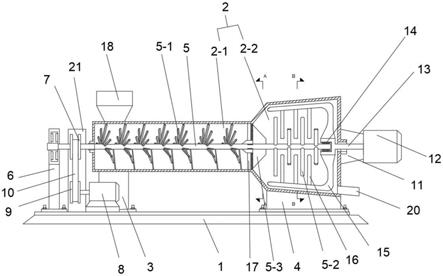
1.本实用新型涉及造粒设备领域,特别是绿色环保的水性钴盐粘合剂制备专用成品造粒装置。
背景技术:2.钴盐是指钴离子和酸根构成的物质,其中也可以含有一定比例的其它离子。钴盐用于增进橡胶与金属的粘合,已得到普遍认可并广泛应用于子午线轮胎和钢丝胶管等产品中。针对于水性钴盐粘合剂进行制备的过程中,需要对水性钴盐粘合剂进行造粒过程,造粒过程一般采用湿法造粒机,其湿法造粒机将水性钴盐原料与粘合剂分别通入造粒设备中,通过造粒设备中转轴的高度旋转带动搅拌杆进行高速转动,搅拌杆与原料之间进行碰撞搅拌打散形成粒子颗粒。现有的造粒装置中,其造粒设备的造粒筒体采用统一直径的形式,且造粒轴的首尾端的转轴转速一致,导致粒子在造粒设备中造粒均匀程度较低,未能实现对原料进行分级粒子成型,造粒设备的成型速率较低。
技术实现要素:3.为了解决上述存在的问题,本实用新型公开了绿色环保的水性钴盐粘合剂制备专用成品造粒装置,其具体技术方案如下:绿色环保的水性钴盐粘合剂制备专用成品造粒装置,包括底座、筒体、第一支架、第二支架、转动轴、支撑座、从动皮带轮、皮带电机、主动皮带轮、传动皮带、尾端支架、尾端电机、尾端转轴、联轴器、外圈搅动杆和侧搅动杆;
4.所述筒体横向设置于所述底座的顶面,所述筒体包括第一筒体和第二筒体,所述第一筒体和第二筒体呈首尾相连;所述第一筒体的内端面设有内衬杆,所述内衬杆的外端与所述第一筒体的内壁面固定设置;所述筒体的顶面一端设有进料斗,所述筒体的顶面一端设有进液管;所述筒体的一端面底侧设有出料口;所述第一支架设置于所述第一筒体的一端底侧,所述筒体通过所述第一支架与所述底座实现支撑;所述第二支架设置于所述第二筒体的一端底侧,所述筒体通过所述第二支架与所述底座实现支撑;所述转动轴横向设置于所述筒体内,所述转动轴的一端贯穿所述内衬杆并伸入所述第二筒体内,所述转动轴的一端贯穿所述第一筒体,并伸入所述支撑座内,通过轴承与所述支撑座实现转动;所述转动轴的中端侧壁设有第一搅动杆,所述第一搅动杆设置于所述第一筒体内,所述第一搅动杆呈螺旋设置;所述转动轴的一端侧壁设有第二搅动杆,所述第二搅动杆设置于所述第二筒体内,所述第二搅动杆呈周向设置;所述支撑座设置于所述底座的顶面一端,且设置于所述筒体的一端,所述支撑座的底端通过螺栓与所述底座呈垂直设置,所述转动轴的一端通过轴承与所述支撑座的顶端实现转动;所述从动皮带轮设置于所述转动轴的外壁,所述从动皮带轮与所述转动轴呈同轴转动;所述皮带电机设置于所述筒体的底端,所述皮带电机通过螺栓与所述底座实现固定;所述主动皮带轮设置于所述皮带电机的一侧,所述主动皮带轮与所述皮带电机同轴转动;所述传动皮带包裹于所述主动皮带轮和所述从动皮带轮的外壁,所述主动皮带轮和所述从动皮带轮通过所述传动皮带实现传动;
5.所述尾端支架设置于所述第二筒体的外端面,并与所述第二筒体呈固定设置;所述尾端电机设置于所述尾端支架的一端,并与所述尾端支架呈固定设置;所述尾端转轴与所述尾端电机同轴转动,所述尾端转轴的一端贯穿并伸入所述第二筒体内,所述尾端转轴通过轴承与所述第二筒体呈转动设置;所述联轴器嵌合于所述尾端转轴的端面,并与所述尾端转轴呈固定设置,且所述转动轴的端部伸入所述联轴器内,并与所述联轴器呈可转动设置;所述外圈搅动杆固定设置于所述尾端转轴的侧壁面,所述侧搅动杆设置于每侧所述外圈搅动杆的一侧,并与所述外圈搅动杆呈固定设置。
6.进一步的,所述第二筒体设置于所述第一筒体的尾端,所述第一筒体的直径小于所述第二筒体的直径,所述第一筒体的长度远长于所述第二筒体的长度;所述第一筒体为圆筒状结构,所述第二筒体呈一端窄一端宽的圆台状结构,所述第二筒体的内侧壁面呈坡面状。
