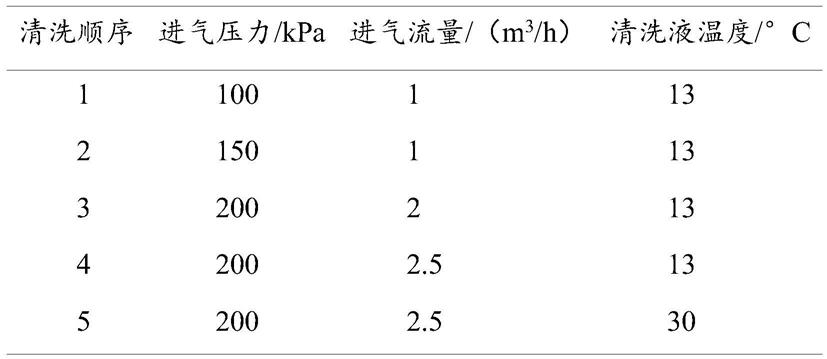
1.本发明涉及渗透膜处理技术领域,更具体的说是涉及一种热电厂废弃反渗透膜的清洗再生装置及清洗再生方法。
背景技术:2.反渗透技术在火力发电厂锅炉水制备领域是目前处理最为高效、应用最为广泛的水脱盐技术。然而,复合型聚酰胺膜在运行一定时间后,都无法避免地产生膜污染现象。一般商业低压反渗透膜的使用寿命约为3至5年,超过使用寿命后每年被废弃的膜元件数以百万计,这不仅给热电厂带来高昂的换膜及废膜处理成本,且可能带来巨大的环境风险。尽管废弃的反渗透膜自身截留率、过滤性能等有所下降,但其依然保持完整的主体结构,经过适当处理,可以在产水水质要求不高的场景中循环利用。
3.膜清洗是废弃反渗透膜循环利用前处理的关键一步。通过膜清洗降低废膜的跨膜压差,可以降低废膜循环利用的运行成本,提高废膜循环利用的经济性。在现有常规清洗工艺中,清洗剂大多是从膜进水端进入膜内,清洗剂与膜面污染物接触反应后,随水流从膜浓水端冲出膜外。但是对主要集中在膜进水端的有机物和微生物污染等,采用清洗剂从膜浓水端反向进入膜内(即清洗剂正洗),使污染物即时从膜进水端冲出膜外,可以防止污染物随清洗液顺流发生粘附再次污染膜表面。张利利等发明了清洗液既能从进水端进入,也能从浓水端进入的双向反渗透清洗装置,但与之相关的文献报道较少。另外,气液两相清洗工艺中,气体的通入增加了膜面剪切力和清洗液的湍流程度,使污染层疏松脱落而达到更好的清洗效果。气液两相清洗在微滤、超滤膜清洗中应用较为成熟,然而针对卷式反渗透膜清洗的相关研究较少。
4.因此,如何针对卷式反渗透膜清洗提供一套合理的清洗装置达到最佳的清洗效果使其能够再生使用是本领域技术人员亟待解决的问题。
技术实现要素:5.有鉴于此,本发明提供了一种热电厂废弃反渗透膜的清洗装置及清洗方法,此清洗再生工艺采用物理清洗与化学清洗相结合的方式对废弃的反渗透元件进行离线清洗,通过清洗液正反洗相结合以及气液两相清洗相结合的工艺方式对废弃反渗透膜元件进行深度清洗,清洗效果好,清洗效率高,可实现废弃反渗透膜元件的再生利用。
6.为实现上述目的,本发明采用如下技术方案:
7.一种热电厂废弃反渗透膜的清洗再生装置,包括膜组件,还包括:与所述膜组件连通的化学清洗组件、清水冲洗组件和气洗组件;
8.所述化学清洗组件包括依次连通的清洗水箱、管路一、增压泵、管路二、管路三、管路四、管路五、管路六和管路七,所述管路二连通所述膜组件的进水端,所述管路三连通所述膜组件的浓水端;所述管路一进水端设置有阀 v1、出水端通过阀v2连通所述管路二,所述增压泵设置在所述管路一上,所述管路三通过阀v6与所述管路四连通,所述管路四通过
阀v10与所述管路五连通,所述管路五出水口连通所述清洗水箱且出水端设置有阀v11,所述管路六进水端连通所述管路一且设置有阀v3、出水端连通所述管路四,所述管路七进水端连通所述膜组件的进水端且设置有阀v5、出水端连通所述管路五;
9.所述清水冲洗组件包括冲洗水箱、管路八、管路九和排水管一,所述管路八的进水端连通所述冲洗水箱且设置有阀v12、出水端连通所述管路一,所述管路九的进水端连通所述管路五、出水端连通所述冲洗水箱且设置有阀 v13,所述排水管一通过阀v8连通所述管路三和地沟;
