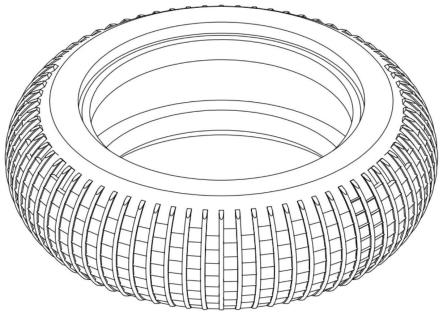
1.本发明涉及一种磨辊,属于金属材料及加工技术领域。
背景技术:2.近年来,立式磨机(简称:立磨)在水泥、火力发电等行业有着越来越多的应用,磨辊是立磨上最容易磨损,最容易失效的,最关键的零部件,因磨辊易磨损、易失效等原因,影响立式磨机的正常运转,由于磨辊的严重磨损或非正常失效,导致立磨停止运行,带来很大的经济损失。为此,研制一种使用安全,使用寿命长的磨辊显得尤为重要,一种安全的磨辊能避免频繁出现失效,更能提高经济效益。
3.关于磨辊的材料及其工艺,科研工作者和相关企业生产者进行了大量的研发工作,研制了多种具有优良性能的磨辊。如专利cn 111590053b,公开了“一种易加工、可修复高耐磨金属陶瓷复合磨辊的制造方法”,首先将陶瓷颗粒进行表面金属化预处理,然后将陶瓷颗粒与粘结剂均匀混合并在混合物中加陶瓷粉末,将颗粒混合物均匀装入泡沫陶瓷模具干燥,干燥出箱后脱模后得陶瓷预制件,然后顺次浇注耐磨合金金属液、碳钢金属液,得到由工作面垂直向下分别为陶瓷预制件/耐磨合金/碳钢三层的金属陶瓷辊皮衬板。该技术磨辊的工作部位使用的是陶瓷材料,陶瓷材料的突出特点是硬度高,韧性差,相比该磨辊的非工作面用的碳钢来说,硬度虽然高于非工作面,韧性远低于非工作面,所以使用时安全性没有保证,陶瓷预制件因为韧性差,很容易出现脱落或大面积裂开等失效情况。另外,陶瓷颗粒虽然经过表面金属化预处理,也很难保证就能与金属液完全熔合。再是专利中对于耐磨合金的材质为高铬铸铁或高锰钢,高锰钢初始硬度hb200左右,跟陶瓷(陶瓷硬度一般大于hb600)相比硬度差距太大,这种配合是非常不合理的。专利cn 210022447 u,公开了一种“磨煤机用耐磨辊套”,该辊套的主要特征是辊套本体由内到外依次包括内衬层、陶瓷颗粒层和外皮层,该专利主要应用工况是磨煤机,陶瓷颗粒层全面覆盖了辊套的磨损部位,大幅度提高了辊套的寿命。该技术辊套的磨损部位大面积、大量使用了高硬度、低韧性的陶瓷材料。专利cn111185273a,提供了“一种金属陶瓷复合磨辊及其制备方法”。该陶瓷复合辊由辊芯和辊芯外侧的高铬铸铁层组成,陶瓷预制块镶嵌在高铬铸铁层,所述陶瓷预制块由氧化锆增强氧化铝陶瓷制备而成。本发明提供的金属陶瓷复合磨辊通过高铬铸铁层将辊芯和由特定陶瓷制成的陶瓷预制块熔渗复合,形成整体结构,内部辊芯易加工,外部陶瓷预制块具有高硬度特性,既保证了耐磨性,又保证了抗冲击性能,同时节约了高碳铬铁,本发明提供的金属陶瓷复合磨辊的使用寿命能够达到530h,且磨损后期,高铬铸铁牢固地贴合在碳钢辊芯外侧,未开裂或脱落。该技术陶瓷预制块镶嵌在高铬铸铁层,高铬铸铁本身已经是脆性材料,在高铬铸铁材料上面再镶嵌硬度高韧性差的陶瓷材料,无疑是脆上加脆,难以应对复杂的工况环境。专利cn114939646a,公开了“一种tic金属陶瓷颗粒增强复合耐磨磨辊及其制备工艺”,本发明中tic金属陶瓷颗粒与铁基体的熔融润湿角小于30度,tic金属陶瓷颗粒与合金基体的热膨胀系数接近,化学键极性相似,因此与基体的结合强度高,使用过程中不易脱落,显著高于zta,可应用于有较高挤压或冲击载荷的工况。该发明的磨辊采用的是tic
金属陶瓷颗粒与铁基体,使用部位是陶瓷颗粒。
4.专利cn 212943173 u,提出了一种“带复合耐磨钉的辊套”,辊套的特征在于辊套本体表面设置有第一耐磨钉和多个第二耐磨钉,第一耐磨钉的外端面为直条形结构,第二耐磨钉的裸露部分为圆柱形结构,第二耐磨钉和第一耐磨钉错位设置,该专利有益技术效果是:提出了一种带复合耐磨钉的辊套,该辊套上设置有两种结构的耐磨钉,可以有效提高辊套的结构性能。该技术只是设计了这样一个结构的辊套,对于耐磨钉的材料,辊套的材料没有明确规定。专利cn110846582a,公开了“一种辊压机中的挤压辊辊套及其制备方法”,辊压机中的挤压辊辊套包括母体,母体外部由熔敷金属a和熔敷金属b硬质合金块组成。硬质合金块均匀地镶铸在母体的外圆上,轴向上间隔整齐排列,熔敷金属a轴向方向上堆焊在所述硬质合金块圆周间隙中,熔敷金属b堆焊在所述熔敷金属a上面,所述熔敷金属b的平均高度大于所述硬质合金块的高度。本发明的挤压辊辊套大幅增加了耐磨性、延长了使用寿命,挤压辊辊套始终处于高效状态,节约成本。其熔敷金属b堆焊在所述熔敷金属a上面,所述熔敷金属b的平均高度大于所述硬质合金块的高度,这样的设计难以保证熔敷金属a和熔敷金属b的稳定性,在工况恶劣的情况下,熔敷金属a和熔敷金属b很容易发生脱落,引起辊套的失效,严重影响正常生产。
