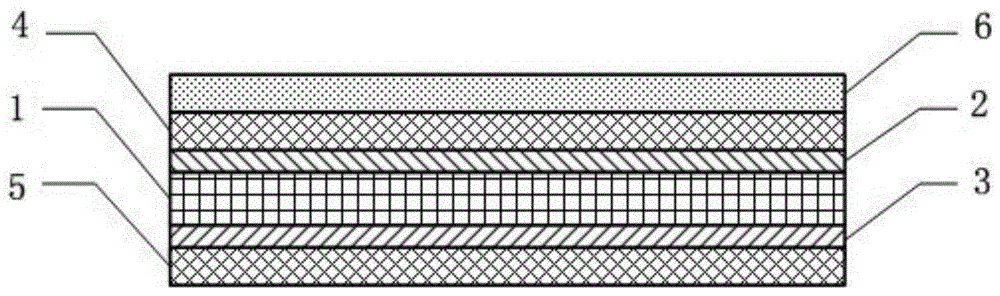
本申请涉及环保除尘过滤材料
技术领域:
,尤其涉及一种高过滤精度的膨化珍珠岩纤维复合滤料及其制备方法。
背景技术:
:在一些特殊工况产生的高温烟尘(240℃以上),其主要成分是烟尘、so2、nox、co、氟化物以及重金属等有毒或腐蚀性物质。此类工况对于除尘的过滤材料提出了很高的要求,包括需要具有高强度低延伸性、耐高温、耐酸腐蚀等特性。在有机合成纤维过滤材料中,聚四氟乙烯(ptfe)材料具有耐高低温、耐腐蚀、耐气候、高润滑不粘附等优异特征,近年来在环保除尘领域得到了大量的应用。与此同时,用于高温气体过滤的聚四氟乙烯滤料由于高成本限制了其工业上的广泛应用。而无机纤维作为高温烟气过滤材料,较ptfe等合成纤维具有很大的优势。无机纤维材料包括玻璃纤维、玄武岩纤维、珍珠岩纤维等,是一种性价比很高的过滤材料。无机纤维材料具有耐高温、耐化学腐蚀、耐水解、强度高、伸长小等特性,是目前用于高温腐蚀性气体和烟尘过滤、腐蚀性液体过滤的优质材料。其中,珍珠岩纤维是一种近年来比较新型的高性能无机纤维,具有高强低伸、耐温耐腐、高性价比等特点,尤其是耐酸性能突出。同比其它材料相比,上述两大类材料作为工业烟尘过滤材料具有突出的综合优势,但是分别存在成本高、部分性能指标缺陷等问题,严重影响了两种材料在工业环保除尘领域的推广应用。而如果将聚四氟乙烯材料与珍珠岩纤维等无机材料简单叠加形成复合滤料,其过滤性能难以保证,并且使用寿命短,不适于耐酸腐蚀等特殊工况除尘的长期应用。技术实现要素:有鉴于此,本申请提供一种膨化珍珠岩纤维复合滤料及其制备方法,所述的膨化珍珠岩纤维复合滤料结构稳定、强力高,耐酸腐蚀,并且过滤性能好,使用寿命长,可满足特殊工况的使用要求。本申请提供一种膨化珍珠岩纤维复合滤料,其包括膨化珍珠岩纤维基层;所述膨化珍珠岩纤维基层的一面复合有依次接触的正面聚四氟乙烯结合层、正面聚四氟乙烯发泡涂层和膨化聚四氟乙烯微孔膜层,所述膨化珍珠岩纤维基层的另一面复合有依次接触的反面聚四氟乙烯结合层、反面聚四氟乙烯发泡涂层;所述正面聚四氟乙烯发泡涂层的气泡孔径小于反面聚四氟乙烯发泡涂层的气泡孔径。优选地,所述膨化珍珠岩纤维基层由5~7微米细旦珍珠岩纤维纱经膨化加工、织造而成。优选地,所述正面聚四氟乙烯发泡涂层的气泡直径小于等于30微米。优选地,所述正面聚四氟乙烯发泡涂层的厚度大于反面聚四氟乙烯发泡涂层的厚度。优选地,所述正面聚四氟乙烯发泡涂层的厚度为20~200微米。优选地,所述膨化聚四氟乙烯微孔膜层的厚度为5~10微米。优选地,所述正面聚四氟乙烯发泡涂层和反面聚四氟乙烯发泡涂层独立地包含直径为0.1~3微米的石墨烯。其中,石墨烯是混合在涂层剂加入涂层中的颗粒物质,可通过均匀搅拌等方式实现均匀分布。优选地,所述膨化珍珠岩纤维复合滤料为采用ptfe缝纫线缝制成的袋状。本申请提供一种膨化珍珠岩纤维复合滤料的制备方法,包括以下步骤:s1、将珍珠岩纤维膨体布用聚四氟乙烯乳液浸渍处理,然后依次干燥、烧结,使珍珠岩纤维膨体布两面分别形成聚四氟乙烯结合层;s2、将形成聚四氟乙烯结合层的珍珠纤维膨体布用第一涂层剂进行正面的发泡涂层处理,所述第一涂层剂包含聚四氟乙烯和第一发泡剂,在该面聚四氟乙烯结合层上形成正面聚四氟乙烯发泡涂层;并且,采用第二涂层剂进行反面的发泡涂层处理,所述第二涂层剂包含聚四氟乙烯和第二发泡剂,所述第一涂层剂和第二涂层剂独立可选地包含石墨烯,在该面聚四氟乙烯结合层上形成反面聚四氟乙烯发泡涂层;所述正面聚四氟乙烯发泡涂层的气泡孔径小于反面聚四氟乙烯发泡涂层的气泡孔径;s3、将膨化聚四氟乙烯微孔薄膜通过热压覆膜的方式复合于所述正面聚乙烯发泡涂层上,制成膨化珍珠岩纤维复合滤料。