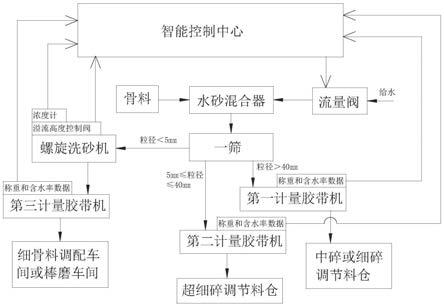
1.本发明属于机制砂石加工技术领域,具体涉及一种机制砂石中细碎车间湿筛干破制砂工艺的控制方法。
背景技术:2.通过干法脱泥处理的半成品矿石中,含有的泥土主要是颗粒大于脱泥筛剔除的粒级或粘附强的细微颗粒。通过中碎破碎后,大颗粒泥土一般会粉碎成细小颗粒,其水溶性增强。故高品质机制砂石制备工艺中细碎车间,采用湿法再次脱泥,确保进入超细碎车间中间产品质量达到控制要求。但是湿法脱泥会再次引入水,在后续的超细碎破碎中,含水率过高会导致破碎效率低下,现有技术中缺乏有效的质量控制手段,含水率缺少监控,将直接影响超细碎破碎效率和质量,不能满足高品质机制砂石的加工要求。
技术实现要素:3.为解决上述技术问题,本发明提供了一种机制砂石中细碎车间湿筛干破制砂工艺的控制方法,实现工艺流程参数的智能控制,掺配骨料采用计量胶带机称重,掺配用水量采用流量阀控制,可有效控制水砂掺合比例,控制在最佳范围,获得最优的脱水脱泥效果。
4.本发明通过以下技术方案得以实现:
5.一种机制砂石中细碎车间湿筛干破制砂工艺的控制方法,包括以下步骤:来自于中细碎车间破碎后的骨料输送至水砂混合器与水混合,然后经一筛后由计量胶带机送至车间各处,计量胶带机上设置含水率检测仪,水砂混合器进水管设置有流量阀,智能控制中心的控制系统中预设水砂混合的质量比控制范围、含水率控制范围及智能调控表,并实时采集计量胶带机称重及含水率数据,按水砂质量比控制流量阀给水流量,当水砂质量比超出控制范围时,进行预警,通知人员进行处理;当水砂质量比不合理,会造成粉砂稀释水量不足或富余,水量不足,则会导致泥粉粘附性强,导致中间产品脱泥效果不佳或筛透率下降。水量过多,则会脱水效果不佳。掺配骨料采用计量胶带机称重,掺配用水量采用流量阀控制,可有效控制水砂掺合比例,控制在最佳范围,获得最优的脱水脱泥效果,并实时判断含水率是否超标,含水率超标时按智能调控表进行调控,仍不能满足各参数的控制范围时进行预警,通知人员进行处理,实时对骨料含水率进行监控,保证后续超细碎破碎效率和质量,满足高品质机制砂石的加工要求。
6.优选地,所述水砂质量比控制范围为35%~40%,其筛分脱水脱泥效果最佳。
7.所述骨料经一筛后,粒径大于40mm的大骨料经第一计量胶带机返回中碎或细碎调节料仓;粒径大于等于5mm且小于等于40mm的中骨料经第二计量胶带机送至超细调节料仓;粒径小于5mm的细骨料送至螺旋洗砂机,再经第三计量胶带机输送至细骨料调配车间或棒磨车间;智能控制中心的控制系统中分别预设大骨料和中骨料输送量与总进料量重量占比及其控制范围,实时采集第一计量胶带机、第二计量胶带机和第三计量胶带机称重,并计算大骨料和中骨料的重量占比,超出控制范围时,按智能调控表进行预警。通过均衡均质破碎
调控,中细碎破碎的产品粒级分布波动较小,如果一筛设备正常,则分级出的各级比例波动较小。故可通过对监测各级受料胶带机输送量,判断筛分设备运行状况及中间产品质量,并实时监控,及时处理异常情况。