5.专利cn 104630610b,发明了“超级耐磨复合立磨辊套及其制作方法”。该超级耐磨复合立磨辊套,包括超耐磨的外层和高韧性的内层的双层结构,外层为含量大于35%的碳化物超耐磨铸铁,内层为高韧性中碳低合金钢,外层与内层靠冶金结合在一起,彻底消除了由于焊接微裂纹带来的掉块、剥落等失效形式,可以做到终身免维护。它用含量35%以上的碳化物超耐磨铸铁材料,其硬度很高的同时,韧性必然很低,所以设计的思路是工作部位高硬度,而忽略了韧性这决定性因素。专利cn 103170392a,发明了一种立磨双金属磨辊,用于水泥和电力工业的立磨双金属磨辊,包括芯体和外硬面层,所述芯体和外硬面层通过离心复合铸造为一体,外硬面层为高速合金钢:0.7%~4.0%碳、《2%硅、《2%锰、4%~18%铬、0.5%~4%镍、3%~10%钒、2%~10%钼、0.5%~7%铌、0~2%钴、0.5%~8%钨。该技术不足之处是:一是芯体和外硬面层通过离心复合铸造为一体,工艺复杂,如果控制不好,可能会不能得到冶金结合较好的铸件,二是外层高速合金钢里面含有大量的贵金属材料,无疑是增加了成本,既然外层为高速合金钢,其中的碳含量设置为0.7~4.0%碳,当碳含量达到4%的时候,已经不是钢的范畴。另外,该双金属磨辊的外面结构没有进行改进。
6.专利cn 114086068 a,一种高耐磨磨辊及其制备方法,高耐磨磨辊包括镶块a、镶块b和基体,镶块a、镶块b均为一头粗一头细的棒状结构,所述的棒状结构埋设在基体中,棒状结构的细头端面露在基体表面与基体表面形成磨辊的工作面,且镶块a与镶块b的细头端面间隔均匀地交错分布于基体表面;其中镶块a采用中高合金钢,镶块b采用超高合金铸铁,基体采用中合金钢。该磨辊具有良好的安全性和耐磨性,使用范围广泛,不易断裂易于回收利用。该技术的不足之处是工作部位依然采用了镶块a和镶块b两种高硬度的材料,在磨辊受力过大或者受力不均匀的情况下,存在异常失效的隐患,不能保证磨辊的安全正常运转。
7.综上所述,目前有关磨辊的技术中主要存在以下不足:
8.(1)现有磨辊的为了提高产品的耐磨性,延长使用寿命,大部分产品都使用了陶瓷或陶瓷颗粒占大部分比重的预制体或类似陶瓷的预制体,将这类高硬度低韧性的材料作为预制体,这种设计镶嵌的材料虽然具有较高的硬度和耐磨性,但韧性却比基体材料有了很
大程度的降低,在磨辊及相关产品使用时,会因为韧性低,出现开裂、脱落、失效等情况,从而造成磨辊等产品失效,不能保证设备的正常运转,使用安全的考虑不足。
9.(2)对于采用金属嵌块与金属基体结合的结构,一方面结合方式都是简单的物理复合,对于镶嵌预制体和磨辊基体的材料化学成分、热处理工艺、熔炼工艺等考虑和涉及的较少,使用过程中存在脱离的风险;另一方面虽然有些技术对镶嵌的材料的外观、形状及相关结构尺寸进行了设计,但实际设计的主观性较强,没有根据磨辊产品的使用工况对结构形状等细节进行精准的设计,在使用过程中,往往局部因受力不匀或韧性不足等问题,引起脱落或掉块或开裂。
10.磨辊的局部受力部位相对于磨辊的基体而言,更需要优良的韧性和硬度,在使用过程中,往往局部因受力不匀或韧性不足等问题,引起脱落或掉块或开裂,从而导致磨辊非正常失效,因此开发一种磨辊局部性能优异的磨辊材料显得尤为重要。
技术实现要素:11.本发明的目的是克服上述不足而提供一种立磨磨辊及其制备方法,能延长使用寿命,保证使用安全。
12.本发明采取的技术方案为:
13.一种立磨磨辊,包括磨辊基体和镶块,镶块包括纵向镶块条和横向镶块条,纵向镶块条和横向镶块条都有与基体外表面贴合的弧度,纵向镶块条间隔排列均匀分布于基体表面,相邻两纵向镶块条间有多组横向镶块条均匀分布,各镶块条与基体融合的那部分(即嵌入基体内的部分)全部采用纵截面为梯形的结构,露在基体外面的部分,纵向镶块条采用纵截面为半圆形的结构,横向镶块条采用纵截面为等边三角形的结构,所述的镶块部分采用中铬合金钢,基体采用高铬合金钢。
