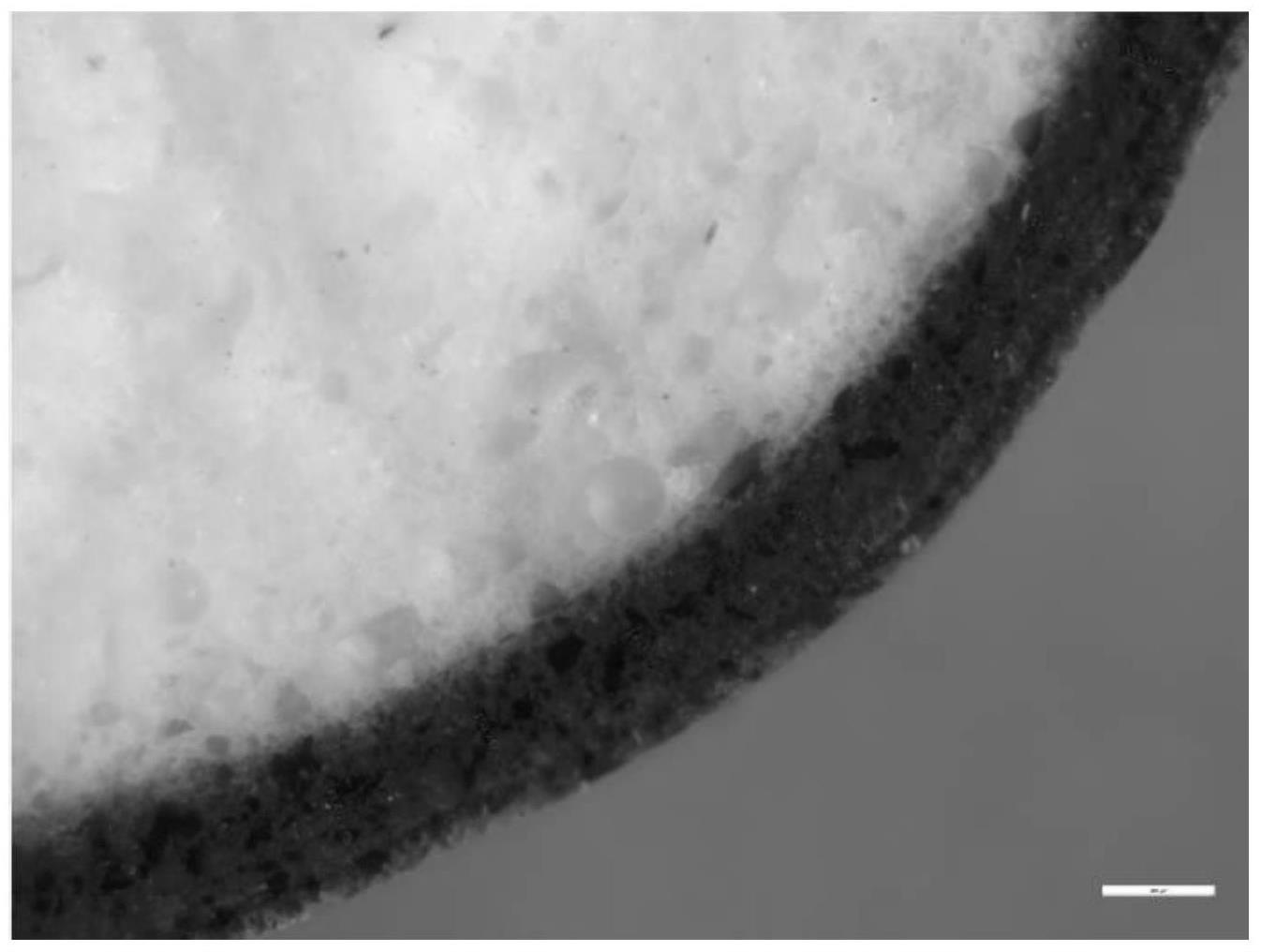
1.本发明涉及一种催化剂及方法,尤其涉及一种乙酰氧化催化剂、其制备方法及制备醋酸烯酯的方法。
背景技术:2.醋酸烯酯是一种重要的有机合成中间体,典型的醋酸烯酯有醋酸乙烯酯、醋酸烯丙酯、甲基丙烯醇醋酸酯等。其中,醋酸烯丙酯是一种无色易燃液体,微溶于水,易溶于醇和醚,能溶于丙酮,它作为一种重要的化工原料,主要用于生产丙烯醇、环氧氯丙烷、甘油等重要有机合成原料,还用于树脂及粘合剂的合成。
3.20世纪80年代,日本昭和电工首次实现了醋酸烯丙酯的工业化生产,昭和电工开发了乙酰氧化技术,在钯和助催化剂存在下,以丙烯、氧气和醋酸为原料,采用固定床气相反应制备醋酸烯丙酯。采用的乙酰氧化催化剂以sio2、al2o3或者sio2和al2o3组成的的混合物为载体,负载有钯、铜和醋酸钾,而且钯、铜活性组分呈蛋壳型分布。
4.公开号为cn 101657259 b的专利申请记载了一种制备乙酸烯丙醋的催化剂,该催化剂制备过程包括四个步骤,其中为了制备活性组分呈“蛋壳”型分布的催化剂,采用了用碱液浸泡载体的方法,虽然制备了“蛋壳”型催化剂,但采用碱液浸泡载体容易造成载体强度降低,孔道破坏,且在浸泡过程中造成活性组分的流失。
5.公开号为cn 1131199c的专利文献申请记载了一种氧酰化催化剂用于制备乙酸烯丙酯,该催化剂在制备过程中添加了金属锡或锡与额外助催化剂金属的混合物,通过添加锡可以在原料中不添加水的情况下维持催化剂寿命不衰退。由于乙酰氧化反应中会生成水,且生成的水会移走乙酰氧化反应产生的部分热量,因此,通过不添加水的方法不具有工业应用优势。
6.公开号为cn 103120961 b的专利申请记载了一种醋酸烯丙酯催化剂及其制备方法。该催化剂以sio2、al2o3或其混合物为载体,负载活性组分包括金属钯、金属铜和碱金属醋酸盐,钯铜晶粒平均粒径为5-7nm;催化剂制备过程中以液态二氧化碳作为浸渍液,所用钯化合物为乙酰丙酮基为配体,该制备方法采用的原料昂贵,造成生产成本过高,不具备工业应用经济性。
7.公开号为106582871b的专利申请记载了一种醋酸烯丙酯生产所用的催化剂,该催化剂的载体包括载体基材和表面涂层,基材为多孔二氧化硅,涂层由铂簇金属元素和iva金属元素中至少一种组成,该制备方法中采用的涂层为铂簇金属价格昂贵,且不易回收分离,因此催化剂生产成本高,不利于工业化大规模应用。
技术实现要素:8.本发明的目的在于提供一种乙酰氧化用催化剂及该催化剂的制备方法,该乙酰氧化催化剂活性组分呈“蛋壳”型分布,形成的钯基合金性质更稳定,活性组分不易流失,催化活性和选择性更高,使用寿命更长。
9.本发明的另一个目的在于提供一种制备醋酸烯酯类化合物的方法,特别是指制备醋酸烯丙酯化合物的方法,在本发明提供的催化剂作用下制备醋酸烯丙酯具有高活性和高选择性的特点。
10.为实现上述目的,本发明所采用的技术方案如下:
11.一种乙酰氧化催化剂,所述催化剂包含载体、活性组分和助剂;
12.所述载体包括sio2以及任意含有或不含有的al2o3、fe2o3;所述活性组分包括(a)钯元素以及(b)元素铜、金、锡中的至少一种;所述助剂为碱金属醋酸盐。
