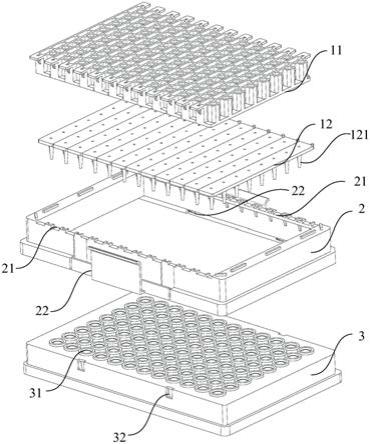
1.本实用新型涉及生物领域,特别涉及一种微液滴生成装置。
背景技术:2.微液滴技术是在微尺度通道内,利用流动剪切力与表面张力之间的相互作用将连续流体分割分离成离散的纳升级及以下体积的液滴的一种微纳技术。
3.微液滴类型主要有气-液相液滴和液-液相液滴两种。液-液相微液滴由于体积小、液滴样品间无扩散、可避免样品间的交叉污染、反应条件稳定、适当操控下可实现迅速混合等优点。
4.液-液相液滴根据连续相和分散相的不同又分为“水包油”,“油包水”,“油包水包油”以及“水包油包水”等。
5.微液滴生成系统能生成直径在微米量级(即10-1000μm)“油包水”或“水包油”微液滴,为生物、化学和材料等领域的众多应用场景提供高灵敏、高效率和高通量的研究场所。
6.96孔板为生物领域常用的实验耗材,但现有技术的微液滴生成装置与96孔板兼容性较差,无法直接将微液滴样本生成到96孔板中,在实际使用时,在微液滴生成装置产生微液滴后往往需要通过其他手段和工具将微液滴转移至96孔板中,流程繁杂且过程中容易产生微液滴样本的污染。因此难以作为生物、化学和材料等领域普适性高的实验系统。
技术实现要素:7.本实用新型要解决的技术问题是为了克服微液滴生成装置与96孔板兼容性较差,无法直接将微液滴样本生成到96孔板中,在实际使用时,在微液滴生成装置产生微液滴后往往需要通过其他手段和工具将微液滴转移至96孔板中,流程繁杂且过程中容易产生微液滴样本的污染的缺陷,提供一种微液滴生成装置。
8.本实用新型是通过下述技术方案来解决上述技术问题:
9.一种微液滴生成装置,其包括:
10.生成芯片,所述生成芯片包含第一隔室和第二隔室,所述生成芯片可将所述第一隔室和所述第二隔室的液体样本生成为微液滴;
11.收集板,所述收集板为96孔板,所述收集板包括收集孔;
12.连接基座,所述连接基座包裹所述收集板,所述连接基座包括芯片支架,所述生成芯片放置并限位于所述芯片支架,所述收集板可拆卸的安装在所述连接基座上。
13.在本方案中,采用上述结构形式,生成芯片与作为收集板的96孔板通过连接基座集成在一起,使得生产芯片生成的微液滴可以直接被作为收集板的96孔板收集。收集板可拆卸地安装于连接基座,也方便在收集微液滴后直接拆卸下来进行后续操作,无需通过其他手段和工具转移微液滴,流程简便且过程中不易污染微液滴样本。
14.较佳的,所述生成芯片包括排样管,所述微液滴通过所述排样管排出,当所述生成芯片放置并限位于所述芯片支架时,所述排样管伸入所述收集孔中。
15.在本方案中,采用上述结构形式,通过芯片支架的限位,可以使得生成芯片放置在其上时其排样管直接伸入到收集板的收集孔中,使得生成芯片与收集板对位。同时,排样管伸入收集孔也可以减少微液滴滴落的高度,降低微液滴滴落的动能,避免滴落的冲击破坏微液滴结构。
16.较佳的,所述生成芯片包含若干芯片模块,所述芯片模块包括若干与所述收集孔一一对应的芯片单元,若干芯片单元一体成型形成芯片模块。
17.在本方案中,采用上述结构形式,生成芯片有多个相同的芯片模块组成,每个芯片模块上又包含多个芯片单元,每个芯片单元可单独生成微液滴,芯片单元的数量与收集板的收集孔的数量一一对应。每个单独的芯片模块一体成型,方便芯片模块的批量加工,可降低生成芯片的生产和维护成本。
18.较佳的,所述芯片模块由热塑材料或热固材料或玻璃形成。
19.在本方案中,采用上述结构形式,热塑材料、热固材料、玻璃等材料加工容易,成本低廉,进一步降低生成芯片的成本。
20.较佳的,所述生成芯片包括:
21.加样层,所述加样层设于所述生成芯片的顶部,所述第一隔室和第二隔室设于所述加样层上;
22.排样层,所述排样层设于所述生成芯片的底部,所述排样管设于所述排样层上,所述排样层顶面与所述加样层的底面相互贴合并密封;
23.微流道层,所述排样层顶面与所述加样层的底面相互贴合并密封形成所述微流道层,所述微流道层包括与所述第一隔室和所述排样管联通的第一流道,与所述第二隔室以及所述第一流道连通的第二流道,所述第二流道沿所述第一流道的垂直方向和所述第一流道在生成区域交汇。
