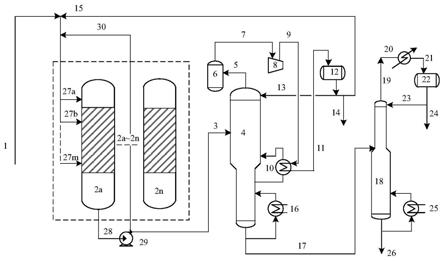
1.本发明涉及固体酸烷基化方法,更进一步说本发明涉及异构烷烃与烯烃的固体酸烷基化生产烷基化汽油的方法,属于石油化工领域。
背景技术:2.主要是异丁烷的异构烷烃与c3~c6烯烃在酸性催化剂的作用下发生烷基化反应是生产清洁、高辛烷值汽油组分的重要过程。该工艺得到的烷基化汽油蒸汽压低、敏感性低、抗爆性能好,不含芳烃、烯烃,硫含量也很低,是高辛烷值汽油的理想调和组分。
3.烷基化反应是一种酸催化反应。目前工业应用的烷基化生产工艺有硫酸法和氢氟酸法,它们是以硫酸或氢氟酸为催化剂由异构烷烃和烯烃合成烷基化油。由于硫酸和氢氟酸本身的腐蚀性、毒性以及工艺过程的废酸排放对环境的危害,使烷基化油生产企业面临的安全环保压力日益增加。
4.固体酸烷基化工艺的核心是性能优良的固体酸催化剂的开发。固体酸催化剂具有诸多优点,如稳定性好,不腐蚀设备,便于与产物分离,对环境污染少,运输过程相对安全性高等,是理想的催化剂形式。烷基化固体酸催化剂主要分为四类:金属卤化物、固体超强酸、负载型杂多酸和分子筛。尽管发展已经数十年,但是由于固体酸催化剂失活较快,使该工艺技术工业化的进程受到影响。
5.us5986158公开了一种烷基化方法,采用的催化剂包含氢化功能成分和固体酸成分,可烷基化物与烷基化剂反应形成烷基化物,并通过饱和烃和临氢条件进行催化剂间歇性再生,并在烷基化剂转化率大于80%的催化剂的活性期内进行再生,以获得高的烷基化收率和质量高的烷基化产物。沸石催化剂是多孔的催化材料,原料中的杂质会吸附在催化剂活性中心或原料中二烯烃聚合生成大分子堵塞孔道,引起催化剂失活。反应过程在固定床反应器中进行,催化剂的活性期仅有不到4~10h,催化剂必须反复再生,从其实施例可以看到,烷基化油的研究法辛烷值(ron)91.2,三甲基戊烷/二甲基己烷为2.9,c
5-c7、c8、c
9+
分别为30.4%,58.2%、11.4%。
6.ep1286769公开了一种新的烷基化催化剂及其用于烷基化烃的用途。
7.ep1392627公开了一种烃类的催化烷基化方法,其包括(i)在固体酸烷基化催化剂上将可烷基化的化合物与烷基化试剂反应生成烷基化物和(ii)在缓和再生条件下以及氢气和烃存在时再生所述催化剂,其中该烃包括至少一部分已形成的烷基化物。
8.尽管上述固体酸催化剂具有一定的催化性能,但仍然需要进一步提高这些催化剂的催化活性、选择性和稳定性,解决催化剂的再生问题,提高烷基化汽油质量。由于固体酸烷基化催化剂本身多孔的特点,在固体酸催化剂活性位上的烷基化反应需要原料从流体主体通过扩散到活性位,产物从活性位扩散到主体,烯烃在活性位的吸附能力更强,要求更高的外部烷烯比才能保证烷基化反应效果,这样产品分离的能耗较高。
技术实现要素:9.本发明的目的是提供一种提高催化剂性能和烷基化汽油质量以及降低烷基化装置能耗,减少烷基化装置的操作费用的固体酸烷基化方法。
10.本发明提供的固体酸烷基化方法,包括烷基化反应单元和烷基化反应产物分离单元组成,其特征在于:
11.所述的烷基化反应单元中,以一种固体酸催化剂催化烷基化反应,所述的固体酸催化剂具有:
12.(1)大孔比体积在0.30~0.40ml/g;
13.(2)大孔比体积与催化剂颗粒比长度之比为1.0~2.5ml/(g
·
mm);
14.(3)比表面积与颗粒长度之比为3.40~4.50m2/mm;且所述的大孔是指直径大于50nm的孔;
15.所述的烷基化反应产物分离单元中,分馏塔顶设置压缩机、中段设置再沸器,塔顶气相经压缩机压缩后温度和压力提高,进入中段再沸器与分馏塔中下部引出的温度较低的液相物流换热,塔顶气相物流在塔中段再沸器内液化。
16.本发明具有以下优点:
17.(1)采用本发明的固体酸催化剂,催化活性高,可进一步提高选择性,解决催化剂的再生问题,提高烷基化汽油质量。