14.所述的基体采用的高铬合金钢材料,其化学成分重量百分比:c:1.315~1.429%,si:0.327~0.465%,mn:0.881~0.926%,s≤0.026%、p≤0.028%,cr:13.281~15.197%,ni:0.621~0.703%,mo:0.891~0.923%,cu:0.627~0.639%,v:0.215~0.338%,ti:0.0299~0.0415%,re:0.132~0.219%,b:0.0811~0.0953%,nb:0.116~0.178%,w:0.233~0.349%,zr:0.0391~0.0456%,al:0.0325~0.0449%,n:0.0018~0.0045%,余量为fe及杂质。
15.所述的镶块部分采用的中铬合金钢材料,其化学成分重量百分比:c:0.568~0.617%,si:0.325~0.457%,mn:0.587~0.751%,s、p≤0.025%,cr:6.155~6.338%,ni:0.183~0.269%,mo:1.115~1.577%,cu:0.513~0.628%,v:1.715~1.747%,ti:0.021~0.0315%,re:0.03~0.04%,b:0.0031~0.0039%,nb:0.268~0.291%,w:0.353~0.464%,al:0.0355~0.0416%,n:0.056~0.078%,余量为fe及杂质,且杂质的总量≤0.038%。
16.上述的纵向镶块条和横向镶块条其在基体内和露在基体外部分为无界面一体结构。各镶块条与基体融合的部分优选采用纵截面为等腰梯形的结构。镶块露在基体外面的部分与埋入基体的部分高度一致。
17.上述的露在基体外面的部分,纵向镶块条采用纵截面为半圆形的结构的半圆形直径为9.6~15.8mm,横向镶块条优选采用纵截面为等边三角形的结构,等边三角形边长为
9.0~15.8mm。
18.上述立磨磨辊的制备方法为:先铸造镶块部分的毛坯并锻造成型,将镶块部分按设计结构预埋到磨辊的铸型内,浇注磨辊基体铁液,基体铁液与镶块冶金结合,获得磨辊毛坯,磨辊毛坯经过退火、淬火、回火获得磨辊成品。
19.所述立磨磨辊的制备方法,具体包括步骤如下:
20.(一)制备镶块预制体
21.(1)准备原材料
22.称取废钢、硅铁、锰铁、铬铁、镍铁、钼铁、铜、钒铁、钛铁、硼铁、铌铁、钨铁、铝线、氮化铬、稀土硅铁材料;
23.(2)造型
24.利用砂型进行造型;
25.(3)原料的熔炼
26.将原材料进行熔炼,熔炼顺序按照废钢、铁合金、废钢、贵重金属的顺序,当铁液达到1506℃~1557℃时,进行预脱氧处理,先加入0.55%锰铁,再加入0.25%硅铁,化验铁水化学成分,调整铁液化学成分重量百分比满足所述中铬合金钢的要求,当炉内铁液温度达到1635℃~1646℃,插入0.028%铝线,然后出炉;
27.(4)孕育浇注
28.将得到的铁液倒入浇包进行变质孕育,铁水经过孕育之后,浇入铸型,冷却至室温获得毛坯;
29.(5)锻造成型
30.将得到的毛坯进行打磨,清理干净之后,放入加热炉进行加热,加热温度控制在1066~1168℃,保温时间2~2.5小时,保温后,将毛坯放入模具中进行锻造成型,始锻温度为1o65~1155℃,终锻温度≥898℃,锻造之后获得镶块预制体,锻造成型的预制体经过再次清理打磨之后待用;
31.(二)制备复合磨辊
32.(1)准备原材料
33.称取废钢、硅铁、锰铁、低碳铬铁、镍铁、钼铁、铜、电解钒、钛铁、稀土硅铁、硼铁、铌铁、钨铁、锆铁、铝线、氮化铬材料;
34.(2)造型
35.将镶块预制体放入铸型造型过程中确保镶块预制体均匀分布于铸型内部,浇注之前,将镶块预制体预热至196℃~265℃;
36.(3)原料的熔炼
37.将原材料进行熔炼,熔炼顺序按照废钢、铁合金、废钢、贵重合金的顺序进行,当铁液达到1548℃~1565℃时,进行预脱氧处理,先加入0.43%锰铁,再加入0.13%硅铁,化验铁水化学成分,调整铁液化学成分重量百分比满足所述高铬合金钢的要求,当炉内铁液温度达到1628℃~1635℃,插入0.023%铝线,然后出炉;
38.(4)变质孕育浇注
39.将得到的铁液倒入浇包进行变质孕育,出炉前提前把变质孕育剂烘干,放入浇包内,浇注至磨辊铸型内,冷却至室温开箱;
40.(5)清理打磨
41.将得到的铸件去除浇冒口,然后清理打磨,得到复合铸造磨辊毛坯;
42.(三)磨辊热处理
43.(1)退火:将得到的磨辊毛坯进行装炉,退火处理;
44.(2)粗加工:将退火之后得到的磨辊按照进行粗加工;
45.(3)淬火:将粗加工得到的磨辊毛坯进行装炉,淬火处理;
