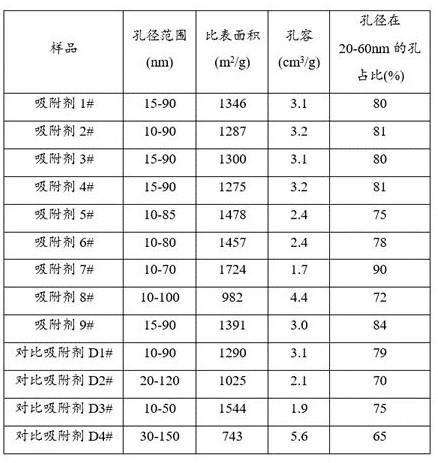
1.本技术涉及一种从石油伴生气中回收二氧化碳的方法,属于二氧化碳回收利用技术领域。
背景技术:2.石油伴生气是指在油田开采过程中,随石油液体出现的气体,其主要成分为甲烷,还含有一定量的二氧化碳、乙烷、氮气、硫化氢和重烃等,通常生产中先将重烃进行分离,再回收二氧化碳,之后再采用加压的方式将伴生气中的甲烷和乙烷回收,实现石油伴生气中各种气体的分离。
3.目前二氧化碳的回收中通常采用吸收分离、膜分离、吸附分离和低温冷凝等方式,然而上述分离方式回收的二氧化碳中含有一定量的氮气和硫化氢,回收得到的二氧化碳纯度不高,掺杂的杂质会在二氧化碳的后续利用中造成负面影响,阻碍后续二氧化碳的重复使用,严重时将会危害人体健康和生态环境。
技术实现要素:4.为了解决上述问题,提供了一种从石油伴生气中回收二氧化碳的方法,该方法先将伴生气中的重烃和水分除去,得到气体a,再使用吸附剂对气体a中的二氧化碳进行选择性吸附,该吸附剂能够快速对二氧化碳进行吸附,并且提高二氧化碳的吸附纯度,使用再生气体再将吸附剂内吸附的二氧化碳进行脱附,可实现吸附剂的重新利用。
5.根据本技术的一个方面,提供了一种从石油伴生气中回收二氧化碳的方法,该方法包括下述步骤:(1)对伴生气进行加压,分离伴生气中的重烃和水分,得到富含二氧化碳的气体a;(2)将气体a与吸附剂接触,以脱除所述气体a中的二氧化碳,得到不含二氧化碳的气体b,吸附剂内吸附有二氧化碳;(3)将所述吸附剂与再生气体接触,以将所述吸附剂内的二氧化碳脱附得到混合气,将混合气中的再生气体与二氧化碳分离,回收得到二氧化碳;所述吸附剂由第一单体、第二单体和吲哚聚合制得,所述第一单体选自3-丁烯-1-胺、顺丁烯二酰肼和4-戊烯-1-胺中的任意一种或多种,所述第二单体为四乙烯基锡和n,n-亚甲基双丙烯酰胺。
6.可选地,所述吸附剂的制备方法包括下述步骤:s1:将重量比为(0.8-1.5):(1-5)的第一单体和第二单体进行预聚得到预聚中间体,所述预聚中间体的聚合度为20-50;s2:向含有所述预聚中间体的溶液中加入吲哚和催化剂聚合,后处理后得到所述吸附剂,其中吲哚与第二单体的重量比为(1-3):1。
7.可选地,所述第一单体和第二单体的重量比为1.5:1;和/或所述吲哚与第二单体的重量比为2:1。
8.可选地,所述第一单体中,3-丁烯-1-胺、顺丁烯二酰肼和4-戊烯-1-胺的重量比为(3-10):(5-15):(0-4)。
9.可选地,所述第二单体中,四乙烯基锡和n,n-亚甲基双丙烯酰胺的重量比为(2-5):1。
10.优选的,所述第一单体中,3-丁烯-1-胺、顺丁烯二酰肼和4-戊烯-1-胺的重量比为5:15:2,所述第二单体中,四乙烯基锡和n,n-亚甲基双丙烯酰胺的重量比为3:1。上述第一单体和第二单体的配比能够提高吸附剂中氨基基团的含量,而吲哚能够影响吸附剂的交联度,从而影响吸附剂的孔径及孔径分布,在上述各单体的配比下,吸附剂的孔径呈一定的分布,既有利于气体a进入到吸附剂内部,又有利于提高吸附剂对二氧化碳的吸附效率和吸附量。
11.可选地,步骤s1中,将第一单体、第二单体和引发剂溶入溶剂中,搅拌均匀,升温至60-80℃,在氮气氛围下反应2-5h后得预聚中间体;所述引发剂为偶氮类、过硫酸类或过氧类引发剂中的任意一种或多种。
12.可选地,步骤s2中,将含有所述预聚中间体的溶液温度调节至70-110℃,加入所述吲哚和催化剂,搅拌均匀,在氮气氛围下反应至少8h,经纯化和干燥后得到所述吸附剂;所述催化剂为alcl3、bf3、sbcl5、febr3、fecl3、sncl4、ticl4、zncl2中的任意一种或多种。
