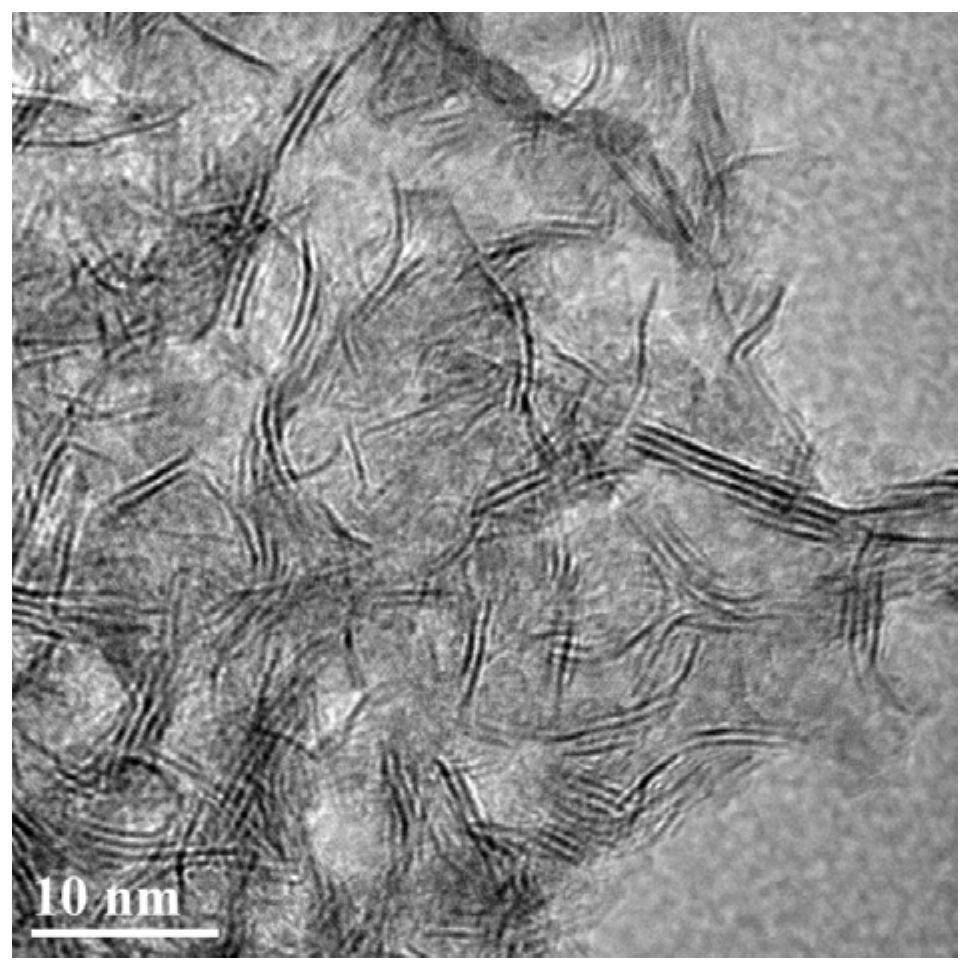
1.本发明涉及石油化工技术领域,具体地,本发明涉及一种用于煤油共炼的重油预加氢降黏催化剂及其制备方法。
背景技术:2.煤油共炼是煤直接液化的一种特殊形式,将煤粉与重油按一定比例混合,在高温、高压及催化剂的条件下,与氢气反应,使煤和重油转化成轻、中质油和少量烃类气体的工艺技术。煤油共炼技术是煤直接液化技术和重油加工技术的耦合,其充分利用了煤炭和重油在加氢反应中的协同作用,大大提高了液体收率。与煤直接液化技术相比,其投资省,能效高,油收率高,操作难度相对较小;与重油加工技术相比,其投资略高,但油收率高,产品质量好,且无需进一步脱硫、脱氮和脱烯烃处理,从而大幅降低了装置运行费用。
3.我国煤炭资源丰富,价格较低,而油气资源严重不足,通过油煤共炼技术对包括渣油、稠油、煤焦油等在内的劣质油与煤一同加氢处理,借助油煤间的协同效应生产出油收率比理论值更高的产品油,既为劣质油和煤炭探索了高效清洁转化的路径,也减轻了环境压力,符合国家清洁能源的方向。
4.在煤油共炼工艺过程中,配制油煤浆是工艺的开端,重油自身性质对油煤浆稳定性、黏温特性等具有重要影响。用于配制油煤浆的劣质重油通常黏度较大,在运输、制浆过程中非常不方便,尤其是在配制高浓度油煤浆时,由于煤粉添加比例较大,油煤浆黏度迅速升高,容易出现浆体浓度不均、泵送困难的问题。因此合理降低重油黏度是改善油煤浆黏温特性,提高油煤浆稳定性,保障后续反应顺利进行的重要手段。同时,也有益于降低油煤浆制浆工段能耗。
5.专利cn110791316a公开了一种重稠油降黏生产合成原油的方法及装置,其采用的催化剂为载体和活性金属复配而成,催化时反应器内温度较高。对于煤油共炼催化剂来讲,既需要加氢功能,也需要裂化功能,同时实现煤与重油的杂原子脱除与轻质化生成清洁油品。而对于重油降黏预处理催化剂,要求具有加氢功能,较弱的裂化功能,同时要具有很好的分散性能和抗结焦性能。还要求添加量少,不能对后续煤油共炼催化剂性能造成影响。目前并没有专门针对重油预处理降低油品黏度开发的催化剂。
技术实现要素:6.本发明针对重油预处理的迫切需求,本发明提出了一种用于煤油共炼的重油预加氢降黏的油溶性催化剂及其制备方法。
7.本发明采用的技术方案为:
8.本发明提出了一种用于煤油共炼的重油预加氢降黏催化剂的制备方法,该方法包括如下步骤:
9.1)、将钼源与有机胺、溶剂油加热搅拌均匀进行反应,钼源、有机胺、溶剂油三者的摩尔比为1:(0.5-3.0):(0.5-20)(优选为:1:(0.8-2.2):(5-15)),反应温度10-150℃(优选
为:60-100℃),反应时间10-120min(优选为:30-90min);
10.2)、将反应温度降至室温,加入硫化剂,硫化剂与钼源摩尔比例为(0.2-3):1,(优选为:(0.5-2.5):1)升温至60-150℃(优选为:80-120℃),反应压力0.01-2mpa(优选为:0.1-1.5mpa),继续反应0.5-12h(优选为:2-8h);
11.3)、反应产物洗涤、干燥后,即得催化剂。
12.在一些实施例中,步骤1)反应气氛选择通入氮气或二氧化碳气体保护,也可以选择不通入。
13.在一些实施例中,步骤1)反应在常压下进行。
14.在一些实施例中,钼源为三氧化钼、氯化钼、钼酸钠、钼酸钾、钼酸锌、钼酸铵或其水合物的一种或两种以上的组合物。