10.所述气洗组件包括压缩气源和管路十,所述管路十的进气端连通所述压缩气源、出气端连通所述管路二且设置有阀v4;
11.所述冲洗水箱、所述清洗水箱均连通有补水管和地沟。
12.进一步的,还包括性能测试组件;
13.所述性能测试组件包括测试水箱、管路十一、管路十二、管路十三、压力变送器、电磁流量计、电导率仪、涡街流量计、排水管二和截止阀,所述管路十一的进水端连通所述测试水箱且设置有阀v14、出水端连通所述管路一,所述管路十二的进水端连通所述管路五、出水端连通所述测试水箱且设置有阀v15,所述管路十三的进水端连通所述膜组件的产水端、出水端通过阀v7连通所述管路四,所述压力变送器和所述电磁流量计依次设置于所述管路三上位于进水端与所述排水管的连接点之间,所述排水管二通过阀v9连通所述管路十三和地沟,所述涡街流量计和所述电导率仪依次设置于所述管路十三上,所述截止阀设置于所述管路三位于所述压力变送器和电磁流量计之间。
14.进一步的,所述测试水箱连接有电加热器一。
15.进一步的,所述清洗水箱连接有电加热器二。
16.进一步的,所述管路一上设置有保安过滤器,所述保安过滤器设置于所述增压泵和管路六与管路一的连接点之间。
17.进一步的,所述管路二上设置有电导率仪和压力变送器。
18.本发明还提供了一种基于如上技术方案所述的再生装置的热电厂废弃反渗透膜的清洗再生方法,包括以下步骤:
19.步骤一:药剂配制:在清洗水箱中配置清洗药剂,待用;
20.步骤二:洗涤
21.正洗:开启阀v1、阀v2、阀v6、阀v10、阀v11和增压泵,气洗还需打开压缩气源和阀v4,其余阀门关闭,正洗,正洗结束后关闭所有阀门和增压泵;
22.反洗:打开阀v1、阀v3、阀v6、阀v5、阀v11和增压泵,进行反洗,反洗结束后关闭所有阀门和增压泵;
23.步骤三:清水冲洗
24.打开阀v12、阀v2、阀v8和增压泵进行冲洗,冲洗结束后关闭所有阀门和增压泵;
25.步骤四:性能测试
26.打开阀v14、阀v2、阀v6、阀v7、阀v10、阀v15和增压泵,关闭其他阀门,在测试水箱中配置2000mg/l的nacl溶液作为测试液,调整膜组件浓水端截止阀开关程度及增压泵的频率,使膜组件产水量固定在1.73m3/h,回收率固定在15%,测试记录进水压力、跨膜压差、脱盐率,满足要求即得再生膜,
27.其中,计算公式如下:
28.跨膜压差计算公式:
29.dp=p
f
‑
p
conc
30.式中p
f
为进水压力,p
conc
为浓水压力,单位为kpa;
31.脱盐率计算公式:
32.sr=(us
f
‑
us
p
)/us
f
×
100%
33.式中sr为脱盐率,us
f
为进水电导,us
p
产水电导,单位为us/cm。
34.优选的,所述清洗药剂为0.1wt%的naoh溶液、 0.1wt%naoh+0.025wt%sds
‑
na溶液或0.2wt%hcl,具体正反洗包括以下步骤:
35.(8.1)在清洗水箱中配置清洗药剂溶液后,开启阀v1、阀v2、阀v6、阀v10、阀v11和增压泵,其余阀门关闭,正洗1h,正洗结束后关闭所有阀和增压泵;
36.(8.2)打开阀v1、阀v3、阀v6、阀v5、阀v11和增压泵,反洗1h,反洗结束后关闭增压泵;
37.(8.3)静置浸泡2h,之后关闭所有阀门;