优选地,步骤s3中,所述热压覆膜的温度为370~415℃,所述热压覆膜的速度为2-7m/min。与现有技术相比,本申请提供的膨化珍珠岩纤维复合滤料主要由六层构成,其中以膨化珍珠岩纤维基材为基础,从滤料正面依次为:膨化聚四氟乙烯微孔膜层、正面聚四氟乙烯发泡涂层、正面聚四氟乙烯结合层、膨化珍珠岩纤维基层、反面聚四氟乙烯结合层、反面聚四氟乙烯发泡涂层;并且,所述正面聚四氟乙烯发泡涂层的气泡孔径小于反面聚四氟乙烯发泡涂层的气泡孔径。本申请采用膨化珍珠岩纤维基材,耐酸腐蚀优异。在本申请中,聚四氟乙烯结合层不仅对滤料珍珠岩纤维全面渗透保护,增强耐磨性和耐折性,而且可以起到桥接的作用,将膨化珍珠岩纤维基层和聚四氟乙烯发泡涂层牢固结合在一起。本申请采用双面发泡涂层技术,滤料正面制成孔径较小的聚四氟乙烯发泡涂层,实现深层过滤向表面过滤的转化;而反面聚四氟乙烯发泡涂层的孔径略大,目的是保证透气性和耐磨性,使极细的粉尘易于通过,防止滤料内部积尘而出现系统压差升高的现象。本申请滤料正面的膨化聚四氟乙烯微孔膜层具有透气性,对滤料内部也有保护作用。运行中,即使薄膜出现破碎,具有双面涂层的滤料仍然可以长时间地保持高效过滤,保证除尘系统正常运行。同时,本申请膨化珍珠岩复合滤料可以在280℃的高温环境下稳定工作,具有良好的耐磨折性、耐酸腐蚀性及高强低伸性能。该滤料的耐酸腐蚀性比常规滤料提高3倍以上,耐磨性能提高50%以上。本申请的膨化珍珠岩纤维复合滤料结构稳定,过滤精度高、耐高温、耐酸腐蚀性好,可用于各种复杂工作环境使用,即使薄膜破损也可以实现高效过滤功能。该膨化珍珠岩纤维复合滤料还可经过裁切、缝制等工序,制成环保用高效膨化珍珠岩纤维复合滤袋。进一步地,本申请加入的石墨烯可改善涂层柔韧性,耐折性能提高10-30%;均匀涂覆的石墨烯具有良好的导电性能,可以在滤料上形成一张导电网而具有抗静电性能。附图说明图1为本申请实施例提供的膨化珍珠岩纤维复合滤料的结构示意图;图2为本申请一些实施例制备膨化珍珠岩纤维复合滤料的工艺流程图。具体实施方式下面对本发明实施例中的技术方案进行清楚、完整地描述,显然,所描述的实施例仅仅是本发明一部分实施例,而不是全部的实施例。基于本发明中的实施例,本领域普通技术人员在没有做出创造性劳动前提下所获得的所有其他实施例,都属于本发明保护的范围。本申请提供了一种膨化珍珠岩纤维复合滤料,其包括膨化珍珠岩纤维基层;所述膨化珍珠岩纤维基层的一面复合有依次接触的正面聚四氟乙烯结合层、正面聚四氟乙烯发泡涂层和膨化聚四氟乙烯微孔膜层,所述膨化珍珠岩纤维基层的另一面复合有依次接触的反面聚四氟乙烯结合层、反面聚四氟乙烯发泡涂层;所述正面聚四氟乙烯发泡涂层的气泡孔径小于反面聚四氟乙烯发泡涂层的气泡孔径。针对目前过滤材料的不足,本申请提供一种高强力、耐高温、耐酸腐蚀、过滤性能好、使用寿命长的膨化珍珠岩纤维复合滤料,将珍珠岩纤维与聚四氟乙烯材料的优点有效结合,满足特殊工况的使用要求。参见图1,图1为本申请实施例提供的膨化珍珠岩纤维复合滤料的结构示意图;其中,1为膨化珍珠岩纤维基层,2为正面聚四氟乙烯结合层,3为反面聚四氟乙烯结合层,4为正面聚四氟乙烯发泡涂层,5为反面聚四氟乙烯发泡涂层,6为膨化聚四氟乙烯微孔膜层。本申请实施例所述膨化珍珠岩纤维复合滤料包括膨化珍珠岩纤维基层1,其主要优选由5~7μm细旦珍珠岩纤维纱线经过膨化加工、织造而成的膨体布,具有珍珠岩纤维过滤材料的优良性能,尤其耐酸性能突出。