15.在一些实施例中,有机胺为碳数分布在1~40范围内烷基基团的二烷基胺的一种或两种以上组合物,烷基基团为饱和的或不饱和的直链、支链、环烷烃或芳烃基团。在一些实施例中,有机胺为二正丁胺、二仲丁胺、二戊胺、二异辛胺、二正辛胺、二苯胺或二环己胺中的一种或两种以上的组合物。
16.在一些实施例中,所述溶剂油为苯、甲苯、二甲苯、四氢萘、十氢萘、脱晶蒽油、庚烷、壬烷、癸烷、十一烷、十二烷、十三烷、十四烷、十六烷、柴油、蜡油、石油醚、甘油、乙二醇、聚乙二醇、聚乙二醇单甲醚、油酸、油酸甲酯或油酸二乙醇酰胺中的一种或两种以上的组合物。
17.在一些实施例中,硫化剂为硫化钾、硫化钠、硫氢化钠、硫化铵、硫脲、硫代乙酰胺、二硫化碳、硫磺中的一种或两种以上的组合物。
18.在一些实施例中,步骤2)反应气氛选择通入氮气或二氧化碳气体保护,也可以选择不通入。
19.在一些实施例中,步骤3)洗涤步骤所用洗涤溶剂为水、甲醇、乙醇、石油醚、洗油、焦化轻油、苯、甲苯、二甲苯、四氢萘、正己烷或正庚烷中的一种或两种以上组合物。在一些实施例中,反应产物与洗涤溶剂摩尔比为1:(5-500)。在一些实施例中,洗涤后得到的混合溶剂,经过精馏分离处理,可实现循环利用,未转化反应物可与新鲜原料混合,进一步得到转化利用。
20.在一些实施例中,所述干燥在真空条件下进行,干燥温度为50-350℃(优选为:80-150℃),真空度为0.001-3kpa(优选为:0.1-2kpa)。
21.本发明还提供了上述方法制备得到的用于煤油共炼的重油预加氢降黏催化剂。该催化剂以mo金属为活性金属的有机化合物,该催化剂进入重油后,当反应温度达到300℃以上时可原位分解为活性组分,活性组分表现为微纳米级低维层状结构。催化剂能均匀分散在各种劣质重油中,并在氢气存在和一定温度条件下,显著降低重油黏度,改善其低温流动性能。实现配制油煤浆的更高匹配性与稳定性。
22.本发明还提供了上述催化剂在用于煤油共炼的重油加氢降黏预处理中的应用。
23.在一些实施例中,催化剂加入量20-300μg/g(以金属计),优选地,50-100μg/g(以金属计)。
24.本发明具有的优点和有益效果为:
25.(1)催化剂添加量低,一般≤300μg/g(以金属计),具有加氢活性高,焦炭产率低,
稳定性好等优点。
26.(2)适用于多种高黏度劣质重油,可有效实现油品黏度可控调节。
27.(3)催化剂的催化活性可以持续保持到制浆后进入反应器,不损害煤油共炼催化剂的催化活性,并且对煤油共炼催化剂具有促进作用,可以减少油煤共炼催化剂添加量,降低催化剂成本。由于预加氢催化剂添加量少,可以不用回收,节省了催化剂回收费用。
28.(4)本发明所用原料来源广泛,溶剂可全部循环使用,没有废水废气排放,环境友好。
29.(5)催化剂合成工艺简单,操作方便,易于现有生产工艺结合,便于工业化生产。
附图说明
30.图1为本发明制备的催化剂在250倍下的扫描电镜图。
31.图2为本发明制备的催化剂反应分解后的高分辨透射电镜图。
32.图3为本发明制备的催化剂的x射线光电子能谱图。
具体实施方式
33.为更进一步阐述本发明为达成预定发明目的所采取的技术手段及功效,下面用具体的实施例对本发明予以进一步的说明,但不因此而限制本发明。
34.实施例1
35.一种用于煤油共炼的重油预加氢降黏催化剂的制备方法,该方法包括如下步骤:
