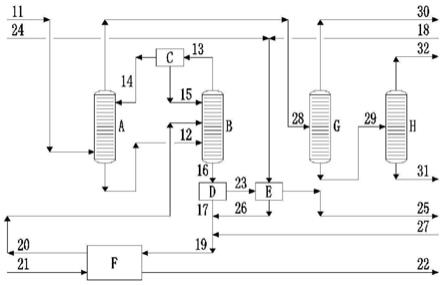
chppo注醇粗分离系统及粗分离方法
技术领域
1.本发明涉及一种异丙苯氧化chppo装置分离单元的分离系统及分离方法,尤其涉及一种chppo装置在粗环氧丙烷po塔精馏分离过程中采用注入有机醇以降低塔釜温度的粗分离系统及粗分离方法。
背景技术:2.环氧丙烷是石油化工的重要中间体之一,也是丙烯系列中的聚丙烯、环氧丙烷和丙烯腈三大衍生产品之一,大量用于生产聚醚多元醇制备聚氨酯塑料,还用于生产不饱和树脂和表面活性剂等,对化学工业及国民经济发展具有深远的影响。目前环氧丙烷已经生产的下游产品近百种,使环氧丙烷成为精细化工产品的重要原料。随着环氧丙烷用途的扩大和环氧丙烷下游产物用量的增长,环氧丙烷市场的需求越来越大。国内外环氧丙烷po生产技术主要有chpo法、po/sm联产法、po/tba联产法、hppo法和chppo法。其中chppo法是一种国际上已经基本成熟的环境友好、清洁绿色环氧丙烷工艺生产技术,该工艺方法的基本生产原理是先将异丙苯在一定温度和压力下用空气氧化生成过氧化氢异丙苯,过氧化氢异丙苯再与丙烯环氧化反应生产环氧丙烷和α,α
‑
二甲基苄醇,α,α
‑
二甲基苄醇经过脱水反应生成α甲基苯乙烯再经过加氢反应生成异丙苯返回再使用。因此chppo法工艺生产技术通过异丙苯、过氧化氢异丙苯、α,α
‑
二甲基苄醇、α甲基苯乙烯、异丙苯的转化而循环使用。
3.专利申请号201711239570.6公开了包括提供含环氧丙烷、萃取剂、以及包括1,2
‑
丙二醇的杂质的原料物流;所述原料物流进入具有第一再沸器的分离塔;所述分离塔在足以使萃取剂和1,2
‑
丙二醇形成共沸物的条件下;在所述分离塔侧线采出含萃取剂和1,2
‑
丙二醇共沸物的第一物流,塔釜得到含萃取剂的第二物流,塔顶得到含环氧丙烷的第三物流;所述第二物流的至少一部分进入萃取剂净化器,得到的气相轻组分第四物流返回所述分离塔,液相第一重组分杂质物流去后处理。该专利仅仅公开了采用萃取剂和1,2
‑
丙二醇形成共沸物的技术手段进行环氧丙烷纯化精制。
4.专利申请号201310568014.9公开了一种针对他汀类药物合成过程废液中甲基叔丁基醚
‑
四氢呋喃回收的双精馏塔串联分离提纯方法,将他汀类药物合成过程废液导入填料塔i中,控制塔顶温度30℃~40℃下进行精馏处理,从塔顶得到异戊二烯与水混合液,再进一步分层处理,得到异戊二烯;填料塔i的塔釜出料液通入填料塔ii中,控制塔顶温度50℃~65℃下进行精馏处理,从填料塔ii塔顶得到甲基叔丁基醚
‑
四氢呋喃混合溶剂。该专利工艺使用两个填料精馏塔串联进行,分离工艺能耗低,流程简单,可以提高溶剂甲基叔丁基醚
‑
四氢呋喃的回收利用率,在提高经济效益的同时,也可减少对环境的污染和破坏。该分离提纯方法仅仅公开了采用控制塔顶温度30~40℃下进行精馏处理,从塔顶得到异戊二烯与水混合液,再进一步分层处理,得到异戊二烯。
技术实现要素:5.发明目的:本发明第一目的是提供一种在系统内注入有机醇,能够降低粗环氧丙
烷分离塔塔釜温度,降低异丙苯损耗,提高环氧丙烷回收率的chppo注醇粗分离系统,本发明的第二目的是提供利用该系统进行chppo环氧化反应物注烃粗分离的方法。。
6.技术方案:本发明所述chppo注醇粗分离系统,包括从精馏塔、回收塔、油水分层罐、脱轻塔、脱重塔、油水分离罐、水洗器和萃取器;其中,所述回收塔分别与精馏塔、油水分层罐、油水分离罐和萃取器相连,脱轻塔分别与精馏塔和脱重塔相连,油水分离罐分别与水洗器和萃取器相连,水洗器与萃取器相连。
7.本发明所述chppo注醇粗分离方法,包括以下步骤:
