遍存在分离效率较低、占地面积较大等缺点,且油污回收效率低,难以满足越来越严苛的环保要求。近年来,材料科学的进步极大地推动了油水分离领域的技术发展。例如,利用材料表面的特殊浸润性所构筑的新型油水分离膜材料,目前已成为表界面材料领域的研究热点之一,并逐渐成为清理水面浮油和油水分离的重要方法,有望对解决水域污染等问题的解决将会起着至关重要的作用。一般来说,利用材料的特殊浸润性进行油水分离与传统的分离方法相比,具有材料性质稳定、分离效果好、分离效率高的优点。一般来说,可根据材料性质将油水分离材料分为两种:1)超疏水-超亲油分离膜,又被称为“除油型”分离膜;2)超亲水-超疏油分离膜,又被称为“除水型”分离膜。其中“除油型”分离膜因其油水选择性强、分离效果好的优点被广泛应用,但其亲油的本质使得这种材料在使用的过程中存在以下问题:极易被油污染,使用后的弃置或焚烧等处理方式往往会造成对环境的二次污染。因此,如何开发出绿色环保、可重复使用,且制备工艺简单,便于工业化生产的的超疏水-超亲油分离膜“除油型”的油水分离膜材料就显得极为重要。随着工业的发展与生态环境保护日益的紧迫,生态文明建设已经成为国家层面的战略任务,工业排放的油水混合体,是生态破坏生态环境的头号杀手。因此,如何净化工业废水,油水混合体,一直是学术界与工业界的研究热门课题。目前的“除油型(超疏水-超亲油)”油水分离膜的技术缺点主要有:1)工艺流程复杂、工业生产的可控性不强,如专利cn201810742339.7采用静电纺丝加层层自组装的复杂工艺制备油水分离膜,其工艺繁多,流程复杂;2)目前的工艺技术,如涂覆、结晶生长、电沉积等,所制备的微纳复合结构一般不稳定,微/纳粒子易磨损和脱落;3)采用聚合物作为主体材料,存在材料重复使用程度低、易污染环境等问题。综上所述,现有技术的油水分离膜存在微纳复合结构一般不稳定,微/纳粒子易磨损和脱落,以及重复使用程度低、易污染环境的技术缺陷。技术实现要素:本发明第一方面提供了一种微纳复合结构强度高,微/纳米粒子不易磨损和脱落,可重复使用,无污染的可进行油水分离的油水分离膜。本发明第二方面提供了一种制备工艺流程简单、工业生产的可控性强的可进行油水分离的油水分离膜的制备方法。有鉴于此,本申请提供了一种油水分离膜的制备方法,包括以下步骤:步骤1、将陶瓷粉体、溶剂和酸碱调节剂混合,得到陶瓷粉体浆料;步骤2、将所述陶瓷粉体浆料与有机酸混合反应,得到第一反应物;步骤3、将所述第一反应物、表面活性剂和有机溶剂混合进行乳化,得到第二反应物;步骤4、将所述第二反应物依次进行成型和干燥处理,得到陶瓷膜素坯;步骤5、将所述陶瓷膜素坯进行烧结处理,得到多孔陶瓷膜;步骤6、将所述油水分离陶瓷膜的表面设置疏水层,得到油水分离膜。作为优选,步骤1中,通过添加酸碱调节剂,调节溶剂的ph值,以提高陶瓷粉体在溶剂的溶解速度,溶剂的ph低于7,可以提高陶瓷粉体在溶剂的溶解速度和溶解性,以使得在酸性条件下少量的溶剂可以融入大量的陶瓷粉体。作为优选,所述酸碱调节剂选自盐酸、硫酸、硝酸等强酸,或弱酸以及氢氧化钠等强碱。更为优选,所述酸碱调节剂选自盐酸和氢氧化钠。作为优选,步骤1中,所述ph范围为3.0~7.0。更优选的,步骤1中,所述ph范围为4.3~6.0。优选的,步骤1中,所述ph为5.3。