13.优选地,所述载体具有以下特征中的一个或多个:
14.a)平均粒径3-10mm;
15.b)比表面积为100-600m2/g,孔容为0.3-1.2ml/g,平均孔径为5-20nm,堆密度为300-900g/l;
16.c)按重量份计,载体中sio2含量为85-100份、al2o3含量为0-10份、fe2o3含量为0-5份。
17.优选地,所述载体比表面积为120-400m2/g,更优选150-300m2/g;孔容为 0.4-1.0ml/g,更优选0.6-0.9ml/g;平均孔径为6-19nm,更优选9-18nm;堆密度为350-800g/l,更优选400-700g/l。
18.所述活性组分包括(a)钯以及(b)元素铜、金、锡中的至少一种,优选地,活性组分中(a)钯的含量为0.5-15g/l,更优选0.6-10g/l;活性组分中(b) 的含量为0.1-10g/l,更优选0.2-6g/l。
19.进一步地,所述活性组分呈“蛋壳”型分布;所述“蛋壳”型分布为活性组分位于载体表面层;活性组分粒径2-10nm,优选3-8nm;活性组分厚度50-500μm,优选100-350μm。
20.所述助剂为碱金属醋酸盐,优选地,碱金属醋酸盐为醋酸钠、醋酸钾和醋酸铯中的至少一种,更优选醋酸钾、醋酸铯;碱金属醋酸盐的含量为10-100g/l,更优选15-80g/l。
21.本发明所述的催化剂的制备方法,包括以下步骤:
22.1)碱金属气相沉积:将碱金属放入气化器中熔融气化,以惰性气体为载气,将一定量的碱金属引入装有载体的反应管中发生化学气相沉积,得到表面负载碱金属的载体;
23.2)活性组分沉积沉淀:配制包含钯盐、(b)元素金属盐和腐植酸的溶液,将配制的金属溶液缓慢加入到步骤1)得到的载体中,得到一定厚度的活性组分为“蛋壳”型催化剂前驱体1;
24.3)活性组分还原:将步骤2得到的催化剂前驱体1与还原剂反应进行还原处理,洗涤并干燥,得到催化剂前驱体2;
25.4)助剂的添加:配制一定量的碱金属醋酸盐浸渍到催化剂前驱体2中,干燥得到催化剂成品。
26.进一步地,根据步骤1气相沉积所用的碱金属。优选地,所述碱金属包括锂、钠、钾、铯中的至少一种,优选钠、钾;所述碱金属的含量为活性组分钯摩尔含量的1.0-4.0倍,优选1.5-3.0倍。根据步骤1气相沉积所用的惰性气体。优选地,所述惰性气体包括氮气、氩气、氦气中的至少一种,优选氩气、氦气。
27.本发明人研究发现,气相沉积所用的碱金属与活性组分钯的摩尔量影响活性组分的“蛋壳”分布和活性组分厚度,碱金属与活性组分钯摩尔比过低,造成活性组分制备过程
中的流失;碱金属与活性组分钯摩尔比过高,造成活性组分的“蛋壳”厚度过厚,催化剂活性过低。本发明人发现,通过调节特定的碱金属与活性组分钯的摩尔比范围,可以有效兼顾催化剂活性组分的“蛋壳”型分布和厚度,可制备高活性和高选择性催化剂。
28.进一步地,步骤2中(a)钯盐为氯钯酸钠、氯钯酸钾、氯化钯、乙酸钯、硝酸钯、硫酸钯中的至少一种,优选氯钯酸钠;(b)元素为铜、金、锡的可溶性氯化物、硝酸盐和硫化物中的至少一种,优选(b)元素可溶性氯化物;所述腐植酸为胡敏酸、吉马多美朗酸和富里酸中的至少一种,优选富里酸;所述腐植酸添加量与活性组分钯添加量的质量比为0.05:1-2:1,优选0.1:1-1:1。