其中,本申请所述的珍珠岩纤维具有高强低伸、耐温、耐酸腐蚀、高性价比等特点。本申请优选采用细旦珍珠岩纤维纱制成膨化珍珠岩纤维基层,单丝直径为5~7μm,优选为6μm。在本申请的实施例中,经过纺纱-膨化加工-整经-织造等常规工序,按照织布工艺,采用织布机制成珍珠岩纤维膨体布,其为膨化珍珠岩纤维基层的基材。经过所述膨化加工,可得到相对原纱表现体积较大、更蓬松的膨体纱;本申请实施例制作而成的珍珠岩纤维膨体布的单位面积重量可为300~900g/m2,优选为450~750g/m2,例如450、500、550、600g/m2、650g/m2、700g/m2、750g/m2等。此外,织造而成的珍珠岩纤维膨体布的织物组织结构一般为双斜纹组织,其正反面参数一样,厚度范围1.6-2.2mm。本申请实施例以膨化珍珠岩纤维基层1为基础,在其两个表面分别复合有正面聚四氟乙烯结合层2、反面聚四氟乙烯结合层3。接着,本申请实施例分别对应地复合有正面聚四氟乙烯发泡涂层4、反面聚四氟乙烯发泡涂层5。其中,所述正面聚氯乙烯结合层设置于膨化珍珠岩纤维基层的正面与正面聚氯乙烯发泡涂层之间;所述的正面通常为迎尘面。所述的聚氯乙烯结合层主要由聚氯乙烯乳液浸渍或涂覆滤料基层表面而形成,优选经过浸渍处理形成聚氯乙烯浸渍层。在本申请的实施例中,所述的聚氯乙烯浸渍层的作用一是在纤维表面形成保护层,聚四氟乙烯乳液充分填充到了滤料基层的内部结构中,以聚四氟乙烯乳液为浸渍处理液,对滤料基层全面渗透保护,在纤维表面形成致密的保护膜,可增加滤料的耐磨性和耐折性。所述聚氯乙烯浸渍层的作用二是起到一个桥接的作用,将滤料基层和聚四氟乙烯发泡涂层牢固结合在一起。所述反面聚氯乙烯结合层设置于膨化珍珠岩纤维基层与反面聚氯乙烯发泡涂层之间,也是优选通过聚氯乙烯乳液浸渍处理形成的。具体地,所述聚四氟乙烯乳液的固含量一般为60%,可包括硅烷偶联剂等助剂组成;浸渍处理后增重范围5-15%。本申请采用双面涂层工艺技术,其中,滤料正面制成聚四氟乙烯发泡涂层,孔隙率高、孔径小,实现深层过滤向表面过滤的转化。而滤料的反面聚四氟乙烯发泡涂层的孔隙率较正面略低、孔径略大,目的是保证滤料的透气性和耐磨性等,使极细的粉尘易于通过,防止滤料内部积尘而出现系统压差升高的现象。运行中,本申请所述具有双面涂层的滤料可以长时间地保持高效过滤,保证除尘系统正常运行。单面的涂层整理是将聚四氟乙烯材料均匀地涂布于滤料表层的工艺过程,采用涂层整理技术使滤料表面形成一层透气疏水的涂膜,可改善滤料理化性能,使产品性能满足特殊工况的使用要求。例如,当高温粉尘撞击滤料时,正面涂层可以起到缓冲和保护滤料的作用。在本申请中,所述正面聚四氟乙烯发泡涂层为滤料的迎尘次表层,主要是由含有聚四氟乙烯和发泡剂的涂层剂经过涂层整理(或称发泡涂层处理)形成的发泡涂膜。所述反面聚四氟乙烯发泡涂层为滤料的净气表层,也是聚四氟乙烯的发泡涂膜结构。并且,本申请所述正面聚四氟乙烯发泡涂层的气泡孔径小于反面聚四氟乙烯发泡涂层的气泡孔径;所述正面聚四氟乙烯发泡涂层的厚度大于反面聚四氟乙烯发泡涂层的厚度。具体地,可控制所述正面聚四氟乙烯发泡涂层的气泡直径≤30μm,例如1~20μm。此处,所述的气泡直径范围一般为最小直径到最大直径之间。所述正面聚四氟乙烯发泡涂层的厚度可控制在20μm~200μm,优选50~180μm。所述的正面涂层较厚、孔径较小,可防止粉尘和气流冲刷,提高过滤精度。作为优选,所述反面聚四氟乙烯发泡涂层的厚度为50μm-300μm,例如100~150μm。所述的反面涂层较薄、孔径较大,主要能够保护滤料本体不受侵蚀,保证干净气流顺利通过,防止滤料堵塞。