作为优选,步骤1中,所述陶瓷粉体选自氧化铝、氧化锆、氧化锆增韧氧化铝陶瓷、氮化硼、氮化硅和氮化铝中的一种或多种;所述溶剂选自去离子水或/和酒精。作为优选,步骤1中,所述陶瓷粉体浆料中的所述陶瓷粉体的固相含量为5vol%~80vol%。更为优选,步骤1中,所述陶瓷粉体浆料中的所述陶瓷粉体的固相含量为30vol%~60vol%。作为优选,步骤1中,所述混合为球磨混合,所述球磨时间为0.5~24h,所述球磨的转速为200~600r/min。更优选的,步骤1中,所述球磨时间为5~12h,所述球磨的转速为250~350r/min。其中,所述酸碱调节剂用于调节ph以形成化学配位反应,球磨混合用以打散团聚,以提供陶瓷粉体浆料的分散性。作为优选,步骤2中,所述有机酸选自丙酸或/和戊酸;所述有机酸的添加量为:每克所述陶瓷粉体添加0.01mmol-0.1mmol所述有机酸;所述混合反应的混合时间为2-10分钟。作为优选,步骤2中,将所述陶瓷粉体浆料与有机酸混合反应为搅拌混合,所述搅拌的时间为0.05~0.5h,所述搅拌的转速为200~300r/min。需要说明的是,本申请发现将陶瓷粉体浆料与有机酸混合反应,对陶瓷粉体进行修饰处理,使得陶瓷粉体浆料的陶瓷粉体的表面接枝羧基官能团,以实现对陶瓷粉体的修饰处理,也便于后续的乳化成微液滴状的第二反应物。作为优选,步骤3中,所述表面活性剂选自聚乙烯醇、聚乙二醇、十八烷基硫酸钠和硬脂酸钠中的一种或多种;所述有机溶剂选自正辛烷、十六烷和正己烷中的一种或多种。作为优选,步骤3中,所述聚乙烯醇在所述第二反应物中的的添加量为:每克所述溶剂添加0.1wt%~10wt%的聚乙烯醇;所述有机溶剂在所述第二反应物中的体积百分比≤95%,其中,所述溶剂为去离子水或/和酒精。需要说明的是,本申请发现,通孔控制所述聚乙烯醇在所述第二反应物中的体积百分比,可控制油水分离膜的多孔结构的孔径,具体的,所述聚乙烯醇在所述第二反应物中占比越大,油水分离膜的的孔径越小。作为优选,步骤3中,将所述第一反应物、表面活性剂和有机溶剂混合包括搅拌混合,所述搅拌的时间为0.05h~0.5h。需要说明的是,请参阅图11,图11为本申请本申请提供的油水分离膜烧结前的三维模拟图,发现将第一反应物、表面活性剂和有机溶剂混合后进行乳化发泡处理,表面活性剂把有机溶剂(例如正辛烷、十六烷和正己烷中的一种或多种)分割成无数小油滴,陶瓷粉体包覆小油滴形成自组装(陶瓷粉体包覆有机溶剂),有机溶剂挥发或/和蒸发后有机溶剂所占据的孔就形成油水分离膜的孔洞,也就是说,第一反应物为表面修饰有羧基官能团的陶瓷粉体,对微液滴的包覆作用,实现自组装功能,形成陶瓷粉体包覆有机溶剂的微液滴,微液滴中的有机溶剂挥发后,形成规则的三维网络多孔镂空结构。具体的,通过表面活性剂和有机溶剂的作用下,使得表面修饰有羧基官能团的陶瓷粉体在陶瓷粉体浆料中实现自组装,形成规律排列的蜂窝状微米尺度油液滴群,将乳化后的陶瓷浆料进行成型和烧结。作为优选,步骤4中,所述成型包括传统模具成型、3d打印成型、注浆成型、注凝成型、压铸成型或流延成型。其中,使用3d打印成型可实现复杂形状的陶瓷膜制备。作为优选,步骤4中,所述3d打印成型为自由直写成型3d打印成型。作为优选,步骤4中,所述干燥用以去除第二反应物成型后的溶剂或液体物质,例如油滴;为后续烧结做干燥处理;所述干燥为自然干燥或烘箱干燥;所述自然干燥的时间为72h。