24.在本方案中,采用上述结构形式,微流道层由加样层和排样层以键合或胶贴等方式形成,芯片三层结构紧密层叠契合,高度集成,面积和体积小,显著降低了微液滴生成的成本。
25.较佳的,所述排样层的顶面和/或所述加样层的底面凹陷形成第一凹槽和第二凹槽,所述第一凹槽和所述第二凹槽通过与所述加样层的底面和/或所述排样层的顶面相互贴合并密封形成所述第一流道和所述第二流道。
26.在本方案中,采用上述结构形式,生成芯片通过第一流道和第二流道生成微液滴,第一流道和第二流道由设在排样层的顶面和/或加样层的底面的凹槽形成,在排样层和加样层以键合或胶贴等方式封装后,这些凹槽成为供液体样本流通交汇的流道,产生微液滴,使得芯片高度集成。
27.较佳的,所述第一流道沿液体样本的流动方向依次包括:连通第一隔室的第一入口、缓冲区域、生成区域和连通排样管的出口;
28.所述缓冲区域包括沿所述第一流道侧面方向延伸的第一延长流道和第二延长流道,所述第一延长流道和所述第二延长流道通过弯折流道连通,所述第一延长流道连通所述第一入口,所述第二延长流道连通所述生成区域。
29.在本方案中,采用上述结构形式,液体样本从第一隔室由第一入口进入第一流道,并与第二流道的液体样本在生成区域交汇形成微液滴,再由出口自排样管流出。缓冲区域
为一段通过向一侧弯折后再返回原流道方向的延长段,在第一入口和生成区域之间设置向一侧延长的缓冲区域,可使得液体样本在进入流道后可以在延长的缓冲区域内进行稳定,使其流速与均匀程度相对稳定后再进入生产区域生产微液滴,可提升微液滴的生成效果。
30.较佳的,所述第一延长流道与所述第二延长流道相互平行。
31.在本方案中,采用上述结构形式,第一延长流道与第二延长流道相互平行,可使两者间的距离恒定并保持最大距离,可使得加样层和排样层以键合或胶贴等方式的封装更容易,封装效果更好。
32.较佳的,所述排样管包括:
33.内腔,所述内腔的腔壁自内腔顶部向内腔底部逐渐收敛;
34.排液口,所述排液口开设于所述内腔的底部的一侧;
35.导流面,所述导流面设于所述内腔的底部,所述导流面一端抵住所述腔壁,所述导流面的另一端向下倾斜并延伸至所述排液口。
36.在本方案中,采用上述结构形式,排样管连通微流道层的出口,微流道层的微液滴从出口流出后流入排样层的内腔,并可沿内腔的腔壁向腔底流动至导流面上,再由导流面缓慢流至排液口排出,可以避免微液滴直接滴落冲击过大可能损害微液滴结构。
37.较佳的,所述排样管还包括引流部,所述引流部设于所述内腔开设所述排液口的一侧的所述腔壁上,所述引流部沿所述腔壁凸起并向所述排液口延伸,所述引流部的末端在垂直方向上的投影位于所述导流面上。
38.在本方案中,采用上述结构形式,排样管开设排液口一侧的腔壁上方还设有凸起的引流部,可通过凸出结构将该侧腔壁上的微液滴导引至导流面上,避免微液滴从该侧腔壁直接从排液口流出,提升排样管的导流效果。
39.本实用新型的积极进步效果在于:通过本实用新型所公开的微液滴生成装置,生成芯片与作为收集板的96孔板通过连接基座集成在一起,使得生产芯片生成的微液滴可以直接被作为收集板的96孔板收集。收集板可拆卸地安装于连接基座,也方便在收集微液滴后直接拆卸下来进行后续操作,无需通过其他手段和工具转移微液滴,流程简便且过程中不易污染微液滴样本。
附图说明
40.图1为本实用新型实施例1的微液滴生成装置结构示意图。
41.图2为本实用新型实施例1的微液滴生成装置的爆炸结构示意图。
42.图3为本实用新型实施例1的连接基座的局部结构示意图。
43.图4为本实用新型实施例1的芯片模块的结构示意图。
44.图5为本实用新型实施例1的芯片模块的俯视结构示意图。
45.图6为本实用新型实施例1的芯片模块与连接基座的连接结构示意图。
46.图7为本实用新型实施例1的微流道层的结构示意图。
47.图8为本实用新型实施例1的微流道层的结构示意图。
48.图9为本实用新型实施例1的微流道层的结构示意图。
49.图10为本实用新型实施例2的排样管的结构示意图。
50.图11为本实用新型实施例2的排样管的内部结构示意图。
51.附图标记说明:
52.生成芯片1
53.加样层11
54.排样层12
55.排样管121
56.出口122