本申请一些实施例所述的滤料包括浸渍层和双面涂层,耐酸腐蚀比常规滤料提高3倍以上;抗结露性突出。其中,反面主要是保护滤料基材,提高耐腐蚀性和耐磨折性,同时反面的孔径与滤料浸渍处理后的孔径一致,避免滤料堵塞造成压差升高,甚至滤料失效。本申请实施例所述的涂层剂可采用聚四氟乙烯乳液与发泡剂及一些添加剂混合制成;通过发泡剂的加入和用量的调整,可控制气泡的数量和气泡的尺寸。在本申请的优选实施例中,所述涂层剂包含石墨烯;石墨烯的加入可以提升制品的物理、化学性能。即,所述正面聚四氟乙烯发泡涂层和反面聚四氟乙烯发泡涂层优选独立地包含石墨烯,其直径为0.1~3微米。本申请实施例经过涂层剂双面涂层后,滤料结构更牢固,提高滤料的强力,滤料耐磨性能提高50%以上。并且,加入的石墨烯可改善涂层柔韧性等,耐折性能提高10-30%。此外,均匀涂覆的石墨烯具有良好的导电性能,可以在滤料上形成一张导电网而具有抗静电性能。在本申请的实施例中,所述膨化珍珠岩纤维复合滤料包括膨化聚四氟乙烯微孔膜层6,其复合在正面聚四氟乙烯发泡涂层4上,提高滤料过滤精度。所述膨化聚四氟乙烯微孔膜层是聚四氟乙烯基带经过双向高温拉伸制成;所述膨化聚四氟乙烯微孔膜层的厚度可为5~15微米,孔径范围0.02-1.8μm。本申请所述的膨化珍珠岩纤维复合滤料整体厚度范围一般为2.3-3.2mm;其可以在280℃以下的高温环境下稳定工作,过滤精度高,并且具有良好的耐磨折性、耐酸腐蚀性及高强低伸性能,使用寿命长,可用于各种复杂工作环境使用。本申请经过裁切、缝制等工序,可制成环保用复合滤袋。例如,按照滤袋的规格,将所述膨化珍珠岩纤维复合滤料裁剪和分切,然后用ptfe缝纫线,将滤料缝制成滤袋。本申请产品主要用于酸性烟气等工业粉尘的过滤和产品收集,应用功能性好。本申请实施例提供了一种膨化珍珠岩纤维复合滤料的制备方法,包括以下步骤:s1、将珍珠岩纤维膨体布用聚四氟乙烯乳液浸渍处理,然后依次干燥、烧结,使珍珠岩纤维膨体布两面分别形成聚四氟乙烯结合层;s2、将形成聚四氟乙烯结合层的珍珠纤维膨体布用第一涂层剂进行正面的发泡涂层处理,所述第一涂层剂包含聚四氟乙烯和第一发泡剂,在该面聚四氟乙烯结合层上形成正面聚四氟乙烯发泡涂层;并且,采用第二涂层剂进行反面的发泡涂层处理,所述第二涂层剂包含聚四氟乙烯和第二发泡剂,所述第一涂层剂和第二涂层剂独立可选地包含石墨烯,在该面聚四氟乙烯结合层上形成反面聚四氟乙烯发泡涂层;所述正面聚四氟乙烯发泡涂层的气泡孔径小于反面聚四氟乙烯发泡涂层的气泡孔径;s3、将膨化聚四氟乙烯微孔薄膜通过热压覆膜的方式复合于所述正面聚乙烯发泡涂层上,制成膨化珍珠岩纤维复合滤料。参见图2,图2为本申请一些实施例制备膨化珍珠岩纤维复合滤料的工艺流程图。本申请实施例的制备工序具体包括:珍珠岩纤维膨化基材——聚四氟乙烯乳液浸渍处理——涂层剂制作——正面涂层加工(也称迎尘面涂层加工)——反面(也称净气面)涂层加工——涂层剂固化——正面覆膜加工——检验检测——裁剪分切——滤袋缝制。本申请实施例按照本领域常规方法进行珍珠岩纤维膨体布的制作:本申请实施例优选采用细旦珍珠岩纤维纱(单丝直径可为5-7微米),经过纺纱——膨化加工——整经——织布等工序,按照织布工艺,采用织布机制成单位面积质量为300-900g/m2的珍珠岩纤维膨体布。其中,所述的膨化加工、整经均为本领域熟知的加工工序;织造而成的珍珠岩纤维膨体布单位面积重量优选为450~750g/m2,其织物组织结构包括双斜纹和缎纹等结构,正反面参数一样。然后,本申请实施例进行聚四氟乙烯浸渍处理:将制成的珍珠岩纤维膨体布引入到后处理生产线,采用聚四氟乙烯乳液浸渍该膨体布。