8.a、环氧化反应产物进入精馏塔,分离得到精馏塔顶料和精馏塔釜料,精馏塔顶料进入脱轻塔,分离得到轻组分和脱轻塔釜料,轻组分送出系统外,脱轻塔釜料进入脱重塔,分离得到粗po产品和重组分分别送出系统外;
9.b、精馏塔釜料进入回收塔,分离得到回收塔顶料和回收塔釜料,回收塔顶料进入油水分层罐,分离得到分层罐油相和分层罐水相,分层罐油相进入精馏塔,分层罐水相返回回收塔;
10.c、回收塔釜料进入油水分离罐,分离得到分离罐油相和分离罐水相,分离罐油相进入水洗器,加入水和有机醇,分离得到水洗水和α,α
‑
二甲基苄醇,α,α
‑
二甲基苄醇送出系统外;
11.d、水洗水和分离罐水相混合,加入碱溶液碱洗得到平衡水,平衡水进入萃取器,用异丙苯萃取得到萃取相和含醇废水,含醇废水送出系统外,萃取相返回回收塔。
12.优选地的,所述分离方法的工艺参数如下:精馏塔的操作压力为0.12~0.24mpaa,塔顶操作温度为45~75℃,塔釜操作温度为80~110℃;回收塔的操作压力为0.08~0.20mpaa,塔顶操作温度为45~75℃,塔釜操作温度为70~110℃;脱轻塔的操作压力为0.26~0.39mpaa,塔顶操作温度为39~79℃,塔釜操作温度为51~91℃;脱重塔的操作压力为0.14~0.27mpaa,塔顶操作温度为35~75℃,塔釜操作温度为63~103℃;油水分层罐的操作压力为0.08~0.20mpaa,操作温度为45~75℃;油水分离罐的操作压力0.18~0.31mpaa,操作温度为70~110℃;水洗器的操作压力为0.16~0.29mpaa,操作温度为70~110℃,萃取级数为3~15级,溶剂比为2~10;萃取器的操作压力为0.14~0.27mpaa,操作温度为70~110℃,萃取级数为30~60级,溶剂比为0.4~8.8。
13.更优选的,所述分离方法的工艺参数如下:精馏塔的操作压力为0.14~0.22mpaa,塔顶操作温度为50~70℃,塔釜操作温度为85~105℃;回收塔的操作压力为0.10~0.18mpaa,塔顶操作温度为50~70℃,塔釜操作温度为75~105℃;脱轻塔的操作压力为0.28~0.37mpaa,塔顶操作温度为44~74℃,塔釜操作温度为56~86℃;脱重塔的操作压力为0.16~0.25mpaa,塔顶操作温度为40~70℃,塔釜操作温度为68~98℃;油水分层罐的操作压力为0.10~0.18mpaa,操作温度为50~70℃;油水分离罐的操作压力为0.20~0.29mpaa,操作温度为75~105℃;水洗器的操作压力为0.18~0.27mpaa,操作温度为75~100℃,萃取级数为5~13级,溶剂比为3~9;萃取器的操作压力为0.16~0.25mpaa,操作温度为75~100℃,萃取级数为35~55级,溶剂比为2.2~7.0。
14.最优选的,所述分离方法的工艺参数如下:精馏塔的操作压力为0.16~0.20mpaa,塔顶操作温度为55~65℃,塔釜操作温度为90~100℃;回收塔的操作压力为0.12~0.16mpaa,塔顶操作温度为55~65℃,塔釜操作温度为80~100℃;脱轻塔的操作压力为
0.30~0.35mpaa,塔顶操作温度为49~69℃,塔釜操作温度为61~81℃;脱重塔的操作压力为0.18~0.23mpaa,塔顶操作温度为45~65℃,塔釜操作温度为73~93℃;油水分层罐的操作压力为0.12~0.16mpaa,操作温度为55~65℃;油水分离罐的操作压力为0.22~0.27mpaa,操作温度为80~100℃;水洗器的操作压力为0.20~0.25mpaa,操作温度为80~90℃,萃取级数为7~11级,溶剂比为4~8;萃取器的操作压力为0.18~0.23mpaa,操作温度为80~90℃,萃取级数为40~50级,溶剂比为4.0~5.2。