29.本发明人研究发现,沉积沉淀制备的催化剂过程中,腐植酸的添加影响活性组分中钯与其他金属元素的合金化,与不添加腐植酸制备的催化剂相比,通过添加适量的腐植酸可以明显促进活性组分形成钯基合金,腐植酸的加入能够促进钯元素与其他金属元素的合金化,更容易形成均一相的合金。通过调节活性组分盐溶液的浓度(0.005-0.02mol/l)和腐植酸的添加量可以促进活性组分钯基合金化,暴露的钯活性位点更多,活性和选择性更高。
30.进一步地,步骤3中所述还原剂包括水合肼、硼氢化钠、甲醛、葡萄糖、氢气、乙烯、丙烯、异丁烯中的至少一种,优选水合肼、氢气;所述还原剂添加量与活性组分钯添加量的摩尔比为1:1-10:1。
31.进一步地,步骤4中所述碱金属醋酸盐为醋酸钠、醋酸钾和醋酸铯中的至少一种,优选醋酸钾。
32.一种制备醋酸烯酯的方法,在前文所述催化剂的存在条件下,以醋酸、氧气、c
2-c4烯烃为原料通过乙酰氧化反应制备醋酸烯酯。
33.进一步地,制备醋酸烯酯方法包括以下步骤:
34.将醋酸、氧气、c
2-c4烯烃原料送入装填有本发明所述的催化剂的反应器中,原料以摩尔比计,c
2-c4烯烃:醋酸:氧气=1:(0.1-0.5):(0.1-0.5),于120-180℃、 0.1-1.5mpag下进行乙酰氧化反应,体积空速为1000-3000h-1
,制备得到醋酸烯酯;
35.优选地,所述c
2-c4烯烃原料为丙烯。
36.进一步地,制备醋酸烯丙酯的方法原料摩尔比计,丙烯:醋酸:氧气:水=1: (0.1-0.5):(0.1-0.5):(0.1-1),于120-180℃、0.1-1.5mpag下进行乙酰氧化反应,体积空速为1000-3000h-1
,制备得到醋酸烯丙酯。
37.本发明具有如下有益效果:
38.1)本发明通过在载体表面气相沉积一定量的碱金属,可制备活性组分呈“蛋壳”型分布、蛋壳厚度可控的乙酰氧化催化剂,并且催化剂的活性和选择性得到提高。
39.2)本发明向活性组分溶液中添加腐植酸,腐植酸促进活性组分钯与其他金属元素的合金化,制备的活性组分更容易形成钯基合金,钯基合金暴露的钯活性位点更多,催化剂活性和选择性明显提高。
40.3)本发明提供的乙酰氧化催化剂与现有催化剂制备技术相比,步骤简单,原料成本低,节约生产成本,活性组分不易流失,更具有工业应用竞争性。本发明中所述的压力为表压。
41.附图说明:图1为实施例1得到的催化剂的活性组分分布的光学显微镜图。
具体实施方式
42.下面通过具体实施例对本发明做进一步说明,本发明所述实施例只是作为对本发明的说明,不限制本发明的范围。
43.主要原料信息:
44.硅胶小球,格雷斯特种化学品和材料公司;
45.蒙脱土小球,科莱恩化工有限公司;
46.腐殖酸,上海易恩化学技术有限公司;
47.其他原料若无特别说明,也均为市售原料。
48.实施例或对比例中所用的计算方法和测试方法如下:
49.1、使用气相色谱法,采用agilent gc 8890a色谱仪分析反应产物中各组分的含量,并按下列公式计算催化剂的活性和选择性
