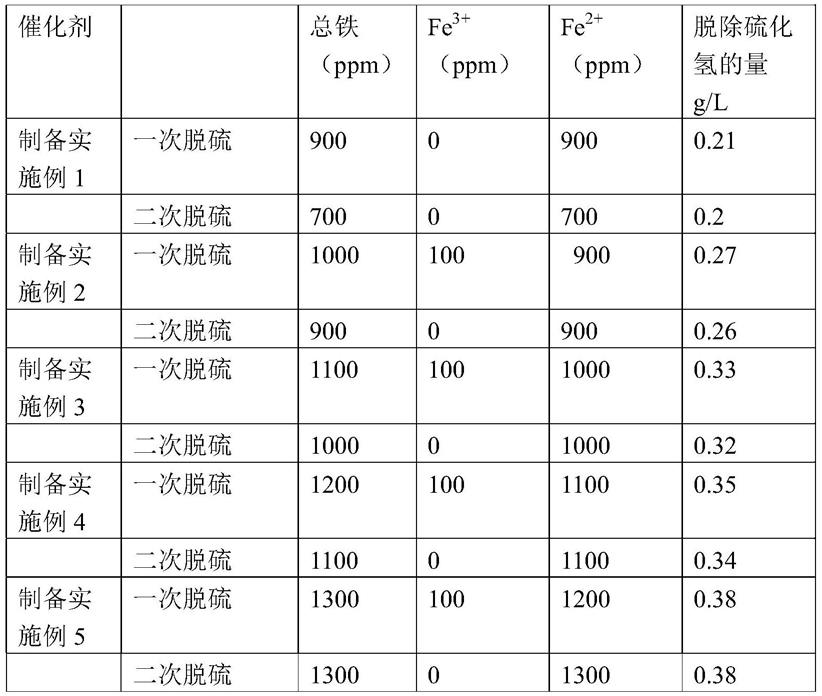
1.本发明属于气体净化领域,具体涉及一种复合型脱硫催化剂。
背景技术:2.以煤、焦炭、天然气和石油等为原料生产的化工原料气中均含不同浓度的h2s气体,高浓度h2s的存在不仅污染环境、腐蚀设备管道、影响化工产品的质量,而且会造成后续工艺生产中的催化剂中毒失活,因此h2s脱除技术受到高度重视。目前,将煤气中的硫化氢吸收主要是通过pds法,部分企业通过络合铁法。
3.pds法是以碳酸钠或氨为碱源,以双核酞菁钴基磺酸盐(pds)为催化剂的湿式脱硫工艺,基本原理是将煤气中的硫化氢吸收至溶液中与碳酸钠或氨反应生成硫氢化钠或硫氢化氨,以催化剂作为载氧体,使其氧化成单质硫,从而达到脱硫的目的。但是pds法反应速度慢,副盐生成量多。
4.络合铁法脱硫是利用不同的配体,将三价铁离子进行络合配位,形成配合物。硫化氢与脱硫液中碳酸钠反应生成硫氢化钠,利用三价铁离子的氧化性将其氧化成硫单质,三价铁离子被还原成二价铁离子。二价铁离子与空气中的氧反应再转化为三价铁离子循环使用。缺点是反应速率太快,硫磺生成快,加上目前的脱硫塔填料选型,造成硫磺在填料上逐渐附着,从而引起系统阻力上升。
技术实现要素:5.本发明对脱硫催化剂使用过程中的问题进行改进,提供一种复合型脱硫催化剂及其制备方法,所述复合型脱硫催化剂适用于脱除焦炉煤气中的硫化氢气体。
6.一方面,本发明提供了一种复合型脱硫催化剂,其包含双核酞菁钴基磺酸盐(pds)和络合铁催化剂,其中,双核酞菁钴基磺酸盐(pds)与络合铁催化剂中所含的铁(fe)的质量比为0.02~3:1,优选地为0.1~1.2:1。
7.在具体实施方式中,所述络合铁催化剂包含:可溶性铁盐、铁盐络合剂、稳定剂、硫磺改性剂、缓蚀剂。
8.在具体实施方式中,所述复合型脱硫催化剂的形式为水溶液。
9.在具体实施方式中,所述水溶液的ph值为8~9。
10.在具体实施方式中,所述可溶性铁盐为选自氯化铁、硫酸铁、硝酸铁、铁铵盐、乙二胺四乙酸铁钠盐和含水氧化铁中的一种或几种。
11.在具体实施方式中,所述铁盐络合剂为选自乙二胺四乙酸二钠、柠檬酸钠、亚氨基二琥珀酸四纳、羟基亚乙基二膦酸、氨三乙酸和羟乙基乙二胺三乙酸中的一种或几种,特别地为乙二胺四乙酸二钠。
12.在具体实施方式中,所述稳定剂为选自无水葡萄糖、麦芽糖中的一种或两种。
13.在具体实施方式中,所述硫磺改性剂为选自聚苯乙烯磺酸钠、甘油、丙二醇、聚乙二醇、聚乙二醇醚中的一种或几种,特别地为聚乙二醇。
14.在具体实施方式中,所述缓蚀剂为选自钼酸钠、锑酸钠、硅酸盐、锌盐、铬酸盐、咪唑类中的一种或几种,特别地为钼酸钠。
15.在具体实施方式中,所述复合型脱硫催化剂包含以下各成分:
16.pds:0.1
‑
5重量份;可溶性铁盐:5
‑
15重量份;铁盐络合剂:8
‑
24重量份;稳定剂:1