7.进一步的,所述内衬杆包括内衬环、内杆和内衬网,所述内衬环与所述第一筒体的圆心呈同心设置,所述转动轴贯穿所述内衬环,并通过轴承实现所述转动轴与所述内衬环转动;所述内杆周向设置于所述内衬环的外壁,所述内杆的数量为三个,所述内衬环通过内杆与所述第一筒体呈固定设置;所述内衬网设置于所述内杆之间,所述内衬网的侧边与所述内杆呈固定设置。
8.进一步的,所述进料斗设置于所述第一筒体的一端,所述进液管设置于所述第一筒体的一端,所述进料斗与所述进液管呈相对设置。
9.进一步的,所述出料口设置于所述第二筒体的端面底端,所述出料口与所述第二筒体的端面呈斜向设置。
10.进一步的,所述第一搅动杆的长度于所述第一筒体的内径相适应,所述第一搅动杆贯穿所述第一筒体内。
11.进一步的,所述转动轴的一端外壁设有刮板,所述刮板设置于所述第二筒体内,且周向设置于所述转动轴的外壁,所述刮板呈“十”字型设置,每个所述刮板的一侧边贴合于所述内杆的端面。
12.进一步的,所述第二搅动杆的长度小于所述第二筒体的内径,所述第二搅动杆呈四层设置,每侧所述第二搅动杆的数量为六个,相邻两层所述第二搅动杆呈交错设置。
13.进一步的,所述从动皮带轮设置于所述第一筒体和所述支撑架之间。
14.进一步的,所述从动皮带轮的外侧包裹有防尘壳体,所述防尘壳体同时包裹于所述传动皮带和主动皮带轮的外侧,所述防尘壳体的底端与所述底座呈固定设置,所述皮带电机设置于所述防尘壳体的外侧。
15.进一步的,所述外圈搅动杆的数量为两个,并于所述联轴器的两端呈对称设置,每侧所述外圈搅动杆的形状呈“l”型结构,所述外圈搅动杆的外侧形状与所述第二筒体的内壁面形状相适应。
16.进一步的,每侧所述外圈搅动杆设置的所述侧搅动杆数量为三个,呈平行设置,每个所述侧搅动杆呈前端窄尾端宽的结构;每个所述侧搅动杆与每层所述第二搅动杆呈交错设置。
17.本实用新型的有益效果是:
18.本实用新型将造粒装置进行结构设计,将筒体结构设计为两段式结构,原料通过
第一筒体内搅动进行横向传送,并进入第二筒体内进行二次搅动造粒成型;本装置通过将造粒工艺进行分级进行,原料进入不同直径的筒体结构内,并配合不同搅动杆的搅动形式,将原料由一次加工的粗集料形成二次加工的粗集料,提高了粒子在造粒设备中的成型速率,造粒后的粒子均匀程度高,且整体装置的结构紧凑,造粒过程具有较高的制备速率。
附图说明
19.图1是本实用新型的整体剖视示意图。
20.图2是本实用新型图1的a
‑
a向局部剖视图。
21.图3是本实用新型图1的b
‑
b向局部剖视图。
22.图4是本实用新型第一筒体处的局部剖视图。
23.附图标记列表:
24.底座1;
25.筒体2;
26.第一筒体2
‑
1、第二筒体2
‑
2;
27.第一支架3;
28.第二支架4;
29.转动轴5;
30.第一搅动杆5
‑
1、第二搅动杆5
‑
2、刮板5
‑
3;
31.支撑座6;
32.从动皮带轮7;
33.皮带电机8;
34.主动皮带轮9;
35.传动皮带10;
36.尾端支架11;
37.尾端电机12;
38.尾端转轴13;
39.联轴器14;
40.外圈搅动杆15;
41.侧搅动杆16;
42.内衬杆17;
43.内衬环17
‑
1、内杆17
‑
2、内衬网17
‑
3;
44.进料斗18;
45.进液管19;
46.出料口20;
47.防尘壳体21。
具体实施方式
48.为使本实用新型的技术方案更加清晰明确,下面结合附图对本实用新型进行进一步描述,任何对本实用新型技术方案的技术特征进行等价替换和常规推理得出的方案均落