57.内腔123
58.排液口124
59.导流面125
60.引流部126
61.芯片模组13
62.芯片单元14
63.第一隔室141
64.第一入口143
65.第二入口144
66.第二隔室142
67.微流道层15
68.第一流道16
69.第一延长流道161
70.第二延长流道162
71.弯折流道163
72.第二流道17
73.生成区域18
74.连接基座2
75.芯片支架21
76.凸块211
77.槽口212
78.卡扣22
79.收集板3
80.收集孔31
81.卡槽32
具体实施方式
82.下面通过实施例的方式进一步说明本实用新型,但并不因此将本实用新型限制在所述的实施例范围之中。
83.实施例一
84.如图1-3所示,本实施例的微液滴生成装置包括生成芯片1、收集板3和连接基座2组成。生成芯片1包含第一隔室141和第二隔室142,生成芯片1可将第一隔室141和第二隔室142的液体样本生成为微液滴。收集板3为96孔板,收集板3包括收集孔31。连接基座2包裹收
集板3,连接基座2包括芯片支架21,生成芯片1放置并限位于芯片支架21,收集板3可拆卸的安装在连接基座2上。
85.本实施例中,生成芯片1的第一隔室141和第二隔室142用于分别注入水相液体和油相液体。通过精密气控装置分别对两个隔室进行加压,使得液体通过生成芯片1生成“油包水”或者“水包油”的微液滴,在排出至收集板3的收集孔31中。
86.本实施例的收集板3为96孔板,是生物领域常用的实验耗材,该板上具有8*12个收集孔31。在其他实施例中,收集板3也可由若干个8连排管组成。
87.如图2、3所示,本实施例的连接基座2为方框型,连接基座2可以套设在收集板3上并包裹在收集板3的四周,通过连接基座2上的卡扣22与收集板3上的卡槽32实现可拆卸地固定。使其与收集板3的连接更为稳固。卡槽32设置在收集板3的两侧,卡扣22则设于连接基座2两侧的对应位置。卡扣22设在一个可进行一定程度弯折的连接板的一端上,连接板的另一端固定于连接基座2侧面,连接板设置卡扣22一端的背面还设有一手柄部,该手柄部向连接板的另一端延伸。通过挤压该手柄部可使连接板向外弯折,使得卡扣22抬起以便嵌入或者脱出收集板3的卡槽32。
88.如图2、3所示,芯片支架21由连接基座2相对的两个侧边顶部有间隔设有多组对应的凸块211组成,当芯片放置于连接基座2上时,芯片的边缘则卡设于两凸块211之间的槽口212内,并与卡设在连接基座2上的收集板3对位。
89.在其他实施例中,连接基座2也可不套设包裹收集板3而采用其他方式与收集板3连接,如制作成上框结构安设在收集板3的顶面上,或制作成底座结构将收集板3直接放入连接基座2内。而芯片支架21也不局限于设置于边缘的凸块211和槽口212,也采用在连接基座2顶部增加一个设有安装槽的顶面,或者在连接基座2内部,收集板3顶面上增加支撑结构等方式实现,只要能实现收集板3的可拆卸安装以及生成芯片1的固定与限位即可。
90.生成芯片1与作为收集板3的96孔板通过连接基座2集成在一起,使得生产芯片生成的微液滴可以直接被作为收集板3的96孔板收集。收集板3可拆卸地安装于连接基座2,也方便在收集微液滴后直接拆卸下来进行后续操作,无需通过其他手段和工具转移微液滴,流程简便且过程中不易污染微液滴样本。
91.如图2所示,生成芯片1包括排样管121,微液滴通过排样管121排出,当生成芯片1放置并限位于芯片支架21时,排样管121伸入收集孔31中。
92.本实施例中,排样管121设于生成芯片1的底面上并向下延伸,当生成芯片1卡设在槽口212时,生成芯片1的排样管121正对收集口并伸入至收集孔31中。
93.通过芯片支架21的限位,可以使得生成芯片1放置在其上时其排样管121直接伸入到收集板3的收集孔31中,使得生成芯片1与收集板3对位。同时,排样管121伸入收集孔31也可以减少微液滴滴落的高度,降低微液滴滴落的动能,避免滴落的冲击破坏微液滴结构。
94.在其他实施例中,排样口也可仅对准收集孔31而不伸入收集孔31中,只是这种结构仅能保证微液滴滴入收集孔31中但无法降低微液滴滴落的动能。