38.(8.2)重复步骤(8.1)和(8.2)一次,之后关闭所有阀门和增压泵。
39.优选的,所述清洗药剂为0.1wt%naoh+压缩气,具体洗涤包括以下步骤:
40.(9.1)在清洗水箱中配置0.1wt%naoh清洗药剂溶液后,开启阀v1、阀v2、阀v6、阀v10、阀v11、阀v4、增压泵和压缩气源,正洗1h,关闭增压泵和压缩气源;
41.(9.2)静置浸泡2h后,打开压缩气源和增压泵再次正洗1h,之后关闭增压泵和压缩气源及所有阀门。
42.优选的,所述压缩气源的进气量为1
‑
1.5m3/h,进气压力为80
‑
150kpa
43.经由上述的技术方案可知,与现有技术相比,本发明公开提供了一种热电厂废弃反渗透膜的清洗装置及清洗方法,通过优化装置结构以及清洗工艺参数,达到最佳效果,采用不同的清洗剂正向和反向清洗相结合的清洗方式进行清洗,对降低废膜的跨膜压差有明显效果,且对膜脱盐率损伤较低,经过清洗后的废膜元件产水量约为新膜的1.5
‑
2.5倍,脱盐率可达95
‑
97.5%,可在低能耗、高通量、低脱盐率要求的场景中循环使用,具有较高的环保价值。
附图说明
44.为了更清楚地说明本发明实施例或现有技术中的技术方案,下面将对实施例或现有技术描述中所需要使用的附图作简单地介绍,显而易见地,下面描述中的附图仅仅是本发明的实施例,对于本领域普通技术人员来讲,在不付出创造性劳动的前提下,还可以根据提供的附图获得其他的附图。
45.图1为本发明一种热电厂废弃反渗透膜的清洗装置的整体结构图;
46.图2为本发明实施例中naoh对废膜清洗效果图;
47.图3为本发明实施例中naoh+sds
‑
na对废膜清洗效果图;
48.图4为本发明实施例中hcl对废膜清洗效果图;
49.图5为本发明实施例中naoh+气源对废膜清洗效果图;
50.图6为本发明实施例中naoh、naoh+sds
‑
na、hcl、naoh+气源清洗废膜后的产水量对
比图。
具体实施方式
51.下面将结合本发明实施例中的附图,对本发明实施例中的技术方案进行清楚、完整地描述,显然,所描述的实施例仅仅是本发明一部分实施例,而不是全部的实施例。基于本发明中的实施例,本领域普通技术人员在没有做出创造性劳动前提下所获得的所有其他实施例,都属于本发明保护的范围。
52.如附图1所示,一种热电厂废弃反渗透膜的清洗再生装置,包括膜组件1,还包括:与所述膜组件1连通的化学清洗组件、清水冲洗组件和气洗组件;
53.所述化学清洗组件包括依次连通的清洗水箱21、管路一22、增压泵23、管路二24、管路三25、管路四26、管路五27、管路六28和管路七29,所述管路二24连通所述膜组件1的进水端,所述管路三25连通所述膜组件1的浓水端;所述管路一22进水端设置有阀v1、出水端通过阀v2连通所述管路二24,所述增压泵23设置在所述管路一22上,所述管路三25通过阀v6与所述管路四26连通,所述管路四26通过阀v10与所述管路五27连通,所述管路五27出水口连通所述清洗水箱21且出水端设置有阀v11,所述管路六 28进水端连通所述管路一22且设置有阀v3、出水端连通所述管路四26,所述管路七29进水端连通所述膜组件1的进水端且设置有阀v5、出水端连通所述管路五27;
