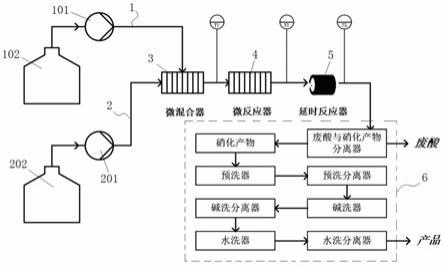
1.本发明涉及精细化工品生产领域,具体地说是一种高选择性连续合成混二硝基苯的装置及方法。
背景技术:2.二硝基苯是间二硝基苯、对二硝基苯及邻二硝基苯的总称,主要用于染料、油漆、涂料的制备,也是生产炸药(tnt)的前体。二硝基苯的合成包括苯的两步法硝化和硝基苯的一步法硝化,而混酸硝化过程有连续和间歇两种方式,但是传统间歇釜式硝化工艺,存在生产过程温差大、易发生爆炸、废酸废水量大和开车过程危险性大等问题,连续法具有小设备、大生产、高效率以及便于自动控制等优点。另外从工艺上来说,硝化工艺主要分为等温硝化和绝热硝化两种硝化工艺,绝热硝化为了防止硝基苯的挥发、热量的损失以及空气的氧化,需要在密闭压力下操作,产生的废酸含量低含水量高,由于反应温度高于反应物的沸点,反应压力高于常压,因此需要耐压设备,闪蒸设备要求用特殊材质钽,投资费用较高。等温硝化工艺反应结束后产生大量热能浓缩废酸,过程中能量浪费大、反应时间长、副产物多,但具有设备简单、投资省、收率高(硝基苯收率≥95%)等特点,目前我国广泛采用的是釜式串联工艺。
3.现有技术中也有在微通道中合成混二硝基苯的硝化工艺,如专利cn112979472a公开了一种连续生产二硝基苯的方法,其采用多级微通道硝化,每级之间需要分离水分,以得到较好的二硝基苯收率,硫酸用量也比较少,但是装置流程复杂,对装备材质要求高,投资很大,不适合大规模生产,且其间位选择性不超过88%。
技术实现要素:4.本发明的目的在于提供一种高选择性连续合成混二硝基苯的装置及方法,其中装置采用微混合器、微反应器、延时反应器串联结构,所述微混合器实现两股物料的充分混合接触,所述微反应器实现物料反应和强化传质传热目的,以实现反应控制在较低温度下进行,延时反应器保障反应时间足够,以提高原料转化率,最终实现了硝化反应的高转化率和高选择性。
5.本发明的目的是通过以下技术方案来实现的:
6.一种高选择性连续合成混二硝基苯的装置,包括混酸入料管路、硝基苯入料管路、微混合器、微反应器、延时反应器和后处理系统,所述微混合器设有第一入料通道和第二入料通道,且混酸入料管路与所述第一入料通道连接,硝基苯入料管路与所述第二入料通道连接,所述混酸入料管路上设有第一计量泵,所述硝基苯入料管路上设有第二计量泵,所述微混合器、微反应器、延时反应器、后处理系统依次串联;所述微混合器包括微混合器基板和设于所述微混合器基板两侧的第一换热板,所述微混合器基板内设有第一分散混合单元组,所述微反应器包括微反应器基板和设于所述微反应器基板两侧的第二换热板,所述微反应器基板内设有第二分散单元组。
7.所述微混合器基板内设有第一入料通道、第二入料通道、出料通道、第一分散混合单元组和第一连接通道,其中各个第一分散混合单元组分别通过对应的第一连接通道依次串联,位于输入侧的第一分散混合单元组入料端设有带两个文丘里型缩径通道的混合接口流道,且所述第一入料通道和第二入料通道分别与所述混合接口流道上对应的文丘里型缩径通道连接,位于输出侧的第一分散混合单元组出料端与所述出料通道连接。
8.所述微反应器基板内设有反应入料通道、反应出料通道、第二分散混合单元组和第二连接通道,其中各个第二分散单元组分别通过对应的第二连接通道依次串联,位于输入侧的第二分散混合单元组输入端与所述反应入料通道连接,位于输出侧的第二分散混合单元组输出端与所述反应出料通道连接。
9.所述第一分散混合单元组包括多个依次串联的第一分散混合单元,所述第二分散混合单元组包括多个依次串联的第二分散混合单元,所述第一分散混合单元与所述第二分散混合单元结构相同,均包括分散流道和汇合流道。