8.所述智能控制中心的控制系统中预设中骨料的含水率控制范围为<3%,当监控中骨料的含水率≥3%时,控制流量阀降低给水量,直至含水率<3%为止,当给水量比例降至水砂质量比的下限时,含水率依然高于3%,则预警,通知人员进行处理。
9.当所述大骨料与总进料量重量占比高于控制范围上限时,预警项目为筛孔堵塞或激振力不足;当所述大骨料与总进料量重量占比低于控制范围下限时,预警项目为筛孔磨损或破裂漏料。
10.所述大骨料与总进料量重量占比的控制范围为
±
3%。
11.当所述中骨料与总进料量重量占比高于控制范围上限时,预警项目为上层筛孔磨损或破裂漏料或本层筛网堵孔;当所述中骨料与总进料量重量占比低于控制范围下限时,预警项目为上层筛网堵孔或本层筛网磨损或破裂漏料。
12.所述中骨料与总进料量重量占比的控制范围为
±
3%。
13.所述螺旋洗砂机中设置有溢流高度控制阀和浓度计,智能控制中心的控制系统中预设螺旋洗砂机流水浓度和溢流量及其控制范围,当螺旋洗砂机清洗后的湿砂输送量升高,导致湿砂含水率升高、溢流量降低、流水浓度降低超过控制范围时,预警洗砂机溢流高度过高,脱泥状况不佳;当湿砂输送量降低,导致湿砂含水率降低、溢流量升高、流水浓度升高超过控制范围时,预警洗砂机溢流高度过低,脱泥状况不佳。在料源均质的状况下,洗砂机溢流槽带走的泥粉量波动较小,故通过监控洗砂机溢流浓度,可间接判断料源与掺配用水比例。同时也可通过工艺性试验确定螺旋洗砂机溢流高度,获得粉砂带走量最小且脱泥效果满足运行要求溢流高度。
14.所述湿砂输送量的控制范围为
±
3%,湿砂含水率的控制范围为
±
2%,螺旋洗砂机流水浓度控制范围为
±
1%,溢流量控制范围为
±
3%。
15.本发明的有益效果在于:
16.与现有技术相比,实现工艺流程参数的智能控制,掺配骨料采用计量胶带机称重,掺配用水量采用流量阀控制,可有效控制水砂掺合比例,控制在最佳范围,获得最优的脱水脱泥效果。实时对骨料含水率进行监控,保证后续超细碎破碎效率和质量,满足高品质机制砂石的加工要求。通过监测一筛后各级受料胶带机输送量,判断筛分设备运行状况及中间产品质量,并实时监控,及时处理异常情况。通过监控洗砂机溢流浓度,间接判断料源与掺配用水比例,提高水砂参合的控制效果,同时控制溢流高度,在脱泥效果满足运行要求的条件下获得粉砂带走量最小的有利效果,能降低后续粉砂含量调控成本。
附图说明
17.图1是本发明的结构及控制连接的示意图。
具体实施方式
18.下面进一步描述本发明的技术方案,但要求保护的范围并不局限于所述。
19.如图1所示,一种机制砂石中细碎车间湿筛干破制砂工艺的控制方法,包括以下步
骤:来自于中细碎车间破碎后的骨料输送至水砂混合器与水混合,然后经一筛后由计量胶带机送至车间各处,计量胶带机上设置含水率检测仪,水砂混合器进水管设置有流量阀,智能控制中心的控制系统中预设水砂混合的质量比控制范围、含水率控制范围及智能调控表,并实时采集计量胶带机称重及含水率数据,按水砂质量比控制流量阀给水流量。经中细碎破碎,泥团粉碎细小颗粒,破碎后的骨料与高压水冲进入水砂混合器中,在经过料斗、溜槽后,细小颗粒(<2mm以下颗粒)和水充分溶合,形成水砂混合物。水砂混合物在一筛第一段筛网(约占1/3筛网面积)时,迅速分离,能有效保证脱泥效果。后半段筛网(约占2/3筛网面积)主要功能为不含粉泥的骨料分级及脱水,故能有效保证脱水效果。
