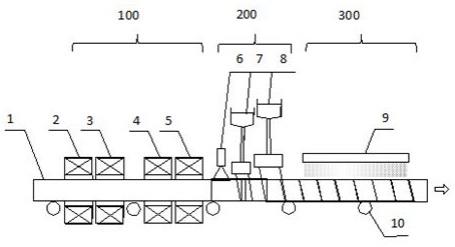
1.本发明涉及一种钢管涂敷加工装置及方法,尤其涉及一种外涂线钢管的变频率感应加热装置及方法。
背景技术:2.在现有技术的uoe(即依次通过u形压力机、o形压力机、扩管(expand)三道工序制成的钢管)焊管外涂敷生产线上,钢管(口径为500-1500mm,壁厚为10-40mm,长度为10-20m)以螺旋运动方式在锥形辊道上向前输送,在加热区通过四台分段布置的中频感应炉对钢管进行感应加热,使钢管外表面逐步预热到涂敷工艺要求温度,即180-240℃。涂敷时,静电喷涂的环氧树脂粉末颗粒在高温钢管表面的热作用下短时间内快速熔化、铺展并与钢管表面紧密结合在一起形成一层具有良好耐环境腐蚀性能的保护涂层,涂层外再包裹粘胶带层、聚乙烯胶带层等进一步增强了钢管表面防护能力;喷淋冷却目的是降低钢管温度使涂层材料固化,并便于进行后道工序加工处理。
3.在上述感应加热过程,每台感应炉电功率和频率均基本相同,电功率约800kw、频率约1000hz。钢管在第一级感应炉内由于感应加热其外表面温度迅速升高,出炉后感应热会向钢管内壁方向传导(也包括部分向周围环境的散热),外表面温度有一定降低,直到进入下一级感应加热炉,钢管温度再次提高。在多级感应加热过程中,钢管外表面和内表面温度在总体上呈逐步升高趋势。在到达涂敷点位置时,钢管外表温度达到涂敷温度,即220-240℃,而不参与喷涂的钢管内表面由于前期感应加热及热传导作用的共同影响下温度也会升高到180-200℃,请参见附图1,图中,横轴为时间,纵轴为钢管温度,实线表示钢管外表面温度,虚线表示钢管内表面温度。现有技术的近乎透热的中频感应加热方式不仅浪费了大量感应电源功率,而且也加大了钢管在涂敷后冷却段的冷却负荷及冷却水消耗(约500m3/h),产线系统能源和资源利用率有待提升。
4.中国发明专利zl200710024745.1公开了一种钢管、石油油井管和钻杆中频感应加热热处理方法,并具体公开了通过中频感应加热对无缝钢管进行淬火和回火的方法,但该加热方式需要的是钢管壁厚通透且均匀加热,一般选择频率为1000hz左右的中频加热,直接应用会导致不参与喷涂的钢管内表面温度也迅速升高,浪费了大量的能源和资源。
技术实现要素:5.本发明的目的之一在于提供一种外涂线钢管的变频率感应加热装置,能通过各感应炉电源功率和电源频率的分配,实现提升钢管外表面温度的同时抑制钢管内表面温升的目的,从而降低能耗。
6.本发明的目的之二在于提供一种外涂线钢管的变频率感应加热方法,通过对感应加热的电源功率和电源频率的调节,实现钢管分级加热,使感应热热量向钢管进行涂敷的外表面集中并减小内表面温升,进一步提高感应加热效率并降低能耗。
7.本发明是这样实现的:
一种外涂线钢管的变频率感应加热装置,包括沿钢管传动方向依次设置的若干级感应炉、喷涂器、中间包覆器、外包覆器和喷淋冷却器,钢管通过若干根输送辊道传动,并依次经过若干级感应炉形成的加热区,喷涂器、中间包覆器和外包覆器形成的涂敷区,以及喷淋冷却器形成的冷却区;所述的若干级感应炉内感应炉线圈的电源频率和功率各不相同,即若干级感应炉内感应炉线圈的电源频率沿钢管传动方向依次升高,且若干级感应炉内感应炉线圈的电源功率沿钢管传动方向依次降低。
8.所述的若干级感应炉内的线圈匝数相同,且相邻两级感应炉内感应炉的线圈绕向相反,在每一级感应炉的感应加热电源上均设置不同电容值的补偿电容c,形成不同电源频率的感应电源r-l-c谐振回路。
9.所述的若干级感应炉内感应炉线圈的补偿电容c的电容值沿钢管传动方向依次减小。
10.所述的若干级感应炉依次布置在喷涂器的入口上游,且若干级感应炉与输送辊道交错设置。
11.每两级所述的感应炉与一根输送辊道交错设置。