13.所述溶剂为水、甲醇、乙醇、己烷、n,n-二甲基甲酰胺、二甲基亚砜、苯、甲苯、二甲苯、乙醚、丙酮中的任意一种或多种。
14.优选的,所述纯化包括使用去离子水和/或溶剂洗涤,并在超声仪器中进行震荡洗涤,所述干燥为在50-80℃下真空干燥至少15h。
15.可选地,所述吸附剂还包括铈锆复合氧化物,步骤s2中,加入所述吲哚和催化剂,搅拌均匀,在氮气氛围下反应0.5-1h后加入所述铈锆复合氧化物,继续搅拌反应至少7.5h,再经纯化和干燥后得到所述吸附剂。
16.可选地,所述铈锆复合氧化物的重量占所述吲哚重量的2%-5%,优选为4%。
17.加入的铈锆复合氧化物为现有技术中制备或购买的,该铈锆复合氧化物自身为多孔材料,其加入后在步骤s2中,形成的反应产物能够附着在铈锆复合氧化物的表面,可将二氧化碳储存在铈锆复合氧化物的内部,提高二氧化碳的吸附量;并且铈锆复合氧化物本身含有纳米级的孔洞,能够在吸附剂形成多孔材料是提供交联位点,便于吸附剂的成型,对吸附剂的孔道起到支撑作用,巩固吸附剂的孔道结构,避免吸附剂在多次使用中出现孔道坍塌,提高吸附剂的再生性能。
18.铈锆复合氧化物在后续的纯化过程中会有一部分的铈锆复合氧化物从吸附剂表面脱除,该脱除的铈锆复合氧化物能够增加吸附剂表面的孔径,便于气体a进入到吸附剂内部进行二氧化碳的吸附。
19.可选地,步骤(1)中,所述伴生气加压的压力为3-3.5mpa,温度为15-25℃;步骤(2)中,气体a与吸附剂接触的压力为0.2-0.5mpa,温度为30-90℃,气体a的通入速度为100-200l/h;步骤(3)中,再生气体为水蒸气,吸附剂与水蒸气接触的温度为110-120℃,压力为0.1-0.4mpa,水蒸气的通入速度为50-80l/h,将混合气体通入水中以使得混合气体中的水
蒸气与二氧化碳分离。
20.本技术的有益效果包括但不限于:1.根据本技术的从石油伴生气中回收二氧化碳的方法,通过步骤(1)先将伴生气中的重烃和水分去除,提高气体a的清洁度,再使用是吸附剂对气体a中的二氧化碳进行选择性吸附,提高二氧化碳的回收纯度,进而可将回收后的二氧化碳重复利用。
21.2.根据本技术的从石油伴生气中回收二氧化碳的方法,吸附剂与气体a接触即可将气体a中的二氧化碳进行吸附得到气体b,气体b再通过后处理即可将甲烷和其余气体进行分离,可有效将伴生气中各种成分进行分离。
22.3.根据本技术的吸附剂,所使用的原料单体易得且毒性小,原料反应生成的吸附剂为多孔材料,吸附剂的孔径在10-100nm之间,并呈现一定的分布,其中孔径在20-60nm之间的孔占比最多,能够为二氧化碳的吸附提供较多的吸附点位,提高单位面积内二氧化碳的吸附量。
23.4.根据本技术的吸附剂,合成的预聚中间体具有初步交联迹象,加入吲哚之后,预聚中间体与吲哚的苯环发生傅克烷基化反应,从而得到交联后的多孔吸附剂,吸附剂表面含有大量的仲胺和伯胺基团,其中仲胺的占比更多,能够对二氧化碳进行选择性吸附,降低对伴生气中其他气体的吸附,回收的二氧化碳的纯度最高可达98%以上。
24.5.根据本技术的吸附剂,低温下对气体a中的二氧化碳进行吸附,并使用水蒸气在高温下将吸附剂中的二氧化碳进行脱附,吸附剂能够循环使用,提高吸附剂的循环使用率,节约生产成本。
具体实施方式
25.下面结合实施例详述本技术,但本技术并不局限于这些实施例。
26.如无特别说明,本技术的实施例中的原料和催化剂均通过商业途径购买,本技术的实施例中,利用傅里叶变换红外光谱仪对吸附剂进行红外光谱分析,将所得的吸附剂在室温下,采用衰减全反射模式进行测试分析。