15.分离步骤c中,所述有机醇注入位置可以是回收塔、者油水分离罐、水洗器或者萃取器。
16.分离步骤c中,所述有机醇为c1~c4有机醇中的一种或一种以上混合物。
17.所述的c1~c4有机醇为甲醇、乙醇、丙醇、异丙醇、叔丁醇中的一种或一种以上混合物。
18.分离步骤c中,所述加入水洗器中的水与有机醇的质量比为mw:ma=1.0:0.4~4.8。
19.分离步骤c中,所述水为一级脱盐水、二级脱盐水、蒸馏水、精制水、净化水、纯水中的一种。
20.发明人研究发现,在现有chppo装置分离环氧丙烷的工艺中,由于没有控制分离塔塔釜温度,使分离塔塔釜温度高达150~210℃,异丙苯发生热敏反应生成并异丙苯,存在分离塔塔釜温度高、异丙苯损失大、粗po回收率低的问题。因此,本发明拟对chppo装置环氧化反应产物分离系统及工艺流程进行优化,解决现有技术存在的问题。
21.有益效果:与现有技术相比,本发明具有如下显著优点:在公称能力为5~90万吨/年chppo生产装置中,将分离塔分成为精馏塔和回收塔双塔进行精馏分离,在精馏塔与回收塔之间设置油水分层罐,将分层罐油相送入精馏塔,分层罐水相作为回流液返回回收塔,以强化精馏塔的分离效率。在系统注入水和有机醇,水与有机醇的质量比为mw:ma=1.0:0.4~4.8,使回收塔带水带醇,以此降低回收塔塔釜温度、防止异丙苯生成并异丙苯、减少异丙苯损耗;回收塔塔釜温度从现有技术150~210℃降低到70~110℃,回收塔塔釜异丙苯生成并异丙苯导致并异丙苯增量从现有技术669~3392wt%降低到8.0~10.0wt%。并在回收塔塔釜设置油水分离罐、水洗器、萃取器,以此回收少量环氧丙烷和α,α
‑
二甲基苄醇,提高粗po塔环氧丙烷产品的回收率,精馏塔环氧丙烷产品的回收率从现有技术99.74~99.94wt%提高到99.95~99.97wt%,取得了较好的技术效果。
附图说明
22.图1为本发明的工艺流程图。
具体实施方式
23.下面结合附图对本发明的技术方案作进一步说明。
24.实施例1
25.以生产规模为5万吨/年chppo工业装置为例,采用本发明所述chppo注醇粗分离系统及粗分离方法,将分离塔分成为双精馏分离塔,前塔为精馏塔a,后塔为回收塔b。同时在精馏塔a与回收塔b之间设置油水分层罐c,将分层罐c油相和分层罐c水相作为回流液分别
送入精馏塔a和回收塔b以强化精馏塔的分离效率,并在回收塔b塔釜设置油水分离罐d、水洗器e、萃取器f,将水24和有机醇18注入水洗器e,异丙苯21注入萃取器,使回收塔b带水带醇,以此降低回收塔b塔釜温度、防止异丙苯生成并异丙苯、减少异丙苯损耗,回收少量环氧丙烷和α,α
‑
二甲基苄醇,提高环氧丙烷产品的回收率。精馏塔a选用粗po精馏塔,回收塔b选用粗po回收塔,水24选用二级脱盐水。所述有机醇18注入位置也可以是回收塔、油水分离罐或者萃取器。所述水24也可为一级脱盐水、蒸馏水、精制水、净化水、纯水中的任意一种。
26.如图1所示,本实施例工艺流程如下:来自界外已经脱除丙烯,含po、轻组分、重组分、异丙苯、α,α
‑
二甲基苄醇的环氧化反应产物11进入粗po精馏塔进行精馏分离,塔顶流出不含水和醇,含轻组分、重组分和po的精馏塔顶料28,塔釜流出含异丙苯、带水带醇的α,α
‑
