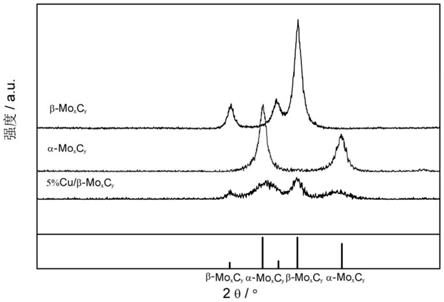
1.本发明涉及一种co2加氢制取甲醇的催化剂及其制备与应用,属于co2加氢催化转化技术领域。
背景技术:2.甲醇是一种重要的化工中间原料,可作为内燃机和燃料电池的燃料,随着不可再生能源的逐渐减少,甲醇作为一种可替代的化工原料可以合成多种化学品以及汽油等燃料。近年来随着分子筛催化剂,甲醇制烯烃(mto),甲醇制芳烃(mtg)等技术的发展,国际市场对于由甲醇所得燃料的需求呈快速增长(johnson,d.global methanol demand growth;ihs inc.,2016)。传统工业上制取甲醇采用合成气转化的方法,但是主要面临催化剂(cu/zno/al2o3)活性位在反应条件下容易烧结所导致的稳定差的问题,此外该过程的原料合成气的产出往往伴随着煤、天然气等化石资源的消耗以及其转化过程造成的co2排放和环境污染。
3.co2是大气中温室气体的主要成分,其产生来自于大量的化石燃料的燃烧,并导致了过去数十年中日益加深的全球气候变化。人类活动每年向大气中排放的co2近400亿吨,2019年大气中co2含量高达407ppm,在过去的40年中增长了20%。降低co2排放量无疑成为一个紧迫的课题。若将co2通过可再生能源转化为化工原料,则不仅可以解决co2过量排放的问题,还可以使co2成为一种替代传统化石燃料的新型碳源。co2分子具有化学惰性,但加入具有高自由能的h2分子作为反应物使得反应在热力学上变得容易,而h2如果采用电解水或光解水等可再生方式获取则可以使得整个过程具有环境和经济上的广阔前景。因此,采用co2催化加氢转化为甲醇是一种具有吸引力的降低co2排放和创造新的碳循环过程的方案。
4.目前co2加氢制甲醇主要采用负载型金属或金属氧化物催化剂,但由于co2的化学稳定性,活化温度较高,一般在250℃或以上。例如传统cu/zno/al2o3(science 352 2016 969
–
974),cu/zro2(j.am.chem.soc.138 201612440
–
12450),pd/zno(j.catal.343 2016 133
–
146)等。gmbh&lurgi gmbh在2010年采用催化剂cu/zno/al2o3在工业示范装置中实现了单程转化率40%下甲醇产率0.6kg ch3oh/l cat
·
h,该类型催化性能常常受cu的表面化学状态的改变而影响,并且在反应产生大量水的条件下容易团聚而失活。在温度稍高的条件下,产物中甲醇的选择性降低,转而生成副产物co。近年采用过渡金属改性的cu
‑
zn材料也得到了广泛的研究,例如cuznga
‑
水滑石在co2转化率20%下,实现了甲醇收率0.59kg ch3oh/l cat
·
h,但甲醇选择性仅为50%左右(acs catal.2018,8,4390
‑
4401)。而采用贵金属负载的pd/ceo2催化剂甲醇选择性达到92%,但co2转化率不理想(j.catal.,1994,150,217
–
220)。鉴于该反应在低温下热力学有利这一特性,设计一种可在较低温度下高效活化co2和h2,并具有较高co2转化率和甲醇选择性的催化剂是实现co2加氢制甲醇工业应用的紧迫问题。有文献指出,co2分子吸附于moc表面时处于弯曲构型,非常有利于其活化,但所生成的co不易脱附会继续解离而加氢生成甲烷。通过掺杂金属原子等方法修饰其表面结构从而抑制其解离碳氧键能力过强的特点,并适度提高解离h2的能力是提高低温co2加氢制甲醇
性能的有效途径。
技术实现要素:5.本发明所要解决的技术问题是:提供一种能在较低温度下高效活化co2和h2,并具有较高co2转化率和甲醇选择性的催化剂。
6.为了解决上述技术问题,本发明的技术方案通过以下技术方案实现:
7.一种碳化钼催化剂,其特征在于,所述碳化钼催化剂的通式为m/mo
x
c
y
,其中m为cu和pt元素中的至少一种,其占催化剂的质量分数为0.02
‑
0.05%,mo
x
c
y
为α或β相碳化钼。
8.本发明还提供了上述碳化钼催化剂的制备方法,其特征在于,将氯铂酸或硝酸铜分别溶解于去离子水中,与moo3粉末混合后旋蒸干燥,所得粉末ch4与h2的混合气体中吹扫,然后碳化,即得碳化钼催化剂,将其在o2与n2的混合气体中钝化后保存。
9.优选地,所述ch4与h2的混合气体中ch4的体积百分比为20%,吹扫时的流速为150ml/min。
10.优选地,所述碳化的工艺参数为:将温度从室温以5℃/min的速度升温至400℃,然后以0.5℃/min的速度升温至700℃,保持1小时。