[0050][0051][0052]
2、催化剂比表面积和孔结构信息的测定方法
[0053]
催化剂的孔结构通过n2物理吸附法测定,比表面积采用bet方法、孔容采用bjh脱附方法得到,测试仪器型号为micromeritics asap 2460。
[0054]
3、催化剂活性组分中钯活性位测定
[0055]
用研钵将一定量的催化剂粉碎,以获得均匀粉末,然后将催化剂粉末用 micromeritics autochem ii 2920化学吸附仪,通过co脉冲化学吸附测定,活性组分中钯活性位=化学吸附的co摩尔量/钯的实际负载摩尔量
×
100%。
[0056]
4、催化剂活性组分粒径的测定
[0057]
用研钵将一定量的催化剂粉碎,以获得均匀粉末,然后将该催化剂粉末在无水乙醇超声分散,采用jeol 2100plus透射电镜(tem)测定。
[0058]
5、催化剂活性组分位置和厚度的测定
[0059]
采用切片机将催化剂一分为二,得到催化剂的横切面,采用蔡司axiolab 5 光学显微镜测定催化剂活性组分的位置和厚度。
[0060]
【实施例1】
[0061]
1)催化剂的制备
[0062]
取1l硅胶小球(平均粒径5mm,比表面积为221m2/g,孔容为0.86ml/g,平均孔径14nm,堆密度为504g/l)放入气相沉积反应器中,取2.4g钾放入气化器中,将钾熔融气化,通入氦气,将气化后的钾引入装有载体的气相沉积反应器中,得到表面均匀负载钾的硅胶小球;配制2l含有3.5gpd和0.5gcu的氯钯酸钠和氯化铜水溶液,加入1.8g富里酸,充分搅拌均匀,然后加入到硅胶小球中,静置2h,得到催化剂前驱体1;然后加入15g浓度为80%的水合肼溶液,充分搅拌后,对催化剂前驱体1静置还原6h,用去离子水对还原后的催化剂前驱体1充分洗涤,110℃干燥4h,得到催化剂前驱体2;取40g醋酸钾溶于400g 去离子水中,浸渍在前驱体2上,110℃干燥2h,得到催化剂成品。
[0063]
经分析,活性组分钯活性位为52.1%,活性组分平均粒径3.8nm,活性组分呈“蛋
壳”型分布,蛋壳平均厚度136μm。
[0064]
2)催化剂性能测试
[0065]
将500ml催化剂放入内径为3cm,高度为150cm的固定床反应器中,催化剂上下两端装填惰性瓷球,用氮气漏后,将反应体系升温,然后通入反应原料,控制反应温度为145℃,反应压力为0.8mpag,体积空速为2500h-1
,原料组成为丙烯:醋酸:氧气:水=1:0.3:0.25:0.35,稳定反应100h后,将上述反应得到的混合物冷却、气液分离后通过气相色谱分析。经分析,该催化剂活性为452.1g/l/h,醋酸烯丙酯选择性为96.3%。持续评价4000h后,催化剂活性为334.5g/l/h,醋酸烯丙酯选择性为94.5%,催化剂活性和选择性仍然能够满足工业化使用要求。
[0066]
【实施例2】
[0067]
1)催化剂的制备
[0068]