10.所述第一换热板和第二换热板结构相同,内部均设有换热介质输入流道、换热介质输出流道、折弯流道段和连接流道段,其中各个折弯流道段分别通过对应的连接流道段依次串联,输入侧的折弯流道段输入端与所述换热介质输入流道连接,输出侧的折弯流道段输出端与所述换热介质输出流道连接。
11.所述微反应器数量至少为一个,所述延时反应器数量至少为一个。
12.所述后处理系统包括依次串联的废酸与硝化产物分离器、预洗器、预洗分离器、碱洗器、碱洗分离器、水洗器和水洗分离器。
13.一种根据所述高选择性连续合成混二硝基苯的装置的方法包括以下步骤:
14.步骤一、配置硝酸和硫酸的混酸溶液;
15.步骤二、混酸通过第一计量泵泵入所述微混合器中,硝基苯通过第二计量泵泵入所述微混合器中,并且通过控制所述第一计量泵和第二计量泵泵入速率控制硝基苯、硝酸和硫酸的摩尔比;
16.步骤三、控制第一换热板和第二换热板温度为60~80℃,控制反应物料在微混合器、微反应器和延时反应器中的总停留时间为150~600秒,硝基苯和混酸的两股原料液在微混合器中混合接触,并在微反应器中发生反应,反应式为:
[0017][0018]
步骤四:反应物料从延时反应器输出进入后处理系统并分离获得目标产品。
[0019]
步骤一中,混酸以硝酸、硫酸和水配置,混酸中水的质量浓度为3%~15%,所述硝酸为浓度大于98%的发烟硝酸,所述硫酸为浓度大于98%的浓硫酸,配置混酸的过程温度控制在40℃以下。
[0020]
步骤二中,控制物料摩尔比为硝基苯:硝酸:硫酸=1:(1.05~1.25):(1.5~2.3),硝基苯和混酸在微通道反应器内的流动压力为0~1mpa。
[0021]
本发明的优点与积极效果为:
[0022]
1、本发明装置采用微混合器、微反应器、延时反应器串联结构,所述微混合器实现
两股物料的充分混合接触,所述微反应器实现物料反应和强化传质传热目的,以实现反应控制在较低温度下进行,延时反应器保障反应时间足够,以提高原料转化率,最终实现了硝化反应的高转化率和高选择性。
[0023]
2、本发明采用硝酸、硫酸和水配置混酸,原料总摩尔比为硝基苯:硝酸:硫酸=1:(1.05~1.25):(1.5~2.3),在这样条件下,混酸有较强的硝化能力,可以提供较快的硝化反应速度,因此反应可以在60~80℃下操作。
[0024]
3、本发明装置对比普通反应釜具有诸多优点,在危险工艺中,最重要的是操作的安全性,而本发明微通道反应器持液量少,比传统釜式反应釜小几个数量级,微通道反应器中的传质传热效率比釜式反应釜高1~3个数量级,能将反应产生热量迅速带走,,彻底杜绝大量危险物料累积放热发生严重事故的可能性。
[0025]
4、本发明方法对比其他现有工艺,具有不输于其他工艺的转化率(>99.5%),还具有优异的间位选择性(>88%),以及非常低的对位选择性,尤其反应温度为60℃时小于0.25%,在后续分离过程中可以忽略对位产物,从而节省大量能耗。
附图说明
[0026]
图1为本发明装置的结构示意图,
[0027]
图2为图1中的微混合器结构示意图,
[0028]
图3为图2中的微混合器基板结构示意图,
[0029]
图4为图3中的第一分散混合单元放大示意图,
[0030]
图5为图2中的第一换热板结构示意图,
[0031]
图6为图1微反应器中的微反应器基板结构示意图。
[0032]