所述浸渍的温度可为50-70℃,生产线速度为2-8m/min。接着,本申请实施例可依次进行挥发—烘干—烧结定型,使珍珠岩纤维膨体布两面分别形成聚四氟乙烯结合层。具体地,所述聚四氟乙烯乳液的固含量一般为60%,可包括硅烷偶联剂等助剂组成,例如采用日本大金公司的市售产品;浸渍处理后增重范围5-15%。所述珍珠岩纤维膨体布经过ptfe乳液浸渍处理后,本申请实施例将形成聚四氟乙烯结合层的膨体布送入涂层设备中,采用涂层剂进行双面的发泡涂层处理,分别形成正面聚四氟乙烯发泡涂层、反面聚四氟乙烯发泡涂层。其中,所述的涂层剂包含聚四氟乙烯和发泡剂,可以采用常规的混合方式制作。例如,在室温20-26℃区间内,将聚四氟乙烯乳液与发泡剂等添加剂混合,5min-10min后,制成均匀的ptfe涂层溶液(即涂层剂)。具体地,所述的聚四氟乙烯乳液固含量一般为50wt%~70wt%,在涂层剂中用量在80wt%以上,优选为83-91%,聚四氟乙烯为涂层主要成分。本申请通过发泡剂的加入和用量的调整,控制气泡的数量和气泡的尺寸;所述发泡剂可为脂肪酸酰胺衍生物,含量在1.5wt%以上。此外,所述涂层剂中还包含增稠剂、泡沫稳定剂等。所述增稠剂包括但不限于丙烯酸乳液、聚乙烯醇和聚丙烯酰胺;增稠剂的加入和用量的控制可以调节涂层溶液的粘度,同时控制滤料表面聚四氟乙烯涂层的厚度。本申请还可加入四氟乙烯、六氟乙烯等含氟助剂,有助于基材与涂层的结合。为便于区分,将用于正面的涂层剂称为第一涂层剂,相应地包含第一发泡剂;用于反面的称为第二涂层剂、第二发泡剂。作为优选,所述第一涂层剂和第二涂层剂独立可选地包含石墨烯,具体采用分散液的形式;石墨烯的加入可以提升制品的物理、化学性能。在本申请的一些优选实施例中,所述第一涂层剂的配方组分及比例可参见表1:表1ptfe涂层溶液配方组分名称组分种类含量(%)聚四氟乙烯乳液固含量60%83-91含氟助剂四氟乙烯、六氟丙烯2-6泡沫稳定剂肥皂氨、羧甲基纤维素、聚乙烯醇4-7发泡剂脂肪酸酰胺衍生物1.5-3增稠剂丙烯酸乳液、聚乙烯醇、聚丙烯酰胺1.2-2石墨烯分散液固含量在0.4~0.5%,石墨烯颗粒直径:0.1-3μm1-5涂层剂制作完成后,本申请实施例同步进行正面发泡涂层、反面涂层。本申请实施例中正面的发泡涂层是采用发泡喷涂器与精密刮刀组合工艺:首先将聚四氟乙烯涂层溶液通过喷涂装置对滤料实施喷涂;然后经过精密刮刀将涂层剂均匀摊开,在滤料表面形成致密、均匀的聚四氟乙烯发泡涂层。所述的致密是发泡多孔,提高过滤精度。其中,用螺旋给料器以30-50l/min的速度将涂层溶液注入发泡罐内。通过供气系统经由旋转轴向搅拌器通入气体,搅拌室中的转速是决定气泡尺寸分布的关键参数之一,气泡尺寸随转速的增加而减小。发泡喷涂器一般以0.8-2.0m/min恒定的速度运行,通过控制发泡机械的转速,控制气泡尺寸分布,发泡机(与喷涂器不同)转速增加气泡会减小。作为优选,所述涂层溶液发起的气泡直径控制在≤40μm;所述的复合滤料正面涂层厚度控制在20μm-200μm。本申请中正面涂层较厚、孔径较小,可防止粉尘和气流冲刷,提高过滤精度。而本申请实施例中反面的发泡涂层是采用辊式涂层与精密刮刀组合工艺,可将调配好的涂层剂置于浆槽中,通过带浆辊旋转带起涂层剂涂覆于滤料表面,再经过精密刮刀将涂层剂涂覆均匀,优选得到厚度为50μm-300μm的反面涂层。所述的反面涂层较薄、孔径较大,主要能够保护滤料本体不受侵蚀,保证干净气流顺利通过,防止滤料堵塞。在本申请的具体实施例中,珍珠岩纤维膨体布的正面和反面涂层剂固化的加工同步进行,即依次经过挥发处理、烘干处理、烧结处理、定型处理等加工,进而制成包括双面涂层的复合滤料。