入本实用新型保护范围。本实施例中所提及的固定连接,固定设置、固定结构均为胶粘、焊接、螺钉连接、螺栓螺母连接、铆接等本领域技术人员所知晓的公知技术。
49.结合附图可见,绿色环保的水性钴盐粘合剂制备专用成品造粒装置,包括底座1、筒体2、第一支架3、第二支架4、转动轴5、支撑座6、从动皮带轮7、皮带电机8、主动皮带轮9、传动皮带10、尾端支架11、尾端电机12、尾端转轴13、联轴器14、外圈搅动杆15和侧搅动杆16;
50.所述筒体2横向设置于所述底座1的顶面,所述筒体2包括第一筒体2
‑
1和第二筒体2
‑
2,所述第一筒体2
‑
1和第二筒体2
‑
2呈首尾相连;所述第一筒体2
‑
1的内端面设有内衬杆17,所述内衬杆17的外端与所述第一筒体2
‑
1的内壁面固定设置;所述筒体2的顶面一端设有进料斗18,所述筒体2的顶面一端设有进液管19;所述筒体2的一端面底侧设有出料口20;所述第一支架3设置于所述第一筒体2
‑
1的一端底侧,所述筒体2通过所述第一支架3与所述底座1实现支撑;所述第二支架4设置于所述第二筒体2
‑
2的一端底侧,所述筒体2通过所述第二支架4与所述底座1实现支撑;所述转动轴5横向设置于所述筒体2内,所述转动轴5的一端贯穿所述内衬杆17并伸入所述第二筒体2
‑
2内,所述转动轴5的一端贯穿所述第一筒体2
‑
1,并伸入所述支撑座6内,通过轴承与所述支撑座6实现转动;所述转动轴5的中端侧壁设有第一搅动杆5
‑
1,所述第一搅动杆5
‑
1设置于所述第一筒体2
‑
1内,所述第一搅动杆5
‑
1呈螺旋设置;所述转动轴5的一端侧壁设有第二搅动杆5
‑
2,所述第二搅动杆5
‑
2 设置于所述第二筒体2
‑
2内,所述第二搅动杆5
‑
2呈周向设置;所述支撑座6设置于所述底座1的顶面一端,且设置于所述筒体2的一端,所述支撑座6的底端通过螺栓与所述底座1 呈垂直设置,所述转动轴5的一端通过轴承与所述支撑座6的顶端实现转动;所述从动皮带轮7设置于所述转动轴5的外壁,所述从动皮带轮7与所述转动轴5呈同轴转动;所述皮带电机8设置于所述筒体2的底端,所述皮带电机8通过螺栓与所述底座1实现固定;所述主动皮带轮9设置于所述皮带电机8的一侧,所述主动皮带轮9与所述皮带电机8同轴转动;所述传动皮带10包裹于所述主动皮带轮9和所述从动皮带轮7的外壁,所述主动皮带轮9和所述从动皮带轮7通过所述传动皮带10实现传动;
51.所述尾端支架11设置于所述第二筒体2
‑
2的外端面,并与所述第二筒体2
‑
2呈固定设置;所述尾端电机12设置于所述尾端支架11的一端,并与所述尾端支架11呈固定设置;所述尾端转轴13与所述尾端电机12同轴转动,所述尾端转轴13的一端贯穿并伸入所述第二筒体 2
‑
2内,所述尾端转轴13通过轴承与所述第二筒体2
‑
2呈转动设置;所述联轴器14嵌合于所述尾端转轴13的端面,并与所述尾端转轴13呈固定设置,且所述转动轴5的端部伸入所述联轴器14内,并与所述联轴器14呈可转动设置;所述外圈搅动杆15固定设置于所述尾端转轴13的侧壁面,所述侧搅动杆16设置于每侧所述外圈搅动杆15的一侧,并与所述外圈搅动杆15呈固定设置。
52.进一步的,所述第二筒体2
‑
2设置于所述第一筒体2
‑
1的尾端,所述第一筒体2
‑
1的直径小于所述第二筒体2
‑
2的直径,所述第一筒体2
‑
1的长度远长于所述第二筒体2
‑
2的长度;所述第一筒体2
‑
1为圆筒状结构,所述第二筒体2
‑
2呈一端窄一端宽的圆台状结构,所述第二筒体2
‑
2的内侧壁面呈坡面状。
53.进一步的,所述内衬杆17包括内衬环17
‑
1、内杆17
‑
2和内衬网17
‑