取1l硅胶小球(平均粒径5mm,比表面积为221m2/g,孔容为0.86ml/g,平均孔径14nm,堆密度为504g/l),放入气相沉积反应器中,取4.5g钾放入气化器中,将钾熔融气化,通入氦气,将气化后的钾引入装有载体的气相沉积反应器中,得到表面均匀负载钾的硅胶小球;配制4l含有5.0gpd、0.5gcu和0.5gau 的氯钯酸钠、氯化铜和氯金酸水溶液,加入0.5g吉马多美朗酸,充分搅拌均匀,然后加入到硅胶小球中,静置2h,得到催化剂前驱体1;然后加入29g浓度为 80%的水合肼溶液,充分搅拌后,对催化剂前驱体1静置还原10h,用去离子水对还原后的催化剂前驱体1充分洗涤,110℃干燥4h,得到催化剂前驱体2;取50g醋酸钾溶于400g去离子水中,浸渍在前驱体2上,110℃干燥2h,得到催化剂成品。
[0069]
经分析,活性组分钯活性位为58.6%,活性组分平均粒径3.0nm,活性组分呈“蛋壳”型分布,蛋壳平均厚度179μm。
[0070]
2)催化剂性能测试
[0071]
催化剂评价条件同实施例1,将反应得到的混合物冷却、气液分离后通过气相色谱分析。经分析,该催化剂活性为465.2g/l/h,醋酸烯丙酯选择性为98.0%。持续评价4000h后,催化剂活性为342.1g/l/h,醋酸烯丙酯选择性为96.2%,催化剂活性和选择性仍然能够满足工业化使用要求。
[0072]
【实施例3】
[0073]
1)催化剂的制备
[0074]
取1l的蒙脱土小球(平均粒径5mm,比表面积为136m2/g,孔容为0.45ml/g,平均孔径12nm,堆密度586g/l,含有5.2%al2o3和1.4%fe2o3),放入气相沉积反应器中,取3.2g钠放入气化器中,将钠熔融气化,通入氦气,将气化后的钠引入装有载体的气相沉积反应器中,得到表面均匀负载钾的硅胶小球;配制6.0l 含有4.0gpd、0.33gcu和0.5gsn的氯钯酸钠、氯化铜和氯化亚锡水溶液,加入 4.0g富里酸,充分搅拌均匀,然后加入到硅胶小球中,静置2h,得到催化剂前驱体1;然后加入10g浓度为80%的水合肼溶液,充分搅拌后,对催化剂前驱体 1静置还原4h,用去离子水对还原后的催化剂前驱体1充分洗涤,110℃干燥 4h,得到催化剂前驱体2;取70g醋酸钾溶于400g去离子水中,浸渍在前驱体 2上,110℃干燥2h,得到催化剂成品。
[0075]
经分析,活性组分钯活性位为47.2%,活性组分平均粒径4.6nm,活性组分呈“蛋壳”型分布,蛋壳平均厚度263μm。
[0076]
2)催化剂性能测试
[0077]
催化剂评价条件同实施例1,将反应得到的混合物冷却、气液分离后通过气相色谱分析。经分析,该催化剂活性为407.6g/l/h,醋酸烯丙酯选择性为94.5%。持续评价4000h后,催化剂活性为329.6g/l/h,醋酸烯丙酯选择性为92.9%,催化剂活性和选择性仍然能够满足工业化使用要求。
[0078]
【对比例1】
[0079]
催化剂制备过程中载体表面不采用气相沉积碱金属,将2l含有3.5gpd和 0.5gcu的氯钯酸钠和氯化铜水溶液,加入到1l硅胶小球中,将3.45g氢氧化钾溶于60ml去离子水中,滴加到活性组分盐溶液中,静置2h,其余的制备条件同实施例1。经分析,活性组分钯活性位为33.9%,活性组分平均粒径7.2nm,活性组分呈均匀型分布,且活性组分存在流失。催化剂评价条件同实施例1,将反应得到的混合物冷却、气液分离后通过气相色谱分析。经分析,该催化剂活性为288.6g/l/h,醋酸烯丙酯选择性为80.3%,该催化剂初始性能不满足工业化使用要求。