18.(2)采用本发明的烷基化产品分离单元设置,通过气体压缩机将脱分馏塔顶气相增压,提高塔顶气相的温度和压力,使塔顶气相可以作为分馏塔中段再沸器的热源加以利用,塔顶气相液化时的相变热得到了充分利用,可以有效降低烷基化装置的总能耗,达到减少烷基化装置操作费用的目的。
附图说明
19.图1是一种固体酸烷基化方法的工艺流程示意图;
20.图2是另一种固体酸烷基化方法工艺流程示意图。
21.图3为固体酸催化剂样品的sem和能谱面扫描表征固体酸催化剂的形貌和元素分布情况。
22.附图中,1为烷基化原料,2a~2n为反应器,3为反应后物料,4、18为分馏塔,5分馏塔塔顶出口物料,6为稳定罐,7为分馏塔塔顶物料,8为压缩机,9为增压后物料,10、16、25为再沸器,11为冷凝后物料,12、22为塔顶回流罐,13、23为回流物料,14、24为分馏塔顶的轻烃馏分副产品,15为循环异丁烷,17为分馏塔的塔釜物料、26为烷基化产品,19为分馏塔顶物料,20为冷却器,21为塔顶冷凝冷却物料,27a~27m为分段进入反应器物料,28为反应器出口物料,29为循环泵,30为反应器出口循环物料。
具体实施方式
23.一种固体酸烷基化方法,包括烷基化反应单元和烷基化反应产物分离单元组成,其特征在于,
24.所述的烷基化反应单元中,以一种固体酸催化剂催化烷基化反应,所述的固体酸催化剂具有:
25.(1)大孔比体积在0.30~0.40ml/g;
26.(2)大孔比体积与催化剂颗粒比长度之比为1.0~2.5ml/(g
·
mm);
27.(3)比表面积与颗粒长度之比为3.40~4.50m2/mm;且所述的大孔是指直径大于50nm的孔;
28.所述的烷基化反应产物分离单元中,分馏塔顶设置压缩机、中段设置再沸器,塔顶气相经压缩机压缩后温度和压力提高,进入中段再沸器与分馏塔中下部引出的温度较低的液相物流换热,塔顶气相物流在塔中段再沸器内液化。
29.本发明中所述的烷基化反应单元,采用一种特殊物化性能的固体酸催化剂,它包括固体酸催化剂颗粒和具有加氢功能的再生助剂,可以实现烷基化反应和催化剂再生。
30.国际纯粹与应用化学联合会(iupac)规定,直径大于50nm的孔以“大孔”表示,并且这样的孔的孔中体积以“大孔体积”表示。大孔比体积是指单位质量催化剂颗粒的大孔体积。大孔比体积在0.30~0.40ml/g、优选为至少0.35ml/g。催化剂颗粒比长度是指催化剂颗粒固体部分的几何体积与几何表面之比。测定几何体积和几何表面的方法是本领域熟练技术人员熟知的,可按例如de2354558中的描述进行测定。需要注意的是,催化剂颗粒的比长度与催化剂颗粒的直径不同。例如,对于圆柱型催化剂颗粒,颗粒的直径比比长度大四至六倍(取决于颗粒的直径和长度),对于球形催化剂颗粒,颗粒的直径比比长度大六倍。该固体酸催化剂,颗粒比长度优选为0.15~0.4mm、更优选为0.18~0.36mm、最优选为0.20~0.32mm。大孔比体积与催化剂颗粒比长度之比为1.0~2.5ml/g
·
mm、优选为1.1~1.8ml/g
·
mm。总孔比体积是指单位质量催化剂颗粒的总孔体积,该固体酸催化剂,总孔比体积为至少0.40ml/g,优选为至少0.45ml/g。本发明以washbum方程为基础,通过压汞法测定大孔体积和总孔体积:d=(-4γcosθ)/p其中d为孔径,p为在测量期间施加的压力,γ为表面张力,取485达因/cm,θ为接触角,取130
°
。
31.催化剂颗粒可具有许多不同形状,包括球形、圆柱形、圆环形和对称或不对称多叶形(如蝶形、三叶形、四叶形)。催化剂颗粒的平均直径优选为至少1.0mm,其上限值优选在5.0mm。所述的催化剂颗粒的平均直径是指连接一个催化剂颗粒的横截面上任意两点的线段中最长的线段,可以采用例如游标卡尺等常规的测量手段进行测量。