54.所述清水冲洗组件包括冲洗水箱31、管路八32、管路九33和排水管一 34,所述管路八32的进水端连通所述冲洗水箱31且设置有阀v12、出水端连通所述管路一22,所述管路九33的进水端连通所述管路五27、出水端连通所述冲洗水箱21且设置有阀v13,所述排水管一34通过阀v8连通所述管路三25和地沟;
55.所述气洗组件包括压缩气源41和管路十42,所述管路十42的进气端连通所述压缩气源41、出气端连通所述管路二24且设置有阀v4;
56.所述冲洗水箱21、所述清洗水箱31均连通有补水管和地沟。
57.还包括性能测试组件;
58.所述性能测试组件包括测试水箱51、管路十一52、管路十二53、管路十三54、压力变送器55、电磁流量计56、电导率仪57、涡街流量计58、排水管二59和截止阀60,所述管路十一52的进水端连通所述测试水箱51且设置有阀v14、出水端连通所述管路一52,所述管路十二53的进水端连通所述管路五27、出水端连通所述测试水箱51且设置有阀v15,所述管路十三54的进水端连通所述膜组件1的产水端、出水端通过阀v7连通所述管路四26,所述压力变送器55和所述电磁流量计56依次设置于所述管路三25上位于进水端与所述排水管一34的连接点之间,所述排水管二59通过阀v9连通所述管路十三54和地沟,所述涡街流量计58和所述电导率仪57依次设置于所述管路十三54上,所述截止阀60设置于所述管路三25位于所述压力变送器55 和电磁流量计56之间。
59.在一些具体改进的方案中,所述测试水箱51连接有电加热器一7。
60.在一些具体改进的方案中,所述清洗水箱31连接有电加热器二8。
61.在一些具体改进的方案中,所述管路一22上设置有保安过滤器9,所述保安过滤器9设置于所述增压泵23和管路六28与管路一22的连接点之间。
62.在一些具体改进的方案中,所述管路二24上设置有电导率仪一241和压力变送器
一242。
63.本发明的技术方案基于上述装置进行清洗测试,具体清洗再生对象为由蓝星东丽公司生产的型号为tm720d
‑
400的高化学耐久性、高脱盐率、高通量反渗透膜元件。该膜元件于2016年在某热电厂作为锅炉补给水的预处理投入使用,在系统中的装填位置为首段首支,运行4年后更换。该热电厂的水源类型为地表水,反渗透膜前的预处理流程为高密度沉淀池
→
空气擦洗滤池
→
碟片过滤器
→
超滤。预处理过程中,在高密度沉淀池连续投加混凝剂pac;在高密度沉淀池进水管以及uf进水管分别连续投加氧化杀菌剂naclo;在反渗透进水母管上连续投加还原剂以及阻垢剂。
64.具体的清洗方法如下:
65.化学清洗:按清洗方式不同共分为三类:正洗,气液冲洗及反洗。正洗时,将阀门v1、v2、v6、v10、v11打开,其余阀门关闭,此时清洗剂经过增压泵加压后从膜元件的进水端进入废膜中,经过膜元件后从浓水端回流至清洗水箱中。气液冲洗时阀门v4打开,其余阀门开关状态与正洗保持一致,此时压缩空气与清洗剂混合后进入膜元件;反洗时将阀门v1、v3、v6、v5、 v11打开,其余阀门关闭,此时清洗剂从浓水端流入废膜后从进水端流出至清洗水箱中。循环清洗时通过调节增压泵频率维持循环流量在9m3/h~10m3/h,进水压力在80kpa~90kpa左右。
66.清水冲洗:打开阀门v12、v2、v8,关闭其余阀门,此时清水从废膜进水端流入,经过废膜后从浓水端流出排入地沟;