其中,1为混酸入料管路,101为第一计量泵,102为第一入料罐,2为硝基苯入料管路,201为第二计量泵,202为第二入料罐,3为微混合器,31为微混合器基板,311为第一入料通道,312为第二入料通道,313为出料通道,314为混合接口流道,315为第一分散混合单元组,3151为第一分散混合单元,316为第一连接通道,317为分散流道,318为汇合流道,32为第一换热板,321为换热介质输入流道,322为换热介质输出流道,323为折弯流道段,324为连接流道段,4为微反应器,41为微反应器基板,411为反应入料通道,412为反应出料通道,413为第二分散混合单元组,4131为第二分散混合单元,414为第二连接通道,5为延时反应器,6为后处理系统。
具体实施方式
[0033]
下面结合附图对本发明作进一步详述。
[0034]
如图1~6所示,本发明包括混酸入料管路1、硝基苯入料管路2、微混合器3、微反应器4、延时反应器5和后处理系统6,其中如图2~3所示,所述微混合器3设有第一入料通道311和第二入料通道312,且混酸入料管路1与所述第一入料通道311连接,硝基苯入料管路2与所述第二入料通道312连接,所述混酸入料管路1上设有第一计量泵101,所述硝基苯入料管路2上设有第二计量泵201,所述微混合器3、微反应器4、延时反应器5、后处理系统6通过管路依次串联。
[0035]
如图2~3所示,所述微混合器3包括微混合器基板31和设于所述微混合器基板31
两侧的第一换热板32,所述微混合器基板31内设有第一入料通道311、第二入料通道312、出料通道313、第一分散混合单元组315和第一连接通道316,其中各个第一分散混合单元组315分别通过对应的第一连接通道316依次串联,位于输入侧的第一分散混合单元组315入料端设有带两个文丘里型缩径通道的混合接口流道314,且所述第一入料通道311和第二入料通道312分别与所述混合接口流道314上对应的文丘里型缩径通道连接,位于输出侧的第一分散混合单元组315出料端与所述出料通道313连接。所述文丘里型缩径通道为本领域公知技术。
[0036]
如图3所示,所述第一分散混合单元组315包括多个依次串联的第一分散混合单元3151,如图4所示,所述第一分散混合单元3151包括分散流道317和汇合流道318,且每个第一分散混合单元3151上的汇合流道318与相邻第一分散混合单元3141上的分散流道317连接,从而实现物料不断分散混合。
[0037]
如图5所示,所述第一换热板32内设有换热介质输入流道321、换热介质输出流道322、折弯流道段323和连接流道段324,其中各个折弯流道段323分别通过对应的连接流道段324依次串联,所述折弯流道段323保证整个基板的换热面积,输入侧的折弯流道段323输入端与所述换热介质输入流道321连接,输出侧的折弯流道段323输出端与所述换热介质输出流道322连接。所述换热板32通过换热介质输入和输出实现与微混合器基板31的换热,进而使基板温度满足要求,所述换热介质可采用热水等流体。
[0038]
所述微反应器4包括微反应器基板41和设于所述微反应器基板41两侧的第二换热板,如图6所示,所述微反应器基板41内设有反应入料通道411、反应出料通道412、第二分散混合单元组413和第二连接通道414,其中各个第二分散单元组413分别通过对应的第二连接通道414依次串联,位于输入侧的第二分散混合单元组413输入端与所述反应入料通道411连接,位于输出侧的第二分散混合单元组413输出端与所述反应出料通道412连接,所述反应入料通道411通过管路与所述微混合器基板31内的出料通道313连接,所述反应出料通道412通过管路与所述延时反应器5输入端连接。所述第二换热板的结构和工作原理与所述第一换热板32相同,另外所述第二分散混合单元组413包括多个依次串联的第二分散混合单元4131,所述第二分散混合单元4131结构与所述第一分散混合单元315相同,区别在于尺寸等结构参数不同。反应物料由微混合器3流出后可依次通过一个或数个微反应器4,所述微反应器4数量根据实际需要设计。