32.该催化剂的固体酸组元优选为分子筛。所述的分子筛可以选自各种分子筛,例如可以是选自y型分子筛、β、mor、mcm-22和mcm-36中的一种或多种。所述的y型分子筛,其晶胞尺寸为2.430-2.470nm、优选的晶胞尺寸为2.440~2.460nm,二氧化硅与氧化铝摩尔比为5~15。如果需要,固体酸组元还可包括非沸石固体酸如杂多酸、二氧化硅-氧化铝,硫酸化氧化物如锆、钛或锡的硫酸化氧化物,锆、钼、钨、磷等的混合氧化物,氯化氧化铝或粘土等。
33.该催化剂中还包含基体材料。所述的基体材料,含量为2~98重量%、优选含量为10~70重量%。基于催化剂中存在的固体酸组元和基体材料的总重,优选包含2~98wt%固体酸组元和2~98wt%基体材料,进一步优选包含5~95wt%固体酸组元和5~95wt%基体材料,更优选包含15~85wt%固体酸组元和15~85wt%基体材料,可以是包含20~80wt%固体酸组元和20-80wt%基体材料,或可以是包含60~80wt%固体酸组元和20-40wt%基体材料。其中,所述的基体材料包含氧化铝,其前身物至少部分来自20~400nm颗粒度的铝溶胶。
34.该催化剂的比表面积不小于500m2/g。固体酸组元在基体材料中以微米级水平高
度分散,固体酸组元的比表面积不小于650m2/g,所说的基体材料比表面积不大于400m2/g。固体酸组元在基质材料中以微米级水平高度分散后,单位长度催化剂颗粒的比表面积应在较窄的范围波动,不会因固体酸组元与基体材料比表面差别较大而发生较大变化。该催化剂比表面积与颗粒长度之比为3.40~4.50m2/mm。所述的颗粒长度是随机挑选1g催化剂颗粒并测量该1g催化剂颗粒中每个颗粒的长度、再将每个颗粒的长度相加得到的。对于球形颗粒,颗粒长度为球的直径;对于条形颗粒(包括横截面为蝶形、三叶型和四叶型以及其他异形),颗粒长度为颗粒的平均条长;对于环形颗粒,颗粒长度为环形的外直径。
35.该催化剂的制备方法包括将包含固体酸组元的浆液与一种铝溶胶混合搅拌均匀、干燥,再与助挤剂、胶溶剂混合并成型的步骤,其中,所述的铝溶胶,其颗粒粒度在20~400nm。所述制备方法中,所述的铝溶胶,其颗粒粒度在20~400nm、优选在20~300nm。所述的助挤剂为本领域技术人员所熟知,常用的助挤剂选自田菁粉、草酸、酒石酸、柠檬酸等,优选田菁粉;所述的胶溶剂也为本领域技术人员所熟知,常用的胶溶剂选自硝酸、盐酸、乙酸、甲酸、柠檬酸和三氯乙酸等,优选硝酸。
36.在负载具有加氢功能的再生助剂后,催化剂在失活的情况下,在临氢和适宜的条件下可获得再生,实现催化剂反复再生、循环使用。因此,本发明烷基化反应单元采用的催化剂,由具有加氢功能的金属构成再生助剂组元。合适的加氢功能的金属主要为viii族金属、优选的为viii族贵金属。所述的viii族贵金属中更优选铑、钯、铂中的一种或多种。以金属计、基于烷基化催化剂的重量,具有加氢功能的金属含量为0.01wt%~10wt%、优选为0.1wt%~1wt%。典型的制备步骤包括通过含有加氢功能的金属的溶液浸渍颗粒和/或通过离子交换,将具有加氢功能的金属加入上述的固体酸催化剂;典型的制备步骤也可以是将具有加氢功能的金属的前身物加入到包括固体酸组元组分和颗粒度在20-400nm铝溶胶的液相混合物中,将所得的混合物干燥、成型。
37.本发明的烷基化反应单元,催化剂装填在反应器中。烷基化反应器可以是多种形式的反应器,例如流化床反应器、淤浆床反应器、环流反应器以及固定床反应器。该方法也可在单个和多个反应器中进行。
38.本发明中的烷基化反应,催化剂装填在反应器中特别是在固定床反应器中发生烷基化反应,反应可以是在温度5~200℃、优选20~150℃、更优选30℃~100℃,压力0.5~6.0mpa、优选1.0~3.0mpa,烷基化反应器的烯烃进料质量空速0.02~2.0h-1