[0080]
【对比例2】
[0081]
催化剂制备过程中活性组分不添加腐植酸。取1l硅胶小球,放入气相沉积反应器中,取2.4g钾放入气化器中,将钾熔融气化,通入氦气,将气化后的钾引入装有载体的气相沉积反应器中,得到表面均匀负载钾的硅胶小球;配制2l 含有3.5gpd和0.5gcu的氯钯酸钠和氯化铜水溶液,然后加入到硅胶小球中,其余的制备条件同实施例1。经分析,活性组分钯活性位为35.6%,活性组分平均粒径8.3nm,活性组分呈“蛋壳”型分布,蛋壳平均厚度147μm。催化剂评价条件同实施例1,将反应得到的混合物冷却、气液分离后通过气相色谱分析。经分析,该催化剂活性为322.3g/l/h,醋酸烯丙酯选择性为87.8%。持续评价1000h后,催化剂活性为300.2g/l/h,醋酸烯丙酯选择性为86.8%,催化剂活性和选择性不能满足工业化使用要求。
[0082]
【对比例3】根据cn 101657259 b中优选方案制备催化剂并进行性能评价
[0083]
取1l硅胶小球,配制445ml含有6.0gpd、0.8gcu和0.6gau的氯钯酸钠、硫酸铜和氯金酸水溶液,浸渍到硅胶小球至完全吸收,将35.6g九水硅酸钠溶于 890ml去离子水中,并将浸渍后的硅胶小球放入,静置20h;然后加入33.3g浓度为80%的水合肼水溶液,静置4h,充分洗涤后,在110℃温度下干燥4h,得到催化剂前驱体;取60g醋酸钾溶于400g去离子水中,浸渍到催化剂前驱体上,在110℃温度下干燥4h,得到催化剂成品。
[0084]
经分析,活性组分钯活性位为38.7%,活性组分平均粒径6.3nm,活性组分呈“蛋壳”型分布,蛋壳平均厚度397μm。催化剂评价条件同实施例1,将反应得到的混合物冷却、气液分离后通过气相色谱分析。经分析,该催化剂活性为387.1 g/l/h,醋酸烯丙酯选择性为83.8%。持续评价2000h后,催化剂活性为302.6g/l/h,醋酸烯丙酯选择性为82.1%,催化剂活性和选择性明显降低。
[0085]
从以上测试结果可以看出:
[0086]
(1)通过实施例1和对比例1可以看出,实施例1通过在载体表面气相沉积一层碱金属可以制备活性组分呈“蛋壳”型分布的催化剂,对比例1未采用气相沉积碱金属制备的活性组分呈均匀型分布,并且对比例1中催化剂的活性和选择性明显低于实施例1中的催化剂活性和选择性;
[0087]
(2)通过实施例1和对比例2可以看出,活性组分溶液中不添加腐植酸制备的催化剂不易形成钯基合金,暴露的钯活性位明显减少,且对比例2中的催化剂活性和选择性明显低于实施例1中的催化剂活性和选择性;
[0088]
(3)通过实施例1与对比例3对比可知,本发明方案相对于先浸渍活性组分后迁移制备“蛋壳”型催化剂的方案,表现出更高的催化剂活性和选择性。
[0089]
以上所述仅是本发明的优选实施方式,应当指出,对于本领域技术的普通技术人员,在不脱离本发明方法的前提下,还可以做出若干改进和补充,这些改进和补充也应视为本发明的保护范围。