12.一种外涂线钢管的变频率感应加热方法,包括以下步骤:步骤1:根据钢管的口径选择感应炉的级数;步骤2:调节步骤1中选择的一级或若干级感应炉所对应的补偿电容c的电容值,使若干级感应炉内感应炉线圈的电源频率沿钢管传动方向依次升高,且若干级感应炉内感应炉线圈的电源功率沿钢管传动方向依次降低;步骤3:通过输送辊道输送钢管,使钢管依次经过加热区、涂敷区和冷却区。
13.所述的步骤1中,在选择感应炉时,沿钢管的传动方向反向选择,即优先选择靠近喷涂器的感应炉。
14.本发明与现有技术相比,具有如下有益效果:1、本发明由于设有电源频率依次升高且电源功率依次降低的多级感应炉,能对钢管进行分级加热,使感应热热量向钢管进行涂敷的外表面集中,升高钢管外表面温度的同时减小内表面温升,进一步提高感应加热效率并减少后续冷却水等能介消耗,改善涂敷产线系统能源利用率,提高钢管涂敷机组生产效率。
15.2、本发明通过功率和频率的优化分配实现非通透感应加热,感应加热效率能提高10-30%,冷却水消耗能减少10-30%,系统能源利用率能提高10-30%,涂敷机组速度能提高10-30%,可带来显著经济效益。
16.3、本发明适用于石油天然气输送用大口径焊管外表面连续涂敷线上,也能推广应用于各种管/线/棒长材钢甚至钢板/坯的感应加热工艺中,有效提高分级式感应加热的加热质量和加热效率。
17.本发明通过对感应加热的电源功率和电源频率的分级分配和调节,从首级感应炉到末级感应炉感应加热电源频率逐步增加,使感应热热量向钢管进行涂敷的外表面集中,升高钢管外表面温度的同时减小内表面温升,进一步提高感应加热效率并降低能耗,尤其适用于石油天然气输送用大口径焊管外表面连续涂敷作业。
附图说明
18.图1是采用现有技术的钢管感应加热使内、外表面温度的变化示意图;图2是本发明外涂线钢管的变频率感应加热装置的结构示意图;图3是采用本发明外涂线钢管的变频率感应加热装置感应加热钢管过程中钢管内、外表面温度的变化示意图。
19.图中,1钢管,2一级感应炉,3二级感应炉,4三级感应炉,5四级感应炉,6喷涂器,7中间包覆器,8外包覆器,9喷淋冷却器,10输送辊道;100加热区200涂敷区,300冷却区。
具体实施方式
20.下面结合附图和具体实施例对本发明作进一步说明。
21.请参见附图2,一种外涂线钢管的变频率感应加热装置,包括沿钢管1传动方向依次设置的若干级感应炉、喷涂器6、中间包覆器7、外包覆器8和喷淋冷却器9,钢管1通过若干根输送辊道10传动,如图2中箭头方向所示,并依次经过若干级感应炉形成的加热区100,喷涂器6、中间包覆器7和外包覆器8形成的涂敷区200,以及喷淋冷却器9形成的冷却区300。
22.所述的若干级感应炉内感应炉线圈的电源频率和功率各不相同,即若干级感应炉内感应炉线圈的电源频率沿钢管1传动方向依次升高,且若干级感应炉内感应炉线圈的电源功率沿钢管1传动方向依次降低。优选的,若干级感应炉的电源频率范围为800-10000hz,使用时可根据加热工艺要求按照逐级升高的原则分段设置,具体可通过设置补偿电容c等方式实现电源频率调节;若干级感应炉的电源功率范围为400-1000kw,使用时可根据加热工艺要求按照逐级降低的原则分段设置,具体可通过变压器等设备实现电源功率调节,同时,感应炉电源频率越高,其对应的电源功率越低。
23.相邻两级所述的感应炉内感应炉的线圈绕向相反,防止感应加热时钢管1感应电压的累积效应,避免钢管1由于累积电势过高而放电打火,从而避免影响钢管1表面质量和输送辊道10安全。
24.所述的若干级感应炉内的线圈匝数基本相同,在每一级感应炉的感应加热电源上均设置有不同电容值的补偿电容c,形成不同电源频率的感应电源r-l-c谐振回路。优选的,补偿电容c的电容值范围为5-800uf,使用时可根据加热工艺要求按照逐级减小的原则分段设置,具体可通过改变电容器的串并联方式来调节。通过调节补偿电容c的电容值改变谐振频率、通过频率跟踪来实现改变不同感应加热电源交变电流工作频率的目的,减小感应炉内感应炉线圈的布置复杂性。