、优选0.05~0.5h-1
,总进料中异构烷烃与烯烃的摩尔比5~50、优选7~30下进行。所述经预处理之后的原料分多段进入烷基化反应器,多个烷基化反应器在反应-再生模式下进行切换操作,反应器出口物料也可以有一部分物料进行内部循环回到反应器入口。在本发明所述的方法中,进入反应器的物料可分为多段进入反应器,分段多点进料,可以降低总的烷烯比,减少分馏塔的能耗。分段至少2段、最多20段,太多的分段会使反应器内部结构更为复杂,优选为3~12段。反应器出口一部分物料循环,能保持高的内部烷烯比,总烷烯比可维持不变,减少总分馏能耗。
39.本发明设置多个反应器进行反应-再生切换,反应器个数由2~10个,优选2~6个。本发明涉及的催化剂再生是在烷基化反应器中在线临氢原位再生,催化剂再生条件为:温度30~500℃、压力0.5~5.0mpa、时间0.5~15h;优选为温度150~300℃、压力0.5~3.0mpa、时间0.5~6h。
40.本发明方法所述的烷基化反应产物分离单元中,可以是一个分馏塔或两个分馏塔进行操作。
41.对于一个分馏塔,从烷基化反应单元来的烷基化反应产物从分馏塔中部进入,塔顶蒸汽出口连通气体压缩机入口增压后,气体压缩机出口物料温度和压力均提升,作为分馏塔的中段再沸器的热源,经分馏塔中段再沸器中发生相变与分馏塔中下部引出的温度较低的液相物流换热后回分馏塔,相变后的液相进入塔顶回流罐,一部分作为分馏塔回流,另一部分作为塔顶轻馏分,分馏塔塔底设置塔底再沸器,烷基化汽油从分馏塔塔底获得,其中正丁烷可从塔上段某一部位引出。
42.对于两个分馏塔,
43.(1)来自于烷基化反应单元的烷基化反应产物引入第一分馏塔中进行分馏分离,第一分馏塔塔顶气相物流经气体压缩机增压后,作为所述的第一分馏塔的中段再沸器的热源,经换热并冷凝后引入塔顶回流罐,一部分作为塔顶回流返回第一分馏塔;
44.(2)第一分馏塔的塔底液相物流引入第二分馏塔,所述的第二分馏塔塔顶引出的气相物流经冷凝冷却后,一部分作为塔顶回流返回分馏塔,另一部分得到轻馏分物流,所述的第二分馏塔塔底液相物流作为烷基化汽油产品。
45.更具体的,烷基化反应产物分离装置,包括依次连通的第一分馏塔和第二分馏塔,所述的第一分馏塔中部设置烷基化反应产物入口,所述的第一分馏塔塔顶蒸汽出口连通气体压缩机入口,气体压缩机出口经第一分馏塔中段再沸器、塔顶回流罐与第一分馏塔塔顶回流入口连通;所述的第一分馏塔中部液相馏分出口经所述的中段再沸器在所述的液相馏分出口之上的位置返回第一分馏塔中部,所述的第一分馏塔设置塔底再沸器,塔底物料出口连通所述的第二分馏塔中部的原料入口,所述的第二分馏塔塔顶设置塔顶冷凝器、塔顶回流罐,并在塔顶回流罐设置轻馏分出口,所述的第二分馏塔塔底设置塔底再沸器,并设置烷基化产品出口。
46.优选的,所述的第一分馏塔顶部回流罐还设置轻馏分出口。优选地,所述的第一分馏塔中部液相馏分出口设置于所述的第一分馏塔由上至下20~98%的位置,优选40~80%的位置。优选的,所述的第一分馏塔中部液相馏分出口设置于所述的第一分馏塔的变径段,上部扩径段与下部分馏塔的高度比为0.25~49:1,优选0.66~4:1,直径比为1~6:1。优选2~4:1。优选地,所述的第一分馏塔为脱异丁烷塔,所述的第二分馏塔为脱正丁烷塔。
47.在本发明的方法中,所述的固体酸烷基化反应单元的烷基化反应产物出口与所述的烷基化反应产物分离单元的烷基化反应产物入口连通。
48.在本发明的方法中,所述的脱异丁烷塔塔顶需设置增压设备对异丁烷馏分增压,增压设备压缩比范围为1.3~4.5:1,出口绝对压力为1.0mpa~3.2mpa。