46.(4)回火:将淬火之后的铸件,重新装炉,进行回火处理;
47.(5)将回火之后的磨辊进行精加工。
48.上述制备方法中,制备镶块预制体的孕育浇注中所用的孕育变质剂为:0.263%硼铁、0.121%铝线、0.256%稀土硅、0.115%碳化硅、0.138%钛铁。制备复合磨辊的变质孕育浇注中所用的孕育变质剂为:0.453%稀土硅铁、0.252%钛铁、0.234%氮化铬、0.068%锆铁、0.245%硼铁。
49.上述制备方法中,热处理中所述的退火处理工艺为:铸件入炉温度控制在185℃以下,300℃以下,升温速度控制29℃~33℃/小时,在300℃时,保温1小时,300℃~650℃之间,升温速度控制41℃~53℃/小时,650℃保温1.5小时,650℃~1006℃之间,升温速度控制62℃~75℃/小时,铸件在1106℃保温3.5~5.5小时,根据铸件壁厚适当调整,1106℃保温之后,随炉在炉内进行冷却。
50.所述的淬火处理工艺为:铸件入炉温度控制在189℃以内,300℃以内,升温速度控制38℃~45℃/小时,在300℃时,保温1小时,300℃~650℃之间,升温速度控制41℃~53℃/小时,650℃保温1.5小时,650℃~1110℃之间,升温速度控制62℃~75℃/小时,铸件在1108℃~1110℃保温3.5~4.5小时,保温时间根据铸件壁厚适当调整;保温之后,断电,随炉冷却,待炉内温度降至1046~1058℃保温1.5~2.5小时,出炉,淬火,淬火采用风冷+喷雾(水雾)的方式,铸件出炉之后就开始风冷+喷雾,待铸件温度降至685℃以下,停止喷雾,继续风冷,风冷至550℃以下,停止吹风,空气中自然冷却。
51.所述的回火处理工艺为:铸件入炉温度控制在188℃以下,升温速度控制48℃~51℃/小时,在500℃~560℃时,保温4.5~7.5小时。保温时间达到之后,出炉,空气中自然冷却,回火1-2次。
52.本发明的有益效果是:
53.(1)本发明的磨辊,镶块选用中合金钢,经过锻造之后再与基体冶金结合铸成磨辊成品,基体材料选用高铬合金钢,镶块的韧性和硬度均高于基体材料,镶块具有足够的韧性,这种设计,保证了使用部位的安全;镶块具有足够的硬度,还能保证使用部位的耐磨性;镶块与基体材料硬度接近,使用时不会出现镶块或基体一方磨损严重的情况。所以,两者相互交叉相互补充,这种材料选择和结构设计保证了安全性,也保证了耐磨性。
54.(2)本发明对镶块结构进行了设计,在基体上镶铸镶块,且纵向镶块条和横向镶块条交叉均匀分布于基体表面,纵向镶块条纵截面为半圆形的设计,纵向镶块条的设计方便物料被挤压入纵向镶块条之间形成的沟槽内;横向镶块条采用纵截面为等边三角形的设计,横向镶块条的这种设计,可以让物料进入沟槽内之后,被挤压破碎,从而提高研磨破碎效率。设备在运转时,物料被挤压入磨辊的沟槽中,同时,被挤压入沟槽的物料又被挤压破碎,这种特殊的设计结构,一方面通过把物料挤入沟槽,减轻了对磨辊基体材料的直接磨
损,另一方面又通过对沟槽内设置横向镶块条作破碎机构,对物料进行二次破碎,提高了生产效率,减轻了磨损,也就延长了磨辊的使用寿命。
55.(3)本发明所述的磨辊全部由金属材料制成,磨辊基体是高合金钢,选用镶嵌体中合金钢,与目前陶瓷金属复合相比,本发明可以有效避免因复合不好出现断裂、掉块等情况。本发明选用的材料和工艺,其韧性指标远远高于陶瓷材料,所以保证了工作部位的绝对安全,不会像陶瓷复合一样,出现脱落或开裂等情况。同时全部采用金属材料,对于使用后的旧磨辊来说,更方便回收,再次利用。而陶瓷金属复合磨辊因基体里面含有大量的陶瓷,不容易回收利用,造成资源的浪费。
56.(4)本发明磨辊经热处理后具有良好的安全性和耐磨性,其中镶块预制体选用中铬合金钢(cr6系列),预制体经过锻造之后,再与基体经过冶金结合,经过热处理之后,镶块预制体的性能达到:基体硬度达到:hrc61~63,冲击性能达到:(试样无缺口)18~26j/cm2。镶块预制体作为主要的工作部位,既保证足够的韧性,又保证足够的硬度,保证了磨辊使用的安全。基体选用高铬铸钢(cr15系列),经过铸造和热处理之后,力学性能达到:硬度:hrc58~61,冲击韧性10~16j/cm2。保证足够的硬度,以提高磨辊的耐磨性。本发明的磨辊的耐磨性是单一高铬铸铁材质磨辊2.5~3倍,具有良好的市场前景,可创造可观的经济效益。