36.在500ml搅拌釜中,将0.05mol钼酸铵加入到含有0.04mol二正丁胺、0.1mol四氢萘和0.01mol聚乙二醇的混合溶液中,将搅拌釜升温至60℃,常压状态反应30min。降低搅拌釜温度至室温,加入0.05mol二硫化碳和0.05mol硫代乙酰胺后充氮气至常温下搅拌釜压力0.1mpa,密闭搅拌釜,升温至90℃,反应4h。反应结束后,过滤反应产物,用5mol甲苯洗涤干净后,在1kpa的真空度下110℃干燥得到催化剂(编号cat1),收率78%,其中mo含量25%。
37.该催化剂在250倍下的扫描电镜图如图1所示,通过图1可以看出,催化剂形成了长度为100-400μm,宽度为10-100μm的棒状固体。棒状结构由层状堆积而来,同时长棒的横截面也十分光滑。规整的棒状结构,单位体积内活性金属含量更高,有利于提升催化效果。
38.图2为催化剂反应后的透射电镜图,通过图2可以看出,反应后催化剂形成了3-6层的层状堆积结构,长约5-20nm。有研究表明催化剂的层数越少,有效活性金属含量比例越高,越有利于提升催化效果。本发明催化剂堆积层数较低,具有良好的催化活性。
39.图3为实施例1制备的催化剂的x射线光电子能谱图。对制备催化剂的xps谱图进行分析,一方面可以了解合成催化剂的mo元素价态,确认mo的还原程度;另一方面也可以计算制备得到的催化剂中硫/氧比。该催化剂中mo元素以4+价为主,s元素以2-价为主,s/o比为1.87。
40.实施例2
41.一种用于煤油共炼的重油预加氢降黏催化剂的制备方法,该方法包括如下步骤:
42.在500ml搅拌釜中,将0.05mol钼酸钠加入到0.04mol二异辛胺、0.3mol甲苯和0.01mol油酸甲酯的混合溶液中,将搅拌釜升温至80℃,常压氮气保护状态下反应60min。降低搅拌釜温度至室温,加入0.05mol二硫化碳和0.05mol硫化钠后密闭搅拌釜,升温至120
℃,反应6h。反应结束后,过滤反应产物,用5mol甲醇水溶液洗涤干净后,在1kpa的真空度下110℃干燥得到催化剂(编号cat2),收率80%,其中mo含量27%。
43.实施例3
44.一种用于煤油共炼的重油预加氢降黏催化剂的制备方法,该方法包括如下步骤:
45.在500ml搅拌釜中,将0.03mol钼酸钠与0.03mol钼酸铵加入到0.05mol二正丁胺、0.5mol正十四烷和0.02mol聚乙二醇单甲醚的混合溶液中,将搅拌釜升温至80℃,常压氮气保护状态下反应60min。降低搅拌釜温度至室温,加入0.05mol二硫化碳和0.05mol硫化钠后充氮气至常温下搅拌釜压力0.1mpa,密闭搅拌釜,升温至100℃,反应5h。反应结束后,过滤反应产物,依次用5mol二甲苯与乙醇洗涤干净后,在1kpa的真空度下110℃干燥得到催化剂(编号cat3),收率82%,其中mo含量26%。
46.催化剂具体应用效果1
47.将实施例2中催化剂分别添加50μg/g和100μg/g至催化裂化油浆中(具体性质分析见表1),在不同氢初压和停留时间条件下,进行了两种不同深度的重油加氢预处理试验,其中浅度加氢条件:催化剂添加量50μg/g,反应温度380℃,氢初压7mpa,停留时间60min;深度加氢条件:催化剂添加量100μg/g,反应温度380℃,氢初压8mpa,停留时间90min。试验结果表明不同程度的预加氢处理可实现重油原料黏度的定向调控,表2中重油原料黏度经降黏预处理后分别可下降28%和69%。
48.表1 催化裂化油浆性质分析
[0049][0050]
表2 预处理前后样品黏度对比
[0051]
样品未加氢原料浅度加氢样品深度加氢样品黏度(90℃)mpa
·
s584218
[0052]
催化剂具体应用效果2
[0053]