49.本发明方法中的分离采用的是与常规分离方法不同的分离方法。常规分离方法是将分馏塔顶的气相物流直接进行冷凝冷却,而烷基化反应需要采用较高的外部烷烯比,使得循环异丁烷的流量为烷基化原料流量的数倍,塔顶气相物流冷凝过程的相变热十分可观,但由于塔顶物流的温位较低,不能作为热源加以利用,分离过程所需的热量全部由分馏塔底再沸器提供,使得分馏塔底再沸器的热负荷很大,能耗较高。本发明采用的分离方法是将分馏塔的塔顶气相物流用气体压缩机增压,增压后的塔顶气相物流的温度提高,可以作为分馏塔中段再沸器的热源,塔顶气相物流在中段再沸器内液化,塔顶物流的相变热得到
了充分利用,提供了从烷基化反应产物中分离异丁烷馏分所需的大部分热量,少量分离所需的热量由分馏塔底再沸器提供,与常规分离方法相比,塔底再沸器的热负荷大大降低,而塔顶气相物流的气体压缩机所增加的电耗远小于塔底再沸器节约的能耗,因此,采用本发明中的分离方法使从烷基化反应产物中分离异丁烷的能耗有效降低。
50.气体压缩机是分离中的重要设备,通过气体压缩机给塔顶气相做功,提升了塔顶气相的压力和温度,为使塔顶气相经过压缩机增压后能够满足作为分馏塔中段再沸热源的要求。
51.由于烷基化反应产物中的第二分馏馏分含量较小,主要脱除原料中未参与反应的正丁烷,所述的脱正丁烷塔采用常规的分离方法将烷基化反应产物中的正丁烷与烷基化汽油进行分离,塔顶得到副产物正丁烷馏分,塔底得到烷基化汽油产品。
52.本发明中的烷基化反应产物分离单元,其分馏塔顶设置压缩机、中段设置再沸器,塔顶气相经压缩机压缩后温度和压力提高,进入中段再沸器与分馏塔中下部引出的温度较低的液相物流换热,塔顶气相物流在塔中段再沸器内液化,塔顶气相物流的相变热得到充分利用,大幅度降低烷基化装置的能耗水平。
53.下面结合附图对本发明的方法予以进一步的说明,附图中只标示出了主要设备及管线,展示的是本发明的方法的主要特点,但并不因此而限制本发明。
54.图1图示了本发明的一种实施方案。
55.在图1中,烷基化原料1与分馏塔4塔顶的循环异丁烷15混合后反应器物料27a~27m分段进入反应器2a~2n中(根据具体要求分段个数可为a~m、m一般小于20,反应器的个数可为a~n,n一般小于10),反应器2a~2n中装填有发明的催化剂。在烷基化反应条件下发生反应,反应后物料3引入分馏塔4进行分馏分离,分馏塔4的塔顶气相物料5进入气体压缩机入口稳定罐6,稳压后的分馏塔塔顶物料7进入压缩机8,增压后物料9的温度和压力提高,引入分馏塔作为中段再沸器10热源,与从分馏塔4中下部引出的温度较低的液相物流换热,塔顶气相物流在分馏塔中段再沸器10内液化,塔顶气相物流的相变热得到充分利用,冷凝后物料11引入分馏塔顶回流罐12,一部分作为回流物料13引入分馏塔4的顶部,另一部分作为轻烃馏分副产品14外送,其余大部分作为循环异丁烷15返回烷基化反应单元。分馏塔4分离过程不足的热量由分馏塔底再沸器16提供,分馏塔4底部的分馏塔的塔釜物料17引入分馏塔18,分馏塔18采用常规的分离方法,分馏塔顶物料19的气相物流经由冷却器20冷凝冷却后塔顶冷凝冷却物料21引入分馏塔18的塔顶回流罐22,一部分作为回流物料23引入分馏塔18的顶部,另一部分得到轻烃馏分副产品24,塔底液相物流为烷基化产品26,分馏塔18分离所需的热量由分馏塔底再沸器25提供。
56.图2图示了本发明的另一种实施方案。
57.在图2中,与图1所不同的是反应器出口物料28的一部分经循环泵29将反应器出口循环物料30循环回到反应器入口,另一部分反应后物料3进入分馏塔4中进行产品分离。
58.通过在本发明所述的方法,能够提高固体酸烷基化催化剂性能和烷基化汽油质量以及降低烷基化装置能耗,减少烷基化装置的操作费用。
59.实施例中,固体酸催化剂颗粒的物化参数表征方法如下:
60.大孔体积和总孔体积的测定以washbum方程为基础,通过压汞法测得。d=(-4γcosθ)/p其中d为孔径,p为在测量期间施加的压力,γ为表面张力,取485达因/cm,θ为接触
角,取130
°
。