57.本发明所述的复合磨辊材料选择合理,结构设计科学,镶嵌体具有优异的韧性和硬度,所以在高应力和硬物料工况条件下,该复合磨辊可以正常安全地运转,大大降低了事故频率,所以,磨辊的寿命得到了延长。
58.表1为几种常见的磨辊指标对比
59.60.附图说明
61.图1为本发明磨辊镶块分布示意图;
62.图2为本发明磨辊的截面图;
63.图3为本发明镶块的结构图;
64.图4为本发明磨辊镶块的金相组织图(100倍),热处理之后,4%硝酸酒精腐蚀(马氏体+少量残余奥氏体);
65.图5为本发明磨辊基体的金相组织图(100倍),热处理之后,4%硝酸酒精腐蚀(马氏体+碳化物+少量残余奥氏体);
66.其中,1.纵向镶块条,2.横向镶块条。
具体实施方式
67.下面结合附图和具体实施例进一步说明。
68.实施例1
69.一种立磨磨辊,包括磨辊基体和镶块,镶块部分包括纵向镶块条1和横向镶块条2,纵向镶块条1和横向镶块条2都有与基体外表面贴合的弧度,纵向镶块条间隔排列均匀分布于基体表面,相邻两纵向镶块条间有多组横向镶块条均匀分布,各镶块条与基体融合的那部分全部采用纵截面为等腰梯形的结构,露在基体外面的部分,纵向镶块条采用纵截面为半圆形的结构,横向镶块条采用纵截面为等边三角形的结构,所述的镶块部分采用中铬合
金钢,基体采用高铬合金钢。镶块露在基体外面的部分与埋入基体的部分高度一致。
70.其制备方法步骤如下:
71.(一)制备镶块预制体
72.(1)准备原材料
73.按照计算好的重量百分比例称取废钢、硅铁、锰铁、铬铁、镍铁、钼铁、铜、钒铁、钛铁、硼铁、铌铁、钨铁、铝线、氮化铬、稀土硅铁等材料;
74.其中,熔炼镶块预制体时用的变质剂原料:硼铁、铝线、稀土硅、碳化硅、钛铁;
75.(2)造型
76.利用树脂砂砂型进行造型;
77.(3)原料的熔炼
78.将第一步的原材料进行熔炼,熔炼顺序按照废钢、铁合金、废钢、贵重金属的顺序,贵重金属后期加入,以免烧损。当铁液达到1556℃时,进行预脱氧处理,先加入0.55%锰铁,8分钟以后再加入0.25%硅铁,化验铁水化学成分,调整铁液化学成分当炉内铁液温度达到1638℃,插入0.028%铝线,然后出炉;
79.(4)孕育变质浇注
80.将得到的铁液倒入浇包进行变质孕育,孕育变质剂为:0.263%硼铁、0.121%铝线、0.256%稀土硅、0.115%碳化硅、0.138%钛铁,铁水出炉之前,提前把这些变质剂进行烘干,混匀,放入浇包底部,铁水经过孕育之后,浇入铸型,冷却至室温得到获得毛坯;
81.(5)锻造成型
82.将得到的毛坯进行打磨,清理干净之后,放入加热炉进行加热,加热温度控制在1168℃,保温时间2~2.5小时,保温后,将毛坯放入模具中进行锻造成型,始锻温度为1155℃,终锻温度≥968℃,锻造之后获得镶嵌预制体,锻造成型的预制体经过再次清理打磨之后待用;
83.制备的镶块预制体化学成分质量百分比:c:0.617%,si:0.365%,mn:0.731%,s:0.021、p:0.025%,cr:6.338%,ni:0.259%,mo:1.577%,cu:0.593%,v:1.747%,ti:0.0315%,re:0.04%,b:0.0039%,nb:0.291%,w:0.464%,al:0.0416%,n:0.066%,余量为fe及杂质,且杂质的总量:0.028%。
84.(二)制备复合磨辊
85.(1)准备原材料
86.称取废钢、硅铁、锰铁、低碳铬铁、镍铁、钼铁、铜、电解钒、钛铁、稀土硅铁、硼铁、铌铁、钨铁、锆铁、铝线、氮化铬等材料。
87.其中,熔炼磨辊基体时用的变质剂原料:稀土硅铁、钛铁、氮化铬、锆铁、硼铁;
88.(2)造型
89.将镶块预制体放入铸型,其中,最终需要露在工作面外面的镶块体需要埋入铸型砂内部,另一部分不需要埋入铸型。目的是浇注合金液之后,不需要外露的那部分被合金液包裹,与磨辊基体合金液熔为一体,造型过程中,确保镶块预制体均匀分布于铸型内部,浇注之前,将镶块预制体预热265℃;
90.(3)原料的熔炼
91.将原材料进行熔炼,熔炼顺序按照废钢、铁合金、废钢、贵重合金的顺序进行,当铁
液达到1560℃时,进行预脱氧处理,先加入0.43%锰铁,10分钟以后再加入0.13%硅铁,化验铁水化学成分,调整铁液化学成分,当炉内铁液温度达到1629℃,插入0.023%铝线,然后出炉;
92.(4)孕育变质浇注