67.膜元件性能测试:打开阀门v14、v2、v6、v7、v10、v15,关闭其他阀门。根据东丽手册上同型号膜元件性能测试条件[5]:配置2000mg/lnacl 溶液作为测试液,调整浓水端截止阀开关程度及高压泵频率,使膜元件产水量固定在1.73m3/h,回收率固定在15%,加热测试液温度至25℃;进行测试记录进水压力、跨膜压差、脱盐率等实验数据。
[0068]
化学清洗按所选药剂及清洗方式不同可分为4类:0.1wt%naoh,0.1wt% naoh+0.025wt%sds
‑
na,0.2wt%hcl,0.1%wtnaoh+气洗。
[0069]
0.1wt%naoh清洗清洗流程为先正反洗各1h后增压泵停止供压,使膜元件静置浸泡2h,再重复正反洗各1h,合计完整清洗一次所需时间为6h。
[0070]
0.1wt%naoh+0.025%sds
‑
na洗和0.2%hcl洗时,清洗流程与0.1%naoh 相同。
[0071]
0.1wt%naoh+气洗时,清洗流程为先正洗1h,静置浸泡2h,再正洗1h,合计完整清洗一次所需时间为4h。气液清洗参数如表1所示:
[0072]
表1气液清洗参数
[0073][0074]
依据进气压力、进气流量、清洗液温度的变化,结合清洗时间,探究最合适的清洗参数。
[0075]
总清洗流程顺序为:0.1wt%naoh正反洗、0.1wt%naoh+0.025wt% sds
‑
na正反洗、0.2wt%hcl正反洗、0.1wt%naoh+气洗。
[0076]
一、数据处理:
[0077]
1)数据标准化
[0078]
膜元件的表观性能受进水组成、进水压力、温度和回收率的影响,例如:温度每下降1℃,产水量就会降低约3%,这属于正常现象。每次测试膜元件性能时无法保证测试时的测试液浓度、进水压力、温度等条件完全一致。为了区分这类正常现象与膜元件性能真正的变化,应对测试数据进行标准化处理。以同型号新膜元件的初始性能作为基准性能进行标准化,这样做考虑了测试参数的影响,更能反映膜元件的真实性能与基准性能的差异。本研究利用东丽提供的专业标准化软件toraytrak软件对数据进行标准化,包括标准化产水量,标准化脱盐率,标准化压差3项。
[0079]
2)计算公式
[0080]
跨膜压差计算公式:
[0081]
dp=p
f
‑
p
conc
[0082]
式中p
f
为进水压力,p
conc
为浓水压力,单位为kpa;
[0083]
脱盐率计算公式:
[0084]
sr=(us
f
‑
us
p
)/us
f
×
100%
[0085]
式中sr为脱盐率,us
f
为进水电导,us
p
产水电导,单位为us/cm;二、测试结果:
[0086]
二、测试结果:各个清洗药剂的清洗效果如附图2
‑
6所示,
[0087]
(一)naoh对废膜清洗效果
[0088]
naoh溶液能与油脂、蛋白、藻类等微生物污垢、胶体污垢、绝大多数有机污垢发生反应,使沉积物松动、乳化、分散。使用0.1wt%naoh对废膜进行首次清洗过程中,正洗时清洗液没有明显变化,由正洗转入反洗后不久,很快清洗液明显变浑浊,表明污染物被冲出膜外,有较理想的清洗效果;用同浓度naoh再次清洗废膜过程中,无论是正洗还是反洗,清洗液都没有明显变化,预示着清洗效果不理想。