25.所述的若干级感应炉内感应炉线圈的补偿电容c的电容值沿钢管1传动方向依次减小。在感应电源r-l-c谐振回路中,其共振频率f=1/(2πsqrt(lc)),在负载电感l基本不变的条件下,补偿电容c越小,频率f越大,因此,若干级感应加热电源的补偿电容c的电容值逐渐减小,由此可实现感应加热电源的频率由低到高的调节分配,并使每一级感应加热电源工作在最佳状态。
26.所述的若干级感应炉依次布置在喷涂器6的入口上游,且若干级感应炉与输送辊道10交错设置。优选的,每两级感应炉与一根输送辊道10交错设置,使若干级感应炉的位置相互集中,且若干级感应炉形成的加热区100的位置靠近涂敷区200的位置,可缩短感应加热过程中钢管1在加热区100内的穿行时间,减小钢管1表面感应热量在钢管1内部的传导和
向周围环境的散失。
27.请参见附图3,图中,横轴表示时间,纵轴表示钢管温度,实线表示钢管外表面温度,虚线表示钢管内表面温度。本发明通过对各级感应炉的电源频率和电源功率进行逐级分配,感应加热时,后一级频率更高的感应加热是在前一级频率更低感应加热所形成的温度较低、深度较深的感应加热温度场的基础上,通过电磁集肤效应进一步快速提升深度更浅部分钢管表面层的温度。在感应加热过程中使感应加热热量向钢管的外表面集中,钢管表面高温部分的深度更浅,热量向钢管内壁传导的热阻更大、时间更短、热量更少,抑制不参与喷涂的钢管内壁的温升,从而使后一级感应加热所需要的电功率可以逐步减小,涂敷后喷淋冷却段所需要的冷却水用量必然相应减少,最终实现提高感应加热效率的同时减小冷却负荷、提高能源利用效率、降低冷却水等能介消耗目的。
28.一种外涂线钢管的变频率感应加热方法,可用于变频率感应加热口径范围500mm至1500mm的常用钢管,包括外径为500-1000mm的小口径焊管、外径为1000-1500mm的大口径焊管等。该变频率感应加热包括以下步骤:步骤1:根据钢管的口径选择感应炉的级数,优选的,在选择感应炉时,可沿钢管1的传动方向反向选择,即优先选择靠近喷涂器6的感应炉,减少感应加热与喷涂两道工序之间的时间间隔,从而减小钢管1表面感应热量在钢管1内部的传导和向周围环境的散失。
29.步骤2:调节步骤1中选择的一级或若干级感应炉所对应的补偿电容c的电容值,使若干级感应炉内感应炉线圈的电源频率沿钢管1传动方向依次升高,且若干级感应炉内感应炉线圈的电源功率沿钢管1传动方向依次降低。
30.步骤3:通过输送辊道10输送钢管1,使钢管1依次经过加热区100、涂敷区200和冷却区300。
31.实施例1:变频率感应加热装置的加热区100内布置四级感应炉,沿钢管1传动方向依次为一级感应炉2、二级感应炉3、三级感应炉4和四级感应炉5,且一级感应炉2和二级感应炉3设置在两根相邻的输送辊道10之间,三级感应炉4和四级感应炉5设置在两根相邻的输送辊道10之间并靠近喷涂器6设置。一级感应炉2的线圈正向缠绕,二级感应炉3的线圈反向缠绕,三级感应炉4的线圈正向缠绕,四级感应炉5的线圈反向缠绕。
32.对外径为660mm的小口径焊管进行加热、涂敷和冷却操作,由于钢管1的口径较小,选用靠近喷涂器6的三级感应炉4和四级感应炉5即可达到加热钢管1外表面至涂敷所需温度的目的。调节三级感应炉4的电源频率为1000hz,电源输出功率为800kw,三级感应炉4对应的补偿电容c的电容值为500uf;调节四级感应炉5电源频率为4000hz,电源输出功率为600kw,四级感应炉5对应的补偿电容c的电容值为31.25uf。钢管1通过输送辊道10依次经过三级感应炉4和四级感应炉5的感应炉线圈感应加热后,外表面温度在涂敷区200达到220℃,满足涂敷工艺要求,而钢管1的内壁温度控制在160-180℃,加热过程节约电能12.5%,同时相应减少后续喷淋冷却器9冷却钢管1所需要的喷淋冷却水,喷淋冷却水的消耗至少能降低10%。
33.实施例2:变频率感应加热装置的加热区100内布置四级感应炉,沿钢管1传动方向依次为一级感应炉2、二级感应炉3、三级感应炉4和四级感应炉5,且一级感应炉2和二级感应炉3设置在两
根相邻的输送辊道10之间,三级感应炉4和四级感应炉5设置在两根相邻的输送辊道10之间并靠近喷涂器6设置。