93.将得到的铁液倒入浇包进行变质孕育,孕育变质剂为0.453%稀土硅铁、0.252%钛铁、0.234%氮化铬、0.068%锆铁、0.245%硼铁。出炉前提前把孕育变质剂烘干,放入浇包内,浇注至磨辊铸型内,冷却至室温开箱;
94.(5)清理打磨
95.将得到的铸件去除浇冒口,然后清理打磨,得到复合铸造磨辊毛坯;
96.制备的磨辊基体的化学成分质量百分比:c:1.428%,si:0.435%,mn:0.881%,s:0.021%、p:0.023%,cr:15.197%,ni:0.703%,mo:0.923%,cu:0.639%,v:0.338%,ti:0.0415%,re:0.219%,b:0.0953%,nb:0.178%,w:0.349%,zr:0.0456%,al:0.0325%,n:0.0045%,余量为fe及杂质。
97.(三)磨辊热处理
98.(1)退火
99.将得到的磨辊毛坯进行装炉,退火处理,退火处理工艺:铸件入炉温度控制在185℃以下,300℃以下,升温速度控制33℃/小时,在300℃时,保温1小时,300℃~650℃之间,升温速度控制53℃/小时,650℃保温1.5小时,650℃~1106℃之间,升温速度控制75℃/小时,铸件在1106℃保温5.5小时,1106℃保温之后,随炉在炉内进行冷却;
100.(2)粗加工
101.将退火之后得到的磨辊按照图纸进行粗加工;
102.(3)淬火
103.将粗加工得到的磨辊毛坯进行装炉,淬火处理,淬火处理工艺:铸件入炉温度控制在189℃以内,300℃以内,升温速度控制45℃/小时,在300℃时,保温1小时,300℃~650℃之间,升温速度控制53℃/小时,650℃保温1.5小时,650℃~1020℃之间,升温速度控制75℃/小时,铸件在1110℃保温4.5小时,保温时间根据铸件壁厚适当调整;保温之后,断电,随炉冷却,待炉内温度降至1058℃保温2.5小时,出炉,淬火,淬火采用风冷+喷雾(水雾)的方式,铸件出炉之后就开始风冷+喷雾,待铸件温度降至685℃以下,停止喷雾,继续风冷,风冷至550℃以下,停止吹风,空气中自然冷却;
104.(4)回火
105.将淬火之后的铸件,重新装炉,进行回火,回火工艺:铸件入炉温度控制在188℃以下,升温速度控制51℃/小时,在560℃时,保温7.5小时。保温时间达到之后,出炉,空气中自然冷却,回火2次;
106.(5)精加工
107.将回火之后的磨辊按照图纸要求,进行精加工;
108.(6)质量检测
109.将磨辊成品进行硬度、冲击韧性,超声波探伤检测;
110.试样随铸件一起热处理,磨辊基体力学性能为:冲击性能(试样无缺口):11j/cm2,hrc59.5。镶块力学性能为:冲击韧性(试样无缺口)23.5j/cm2,hrc62;
111.(7)包装入库
112.将满足图纸要求的磨辊成品包装,入库。
113.实施例2
114.一种立磨磨辊,包括磨辊基体和镶块,镶块部分包括纵向镶块条1和横向镶块条2,纵向镶块条1和横向镶块条2都有与基体外表面贴合的弧度,纵向镶块条间隔排列均匀分布于基体表面,相邻两纵向镶块条间有多组横向镶块条均匀分布,各镶块条与基体融合的那部分全部采用纵截面为等腰梯形的结构,露在基体外面的部分,纵向镶块条采用纵截面为半圆形的结构,横向镶块条采用纵截面为等边三角形的结构,所述的镶块部分采用中铬合金钢,基体采用高铬合金钢。镶块露在基体外面的部分与埋入基体的部分高度一致。
115.其制备方法步骤如下:
116.(一)制备镶块预制体
117.(1)准备原材料
118.按照计算好的重量百分比例称取废钢、硅铁、锰铁、铬铁、镍铁、钼铁、铜、钒铁、钛铁、硼铁、铌铁、钨铁、铝线、氮化铬、稀土硅铁等材料;
119.其中,熔炼镶嵌预制体时用的变质剂原料:硼铁、铝线、稀土硅、碳化硅、钛铁;
120.(2)造型
121.利用树脂砂砂型进行造型;
122.(3)原料的熔炼
123.将原材料进行熔炼,熔炼顺序按照废钢、铁合金、废钢、贵重金属的顺序,贵重金属后期加入,以免烧损。当铁液达到1550℃时,进行预脱氧处理,先加入0.55%锰铁,8分钟以后再加入0.25%硅铁,化验铁水化学成分,调整铁液化学成分当炉内铁液温度达到1630℃,插入0.028%铝线,然后出炉;
124.(4)孕育浇注