作为优选,步骤5中,所述烧结的温度为1000℃~1700℃;所述烧结温度在800℃以下,所述烧结的升温速度不超过10℃/min,所述烧结温度在800℃以上,所述烧结的升温速度不超过5℃/min,在最高温度处保温两小时。更为优选,步骤5中,所述烧结的温度为1200℃~1700℃;所述烧结温度在800℃以下,所述烧结的升温速度不超过10℃/min,所述烧结温度在800℃以上,所述烧结的升温速度不超过5℃/min,在最高温度处保温两小时。作为优选,步骤6中,所述疏水层的材质选自聚二甲基硅氧烷、硬脂酸、聚四氟乙烯、聚硅氮烷和三甲氧基(1h,1h,2h,2h-十七氟癸基)硅烷中的一种或多种。更为优选,步骤6中,所述疏水层的材质选自聚二甲基硅氧烷。作为优选,将所述油水分离陶瓷膜的表面设置疏水层的方法包括:气相沉积法、物理涂覆或浸泡法。其中,在所述油水分离陶瓷膜的表面设置疏水层,使得所述油水分离陶瓷膜为水不可通过,油可通过的超疏水-超亲油的油水分离膜。其中,所述气相沉积的温度为200℃~300℃。优选的,所述气相沉积的温度为235℃。其中,所述物理涂覆和浸泡的温度为室温。本发明第二方面公开了一种油水分离膜,包括上述所述制备方法制得的油水分离膜。具体的,本申请提供了具体的油水分离膜的制备方法,以去离子水作为溶剂,氧化铝陶瓷粉体作为粉体材料,混合比例为58vol%粉体在超声环境与搅拌环境下逐渐加入,并逐步用hcl调节ph,调节ph低于5.0,球磨混合,球磨处理时间及转速分别设为12h、300r/min;接着,球磨后的悬浮液用去离子水稀释为46vol%的浆料样品,采用丙酸作为有机酸分子,并在大力搅拌下加入丙酸;然后,添加表面活性剂pva及有机溶剂正辛烷,在搅拌状态下先加pva,混合均匀后加入正辛烷,搅拌发泡10min;采用模具成型实现陶瓷素坯的成型制备,采用自然干燥作为干燥条件,时间为72h;脱模后进行1550℃的烧结处理;磨样后选择pdms作为疏水分子,采用气相沉积方法实现疏水分子在陶瓷膜体表面及内部的均匀涂覆与镀层。从以上技术方案可以看出,本申请具有以下优点:本申请提供了一种油水分离膜,将陶瓷粉体的表面修饰接枝羧基官能团,有利于修饰后的陶瓷粉体在特定环境下实现自组装,即表面活性剂把有机溶剂(例如正辛烷、十六烷和正己烷中的一种或多种)分割成无数小油滴,陶瓷粉体包覆小油滴形成自组装(陶瓷粉体包覆有机溶剂),有机溶剂挥发或/和蒸发后有机溶剂所占据的孔就形成油水分离膜的孔洞,因此,将乳化后的最终浆料进行成型和烧结后,再在表面设置疏水层,形成具有超亲油—超疏水、油水分离效率高、轻质高强、耐磨抗压,且绿色环保、可多次重复使用的具有多孔结构的油水分离膜。同时,本申请的油水分离膜的制备方法简单,可以通过控制原料的添加量以控制油水分离膜的孔径,其工业生产的可控性强。实验表明,本申请的油水分离膜油水分离效率高、抗压强度大,使得其结构强度高,表面微纳米粒子不易磨损,不会脱落;油水分离膜具有多孔结构,具体是有序排列的规则的三维网格多孔镂空结构;并且其结构三维可控,可通过原料的添加量实现多孔结构中孔径与通孔的任意大小比例;且油水分离膜可以重复使用,无污染。附图说明为了更清楚地说明本发明实施例或现有技术中的技术方案,下面将对实施例或现有技术描述中所需要使用的附图作简单地介绍。