二甲基苄醇和po的精馏塔釜料12;精馏塔顶料28进入脱轻塔g进行精馏分离,塔顶流出轻组分30送出界外,塔釜流出含重组分和粗po的脱轻塔釜料29;脱轻塔釜料29进入脱重塔h进行精馏分离,塔顶流出粗po产品32送出界外去po精制单元,塔釜流出重组分31送出界外;精馏塔釜料12进入粗po回收塔进行精馏分离,塔顶流出回收塔顶料13,塔釜流出回收塔釜料16;回收塔顶料13进入油水分层罐c中进行油水分离,分层罐油相14进入粗po精馏塔塔顶作为回流液继续精馏分离,分层罐水相15返回粗po回收塔塔顶作为回流液继续精馏分离;回收塔釜料16进入油水分离罐d进行油水分离,得到分离罐油相23和分离罐水相17;分离罐油相23进入水洗器e,加入二级脱盐水和有机醇18进行水洗处理,水洗后的含水的α,α
‑
二甲基苄醇25送出界外去氢解单元,水洗器e水洗后含醇的水洗水26和分离罐水相17混合,再与来自界外的碱溶液27混合并进行碱洗处理,得到平衡水19;平衡水19进入萃取器f,用来自界外的异丙苯21萃取分离,含少量po和α,α
‑
二甲基苄醇的萃取相20返回粗po回收塔,含醇的萃余相作为废水22送出界外回收有机醇后再进行环保处理达标排放。
27.本实施例工艺操作参数如下:粗po精馏塔的操作压力为0.15mpaa,塔顶操作温度为53℃,塔釜操作温度为87℃;粗po回收塔的操作压力为0.11mpaa,塔顶操作温度为54℃,塔釜操作温度为78℃;脱轻塔g的操作压力为0.29mpaa,塔顶操作温度为47℃,塔釜操作温度为58℃;脱重塔h的操作压力为0.17mpaa,塔顶操作温度为43℃,塔釜操作温度为70℃;油水分层罐c的操作压力为0.11mpaa,操作温度为54℃;油水分离罐d的操作压力为0.22mpaa,操作温度为78℃;水洗器e的操作压力为0.20mpaa,操作温度为78℃,萃取级数为6级,溶剂比为8.2;萃取器f的操作压力为0.18mpaa,操作温度为78℃,萃取级数为40级,溶剂比为5.6;加入水洗器e中的有机醇18为100wt%乙醇,二级脱盐水与有机醇18的质量比为mw:ma=1.0:4.2。
28.由此采用所述chppo注醇粗分离系统及分离方法,粗po回收塔塔釜操作温度从现有技术180℃降低到本发明78℃,粗po塔塔釜异丙苯生成并异丙苯导致并异丙苯增量从现有技术894wt%降低到本实施例8.4wt%,粗po精馏塔环氧丙烷产品的回收率从现有技术99.92wt%提高到本实施例99.96wt%,取得了较好的技术效果。
29.实施例2
30.同实施例1,仅仅公称能力和工艺操作参数改变,公称能力改为15万吨/年chppo商业化工业生产装置,工艺操作参数修改如下:粗po精馏塔的操作压力为0.21mpaa,塔顶操作温度为63℃,塔釜操作温度为98℃;粗po回收塔的操作压力为0.13mpaa,塔顶操作温度为60℃,塔釜操作温度为82℃;脱轻塔g的操作压力为0.35mpaa,塔顶操作温度为63℃,塔釜操作
温度为77℃;脱重塔h的操作压力为0.22mpaa,塔顶操作温度为61℃,塔釜操作温度为89℃;油水分层罐c的操作压力为0.13mpaa,操作温度为60℃;油水分离罐d的操作压力为0.26mpaa,操作温度为82℃;水洗器e的操作压力为0.24mpaa,操作温度为82℃,萃取级数为12级,溶剂比为4.8;萃取器f的操作压力为0.22mpaa,操作温度为82℃,萃取级数为52级,溶剂比为3.2;加入水洗器e中的有机醇18为100wt%异丙醇,二级脱盐水与有机醇18的质量比为mw:ma=1.0:3.0。
31.由此采用所述chppo注醇粗分离系统及分离方法,粗po回收塔塔釜操作温度从现有技术188℃降低到本发明82℃,粗po塔塔釜异丙苯生成并异丙苯导致并异丙苯增量从现有技术1338wt%降低到本实施例8.6wt%,粗po精馏塔环氧丙烷产品的回收率从现有技术99.90wt%提高到本实施例99.96wt%,取得了较好的技术效果。
32.实施例3