61.催化剂颗粒的平均直径的测量:采用游标卡尺测量颗粒截面的最长边距离即为颗粒的平均直径。
62.比表面积的测量:催化剂比表面积采用氮气低温吸附法测量,用bet公式计算比表面积。
63.颗粒长度的测量:是随机挑选1g催化剂颗粒并测量该1g催化剂颗粒中每个颗粒的长度、再将每个颗粒的长度相加得到的;每个颗粒的长度采用游标卡尺测量。
64.烷基化反应性能反应评价分析方法如下:
65.称取石英砂(20~40目)装入管式反应器下端非恒温段,压实后,装入三层镍网,将上述100g催化剂装填、压实,装入三层镍网,将反应器上层非恒温段同样装入20~40目的石英砂,压实。最后,先后装填适量的石英棉和镍网。
66.将反应器接入管线,检测管路的密闭性和通畅性以后,用氮气置换装置中的空气三次以上,然后用氢气置换三次。设置氢气流量为300ml/min背压3.0mpa,打开加热源,设置升温速度1℃/min,升温至200℃并保持1h;然后以1℃/min,升温至450℃并保持3h。预处理完后,催化剂降温至实施例中的反应温度,氮气置换装置中的氢气置换三次以上,置换完后以一定的进料流量进料在实施例所述的反应条件下反应。
67.产物分布通过装有al2o3和pona柱及高压进样器的安捷伦7890a气相色谱获得。在背压阀后,尾气放空前取样,每两个小时取一次样,在进样口样品被分成两部分,0.01~0.1分钟的低沸点混合物(c4以下烃类)进入al2o3柱,0.2~9.5分钟的高沸点物质(c5以上烃类)被载气吹入pona柱中。得到的谱图通过石油化工科学研究院开发的汽油分析软件识别并计算各组分的百分含量。
68.实施例或对比例中用到的原料:
69.1、y型分子筛(中国石化催化剂有限公司),比表面积680m2/g,孔体积0.36ml/g,晶胞常数2.457nm,m(sio2/al2o3)=9,编号为ya。
70.2、几种纳米铝溶胶(中国石化催化剂分公司):
71.编号al1:氧化铝浓度为5%,平均粒度20nm。
72.编号al2:氧化铝浓度为15%,平均粒度150nm。
73.编号al3:氧化铝浓度为20%,平均粒度300nm。
74.3、al2o3粘结剂粉:比表面积280m2/g,孔体积0.98ml/g。
75.实施例1
76.本实施例说明本发明采用的烷基化催化剂。
77.将编号为ya的y型分子筛加水打浆成固含量为200kg/m3的分子筛浆液,按照ya和al1重量干基百分比为60:40的比例加入编号为al1的铝溶胶,搅拌4h,使其混合均匀,干燥后的混粉再添加3%重量百分比(以分子筛与铝溶胶600℃焙烧后的干基重量为准)的硝酸和田菁粉,并通过添加水保证水粉比为0.8,混捏均匀后进行挤条,所得湿条经干燥、焙烧后即得成型固体酸催化剂样品,命名为60a1,性质见表1。
78.将实施例1的固体酸催化剂样品60a1在真空下分别加入含加氢金属pt(h2ptcl6·
6h2o为前驱体)、液固比2:1的浸渍液,加完后常压浸渍不超过10小时,浸渍结束,在不高于80℃的情况下抽真空,蒸发催化剂中的水分,蒸发至催化剂重量为固体酸催化剂母体的1.2
~1.5倍,蒸发完取出催化剂干燥、焙烧。
79.所得烷基化催化剂编号为c1,pt含量为0.25wt%。
80.实施例2
81.本实施例说明本发明采用的烷基化催化剂。
82.将编号为ya的y型分子筛加水打浆成固含量为200kg/m3的分子筛浆液,按照ya和al2重量干基百分比为80:20的比例加入编号为al2的铝溶胶,搅拌4h,使其混合均匀,干燥后的混粉再添加3%重量百分比(以分子筛与铝溶胶600℃焙烧后的干基重量为准)的硝酸和田菁粉,并通过添加水保证水粉比为0.8,混捏均匀后进行挤条,所得湿条经干燥、焙烧后即得成型固体酸催化剂样品,命名为80a2,性质见表1。
83.将实施例2的固体酸催化剂样品80a2在真空下分别加入含加氢金属pt(h2ptcl6·