图1为本申请提供实施例1的油水分离膜的超疏水接触角表征试验图;图2为本申请提供实施例1的油水分离膜的超亲油接触角表征试验图;图3为本申请提供实施例1的油水分离膜进行油水分离侵润性实物图;图4为本申请提供对比例1的产品进行油水分离侵润性实物图;图5为本申请提供实施例1的油水分离膜的油水分离试验的示意图,其中,a为同时往实施例1的油水分离膜上滴加油滴1和水滴2,b为油滴1穿过实施例1的油水分离膜,水滴2不通过实施例1的油水分离膜,c为水滴2以水滴状停留在实施例1的油水分离膜的表面;图6为本申请实施例的油水分离膜(pva1wt%)放大100倍的扫描电镜图;图7为本申请实施例的油水分离膜(pva1wt%)放大200倍的扫描电镜图;图8为本申请实施例的油水分离膜(pva1wt%)放大400倍的扫描电镜图;图9为本申请实施例的油水分离膜(pva1wt%)放大1200倍的扫描电镜图;图10为本申请实施例的油水分离膜(pva1wt%)放大10000倍的扫描电镜图;图11为本申请本申请提供的油水分离膜烧结前的三维模拟图。具体实施方式本发明提供了一种油水分离膜及其制备方法,有效解决了现有技术的油水分离膜存在微纳复合结构一般不稳定,微/纳粒子易磨损和脱落,以及重复使用程度低、易污染环境的技术缺陷。下面将对本发明实施例中的技术方案进行清楚、完整地描述,显然,所描述的实施例仅仅是本发明一部分实施例,而不是全部的实施例。基于本发明中的实施例,本领域普通技术人员在没有做出创造性劳动前提下所获得的所有其他实施例,都属于本发明保护的范围。其中,以下实施例所用原料均为市售或自制;陶瓷粉体:α-al2o3,购自大明氧化铝tm-dar(粒径0.2um;密度3.98g/ml;日本大明化学);丙酸:化学式为ch3ch2cooh,纯度99%,mw为74.08,百灵威科技;聚乙烯醇:pva,醇解度99.0-99.4mol%;粘度:12.0-16.0mpa.s;mw为44.05;阿拉丁试剂公司;正辛烷:c8h18纯度96%,mw为114.23;阿拉丁试剂公司;聚二甲基硅氧烷:pdms,184硅橡胶,美国道康宁sylgard;聚乙二醇:ho(ch2ch2o)nhaveragemn为6000,阿拉丁试剂公司;甲基蓝:分子式c37h27n3na2o9s3,mw为799.8麦克林;油红o:oilredo,二甲基苯基,分子式为c26h24n4o,mw为408.495,麦克林。sem采用扫描电镜su8220,日立,日本。接触角测量采用xg-cam接触角测量仪,contactanglemeter上海轩轶创析工业设备有限公司。致密度采用阿基米德排水法、恒温加热台、分析天平,ptx-fa电子分析天平;usa.hz&huazhi,美国康州hz电子有限公司。烧结实验采用马弗炉tsx1700型,西尼特(北京)电炉有限公司。抛光实验采用mp-2b研磨抛光机,莱州市蔚仪试验器械制造有限公司。实施例1本申请实施例提供了一种油水分离膜,其具体制备步骤如下:一、陶瓷粉体浆料的制备1、按照表1的添加量,在搅拌与超声的作用下,逐渐往去离子水中加入α-al2o3粉体,用盐酸调控ph最终配置固含量为53.7vol%,ph为5.36的氧化铝悬浮液。其中,乳化发泡后,去离子水为16.2vol%,α-al2o3粉体为27.6vol%。2、按球料比1:1的比例,添加氧化铝球磨球,其中球磨球φ10mm、φ5mm球磨球比例为1:1。用行星球磨机球磨一夜(转速300r/min)。3、球磨后去除球磨球,得到陶瓷粉体浆料。