33.同实施例1,仅仅公称能力和工艺操作参数改变,公称能力改为30万吨/年chppo商业化工业生产装置,工艺操作参数修改如下:粗po精馏塔的操作压力为0.21mpaa,塔顶操作温度为63℃,塔釜操作温度为98℃;粗po回收塔的操作压力为0.15mpaa,塔顶操作温度为65℃,塔釜操作温度为91℃;脱轻塔g的操作压力为0.35mpaa,塔顶操作温度为63℃,塔釜操作温度为77℃;脱重塔h的操作压力为0.22mpaa,塔顶操作温度为61℃,塔釜操作温度为89℃;油水分层罐c的操作压力为0.15mpaa,操作温度为65℃;油水分离罐d的操作压力为0.26mpaa,操作温度为91℃;水洗器e的操作压力为0.24mpaa,操作温度为91℃,萃取级数为12级,溶剂比为4.8;萃取器操f的作压力为0.22mpaa,操作温度为91℃,萃取级数为52级,溶剂比为3.2;加入水洗器e中有机醇18为50wt%异丙醇和50wt%叔丁醇的混合物,二级脱盐水与有机醇18的质量比为mw:ma=1.0:1.4。
34.由此采用所述chppo注醇粗分离系统及分离方法,粗po回收塔塔釜操作温度从现有技术196℃降低到本发明91℃,粗po塔塔釜异丙苯生成并异丙苯导致并异丙苯增量从现有技术1943wt%降低到本实施例9.0wt%,粗po精馏塔环氧丙烷产品的回收率从现有技术99.87wt%提高到本实施例99.96wt%,取得了较好的技术效果。
35.实施例4
36.同实施例1,仅仅公称能力和工艺操作参数改变,公称能力改为90万吨/年chppo商业化工业生产装置,工艺操作参数修改如下:粗po精馏塔的操作压力为0.21mpaa,塔顶操作温度为63℃,塔釜操作温度为98℃;粗po回收塔的操作压力为0.17mpaa,塔顶操作温度为71℃,塔釜操作温度为102℃;脱轻塔g的操作压力为0.35mpaa,塔顶操作温度为63℃,塔釜操作温度为77℃;脱重塔h的操作压力为0.22mpaa,塔顶操作温度为61℃,塔釜操作温度为89℃;油水分层罐c的操作压力为0.17mpaa,操作温度为71℃;油水分离罐d的操作压力为0.26mpaa,操作温度为102℃;水洗器e的操作压力为0.24mpaa,操作温度为102℃,萃取级数为12级,溶剂比为4.8;萃取器f的操作压力为0.22mpaa,操作温度为102℃,萃取级数为52级,溶剂比为3.2;加入水洗器e中有机醇18为25wt%丙醇和75wt%叔丁醇的混合物,二级脱盐水与有机醇18的质量比为mw:ma=1.0:0.8。
37.由此采用所述chppo注醇粗分离系统及分离方法,粗po回收塔塔釜操作温度从现有技术204℃降低到本发明102℃,粗po塔塔釜异丙苯生成并异丙苯导致并异丙苯增量从现有技术2711wt%降低到本实施例9.6wt%,粗po精馏塔环氧丙烷产品的回收率从现有技术
99.82wt%提高到本实施例99.96wt%,取得了较好的技术效果。
38.实施例5
39.同实施例1,仅仅公称能力和工艺操作参数改变,公称能力改为30万吨/年chppo商业化工业生产装置,工艺操作参数修改如下:粗po精馏塔的操作压力为0.12mpaa,塔顶操作温度为45℃,塔釜操作温度为80℃;粗po回收塔的操作压力为0.08mpaa,塔顶操作温度为45℃,塔釜操作温度为70℃;脱轻塔g的操作压力为0.26mpaa,塔顶操作温度为39℃,塔釜操作温度为51℃;脱重塔h的操作压力为0.14mpaa,塔顶操作温度为35℃,塔釜操作温度为63℃;油水分层罐c的操作压力为0.08mpaa,操作温度为45℃;油水分离罐d的操作压力为0.18mpaa,操作温度为70℃;水洗器e的操作压力为0.16mpaa,操作温度为70℃,萃取级数为3级,溶剂比为10;萃取器f的操作压力为0.14mpaa,操作温度为70℃,萃取级数为30级,溶剂比为8.8;加入水洗器e中有机醇18为100wt%甲醇,二级脱盐水与有机醇18的质量比为mw:ma=1.0:4.8。