6h2o为前驱体)、液固比2:1的浸渍液,加完后常压浸渍不超过10小时,浸渍结束,在不高于80℃的情况下抽真空,蒸发催化剂中的水分,蒸发至催化剂重量为固体酸催化剂母体的1.2~1.5倍,蒸发完取出催化剂干燥、焙烧。
84.所得烷基化催化剂编号为c2,pt含量为0.25wt%。
85.实施例3
86.本实施例说明本发明采用的烷基化催化剂。
87.将编号为ya的y型分子筛加水打浆成固含量为200kg/m3的分子筛浆液,按照ya和al3重量干基百分比为95:5的比例加入编号为al3的铝溶胶,搅拌4h,使其混合均匀,干燥后的混粉再添加3%重量百分比(以分子筛与铝溶胶600℃焙烧后的干基重量为准)的硝酸和田菁粉,并通过添加水保证水粉比为0.8,混捏均匀后进行挤条,所得湿条经干燥、焙烧后即得成型固体酸催化剂样品,命名为95a3,性质见表1。
88.将实施例3的固体酸催化剂样品95a3在真空下分别加入含加氢金属pt(h2ptcl6·
6h2o为前驱体)、液固比2:1的浸渍液,加完后常压浸渍不超过10小时,浸渍结束,在不高于80℃的情况下抽真空,蒸发催化剂中的水分,蒸发至催化剂重量为固体酸催化剂母体的1.2~1.5倍,蒸发完取出催化剂干燥、焙烧。
89.所得烷基化催化剂编号为c3,pt含量为0.25wt%。
90.对比例1-3
91.对比例1-3说明以y型分子筛和al2o3粘结剂粉固相混合成型的过程和得到的对比固体酸催化剂样品。
92.将编号为ya的y型分子筛和al2o3粘结剂粉按重量干基百分比分别为60:40、80:20和95:5比例混合,添加3%重量百分比(以分子筛与al2o3粘结剂粉600℃焙烧后的干基重量为准)的硝酸和田菁粉,并通过添加水保证最终混合粉的水粉比为0.8,混捏均匀后进行挤条,所得湿条经干燥、焙烧后即得成型的对比固体酸催化剂样品。
93.对比固体酸催化剂样品分别命名为60a、80a和95a,性质见表1。
94.将对比固体酸催化剂60a、80a和95a负载加氢金属pt得到(pt含量为0.25wt%)的烷基化催化剂,其编号分别为db1、db2和db3。
95.表1
[0096][0097]
对编号为80a2的固体酸催化剂样品和编号为80a的对比固体酸催化剂样品采用sem和能谱面扫描表征,形貌和元素分布结果见图3。从图3可以看出,编号为80a2固体酸催化剂样品,其硅铝元素分布更均匀,说明液相混合下y型分子筛与al2o3颗粒大小分布均一,酸性位分散性好。
[0098]
实施例4-5
[0099]
实施例4-5说明本发明采用的烷基化催化剂。
[0100]
在实施例2的固体酸催化剂样品80a2的基础上负载加氢金属得到pt含量分别为0.1wt%和0.7wt%的烷基化催化剂样品编号为c4-c5。
[0101]
实施例6
[0102]
本实施例说明本发明采用的烷基化催化剂。
[0103]
在实施例2的固体酸催化剂80a2的基础上负载加氢金属得到烷基化催化剂,编号c6,区别在于加氢金属为pd(硝酸钯为前驱体),pd含量0.5wt%。
[0104]
实施例7
[0105]
本实施例说明本发明方法,流程见图1。
[0106]
作为烷基化反应的碳四原料的主要组分重量组成为异丁烷:47.49%,正丁烷:14.62%,丁烯:37.56%,其余为杂质。
[0107]
反应器为固定床反应器,反应器个数n=2,分段数m=5。装填的固体酸烷基化催化剂为烷基化催化剂样品c2。
[0108]
烷基化反应条件:反应温度70℃、压力3.0mpa、总进料中异构烷烃与烯烃的摩尔比为25,烯烃进料质量空速为0.15h-1
,催化剂为实施例2制备的烷基化催化剂c2。其中,周期寿
命定义为丁烯转化率小于99%时催化剂单程运行时间;采用气相色谱分析检测反应器出口烯烃含量,收集的烷基化产品烷基化汽油进行辛烷值测定。
[0109]