20.所述骨料经一筛后,粒径大于40mm的大骨料经第一计量胶带机返回中碎或细碎调节料仓;粒径大于等于5mm且小于等于40mm的中骨料经第二计量胶带机送至超细调节料仓;粒径小于5mm的细骨料送至螺旋洗砂机,经螺旋洗砂机清洗后的细骨料在行业内称为湿砂,湿砂再经第三计量胶带机输送至细骨料调配车间或棒磨车间;智能控制中心的控制系统中分别预设大骨料和中骨料输送量与总进料量重量占比及其控制范围,并实时采集第一计量胶带机和第二计量胶带机称重计算大骨料和中骨料的重量占比,超出控制范围时,按智能调控表进行预警。
21.细骨料在螺旋洗砂机中,经过螺旋搅拌,泥粉水溶性佳、沉淀速度慢的细小颗粒,与水一起从螺旋洗砂机溢流口溢出。所述螺旋洗砂机中设置有溢流高度控制阀和浓度计,智能控制中心的控制系统中预设螺旋洗砂机流水浓度和溢流量及其控制范围。
22.智能控制中心监控上述各参数,当任一参数出现异常时,按智能调控表方案进行调控,仍不能满足各参数的控制范围时进行预警,通知人员进行处理。智能控制中心监控参数见表1,智能调控及预警参数表方案见表2。
23.表1湿筛干破工序检测参数表
[0024][0025]
表2智能调控及预警参数表
[0026][0027]
主要监控参数及原理:
[0028]
①
水砂质量比:当水砂质量比不合理,会造成粉砂稀释水量不足或富余,水量不足,则会导致泥粉粘附性强,导致中间产品脱泥效果不佳或筛透率下降。水量过多,则会脱水效果不佳。生产性试验表明,在当稀释用水量在进料量质量比的35%~40%时,其筛分脱水脱泥效果最佳。故采用掺配骨料采用计量胶带机计量,中水量采用流量控制阀。则可有效控制水砂掺合比例。
[0029]
②
分级比例监控:通过均衡均质破碎调控,中细碎破碎的产品粒级分布波动较小,如果一筛设备正常,则分级出的各级比例波动较小。故可通过对监测各级受料胶带机输送量,判断筛分设备运行状况及中间产品质量。
[0030]
③
洗砂机溢流水浓度:在料源均质的状况下,洗砂机溢流槽带走的泥粉量波动较小,故通过监控洗砂机溢流浓度,可间接判断料源与中水比例。同时也可通过工艺性试验确定螺旋洗砂机溢流高度,获得粉砂带走量最小且脱泥效果满足运行要求溢流高度。
[0031]
另外由于不同的矿山原料质量差异较大,因此,各控制参数可根据生产性试验作小范围的调整。
[0032]
本发明提供的一种机制砂石中细碎车间湿筛干破制砂工艺的控制方法,实现工艺流程参数的智能控制,掺配骨料采用计量胶带机称重,掺配用水量采用流量阀控制,可有效控制水砂掺合比例,控制在最佳范围,获得最优的脱水脱泥效果。实时对骨料含水率进行监
控,保证后续超细碎破碎效率和质量,满足高品质机制砂石的加工要求。通过监测一筛后各级受料胶带机输送量,判断筛分设备运行状况及中间产品质量,并实时监控,及时处理异常情况。通过监控洗砂机溢流浓度,间接判断料源与掺配用水比例,提高水砂参合的控制效果,同时控制溢流高度,在脱泥效果满足运行要求的条件下获得粉砂带走量最小的有利效果,能降低后续粉砂含量调控成本。控制参数根据生产性试验作小范围的调整,以消除不同的矿山原料质量差异。