[0089]
经naoh清洗后,废膜的跨膜压差和脱盐率的变化如图2所示。首次清洗6h后,膜元
件跨膜压差下降约10%,继续清洗6h后,跨膜压差几乎不变,跨膜压差反映的清洗效果与清洗过程中清洗液的变化是一致的。首次清洗后,膜元件脱盐率降低了1.1%,再次清洗后,脱盐率进一步下降,降低了0.8%。
[0090]
综上可知:(1)采用清洗液正反洗相结合的方式效果比较理想,由正洗转入反洗时,清洗液明显变浑浊,表明有污染物被冲出膜外;(2)采用0.1wt% naoh进行清洗,对降低废膜跨膜压差有一定的效果,但同时会引起废膜脱盐率的降低;(3)另外采用naoh清洗时延长清洗时间对继续降低跨膜压差没有效果,反倒会进一步损害膜元件脱盐率,因此清洗时间不宜过长。
[0091]
(二)naoh+sds
‑
na对废膜的清洗效果
[0092]
sds
‑
na作为表面活性剂能降低分子表面张力,提高膜表面亲水性,因而搭配naoh可有效去除微生物及有机污染物。采用naoh+sds
‑
na对废膜首次进行清洗时,同碱洗过程类似,由正洗转入反洗不久,清洗液泡沫上粘附有大量的黄色固体物质,清洗液也由清澈变得浑浊;第二次清洗时,清洗液泡沫上仍粘附有部分黄色固体物质,清洗液变浑浊;第三次清洗时,清洗液泡沫上基本没有黄色物质,清洗液依然变浑浊;第四次清洗时,清洗液泡沫和清洗液都没有明显变化。
[0093]
经naoh+sds
‑
na清洗后,废膜元件的跨膜压差和脱盐率变化如图3所示,以最后一次naoh洗的数据作为0点的初始数据。经过三次清洗,废膜的跨膜压差稳步降低,从初始值的47kpa,依次降低6.4%、6.8%、5.1%,最终降至39kpa,合计降低了17%;第四次清洗后,跨膜压差相比上一次没能继续降低。废膜的脱盐率在清洗过程中基本维持不变,甚至还略微升高,经过 18h累计清洗后,脱盐率相比碱洗结束时回升约0.3%,恢复至95.6%。
[0094]
综上可知:(1)采用0.1wt%naoh+0.025wt%sds
‑
na对废膜有较理想的清洗效果,经清洗后废膜的跨膜压差显著降低,废膜的脱盐率清洗前后维持不变,甚至略有恢复。(2)比较单纯naoh清洗以及naoh+sds
‑
na清洗结果可以发现naoh+sds
‑
na相对于单纯naoh是较温和清洗剂,能够在降低跨膜压差的同时不损害废膜的脱盐率,因此是更为推荐的清洗剂。(3)采用naoh+sds
‑
na对废膜进行清洗时,需要保证足够长的清洗时间,在本实验中清洗加浸泡时间建议不少于18h。
[0095]
(三)hcl对废膜的清洗效果
[0096]
酸性试剂主要用于去除沉积于膜表面的无机盐沉淀,能使mg
2+
、ca
2+
等无机盐垢溶解。用0.2wt%hcl溶液对废膜进行的三次清洗过程中,清洗液均没有明显变浑浊的现象。酸洗后废膜元件的跨膜压差和脱盐率变化如图4所示,以最后一次naoh+sds
‑
na清洗的结果作为0点的初始数据。经过三次 hcl酸洗后,废膜的跨膜压差进一步小幅下降,相比酸洗前总共下降了约 7.7%;而废膜的脱盐率经酸洗后得到了部分恢复,脱盐率由酸洗前的95.9%恢复至97%,恢复后的脱盐率与清洗开始前废膜的脱盐率相当。可见,酸洗对膜的脱盐率的恢复效果较好。这是因为当低交联度的聚酰胺膜接触强碱性溶液时,填塞于膜孔之间的低聚物在强碱性条件下发生溶解,引起膜孔增大、膜面膨胀,从而导致膜的脱盐率暂时降低。这种现象一般是可逆的,碱洗后用清水长时间持续冲洗可以适当恢复膜的脱盐率;而碱洗后再用酸洗则可以加速膜的脱盐率的恢复。