作为优选,所述挥发的温度为91-99℃;所述烘干的温度为180-220℃。所述烧结的固化温度为370-400℃,固化时间为2min-8min。在定型温度220-260℃定型的同时,滤料表层被15-25psi的压力压扁,使滤料正面形成20μm-200μm涂层,反面形成50μm-300μm涂层。最后,本申请实施例进行覆膜加工:将上述双面涂层后的珍珠岩纤维膨体布和膨化聚四氟乙烯微孔薄膜,同步引入覆膜机,采用热压覆膜的方式,将膨化聚四氟乙烯微孔薄膜牢固地复合在所述正面聚乙烯发泡涂层上,制成膨化珍珠岩纤维复合滤料。其中,所述的膨化聚四氟乙烯微孔薄膜的孔隙率85%以上,孔径0.02-1.8μm。作为优选,所述热压覆膜的温度为370~415℃,覆膜的速度为2-7m/min,利于保证覆膜牢度高,透气性均匀。本申请还提供了膨化珍珠岩纤维复合滤袋及其制作,即采用上述加工工艺制成的膨化珍珠岩纤维复合滤料,按照滤袋的规格裁剪和分切,然后用聚四氟乙烯缝纫线将滤料缝制成滤袋,产品主要用于酸性烟气的过滤和产品收集。在本申请的实施例中,所述的滤料基材经过浸渍处理和双面涂层处理,耐酸腐蚀比常规滤料提高3倍以上;抗结露性突出。本申请经过涂层剂双面涂层后,滤料结构更稳定,可提高滤料的强力,滤料耐磨性能提高50%以上。其中的反面主要是保护滤料基材,提高耐腐蚀性和耐磨折性,同时反面的孔径与滤料浸渍处理后的孔径一致,避免滤料堵塞造成压差升高,甚至滤料失效。本申请优选在发泡涂层中加入石墨烯,可以显著提升环保滤料的拉伸断裂强力、耐温性能、耐腐蚀性能等。其中,石墨烯可改善涂层柔韧性,耐折性能提高10-30%;均匀涂覆的石墨烯具有良好的导电性能,可以在滤料上形成一张导电网而具有抗静电性能。本申请所述含有石墨烯的滤料的导电性能、过滤清灰性能有所提升,还提高了纤维及滤料的柔韧性,改善无机纤维材料的耐折性和耐磨性。经实验,石墨烯的加入可以将环保滤料的物理性能、化学性能、应用性能等综合性能提升15%以上。为了进一步理解本申请,下面结合实施例对本申请提供的膨化珍珠岩纤维复合滤料及其制备方法进行具体地描述。但是应当理解,这些实施例是在以本发明技术方案为前提下进行实施,给出了详细的实施方式和具体的操作过程,只是为进一步说明本发明的特征和优点,而不是对本发明权利要求的限制,本发明的保护范围也不限于下述的实施例。以下实施例中,所涉及的物料均为市售。实施例1膨化珍珠岩纤维复合滤袋的具体制作方案如下:1、珍珠岩纤维膨体布的制作。采用6μm细旦珍珠岩纤维纱,经过纺纱—膨化加工—整经—织布等工序,采用双斜纹组织、剑杆织机制成单位面积质量为550g/m2的珍珠岩纤维膨体布,厚度1.7mm。2、浸渍处理。将制成的珍珠岩纤维膨体布引入到后处理生产线中,首先进行聚四氟乙烯乳液浸渍,浸渍温度50℃,速度4m/min,然后依次进行挥发—烘干—烧结定型。3、涂层剂制作。在室温26℃,采用聚四氟乙烯乳液与一些添加剂均匀混合5min,制成涂层溶液;配方及比例详见表2:表2ptfe涂层溶液配方组分及比例组分名称组分种类含量(%)聚四氟乙烯乳液固含量60%85含氟助剂四氟乙烯4泡沫稳定剂肥皂氨5发泡剂脂肪酸酰胺衍生物2增稠剂丙烯酸乳液1.5石墨烯分散液固含量0.5%,石墨烯颗粒直径:1.1μm2.54、正面发泡涂层珍珠岩纤维膨体布经过上述ptfe乳液浸渍处理后,进入涂层设备,正面的涂层处理是采用发泡喷涂器与精密刮刀组合工艺,首先将涂层溶液通过喷涂装置对滤料实施喷涂,然后经过精密刮刀将涂层溶液均匀摊开,在滤料基材表面形成致密、均匀的聚四氟乙烯发泡涂层。