[0039]
所述延时反应器5由一段不锈钢材质的直径为φ3的管线盘制成,用来延长物料在管路内的停留时间。反应物料从最后一个微反应器4流出后可依次通过一个或者数个延时反应器5,所述延时反应器5数量根据实际需要设计。
[0040]
如图1所示,所述后处理系统6包括依次串联的废酸与硝化产物分离器、预洗器、预洗分离器、碱洗器、碱洗分离器、水洗器和水洗分离器,其中废酸与硝化产物分离器将废酸分离,硝化产物则依次经过所述预洗器、预洗分离器、碱洗器、碱洗分离器、水洗器和水洗分离器,最终形成产品产物。所述废酸与硝化产物分离器、预洗器、预洗分离器、碱洗器、碱洗分离器、水洗器和水洗分离器均为本领域公知技术。
[0041]
如图1所示,所述混酸入料管路1与一个承装混酸的第一入料罐102连通,所述硝基苯入料管路2与一个承装硝基苯的第二入料罐202连通。
[0042]
本发明的工作原理为:
[0043]
本发明微通道合成方法反应路线图如下:
[0044][0045]
本发明以硝基苯为起始原料,混酸作为硝化试剂,混酸以硝酸、硫酸和水配置,混酸中水的质量浓度为3%~15%,所述硝酸为浓度大于98%的发烟硝酸,所述硫酸为浓度大于98%的浓硫酸,所述硝基苯浓度大于99%,以上均为工业品。
[0046]
本发明以硝基苯为原料合成二硝基苯时,原料总摩尔比为硝基苯:硝酸:硫酸=1:(1.05~1.25):(1.5~2.3),在这样条件下,混酸有较强的硝化能力,可以提供较快的硝化反应速度,因此反应可以在60~80℃下操作,本发明微混合器3和微反应器4两侧均设有换热板保证反应温度。
[0047]
本发明可通过第一计量泵101和第二计量泵102控制控制两股物料的速率之比,进而获得想要的硝基苯和混酸的摩尔比,物流进料速率基于计量泵的最大压力和微混合器3及微反应器4的混合效果选取,偏低时不利于获得最优反应速率,偏高时容易超压停机,宜控制在保证不超压的情形下获得较高的进料速率,越高反应速率理论越快,但是过高可能导致反应器换热能力跟不上,易引起飞温。因此可以根据具体实验选取适合的通量,并保证在延时反应器5内反应完全,进而保证硝基苯尽可能转化为二硝基苯,从而获得较优的转化率和选择性。
[0048]
本发明优选起始硝基苯和混酸泵入微混合器3的速率可根据实际配比需要设定,优选所述硝基苯和混酸在微通道反应器内的流动压力为0~1mpa,反应物在微混合器3和微反应器4内停留时间为150~600秒。
[0049]
本发明列举若干实施例如下表1所示,其中各个实施例采用发烟硝酸(≥98%)和浓硫酸(≥98%)配置混酸,配置混酸的过程温度控制在40℃以下。在常温条件下,混酸和硝基苯连续泵入微通道混合器3和微通道反应器4中进行反应反,应温度分别为60℃、70℃和80℃。控制硝基苯、硝酸和硫酸的摩尔比为1:1.05~1.25:1.5~2.3,具体条件见下表1。
[0050]
表1
[0051][0052]
本发明对比现有工业生产工艺和其他专利的选择性优势具体见下表2。
[0053]
表2
[0054] 间二硝基苯选择性(%)对二硝基苯送择性(%)实施例191.520.20工业生产85-882-3cn 112552180a87.52.41
[0055]
由上述表1和表2可知,本发明反应温度在60~80℃范围时,间二硝基苯选择性均大于88%,高于现有技术水平,而本发明反应温度在60~70℃范围时,不仅间二硝基苯选择性高于现有水平,对二硝基苯选择性也低于现有水平,尤其在60℃时,对二硝基苯选择性<0.25%,可在后续分离过程中忽略该组分,节省大量分离能耗。