‑
10重量份;硫磺改性剂:0.1
‑
2重量份;缓蚀剂:0.01
‑
1重量份。
17.在具体实施方式中,所述复合型脱硫催化剂包含以下各成分:
18.pds:0.1
‑
5重量份;氯化铁:5
‑
15重量份;乙二胺四乙酸二钠:8
‑
24重量份;无水葡萄糖:1
‑
10重量份;聚乙二醇:0.1
‑
2重量份;钼酸钠:0.01
‑
1重量份。
19.在具体实施方式中,所述复合型脱硫催化剂包含以下各成分:
20.pds:0.5
‑
3重量份;氯化铁:7
‑
15重量份;乙二胺四乙酸二钠:12
‑
24重量份;无水葡萄糖:3
‑
10重量份;聚乙二醇:0.5
‑
2重量份;钼酸钠:0.4
‑
1重量份。
21.在具体实施方式中,所述复合型脱硫催化剂包含以下各成分:
22.水:1000重量份;pds:0.1
‑
5重量份;可溶性铁盐:5
‑
15重量份;铁盐络合剂:8
‑
24重量份;稳定剂:1
‑
10重量份;硫磺改性剂:0.1
‑
2重量份;缓蚀剂:0.01
‑
1重量份。
23.在具体实施方式中,所述复合型脱硫催化剂包含以下各成分:
24.水:1000重量份;pds:0.1
‑
5重量份;氯化铁:5
‑
15重量份;乙二胺四乙酸二钠:8
‑
24重量份;无水葡萄糖:1
‑
10重量份;聚乙二醇:0.1
‑
2重量份;钼酸钠:0.01
‑
1重量份。
25.在具体实施方式中,所述复合型脱硫催化剂包含以下各成分:
26.水:1000重量份;pds:0.5
‑
3重量份;氯化铁:7
‑
15重量份;乙二胺四乙酸二钠:12
‑
24重量份;无水葡萄糖:3
‑
10重量份;聚乙二醇:0.5
‑
2重量份;钼酸钠:0.4
‑
1重量份。
27.另一方面,本发明提供一种上述复合型脱硫催化剂的制备方法,所述方法包括:
28.向水中先加入铁盐络合剂、再加入可溶性铁盐、依次加入稳定剂、硫磺改性剂以及缓蚀剂,待所有物质混合均匀,再加入pds。
29.在具体实施方式中,所述方法进一步包括将上述得到的混合物溶液用碱性物质调节至ph值至8~9。
30.在具体实施方式中,所述碱性物质可选自碳酸钠、碳酸氢钠、氢氧化钠和氢氧化钾中的一种或几种,特别地,所述碱性物质为碳酸钠。
31.再一方面,本发明提供了上述复合型脱硫催化剂在焦炉煤气或化工原料气脱硫中的应用。
32.再一方面,本发明提供一种用于煤气或化工原料气的脱硫装置,其包括以下处理单元:
33.有机硫反应器,其用于去除预冷煤气或化工原料气中的有机硫;
34.脱硫塔,其与有机硫反应器通过管线连接,在所述脱硫塔中容纳上述复合型脱硫催化剂,所述脱硫塔用于脱除煤气或化工原料气中的无机硫(例如硫化氢);
35.反应槽,其与脱硫塔通过管线连接,用于容纳从脱硫塔流出的脱硫液;
36.再生器,其通过管线分别与反应槽以及脱硫塔连接,并通过注入的空气用于复合型脱硫催化剂的再生,在所述再生器中,经过再生的脱硫催化剂从其顶部溢流并进入脱硫塔中循环使用;以及