125.将得到的铁液倒入浇包进行变质孕育,变质剂为:0.263%硼铁、0.121%铝线、0.256%稀土硅、0.115%碳化硅、0.138%钛铁,铁水出炉之前,提前把这些变质剂进行烘干,混匀,放入浇包底部,铁水经过孕育之后,浇入铸型,冷却至室温得到获得毛坯;
126.(5)锻造成型
127.将得到的毛坯进行打磨,清理干净之后,放入加热炉进行加热,加热温度控制在1118℃,保温时间2.5小时,保温后,将毛坯放入模具中进行锻造成型,始锻温度为1110℃,终锻温度≥988℃,锻造之后获得镶嵌预制体,锻造成型的预制体经过再次清理打磨之后待用;
128.制备的镶块预制体化学成分质量百分比:c:0.598%,si:0.425%,mn:0.628%,s:0.021%、p:0.021%,cr:6.238%,ni:0.239%,mo:1.437%,cu:0.528%,v:1.726%,ti:0.0235%,re:0.031%,b:0.0036%,nb:0.288%,w:0.398%,al:0.0395%,n:0.066%,余量为fe及杂质。
129.(二)制备复合磨辊
130.(1)准备原材料
131.称取废钢、硅铁、锰铁、低碳铬铁、镍铁、钼铁、铜、电解钒、钛铁、稀土硅铁、硼铁、铌铁、钨铁、锆铁、铝线、氮化铬等材料;
132.其中,熔炼磨辊基体时用的变质剂原料:稀土硅铁、钛铁、氮化铬、锆铁、硼铁;
133.(2)造型
134.将镶块预制体放入铸型,其中,最终需要露在工作面外面的镶嵌体需要埋入铸型砂内部,另一部分不需要埋入铸型;目的是浇注合金液之后,不需要外露的那部分被合金液包裹,与磨辊基体合金液熔为一体;造型过程中,确保镶块预制体均匀分布于铸型内部;浇注之前,将镶块预制体预热245℃;
135.(3)原料的熔炼
136.将原材料进行熔炼,熔炼顺序按照废钢、铁合金、废钢、贵重合金的顺序进行,当铁液达到1550℃时,进行预脱氧处理,先加入0.43%锰铁,10分钟以后再加入0.13%硅铁,化验铁水化学成分,调整铁液化学成分,当炉内铁液温度达到1630℃,插入0.023%铝线,然后出炉;(4)变质孕育浇注
137.将得到的铁液倒入浇包进行变质孕育,变质孕育剂为0.453%稀土硅铁、0.252%钛铁、0.234%氮化铬、0.068%锆铁、0.245%硼铁。出炉前提前把变质孕育剂,提前把变质孕育剂烘干,放入浇包内,浇注至磨辊铸型内,冷却至室温开箱;
138.(5)清理打磨
139.将得到的铸件去除浇冒口,然后清理打磨,得到复合铸造磨辊毛坯;
140.制备的磨辊基体的化学成分质量百分比:c:1.315%,si:0.327%,mn:0.881%,s:0.022%、p:0.023%,cr:13.281%,ni:0.621%,mo:0.891%,cu:0.627%,v:0.215%,ti:0.0299%,re:0.132%,b:0.0811%,nb:0.116%,w:0.233%,zr:0.0391%,al:0.0325%,n:0.0018%,余量为fe及杂质。
141.(三)磨辊热处理
142.(1)退火
143.将得到的磨辊毛坯进行装炉,退火处理,退火处理工艺:铸件入炉温度控制在185℃以下,300℃以下,升温速度控制33℃/小时,在300℃时,保温1小时,300℃~650℃之间,升温速度控制53℃/小时,650℃保温1.5小时,650℃~1100℃之间,升温速度控制75℃/小时,铸件在1100℃保温5.5小时。1100℃保温之后,随炉在炉内进行冷却;
144.(2)粗加工
145.将退火之后得到的磨辊按照图纸进行粗加工;
146.(3)淬火
147.将粗加工得到的磨辊毛坯进行装炉,淬火处理,淬火处理工艺:铸件入炉温度控制在189℃以内,入炉后300℃以内,升温速度控制45℃/小时,在300℃时,保温1小时,300℃~650℃之间,升温速度控制53℃/小时,650℃保温1.5小时,650℃~1110℃之间,升温速度控制75℃/小时,铸件在1110℃保温4.5小时,保温时间根据铸件壁厚适当调整;保温之后,断电,随炉冷却,待炉内温度降至1056℃保温2.5小时,出炉,淬火,淬火采用风冷+喷雾(水雾)的方式,铸件出炉之后就开始风冷+喷雾,待铸件温度降至685℃以下,停止喷雾,继续风冷,风冷至550℃以下,停止吹风,空气中自然冷却;
148.(4)回火
149.将淬火之后的铸件,重新装炉,进行回火,回火工艺:铸件入炉温度控制在188℃以下,升温速度控制51℃/小时,在555℃时,保温7.5小时,保温时间达到之后,出炉,空气中自