95.如图1-5所示,生成芯片1包含若干芯片模块,芯片模块包括若干与收集孔31一一对应的芯片单元14,若干芯片单元14一体成型形成芯片模块。
96.本实施例中,每个芯片单元14都可以单独生成微液滴,包括一组第一隔室141、第二隔室142和排样管121,一个单独的芯片模块具有8个横向排列的芯片单元14。本实施例的
生成芯片1由12个芯片模块组成,共具有8*12个芯片单元14,与作为收集板3的96孔板相对应。
97.在其他实施例中,芯片模组13的芯片单元14排列方向和数量也不局限于此,可以根据使用场景的不同和需求的不同进行调整,只要保证能够与收集板3的收集孔31对应即可。
98.生成芯片1有多个相同的芯片模块组成,每个芯片模块上又包含多个芯片单元14,每个芯片单元14可单独生成微液滴,芯片单元14的数量与收集板3的收集孔31的数量一一对应。每个单独的芯片模块一体成型,方便芯片模块的批量加工,可降低生成芯片1的生产和维护成本。
99.本实施例中,芯片模块由热塑材料、热固材料、玻璃形成。该类材料加工容易,成本低廉,进一步降低生成芯片1的成本。
100.在其他实施例中,也可使用其他常见的热成型材料制成本产品。
101.如图2-8所示,生成芯片1包括加样层11,排样层12和微流道层15。加样层11设于生成芯片1的顶部,第一隔室141和第二隔室142设于加样层11上;排样层12设于生成芯片1的底部,排样管121设于排样层12上,排样层12顶面与加样层11的底面相互贴合并密封;排样层12顶面与加样层11的底面相互贴合并密封形成微流道层15,微流道层15包括与第一隔室141和排样管121联通的第一流道16,与第二隔室142以及第一流道16连通的第二流道17,第二流道17沿第一流道16的垂直方向和第一流道16在生成区域18交汇。
102.本实施例中,第一隔室141通过第一入口143与第一流道16相连通,第二隔室142通过第二入口144与第二流道17相连通,第二流道17在生成区域18从两侧与第一流道16连通。两隔室的液体通过气压作用下进入两流道中向出口122方向流动。第一隔室141中的液体在第一流道16内流经生成区域18时,在第二流道17的液体的流动剪切力作用下生成相应微液滴。
103.本实施例中,排样层12顶面与加样层11的底面相互贴合并以键合等方式封装,在其他实施例中,也可选用胶贴等其他常见的封装方式。
104.当第一隔室141内为油相液体,第二隔室142内为水相液体时,可以生成“水包油”微液滴;
105.当第一隔室141内为水相液体,第二隔室142内为油相液体时,可以生成“油包水”微液滴。
106.本实施例的微流道层15由加样层11和排样层12以键合或胶贴等方式形成。在其他实施例中,也可以另设一层独立的微流道层15并与加样层11和排样层12的第一入口143,第二入口144以及出口122连通。
107.微流道层15由加样层11和排样层12以键合或胶贴等方式形成,芯片三层结构紧密层叠契合,高度集成,面积和体积小,显著降低了微液滴生成的成本。
108.如图7所示,排样层12的顶面和/或加样层11的底面凹陷形成第一凹槽和第二凹槽,第一凹槽和第二凹槽通过与加样层11的底面和/或排样层12的顶面以键合或胶贴等方式形成第一流道16和第二流道17。
109.本实施例中,第一凹槽和第二凹槽都形成在加样层11的底面。排样层12通过键合或胶贴等方式将凹槽封闭形成流道。
110.在其他实施例中,该凹槽也可形成于排样层12的顶面,或者分别形成在两面上。
111.生成芯片1通过第一流道16和第二流道17生成微液滴,第一流道16和第二流道17由设在排样层12的顶面和/或加样层11的底面的凹槽形成,在排样层12和加样层11以键合或胶贴等方式封装后,这些凹槽成为供液体样本流通交汇的流道,产生微液滴,使得芯片高度集成。
112.如图8所示,第一流道16沿液体样本的流动方向依次包括:连通第一隔室141的第一入口143、缓冲区域、生成区域18和连通排样管121的出口122。缓冲区域包括沿第一流道16侧面方向延伸的第一延长流道161和第二延长流道162,第一延长流道161和第二延长流道162通过弯折流道163连通,第一延长流道161连通第一入口143,第二延长流道162连通生成区域18。