其中,用螺旋给料器以30l/min的速度将涂层溶液注入发泡罐内。通过供气系统经由旋转轴向搅拌器通入气体;发泡喷涂器运行速度1.0m/min。所述涂层溶液发起的气泡控制在直径5μm-15μm;所述膨化珍珠岩纤维滤料正面涂层厚度控制在145μm。5、反面涂层反面采用辊式涂层与精密刮刀组合工艺,将调配好的涂层剂置于浆槽中,通过带浆辊旋转带起涂层剂涂覆于滤料反面,再经过精密刮刀将涂层剂涂覆均匀,反面涂层厚度为120μm,气泡直径18μm-30μm。6、涂层固化所述膨化珍珠岩纤维基材正面和反面的涂层加工同步进行,然后依次经过挥发处理、烘干处理、烧结处理、定型处理等工序的加工,制成膨化珍珠岩纤维双面涂层滤布。其中,挥发温度98℃,烘干温度210℃。烧结固化温度380℃,固化时间2min。在定型温度260℃定型的同时,滤料表层被15psi的压力压扁,最终正面形成145μm涂层、反面形成120μm涂层。7、覆膜加工膨化珍珠岩纤维双面涂层滤布和膨化聚四氟乙烯微孔薄膜(孔隙率90%,孔径0.02μm-1.6μm),同步引入覆膜机进行覆膜加工。采用高温热压的方式将膨化聚四氟乙烯微孔薄膜与膨化珍珠岩纤维双面涂层滤布牢固的覆合在一起,制成膨化珍珠岩纤维复合滤料。其中,覆膜温度405℃,覆膜速度3m/min。8、膨化珍珠岩纤维复合滤袋制作采用上述加工工艺制成的膨化珍珠岩纤维复合滤料685±5g/m2,按照滤袋的规格裁剪和分切,然后用ptfe缝纫线将滤料缝制成滤袋。实施例2膨化珍珠岩纤维复合滤袋的具体制作方案如下:1、珍珠岩纤维膨体布的制作。采用5.5μm细旦珍珠岩纤维纱,经过纺纱—膨化加工—整经—织布等工序,采用双斜纹组织、剑杆织机制成单位面积质量为600g/m2的珍珠岩纤维膨体布,厚度1.8mm。2、浸渍处理。将制成的珍珠岩纤维膨体布引入到后处理生产线中,首先进行聚四氟乙烯乳液浸渍,浸渍温度50℃,速度4m/min,然后依次进行挥发—烘干—烧结定型。3、涂层剂制作。在室温26℃,采用聚四氟乙烯乳液与一些添加剂均匀混合5min,制成涂层溶液;配方及比例详见表3:表3ptfe涂层溶液配方组分及比例组分名称组分种类含量(%)聚四氟乙烯乳液固含量60%86含氟助剂六氟丙烯3泡沫稳定剂羧甲基纤维素4发泡剂脂肪酸酰胺衍生物2.5增稠剂聚乙烯醇2石墨烯分散液固含量在0.5%,石墨烯颗粒直径:0.8μm2.54、正面发泡涂层珍珠岩纤维膨体布经过上述ptfe乳液浸渍处理后,进入涂层设备,正面的涂层处理是采用发泡喷涂器与精密刮刀组合工艺,首先将涂层溶液通过喷涂装置对滤料实施喷涂,然后经过精密刮刀将涂层溶液均匀摊开,在滤料基材表面形成致密、均匀的聚四氟乙烯发泡涂层。其中,用螺旋给料器以30l/min的速度将涂层溶液注入发泡罐内。通过供气系统经由旋转轴向搅拌器通入气体;发泡喷涂器以1.2m/min恒定的速度运行。所述涂层溶液发起的气泡控制在直径5-12μm;所述膨化珍珠岩纤维滤料正面涂层厚度控制在160μm。5、反面涂层反面采用辊式涂层与精密刮刀组合工艺,将调配好的涂层剂置于浆槽中,通过带浆辊旋转带起涂层剂涂覆于滤料反面,再经过精密刮刀将涂层剂涂覆均匀,反面涂层厚度为150μm,气泡直径15-22μm。6、涂层固化所述膨化珍珠岩纤维基材正面和反面的涂层加工同步进行,然后依次经过挥发处理、烘干处理、烧结处理、定型处理等工序的加工,制成膨化珍珠岩纤维双面涂层滤布。其中,挥发温度97℃,烘干温度215℃。烧结固化温度390℃,固化时间2min。定型温度260℃.在定型的同时滤料表层被16psi的压力压扁,最终正面形成160μm涂层、反面形成150μm涂层。