37.泡沫槽,其与再生器通过管线连接,用于再生器顶部浮选出的硫磺的处理。
38.又一方面,本发明提供一种采用上述脱硫装置对煤气或化工原料气进行连续脱硫的方法,所述方法包括以下步骤:
39.1).有机硫去除:通过有机硫反应器去除煤气或化工原料气中的有机硫;
40.2).无机硫去除:去除有机硫的煤气或化工原料气进入脱硫塔,并通过脱硫塔中的复合型脱硫催化剂处理脱除其中的无机硫(如硫化氢);
41.3).催化剂的再生及循环使用,即再生后返回脱硫塔用于脱除无机硫,该步骤包括:
42.在脱硫塔中经过脱硫过程的脱硫液从脱硫塔流入反应槽中,并被送入(例如通过泵送)再生器中;
43.流入再生器的脱硫液在再生器中与空气接触再生后被送入脱硫塔中循环使用;
44.再生器中顶部浮选出的硫磺进入泡沫槽中处理。
45.有益效果
46.本发明人考虑了在脱硫过程中,络合铁催化剂反应速率快,而pds反应速率慢,因此创造性地将二者结合使得脱硫反应速度适中。另外,考虑到生成物硫磺在塔内沉积造成阻力,因此控制适中的反应速度可以避免硫磺在塔内沉积,并在后续工序中将其分离。
47.因此,本发明提供的复合型脱硫催化剂具有以下优异效果:反应速率稳定,脱硫效果良好,副盐生成量低,生成的硫磺颜色正,另外,缓蚀剂的选用大大降低了脱硫催化剂本身对脱硫设备的腐蚀,长周期运行压力降稳定在较低水平。
附图说明
48.图1为使用本技术的复合型脱硫催化剂的小试试验装置流程图。
49.图2为使用本技术的复合型脱硫催化剂的中试侧线工艺流程图。
50.附图标记说明:
51.1:有机硫反应器
52.2:脱硫塔
53.3:反应槽
54.4:再生器
55.5:泡沫槽
56.6:脱硫液泵
[0057]6’
:泡沫泵
具体实施方式
[0058]
下面通过实施例来证明本发明复合型脱硫催化剂的效果,但不局限于以下实施方式,其中采用的原料、设备和方法,如无特殊说明,均为本领域常规的原料、设备和方法。
[0059]
制备实施例1
[0060]
取1kg水为溶剂,先加入乙二胺四乙酸二钠12g,充分搅拌溶解后,再加入氯化铁7.5g待完全溶解后,依次加入稳定剂无水葡萄糖3g、硫磺改性剂聚乙二醇0.75g、缓蚀剂钼酸钠0.4g,待所有物质完全混合均匀,再加入pds 3g,最后用碱性物质碳酸钠调节溶液ph值到8~9,即可配制复合脱硫催化剂。
[0061]
制备实施例2
[0062]
取1kg水为溶剂,先加入乙二胺四乙酸二钠15.2g,充分搅拌溶解后,再加入氯化铁9.5g待完全溶解后,依次加入稳定剂无水葡萄糖3.8g、硫磺改性剂聚乙二醇0.95g、缓蚀剂钼酸钠0.51g,待所有物质完全混合均匀,再加入pds 2.4g,最后用碱性物质碳酸钠调节溶液ph值到8~9,即可配制复合脱硫催化剂。
[0063]
制备实施例3
[0064]