113.本实施例中,第二流道17自第二出口122位置,从两侧以分别延伸出去,并在生成区域18位置从第一流道16的垂直方向的两侧与第一流道16交汇,然后再导通至出口122。而第一流道16则从第一入口143位置先经过一个通过弯折方式延长的缓冲区域后,再延伸到生成区域18与第二流道17交汇,再导通至出口122位置。
114.如图8所示,本实施例的缓冲区域由连通第一入口143并横向延伸的第一延长流道161,连通第一延长流道161尾端并纵向弯折的弯折流道163,以及连通弯折流道163尾端并沿横向朝第一延长流道161延伸反向相反的方向延伸的第二延长流道162组成。缓冲区域整个呈一个螺旋式结构。
115.在其他实施例中,缓冲区域也可设置更多延长流道和弯折流道163,使其呈多层螺旋结构以进一步延长缓冲区域的整体长度,增加其稳流效果。但在总长度不变的情况下,只使用一个弯折结构的缓冲区域可使得两延长流道的距离最长,可以降低加样层11和排样层12之间以键合或胶贴等方式封装的难度。
116.液体样本从第一隔室141由第一入口143进入第一流道16,并与第二流道17的液体样本在生成区域18交汇形成微液滴,再由出口122自排样管121流出。缓冲区域为一段通过向一侧弯折后再返回原流道方向的延长段,在第一入口143和生成区域18之间设置向一侧延长的缓冲区域,可使得液体样本在进入流道后可以在延长的缓冲区域内进行稳定,使其流速与均匀程度相对稳定后再进入生产区域生产微液滴,可提升微液滴的生成效果。
117.如图8所示,第一延长流道161与第二延长流道162相互平行。
118.第一延长流道161与第二延长流道162相互平行,可使两者间的距离恒定并保持最大距离,可使得加样层11和排样层12的以键合或胶贴等方式封装更容易,封装效果更好。
119.如图9所示,本实施例的排样管121包括内腔123和排液口124,内腔123的腔壁自内腔123顶部向内腔123底部逐渐收敛。排液口124开设于内腔123的底部。
120.排样管121内部中空形成内腔123,内腔123的顶部连通微流道层15的出口122,微流道层15形成的微液滴自该出口122沿内腔123的腔壁向下流动。并从内腔123底部的排液口124滴落至收集板3的收集孔31中。
121.实施例二
122.本实施的微液滴生成装置其结构与实施例一大致相同,对其相同部分不在赘述,不同之处在于本实施例的排样管121。
123.如图10,11所示,排样管121包括内腔123,排液口124和导流面125。内腔123的腔壁
自内腔123顶部向内腔123底部逐渐收敛。排液口124开设于内腔123的底部的一侧。导流面125设于内腔123的底部,导流面125一端抵住腔壁,导流面125的另一端向下倾斜并延伸至排液口124。
124.本实施例中,排样管121内部中空形成内腔123,内腔123的顶部连通微流道层15的出口122,微流道层15形成的微液滴自该出口122沿内腔123的腔壁向下流动。排液口124开设于排样管121的侧面底部,导流面125则是设于内腔123底部沿着内腔123腔壁向排液口124向下倾斜的斜面。
125.微液滴可沿内腔123的腔壁向腔底流动至导流面125上,再由导流面125缓慢流至排液口124排出,可以避免微液滴直接滴落冲击过大可能损害微液滴结构。
126.如图10,11所示,排样管121还包括引流部126,引流部126设于内腔123开设排液口124的一侧的腔壁上,引流部126沿腔壁凸起并向排液口124延伸,引流部126的末端在垂直方向上的投影位于导流面125上。
127.本实施例中,引流部126的倾斜角度略大于腔壁的倾斜角度,并且其末端在垂直方向上位于导流面125上,保证从引流部126滴落的微液滴可落在导流面125上,避免微液滴从该侧腔壁直接从排液口124流出,提升排样管121的导流效果。
128.虽然以上描述了本实用新型的具体实施方式,但是本领域的技术人员应当理解,这仅是举例说明,本实用新型的保护范围是由所附权利要求书限定的。本领域的技术人员在不背离本实用新型的原理和实质的前提下,可以对这些实施方式做出多种变更或修改,但这些变更和修改均落入本实用新型的保护范围。