[0097]
(四)气液两相清洗对废膜的清洗效果
[0098]
汽水脉冲是以水为介质,向管道内注入压缩空气作为推动力,通过空气的压缩扩
张使汽水混合流体在管道内形成冲击力和振荡波,剧烈的絮流使原本的水流剪切力增大,能有效剥离附着于膜上和网格上的污染物。第一次气液清洗时,清洗液明显变浑浊,而后的几次气液清洗时,清洗液均没有明显变化。气液两相清洗对废膜的清洗效果如图5所示,使用最后一次0.2wt%hcl 清洗结果作为参照数据。经过第一次气液清洗后,废膜压差进一步降低至31kpa,与同型号新膜压差几乎相同;脱盐率略微升高0.3%,升高至97.3%,与清洗前废膜的脱盐率一致。第二次气液清洗时,提高了压缩空气的进气压力;第三、第四次气液清洗时,同时提高了压缩空气的进气压力和进气量;第五次气液清洗时,对清洗液进行加热升温。随后的几次气液清洗过程中废膜的跨膜压差及脱盐率几乎没有变化。
[0099]
综上可知,(1)采用0.1wt%naoh以及1m3/h,100kpa的压缩空气相结合的气液两相清洗能够进一步降低废膜的跨膜压差,直至与新膜的跨膜压差相同;(2)提升压缩空气的进气压力、进气量、清洗时间及清洗液温度,废膜性能并未得到进一步改善。
[0100]
图6所示的是在上述组合清洗过程中废膜元件的产水量变化,最终经过气液清洗后废膜元件的标准化产水量为4.14m3/h,为同型号新膜的2.4倍。
[0101]
综上,(1)针对本实验以有机污染为主的废弃反渗透膜,以0.1wt%naoh、 0.1wt%naoh+0.025wt%sds
‑
na、0.1wt%hcl作为清洗剂,采用清洗剂正向和反向清洗相结合的清洗方式进行清洗,对降低废膜的跨膜压差有明显效果,且对膜脱盐率损伤较低。
[0102]
(2)进一步采用0.1wt%naoh辅以100kpa,1m3/h压缩空气的气液两相清洗的方式对废膜进行清洗,可将跨膜压差降至与新膜同等水平。
[0103]
(3)清洗前,废膜称重质量为16.45kg;清洗后,称重质量为14.9kg,接近新膜质量;说明清洗后污染物从废膜上剥落,清洗效果显著。
[0104]
(4)经过清洗之后,废膜元件产水量约为新膜的2.4倍,脱盐率为97.3%左右,可在低能耗、高通量、低脱盐率要求的场景中循环使用。
[0105]
本说明书中各个实施例采用递进的方式描述,每个实施例重点说明的都是与其他实施例的不同之处,各个实施例之间相同相似部分互相参见即可。对于实施例公开的装置而言,由于其与实施例公开的方法相对应,所以描述的比较简单,相关之处参见方法部分说明即可。
[0106]
对所公开的实施例的上述说明,使本领域专业技术人员能够实现或使用本发明。对这些实施例的多种修改对本领域的专业技术人员来说将是显而易见的,本文中所定义的一般原理可以在不脱离本发明的精神或范围的情况下,在其它实施例中实现。因此,本发明将不会被限制于本文所示的这些实施例,而是要符合与本文所公开的原理和新颖特点相一致的最宽的范围。