27.利用得到的吸附剂对石油伴生气中的二氧化碳进行捕集,将石油伴生气经过步骤(1)重烃和水分的分离后得到气体a,将气体a通入含有吸附剂的吸附装置,控制吸附剂进行吸附的温度为70℃,压力为常压,其中吸附装置为现有技术中的常见吸附装置,使用吸附剂对气体a中的二氧化碳进行吸附。吸附完成后的吸附装置停止通入气体a,之后向吸附装置中通入水蒸气对吸附剂进行脱附得到混合气体,控制脱附的温度为110℃,将混合气体通入水中即可实现再生气体与二氧化碳气体的分离,回收吸附的二氧化碳,计算回收后二氧化碳的纯度,并且将脱附后的吸附剂重复上述吸附与脱附过程,计算五次吸附-脱附循环后吸附剂的吸附量。
28.实施例1本实施例设计一种吸附剂的制备方法,该制备方法括下述步骤:s1:将重量比为(0.8-1.5):(1-5)的第一单体和第二单体溶于溶剂中,加入偶氮二异丁腈引发剂,搅拌均匀,升温至60-80℃,在氮气氛围下反应2-5h后得预聚中间体;s2:将含有预聚中间体的溶液温度调节至70-110℃,加入吲哚和催化剂,其中吲哚与第二单体的重量比为(1-3):1,聚合,搅拌均匀,在氮气氛围下反应至少8h,经纯化和干燥
后得到吸附剂。
29.优选的,步骤s2中,将含有预聚中间体的溶液温度调节至70-110℃,加入吲哚和催化剂,搅拌均匀,在氮气氛围下反应0.5-1h后加入铈锆复合氧化物,继续搅拌反应至少7.5h,再经纯化和干燥后得到吸附剂,其中加入的铈锆复合氧化物的重量占吲哚重量的2%-5%。
30.根据上述制备方法制备吸附剂1#-9#和对比吸附剂d1#-d4#,具体合成过程如下:吸附剂1#s1:分别称量17.0g的3-丁烯-1-胺、51.1g的顺丁烯二酰肼和6.9g的4-戊烯-1-胺溶于600.0g 溶剂中,溶剂为去离子水和乙醇,去离子水和乙醇的重量比为3:1,之后再向溶剂中加入37.5g的四乙烯基锡、12.5g的n,n-亚甲基双丙烯酰胺和2.0g的偶氮二异丁腈,升温至70℃,在氮气氛围下反应3h后得预聚中间体;s2:将含有预聚中间体的溶液温度升温至80℃,加入100.0g的吲哚和5.0g alcl3,搅拌均匀,在氮气氛围下反应12h,经纯化和干燥后得到吸附剂1#。
31.吸附剂2#吸附剂2#与吸附剂1#的区别在于,步骤s1中第一单体中各个原料的重量发生改变,分别称量11.3g的3-丁烯-1-胺、56.2g的顺丁烯二酰肼和7.5g的4-戊烯-1-胺溶于600.0g 溶剂中,剩余步骤与吸附剂1#相同,得到吸附剂2#。
32.吸附剂3#吸附剂3#与吸附剂1#的区别在于,步骤s1中第一单体中各个原料的重量发生改变,分别称量37.5g的3-丁烯-1-胺和37.5g的顺丁烯二酰肼溶于600.0g 溶剂中,剩余步骤与吸附剂1#相同,得到吸附剂3#。
33.吸附剂4#吸附剂4#与吸附剂1#的区别在于,步骤s1中第一单体中各个原料的重量发生改变,分别称量37.5g的3-丁烯-1-胺、22.5g的顺丁烯二酰肼和15.0g的4-戊烯-1-胺溶于600.0g 溶剂中,剩余步骤与吸附剂1#相同,得到吸附剂4#。
34.吸附剂5#吸附剂5#与吸附剂1#的区别在于,步骤s1中第一单体的总重量发生改变,第一单体中各个原料的配比不变,分别称量5.7g的3-丁烯-1-胺、17.0g的顺丁烯二酰肼和2.3g的4-戊烯-1-胺溶于600.0g 溶剂中,剩余步骤与吸附剂1#相同,得到吸附剂5#。
35.吸附剂6#吸附剂6#与吸附剂1#的区别在于,步骤s1中第二单体中各个原料的重量发生改变,步骤s1中,分别称量17.0g的3-丁烯-1-胺、51.1g的顺丁烯二酰肼和6.9g的4-戊烯-1-胺溶于600.0g 溶剂中,溶剂为去离子水和乙醇,去离子水和乙醇的重量比为3:1,之后再向溶剂中加入41.7g的四乙烯基锡、8.3g的n,n-亚甲基双丙烯酰胺和2.0g的偶氮二异丁腈,升温至70℃,在氮气氛围下反应3h后得预聚中间体,剩余步骤与吸附剂1#相同,得到吸附剂6#。