二、陶瓷粉体浆料的修饰处理1、将步骤一的陶瓷粉体浆料中添加去离子水稀释到固含量为46vol%;按每克氧化铝粉体添加0.04mmol的丙酸,并在搅拌下逐滴加入。搅拌实现对陶瓷粉末的修饰处理,得到第一反应物。三、乳化发泡处理1、将步骤二的第一反应物均分为6份,每份第一反应物添加聚乙烯醇,分别标记为:pva0wt%、pva1wt%、pva2wt%、pva3wt%、pva4wt%和pva10wt%,即pva0wt%为聚乙烯醇的添加量为0,pva1wt%为第一反应物中每克去离子水添加0.01g的聚乙烯醇,pva2wt%为第一反应物中每克去离子水添加0.02g的聚乙烯醇,pva3wt%为第一反应物中每克去离子水添加0.03g的聚乙烯醇,pva4wt%为第一反应物中每克去离子水添加0.04g的聚乙烯醇,pva10wt%为第一反应物中每克去离子水添加0.1g的聚乙烯醇;之后按照体积百分比分别添加70vol%的正辛烷进行搅拌发泡,搅拌时间为7分钟。直达正辛烷全部融进悬浮液中行程乳液。即是第一反应物的体积与添加的正辛烷体积比例为3:7,得到不同浓度的聚乙烯醇的第二反应物,分别记为pva0wt%、pva1wt%、pva2wt%、pva3wt%、pva4wt%和pva10wt%,其中,根据需要,在搅拌的情况下用naoh溶液调节乳液ph值为4.4,直到适合3d打印的粘度。四、成型处理1、取上一步骤中的每种第二反应物,借助3d打印成型设备实现宏观陶瓷素坯的成型和干燥处理,干燥为置于室温下自然干燥,得到陶瓷膜素坯,分别记为pva0wt%、pva1wt%、pva2wt%、pva3wt%、pva4wt%和pva10wt%。五、烧结1、取上一步骤的每种陶瓷膜素坯进行烧结处理,获得多孔陶瓷膜,分别记为pva0wt%、pva1wt%、pva2wt%、pva3wt%、pva4wt%和pva10wt%;烧结参数为:烧结温度800℃以下,以10℃/min的速度升温;温度在800-1550℃,以3.75℃/min的速度升温,到达1550℃后保温2小时,然后降温,温度在800-1550℃,以3.75℃/min的速度降温,之后随炉冷。六、油水分离陶瓷膜疏水处理1、取上一步骤中的每种多孔陶瓷膜用200目金刚磨盘进行抛光,制作片厚为0.8mm的过滤陶瓷膜样品,通过235℃的气相沉积(取每种过滤陶瓷膜样品置于培养皿1中,pdms液体胶水置于培养皿2中,用烧杯倒置盖住培养皿1、2,烧杯口用锡箔纸适当密封,之后整体置于马弗炉中缓慢加热升温到235℃,保温8小时,培养皿2中的pdms形成蒸汽,在过滤陶瓷膜样品的表面蒸发并沉积一层pdms分子层,气相沉积参数为以7.8℃/min升温至235℃,在235℃下保温8个小时,之后随炉冷),在样品表面镀上一层pdms(聚二甲基硅氧烷)分子,实现疏水处理,得到6种油水分离膜,分别记为pva0wt%、pva1wt%、pva2wt%、pva3wt%、pva4wt%和pva10wt%。表1测量制得的6种油水分离膜的平均孔径、接触角、油水分离效率和抗压强度的性能,结果如表2所示。