然冷却,回火2次;
150.(5)精加工
151.将回火之后的磨辊按照图纸要求,进行精加工;
152.(6)质量检测
153.将磨辊成品进行硬度、冲击韧性,超声波探伤检测;
154.试样随铸件一起热处理,磨辊基体力学性能为:冲击性能(试样无缺口):12j/cm2,hrc60。镶块力学性能为:冲击韧性(试样无缺口)22.5j/cm2,hrc61.5;
155.(7)包装入库
156.将满足图纸要求的磨辊成品包装,入库。
157.实施例3
158.结构和制备方法步骤与实施例2相同,不同的是磨辊基体的化学成分:
159.(1)磨辊基体化学成分重量百分比含量为:c:1.388%,si:0.427%,mn:0.893%,s:0.021%、p:0.021%,cr:14.281%,ni:0.665%,mo:0.891%,cu:0.629%,v:0.225%,ti:0.0415%,re:0.182%,b:0.0811%,nb:0.156%,w:0.349%,zr:0.0391%,al:0.0325%,n:0.0028%,余量为fe及杂质。
160.(2)热处理后磨辊基体力学性能指标:冲击性能(试样无缺口):13j/cm2,hrc59.5。
161.(3)镶块化学成分、力学性能与实施例2相同。
162.实施例4
163.制备方法步骤与实施例2相同,不同的是磨辊基体的化学成分。
164.(1)磨辊基体化学成分重量百分比含量为:c:1.355%,si:0.427%,mn:0.889%,s:0.021%、p:0.021%,cr:14.556%,ni:0.671%,mo:0.923%,cu:0.637%,v:0.338%,ti:0.0299%,re:0.136%,b:0.0811%,nb:0.136%,w:0.233%,zr:0.0391%,al:0.0375%,n:0.0038%,余量为fe及杂质。
165.(2)热处理后磨辊基体力学性能指标:冲击性能(试样无缺口):10.5j/cm2,hrc61。
166.(3)镶块化学成分、力学性能与实施例2相同。
167.实施例5
168.制备方法步骤与实施例2相同,不同的是磨辊基体的化学成分。
169.(1)磨辊基体化学成分重量百分比含量为:c:1.365%,si:0.455%,mn:0.886%,s:0.022%、p:0.023%,cr:15.111%,ni:0.621%,mo:0.923%,cu:0.637%,v:0.265%,ti:0.0299%,re:0.219%,b:0.0953%,nb:0.116%,w:0.233%,zr:0.0391%,al:0.0325%,n:0.0035%,余量为fe及杂质。
170.(2)热处理后磨辊基体力学性能指标:冲击性能(试样无缺口):12.5j/cm2,hrc60。
171.(3)镶块化学成分、力学性能与实施例2相同。
172.实施例6
173.制备方法步骤与实施例2相同,不同的是磨辊基体的化学成分和镶块的化学成分。
174.(1)磨辊基体化学成分重量百分比含量为:c:1.386%,si:0.442%,mn:0.899%,s:0.021%、p:0.023%,cr:14.355%,ni:0.699%,mo:0.911%,cu:0.628%,v:0.331%,ti:0.0299%,re:0.136%,b:0.0811%,nb:0.166%,w:0.349%,zr:0.0456%,al:0.0325%,n:0.0018%,余量为fe及杂质。
175.(2)镶块化学成分重量百分比含量为:c:0.611%,si:0.421%,mn:0.588%,s:0.021%、p:0.024%,cr:6.186%,ni:0.198%,mo:1.115%,cu:0.513%,v:1.726%,ti:0.029%,re:0.031%,b:0.0031%,nb:0.268%,w:0.353%,al:0.0355%,n:0.056%,余量为fe及杂质。
176.(3)磨辊基体热处理后力学性能指标:冲击性能(试样无缺口):13.5j/cm2,hrc60.5。
177.(4)镶块热处理后力学性能指标:冲击性能(试样无缺口):19.5j/cm2,hrc62。
178.以上是结合具体实施例对本发明的详细介绍,本发明的保护范围不限于此。