36.吸附剂7#吸附剂7#与吸附剂1#的区别在于,步骤s2中,加入吲哚的重量发生改变,步骤s2中,将含有预聚中间体的溶液温度升温至80℃,加入150.0g的吲哚和5.0g alcl3,搅拌均匀,在氮气氛围下反应12h,剩余步骤与吸附剂1#相同,得到吸附剂7#。
37.吸附剂8#吸附剂8#与吸附剂1#的区别在于,步骤s2中,加入吲哚的重量发生改变,步骤s2中,将含有预聚中间体的溶液温度升温至80℃,加入50.0g的吲哚和5.0g alcl3,搅拌均匀,在氮气氛围下反应12h,剩余步骤与吸附剂1#相同,得到吸附剂8#。
38.吸附剂9#吸附剂9#与吸附剂1#的区别在于,步骤s2中,还加入了铈锆复合氧化物,步骤s2中,将含有预聚中间体的溶液温度升温至80℃,加入100.0g的吲哚和5.0g alcl3,搅拌均匀,在氮气氛围下反应0.5h后加入4.0g的铈锆复合氧化物,继续搅拌反应11.5h,剩余步骤与吸附剂1#相同,得到吸附剂9#。
39.对比吸附剂d1#对比吸附剂d1#与吸附剂1#的区别在于,步骤s1中的顺丁烯二酰肼替换为n-(羟甲基)丙烯酰胺,步骤s1中,分别称量5.7g的3-丁烯-1-胺、17.0g的n-(羟甲基)丙烯酰胺和2.3g的4-戊烯-1-胺溶于600.0g 溶剂中,剩余步骤与吸附剂1#相同,得到对比吸附剂d1#。
40.对比吸附剂d2#对比吸附剂d2#与吸附剂1#的区别在于,步骤s1中的四乙烯基锡替换为三乙烯二胺,步骤s1中,分别称量17.0g的3-丁烯-1-胺、51.1g的顺丁烯二酰肼和6.9g的4-戊烯-1-胺溶于600.0g 溶剂中,溶剂为去离子水和乙醇,去离子水和乙醇的重量比为3:1,之后再向溶剂中加入37.5g的三乙烯二胺、12.5g的n,n-亚甲基双丙烯酰胺和2.0g的偶氮二异丁腈,升温至70℃,在氮气氛围下反应3h后得预聚中间体,剩余步骤与吸附剂1#相同,得到对比吸附剂d2#。
41.对比吸附剂d3#对比吸附剂d3#与吸附剂1#的区别在于,步骤s1中,第二单体仅选用单一的四乙烯基锡,步骤s1中,分别称量17.0g的3-丁烯-1-胺、51.1g的顺丁烯二酰肼和6.9g的4-戊烯-1-胺溶于600.0g 溶剂中,溶剂为去离子水和乙醇,去离子水和乙醇的重量比为3:1,之后再向溶剂中加入50.0g的四乙烯基锡和2.0g的偶氮二异丁腈,升温至70℃,在氮气氛围下反应3h后得预聚中间体,剩余步骤与吸附剂1#相同,得到对比吸附剂d3#。
42.对比吸附剂d4#对比吸附剂d4#与吸附剂1#的区别在于,步骤s2中,加入吲哚的重量发生改变,步骤s2中,将含有预聚中间体的溶液温度升温至80℃,加入25.0g的吲哚和5.0g alcl3,搅拌均匀,在氮气氛围下反应12h,剩余步骤与吸附剂1#相同,得到对比吸附剂d4#。
43.对所制得的吸附剂1#-9#和对比吸附剂d1#-d4#进行孔径、比表面积和孔容进行测试,具体测试结果见下表1。
44.表1
将石油伴生气经过步骤(1)重烃和水分的分离后得到气体a,气体a中二氧化碳的占比为20%-40%,甲烷的占比为20%-50%,硫化氢的占比为1%-5%,剩余还有少量的氮气、氮氧化物和水蒸气,将上述吸附剂1#-9#、对比吸附剂d1#-d4#固定与吸附装置中,吸附剂的用量为10.0g,向吸附装置中通入气体a,气体a的气体流量为120l/h,在温度为70℃,压力为0.5 mpa下,吸附剂对气体a中的二氧化碳进行吸附,并使用水蒸气在110℃下进行脱附得到混合气,压力为0.2 mpa下,水蒸气的通入速度为50 l/h,吸附剂与气体a的吸附时间为2h,测试上述吸附剂对于二氧化碳的吸附量和回收后二氧化碳的纯度,并测试五次循环后上述吸附剂对于二氧化碳的吸附量和回收得到的二氧化碳的纯度,具体测试结果见下表2。表2中的五次循环后吸附是指吸附剂经历五次吸附-脱附循环后的第六次吸附。