11.优选地,所述o2与n2的混合气体中o2的体积百分比为0.5%,钝化时间为220min。
12.优选地,所述催化剂为pt/α
‑
mo
x
c
y
时,采用氯铂酸为前体;所述催化剂为cu/β
‑
mo
x
c
y
时,采用硝酸铜为前体。
13.上述催化剂在反应性能评价前原位还原,还原温度为500℃,还原时间为1h,氢气空速为30000ml/g/h,还原压力为0.1mpa。
14.本发明还提供了一种基于碳化钼催化剂的二氧化碳加氢制甲醇的方法,将上述碳化钼催化剂用于二氧化碳加氢制甲醇,反应条件为:反应温度200
‑
300℃,反应压力5mpa,原料气的空速为12000ml/g/h。
15.优选地,所述原料气由co2与h2以体积比1:3组成。
16.本发明提供一种基于碳化钼的新型金属负载型催化剂的制备方案,并在固定床反应器进行反应性能评价,具有反应温度低,甲醇时空收率高的特点,其中铂基催化剂在200℃,5mpa和空速12000ml/g cat
·
h条件下,co2转化率为9.8%,而铜基催化剂在相同条件下,甲醇时空收率可达72.6g ch3oh/kg cat
·
h,相比于已有专利报告的结果,可在更低温度实现相同性能,该系列催化剂的发明为后续低温工业应用提供了广泛前景。
17.与现有技术相比,本发明所提供的用于co2加氢制甲醇的催化剂有益效果主要体现在以下方面:
18.(1)本发明将金属pd与cu掺杂入传统的碳化钼催化剂中,保持碳化钼材料co2吸附解离能力强的特点,同时抑制碳氧键的过度解离而生成甲烷,提高甲醇的选择性。达到在低温下合成甲醇的目的。
19.(2)本发明的催化剂具有在低温下较好的催化性能,所制备催化剂pt/α
‑
mo
x
c
y
中pt含量为2%,cu/β
‑
mo
x
c
y
中cu的含量为5%,前者在200℃下实现co2转化率10%,而后者在200℃甲醇时空收率达72.6g ch3oh/kg cat
·
h。
20.(3)本发明催化剂在反应中,通过对反应温度的调控,在200℃
‑
300℃的范围内,反应转化率和甲醇选择性可以分别得到调控,在高温下甲醇选择性降低而甲烷选择性提高,
有利于实现工业生产中催化剂在不同温度下实现不同的功能。
21.(4)催化剂制备过程简单、易于重复,可大规模制备。
附图说明
22.图1为实施例1
‑
3所得的cu负载量为5%的cu/β
‑
mo
x
c
y
催化剂和β
‑
mo
x
c
y
以及实施例4
‑
6涉及的纯相的α
‑
mo
x
c
y
的xrd谱图。
具体实施方式
23.为使本发明更明显易懂,兹以优选实施例,并配合附图作详细说明如下。
24.本发明制备的mo
x
c
y
中x、y不限定于自然数,也可以为分数、非自然数,例如0.1、0.3、0.5
……
等,本发明不对x、y的比例进行研究,根据现有技术可知,两者比例和数值可以为任意自然数或非自然数的正数。实施例所得的产品可以通过测试得知两者之间的比例,但该数据这并不影响本发明技术方案的实施,因此本发明中并未提供相关比例数据。本发明仅对碳化钼类催化剂在制备甲醇中的性能进行研究。
25.实施例1
26.称取1g moo3与40ml去离子水混合,超声分散,称取190mg硝酸铜并溶解于moo3的分散液中,旋蒸干燥后将粉末移入管式炉中,在20%ch4/h2气氛中以150ml/min流速吹扫,开始程序升温碳化(室温
→
400℃,5℃/min,400
→
700℃,0.5℃/min,保持1小时),最后在含有体积百分比0.5%的氧气、其余为氮气的混合气体气氛下钝化220min后得到质量浓度5%cu/β
‑
mo
x
c
y
。
27.将所得催化剂在反应性能评价前原位还原,还原温度为500℃,还原时间为1h,氢气空速为30000ml/g/h,还原压力为0.1mpa。还原后炉温降到200℃,反应条件为:反应温度为200℃,反应压力为5mpa,催化剂装量为100mg,原料气空速为12000ml/g/h,反应原料气由co2和h2组成,co2与h2的体积比为1:3。活性评价结果见表1。
28.实施例2
29.称取1g moo3与40ml去离子水混合,超声分散,称取190mg硝酸铜并溶解于moo3的分散液中,旋蒸干燥后将粉末移入管式炉中,在20%ch4/h2气氛中以150ml/min流速吹扫,开始程序升温碳化(室温
→
400℃,5℃/min,400
→
700℃,0.5℃/min,保持1小时),最后在含有体积百分比0.5%的氧气、其余为氮气的混合气体气氛下钝化220min后得到质量浓度5%cu/β
‑
mo
x
c
y
。