40.由此采用所述chppo注醇粗分离系统及分离方法,粗po回收塔塔釜操作温度从现有技术150℃降低到本发明70℃,粗po塔塔釜异丙苯生成并异丙苯导致并异丙苯增量从现有技术669wt%降低到本实施例8.0wt%,粗po精馏塔环氧丙烷产品的回收率从现有技术99.94wt%提高到本实施例99.97wt%,取得了较好的技术效果。
41.实施例6
42.同实施例1,仅仅公称能力和工艺操作参数改变,公称能力改为90万吨/年chppo商业化工业生产装置,工艺操作参数修改如下:粗po精馏塔的操作压力为0.24mpaa,塔顶操作温度为75℃,塔釜操作温度为110℃;粗po回收塔的操作压力为0.20mpaa,塔顶操作温度为75℃,塔釜操作温度为110℃;脱轻塔g的操作压力为0.39mpaa,塔顶操作温度为79℃,塔釜操作温度为91℃;脱重塔h的操作压力为0.27mpaa,塔顶操作温度为75℃,塔釜操作温度为103℃;油水分层罐c的操作压力为0.20mpaa,操作温度为75℃;油水分离罐d的操作压力为0.31mpaa,操作温度为110℃;水洗器e的操作压力为0.29mpaa,操作温度为110℃,萃取级数为15级,溶剂比为2;萃取器f的操作压力为0.27mpaa,操作温度为110℃,萃取级数为60级,溶剂比为0.4;加入水洗器e中有机醇18为100wt%丙醇,二级脱盐水与有机醇18的质量比为mw:ma=1.0:0.4。
43.由此采用所述chppo注醇粗分离系统及分离方法,粗po回收塔塔釜操作温度从现有技术210℃降低到本发明110℃,粗po塔塔釜异丙苯生成并异丙苯导致并异丙苯增量从现有技术3392wt%降低到本实施例10.0wt%,粗po精馏塔环氧丙烷产品的回收率从现有技术99.74wt%提高到本实施例99.95wt%,取得了较好的技术效果。
44.对比例1~6
45.设置对比例1~6,在公称能力30万吨/年chppo商业化工业生产装置中,分离塔未分成双精馏分离塔,且系统内也未注入有机醇和水,粗po塔塔釜操作温度为150~210℃,工艺步骤和其它工艺参数同实施例3,由此粗po塔塔釜并异丙苯增量为669~3392wt%,粗po回收率为99.74~99.94wt%,见表1。
46.表1改变粗po塔釜温度的并异丙苯增量及粗po回收率表
[0047][0048]
对比例7~12
[0049]
设置对比例7~12,在公称能力为30万吨/年chppo商业化工业生产装置中,分离塔未分成双精馏分离塔,且系统内也未注入有机醇和水,粗po塔操作压力为0.08~0.20mpaa,工艺步骤和其它工艺参数同实施例3,由此粗po塔塔釜并异丙苯增量为669~3392wt%,粗po回收率为99.74~99.94wt%,见表2。
[0050]
表2改变粗po塔压力的并异丙苯增量及粗po回收率表
[0051][0052]
对比例13~18
[0053]
设置对比例13~18,在公称能力为5~90万吨/年chppo商业化工业生产装置中,分离塔未分成双精馏分离塔,且系统内也未注入有机醇和水,粗po塔塔釜操作温度为182℃,工艺步骤和其他工艺参数同实施例3,由此粗po塔塔釜并异丙苯增量为989~990wt%,粗po回收率为99.86~99.93wt%,见表3。
[0054]
表3改变chppo工业生产装置公称能力的并异丙苯增量及粗po回收率表
[0055][0056]