表2平均孔径(μm)接触角(o)油水分离效率(%)抗压强度(mpa)pva0%137.5147.6499.87不稳定pva1%18.0152.8599.8651.136pva2%11.1152.5799.8745.872pva3%15.5152.4799.8744.752pva4%10.3152.7599.9136.767pva10%7.8153.3599.9125.608从表2可知,当添加浓度为0wt%的聚乙烯醇水溶液时,得到的油水分离膜抗压强度不稳定,且油水分离膜的平均孔径过大,空隙分布不均衡,油滴的接触角过小。随着聚乙烯醇的浓度增大,油水分离膜平均孔径越来越小。抗压强度都相对较高,水接触角均高于超疏水边界150°,油水分离效率均达到99.8%以上。对本实施例的油水分离膜(pva1%)进行扫描电镜检测,结果如图6-9所示,图6为本申请实施例的油水分离膜(pva1wt%)放大100倍的扫描电镜图,图7为本申请实施例的油水分离膜(pva1wt%)放大200倍的扫描电镜图,图8为本申请实施例的油水分离膜(pva1wt%)放大400倍的扫描电镜图,图9为本申请实施例的油水分离膜(pva1wt%)放大1200倍的扫描电镜图,图10为本申请实施例的油水分离膜(pva1wt%)放大10000倍的扫描电镜图,从图6-10可知,本申请实施例的油水分离膜(pva1wt%)具有有序排列的规则的三维网格多孔镂空结构,图10可知,在10000倍的扫面电镜图下可知,本申请的自组装方法堆垛出来的多孔结构,其孔壁上的晶粒能堆垛成精密排列的坚固孔壳,故而宏观层面才有了高强度的抗压性能,又是多孔结构,故而具有轻质高强性能。实施例2测定本申请实施例1的油水分离膜的超疏水和超亲油特性,请查阅图1-2,图1为本申请提供实施例1的油水分离膜的超疏水试验图,图2为本申请提供实施例1的油水分离膜的超亲油试验图,从图1-2可知,本申请实施例1的油水分离膜具备超疏水和超亲油特性。对比例1本申请对比例提供一种对照的油水分离膜,其具体制备步骤如实施例1的制备步骤类型,区别在于不进行实施例1步骤六的疏水处理,其余步骤与实施例1相同,制得对比例1的产品。实施例3请查阅图5,图5为本申请提供实施例1的油水分离膜的油水分离试验的示意图,其中,图5a为同时往实施例1的油水分离膜上滴加油滴1和水滴2,图5b为油滴1穿过实施例1的油水分离膜,水滴2不通过实施例1的油水分离膜,图5c为水滴2以水滴状停留在实施例1的油水分离膜的表面。按照图5的流程,还对对比例1的产品进行油水分离试验,实物结果如图3和图4所示,图3为本申请提供实施例1的油水分离膜进行油水分离试验后的实物图,图4为本申请提供对比例1的产品进行油水分离试验后的实物图,从图3-4可知,不进行实施例1步骤六的疏水处理得到的对比例1不具备油水分离的性能。本申请的说明书及上述附图中的术语“第一”、“第二”、“第三”、“第四”等(如果存在)是用于区别类似的对象,而不必用于描述特定的顺序或先后次序。应该理解这样使用的数据在适当情况下可以互换,以便这里描述的本申请的实施例例如能够以除了在这里图示或描述的那些以外的顺序实施。此外,术语“包括”和“具有”以及他们的任何变形,意图在于覆盖不排他的包含,例如,包含了一系列步骤或单元的过程、方法、系统、产品或设备不必限于清楚地列出的那些步骤或单元,而是可包括没有清楚地列出的或对于这些过程、方法、产品或设备固有的其它步骤或单元。以上所述仅是本发明的优选实施方式,应当指出,对于本
技术领域:
的普通技术人员来说,在不脱离本发明原理的前提下,还可以做出若干改进和润饰,这些改进和润饰也应视为本发明的保护范围。当前第1页12