取1kg水为溶剂,先加入乙二胺四乙酸二钠18.4g,充分搅拌溶解后,再加入氯化铁11.5待完全溶解后,依次加入稳定剂无水葡萄糖4.6g、硫磺改性剂聚乙二醇1.15g、缓蚀剂钼酸钠0.61g,待所有物质完全混合均匀,再加入pds 1.8g,最后用碱性物质碳酸钠调节溶液ph值到8~9,即可配制复合脱硫催化剂。
[0065]
制备实施例4
[0066]
取1kg水为溶剂,先加入乙二胺四乙酸二钠21.6g,充分搅拌溶解后,再加入氯化铁13.5g待完全溶解后,依次加入稳定剂无水葡萄糖5.4g、硫磺改性剂聚乙二醇1.35g、缓蚀剂钼酸钠0.72g,待所有物质完全混合均匀,再加入pds 1.2g,最后用碱性物质碳酸钠调节溶液ph值到8~9,即可配制复合脱硫催化剂。
[0067]
制备实施例5
[0068]
取1kg水为溶剂,先加入乙二胺四乙酸二钠24g,充分搅拌溶解后,再加入氯化铁15g待完全溶解后,依次加入稳定剂无水葡萄糖6g、硫磺改性剂聚乙二醇1.5g、缓蚀剂钼酸钠0.8g,待所有物质完全混合均匀,再加入pds0.6g,最后用碱性物质碳酸钠调节溶液ph值到8~9,即可配制复合脱硫催化剂。
[0069]
本发明采用络合铁与pds复配的方式形成一种新的脱硫催化剂,通过调整二者的比例来筛选出最优的复配比例。为了进一步说明本发明的脱硫效果,对制备实施例中的脱硫催化剂进行性能测试。
[0070]
实施例1:小试性能测试
[0071]
1.实验条件
[0072]
硫化氢浓度6000ppm(平衡气为氮气)的实验气体
[0073]
实验气体流量150ml/min
[0074]
复合脱硫催化剂ph值8.5
‑9[0075]
2.实验过程
[0076]
(1)一次脱硫:
[0077]
分别用水将制备实施例1
‑
5中制得的脱硫催化剂稀释3倍后得到脱硫液,取100ml置于250ml圆底烧瓶中,将6000ppm硫化氢气体通过鼓泡吸收的形式,以160ml/min的速度注入250ml圆底烧瓶中,通过硫化氢检测仪对出口硫化氢进行在线检测,直至能够检测到出口硫化氢为止,记录通气时间。试验时通过ph计检测玻璃容器内的脱硫液的ph,通过分液漏斗的方式使得实验过程中脱硫液的ph维持在初始ph。试验结束通过以下公式计算单位体积脱硫催化剂饱和脱除硫化氢的质量s。实验结束后取样测总铁浓度、三价铁及二价铁的浓度。小试评价装置流程图如图1。
[0078]
计算公式:
[0079]
(2)脱硫后再生:
[0080]
接仪表空气同样以鼓泡吸收的形式对一次脱硫后的脱硫液进行再生,待脱硫液的颜色恢复到一次脱硫之前的颜色时,观察烧瓶内出现淡黄色颗粒产生,说明稀释后的脱硫催化剂已经再生完全。停止通入仪表空气,对再生后的脱硫液进行过滤分离,滤饼上的淡黄色颗粒即为硫磺,滤液为再生后的脱硫液。取样分析再生后脱硫液的总铁浓度、三价铁及二价铁的浓度。
[0081]
(3)再生后脱硫液再次脱硫:
[0082]
再生后的脱硫液100ml置于250ml圆底烧瓶中,将6000ppm硫化氢气体通过鼓泡吸收的形式,以160ml/min的速度注入250ml圆底烧瓶中,通过硫化氢检测仪对出口硫化氢进行在线检测,直至能够检测到出口硫化氢为止,记录通气时间。试验时通过ph计检测玻璃容器内的脱硫液的ph,通过分液漏斗的方式使得实验过程中脱硫液的ph维持在初始ph。实验结束通过以上公式计算单位体积脱硫催化剂饱和脱除硫化氢的质量。实验结束后取样测总铁浓度、三价铁及二价铁的浓度。
[0083]
3、实验结果:
[0084]
表1:小试试验结果
[0085][0086]
从以上表1中的数据可以看出,催化剂中总铁含量与pds的比值从实施例1至5逐渐增加,从试验结果看出,二者比值越高,脱除硫化氢的效果越好,表中的试验数据显示脱硫液经过一次脱硫、二次脱硫后总铁浓度变化不大,说明催化剂中络合铁比较稳定,没有发生铁离子沉淀。
[0087]
实施例2:中试侧线性能评价:
[0088]
以河北某焦化厂2500m3/h焦炉煤气脱硫侧线进行催化剂的性能评价。焦炉煤气中硫化氢的含量为3
‑
4g/m3,侧线工艺流程如图2所示。预冷后煤气先经过有机硫反应器1去掉有机硫后,再进入脱硫塔2,用如上制备实施例中制备的复配催化剂进行脱除无机硫(主要是硫化氢),脱硫塔2底流出的脱硫液经过反应槽3(即中间槽),经脱硫液泵6进入再生器4,催化剂进行再生,再生后的脱硫催化剂通过再生器4顶部溢流进入脱硫塔2循环使用,再生器4顶部浮选出的硫磺进入泡沫槽5处理,并通过泡沫泵6’送至压滤机。
[0089]
选择制备实施例5的催化剂进行脱除硫化氢、副盐生成量及系统运行压力方面的评价,试验结果如下表2
‑
4所示。
[0090]
表2:脱除硫化氢的运行结果
[0091][0092]
表3:副盐生成量的运行结果
[0093][0094]
表4:系统运行压力
[0095][0096]
以下表5和表6中分别显示采用现有pds法的副盐生成量运行结果以及采用现有络合铁法的系统运行压力结果。
[0097]
表5:现有pds法副盐生成量运行结果
[0098][0099]
表6:现有络合铁法系统运行压力结果
[0100][0101]
1、从上面表2中脱除硫化氢的长期运行结果来看,本发明脱硫催化剂控制煤气脱硫后硫化氢含量在20ppm以下,符合煤气的脱硫标准;
[0102]
2、从表3和表5中副盐生成量运行结果看,本发明催化剂副盐生成量相对于目前单纯pds法副盐生成量降低,因此在长周期运行的情况下,本发明产生的废液量相对较少,减轻了后续提盐工序的压力,同时顺应了当前的环保形势。
[0103]
3、与表6中的现有络合铁法的系统运行压力结果相比,表4中显示使用本技术的复合型脱硫催化剂,系统长周期运行压力下降明显,在运行半年后可降至1.5kpa以下,符合现有脱硫塔的控制指标。