34.对外径为660mm的小口径焊管进行加热、涂敷和冷却操作,由于钢管1的口径较小,选用靠近喷涂器6的三级感应炉4和四级感应炉5即可达到加热钢管1外表面至涂敷所需温度的目的。调节三级感应炉4的电源频率为1000hz,电源输出功率为800kw,三级感应炉4对应的补偿电容c的电容值为500uf;调节四级感应炉5电源频率为10000hz,电源输出功率为400kw,四级感应炉5对应的补偿电容c的电容值为5uf。钢管1通过输送辊道10依次经过三级感应炉4和四级感应炉5的感应炉线圈感应加热后,外表面温度在涂敷区200达到220℃,满足涂敷工艺要求,而钢管1的内壁温度控制在140-160℃,加热过程节约电能25%,同时相应减少后续喷淋冷却器9冷却钢管1所需要的喷淋冷却水,喷淋冷却水的消耗至少能降低20%。
35.实施例3:变频率感应加热装置的加热区100内布置四级感应炉,沿钢管1传动方向依次为一级感应炉2、二级感应炉3、三级感应炉4和四级感应炉5,且一级感应炉2和二级感应炉3设置在两根相邻的输送辊道10之间,三级感应炉4和四级感应炉5设置在两根相邻的输送辊道10之间并靠近喷涂器6设置。
36.对外径为1420mm的大口径焊管进行加热、涂敷和冷却操作,由于钢管1的口径较大,选用四级感应炉加热以达到加热钢管1外表面至涂敷所需温度的目的。调节一级感应炉2的电源频率为1000hz,电源输出功率为800kw,一级感应炉2对应的补偿电容c的电容值为500uf;调节二级感应炉3电源频率为2000hz,电源输出功率为700kw,二级感应炉3对应的补偿电容c的电容值为125uf;调节三级感应炉4的电源频率为4000hz,电源输出功率为600kw,三级感应炉4对应的补偿电容c的电容值为31.25uf;调节四级感应炉5电源频率为10000hz,电源输出功率为400kw,四级感应炉5对应的补偿电容c的电容值为5uf。钢管1通过输送辊道10依次经过一级感应炉2、二级感应炉3、三级感应炉4和四级感应炉5的感应炉线圈感应加热后,外表面温度在涂敷区200达到220℃,满足涂敷工艺要求,而钢管1的内壁温度控制在120-140℃,加热过程节约电能21.88%,同时相应减少后续喷淋冷却器9冷却钢管1所需要的喷淋冷却水,喷淋冷却水的消耗至少能降低20%。
37.实施例4:变频率感应加热装置的加热区100内布置四级感应炉,沿钢管1传动方向依次为一级感应炉2、二级感应炉3、三级感应炉4和四级感应炉5,且一级感应炉2和二级感应炉3设置在两根相邻的输送辊道10之间,三级感应炉4和四级感应炉5设置在两根相邻的输送辊道10之间并靠近喷涂器6设置。
38.对外径为1420mm的大口径焊管进行加热、涂敷和冷却操作,由于钢管1的口径较大,选用四级感应炉加热以达到加热钢管1外表面至涂敷所需温度的目的。调节一级感应炉2的电源频率为1000hz,电源输出功率为700kw,一级感应炉2对应的补偿电容c的电容值为500uf;调节二级感应炉3电源频率为2500hz,电源输出功率为600kw,二级感应炉3对应的补偿电容c的电容值为80uf;调节三级感应炉4的电源频率为5000hz,电源输出功率为500kw,三级感应炉4对应的补偿电容c的电容值为20uf;调节四级感应炉5电源频率为10000hz,电源输出功率为400kw,四级感应炉5对应的补偿电容c的电容值为5uf。钢管1通过输送辊道10依次经过一级感应炉2、二级感应炉3、三级感应炉4和四级感应炉5的感应炉线圈感应加热
后,外表面温度在涂敷区200达到220℃,满足涂敷工艺要求,而钢管1的内壁温度控制在110-130℃,加热过程节约电能31.25%,同时相应减少后续喷淋冷却器9冷却钢管1所需要的喷淋冷却水,喷淋冷却水的消耗至少能降低30%。
39.以上仅为本发明的较佳实施例而已,并非用于限定本发明的保护范围,因此,凡在本发明的精神和原则之内所作的任何修改、等同替换、改进等,均应包含在本发明的保护范围之内。