3,所述内衬环17
‑
1 与所述第一筒体2
‑
1的圆心呈同心设置,所述转动轴5贯穿所述内衬环17
‑
1,并通过轴
承实现所述转动轴5与所述内衬环17
‑
1转动;所述内杆17
‑
2周向设置于所述内衬环17
‑
1的外壁,所述内杆17
‑
2的数量为三个,所述内衬环17
‑
1通过内杆17
‑
2与所述第一筒体2
‑
1呈固定设置;所述内衬网17
‑
3设置于所述内杆17
‑
2之间,所述内衬网17
‑
3的侧边与所述内杆17
‑
2 呈固定设置。
54.进一步的,所述进料斗18设置于所述第一筒体2
‑
1的一端,所述进液管19设置于所述第一筒体2
‑
1的一端,所述进料斗18与所述进液管19呈相对设置。
55.进一步的,所述出料口20设置于所述第二筒体2
‑
2的端面底端,所述出料口20与所述第二筒体2
‑
2的端面呈斜向设置。
56.进一步的,所述第一搅动杆5
‑
1的长度于所述第一筒体2
‑
1的内径相适应,所述第一搅动杆5
‑
1贯穿所述第一筒体2
‑
1内。
57.进一步的,所述转动轴5的一端外壁设有刮板5
‑
3,所述刮板5
‑
3设置于所述第二筒体 2
‑
2内,且周向设置于所述转动轴5的外壁,所述刮板5
‑
3呈“十”字型设置,每个所述刮板5
‑
3的一侧边贴合于所述内杆17
‑
2的端面。
58.进一步的,所述第二搅动杆5
‑
2的长度小于所述第二筒体2
‑
2的内径,所述第二搅动杆 5
‑
2呈四层设置,每侧所述第二搅动杆5
‑
2的数量为六个,相邻两层所述第二搅动杆5
‑
2呈交错设置。
59.进一步的,所述从动皮带轮7设置于所述第一筒体2
‑
1和所述支撑架之间。
60.进一步的,所述从动皮带轮7的外侧包裹有防尘壳体21,所述防尘壳体21同时包裹于所述传动皮带10和主动皮带轮9的外侧,所述防尘壳体21的底端与所述底座1呈固定设置,所述皮带电机8设置于所述防尘壳体21的外侧。
61.进一步的,所述外圈搅动杆15的数量为两个,并于所述联轴器14的两端呈对称设置,每侧所述外圈搅动杆15的形状呈“l”型结构,所述外圈搅动杆15的外侧形状与所述第二筒体2
‑
2的内壁面形状相适应。
62.进一步的,每侧所述外圈搅动杆15设置的所述侧搅动杆16数量为三个,呈平行设置,每个所述侧搅动杆16呈前端窄尾端宽的结构;每个所述侧搅动杆16与每层所述第二搅动杆 5
‑
2呈交错设置。
63.本实用新型的结构原理是:
64.本实用新型使用时,将水性钴盐原料通过进料斗通入第一筒体内,将粘合剂通过进液管通入第一筒体内;启动皮带电机带动主动皮带轮进行转动,通过传动皮带的传动作用,从动皮带轮进行传动转动,转动轴带动第一搅动杆和第二搅动杆进行转动,第一搅动杆搅动时对水性钴盐原料和粘合剂进行搅动并进行横向传送,并通过内衬杆的内衬网进入第二筒体内,第二筒体内的刮板进行旋转时将通过内衬网的混合料进行刮除,并在第二筒体内受第二搅动杆的搅动作用;启动尾端电机,尾端电机带动尾端转轴、联轴器进行转动,尾端转轴与转动轴承反向转动,外圈搅动杆沿着第二筒体的内壁进行周向转动,侧搅动杆与第二搅动杆进行交错混合搅动,搅动后的粒子颗粒通过出料口排出筒体。
65.本实用新型的有益效果是:
66.本实用新型将造粒装置进行结构设计,将筒体结构设计为两段式结构,原料通过第一筒体内搅动进行横向传送,并进入第二筒体内进行二次搅动造粒成型;本装置通过将造粒工艺进行分级进行,原料进入不同直径的筒体结构内,并配合不同搅动杆的搅动形式,
将原料由一次加工的粗集料形成二次加工的粗集料,提高了粒子在造粒设备中的成型速率,造粒后的粒子均匀程度高,且整体装置的结构紧凑,造粒过程具有较高的制备速率。