7、覆膜加工膨化珍珠岩纤维双面涂层滤布和膨化聚四氟乙烯微孔薄膜(孔隙率88%,孔径0.02-1.5μm),同步引入覆膜机进行覆膜加工。采用高温热压的方式将膨化聚四氟乙烯微孔薄膜与膨化珍珠岩纤维双面涂层滤布牢固的覆合在一起,制成膨化珍珠岩纤维复合滤料。其中,覆膜温度411℃,覆膜速度3.5m/min。8、膨化珍珠岩纤维复合滤袋制作采用上述加工工艺制成的膨化珍珠岩纤维复合滤料745±5g/m2,按照滤袋的规格裁剪和分切,然后用聚四氟乙烯缝纫线将滤料缝制成滤袋。实施例3膨化珍珠岩纤维复合滤袋的具体制作方案如下:1、珍珠岩纤维膨体布的制作。采用6μm细旦珍珠岩纤维纱,经过纺纱—膨化加工—整经—织布等工序,采用双斜纹组织、剑杆织机制成单位面积质量为750g/m2的珍珠岩纤维膨体布,厚度2.0mm。2、浸渍处理。将制成的珍珠岩纤维膨体布引入到后处理生产线中,首先进行聚四氟乙烯乳液浸渍,浸渍温度45℃,速度3m/min,然后依次进行挥发—烘干—烧结定型。3、涂层剂制作。在室温26℃,采用聚四氟乙烯乳液与一些添加剂均匀混合5min,制成涂层溶液;配方及比例详见表4:表4ptfe涂层溶液配方组分及比例组分名称组分种类含量(%)聚四氟乙烯乳液固含量60%83含氟助剂四氟乙烯5泡沫稳定剂聚乙烯醇5发泡剂脂肪酸酰胺衍生物2.5增稠剂聚丙烯酰胺2石墨烯分散液固含量在0.5%,石墨烯颗粒直径:1.5μm2.54、正面发泡涂层珍珠岩纤维膨体布经过上述ptfe乳液浸渍处理后,进入涂层设备,正面的涂层处理是采用发泡喷涂器与精密刮刀组合工艺,首先将涂层溶液通过喷涂装置对滤料实施喷涂,然后经过精密刮刀将涂层溶液均匀摊开,在滤料基材表面形成致密、均匀的聚四氟乙烯发泡涂层。其中,用螺旋给料器以50l/min的速度将涂层溶液注入发泡罐内。通过供气系统经由旋转轴向搅拌器通入气体;发泡喷涂器一般以0.8m/min恒定的速度运行。所述涂层溶液发起的气泡控制在直径3μm-11μm;所述膨化珍珠岩纤维滤料正面涂层厚度控制在180μm。5、反面涂层反面采用辊式涂层与精密刮刀组合工艺,将调配好的涂层剂置于浆槽中,通过带浆辊旋转带起涂层剂涂覆于滤料反面,再经过精密刮刀将涂层剂涂覆均匀,反面涂层厚度为130μm,气泡直径15μm-22μm。6、涂层固化所述膨化珍珠岩纤维基材正面和反面的涂层加工同步进行,然后依次经过挥发处理、烘干处理、烧结处理、定型处理等工序的加工,制成膨化珍珠岩纤维双面涂层滤布。其中,挥发温度98.5℃,烘干温度225℃。烧结固化温度385℃,固化时间3min。定型温度260℃,在定型的同时,滤料表层被25psi的压力压扁,最终正面形成180μm涂层、反面形成130μm涂层。7、覆膜加工膨化珍珠岩纤维双面涂层滤布和膨化聚四氟乙烯微孔薄膜(孔隙率90%,孔径0.02μm-1.6μm),同步引入覆膜机进行覆膜加工。采用高温热压的方式将膨化聚四氟乙烯微孔薄膜与膨化珍珠岩纤维双面涂层滤布牢固的覆合在一起,制成膨化珍珠岩纤维复合滤料。其中,覆膜温度415℃,覆膜速度3.5m/min。8、膨化珍珠岩纤维复合滤袋制作采用上述加工工艺制成的膨化珍珠岩纤维复合滤料880±5g/m2,按照滤袋的规格裁剪和分切,然后用ptfe缝纫线将滤料缝制成滤袋。本发明实施例与普通复合滤料主要参数指标对比如下,按照国家相关标准检测:表5本发明实施例所述复合滤料的性能以上所述仅是本发明的优选实施方式,应当指出,对于使本
技术领域:
的专业技术人员,在不脱离本发明技术原理的前提下,是能够实现对这些实施例的多种修改的,而这些修改也应视为本发明应该保护的范围。当前第1页12