在反应温度380℃、氢初压7mpa、停留时间60min和添加实施例3中催化剂50μg/g条件下对煤焦油进行加氢预处理。表3为煤焦油组成分析及元素分析数据,表4为煤焦油加氢预处理前后元素分析数据对比。
[0054]
表3 煤焦油组成分析及元素分析
[0055][0056][0057]
表4 加氢前后煤焦油性质对比
[0058]
项目黏度(60℃)mpa
·
sc%h%n%s%h/c预处理前样品13691.015.711.160.290.75预处理后样品11291.296.240.910.150.82
[0059]
从表4数据中可以看出采用实施例3中催化剂对煤焦油进行加氢预处理后,样品黏度下降18%,h/c原子比提高9%。进一步,将预处理后煤焦油与煤样进行煤油共炼试验,采用的试验设备为高压釜,试验重油与煤粉质量比2:1,fe基催化剂添加量1%,反应温度450℃,氢初压10mpa,停留时间2h。氢耗为消耗氢气量与原料的比值,气体产物为扣除氢气后的不凝性气体,固液体产物依次用正己烷、四氢呋喃进行索氏萃取分析,依次得到油、沥青质、未反应物产率。与同等条件下未进行预处理样品煤油共炼试验结果对比见表5。
[0060]
表5 重油预处理对煤油共炼反应性能影响
[0061]
项目氢耗%气产率%油产率%沥青质%转化率%未处理4.039.4080.845.1197.48预处理3.749.2384.102.8298.74
[0062]
从表5结果来看,重油原料适当程度的加氢预处理在降低油浆黏度的同时,还可以起到降低氢耗和气产率,提高油产率,促进煤的加氢裂解和重质组分向轻质组分转移的作用。在同等反应条件下,含有预加氢催化剂的重油与煤粉、煤油共炼催化剂混合制浆后进行反应,不损害煤油共炼催化剂的催化活性,并且对煤油共炼催化剂具有促进作用。
[0063]
进一步,将催化剂具体应用效果1中经过浅度加氢的催化裂化油浆与煤粉配成油煤浆,重油与煤粉质量比3:1,添加fe基催化剂0.8%,反应温度420℃,氢初压8mpa,停留时间60min,进行煤油共炼反应,与同等温度、压力、停留时间条件下,未经过预处理的重油配制的油煤浆反应效果对比,此时fe基催化剂添加量1%。具体结果见表6。
[0064]
表6 重油预处理对催化剂性能影响
[0065]
重油fe基催化剂气体收率/%液体收率/%固体收率/%煤转化率/%
未处理1%6.9282.5210.7758.46预处理0.8%6.5982.9810.4260.30
[0066]
从表6可看出,经过降黏预处理后的催化裂化油浆进行煤油共炼反应,在煤油共炼催化剂添加量减少20%的条件下,产物组成与同等条件下未处理的重油进行煤油共炼反应得到的结果基本一致。
[0067]
在本发明中,术语“一个实施例”、“一些实施例”、“示例”、“具体示例”、或“一些示例”等意指结合该实施例或示例描述的具体特征、结构、材料或者特点包含于本发明的至少一个实施例或示例中。在本说明书中,对上述术语的示意性表述不必须针对的是相同的实施例或示例。而且,描述的具体特征、结构、材料或者特点可以在任一个或多个实施例或示例中以合适的方式结合。此外,在不相互矛盾的情况下,本领域的技术人员可以将本说明书中描述的不同实施例或示例以及不同实施例或示例的特征进行结合和组合。
[0068]
尽管上面已经示出和描述了本发明的实施例,可以理解的是,上述实施例是示例性的,不能理解为对本发明的限制,本领域的普通技术人员在本发明的范围内可以对上述实施例进行变化、修改、替换和变型。