45.表2
根据上表1和表2可知,各个单体的加入量将会影响吸附剂的交联度,进而影响吸附剂的孔径、比表面积和孔容,吸附剂7#相比于吸附剂1#而言,交联程度变大,吸附剂7#的孔径和孔容表小,比表面积增大,虽然比表面积增大能够提供较多的二氧化碳吸附点位,但是由于孔径变小,不利于气体a进入吸附剂内部,孔容变小也降低了二氧化碳在吸附剂7#的储存量,导致二氧化碳的吸附量降低;吸附剂8#和对比吸附剂d4#与吸附剂1#对比,吸附剂8#和对比吸附剂d4#的交联程度变低,孔径和孔容增大,虽然有利于气体a进入吸附剂内部,但是由于比表面积减少,吸附点位变少,二氧化碳的吸附量也显著降低。
46.对比吸附剂d1#-d3#更换了第一单体或第二单体的原料,更换的原料直接影响吸附剂的吸附量和吸附纯度,对气体a中的二氧化碳不能进行特异性吸附。吸附剂中加入铈锆复合氧化物有利于吸附剂形成均匀的孔道,并提高吸附剂比表面积的同时,也能维持较大的孔容积,提高二氧化碳的吸附量和吸附纯度,并且铈锆复合氧化物能够提高吸附剂孔道的稳定性,在多次吸附-脱附循环后仍能保持较高的吸附量和吸附纯度。
47.实施例2本实施例涉及从石油伴生气中回收二氧化碳的方法,本实施例使用实施例1中的吸附剂1#和常规的吸附装置,对石油伴生气进行处理,具体回收方法如下:(1)15-25℃下,对伴生气进行加压至压力为3-3.5mpa,分离伴生气中的重烃和水分,得到富含二氧化碳的气体a;(2)将气体a与吸附剂接触,气体a与吸附剂接触的压力为0.2-0.5mpa,温度为30-90℃,气体a的通入速度为100-200l/h,以脱除所述气体a中的二氧化碳,通入时间为3h,得
到不含二氧化碳的气体b;(3)将所述吸附剂与水蒸气接触,吸附剂与水蒸气接触的温度为110-120℃,压力为0.1-0.4mpa,水蒸气的通入速度为50-80l/h,以将所述吸附剂内的二氧化碳脱附得到混合气,将混合气中的水蒸气与二氧化碳分离,回收得到二氧化碳。
48.使用上述方法对石油伴生气进行处理,其中石油伴生气中重烃的占比为10%-20%,水蒸气的占比为5%-10%,二氧化碳的占比为15%-35%,甲烷的占比为15%-45%,硫化氢的占比为0.5%-4%,剩余还有氮气和氮氧化物,具体的方法不同之处见下表3。
49.表3通过上述方法对回收后的二氧化碳的纯度及回收量进行统计,具体结果见下表4。
50.表4根据上述回收方法中各个步骤条件参数的变化可知,步骤(1)的温度及压力影响重烃的分离效率,进而影响吸附剂对吸附剂的吸附量和回收后二氧化碳的纯度;通过方法3和方法4与方法1的对比可知,吸附剂与气体a接触的温度会影响吸附剂的吸附量,气体a的通入速度过大时,虽然会增加吸附剂对二氧化碳的吸附量,但是会降低二氧化碳的回收纯度,另外若气体a的通入速度过快,则会使得吸附剂对气体a中的二氧化碳吸附不完全,气体b中仍会残存少量的二氧化碳;通过方法5和方法6与方法1的对比可知,水蒸气与吸附剂接触的温度及水蒸气的通入速度会影响吸附剂内的二氧化碳的脱附量,然而对于回收纯度的影响不大。
51.以上所述,仅为本技术的实施例而已,本技术的保护范围并不受这些具体实施例的限制,而是由本技术的权利要求书来确定。对于本领域技术人员来说,本技术可以有各种更改和变化。凡在本技术的技术思想和原理之内所作的任何修改、等同替换、改进等,均应包含在本技术的保护范围之内。