反应后物料经过两个分馏塔进行分离得到烷基化产物,分馏流程见图1。分馏塔4的操作条件为塔顶温度53℃,塔釜温度130℃,塔顶操作压力0.7mpa;分馏塔18操作条件为塔顶温度53℃,塔釜温度158℃,塔顶操作压力0.5mpa。压缩机压缩比2.3:1,压缩机出口压力1.7mpa。
[0110]
烷基化反应结果如表2所示。
[0111]
烷基化反应产物分离过程的物料平衡数据如表3所示。
[0112]
采用本实施例的烷基化反应产物分离过程的能耗如表4所示。
[0113]
实施例8
[0114]
同实施例7,区别在于流程为图2。
[0115]
烷基化反应结果如表2所示。
[0116]
烷基化反应产物分离过程的物料平衡数据如表3所示。
[0117]
采用本实施例的烷基化反应产物分离过程的能耗如表4所示。
[0118]
实施例9
[0119]
同实施例7,区别在于采用实施例1的催化剂c1。
[0120]
烷基化反应结果如表2所示。
[0121]
实施例10
[0122]
同实施例7,区别在于采用实施例3的催化剂c3。
[0123]
烷基化反应结果如表2所示。
[0124]
实施例11
[0125]
同实施例7,区别在于采用实施例4的催化剂c4。
[0126]
烷基化反应结果如表2所示。
[0127]
实施例12
[0128]
同实施例7,区别在于采用实施例5的催化剂c5。
[0129]
烷基化反应结果如表2所示。
[0130]
实施例13
[0131]
同实施例7,区别在于采用实施例6的催化剂c6。
[0132]
烷基化反应结果如表2所示。
[0133]
对比例4-6
[0134]
对比例4-6说明采用对比烷基化催化剂的情况。
[0135]
同实施例7的原料、预处理步骤和烷基化反应条件和产物分离步骤,区别在于采用的烷基化催化剂为对比例1、2、3制备的对比烷基化催化剂db1、db2、db3。
[0136]
烷基化反应结果如表2所示。
[0137]
表2
[0138][0139]
对比例7
[0140]
本对比例与实施例7的区别在于仅在于产物分离步骤不同。即:分馏塔塔顶的气相物流经冷凝冷却后,进入回流罐,塔顶气相物流相变过程的热量不加以回收和利用,分离过程所需的热量全部由塔底再沸器提供。烷基化反应产物来自于固体酸烷基化技术的烷基化反应单元。
[0141]
本对比例的烷基化反应产物分离过程的物料平衡数据如表3所示。
[0142]
采用本对比例的烷基化反应产物分离过程的能耗如表4所示。
[0143]
对比例8
[0144]
本对比例与实施例8的区别在于仅在于产物分离步骤。即:分馏塔塔顶的气相物流经冷凝冷却后,进入回流罐,分离过程所需的热量全部由塔底再沸器提供。烷基化反应产物来自于固体酸烷基化技术的烷基化反应单元。
[0145]
本对比例的烷基化反应产物分离过程的物料平衡数据如表3所示。
[0146]
采用本对比例的烷基化反应产物分离过程的能耗如表4所示。
[0147]
表3
[0148] 实施例7,8对比例7,8烷基化反应产物,kg/h288.5288.5循环异丁烷,kg/h263.7263.7异丁烷馏分,kg/h2.02.0
正丁烷馏分,kg/h3.33.3烷基化汽油,kg/h19.519.5
[0149]
表4
[0150] 实施例7对比例7实施例8对比例8电用量折算能耗,mj/t烷油2239.6568.12478.2702.2蒸汽用量折算能耗,mj/t烷油4460.17674.71362.24798.7循环水用量折算能耗,mj/t烷油525.7987.3149.6353.3能耗合计,mj/t烷油7225.49230.13990.15854.2
[0151]
由表4可知:实施例7能耗合计小于对比例7约21.7%,实施例8能耗合计小于对比例8约31.8%,说明采用本发明所述包括产物分离步骤在内的方法可大幅度减少烷基化装置的能耗水平。