30.将所得催化剂在反应性能评价前原位还原,还原温度为500℃,还原时间为1h,氢气空速为30000ml/g/h,还原压力为0.1mpa。还原后炉温降到260℃,反应条件为:反应温度为260℃,反应压力为5mpa,催化剂装量为100mg,原料气空速为12000ml/g/h,反应原料气由co2和h2组成,co2与h2的体积比为1:3。活性评价结果见表1。
31.实施例3
32.称取1g moo3与40ml去离子水混合,超声分散,称取190mg硝酸铜并溶解于moo3的分散液中,旋蒸干燥后将粉末移入管式炉中,在20%ch4/h2气氛中以150ml/min流速吹扫,开始程序升温碳化(室温
→
400℃,5℃/min,400
→
700℃,0.5℃/min,保持1小时),最后在含有体积百分比0.5%的氧气、其余为氮气的混合气体气氛下钝化220min后得到质量浓度5%cu/
β
‑
mo
x
c
y
。
33.将所得催化剂在反应性能评价前原位还原,还原温度为500℃,还原时间为1h,氢气空速为30000ml/g/h,还原压力为0.1mpa。还原后炉温降到300℃,反应条件为:反应温度为300℃,反应压力为5mpa,催化剂装量为100mg,原料气空速为12000ml/g/h,反应原料气由co2和h2组成,co2与h2的体积比为1:3。活性评价结果见表1。
34.实施例4
35.称取1g moo3与40ml去离子水混合,超声分散,移取5.6ml氯铂酸溶液(1.834
×
10
‑2mol/l)并溶解于moo3的分散液中,旋蒸干燥后将粉末移入管式炉中,在20%ch4/h2气氛中以150ml/min流速吹扫,开始程序升温碳化(室温
→
400℃,5℃/min,400
→
700℃,0.5℃/min,保持1小时),最后在含有体积百分比0.5%的氧气、其余为氮气的混合气体气氛下钝化220min后得到质量浓度2%pt/α
‑
mo
x
c
y
。
36.将所得催化剂在反应性能评价前原位还原,还原温度为500℃,还原时间为1h,氢气空速为30000ml/g/h,还原压力为0.1mpa。还原后炉温降到200℃,反应条件为:反应温度为200℃,反应压力为5mpa,催化剂装量为100mg,原料气空速为12000ml/g/h,反应原料气由co2和h2组成,co2与h2的体积比为1:3。活性评价结果见表1。
37.实施例5
38.称取1g moo3与40ml去离子水混合,超声分散,移取5.6ml氯铂酸溶液(1.834
×
10
‑2mol/l)并溶解于moo3的分散液中,旋蒸干燥后将粉末移入管式炉中,在20%ch4/h2气氛中以150ml/min流速吹扫,开始程序升温碳化(室温
→
400℃,5℃/min,400
→
700℃,0.5℃/min,保持1小时),最后在含有体积百分比0.5%的氧气、其余为氮气的混合气体气氛下钝化220min后得到质量浓度2%pt/α
‑
mo
x
c
y
。
39.将所得催化剂在反应性能评价前原位还原,还原温度为500℃,还原时间为1h,氢气空速为30000ml/g/h,还原压力为0.1mpa。还原后炉温降到260℃,反应条件为:反应温度为260℃,反应压力为5mpa,催化剂装量为100mg,原料气空速为12000ml/g/h,反应原料气由co2和h2组成,co2与h2的体积比为1:3。活性评价结果见表1。
40.实施例6
41.称取1g moo3与40ml去离子水混合,超声分散,移取5.6ml氯铂酸溶液(1.834
×
10
‑2mol/l)并溶解于moo3的分散液中,旋蒸干燥后将粉末移入管式炉中,在20%ch4/h2气氛中以150ml/min流速吹扫,开始程序升温碳化(室温
→
400℃,5℃/min,400
→
700℃,0.5℃/min,保持1小时),最后在含有体积百分比0.5%的氧气、其余为氮气的混合气体气氛下钝化220min后得到质量浓度2%pt/α
‑
mo
x
c
y
。
42.将所得催化剂在反应性能评价前原位还原,还原温度为500℃,还原时间为1h,氢气空速为30000ml/g/h,还原压力为0.1mpa。还原后炉温降到300℃,反应条件为:反应温度为300℃,反应压力为5mpa,催化剂装量为100mg,原料气空速为12000ml/g/h,反应原料气由co2和h2组成,co2与h2的体积比为1:3。活性评价结果见表1。
43.表1各实施例的催化性能数据
44.[0045][0046]
图1为实施例1
‑
3所得的cu负载量为5%的cu/β
‑
mo
x
c
y
催化剂和β
‑
mo
x
c
y
以及实施例4
‑
6涉及的纯相的α
‑
mo
x
c
y
的xrd谱图。